BGA
BGA的优点与结构及制造流程

BGA的优点与结构及制造流程BGA(Ball Grid Array)是一种集成电路封装技术,具有以下几个优点:1.高集成度:BGA封装技术可以实现高集成度的电路封装,可以集成更多的功能单元和器件,提高电路板的性能和功能。
2.优良的散热性能:BGA封装的芯片与电路板之间采用多个导热球连接,导热性能优于传统的封装技术,能够更好地散热,提高设备的工作稳定性,延长使用寿命。
3.高密度连接:BGA封装的芯片与电路板之间的连接是通过多个焊点球来实现的,焊点球较小且较密集,可以实现更高的连接密度,更好地满足高速传输和高性能需求。
4.优良的电气性能:BGA封装技术可以提供更短的电连接长度和更低的电阻值,提高电路的电气性能,减少信号传输的干扰和损耗。
BGA封装的结构一般包括芯片、基板和焊点球三个主要部分:1.芯片:芯片是BGA封装的核心部分,芯片通常以裸片的形式放置在基板上,裸片上会有多个引脚用于与基板进行电连接。
2.基板:基板是BGA封装的主要支撑物,其上有多个金属层和层间绝缘层。
基板上不仅布满了与芯片引脚对应的通孔和线路,还有用于与其他器件连接的引脚。
3.焊点球:焊点球是BGA封装的重要组成部分,通常由锡合金制成,焊点球承担起芯片和基板之间的连接和传输电信号的作用。
焊点球分布在基板上与芯片引脚相对应的位置。
BGA封装的制造流程主要包括以下几个步骤:1.基板制备:选择适当的基板,进行表面处理并制造多层金属层和层间绝缘层。
2.焊点球制备:通过真空吸锡等方法,在基板上预先布置焊点球,焊点球的形状和尺寸要与芯片引脚相对应。
3.芯片粘贴:将芯片以封装前的形式粘贴在基板上,保持良好的定位和连接。
4.焊接:将基板与芯片加热至合适温度,使焊点球熔化并与芯片引脚和基板相连接,焊接完成后冷却固化。
5.检测:进行BGA焊接良好性、焊点位置和按压试验等测试,保证焊接质量和稳定性。
6.完成封装:将已焊接和测试完成的芯片和基板封装成整体,以保护芯片和电路结构。
bga焊接流程
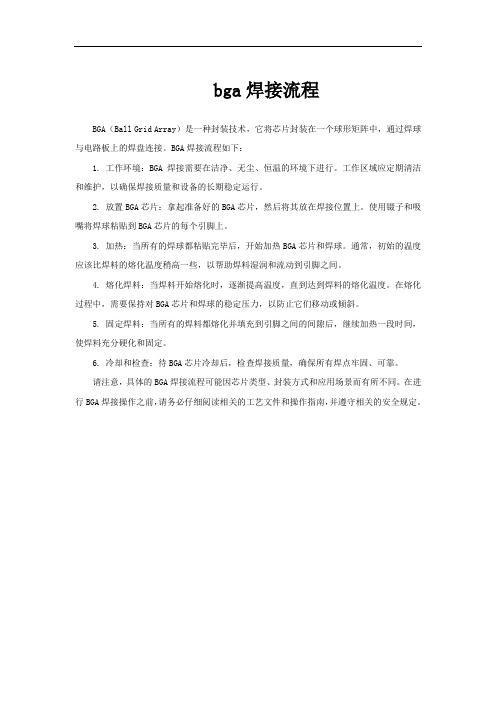
bga焊接流程
BGA(Ball Grid Array)是一种封装技术,它将芯片封装在一个球形矩阵中,通过焊球与电路板上的焊盘连接。
BGA焊接流程如下:
1. 工作环境:BGA焊接需要在洁净、无尘、恒温的环境下进行。
工作区域应定期清洁和维护,以确保焊接质量和设备的长期稳定运行。
2. 放置BGA芯片:拿起准备好的BGA芯片,然后将其放在焊接位置上。
使用镊子和吸嘴将焊球粘贴到BGA芯片的每个引脚上。
3. 加热:当所有的焊球都粘贴完毕后,开始加热BGA芯片和焊球。
通常,初始的温度应该比焊料的熔化温度稍高一些,以帮助焊料湿润和流动到引脚之间。
4. 熔化焊料:当焊料开始熔化时,逐渐提高温度,直到达到焊料的熔化温度。
在熔化过程中,需要保持对BGA芯片和焊球的稳定压力,以防止它们移动或倾斜。
5. 固定焊料:当所有的焊料都熔化并填充到引脚之间的间隙后,继续加热一段时间,使焊料充分硬化和固定。
6. 冷却和检查:待BGA芯片冷却后,检查焊接质量,确保所有焊点牢固、可靠。
