连铸机典型漏钢的特征及成因分析
漏钢

漏钢是指连铸初期或浇注过程中,铸坯坯壳凝固情况不好或因其他外力作用引起坯壳断裂或破漏使内部钢水流出的现象。
主要类型:1、开浇漏钢原理:由于生产准备不足,出现引锭头密封不严、结晶器角缝超标、中包或浸入式水口烘烤温度不达标,开浇时在塞棒头与水口碗部结冷钢使塞棒控流失败,钢流过小多次开浇或出苗时间控制过短、过长,开浇钢水温度过低、过高等均容易造成开浇漏钢。
特征:开浇起步期间,引锭头刚拉出结晶器就发生漏钢。
2、裂纹漏钢原理:浇铸时,由于初生坯壳在结晶器内产生纵裂、角裂或横裂,出结晶器后,因二次冷却强度不匹配,产生裂纹扩大或由于铸坯在二冷段产生严重的变形,随着钢水静压力的增大坯壳破裂,造成漏钢。
特征:漏钢后在残坯部位可看到明显的裂纹,漏钢部位通常在二冷段。
3、粘结漏钢原理:在结晶器弯月面处,钢水与结晶器铜板直接接触,初生坯壳与结晶器铜板的摩擦力大于坯壳的抗拉强度,导致粘结处被拉裂,钢液从裂口流出,形成新的坯壳,新坯壳再次被拉裂,此过程反复进行,若坯壳到了结晶器下口仍无法焊合裂口,出结晶器下口后坯壳撕裂发生漏钢。
特征:粘结漏钢多为结晶器内坯壳上厚下薄,坯壳的振痕是呈不对称分布,振痕紊乱,结晶器内坯壳呈V字型或倒三角状,粘结点明显。
4、卷渣漏钢原理:由于结晶器保护渣、夹杂物、耐火材料等卷入凝固坯壳局部区域,造成坯壳厚薄不均匀,坯壳出结晶器进格栅之前,由于卷渣部位的坯壳强度较低,不熔于基体的高熔点夹杂物被冲刷,在坯壳上产生漏洞,坯壳失去支撑,在钢水静压力导致漏钢。
特征:漏钢后一般可在残坯漏钢部位看到明显的结渣,漏钢部位一般在结晶器出口与格栅之间。
5、飞边(悬挂)漏钢原理:由于结晶器角缝大或铜板划伤,钢水渗入结晶器角缝,凝固后铸坯边角部产生带毛刺的飞边,造成结晶器内边部拉坯阻力增大,坯壳极易被撕裂,产生漏钢。
特征:漏钢后在残坯部位窄边有带毛刺的飞边,漏点多在边部且有明显的撕裂痕迹,振痕呈角拉斜状,可见飞边悬挂。
各类漏钢所占比例:开浇9.1%,夹渣2.3%,粘结54.%,裂纹22.7%,鼓肚4.6%,水口凝钢2.3%,其他4.5%。
连铸车间65Mn套眼漏钢事故分析.doc

YJ0713-连铸车间65Mn套眼漏钢事故分析案例简要说明:依据国家职业标准和冶金技术专业教学要求,归纳提炼出所包含的知识和技能点,弱化与教学目标无关的内容,使之与课程学习目标、学习内容一致,成为一个承载了教学目标所要求知识和技能的教学案例。
该案例是连续铸钢漏钢事故分析与处理里案例,体现了凝固理论、金属学等知识点和岗位技能,与本专业连续铸钢、炉外精炼课程漏钢事故分析单元的教学目标相对应。
连铸车间65Mn套眼漏钢事故分析1.背景介绍某中型转炉炼钢厂,采用喷吹颗粒镁预脱硫,拥有三座120t的转炉, 采用、LF炉、RH精炼装置,两台不同断面的大型厚板坯连铸机,连铸机采用双排热电偶漏钢预报装置及电磁搅拌技术。
该厂主要生产管线、优碳钢、耐候钢等中厚板。
