关键过程控制程序
关键过程控制程序

关键过程控制程序关键过程控制程序1 范围本程序规定了对形成产品质量起决定作用的关键过程进行识别、确定的方法和质量控制要求,目的在于对关键过程实施有效控制。
本程序适用于航空产品生产中关键过程的质量控制。
2 规范性引用文件下列文件中的条款通过本程序的引用而成为本程序的条款。
凡是注日期的引用文件,其随后所有的修改单(不包括勘误的内容)或修订版本均不适用于本程序。
凡是不注日期的引用文件,其最新版本适用于本程序。
GJB9001A-2001 质量管理体系要求 GJB190 特性分类GJB467 工序质量控制要求 Q/1DZG2.3 记录控制程序BD17 关于贯彻“GJB190—86特性分类”的规定 3 术语和定义本程序采用GJB467和GJB9001A给出的术语和定义。
4 管理职责4.1 质量管理部门对本程序的正确执行在管理上负责。
4.2 设计研究部门对确定的产品关键件(特性)、重要件(特性)的正确性负责。
4.3 工艺、冶金管理部门对本系统生产单位编制工艺规程中确定的关键过程的正确性、完整性负责。
4.4 供应部门对关键材料、元器件符合技术要求负责。
4.5 质量检验部门对生产过程中正确贯彻关键过程控制要求进行监督,并对检测质量直接负责。
4.6 各生产单位对生产过程中具体实施关键过程控制的要求负责。
5 工作程序识别和确定关键过程的关键过程标识关键过程控制关键过程控制有效性的评价5.1 关键过程的识别和确定1关键过程一般包括形成关键、重要特性的过程;加工难度大、质量不稳定、易造成重大经济损失的过程;被确定为关键、重要特性的外购、外协件入厂验收工序等。
5.1.1 编制关键件(特性)、重要件(特性)项目明细表设计研究部门根据GJB190和BD17的规定,在对产品进行特性分析的基础上,确定关键件(特性)、重要件(特性),并按产品汇总编制“关键件、重要件目录和特性分类表”,经顾客代表审签同意后归档分发给各生产单位和工艺管理、冶金管理、质量管理、质量检验、供应等部门及顾客代表。
关键过程控制程序
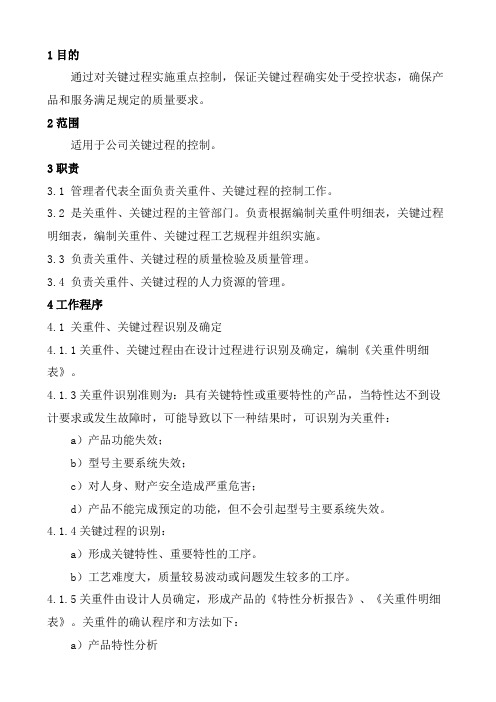
1目的通过对关键过程实施重点控制,保证关键过程确实处于受控状态,确保产品和服务满足规定的质量要求。
2范围适用于公司关键过程的控制。
3职责3.1 管理者代表全面负责关重件、关键过程的控制工作。
3.2 是关重件、关键过程的主管部门。
负责根据编制关重件明细表,关键过程明细表,编制关重件、关键过程工艺规程并组织实施。
3.3 负责关重件、关键过程的质量检验及质量管理。
3.4 负责关重件、关键过程的人力资源的管理。
4工作程序4.1 关重件、关键过程识别及确定4.1.1关重件、关键过程由在设计过程进行识别及确定,编制《关重件明细表》。
4.1.3关重件识别准则为:具有关键特性或重要特性的产品,当特性达不到设计要求或发生故障时,可能导致以下一种结果时,可识别为关重件:a)产品功能失效;b)型号主要系统失效;c)对人身、财产安全造成严重危害;d)产品不能完成预定的功能,但不会引起型号主要系统失效。
