影响板坯氧化因素分析_刘派
连铸减少铸坯氧化铁皮方案

连铸减少铸坯氧化铁皮方案一、减少氧化铁皮的意义目前铸造一车间连铸机主要生产20#、45#钢坯,生产过程中,铸坯表面产生大量的氧化铁皮,铸坯出拉矫机后,氧化铁皮大块大块的脱落,既影响铸坯质量及钢水收得率,同时也造成氧化铁皮清理量大,清理困难。
因而减少和防止连铸坯在冷却过程中的氧化,对提高成材率具有十分重要的意义。
解决这个问题,可有效的提高产量、减少单位成品的金属消耗、降低成本,得到显着的经济效益。
二、氧化铁皮形成机理高温钢水在连铸结晶器内凝固成型,形成一定厚度的坯壳,铸坯出结晶器后表面温度较高,暴露在空气中,与氧气及二冷室的水蒸汽发生反应,生成氧化铁。
具体反应式如下:⑴、钢与氧气的反应:2Fe+O2=2FeO3Fe+2O2=Fe3O42Fe3O4+1/2O2=3Fe2O3⑵、钢与水的反应:Fe+H2O=FeO+H23Fe+4H2O=Fe3O4+4H23FeO+H2O=Fe3O4+H2由以上反应可知,连铸坯表面的氧化铁在整个厚度上不仅仅是一种氧化铁,最多可能存在三种氧化铁,从外到内Fe2O3、Fe3O4、FeO同时存在。
而且形貌、成分、结构不同的氧化层与基体的结合力不同,FeO为面心立方、晶轴为,Fe3O4为立方晶体,晶轴为,面心立方的FeO 分解成立方晶体的Fe3O4,组织结构转变,体积产生膨胀,这就是高温铸坯表面产生氧化铁皮并容易脱落的原因。
三、铸坯氧化的影响因素1、钢水温度的影响钢水温度高,钢坯出结晶器后温度也相应增高,氧化铁皮的生成几率增大。
目前,我司连铸钢水受生产节奏及钢包、中间包保温效果差,散热快等因素的影响,上台温度普通偏高,这是造成铸坯氧化铁皮厚的一个主要原因。
2、钢中化学成份的影响钢中的一些合金元素对于连铸坯表面氧化铁皮的生成速度也有一定的影响,其中碳、硅、镍、铜、硫促进氧化铁皮形成,锰、铝、铬可以减缓氧化铁皮的形成。
因而在生产过程中,降低易产生氧化铁皮的合金元素含量,有利于减少铸坯氧化铁皮的生成。
降低加热炉氧化烧损的研究_罗宝军
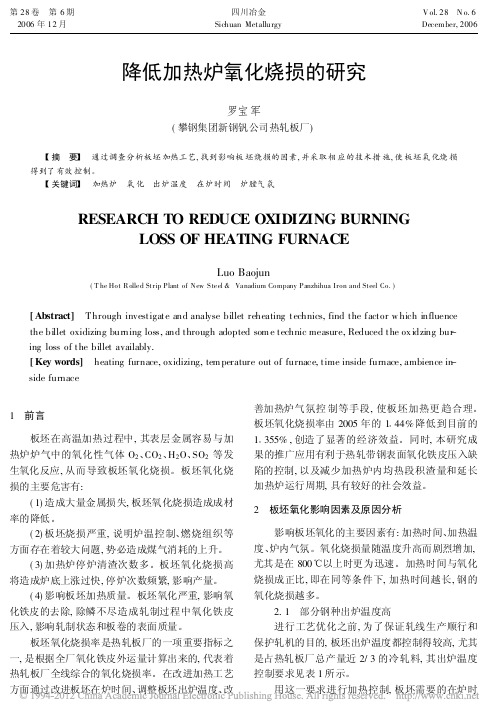
( 4) 影响板坯加热质量。板坯氧化严重, 影响氧 化铁皮的去除, 除鳞不尽造成轧制过程中氧化铁皮 压入, 影响轧制状态和板卷的表面质量。
板坯氧化烧损率是热轧板厂的一项重要指标之 一, 是根据全厂氧化铁皮外运量计算出来的, 代表着 热轧板厂全线综合的氧化烧损率。在改进加热工艺 方面通过改进板坯在炉时间、调整板坯出炉温度、改
宽度 ( mm) 1080 1080 1080 1080 1080 1080 1080 1080 1080 1080 1080 1080
冷轧料出 炉温度和精轧轧制力对比情况表
钢种
ST 12 ST 12 ST 12 ST 12 ST 12 ST 12 ST 12 ST 12 ST 12 ST 12 ST 12 ST 12
第6期
Sichuan M etallur gy
时间后, 板坯的加热质量没有受到影响, 说明优化是 合理的。
表 4 优化后的冷 轧料加热目标温度与现行工艺制度加热目标温度对比
钢种
板坯规格 ( mm)