2.主要内容2.1.事故经过2012年3月4日,连铸车间浇注65Mn钢种,连浇过程发生水口套眼现象,导致被迫更换水口,更换水口过程拉速降至几乎为零,发生了漏钢事故。
2.2.事故原因分析一、精炼套眼原因分析120吨区域自2011年至今共浇铸65Mn钢种5个较次,下面将不同时期精炼进站条件及冶炼状况进行对比,具体内容如下:(一)精炼进出站温度的控制从5个浇次精炼进出站温度变化情况来看,进出站温度控制变化比较大,3月4日进站温度最低,但是出站温度与其他浇次相比并不低,因此温度的变化不是造成本次套眼事故的主要原因。
(二)精炼进出站S含量的变化:从精炼进出站S含量来看,5各浇次精炼进站S含量发生的巨大的变化,2012年3月4日进站钢水S含量急剧上升,与2011年6月4日相比,进站S 上升0.013%,上升比例达86.7%,由于钢种自身液相线温度的限制,直接给精炼脱S造成影响,导致3月4日精炼出站S含量高,脱硫率下降。
(三)精炼冶炼周期的变化3月4日本浇次进站温度最低、精炼S含量最高,从冶炼周期来看,冶炼时间与其他浇次相比最短,严重威胁到精炼软吹时间及夹杂物上浮的效果。
方坯连铸漏钢原因及控制措施

方坯连铸漏钢原因及控制措施随着铸造工艺的不断发展,连铸漏钢也越来越常见。
“漏钢”是指新铸件,尤其是连铸生产的铸件,在凝固过程中发生熔点介质损失,导致铸件质量严重损失的现象。
下面一起来介绍连铸漏钢原因及控制措施:一、连铸漏钢的原因1、擦模失效:擦模上不均匀的加热,擦模表面污染,接触夹头失效,都会导致擦模无法有效传热,从而出现漏钢现象。
2、溶解熔点低:金属的溶解能力不佳,无法对熔点介质起到有效的溶解,导致熔液中的金属析出或运动造成液强度减轻,漏出来。
3、连铸工艺失控:铸流过快,加熔温过高或低,注浆缺陷,铸件内部充满气体等操作失误,都会导致漏钢问题发生。
4、工艺板型失控:熔点介质密度不足或对外形尺寸不精确,以及外形板型尺寸分配不合理,都会导致漏钢。
二、连铸漏钢的控制措施1、精心选择工艺板型:要求板型尺寸分配合理,减轻内外形尺寸缺陷,保证熔点介质密度达到要求。
2、控制凝固温度:熔温要按要求降低,较低时保证金属密度,消除凝固时金属内部气体析出,提高液体凝固强度,从而避免漏钢。
3、控制连铸流条状:速度要求标准稳定,铸流周边无屑物,熔点介质体流均匀,防止凝固过程发生变形,防止熔点差异引起的漏钢。
4、做好擦模的质量检查:对于熔温比较低,可以把擦模上的温度控制在10℃以上,采用精度高的擦模,并定期更换夹头,保证擦模的有效性。
5、控制注浆:注浆量要求恒定,注浆温度要按规定进行维护,保持良好的注浆状态。
总之,要想有效抑制连铸漏钢发生,需要严格按照铸造工艺流程,控制铸流和熔温,擦模要按要求维护,并定期检测,保持传热媒介熔点一致,严格控制工艺板型尺寸,保证良好的注浆状态,体现对材料及加工质量的关注。
只有严格控制好上述各个环节,才能解决连铸漏钢问题,保证铸件质量更好的实现。
板坯连铸机漏钢原因分析及控制措施

板坯连铸机漏钢原因分析及控制措施1.操作不当:操作人员操作不规范或经验不足,如操作时间过长、操作不准确等,容易导致板坯连铸机漏钢。