4.1.4关键过程的识别:a)形成关键特性、重要特性的工序。
b)工艺难度大,质量较易波动或问题发生较多的工序。
4.1.5关重件由设计人员确定,形成产品的《特性分析报告》、《关重件明细表》。
关重件的确认程序和方法如下:a)产品特性分析产品特性分析过程分为:技术要求分析、设计分析、选定检测单元和划定特性类别。
技术要求分析主要包括:产品功能分析、功能要求的性能持续时间、环境条件、可维修性、失效影响分析等。
设计分析应考虑:材料性能及选用、工艺过程分析、配合与互换性、设计寿命、可靠性和安全性分析等。
根据技术要求分析和设计分析选定保证特性可检验(检测)的检测单元项目,形成《特性分析报告》。
b)形成清单(明细表),制定过程控制措施。
设计人员经过产品特性分析确定关重件,形成清单并制定过程控制措施(必要时征求外包承制方意见)。
c)审批关重件的产品特性分析报告需经技术负责人审批,经批准后的《特性分析报告》应随设计文件、图样同时下发,作为确定关键工序的主要依据之一。
关键特殊过程确认控制程序
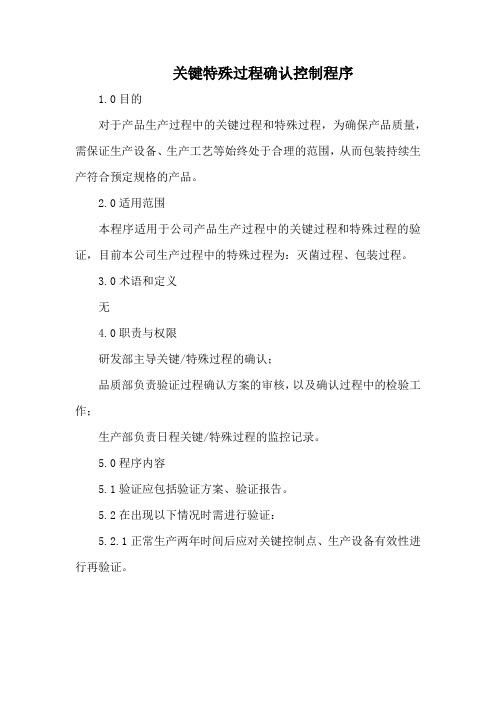
关键特殊过程确认控制程序1.0目的对于产品生产过程中的关键过程和特殊过程,为确保产品质量,需保证生产设备、生产工艺等始终处于合理的范围,从而包装持续生产符合预定规格的产品。
2.0适用范围本程序适用于公司产品生产过程中的关键过程和特殊过程的验证,目前本公司生产过程中的特殊过程为:灭菌过程、包装过程。
3.0术语和定义无4.0职责与权限研发部主导关键/特殊过程的确认;品质部负责验证过程确认方案的审核,以及确认过程中的检验工作;生产部负责日程关键/特殊过程的监控记录。
5.0程序内容5.1验证应包括验证方案、验证报告。
5.2在出现以下情况时需进行验证:5.2.1正常生产两年时间后应对关键控制点、生产设备有效性进行再验证。
5.2.2当关键/特殊过程中,影响产品质量的主要因素(如工艺、质量控制方法、主要原料、主要生产设备等)发生改变时,质检或用户反馈出现严重不合格项时,应进行相关内容的重新验证。
5.2.3当生产车间停产超过六个月的期限后又重新生产前应对生产环境、主要生产设备、关键工序进行验证。
5.2.4 新产品试生产前对设计开发进行验证。
5.2.5主要原料生产商发生变化,投料使用前需要进行验证。
5.3验证方案:验证方案应包括以下内容1)验证目的。
2)验证范围。
3)验证小组成员。
4)验证相关材料。
5)验证方法及标准。
5.4验证方法:5.4.1变换方法进行计算,用不同的计算方法都能达到同一结果,证明计算方法是可信的。
5.4.2 将新设计结果与已证实的类似设计进行比较。
5.4.3 对样品进行检验和试验。
5.4.4 对文件发放前的设计阶段文件进行评审。
5.4.5由公司在供方处对产品进行验证或对其服务能力进行评价。
5.4.6 由公司对供方的送货进行检验。
5.4.7由公司组织生产连续多批并进行检测。
5.5 验证方案及报告的批准验证方案及验证报告由管理者代表或总经理批准。
5.6验证报告:验证报告应包括以下内容a)验证目的。
关键过程控制程序
