方坯连铸漏钢原因及控制措施
大方坯连铸机粘结漏钢的原因分析及控制23

大方坯连铸机粘结漏钢的原因分析及控制摘要:方坯连铸漏钢的类型及原因诸多,影响因素复杂,本文通过某次漏钢后残留的坯壳进行科学的检验及分析确定出了漏钢的类型,结合当时实际工况及技术参数阐述了漏钢的原因及提出应对措施。
关键词:方坯粘结漏钢原因措施1.前言:通常把断面大于220mm×220mm的铸坯称为大方坯,大方坯主要用于轧制硬线、管材、棒材、型材以及轴承钢、齿轮钢等特殊用钢。
大方坯连铸机对比小方坯铸机设备精度更高,投资成本更大,如果生产中发生发生漏钢事故危害极大,不但对设备造成较大损失还会导致停机甚至危害操作人员的安全。
国内冶金工作者对连铸的漏钢原因做了大量的研究及实践,本文主要针对韶钢7号大方坯连铸机某次漏钢进行完整的取样及分析找出了漏钢的类型及原因提出控制措施。
2.主要工艺及装备:韶钢7号连铸机是2013年从达利涅引进的5机5流大方坯连铸机,主要断面为280×280、320×320、320×425,铸机半径14m,冶金长度27m,拥有E-EMS、F-EMS,动态轻压下等技术,结晶器铜管为多锥度弧形,常用拉速0.5-0.9m/min。
3.漏钢原因调查3.1生产过程3.1.1漏钢炉次成份及温度3.1.3保护渣使用情况:所用结晶器保护渣为生产日期为2016年1月23日,2月中旬开始在7号机低碳系列钢使用,3月16日在15CrMoG钢四炉单流统计,渣耗量约0.60 kg/t。
3.1.4结晶器铜管磨损情况:1流铜管使用次数为342炉钢,与目标使用次数800炉相比,炉次较少,从漏钢后的铜管内壁状态反映铜管磨损状况良好。
漏钢后的铜管内壁情况如下图片:3.1.5振动台运行情况:现场调查未发现1流结晶器振动台运行异常的情况。
3.1.6浸入水口插入深度情况:由于漏钢1流浸入水口未能保留,其它流水口插入深度在120-130mm,渣线浸蚀及插入深度正常。
3.2 取样在漏钢后残留坯壳(650mm)上取样,从结晶器液面开始每隔90mm采用锯切方法截取横断面试样,其编号为1-4,试样宽度为90mm,最后做横截面热酸浸。
板坯连铸机漏钢原因分析及控制措施

板坯连铸机漏钢原因分析及控制措施1.操作不当:操作人员操作不规范或经验不足,如操作时间过长、操作不准确等,容易导致板坯连铸机漏钢。
为了避免操作不当导致漏钢,应加强操作人员培训,提高他们的技术水平和操作经验,严格遵循操作规程,并进行必要的考核和监督。
2.连铸结晶器破损:连铸结晶器是冷却板坯的关键部件,如果结晶器破损,冷却水可能会直接进入铸坯中,导致漏钢。
为了避免这种情况,应定期对结晶器进行检查和维修,及时发现并更换破损的部件。
3.气孔:气孔是指铸坯内部存在的空隙,通常由于钢水中的氢气无法完全逸出而形成。
气孔会影响铸坯的质量,导致漏钢。
为了减少气孔,可以采取以下措施:(1)控制钢水的合金成分,控制钢水中的氢含量。
(2)在铸造过程中加入除氧剂,提高钢水中的溶解氧含量,减少气体生成。