成品厚度 ( mm)
加热目标温度( ) 优化后
08AL ST W22( SPHC) STW 23( SPHD ) STW 24( SPHE)
1 前言
板坯在高温加热过程中, 其表层金属容易与加 热炉炉气中的氧化性气体 O2、CO2、H2O、SO2 等发 生氧化反应, 从而导致板坯氧化烧损。板坯氧化烧 损的主要危害有:
( 1) 造成大量金属损失, 板坯氧化烧损造成成材 率的降低。
( 2) 板坯烧损严重, 说明炉温控制、燃烧组织等 方面存在着较大问题, 势必造成煤气消耗的上升。
薄宽规格船板氧化铁皮压入形貌缺陷成因分析及对策
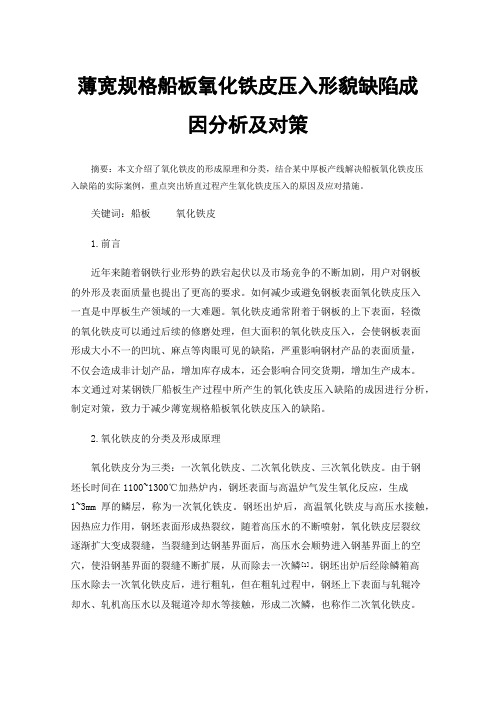
薄宽规格船板氧化铁皮压入形貌缺陷成因分析及对策摘要:本文介绍了氧化铁皮的形成原理和分类,结合某中厚板产线解决船板氧化铁皮压入缺陷的实际案例,重点突出矫直过程产生氧化铁皮压入的原因及应对措施。
关键词:船板氧化铁皮1.前言近年来随着钢铁行业形势的跌宕起伏以及市场竞争的不断加剧,用户对钢板的外形及表面质量也提出了更高的要求。
如何减少或避免钢板表面氧化铁皮压入一直是中厚板生产领域的一大难题。
氧化铁皮通常附着于钢板的上下表面,轻微的氧化铁皮可以通过后续的修磨处理,但大面积的氧化铁皮压入,会使钢板表面形成大小不一的凹坑、麻点等肉眼可见的缺陷,严重影响钢材产品的表面质量,不仅会造成非计划产品,增加库存成本,还会影响合同交货期,增加生产成本。
本文通过对某钢铁厂船板生产过程中所产生的氧化铁皮压入缺陷的成因进行分析,制定对策,致力于减少薄宽规格船板氧化铁皮压入的缺陷。
2.氧化铁皮的分类及形成原理氧化铁皮分为三类:一次氧化铁皮、二次氧化铁皮、三次氧化铁皮。
由于钢坯长时间在1100~1300℃加热炉内,钢坯表面与高温炉气发生氧化反应,生成1~3mm厚的鳞层,称为一次氧化铁皮。
钢坯出炉后,高温氧化铁皮与高压水接触,因热应力作用,钢坯表面形成热裂纹,随着高压水的不断喷射,氧化铁皮层裂纹逐渐扩大变成裂缝,当裂缝到达钢基界面后,高压水会顺势进入钢基界面上的空穴,使沿钢基界面的裂缝不断扩展,从而除去一次鳞[1]。
钢坯出炉后经除鳞箱高压水除去一次氧化铁皮后,进行粗轧,但在粗轧过程中,钢坯上下表面与轧辊冷却水、轧机高压水以及辊道冷却水等接触,形成二次鳞,也称作二次氧化铁皮。
精轧过程中,中间坯表面残余的氧化铁皮与水、空气直接接触,在钢板表面形成较薄的三次鳞,也称为三次氧化铁皮。
3.船板氧化铁皮压入过程调查分析某中厚板产线生产的多批规格厚度:(13-16mm)×宽度:(3000-3500mm)×长度:(8800-14550mm)牌号为AB/AH36的船板存在批量性氧化铁皮压入缺陷,如图1所示,钢板表面氧化铁皮呈红褐色粉末状,厚度在0.1~0.3mm。
连铸钢坯氧化铁皮产生的原因及降低措施

( X i n l i n I r o n& S t e e l G r o u p C o . , L t d . , Y i c h u n He i l o n g j i a n g , 1 5 3 0 2 5 C h i n a )
效果。
~