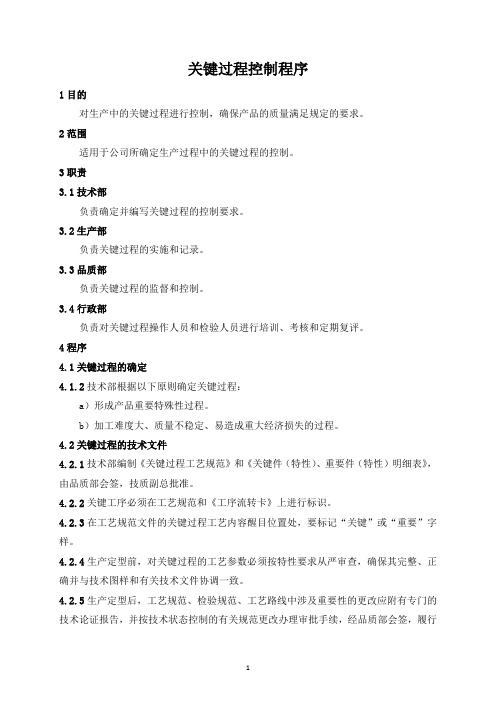
关键过程控制程序1目的对生产中的关键过程进行控制,确保产品的质量满足规定的要求。
2范围适用于公司所确定生产过程中的关键过程的控制。
3职责3.1技术部负责确定并编写关键过程的控制要求。
3.2生产部负责关键过程的实施和记录。
3.3品质部负责关键过程的监督和控制。
3.4行政部负责对关键过程操作人员和检验人员进行培训、考核和定期复评。
4程序4.1关键过程的确定4.1.2技术部根据以下原则确定关键过程:a)形成产品重要特殊性过程。
b)加工难度大、质量不稳定、易造成重大经济损失的过程。
4.2关键过程的技术文件4.2.1技术部编制《关键过程工艺规范》和《关键件(特性)、重要件(特性)明细表》,由品质部会签,技质副总批准。
4.2.2关键工序必须在工艺规范和《工序流转卡》上进行标识。
4.2.3在工艺规范文件的关键过程工艺内容醒目位置处,要标记“关键”或“重要”字样。
4.2.4生产定型前,对关键过程的工艺参数必须按特性要求从严审查,确保其完整、正确并与技术图样和有关技术文件协调一致。
4.2.5生产定型后,工艺规范、检验规范、工艺路线中涉及重要性的更改应附有专门的技术论证报告,并按技术状态控制的有关规范更改办理审批手续,经品质部会签,履行比一般件更高一级的审批手续。
4.2.6对加工中难度大、要求高、技术复杂的关键过程,技术部应编制具体的作业指导书,以保证生产的顺利进行。
4.3关键过程的控制4.3.1重要材料、外包件的控制a)重要材料、外包件应由经评定合格的供方定点供应,对于影响重要材料、外包件的辅助材料也应由经评定合格的供方定点供应。
如改变供方,则必须按规定对其重新进行评定合格并经品质部同意方可进货,如改变供应技术条件和生产条件时,则必须按规定对其重新进行评定合格并经技术部和品质部同意后方可进货。
b)重要材料、外包件到货后,由采购员作出明确标识后报品质部检验员进行检验。
检验员应按照重要材料、外包件的检验工艺规范进行检验。
关键过程质量控制程序

关键过程质量控制程序
关键过程质量控制程序是一种通过管理和监控关键过程,以确保产品或服务质量达到预期要求的程序。
以下是一个基本的关键过程质量控制程序的步骤:
1. 确定关键过程:,需要明确哪些过程是整个生产流程中最关键和关键的过程。
这些关键过程对产品或服务的质量有直接影响,需要重点管理和控制。
2. 制定质量标准:制定明确的质量标准,以确定产品或服务需要达到的质量要求。
这些标准可以包括尺寸、外观、性能等方面的要求。
3. 设计质量控制计划:根据关键过程和质量标准,制定详细的质量控制计划。
该计划应包括实施质量检查的时间、方法和责任人员。
4. 实施质量控制措施:按照质量控制计划,执行相应的质量控
制措施。
这包括监督关键过程,确保其按照标准进行操作,并采取
必要的纠正措施。
5. 进行质量检查:定期进行质量检查,以确保关键过程达到质
量要求。
检查可以在关键过程进行时进行,也可以在过程完成后进行。
6. 分析并纠正问题:如果发现关键过程存在问题或不符合质量