请注意,具体的BGA焊接流程可能因芯片类型、封装方式和应用场景而有所不同。
在进行BGA焊接操作之前,请务必仔细阅读相关的工艺文件和操作指南,并遵守相关的安全规定。
BGA封装技术范文
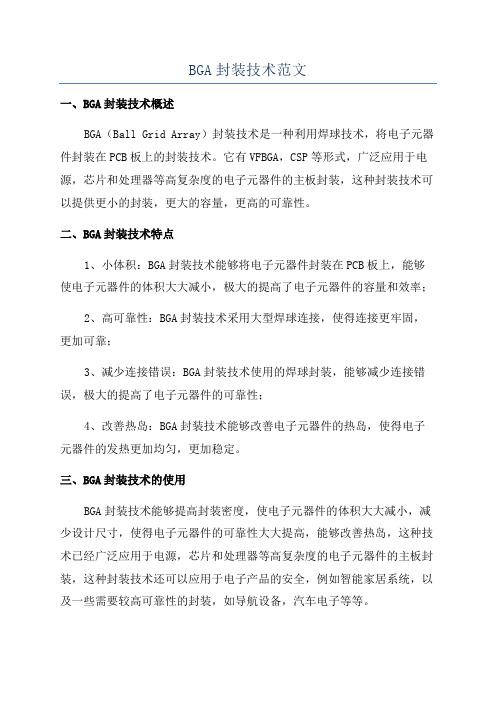
BGA封装技术范文
一、BGA封装技术概述
BGA(Ball Grid Array)封装技术是一种利用焊球技术,将电子元器件封装在PCB板上的封装技术。
它有VFBGA,CSP等形式,广泛应用于电源,芯片和处理器等高复杂度的电子元器件的主板封装,这种封装技术可以提供更小的封装,更大的容量,更高的可靠性。
二、BGA封装技术特点
1、小体积:BGA封装技术能够将电子元器件封装在PCB板上,能够使电子元器件的体积大大减小,极大的提高了电子元器件的容量和效率;
2、高可靠性:BGA封装技术采用大型焊球连接,使得连接更牢固,更加可靠;
3、减少连接错误:BGA封装技术使用的焊球封装,能够减少连接错误,极大的提高了电子元器件的可靠性;
4、改善热岛:BGA封装技术能够改善电子元器件的热岛,使得电子元器件的发热更加均匀,更加稳定。
三、BGA封装技术的使用
BGA封装技术能够提高封装密度,使电子元器件的体积大大减小,减少设计尺寸,使得电子元器件的可靠性大大提高,能够改善热岛,这种技术已经广泛应用于电源,芯片和处理器等高复杂度的电子元器件的主板封装,这种封装技术还可以应用于电子产品的安全,例如智能家居系统,以及一些需要较高可靠性的封装,如导航设备,汽车电子等等。
bga是什么芯片
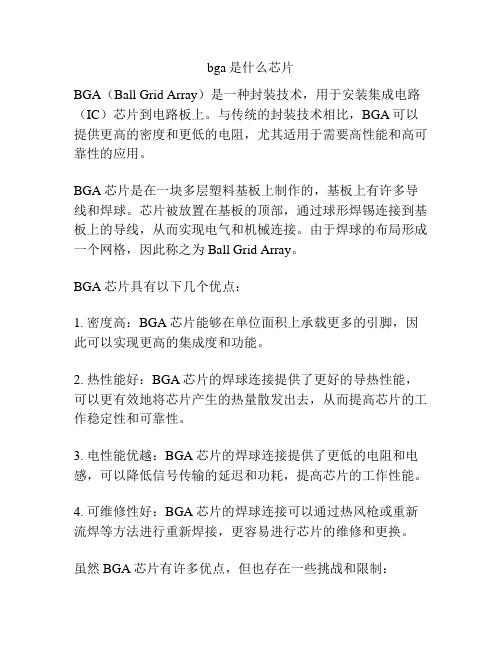
bga是什么芯片BGA(Ball Grid Array)是一种封装技术,用于安装集成电路(IC)芯片到电路板上。
与传统的封装技术相比,BGA可以提供更高的密度和更低的电阻,尤其适用于需要高性能和高可靠性的应用。
BGA芯片是在一块多层塑料基板上制作的,基板上有许多导线和焊球。
芯片被放置在基板的顶部,通过球形焊锡连接到基板上的导线,从而实现电气和机械连接。
由于焊球的布局形成一个网格,因此称之为Ball Grid Array。
BGA芯片具有以下几个优点:1. 密度高:BGA芯片能够在单位面积上承载更多的引脚,因此可以实现更高的集成度和功能。
2. 热性能好:BGA芯片的焊球连接提供了更好的导热性能,可以更有效地将芯片产生的热量散发出去,从而提高芯片的工作稳定性和可靠性。
3. 电性能优越:BGA芯片的焊球连接提供了更低的电阻和电感,可以降低信号传输的延迟和功耗,提高芯片的工作性能。
4. 可维修性好:BGA芯片的焊球连接可以通过热风枪或重新流焊等方法进行重新焊接,更容易进行芯片的维修和更换。
虽然BGA芯片有许多优点,但也存在一些挑战和限制:1. 安装和维修困难:由于BGA芯片的焊球连接在基板上,因此无法直接观察和接触芯片的引脚。
这使得BGA芯片的安装和维修变得更加困难,需要专业的设备和技术。
2. 可靠性问题:由于BGA芯片的焊球连接较小且不可见,因此很难检测焊接质量和可能的焊接缺陷。