(3)合理设计结晶器,使气泡易于从铸坯中升出。
4.结晶器堵塞:连铸结晶器内部可能会堵塞,导致冷却水无法均匀地冷却铸坯,造成漏钢。
为了避免结晶器堵塞,应定期对结晶器进行清洗和维修,保证结晶器内部的冷却水流通畅。
5.铸坯温度过高:铸坯温度过高会导致铸坯内部产生过多的气体,增加气孔的形成,从而引起漏钢。
为了控制铸坯温度,可以在连铸过程中控制冷却水的流量和温度,以达到合理的冷却效果;同时,在连铸过程中加强温度监控,及时调整连铸速度和冷却水的冷却效果。
6.铸模破损:铸模破损会导致铸坯内部形成孔洞和裂缝,导致漏钢。
为了避免铸模破损,应定期进行铸模的检查和维修,及时更换破损的部件。
7.其他原因:除了以上几点外,板坯连铸机漏钢还可能受到其他因素的影响,如连铸设备的老化、设备维护不当等。
为了确保连铸机的正常运行和减少漏钢,应加强设备的维护保养,定期进行设备的检修和更换关键部件。
综上所述,要控制板坯连铸机漏钢,需要从操作规范、设备维护、冷却控制等多个方面着手,以保证连铸过程的正常进行和铸坯质量的提高。
只有在整个生产过程中严格按照操作规程进行操作,定期维护检修设备,并加强钢水质量控制,才能有效控制和减少板坯连铸机漏钢的发生。
7号方坯连铸机角裂漏钢分析与对策
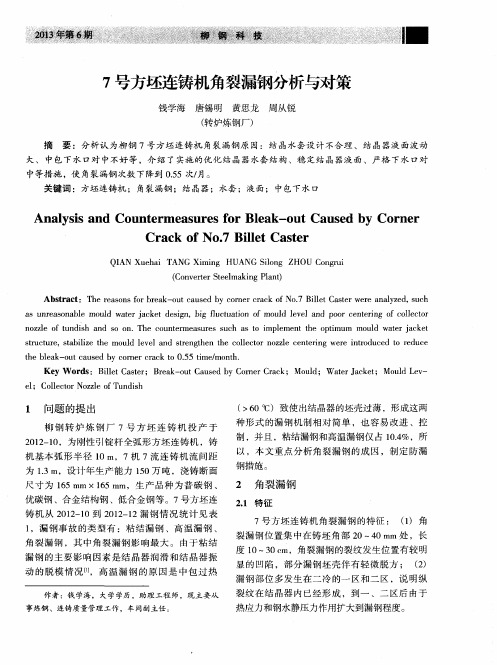
漏 钢 的 主 要 影 响 因素 是 结 晶 器 润 滑 和 结 晶器 振 动 的脱 模 情 况 【 1 1 , 高 温 漏 钢 的 原 因 是 中 包 过 热
Ab s t r a c t :T h e r e a s o n s f o r b r e a k — o u t c a u s e d b y c o r n e r c r a c k o f No . 7 B i l l e t Ca s t e r w e r e a n a l y z e d , s u c h
.
Cr a c k o f No 7 Bi l l e t Ca s t e r
.
Q I A N X u e h a i T A N G X i mi n g HU A N G S i l o n g Z H O U C o n g r u i
( C o n v e r t e r S t e e l ma k i n g P l a n t )
s t r uc t u r e ,s t a b i l i z e t h e mo u l d l e v e l a nd s t r e ng t h e n t h e c o l l e c t o r n o z z l e c e nt e r i n g we r e i n t r o du c e d t o r e d u c e t h e b l e a k —o ut c a us e d b y c o r n e r c r a c k t o 0. 5 5 t i me / mo n t h.