要求,需要进行分析,并采取纠正措施。
这可能包括调整过程、修
复设备或重新培训员工等措施。
7. 持续改进:根据质量检查和问题分析的结果,推动持续改进。
通过改善关键过程,提高产品或服务的质量水平。
8. 文档和记录:对于所有的质量控制活动,应进行文档和记录。
这包括记录关键过程的操作和检查结果,以及相关的纠正和改进措施。
以上是一个基本的关键过程质量控制程序的步骤,具体的程序可以根据组织的需求和特定行业的要求进行定制。
关键过程质量控制程序
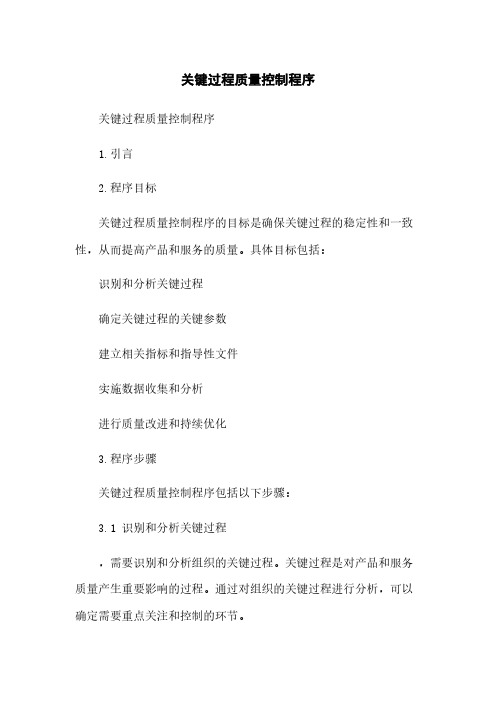
关键过程质量控制程序关键过程质量控制程序1.引言2.程序目标关键过程质量控制程序的目标是确保关键过程的稳定性和一致性,从而提高产品和服务的质量。
具体目标包括:识别和分析关键过程确定关键过程的关键参数建立相关指标和指导性文件实施数据收集和分析进行质量改进和持续优化3.程序步骤关键过程质量控制程序包括以下步骤:3.1 识别和分析关键过程,需要识别和分析组织的关键过程。
关键过程是对产品和服务质量产生重要影响的过程。
通过对组织的关键过程进行分析,可以确定需要重点关注和控制的环节。
3.2 确定关键过程的关键参数在识别了关键过程后,需要确定关键过程的关键参数。
关键参数是对关键过程实现质量控制的关键要素。
通过确定关键参数,可以制定相应的控制策略和措施。
3.3 建立相关指标和指导性文件为了对关键过程进行质量控制,需要建立相关指标和指导性文件。
指标可以用来衡量关键过程的性能和质量,指导性文件可以提供操作指南和标准,以确保关键过程的执行符合要求。
3.4 实施数据收集和分析为了了解关键过程的实际运行情况,需要进行数据收集和分析。
通过收集和分析数据,可以评估关键过程的稳定性和一致性,并及时发现异常情况和问题。
3.5 进行质量改进和持续优化根据数据分析的结果,可以进行质量改进和持续优化。
通过改进关键过程的控制策略和措施,可以提高关键过程的稳定性和一致性,进一步提高产品和服务的质量。
4.程序执行和监督关键过程质量控制程序的执行和监督是确保程序有效实施的关键环节。
通过执行和监督,可以及时发现和解决问题,确保关键过程质量控制的有效性和持续性。
5.关键过程质量控制程序是一种有效管理和控制关键过程的方法。
通过识别和分析关键过程,确定关键参数,建立指标和指导性文件,实施数据收集和分析,以及进行质量改进和持续优化,可以提高产品和服务的质量,满足客户的需求和期望。
组织应该重视关键过程质量控制,并建立相应的程序和机制。
关键过程控制点控制程序(质量控制点控制程序)4
(质量控制点)关键过程控制点控制程序一、目的:根据《质量管理办法》第十四条生产工艺的质量管理的要求,建立(质量控制点)关键过程控制点,应用数理统计等科学方法加强管理,使主要工艺参数和质量指标处于受控状态,保证产品质量。
二、范围:反应岗位精馏岗位三、必备的条件及岗位职责:①设备:定期维护保养,定期检查,定期修理,确保正常运行。
②工艺:严格执行工艺操作规程,确保工艺合格率95%。
③检验:严格执行半成品、成品检验中的规定,确保检验准确率100%。