不良的焊接质量可能导致芯片失效或故障。
3. 成本和制造复杂度:与传统的封装技术相比,BGA芯片的制造和组装过程更为复杂,需要更多的设备和材料。
这可能导致BGA芯片的制造成本较高。
总的来说,BGA芯片是一种先进的封装技术,可以提供更高的密度、更好的热性能和电性能。
然而,它也面临着安装和维修困难、可靠性问题以及制造复杂度较高的挑战。
随着技术的不断发展,BGA芯片的应用还将继续扩大,同时也需要进一步解决其中的问题和限制。
bga国际认证指导意见
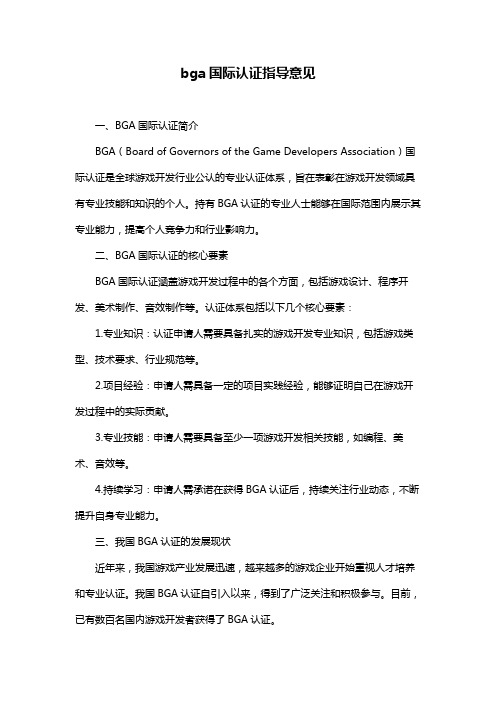
bga国际认证指导意见一、BGA国际认证简介BGA(Board of Governors of the Game Developers Association)国际认证是全球游戏开发行业公认的专业认证体系,旨在表彰在游戏开发领域具有专业技能和知识的个人。
持有BGA认证的专业人士能够在国际范围内展示其专业能力,提高个人竞争力和行业影响力。
二、BGA国际认证的核心要素BGA国际认证涵盖游戏开发过程中的各个方面,包括游戏设计、程序开发、美术制作、音效制作等。
认证体系包括以下几个核心要素:1.专业知识:认证申请人需要具备扎实的游戏开发专业知识,包括游戏类型、技术要求、行业规范等。
2.项目经验:申请人需具备一定的项目实践经验,能够证明自己在游戏开发过程中的实际贡献。
3.专业技能:申请人需要具备至少一项游戏开发相关技能,如编程、美术、音效等。
4.持续学习:申请人需承诺在获得BGA认证后,持续关注行业动态,不断提升自身专业能力。
三、我国BGA认证的发展现状近年来,我国游戏产业发展迅速,越来越多的游戏企业开始重视人才培养和专业认证。
我国BGA认证自引入以来,得到了广泛关注和积极参与。
目前,已有数百名国内游戏开发者获得了BGA认证。
四、我国BGA认证面临的挑战尽管我国BGA认证取得了一定成果,但仍面临一些挑战,如:1.认证体系与国内游戏产业需求的匹配度有待提高。
2.认证过程中,部分企业及开发者对BGA认证的价值认识不足。
3.认证机构与国内游戏产业的互动不足,导致认证质量参差不齐。
五、推动我国BGA认证发展的策略1.加强BGA认证的宣传与推广,提高行业对认证价值的认识。
2.结合我国游戏产业发展需求,优化认证体系,提高认证的针对性。
3.加强与国内外游戏产业相关机构的合作,提高认证质量。
4.鼓励企业将BGA认证纳入人才培养计划,加大认证人才的储备。
六、企业如何应对BGA认证要求1.建立完善的内部培训体系,提升员工的专业技能。
bga检验标准

bga检验标准BGA(Ball Grid Array)是一种常见的电子元件封装形式,广泛应用于PCB电路板上。
为保证BGA元件的质量和可靠性,进行BGA检验是十分重要的环节。
本文将介绍一些常用的BGA检验标准,以确保BGA元件的质量和性能符合要求。
1. 外观检验外观检验是BGA元件检验中的首要步骤。
检查元件表面是否有明显划痕、变形、氧化等问题。
还需注意焊球的规格和分布是否符合标准要求,是否存在过度焊接或未焊接的问题。
外观检验时,可以使用显微镜或放大镜来检查元件表面,确保没有明显的缺陷或损坏。