皮 的主要 因素有连铸 二次冷 却 配水量 , 连铸 过程 的 铸坯温度 , 连铸二 次冷却水 的温度 、 钢水 成分等 。
2 . 1 连铸二次冷却 配水 量对铸坯 氧化铁 皮的影响
3 、 4 连铸 机结 晶器 的配 水量 一般 控 制 在 1 2 0 1 4 0 t / h , 钢水 在 结 晶器 内与 铜 管壁 接 触 后 , 受 到 强 制冷 却 , 凝 结成 细小 等 轴 晶的 坯壳 , 初 生 坯壳 的 厚 度大 于 1 0 m m, 由结 晶器 拉 出的铸 坯 进入 二 次冷
Ab s t r a c t : T h r o u g h a n a l y z i n g t h e r e a s o n s f o r o x i d i z e d s c a l e o n c o n t i n u o u s c a s t i n g b i l l e t ,t h e me a s u r e s we r e f o r mu l a t e d t o r e d u c e t h e c o n t i n u o u s c a s t i n g b i l l e t o x i d a t i o n o f i r o n a n d s o me r e s u l t s h a d b e e n a .
降低加热炉板坯氧化烧损的分析与控制措施

高 月 :助理工程师 。收 ̄/ 2 0 1 3 - 0 6 . 2 4
铁在 加热 炉 内高 温 环 境 下 的 氧 化 过 程 是 F e F e O _ ÷ F e , 0 一F e : 0 。该 过 程是 氧含 量 逐 步增
f u r n a c e .B y m e a n s o f a d j u s t i n g t h e h e a t i n g s y s t e m,c o n t r o l he t c o mp o s i t i o n o f he t f u r n a c e g a s ,
加过程 ,氧原 子是 由板坯 表面 向铁基 体 内部 扩
散 、而铁原子是由板坯 内部 向外部扩散过程 。该
氧 化过 程主 要 是 铁 与 炉 气 中 O 、H O 、C O 和
板坯 氧化烧 损 的 内因 。板 坯 的合 金元 素对 其 氧化 有显 著影 响 。 a .铬 和 铝 。铬 和 铝 等 元 素 能显 著 提 高 板 坯
A b s t r a c t T h r o u g h a n a l y z i n g t h e s t r u c t u r e o f t h e o x i d e s c l a e ,t h e m a j o r f a c t o r s o f o x y g e n a t i o n l o s s
we r e r e s e a r c h e d:t h e g a s c o mp o n e n t s i n he t he a t i ng f u r n a c e,h e a t i n g t e mp e r a t u r e a n d t i me i n t h e