④人员:操作人员培训考核,合格后持证上岗。
四、关键过程控制点(质量控制点)控制程序:1、关键过程控制点(质量控制点)是按产品制造过程中必须重点控制质量特性的环节,凡符合下列要求的需考虑设立控制点:1)、产品性能、安全、寿命有直接影响的;2)、出现不良品较多的工序;3)、用户反映、定期检查等多次出现不稳定的项目。
2、关键过程控制点由生产运行部会同质检中心和有关车间,根据工艺文件或内容标准的质量特性确定。
公司加工生产中的关键过程控制点(质量控制点):反应、精馏。
关键过程控制点(质量控制点)应做独立的原始记录。
3、关键过程控制点(质量控制点)由车间负责人按人、设备、工艺物料、方法和环境等方面严格管理,应对特殊工况下的关键过程控制点(质量控制点)的参数调整及时做好记录,分析。
4、关键过程控制点(质量控制点)的操作人员必须按技术文件的内容,保证进行正确操作,并按要求做好原始记录工作,及时分析,及时解决,及时上报反馈。
5、关键过程控制点(质量控制点)上的设备、工艺条件应按时巡检,需要校验和维护的按相关规定进行。
6、关键过程控制点(质量控制点)应配备相应的操作规程,应包括非正常操作时的处理方法。
7、生产车间对关键过程控制点(质量控制点)资料应及时分析,每月工艺分析会议上汇总分析。
8、公司根据《质量管理办法》的相关规定,对工艺质量管理好,产品质量稳定或有所提高的关人员给予奖励,对管理不好造成质量下降的给予处罚。
关键工序控制程序
关键工序控制程序1 目的通过对关键工序(质量控制点)的有效控制,以确保产品质量满足顾客及法律法规的要求。
2 适用范围适用于对公司所有改装车产品。
3 职责3.1 工艺部门负责关键工序的确定及其作业指导书的编制。
3.2 质量部门负责质量控制点的设置和检验。
3.3 工艺部门负责关键工序工艺纪律检查。
4 程序4.1 关键控制点的确定4.1.1 工艺部门根据设计文件【产品质量特性重要度分级表】编制【产品质量控制图】,【产品质量控制图】上应标明关键过程和控制内容指标。
4.1.2 【产品质量控制图】编制应考虑到产品适用法律法规和强制性标准的要求,以及本公司的工艺条件和顾客对以往产品的质量反馈。
4.1.3 【产品质量控制图】审批前,工艺部门应会同设计部门和质量部门进行会议评审。
4.1.4 质量部门根据【产品质量控制图】指定的关键工序设置质量控制点,确定其检查项目、指标、偏差和检验频次。
4.2 工艺文件4.2.1 工艺部门应编制关键过程作业指导书,作业指导书应内容完整并能指导作业人员进行正确操作。
4.2.2 作业指导书发布前应进行审批,必要时经组织专家审查。
4.3 过程控制4.3.1 材料关键工序所用原辅材料、配件和半成品应经质量部门检验接收,流入本工序加工前操作人员应予复验,确保其适用性。
复验发现不适用及时标识并通知检验人员。
4.3.2 设备设备管理部门根据工艺要求,配置适宜的设备,确保其精度和加工能力;制造工程部根据工艺要求制造工艺工装。
设备管理部门应编制设备工装安全操作规程、检修计划和维护保养细则。
操作人员按【设备维护保养细则】的要求,对设备工装进行日常维护保养。