为了避免操作不当导致漏钢,应加强操作人员培训,提高他们的技术水平和操作经验,严格遵循操作规程,并进行必要的考核和监督。
2.连铸结晶器破损:连铸结晶器是冷却板坯的关键部件,如果结晶器破损,冷却水可能会直接进入铸坯中,导致漏钢。
为了避免这种情况,应定期对结晶器进行检查和维修,及时发现并更换破损的部件。
3.气孔:气孔是指铸坯内部存在的空隙,通常由于钢水中的氢气无法完全逸出而形成。
气孔会影响铸坯的质量,导致漏钢。
为了减少气孔,可以采取以下措施:(1)控制钢水的合金成分,控制钢水中的氢含量。
(2)在铸造过程中加入除氧剂,提高钢水中的溶解氧含量,减少气体生成。
(3)合理设计结晶器,使气泡易于从铸坯中升出。
4.结晶器堵塞:连铸结晶器内部可能会堵塞,导致冷却水无法均匀地冷却铸坯,造成漏钢。
为了避免结晶器堵塞,应定期对结晶器进行清洗和维修,保证结晶器内部的冷却水流通畅。
5.铸坯温度过高:铸坯温度过高会导致铸坯内部产生过多的气体,增加气孔的形成,从而引起漏钢。
为了控制铸坯温度,可以在连铸过程中控制冷却水的流量和温度,以达到合理的冷却效果;同时,在连铸过程中加强温度监控,及时调整连铸速度和冷却水的冷却效果。
6.铸模破损:铸模破损会导致铸坯内部形成孔洞和裂缝,导致漏钢。
为了避免铸模破损,应定期进行铸模的检查和维修,及时更换破损的部件。
7.其他原因:除了以上几点外,板坯连铸机漏钢还可能受到其他因素的影响,如连铸设备的老化、设备维护不当等。
为了确保连铸机的正常运行和减少漏钢,应加强设备的维护保养,定期进行设备的检修和更换关键部件。
综上所述,要控制板坯连铸机漏钢,需要从操作规范、设备维护、冷却控制等多个方面着手,以保证连铸过程的正常进行和铸坯质量的提高。
只有在整个生产过程中严格按照操作规程进行操作,定期维护检修设备,并加强钢水质量控制,才能有效控制和减少板坯连铸机漏钢的发生。
方坯连铸机漏钢原因分析及改进措施
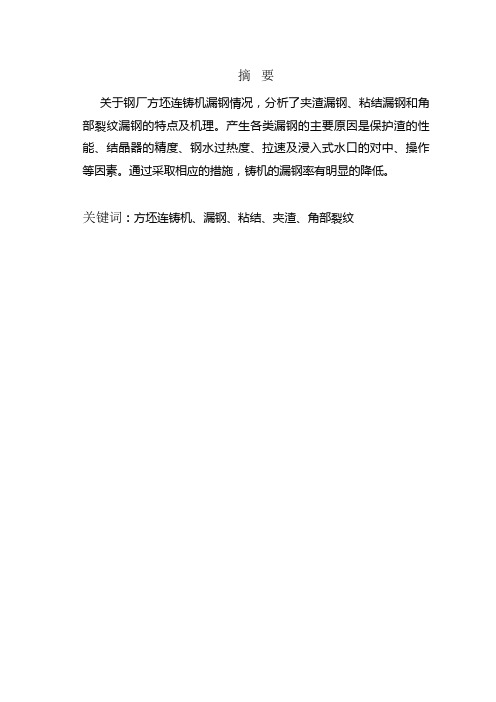
摘要关于钢厂方坯连铸机漏钢情况,分析了夹渣漏钢、粘结漏钢和角部裂纹漏钢的特点及机理。
产生各类漏钢的主要原因是保护渣的性能、结晶器的精度、钢水过热度、拉速及浸入式水口的对中、操作等因素。
通过采取相应的措施,铸机的漏钢率有明显的降低。
关键词:方坯连铸机、漏钢、粘结、夹渣、角部裂纹1概述在连铸生产中,漏钢是危害很大的事故,轻则影响铸坯质量,造成废品,重则影响连铸机作业率,损坏设备,危机操作人员安全。
近年来,随着连铸工艺技术的进步,漏钢事故得到了有效抑制,但仍不能完全避免。
在连铸日趋高效化的今天,要保障生产的顺利进行,提高连铸机作业率,就必须减少和控制漏钢次数。
唐钢漏钢事故较多,漏钢率达到了0.209%,严重影响生产的畅行,对漏钢的成因进行分析,并采取相应措施,从而控制了漏钢事故的发生。