浅谈热轧带钢表面氧化铁皮的成因及控制

浅谈热轧带钢表面氧化铁皮的成因及控制摘要:近期热轧压氧问题出现较为频繁,导致产品降级改判情况较为严重,本论文针对出现的几种压氧产生的原因进行初步原因分析,并简单制定几种措施。
关键词:氧化铁皮,加热炉,除鳞氧化铁皮压入是影响热轧带钢表面质量的重要因素,特别是一次、二次氧化铁皮的压入,严重影响产品的表面质量,引起产品降级和质量异议,尤其对热轧酸洗板等表面质量要求比较高的产品。
针对酸洗反馈压氧、麻点、W压氧较多,影响产品质量,提出了一些措施,减少这些缺陷的产生。
1.氧化铁皮的分类及产生原因1.1.氧化铁皮形成的原因板坯在加热炉中加热时,空气中的氧气与加热状态的板坯中铁发生反应 ,在这个过程中,就会形成较厚的氧化铁皮表层,氧化铁皮由板坯内部向外依次分为FeO、Fe2O3、Fe3O4,并且越像表面氧化铁皮形成的膜就会越致密。
1.1.一次氧化铁皮(一次鳞)板坯在经过轧机轧制之前,需要在1100~1300℃的加热炉中经过预热、加热和均热阶段。
同时在马钢生产的主要汽车板和家电板的主要加热温度在1200℃以上,而在此温度下,板坯表面就容易与接触到的炉气中的氧原子发生氧化反应,从而生成一层1~3mm厚的氧化铁皮,这层氧化铁皮就称作一次氧化铁皮(一次鳞)。
一次氧化铁皮内部存在较大的空穴和缝隙,当板坯从加热炉出来之后,进入一次除鳞箱,除鳞箱中高压水在一排除鳞喷嘴的作用下,形成一条具有巨大冲击力的扇形水束,喷射到板坯表面,将板坯表面的氧化铁皮切开,形成裂缝,同时高压水透过裂缝遇到高温板坯内部急速汽化蒸发,形成类似爆破的效果,将氧化铁皮和母材剥离,同时高速流动的除鳞水与板坯呈现一定的倾斜角度将与板坯剥离的氧化铁皮冲刷离开板坯表面。
避免表面留存的氧化铁皮在轧制的时候压入到板坯中无法去除。
1.1.二次氧化铁皮(二次鳞)板坯经过出炉后的高压水一次除鳞后,一次氧化铁皮被除去,进入粗轧机进行8道次的往返粗轧,此时板坯温度一般在1100℃左右,此时在短时间的粗轧过程中板坯表面与水和空气接触,板坯表面会再次产生一层氧化铁皮,此层氧化铁皮称为二次氧化磁轭皮(二次鳞)。
板坯连铸结晶器保护渣卷渣及其影响因素的研究
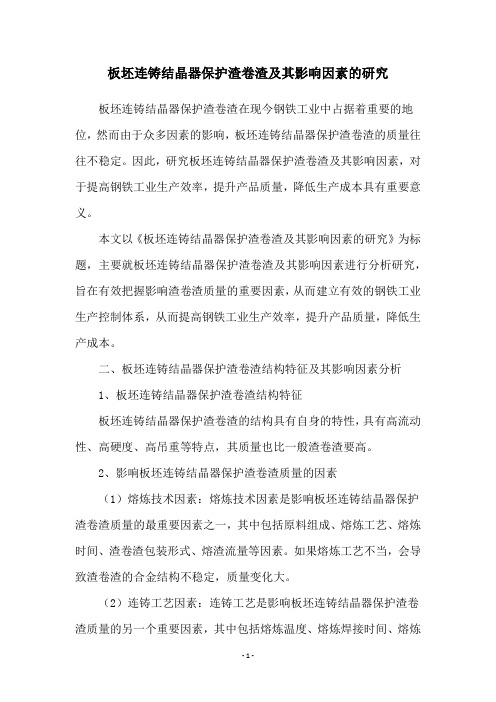
板坯连铸结晶器保护渣卷渣及其影响因素的研究板坯连铸结晶器保护渣卷渣在现今钢铁工业中占据着重要的地位,然而由于众多因素的影响,板坯连铸结晶器保护渣卷渣的质量往往不稳定。
因此,研究板坯连铸结晶器保护渣卷渣及其影响因素,对于提高钢铁工业生产效率,提升产品质量,降低生产成本具有重要意义。
本文以《板坯连铸结晶器保护渣卷渣及其影响因素的研究》为标题,主要就板坯连铸结晶器保护渣卷渣及其影响因素进行分析研究,旨在有效把握影响渣卷渣质量的重要因素,从而建立有效的钢铁工业生产控制体系,从而提高钢铁工业生产效率,提升产品质量,降低生产成本。
二、板坯连铸结晶器保护渣卷渣结构特征及其影响因素分析1、板坯连铸结晶器保护渣卷渣结构特征板坯连铸结晶器保护渣卷渣的结构具有自身的特性,具有高流动性、高硬度、高吊重等特点,其质量也比一般渣卷渣要高。