设备维修人员应【设备年度检修计划】的要求,对设备工装的功能、精度和安全防护进行周期检修。
4.3.3 人员操作人员应经过培训、考核合格;法律法规对岗位有要求的按其要求执行。
操作人员应能看懂设计文件、工艺文件,应能正确操作设备工装,应知晓质量控制点验收标准。
关键工序控制程序
关键工序控制程序一、目的为稳定和提高产品质量,应对产品生产流程中,对重要环节加以控制,规范抄造,确保产品在生产过程中安全、符合工艺要求二、范围品保部、制浆车间,造纸车间全体员工三、程序1.打浆1.1.交接时应使本岗位各部处于正常运行状态,如本班所属岗位有异常和故障(包括修复和未修复暂不影响生产的),临时接通知的一些注意事项,交班人都应向接班人交待清楚,认真填写岗位原始纪录,待接班人检查完毕,无异常,签字认可后方可下班.1.2.根据工艺要求进行调节磨盘间隙,控制进出浆的压力,流量及电流(电流不得超过电机载荷电流的极限)。
控制好浆料浓度,及时取样检测,浆料合格后,关闭回流管阀门,开启成浆管路阀门。
1.3.打浆工检验员必须每1小时对成品浆料检测一次并做好记录,当班检验员将检测结果及时通知打浆工,以便打浆工调整。
1.4.车间主任应每星期对磨片检查是否有破损,定期对磨片进行更换。
1.5.品保部不定时对半成品/成品浆料进行检测,检测其是否达到工艺要求。
2.调料2.1)交接时应使本岗位各部处于正常运行状态,如本班所属岗位有异常和故障(包括修复和未修复暂不影响生产的),临时接通知的一些注意事项,交班人都应向接班人交待清楚,认真填写岗位原始纪录,待接班人检查完毕,无异常,签字认可后方可下班.2.2)检查机前池、配料池库存浆料情况,保证纸机浆料供应;2.3)依生产工艺通知单要求就化工辅料予以稀释,确保生产的正常运行;2.4)根据纸机的开停来控制好单圆网的运行于停止,并调节好浆位;2.5)配料工检验员每缸浆必须检测PH值一次并做好记录;2.6)化工原料在稀释前必须过滤。
化工桶每班必须清洗一次。
2.7)每隔1个小时:检查连续添加化工辅料贮存桶的剩余贮存量,及时按照化工辅料添加浓度稀释待用;2.8)检查计量泵、圆网浓缩机的使用情况,有异常时应及时处理或通知班长。
2.9)每隔2个小时:检查配浆池,抄造池,损纸池各浆池贮浆情况,及时按照生产工艺通知单要求进行配浆;2.10)品保部、车间负责人不定时对车间进行抽检已确保其指标符合要求;3.抄造3.1)交接时应使本岗位各部处于正常运行状态,如本班所属岗位有异常和故障(包括修复和未修复暂不影响生产的),临时接通知的一些注意事项,交班人都应向接班人交待清楚,认真填写岗位原始纪录,待接班人检查完毕,无异常,签字认可后方可下班.3.2)检查各压区的压力和烘缸的进汽压力是否按照工艺要求执行。
关键工序控制程序
1目的:明确品质关键点,并加以控制,以确保产品质量,满足客户要求。
2范围:铁罐生产、品管。
3定义:关键工序:对产品性能、质量影响较大或客户要求重点控制之工序。
4职责:4.1品管课应在产品生产前制定《质量控制计划》。
4.2品管课应安排人员按要求对关键工序进行检验。
4.3品管人员应将检验数据进行记录及统计分析。