2铸机参数及漏钢情况2.1连铸机的主要工艺参数唐钢二钢轧厂有两台四机四流、三台六机六流方坯连铸机,实际年产能力400万t,浇铸的断四种:150 mmX 150 mnl、165 mmX 165 Innl、165 InnlX225 nlITl、165 mmX280 nnTl,所生产的钢种主要有建筑用钢、低合金钢、硬线钢、轴承钢、焊接用钢等近100个品种。
铸机采用定径水口和塞棒控制两种,浸入式水口加保护渣进行保护浇铸。
2.1.1 漏钢情况对该厂一年全年的漏钢情况分类统计,以夹渣漏钢、粘结漏钢和角部裂纹漏钢为主要漏钢类型,分别占漏钢总数的33.2%、26.5%和22%。
2.1.2夹渣漏钢、粘结漏钢和角部裂纹漏钢的原因分析2.1.3夹渣漏钢特点及机理第二钢轧厂方坯连铸机发生夹渣漏钢主要有以下特点。
1)漏钢处坯壳有一定的弧度,不像裂纹漏钢,有撕裂的感觉。
同时一般在漏钢后结晶器内没有残余坯壳。
2)夹渣漏钢主要是由于坯壳形成时夹带保护渣或大颗粒高熔点杂物导致传热减少,形成薄坯壳而漏钢。
方坯连铸时二次氧化产物、低碳钢冶炼时高粘性渣中不当的脱氧产物、结晶器中铝丝喷加不当造成氧化铝偏高、各种耐材脱落、浇铸过程中结晶器液位波动等,都会促使坯壳夹渣,抑制坯壳生长,造成漏钢。
黑色冶金技术《连铸机漏钢事故分析4》

连铸机漏钢事故分析4一、事故经过丁白班发生漏钢事故。
经分析此次漏钢为粘结漏钢,漏钢发生在外弧侧,此次漏钢更换了结晶器和弯曲段,一段有局部粘钢,在线清理后继续使用。
二次拉钢开浇时间为18:46分,漏钢处理5小时零8分钟。
事故经过为:发生漏钢的炉次为快换中包第一炉,钢种Q235B,铸机等钢水到站大包未测温,中包温度为1542〔℃〕,钢水成分未见异常。
本炉次13:19分大包开浇,13:21分中包开浇。
〔1〕开浇后,待结晶器内钢液面没过坯壳后,试棒,再开流,待液面上升正常后,启动拉矫,拉速升至0.3m/min。
此时主控室通知结晶器外弧第9、8、3个热电偶温度异常,中包工立即停拉矫收流;〔2〕再次启动拉矫后,拉速升至0.3m/min,主控室再次通知结晶器外弧第9个热电偶温度仍异常,中包工打到拉速爬行状态,收流观察坯壳未见异常。
〔3〕主控通知第9个热电偶温度异常消除,中包工开流操作上升液面,拉速由0.3m/min自动升至0.4m/min,开始更换结晶器内的旧保护渣;〔4〕保护渣更换完毕后,缓慢提速至0.6m/min,此时,结晶器北侧的中包工发现内弧露出坯壳〔换包后7分钟,漏钢前10分钟〕,立即停拉矫。
〔5〕停拉矫几秒后,再次启动拉矫,拉速升至0.3m/min,收流观察液面及坯壳未见异常,拉速自动升至0.4 m/min;〔6〕提速至0.5 m/min时,再次收流观察液面及坯壳,无异常,缓慢升速至0.6 m/min时,结晶器南侧的操作工发现外弧露出坯壳,立即打到爬行拉速,收流观察液面及坯壳,无异常后,升速至0.3 m/min,再次收流观察液面及坯壳,无异常后开大流升液面缓慢提速至0.70 m/min时发生漏钢。
漏钢点发生在外弧侧,距换包接头距离为3200mm,踞结晶器液面为800mm,踞结晶器左窄面为900mm,位于热电偶第4、5位置。