2、影响板坯连铸结晶器保护渣卷渣质量的因素(1)熔炼技术因素:熔炼技术因素是影响板坯连铸结晶器保护渣卷渣质量的最重要因素之一,其中包括原料组成、熔炼工艺、熔炼时间、渣卷渣包装形式、熔渣流量等因素。
如果熔炼工艺不当,会导致渣卷渣的合金结构不稳定,质量变化大。
(2)连铸工艺因素:连铸工艺是影响板坯连铸结晶器保护渣卷渣质量的另一个重要因素,其中包括熔炼温度、熔炼焊接时间、熔炼焊接气体类型等。
如果连铸工艺不当,会导致渣卷渣的熔炼结构不稳定,影响渣卷渣的性能。
(3)结晶器工艺因素:结晶器工艺也是影响板坯连铸结晶器保护渣卷渣质量的重要因素,其中包括结晶器的工作状态、梁板的尺寸及材料、梁板内部温度、结晶器温度差、保护气体类型、结晶器转速等因素。
如果结晶器工艺不当,会导致渣卷渣的熔晶结构不稳定,影响渣卷渣的性能和质量。
三、板坯连铸结晶器保护渣卷渣优化技术1、优化熔炼技术优化熔炼技术是提高板坯连铸结晶器保护渣卷渣质量的重要手段之一。
需要注意的是,熔炼技术的改善应从有效的控制原料组成、熔炼工艺、熔炼时间、渣卷渣包装形式、熔渣流量等因素入手,以确保板坯连铸结晶器保护渣卷渣质量稳定可靠。
环形炉坯料氧化烧损的影响及措施精品资料

环形炉;氧化烧损;仿真计算;空燃比;加热制度
坯料在环形加热炉内加热过程中表面会产生氧化,氧化铁皮的产生不仅损害了钢的性能,还降低了钢的成材率[1]。氧化铁皮的热导率比金属低很多,降低了坯料的传热效率,从而使产量降低,燃耗增高[2-4]。坯料在出炉后运往轧线的过程中,其表面的氧化铁皮坯料分离,掉落并堆积在相关设备底部,导致清渣周期缩短,增加劳动强度。因此,研究坯料加热时的氧化特性,减少氧化烧损具有非常重要的意义。
1)SO2的影响S与Fe生成FeS的比例在氧化铁皮中的含量较低,但S的存在对坯料的加热质量和成品钢材的质量影响最大,含有SO2的氧化铁皮熔点显著降低。当温度高于1150℃时,硫化铁皮为液态化合物,其渗入铁碳组织晶格间,不仅增加铁的烧损而且表面含硫量增加,对钢材机械性能尤其对合金钢危害更大。SO2主要来源于燃料中的H2S,使用低硫燃料对控制坯料加热质量,减少坯料氧化烧损的作用非常明显。
3.5提高操作工的责任
心加强操作工的责任心,及时调整炉温、炉压、空燃比、热负荷分配,防止出现局部过热熔化的现象,防止炉内出现强氧化气氛,可有效防止坯料的氧化。
4结语
坯料在炉内加热出现氧化烧损是不可避免的,但准确控制炉内气氛、准确控制坯料的加热温度、合理缩短坯料在炉时间和加强仪表及热工设备管理等措施,可以有效降低坯料氧化烧损率。具体做法就是在环形加热炉的生产过程中,优化燃烧控制模型、合理控制空燃比、优化加热制度和和工艺参数、实现合理快速加热和提高操作工的责任心等,可以把加热炉目前的烧损率从2.3%降低到1.5%以下,每年可节约钢材约4000t(按50万t/a计算),将创造显著的经济效益。
2氧化铁皮形成影响因素
坯料加热过程产生的氧化铁皮量主要与加热温度、加热时间、炉内气氛以及钢的化学成分有关。式(1)反映了加热温度、加热时间对氧化烧损量的影响。W=at0.5e-bT时间,min;T为温度,K。