2. X射线检验X射线检验是一种非破坏性检验方法,用于检查BGA焊接的质量。
通过扫描整个BGA元件,可以观察焊盘与焊球之间的连接情况,检测是否存在焊球偏移、错位、接触不良等问题。
此外,X射线检验还可以检测焊球内部空洞、裂纹以及焊盘上的焊接过剩等问题。
X射线检验可以提高BGA焊接的可靠性和质量。
3. 焊接质量检验焊接质量是评估BGA元件可靠性的关键指标之一。
通过检查焊点的质量,可以预测BGA元件的使用寿命和性能。
常用的焊接质量检验方式包括剪切试验、拉力试验和压力试验。
在剪切试验中,通过施加剪切力来测试焊点的强度。
拉力试验则是通过施加拉伸力来评估焊接质量。
压力试验是通过施加压力,测试焊点是否能够承受力的作用。
以上方法的使用可以确定焊点的质量,并确保其能够在正常使用条件下保持良好的连接。
4. 焊接温度应力检验在进行BGA焊接过程中,焊枪会提供高温加热,从而使得焊盘上的焊料熔化,并与PCB实现连接。
焊接温度和时间会对BGA元件的可靠性产生影响。
因此,进行焊接温度应力检验非常重要。
检验过程中,BGA元件需要暴露在高温环境中一段时间后,再进行外观检查和功能测试,以验证其在高温环境下的稳定性。
焊接温度应力检验是确保BGA焊接质量以及元件可靠性的重要步骤。
5. 功能性测试最后,对焊接后的BGA元件进行功能性测试是非常关键的。
bga封装标准

BGA(Ball Grid Array)封装是一种表面贴装型封装之一。
在印刷基板的背面按陈列方式制作出球形凸点用以代替引脚,在印刷基板的正面装配LSI芯片,然后用模压树脂或灌封方法进行密封。
以下是一些BGA封装的标准:
1. 球形触点陈列:BGA的封装体正面装配了LSI芯片,而背面则按陈列方式制作出球形凸点用以代替引脚。
2. 表面贴装型封装:BGA属于表面贴装型封装之一,引脚可超过200,是多引脚LSI用的一种封装。
3. 封装本体小型化:与QFP(四侧引脚扁平封装)相比,BGA的封装本体可以做得更小。
例如,引脚中心距为1.5mm的360引脚BGA 仅为31mm见方;而引脚中心距为0.5mm的304引脚QFP为40mm见方。
4. 不用担心引脚变形:与QFP相比,BGA不用担心引脚变形的问题。
5. 回流焊后的外观检查:BGA的问题在于回流焊后的外观检查。
此外,BGA封装技术使每平方英寸的存储量有了很大提升,采用BGA 封装技术的内存产品在相同容量下,体积只有TSOP封装的三分之一;另外,与传统TSOP封装方式相比,BGA封装方式有更加快速和有效的散热途径。
以上信息仅供参考,如需了解更多信息,建议咨询专业人士或查阅
相关书籍资料。
bga 结构术语
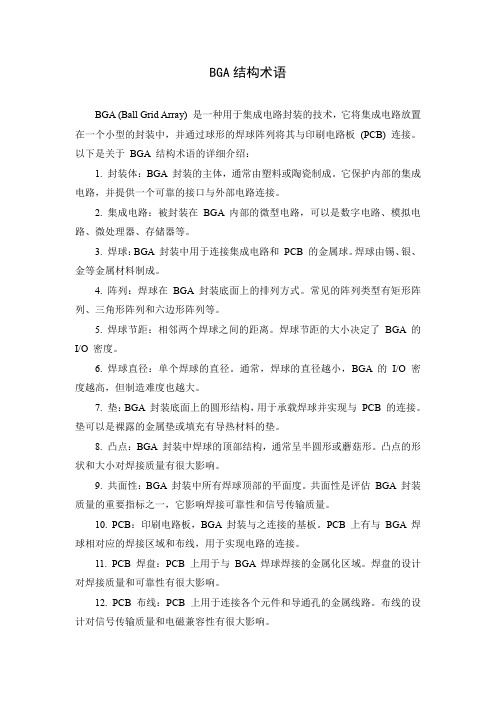
BGA结构术语BGA (Ball Grid Array) 是一种用于集成电路封装的技术,它将集成电路放置在一个小型的封装中,并通过球形的焊球阵列将其与印刷电路板(PCB) 连接。
以下是关于BGA 结构术语的详细介绍:1. 封装体:BGA 封装的主体,通常由塑料或陶瓷制成。
它保护内部的集成电路,并提供一个可靠的接口与外部电路连接。