漏钢时水口插入深度为140mm,塞棒行程82mm。
漏钢前热电偶有波动,北侧结晶器液面有结壳现象。
中薄板连铸机漏钢的原因分析及其预防措施

中薄板连铸机漏钢的原因分析及其预防措施中薄板连铸机漏钢是指在铁水喷射过程中,由于铁水的喷射量不足或喷射口尺寸、压力不合理等原因,使铁水不能完全覆盖熔池上的碳切削渣片而形成的裂缝,而从这些裂缝中喷出的铁水为漏钢。
漏钢的现象对板材的质量有很大的影响,如果发生漏钢,将会破坏中薄板的性能,从而影响板材的使用价值。
薄板连铸机漏钢的原因主要有以下几点:1、喷射量不足:当铁水在喷射口流出的速度太慢时,将会形成漏钢现象。
2、喷射口尺寸太大:当喷射口的尺寸太大时,由于局部高温和气体的作用,铁水将会被分散,产生空洞,从而形成漏钢现象。
3、喷射压力不合理:当喷射压力过大或过小时,铁水会出现分散,流程不均匀,也会出现漏钢现象。
4、铁水温度不合适:当铁水温度太低时,容易形成渣壁高度偏大,使中薄板无法完全覆盖,从而发生漏钢。
为了预防和消除薄板连铸机漏钢现象,需要采取一些措施:1、检查连铸机的工作状态,确保各机构的正常运转和参数的正确调整,尤其是检查喷射口的尺寸和喷射压力是否合理以及是否有小破损现象。
2、检查熔池的工作状态,确保铁水的温度、流量、浓度和流速等参数处于标准范围内,以保证充分覆盖熔池上的碳切削渣片,以防止漏钢。
3、采用专业的控制装置,实时监测铁水出口,一旦检测到漏钢,就可以及时调整参数或停止喷射,以避免漏钢现象发生,从而提高产品质量。
4、定期检查板材表面,及时发现漏钢现象,及时处理,以防止漏钢扩散,影响板材的整体质量。
综上所述,中薄板连铸机漏钢的原因主要有喷射量不足、喷射口尺寸过大、喷射压力不合理和铁水温度不合适等,为了预防漏钢,应该检查连铸机及熔池工作状态,控制参数,采用相应的控制装置,定期检查板材表面,从而保证中薄板材质量,提高产品的使用价值。
厚板坯连铸机漏钢原因分析及预防措施
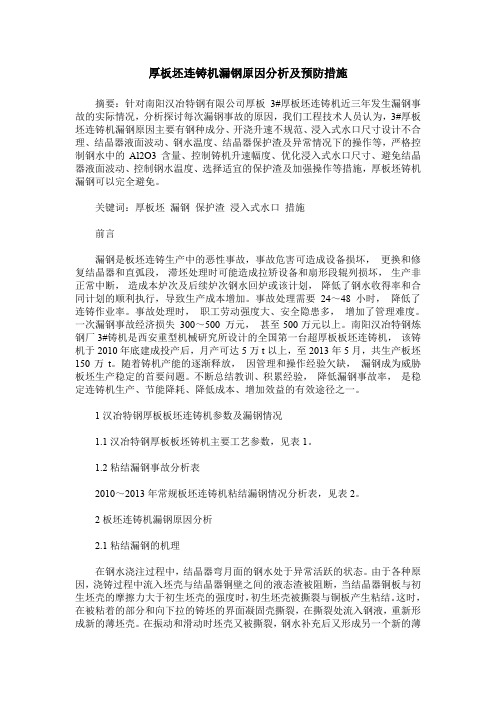
厚板坯连铸机漏钢原因分析及预防措施摘要:针对南阳汉冶特钢有限公司厚板3#厚板坯连铸机近三年发生漏钢事故的实际情况,分析探讨每次漏钢事故的原因,我们工程技术人员认为,3#厚板坯连铸机漏钢原因主要有钢种成分、开浇升速不规范、浸入式水口尺寸设计不合理、结晶器液面波动、钢水温度、结晶器保护渣及异常情况下的操作等,严格控制钢水中的Al2O3含量、控制铸机升速幅度、优化浸入式水口尺寸、避免结晶器液面波动、控制钢水温度、选择适宜的保护渣及加强操作等措施,厚板坯铸机漏钢可以完全避免。
关键词:厚板坯漏钢保护渣浸入式水口措施前言漏钢是板坯连铸生产中的恶性事故,事故危害可造成设备损坏,更换和修复结晶器和直弧段,滞坯处理时可能造成拉矫设备和扇形段辊列损坏,生产非正常中断,造成本炉次及后续炉次钢水回炉或该计划,降低了钢水收得率和合同计划的顺利执行,导致生产成本增加。
事故处理需要24~48小时,降低了连铸作业率。
事故处理时,职工劳动强度大、安全隐患多,增加了管理难度。