- 1、下载文档前请自行甄别文档内容的完整性,平台不提供额外的编辑、内容补充、找答案等附加服务。
- 2、"仅部分预览"的文档,不可在线预览部分如存在完整性等问题,可反馈申请退款(可完整预览的文档不适用该条件!)。
- 3、如文档侵犯您的权益,请联系客服反馈,我们会尽快为您处理(人工客服工作时间:9:00-18:30)。
影响板坯氧化因素分析
刘派(江苏沙钢集团有限公司宏昌钢板厂张家港22
摘要阐述了板坯形成氧化铁皮的原因从加热温度空气过剩系数在炉时间等方面探讨了对板坯氧化的具体
影响和应注意的事项并提出了宏昌钢板厂控制氧化烧损量的一些方法和途径关健词加热炉;板坯;氧化烧损;炉压;空气过剩系数;加热温度;出钢节奏;在
炉时
间
1前言
沙钢集团有限公司宏昌钢板厂是利用引进德国二手设备并进行了必要的升级改造建成的新型现代化工厂自从2005年6月19日该生产线成功生产出第一捆钢卷以来到n月份已经累积生产钢卷近50万吨取得了较好的业绩由于该生产线处于调试试生产阶段加热炉内的板坯氧化较严重使得加热炉内的氧化铁皮积累的较多其中1#加热炉在连续生产近5个月后不得不停炉进行炉内氧化铁皮的清除影响
了
生产的产量另外国内外大型的钢铁联合企业已经采用一些相应的技术措施来提高加热炉的加热效率以便减少板
坯的氧化烧损提高金属收得率提高生产效益获得可观的经济利润
因此研究减少板坯氧化铁皮和烧损已经成为宏昌钢板厂迫在眉睫急需解决的重要问题
2板坯氧化铁皮的形成原因
钢在较高温度的炉内进行加热由于炉气中含有qco:H20等气体钢的表面发生了氧化反应川热轧氧化铁皮的组成主要为eFOeF30;和Fe203等氧化物铁的氧化层通常由内到外按eFoeF3qeF
ZO3
的顺序分布不过加热炉中高温形成的氧化层大部分是eFo只有10%左右为eF3马及eF203z[]连铸板坯在热轧前往往要在1100一1300℃加热和保温在此温度下板坯表面生成1一3mm厚的氧化铁皮[’〕
3影响板坯氧化程度的因
素
许多文献汇’45“〕中都详细的阐明了加热时间炉内气氛加热温度等因素对板坯的氧化程度有很大的影响
31板坯加热时间在板坯达到出炉的目标温度后立即进行轧制降低板坯出炉温度提高轧制速度最大限度地缩短加热时间可减少氧化烧损量[’]我厂10月下旬生产实践表明由于轧制线上产较为正常导致板坯的在炉时间比不生产正常时减少了近1一2个小时板坯的氧化烧损明显降低减少板坯在第一加热段和第二加热段的停留时间
32
空气过剩系数
合理的空气燃料比不但可以提高燃料的燃烧效率减少排烟热损失而且还可以合理控制炉内的氧含
量减
少板坯的氧化烧损提高板坯的成材率空气过剩系数太小会导致燃料的不完全燃烧空气过剩系数太大会导致板坯的氧化情况加剧现场的操作人员可以通过修正空燃比来防止空气过剩而造成过多的热量随烟气排出同时也避免了富氧燃烧减少了燃损提高燃料利用率为轧钢厂节能降耗做出了突出的贡献仁’}33加热温度一150一根据文献川中碳钢氧化烧损量与温度及时间的函数关系一1℃的经验公式=3/e
9
汀
由上述公式我们可以看出随着温度的增加和板坯加热时间的增长板坯的氧化程度将加剧34入炉温
度