2. 集成电路:被封装在BGA 内部的微型电路,可以是数字电路、模拟电路、微处理器、存储器等。
3. 焊球:BGA 封装中用于连接集成电路和PCB 的金属球。
焊球由锡、银、金等金属材料制成。
4. 阵列:焊球在BGA 封装底面上的排列方式。
常见的阵列类型有矩形阵列、三角形阵列和六边形阵列等。
5. 焊球节距:相邻两个焊球之间的距离。
焊球节距的大小决定了BGA 的I/O 密度。
6. 焊球直径:单个焊球的直径。
通常,焊球的直径越小,BGA 的I/O 密度越高,但制造难度也越大。
7. 垫:BGA 封装底面上的圆形结构,用于承载焊球并实现与PCB 的连接。
垫可以是裸露的金属垫或填充有导热材料的垫。
8. 凸点:BGA 封装中焊球的顶部结构,通常呈半圆形或蘑菇形。
凸点的形状和大小对焊接质量有很大影响。
9. 共面性:BGA 封装中所有焊球顶部的平面度。
共面性是评估BGA 封装质量的重要指标之一,它影响焊接可靠性和信号传输质量。
10. PCB:印刷电路板,BGA 封装与之连接的基板。
PCB 上有与BGA 焊球相对应的焊接区域和布线,用于实现电路的连接。
11. PCB 焊盘:PCB 上用于与BGA 焊球焊接的金属化区域。
焊盘的设计对焊接质量和可靠性有很大影响。
12. PCB 布线:PCB 上用于连接各个元件和导通孔的金属线路。
布线的设计对信号传输质量和电磁兼容性有很大影响。
13. 热设计:为了确保BGA 封装的可靠运行,需要进行有效的热设计。
这包括选择适当的导热材料、设计合理的散热路径和散热结构等。
- 1、下载文档前请自行甄别文档内容的完整性,平台不提供额外的编辑、内容补充、找答案等附加服务。
- 2、"仅部分预览"的文档,不可在线预览部分如存在完整性等问题,可反馈申请退款(可完整预览的文档不适用该条件!)。
- 3、如文档侵犯您的权益,请联系客服反馈,我们会尽快为您处理(人工客服工作时间:9:00-18:30)。
BGABGA的全称是Ball Grid Array(球栅阵列结构的PCB),它是集成电路采用有机载板的一种封装法。
它具有:①封装面积减少②功能加大,引脚数目增多③PCB 板溶焊时能自我居中,易上锡④可靠性高⑤电性能好,整体成本低等特点。
有BGA的PCB板一般小孔较多,大多数客户BGA下过孔设计为成品孔直径8~12mil,BGA处表面贴到孔的距离以规格为31.5mil为例,一般不小于10.5mil。
BGA下过孔需塞孔,BGA焊盘不允许上油墨,BGA焊盘上不钻孔。
目录BGA拆焊机英文全称为Tiny Ball Grid Array(小型球栅阵列封装),属于是BGA封装技术的一个分支。
是Kingmax公司于1998年8月开发成功的,其芯片面积与封装面积之比不小于1:1.14,可以使内存在体积不变的情况下内存容量提高2~3倍,与TSOP封装产品相比,其具有更小的体积、更好的散热性能和电性能。
编辑本段BGA元件结构与特点PBGA载体为普通的印制板基材,芯片通过金属丝压焊方式连接到载体上表面,塑料模压成形载体表面连接有共晶焊料球阵列。