一次漏钢事故经济损失300~500 万元,甚至500万元以上。
南阳汉冶特钢炼钢厂3#铸机是西安重型机械研究所设计的全国第一台超厚板板坯连铸机,该铸机于2010年底建成投产后,月产可达5万t以上,至2013年5月,共生产板坯150万t。
随着铸机产能的逐渐释放,因管理和操作经验欠缺,漏钢成为威胁板坯生产稳定的首要问题。
不断总结教训、积累经验,降低漏钢事故率,是稳定连铸机生产、节能降耗、降低成本、增加效益的有效途径之一。
1汉冶特钢厚板板坯连铸机参数及漏钢情况1.1汉冶特钢厚板板坯铸机主要工艺参数,见表1。
1.2粘结漏钢事故分析表2010~2013年常规板坯连铸机粘结漏钢情况分析表,见表2。
2板坯连铸机漏钢原因分析2.1粘结漏钢的机理在钢水浇注过程中,结晶器弯月面的钢水处于异常活跃的状态。
由于各种原因,浇铸过程中流入坯壳与结晶器铜壁之间的液态渣被阻断,当结晶器铜板与初生坯壳的摩擦力大于初生坯壳的强度时,初生坯壳被撕裂与铜板产生粘结。
- 1、下载文档前请自行甄别文档内容的完整性,平台不提供额外的编辑、内容补充、找答案等附加服务。
- 2、"仅部分预览"的文档,不可在线预览部分如存在完整性等问题,可反馈申请退款(可完整预览的文档不适用该条件!)。
- 3、如文档侵犯您的权益,请联系客服反馈,我们会尽快为您处理(人工客服工作时间:9:00-18:30)。
连铸机典型漏钢的特征及成因分析
摘要:连铸机在运行过程中,漏钢问题属于常见问题之一,漏钢问题的出现
将会严重影响到连铸机运行质量,降低工作效率,所以需要通过分析典型漏钢的
特征与出现原因,以此来防止漏钢问题的发生。
本文通过对连铸机的运行进行研究,并结合实际对连铸机漏钢特征、原因提出个人观点,希望为关注连铸机典型
漏钢问题的人群提供参考。
关键词:连铸机;典型漏钢;故障分析
引言:连铸机的主要作用就是对高温钢水进行持续浇筑,为了保证浇筑质量,需要对漏钢问题进行严格控制,通过控制钢水成分、温度等方式可以较少漏钢带
来的危害,进而提高浇筑效果。
因此,有必要对连铸机漏钢特征与原因进行分析。
一、连铸机漏钢类型与原因
高温钢水在结晶器内部发生凝固时,将会出现凝固收缩的情况,此时体积将
会变小。
通常情况下,凝固收缩问题可以分为相变收缩、温降收缩两个不同的阶段,钢水在凝固时会因为各种原因而导致浇筑出的胚壳出现局部脆弱的问题,进
而发生漏钢的情况。
漏钢问题发生时,往往会伴随着非常大的声音,并且在顶弯
区域能够看到钢花喷出[1]。
除此之外,还能够在主控室的钢水液位监控中,发现
液位大幅下滑,漏钢问题出现时,其曲线多会表现出小幅下降转大幅下降或始终
急速下降的趋势。
在钢水浇筑时,漏钢问题非常常见而且很难避免,因为其产生
的原因非常复杂,连铸机较为典型的漏钢问题可以分为以下几种。
(一)粘结型漏钢
粘结型漏钢是极为常见的漏钢问题,一般会在结晶器出口发生。
在连铸机运
行期间,初生坯壳会在结晶器周围生成热点,热点会在拉坯作用下出现破裂,粘
结在结晶器钢板上,在坯壳经过下口气隙区时,如果裂口无法及时焊合,就会导