板坯的人炉温度对加热炉的生产效率有重要的影响因此提高热装比例不仅能够提高产量而且还可以降低板坯的氧化烧损率所以应该尽量提高
加热炉的热装比加热炉燃耗及板坯氧化烧损随着热装率
及
热装温度逐步提高而下降高温连铸坯的显热得到了较为充分的利用〔“〕
35炉
压
保证加热炉内的炉膛压力为微正压避免吸人大量冷空气川进而减少铁原子与炉内剩余空气中的氧原子的结合机会减少板坯氧化铁皮氧化率过高
总而言之加热温度加热时间炉内气氛及炉压等都是造成板坯氧化烧损过高的主要原因也是解决问题的关键所在
4宏昌钢板厂对板坯氧化皮问题的解决措施
41宏昌钢板厂板坯氧化情况
根据文献甲介绍氧化皮的形成过程是氧和铁两种元素的扩散过程氧由表面向铁的内部扩散而铁则
向外部扩散氧化烧损层的厚度有以下关系:S=a
命g
变化后可得:a=S咫将宏昌钢板厂板坯的相关数据带入其中得
:
a=
000251X3950x075646
a=7skgn1/
2
因此现在沙钢宏昌钢板厂板坯的氧化烧损量计算数值为7skg/
m
“
以2005年10月下旬常用板坯尺寸规格(长X宽X厚)11500火1500X220n飞m板坯的密度为7
8xl000
kgm/3为计算数据我们可以得出一块板坯的氧化烧损量为30165kg其
中一块板坯的氧化烧损率为
10253%这样的烧损率是基于轧制线上生产比较正常时得出的
在沙钢宏昌钢板厂调试初期由于生产经验和操作经验原因造成了板坯经过加热炉加热后板坯的表面氧化铁皮较厚主要是板坯在加热炉内加热的加热时间过长通常为(5一6小时)和加热温度偏高(1350℃)轧机与加热炉的配合不紧密造成轧制节奏不均匀轧制节奏时快时慢所以板坯的氧化烧损比较严重经过现场实际测量所的数据归类统计可得在板坯的在炉时间较长时氧化铁皮较厚坯的在炉时间较
短时氧化铁皮较薄降低板坯出炉温度提高轧制速度最大限度地缩短加热时间可减少氧化烧损量4[]宏昌钢板厂10月下旬生产实践表明由于轧制线上生产较为正常使得板坯的在炉时间比不生产正常时减
少了近1一2个小时板坯的氧化烧损明显降低
42板坯氧化问题的解决措施
由于加热炉炉内温度加热时间及炉内气氛等因素都是造成板坯氧化烧损过高的主要原因所以我们着重从以下方面人手进行解决板坯氧化严重的问题421缩短板坯在炉时间
在板坯达到出炉的目标温度后立即进行轧制保证板坯出路温度的前提下尽量减少板坯在第一加热
段和第二加热段的停留时间当轧制线进行检修时间超过4小时加热炉必须进行清炉保证加热炉内没有板坯使得板坯的在炉时间减少促使板坯的氧化程度最小
422选择适宜的空气过剩系数在一定的炉温制度下板坯的氧化主要是通过氧化性气氛气体与钢铁中的铁原子进行化学反应而形成
氧化铁皮的由于板坯的氧化是通过炉内存在的氧化性气氛进行氧化的所以在保证燃料完全燃烧的前提下选择合理的空气燃料比合理控制炉内的氧含量能够减少板坯的氧化烧损提高板坯的成材率根据现一151
一场烧嘴的实际燃烧情况我们将燃料配比和空气过剩系数做了如下调整:项目预热段第一加热段第二加热段氧气含量测量仪显示范围1样炉空气流量/煤气流量参考值2材炉空气流量/煤气流量参考值420l415425l4151425l415l均热段40l361<5%<5%
保证了燃料完全燃烧降低了烟气中氧气的含量控制了加热炉的炉内气氛降低了氧化性气氛使得测