钢措 施 。
2 角裂漏钢
浅析漏钢的原因及预防

浅析漏钢的类型及预防连铸二车间技术组-郭幼永一、前言:板坯漏钢的形式多种多样但重点主要集中在粘结漏钢和开浇起步后的漏钢。
本文简要介绍常见漏钢的类型、漏钢的起因及相应的预防措施。
为各班组在实际浇钢过程中提供参考便于降低漏钢事故的发生。
二、漏钢的类型1、粘结漏钢粘结漏钢是连铸生产过程中的主要漏钢形式,据统计诸多漏钢中粘结漏钢占50%以上。
所谓粘结的引起是由于结晶器液位波动,弯月面的凝固壳与铜板之间没有液渣,严重时发生粘结。
当拉坯时磨擦阻力增大,粘结处被拉断,并向下和两边扩大,形成V型破裂线,到达出结晶器口就发生漏钢。
粘结漏钢的发生有以下情况:内弧宽面漏钢发生率比外弧宽面高(大约3:1);宽面中部附近(约在水口左右300mm)更易发生粘结漏钢;大断面板坯容易发生宽面中部漏钢;而小断面则发生在靠近窄面的区域;铝镇静钢比铝硅镇静钢发生漏钢几率高;保护渣耗量在0.25kg/t钢以下,漏钢几率增加。
2、发生粘结漏钢的原因:1)、形成的渣圈堵塞了液渣进入铜管内壁与坯壳间的通道;2)、结晶器保护渣Al2O3含量高、粘度大、液面结壳等,使渣子流动性差,不易流入坯壳与铜板之间形成润滑渣膜。
3)、异常情况下的高拉速。
如液面波动时的高拉速,钢水温度较低时的高拉速。
4)、结晶器液面波动过大,如浸入式水口堵塞,水口偏流严重,更换钢包时水口凝结等会引起液面波动。
3、防止粘结性漏钢预防措施在浇注过程中防止粘结漏钢的对策有:(1)监视保护渣的使用状况,确保保护渣有良好性能。
如测量结晶器液渣层厚度经常保持在8~15mm,保护渣消耗量不小于0.4kg/t钢,及时捞出渣中的结块等。
(2)提高操作水平,控制液位波动。
(3)确保合适的拉速,拉速变化幅度要小。
升降拉速幅度以0.05m/min为宜。
(4)严格控制钢水质量,提高钢水洁净度,减少钢中夹杂物。
(5)加强对结晶器铜板的检查,发现有龟裂或其他影响铜板平整度的因素,必须进行打磨处理,如果问题严重必须下线。
连铸板坯漏钢的影响因素及防止措施
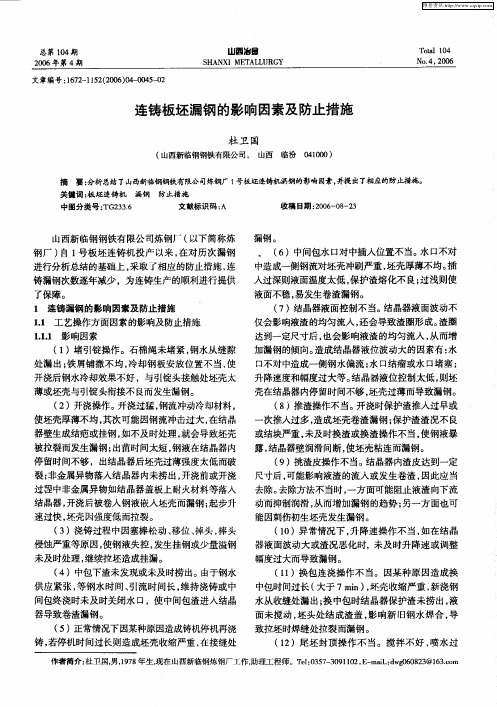
生松动, 缝隙小的—侧则堵不到位 , 造成开浇漏钢。
序进行封堵, 保证石棉绳堵紧并与引锭头端部对齐。 引 () 5 堵引锭后等待时间过长 , 引锭头下滑引起 锭头堵好后冷却铁屑要铺撒均匀 ,厚度在 l m左 石棉绳松动导致漏钢。 5m 右, 燕尾槽内铁屑厚度约 1 i, 0 n冷却钢板交叉放置。 a r 1 . 相应的防止措施 .2 2
文献标识码 : A
收稿 日期 :0 6 0 — 3 20 — 8 2
山西新临钢钢铁有限公司炼钢厂 ( 以下简称炼
漏钢 。
.