5内容:5.1关键工序确认:5.1.1所有产品在生产前,品管应确认是否存在对产品性能、质量影响较大导致无法满足客户预期要求之工序,如有,应在《质量控制计划》中标为关键工序,并按本规定进行控制。
5.1.2如客户要求对某工序进行重点控制,亦应在《质量控制计划》中标为关键工序,并按本规定进行控制。
5.2关键工序之控制:5.2.1品管课应在《质量控制计划》、《检验标准书》中确认关键尺寸及公差范围。
5.2.2 2.2在生产过程中,品管应每四小时对关键工序、关键尺寸进行抽检;每次抽查20PCS产品,并记录检测数值。
5.2.3如检查时,发现产品尺寸超出关键尺寸的可接受范围,应立即查找原因,并向上级反馈:A发现不合格时,立即再抽检50pcs,确认是否为个例。
B如为个例,应立即查找不合格原因,并进行改善。
C如非个例,应立即要求生产线停线整改,直至问题解决。
D发现不合格时,立即品管主管进行反馈,由品管主管另行开具《纠正、预防措施报告》进行再调查,直至问题改善。
5.3记录控制:检查后,品管人员应交检验结果记录于《关键尺寸统计控制图》,并进行统计分析。
6附件:《关键尺寸统计控制图》《纠正、预防措施报告》《质量控制计划》。
- 1、下载文档前请自行甄别文档内容的完整性,平台不提供额外的编辑、内容补充、找答案等附加服务。
- 2、"仅部分预览"的文档,不可在线预览部分如存在完整性等问题,可反馈申请退款(可完整预览的文档不适用该条件!)。
- 3、如文档侵犯您的权益,请联系客服反馈,我们会尽快为您处理(人工客服工作时间:9:00-18:30)。
关键过程控制程序
编制:
审核:
批准:
版次:_B—1.0—
分发号:______________
受控状态:_____________
2018-01-02 发布2018-01-02 实施
目次
目次. (1)
关键过程控制程序. (3)
1 目的 (3)
2 适用范围 (3)
3 职责与权限 (3)
4 工作程序 (3)
4.1 本公司关键过程为生产产品的关键过程 (3)
4.2 关键过程的确定 (3)
4.3 关键过程的评审 (3)
4.4 产品生产关键过程的控制. (4)
4.5 标识 (4)
4.6 不合格品控制 (4)
4.7 记录控制 (4)
4.8 更改控制 (5)
4.9 防护控制 (5)
5 记录 (5)
关键过程控制程序
1 目的
按Q/XX QF01-2018《质量手册》7.5.6关键过程要求规定,识别关键过程,并对其实施有效控制,特编制本程序文件。
实施和保持本程序,确保在生产和服务提供过程中关键过程得到有效的控制。
2 适用范围
适用于本公司在所有生产和服务提供过程中对关键过程的识别与控制。
3 职责与权限
3.1 技术中心是关键控制过程的归口管理部门,对生产产品关键过程进行识别、控制,负责:
a) 编制机械加工关键过程明细表;
b) 编制关键工序作业指导书;
c) 对关键工序工艺文件进行工艺评审;
d) 对关键工序在加工时进行技术跟踪,对首件进行工艺、工装验证。
3.2 生产制造中心负责:在关键工序首件加工时,通知工艺人员进行工序验证,并参与验证工