优点:封装成本相对较低;和QFP相比,不易受到机械损伤;适用大批量的电子组装;字体与PCB基材相同,热膨胀系数几乎相同,焊接时,对函电产生应力很小,对焊点可靠性影响也较少。
缺点:容易吸潮。
CBGA载体为多层陶瓷,芯片与陶瓷载体的连接可以有两种形式:金属丝压焊;倒装芯片技术优点:电性能和热性能优良;既有良好的密封性;和QFP相比,不易受到机械损伤;适用于I/O数大于250的电子组装。
缺点:与PCB相比热膨胀系数不同,封装尺寸大时,导致热循环函电失效。
CCGACCGA是CBGA尺寸大于在32*32mm时的另一种形式,不同之处在于采用焊料柱代替焊料球。
焊料柱采用共晶焊料连接或直接浇注式固定在陶瓷底部。
优缺点与CCGA大体相同,不同在于焊料柱能够承受CTE不同所产生的应力,能够应用在大尺寸封装。
载体采用双金属层带,芯片连接采用倒装技术实现。
优点:可以实现更轻更小封装;适合I/O数可以较多封装;有良好的电性能;适于批量电子组装;焊点可靠性高。
缺点:容易吸潮;封装费用高。
编辑本段BGA的返修及植球工艺简介一:普通SMD的返修普通SMD返修系统的原理:采用热气流聚集到表面组装器件(SMD)的引脚和焊盘上,使焊点融化或使焊膏回流,以完成拆卸和焊接功能。
不同厂家返修系统的相异之处主要在于加热源不同,或热气流方式不同,有的喷嘴使热风在SMD的上方。
从保护器件的角度考虑,应选择气流在PCB四周流动比较好,为防止PCB翘曲还要选择具有对PCB进行预热功能的返修系统。
二:BGA的返修使用HT996进行BGA的返修步骤:1:拆卸BGA把用烙铁将PCB焊盘残留的焊锡清理干净、平整,可采用拆焊编织带和扁铲形烙铁头进行清理,操作时注意不要损坏焊盘和阻焊膜。
用专用清洗剂将助焊剂残留物清洗干净。
2:去潮处理由于PBGA对潮气敏感,因此在组装之前要检查器件是否受潮,对受精密维修系统潮的器件进行去潮处理。
3:印刷焊膏因为表面组装板上已经装有其他元器件,因此必须采用BGA专用小模板,模板厚度与开口尺寸要根据球径和球距确定,印刷完毕后必须检查印刷质量,如不合格,必须将PCB清洗干净并凉干后重新印刷。
对于球距为0.4mm以下的CSP,可以不印焊膏,因此不需要加工返修用的模板,直接在PCB的焊盘上涂刷膏状助焊剂。
需要拆元件的PCB放到焊炉里,按下再流焊键,等机器按设定的程式走完,在温度最高时按下进出键,用真空吸笔取下要拆下的元件,PCB板冷却即可。
4:清洗焊盘用烙铁将PCB焊盘残留的焊锡清理干净、平整,可采用拆焊编制带和扁铲形烙铁头进行清理,操作时注意不要损坏焊盘和阻焊膜。
5:去潮处理由于PBGA对潮气敏感,因此在组装之前要检查器件是否受潮,对受潮的器件进行去潮处理。
6:印刷焊膏因为表面组装板上已经装有其他元器件,因此必须采用BGA专用小模板,模板厚度与开口尺寸要根据球径和球距确定,印刷完毕后必须检查印刷质量,如不合格,必须将PCB清洗干净并凉干后重新印刷。
对于球距为0.4mm以下的CSP,可以不印焊膏,因此不需要加工返修用的模板,直接在PCB的焊盘上涂刷膏状助焊剂。
7:贴装BGA如果是新BGA,必须检查是否受潮,如果已经受潮,应进行去潮处理后再贴装。