钢厂 ) 1 自 号板坯连铸机投产 以来 , 对历次漏钢 在
进行分析总结的基础上 , 采取了相应的防止措施 , 连
( )中间包水 口对中插入位置不当。 口不对 6 水
一
() 2 开浇操作。 开浇过猛 , 钢流冲动冷却材料, 使坯壳厚薄不均 , 其次可能因钢流冲击过大 , 晶 在结
器壁生成结疤或挂钢 , 如不及时处理 , 就会导致坯壳
次推人过多 , 造成坯壳卷渣漏钢 ; 保护渣渣况不良
或结块严重, 未及时换渣或换渣操作不当, 使钢液暴 露, 结晶器壁润滑间断 , 使坯壳粘连而漏钢。 () 9 挑渣皮操作不当。 晶器 内渣皮达到一定 结
口 不对中造成一侧钢水偏流 ; 口结瘤或水 口堵塞 ; 水
处漏 出 ; 铁屑铺撒不均 , 冷却钢板安放位置不当 , 使 开浇后钢水冷却效果不好 ,与引锭头接触处坯壳太 薄或坯壳与引锭头衔接不 良而发生漏钢。
升降速度和幅度过大等。 结晶器液位控制太低 , 则坯
壳在结晶器内停留时间不够 , 坯壳过薄而导致漏钢。 () 8 推渣操作不 当。 开浇时保护渣推人过早或
作者简介: 卫国, , 7 杜 男 1 8年生, 9 现在山西新 临钢炼钢厂工作 , 助理工程师 。Tl0 5 — 0 10 , — i :w 0 0 2 @13cm e:3 7 3 9 2 E ma d g6 8 3 6 . 1 L o
板坯连铸机粘接漏钢的原因与预防措施
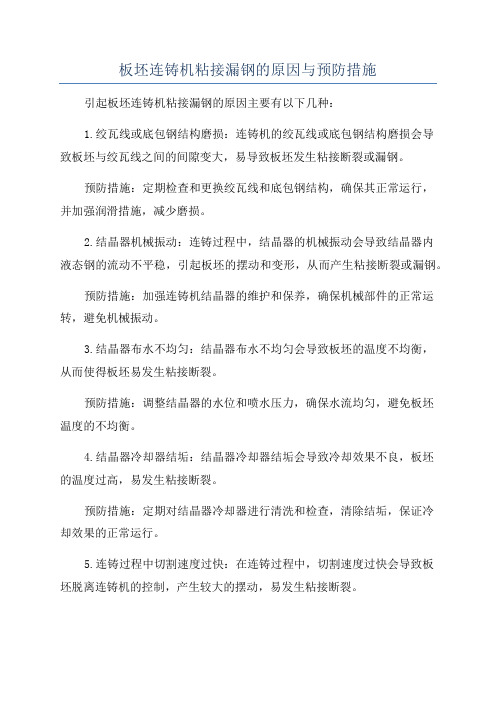
板坯连铸机粘接漏钢的原因与预防措施引起板坯连铸机粘接漏钢的原因主要有以下几种:1.绞瓦线或底包钢结构磨损:连铸机的绞瓦线或底包钢结构磨损会导致板坯与绞瓦线之间的间隙变大,易导致板坯发生粘接断裂或漏钢。
预防措施:定期检查和更换绞瓦线和底包钢结构,确保其正常运行,并加强润滑措施,减少磨损。
2.结晶器机械振动:连铸过程中,结晶器的机械振动会导致结晶器内液态钢的流动不平稳,引起板坯的摆动和变形,从而产生粘接断裂或漏钢。
预防措施:加强连铸机结晶器的维护和保养,确保机械部件的正常运转,避免机械振动。
3.结晶器布水不均匀:结晶器布水不均匀会导致板坯的温度不均衡,从而使得板坯易发生粘接断裂。
预防措施:调整结晶器的水位和喷水压力,确保水流均匀,避免板坯温度的不均衡。
4.结晶器冷却器结垢:结晶器冷却器结垢会导致冷却效果不良,板坯的温度过高,易发生粘接断裂。
预防措施:定期对结晶器冷却器进行清洗和检查,清除结垢,保证冷却效果的正常运行。
5.连铸过程中切割速度过快:在连铸过程中,切割速度过快会导致板坯脱离连铸机的控制,产生较大的摆动,易发生粘接断裂。
预防措施:调整切割速度,使其适应板坯的尺寸和形状,减少切割过程中的摆动。
6.进料辊道制动控制不当:进料辊道制动控制不当会导致板坯的速度不稳定,易产生粘接断裂。