量的氧含量数值镇5%根据现场观察记录可知这种方式对控制板坯的氧化烧损起到了一定的有效控制
423板坯加热温度由于受到生产线上VZ轧机电机负荷的限制因此加热炉温度制度并没有做较大的调整我们主要是在能够满足轧机轧制的前提条件下尽量采取板坯加热制度中的中下限进行加热424增加板坯入炉温度板坯的人炉温度对加热炉的生产效率有重要的影响因此提高热装比例不仅能够提高产量而且还可以降低板坯的氧化烧损率所以应该尽量提高加热炉的热装
比
韶钢热轧工厂实施连铸坯热送热装方案获得了板坯烧损少和降低能耗的良好效果[“〕沙钢宏昌钢板
厂也实行了热送热装技术实施这一方案缩短了加热时间将原来的加热时间由135分钟减少到
了10
0分钟
左右板坯烧损率也下降到了1%左右同时降低了焦炉煤气的能耗取得了良好的经济效益425适当增加炉压
一般加热炉的炉压设定是微正压以便防止炉门吸风因为沙钢宏昌钢板厂加热炉的炉门长时间在高
温下进行生产炉门发生了严重的变形已经不能够有效的起到隔热的作用加热炉门口有很多的冷风吸人所以我们将正常生产时的炉压由原来的12aP改为18aP降低了冷风的吸入减少了板坯的氧化率实践
证明增加炉压对我厂的板坯氧化的防止起到了积极的作用426执行停札降温制
度
在轧机出现故障时及时采取相应的待轧策略(即停轧降温制度)在沙钢宏昌钢板厂调试初期由于停
轧降温制度停轧降温制度没有很好的得到执行造成了板坯长时间呆在高温环境中使得板坯的氧化程度加重我们执行停轧降温制度后板坯的氧化烧损得到了很好的控制
427手动控制与计算机自动控制相结合
加热炉的自动化是控制是加热炉的发展方向由于实行热工的自动调节可以及时准确地反映和有效地控制炉温炉压等一系列热工参数从而更好地实现所希望的加热制度实现加热的最优化提高加热炉的产量沙钢宏昌钢板厂引进了奥钢联的二级加热控制模型进行加热控制来实现板坯的温度控制与轧制控制相结合但是由于该二级系统的一级控制系统部分中的检测元件部分存在检测不准和执行元件不能够执行
到位等问题因此执行该系统不能够有效的运行目前该厂只能通过工人积累的丰富经验与二级计算机控
制相结合的新型控制方式来对板坯进行加热这种新的控制方式和手段有效的弥补了执行元件的控制反应
较慢的问题通过采用以上这些措施和手段沙钢宏昌钢板厂的板坯氧化情况得到明显的改善(详见趋势图)目前板坯的氧化烧损率已经降到085%接近韩国浦项07%的氧化烧损率
43影响宏昌钢板厂板坯氧化的主
要因
素
通过现场的实践我们发现在炉时间的长短是影响板坯氧化的首要因素详见图1当在生产线非正常
生产在炉时间为5一6小时时氧化烧损约为3%左右而在生产线正常生产时约在炉时间为130分钟左右
板坯的氧化烧损仅为1%左右轧机与加热炉之间的配合也是一个主要原因由于在调试初期生产人员确
定事故处理时间还不是很精确所以造成了板坯在炉时间很长停轧降温制度没有很好的得到落实板坯热装比率的高低也是一个原因板坯热装率高时板坯的氧化较少炉压的控制也是一个重要原因适当的增加炉压将原来的炉压12Pa增加到18aP使得板坯的氧化烧损率减少另外空气过剩系数也是一个重要的影响因素适宜的过剩系数保证了板坯的氧化烧损率较小
152