拆下的BGA器件一般情况可以重复使用,但必须进行植球处理后才能使用。
贴装BGA器件的步骤如下:A:将印好焊膏的表面组装板放在工作台上B:选择适当的吸嘴,打开真空泵。
将BGA器件吸起来,BGA器件底部与PCB焊盘完全重合后将吸嘴向下移动,把BGA器件贴装到PCB上,然后关闭真空泵。
8:再流焊接设置焊接温度可根据器件的尺寸,PCB的厚度等具体情况设置,BGA的焊接温度与传统SMD相比,要高出15度左右。
9:检验BGA的焊接质量检验需要X光或超声波检查设备,在没有检查设备的的情况下,可通过功能测试判断焊接质量,也可凭经验进行检查。
把焊好的BGA的表面组装板举起来,对光平视BGA四周,观察是否透光、BGA四周与PCB之间的距离是否一致、观察焊膏是否完全融化、焊球的形状是否端正、焊球塌陷程度等。
如果不透光,说明有桥接或焊球之间有焊料球;如果焊球形状不端正,有歪扭现象,说明温度不够,焊接不充分,焊料再流动时没有充分的发挥自定位效应的作用;焊球塌陷程度:塌陷程度与焊接温度、焊膏量、焊盘大小有关。
在焊盘设计合理的情况下,再流焊后BGA底部与PCB之间距离比焊前塌陷1/5-1/3属于正常。
如果焊球塌陷太大,说明温度过高,容易发生桥接。
如果BGA四周与PCB之间的距离是不一致说明四周温度不均匀。
三:BGA植球1:去处BGA底部焊盘上的残留焊锡并清洗用烙铁将PCB焊盘残留的焊锡清理干净、平整,可采用拆焊编织带和扁铲形烙铁头进行清理,操作时注意不要损坏焊盘和阻焊膜。
用专用清洗剂将助焊剂残留物清洗干净。
2:在BGA底部焊盘上印刷助焊剂一般情况采用高沾度的助焊剂,起到粘接和助焊作用,应保证印刷后助焊剂图形清晰、不漫流。
有时也可以采用焊膏代替,采用焊膏时焊膏的金属组分应与焊球的金属组分相匹配。
印刷时采用BGA专用小模板,模板厚度与开口尺寸要根据球径和球距确定,印刷完毕必须检查印刷质量,如不合格,必须清洗后重新印刷。
3:选择焊球选择焊球时要考虑焊球的材料和球径的尺寸。
目前PBGA焊球的焊膏材料一般都是63Sn/37Pb,与目前再流焊使用的材料是一致的,因此必须选择与BGA器件焊球材料一致的焊球。
焊球尺寸的选择也很重要,如果使用高粘度助焊剂,应选择与BGA器件焊球相同直径的焊球;如果使用焊膏,应选择比BGA器件焊球直径小一些的焊球。
4:植球A) 采用植球器法如果有植球器,选择一块与BGA焊盘匹配的模板,模板的开精密贴片焊接系统口尺寸应比焊球直径大0.05--0.1mm,将焊球均匀地撒在模板上,摇晃植球器,把多馀的焊球从模板上滚到植球器的焊球收集槽中,使模板表面恰好每个漏孔中保留一个焊球。
把植球器放置在工作台上,把印好助焊剂或焊膏的BGA器件吸在吸嘴上,按照贴装BGA的方法进行对准,将吸嘴向下移动,把BGA器件贴装到植球器模板表面的焊球上,然后将BGA器件吸起来,借助助焊剂或焊膏的黏性将焊球粘在BGA器件相应的焊盘上。
用镊子夹住BGA器件的外边框,关闭真空泵,将BGA器件的焊球面向上放置在工作台上,检查有无缺少焊球的地方,若有,用镊子补齐。
B) 采用模板法把印好助焊剂或焊膏的BGA器件放置在工作台上,助焊剂或焊膏面向上。