预防措施:加强对进料辊道的制动控制,确保板坯的进料速度平稳,减少速度变化造成的影响。
为了预防板坯连铸机粘接漏钢问题1.定期检查和更换关键部件,确保设备的正常运行。
2.加强润滑措施,减少设备磨损。
3.定期对连铸机进行维护和保养,避免机械振动。
4.调整结晶器的水位和喷水压力,保证水流均匀。
5.定期清洗结晶器冷却器,确保冷却效果的正常运行。
6.调整切割速度,使其适应板坯的尺寸和形状。
7.加强对进料辊道的制动控制,保证板坯的进料速度平稳。
综上所述,板坯连铸机粘接漏钢问题的原因多种多样,但通过采取相应的预防措施,可以有效减少粘接漏钢问题的发生,提高连铸工艺的稳定性和良品率。
连铸小方坯角部纵裂纹及角部纵裂漏钢的成因及防止措施
连铸小方坯角部纵裂纹及角部纵裂漏钢的成因及防止措
施
1.连铸小方坯角部纵裂纹的成因:
①角部罩覆不均匀或罩覆层太厚,使液体钢在连铸过程中受到热应力引起膨胀产生断裂;
②炉内温度分布不均匀;
③小方坯结构极差,钢水温度偏低,造成渣覆盖不均匀;
④小方坯温度过低,且温差大;
⑤冶炼操作不当,料柱受冷凝后,小方坯容易出现纵裂现象;
2.防止措施:
①加强实验室指导料柱的冶炼操作,使小方坯温度和温度分布均匀;
②合理控制罩覆层厚度,使其尽量均匀;
③及时缓和小方坯温度过快下降,尤其是角部;
④检验小方坯投料前后温度梯度,避免温度太大;
⑤增加添加剂,提高液体钢的流动性和结晶性;
⑥检查炉内温度分布是否均匀,及时调整炉内温度控制;
⑦加强铸坯结构的矫正,提高钢水温度及其均匀性,消除结晶缺陷。
防止连铸漏钢的方法是哪些
防止连铸漏钢的方法是哪些连铸漏钢是指在连铸过程中,铸造钢液从铸模内部泄漏出来,导致连铸结晶器和连铸立管等设备的损坏,造成生产事故和经济损失。
为了防止连铸漏钢,需要从多个方面进行控制和防范。
以下是一些常用的方法:1. 提高连铸结晶器的密封性能:连铸结晶器是连铸过程中钢液与外界交界的地方,结晶器的密封性能直接影响着连铸漏钢的发生。
可以采用提高结晶器壁厚度、改善结晶器内壁的光洁度、使用耐磨耐蚀材料等措施,确保结晶器的完好性和密封性。
2. 加强结晶器和连铸立管的保护措施:结晶器和连铸立管常受到高温钢液的冲击和侵蚀,容易出现烧穿和烧蚀现象。
可以通过增加保护层、使用耐磨耐蚀材料、进行定期维修和更换等方式,延长设备的使用寿命,减少漏钢的可能性。
3. 优化浇注系统设计:浇注系统的设计要合理,减少钢液在输送过程中的剧烈振荡和冲击,提高钢液的均质性和稳定性。
可以通过合理设置导流板、增加滑槽等措施,控制钢液的流动,降低可能的漏钢风险。
4. 定期检查和维修设备:定期检查结晶器、连铸立管和其他关键设备的密封性能和机械状况,及时发现并处理可能存在的问题。
设备的维修和更换必要的零部件,保持设备的良好状态,防止因设备破损导致的连铸漏钢。