致漏钢问题的发生。
在发生粘结型漏钢时,坯壳振痕会出现不对称的情况,而且
在多数时间都会在结晶器的内部残留一截坯壳。
粘结型漏钢的出现原因大致可以
分为以下几种。
1.保护渣
当保护渣自身的理化性能无法与钢种、钢水温度等参数匹配时,就有可能出
现粘结型漏钢的问题,因为保护渣的熔化速度、熔点等参数性能都将会影响到连
铸机的浇筑质量。
例如,当保护渣的粘度、熔点高且熔化速度慢时,就会在钢水
拉速慢且温度低时出现热流低的问题,进而产生粘结型漏钢。
在加入保护渣时,
保护渣应该避免出现过薄的问题发生。
除此之外,连铸钢水还会因为脱氧、引流、保护等问题而导致氧化铝夹杂物的含量出现大幅上升,夹杂物混入结晶器时,会
使保护渣碱度、熔点等参数发生改变。
在保护渣含水量大于1%后,结晶器由水分
解而出现的氢,将使保护渣中的二氧化硅还原,进而提高保护渣的整体碱度与熔点,此时也有可能导致粘结型漏钢问题的出现[2]。
2.结晶器液面波动与钢水紊流
在连铸机运行期间,若结晶器液面波动较大,就容易导致保护渣出现下渣质
量问题,因为波动的液面将会导致下渣不均匀,此时便会在坯壳局部位置产生热点,进而导致粘结型漏钢问题的发生。
能够造成液面波动问题的原因有很多,例
如振动器偏振、液面控制系统故障等,此外,若连铸期间存在连铸机的问题,同
样会导致粘结型漏钢的情况出现。
因为在钢水紊流较为严重时,就会出现卷渣问题,钢水对坯壳进行冲击之后,将有可能造成卷渣漏钢、粘结型漏钢问题的发生,所以为了保证连铸质量,就需要对结晶器的液面波动与钢水紊流问题进行合理管控,以此来保证连铸机的运行效果。
3.操作工艺与其他原因
当操作工艺不当时,就有可能连铸期间钢水中的氧化铝夹杂物与氢的含量过高,进而导致保护渣性质发生改变,在钢水拉速出现频繁变化时,也会导致下渣
质量出现问题,进而产生粘结型漏钢。
除此之外,若结晶器钢板划伤过于严重或
漏斗存在严重磨损时,也会影响到连铸质量,并导致漏钢问题的发生。
(二)卷渣漏钢
保护渣卷入、耐材卷入等问题情况出现后,都会导致卷渣漏钢情况的出现。
在坯壳进入格栅之前,因为坯壳丧失了支撑,所以在钢水静压力的作用下,将会
产生漏钢的问题。
在漏钢发生后,通常可以在残坯漏钢位置处发现相对较为明显
的结渣。
通常情况下,卷渣漏钢问题通常会在结晶器出口位置、格栅位置处产生,而漏钢表现出的曲线,则会以液位缓慢下降、或者在小幅下降之后突然大幅下滑
的形式出现。
在SEN设计期间,如果设计不合理,就有可能导致SEN插入过浅、对中不良、穿孔破裂等问题,这些问题都有可能导致保护渣出现卷入漏钢的问题发生,而在
加入保护渣时,如果操作人员的操作方式、捞渣作业不合理,也有可能导致卷渣
问题的出现。
所以为了避免因为保护渣卷入而产生漏钢的情况,就应该针对SEN
设计与操作工艺做出严格规范。
(三)开浇漏钢
1.结晶器准备不足
在正式开始浇筑之前,如果结晶器自身的使用时间相对较长,就有可能导致
变形问题的发生,如果没有针对变形做出修磨处理,就有可能在连铸机启动时因