准备一块BGA焊盘匹配的模板,模板的开口尺寸应比焊球直径大0.05~0.1㎜,把模板四周用垫块架高,放置在印好助焊剂或焊膏的BGA器件上方,使模板与BGA之间的距离等于或略小于焊球的直径,在显微镜下对准。
将焊球均匀的撒在模板上,把多馀的焊球用镊子拨(取)下来,使模板表面恰好每个漏孔中保留一个焊球。
移开模板,检查并补齐。
C)手工贴装把印好助焊剂或焊膏的BGA器件放置在工作台上,助焊剂或焊膏面向上。
如同贴片一样用镊子或吸笔将焊球逐个放好。
D)刷适量焊膏法加工模板时,将模板厚度加厚,并略放大模板的开口尺寸,将焊膏直接印刷在BGA的焊盘上。
由于表面张力的作用,再流焊后形成焊料球。
5:再流焊接进行再流焊处理,焊球就固定在BGA器件上了。
6:焊接后完成植球工艺后,应将BGA器件清洗干净,并尽快进行贴装和焊接,以防焊球氧化和器件受潮。
编辑本段BGA器件及其焊点的质量控制随着科学技术的不断发展,现代社会与电子技术息息相关,超小型移动电话、超小型步话机、便携式计算机、存储器、硬盘驱动器、光盘驱动器、高清晰度电视机等都对产品的小型化、轻型化提出了苛刻的要求。
要达到达一目标,就必须在生产工艺、元器件方面着手进行深入研究。
SMT(Surface Mount Technology 表面安装)技术顺应了这一潮流,为实现电子产品的轻、薄、短、小打下了基础。
SMT技术进入90年代以来,走向了成熟的阶段,但随着电子产品向便据式/小型化、网络化和多媒体化方向的迅速发展,对电子组装技术提出了更高的要求,新的高密度组装技术不断涌现,其中BGA(Ball Grid Array 球栅阵列封装)就是一项已经进入实用化阶段的高密度组装技术。
本文试图就BGA器件的组装特点以及焊点的质量控制作一介绍。
1 BGA 技术简介BGA技术的研究始于60年代,最早被美国IBM公司采用,但一直到90年代初,BGA 才真正进入实用化的阶段。
在80年代,人们对电子电路小型化和I/O引线数提出了更高的要求。
虽然SMT使电路组装具有轻、薄、短、小的特点,对于具有高引线数的精细间距器件的引线间距以及引线共平面度也提出了更为严格的要求,但是由于受到加工精度、可生产性、成本和组装工艺的制约,一般认为 QFP(QuadFlat Pack 方型扁平封装)器件间距的极限为0.3mm,这就大大限制了高密度组装的发展。
另外,由于精细间距QFP器件对组装工艺要求严格,使其应用受到了限制,为此美国一些公司就把注意力放在开发和应用比QFP器件更优越的BGA器件上。
精细间距器件的局限性在于细引线易弯曲、质脆而易断,对于引线间的共平面度和贴装精度的要求很高。
BGA技术采用的是一种全新的设计思维方式,它采用将圆型或者柱状点隐藏在封装下面的结构,引线间距大、引线长度短。
这样,BGA就消除了精细间距器件中由于引线问题而引起的共平面度和翘曲的问题。
JEDEC(电子器件工程联合会)(JC-11)的工业部门制定了BGA封装的物理标准,BGA与QFD相比的最大优点是I/O引线间距大,已注册的引线间距有1.0、1.27和1.5mm,而且目前正在推荐由1.27mm 和1.5mm间距的BGA 取代0.4mm-0.5mm的精细间距器件。