5. 精确控制铸模内冷却水温度和流量:铸模内的冷却水温度和流量对连铸过程非常重要,直接影响结晶器的温度和工作状态。
必须精确控制冷却水的温度和流量,避免过冷或过热,保持结晶器的稳定性。
6. 严格控制钢水质量:钢水质量对连铸漏钢也有很大影响。
合理控制钢水的温度、含氧量、硫含量等指标,减少钢液的粘度和表面张力,降低漏钢可能性。
7. 加强操作规范和培训:连铸工艺的操作规范对于防止连铸漏钢也至关重要。
必须加强员工的操作培训,确保他们熟练掌握工艺要求和操作方法,增强操作技能,提高操作水平,减少因操作不当导致的事故风险。
8. 安装漏钢检测设备:可以在连铸设备上安装漏钢检测设备,及时监测和探测钢液的泄漏情况。
检测设备包括红外线测温仪、压力传感器、流量计等,可以实时监测钢液的温度、压力和流量变化,及早发现并处理漏钢问题。
方坯连铸机漏钢的成因及对策
Teeh.Adv.Mater.,4(2003),183.
[6] IC Nakajima, H. Hasegawa, S. Khumkoa and M. [14】S.Mukae,K.Nishio,M.Katoh and T.Isayama:Q.J.
Hayashi:ISIJ Int.,46(2006),801.
[9】J.Janis,K.Nakajima,A.Karasev,S.Jonsson,R.Inoue 29.
and P.J?nsson:ISU Int.,53(2013),221.
[17】C.G.Gra nqvist and R.A.Buhrman:J.App1.Phys.,47
[1O]H.Chikama,H.Shibata,T.Emi and M.Suzuki:Mater. (1976),2200.
32B ̄001),629.
[2O】M.Opiela:JAMME,47(2Ol 1)’7. .
[12]J.Janis,K.Nak ̄ima,A.Karasev,H.Shibata and P.G.
· 15 ·
Jpn.Weld.Soc.,3(1985),566.
[7]H.Fujimura,S.Tsuge,Y.Komizo and T.Nishizawa: [15】S.Mamuda and N.Okumura:Tetsu-to-Hagan6,62
Tetsu_t0_Hagan6,87 ̄ooi),707.
Trans.JIM,37(1996),No.4,620.
[1 8】H.Ohta a nd H.Suito:ISU Int.,46(2006),42.
[1 1】K.Nakajima and S.Mizoguchi:MetaU.Mater.Trans.B, [19]A.V.K.ara ̄v and H.Suito:ISIJ Int.,46 (2006),718.