为启动速度过快、过慢而导致开浇坯壳拉破漏钢,若钢板宽窄面相互之间的缝隙
过大,也会导致开浇时出现毛刺漏钢的情况发生。
若在封引锭期间其丢失块长度
不足、塞纳板长度不足,同样会导致开浇漏钢的问题出现。
此外,丢失快连接较松、引锭杆变形后,也会导致连铸机运行时发生开浇漏钢的情况[3]。
2.工艺操作问题
在连铸机运行时,操作人员的技术水平非常关键,若个人专业能力不足,就
会因为操作问题而导致漏钢情况的发生。
例如在中间包钢水过热度小于20℃时,
如果开浇之后无法快速完成设备启动,就会导致钢水搭桥的问题发生,严重时甚
至还会导致出现坯壳破裂漏钢的情况。
通常情况下,在钢水过热度超出45℃后,
如果在开浇时,拉速达到了应有的速度但是却没有及时对锥度进行调整,就会出现开浇漏钢的情况。
(四)裂纹漏钢
在裂纹漏钢出现之后,铸坯通常可以拉出扇形段,而且裂纹漏钢所产生的坯壳破裂面积往往非常大,所以将会对连铸机的正常运行带来较为严重的影响。
通常情况下,裂纹漏钢是在热应力、机械应力的影响下形成的,当各种应力超出坯壳承受极限时,就会带动坯壳产生破裂的情况,从而出现裂纹漏钢。
1.钢水成分
若钢水内部的碳含量在0.08~0.16%时,浇注期间将会产生包晶反应,此时还会出现跳跃性体积收缩以及相变应力。
如果此时冷却强度过高,就会产生表面裂纹。
而在钢水内部磷含量较高时,将会在富集区出现低强度物质,而且还会在不同应力的影响下出现纵裂问题,进而引发漏钢现象的出现。
当钢水内部硫含量相对较高时,如果在偏析情况下产生了低熔点的硫化亚铁,就会因为热脆而发生漏钢。
当钢水铜含量偏高时,会在晶界析出液态物质,此时便会发生裂纹,而氧含量过高则会影响到保护渣的性能,从而出现表面纵裂。
所以钢水自身的成分问题极为关键,只有强化对于钢水成分的合理管控,才能够降低漏钢问题的发生。
2.钢水温度与二次冷却水
如果钢水自身的过热度不足15℃,则在低拉速的影响下,就会发生钢水搭桥的情况,从而造成坯壳破裂。
如果钢水的过热度大于40℃,还会在高拉速的情况下,出现热流过高的问题,此时坯壳将会在静压力的作用下产生破裂。
扇形段过冷时,热应力将出现大幅上升,并且还有可能导致坯壳产生纵裂漏钢的问题,如果扇形段自身的冷却存在问题,则在死辊、黑石等问题出现时便会产生应力,进而影响到坯壳质量,这种漏钢问题一般会在扇形段的中、下位置出现。
二、结论
总而言之,在连铸机的运行过程中,漏钢属于较为常见的问题,漏钢问题的出现不仅能够影响到浇注质量,还会促使设备的工作运行效率出现大幅下滑,进
而降低经济效益。
相信随着更多人了解到漏钢问题的严重性,连铸机的漏钢问题一定能够得到完美解决。
参考文献:
[1]郭达.小方坯连铸机正角部纵裂漏钢的分析与改进[J].南方金
属,2021(01):45-48.
[2]邢磊.连铸漏钢报警自动降速控制系统的应用与研究[J].电子世
界,2020(12):155-156.
[3]张晓峰.优化连铸工艺操作降低漏钢报警次数[J].冶金与材
料,2020,40(03):77-78.。