作。
3.3 质量管理部负责对关键过程的监督管理,编制检验规程,对关键过程实施严格的监控和检
验。
按评审后的工艺文件、相关标准、产品图纸组织生产,进行过程控制。
4 工作程序
4.1 本公司关键过程为生产产品的关键过程
4.2 关键过程的确定
对产品质量起决定作用的工序,一般包括形成关键、重要特性的工序和加工难度大、质量部稳定、易造成重大经济损失的工序;设计人员对产品进行特性分析的基础上,确定关键过程,并在相应的设计文件上做标识。
4.3 关键过程的评审
4.3.1 对关键过程设计参数和制造工艺必须严格审查,在设计评审、工艺评审中应作为重点内
容。
关键过程的评审,不必单独安排,可结合其他质量评审实施:
a) 设计文件上确定关键过程(特性)的评审,可结合设计评审进行;
b) 工艺文件中对关键特性的评审,可结合工艺评审进行;
c) 生产过程中关键过程的控制情况,可结合内部审核或产品质量评审进行;
4.3.2 特性分析报告和关键过程必须经设计人员、质量人员会签,总工批准后生效。
4.4 产品生产关键过程的控制
4.4.1 技术中心根据产品技术文件/ 资料结合生产和服务过程,确定产品的关键过程,再对已
确定的关键过程进行汇总,编制《关键过程明细表》并进行归档。
4.4.2 编制生产产品关键过程的控制文件等内容除按照Q/XXQF01-201《8 质量手册》
7.5.1
“生产和服务提供的控制”要求外,还应包括:
a) 对关键过程进行标识;
b) 对与关键过程有关人员(操作者、检验员)实行资格考核,持证上岗。
需要时,关键岗
位实行双岗制;
c) 对首件产品进行“三检” :自检、互检、专检;
d) 必要时,对关、重特性加工过程能力进行验证;
e) 适用时,运用统计技术对产品质量特性趋势进行监视;
f) 关键特性和重要特性实施百分之百检验。
不能实施百分之百检验的,应规定检验或验证方法并征得顾客
同意;
g) 填写质量记录,并归档,保存期限与产品寿命一致,保持可追溯性。
4.4.3 在关键过程明细表中,应明确与关键过程有关的产品、过程(工序)和特性要求。
4.5 标识
本公司关键过程的标识,在识别出的关键特性标识“G,重要特性标识“ Z”,一般特
性不作规定。
在《零件工艺过程卡》中按GJB190的标注方法注明关键特性、重要特性。
其相应的《零件工艺过程卡》封面或首页及质量跟踪卡上应分别进行标识。
4.6 不合格品控制
关键件、重要件的不合格品审理,按《不合格输出控制程序》Q/XX PF18-17执行。
对关键件、重要件办理次品放用(让步使用)时,应由公司级审理员审批,并征得顾客同意,关键特性不允许让步使用。
4.7 记录控制
关键过程控制所形成的记录将按照Q/XXPF18-06《成文信息控制程序》进行有效的管
理和控制
4.8 更改控制
关键过程控制的过程中,在引起文件更改时,按Q/XX PF18-06《成文信息控制程序》执行。
4.9 防护控制关键件、重要件在存放、周转和运输中,必须采取严格保护措施。
其专用包装箱或周转箱应分别用“ G'、“ Z”做出醒目标识。
5 记录
《关键过程明细表》。