连铸机漏钢的原因及防范措施
连铸机漏钢的原因及防范措施1.机械密封磨损:由于连铸机设备长期高速运转,机械密封件会因为摩擦而磨损,导致钢水从密封部位泄漏出来。
2.设备老化:随着连铸机的使用时间增加,设备可能会出现老化现象,如设备结构松动、焊缝开裂等,从而引发漏钢问题。
3.冷却系统故障:连铸机的冷却系统中通常使用大量的冷却水来保持设备和钢水的温度。
如果冷却系统存在故障,例如水管破裂、阀门关闭不严等,就会导致钢水泄露。
4.操作不当:操作人员的操作技术和操作规程不当可能导致连铸机漏钢。
例如,钢水浇注时没有及时关闭阀门、不按照规定程序进行操作等。
1.定期检查和维护机械密封:定期检查和维护机械密封是防止漏钢的关键。
可以根据生产情况设定维护频率,及时更换磨损的机械密封件,确保设备的正常工作和钢水的密封。
2.防止设备老化:定期检查设备的结构和焊缝,及时发现问题并修复,避免设备老化导致的漏钢。
3.定期维护和检查冷却系统:定期维护和检查冷却系统,确保冷却水管道和阀门的完好和紧密连接。
定期清洗冷却系统,防止积垢和堵塞。
4.提高操作技术和规程:加强操作人员的培训,提高其操作技术水平。
制定和执行严格的操作规程,确保每个环节都按照规程进行操作,避免因操作不当导致的漏钢问题。
5.安装漏钢探测器:安装漏钢探测器来及时检测和报警漏钢,以便能够迅速停机修复,避免漏钢问题扩大。
6.提高设备的自动化程度:通过提高设备的自动化程度,减少人为的操作,从而降低操作失误导致的漏钢风险。
总之,连铸机漏钢的原因多种多样,需要通过定期检查和维护设备,提高操作技术和规程,安装漏钢探测器等方式来加强防范措施,确保连铸机的正常运行和钢水的安全。
- 1、下载文档前请自行甄别文档内容的完整性,平台不提供额外的编辑、内容补充、找答案等附加服务。
- 2、"仅部分预览"的文档,不可在线预览部分如存在完整性等问题,可反馈申请退款(可完整预览的文档不适用该条件!)。
- 3、如文档侵犯您的权益,请联系客服反馈,我们会尽快为您处理(人工客服工作时间:9:00-18:30)。
方坯连铸漏钢原因及控制措施
随着铸造工艺的不断发展,连铸漏钢也越来越常见。
“漏钢”是指新铸件,尤其是连
铸生产的铸件,在凝固过程中发生熔点介质损失,导致铸件质量严重损失的现象。
下面一
起来介绍连铸漏钢原因及控制措施:
一、连铸漏钢的原因
1、擦模失效:擦模上不均匀的加热,擦模表面污染,接触夹头失效,都会导致擦模
无法有效传热,从而出现漏钢现象。
2、溶解熔点低:金属的溶解能力不佳,无法对熔点介质起到有效的溶解,导致熔液
中的金属析出或运动造成液强度减轻,漏出来。
3、连铸工艺失控:铸流过快,加熔温过高或低,注浆缺陷,铸件内部充满气体等操
作失误,都会导致漏钢问题发生。
4、工艺板型失控:熔点介质密度不足或对外形尺寸不精确,以及外形板型尺寸分配
不合理,都会导致漏钢。
二、连铸漏钢的控制措施
1、精心选择工艺板型:要求板型尺寸分配合理,减轻内外形尺寸缺陷,保证熔点介
质密度达到要求。
2、控制凝固温度:熔温要按要求降低,较低时保证金属密度,消除凝固时金属内部
气体析出,提高液体凝固强度,从而避免漏钢。
3、控制连铸流条状:速度要求标准稳定,铸流周边无屑物,熔点介质体流均匀,防
止凝固过程发生变形,防止熔点差异引起的漏钢。
4、做好擦模的质量检查:对于熔温比较低,可以把擦模上的温度控制在10℃以上,
采用精度高的擦模,并定期更换夹头,保证擦模的有效性。
5、控制注浆:注浆量要求恒定,注浆温度要按规定进行维护,保持良好的注浆状态。
总之,要想有效抑制连铸漏钢发生,需要严格按照铸造工艺流程,控制铸流和熔温,
擦模要按要求维护,并定期检测,保持传热媒介熔点一致,严格控制工艺板型尺寸,保证
良好的注浆状态,体现对材料及加工质量的关注。
只有严格控制好上述各个环节,才能解
决连铸漏钢问题,保证铸件质量更好的实现。