注塑结构及工作原理
注塑机的工作原理
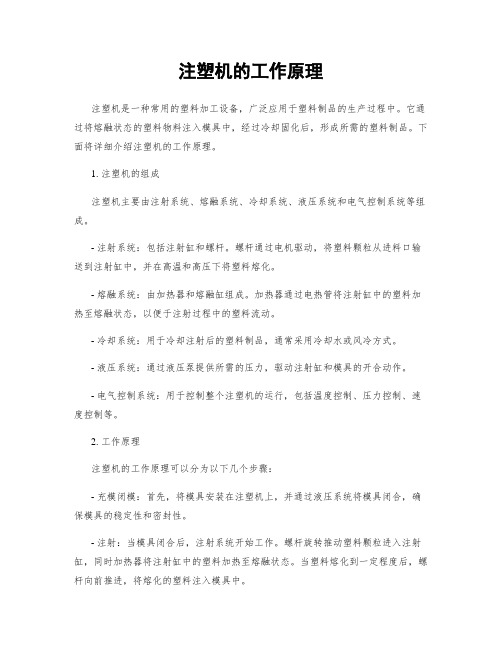
注塑机的工作原理注塑机是一种常用的塑料加工设备,广泛应用于塑料制品的生产过程中。
它通过将熔融状态的塑料物料注入模具中,经过冷却固化后,形成所需的塑料制品。
下面将详细介绍注塑机的工作原理。
1. 注塑机的组成注塑机主要由注射系统、熔融系统、冷却系统、液压系统和电气控制系统等组成。
- 注射系统:包括注射缸和螺杆。
螺杆通过电机驱动,将塑料颗粒从进料口输送到注射缸中,并在高温和高压下将塑料熔化。
- 熔融系统:由加热器和熔融缸组成。
加热器通过电热管将注射缸中的塑料加热至熔融状态,以便于注射过程中的塑料流动。
- 冷却系统:用于冷却注射后的塑料制品,通常采用冷却水或风冷方式。
- 液压系统:通过液压泵提供所需的压力,驱动注射缸和模具的开合动作。
- 电气控制系统:用于控制整个注塑机的运行,包括温度控制、压力控制、速度控制等。
2. 工作原理注塑机的工作原理可以分为以下几个步骤:- 充模闭模:首先,将模具安装在注塑机上,并通过液压系统将模具闭合,确保模具的稳定性和密封性。
- 注射:当模具闭合后,注射系统开始工作。
螺杆旋转推动塑料颗粒进入注射缸,同时加热器将注射缸中的塑料加热至熔融状态。
当塑料熔化到一定程度后,螺杆向前推进,将熔化的塑料注入模具中。
- 压力保持:注射完成后,螺杆停止旋转,但继续向前推进,保持一定的压力,使塑料在模具中充分填充,并确保塑料制品的密度和形状。
- 冷却固化:在一定的注射时间后,注射缸停止加压,开始冷却。
冷却系统通过冷却水或风冷方式,将注射后的塑料制品迅速冷却固化,使其保持所需的形状和结构。
- 开模脱模:当塑料制品完全冷却后,模具打开,将制品取出。
通常使用顶出杆或顶出板的方式将制品从模具中顶出,完成一次注塑过程。
3. 注塑机的应用注塑机广泛应用于塑料制品的生产过程中,如日常生活用品、电子产品外壳、汽车零部件、医疗器械等。
其优势包括生产效率高、成本低、制品精度高等。
总结:注塑机通过将熔融状态的塑料注入模具中,经过冷却固化后,形成所需的塑料制品。
注塑机工作原理及构造

第一章 注塑机工作原理及构造第一节 注塑机工作原理一、注塑机工作原理 注塑成型机简称注塑机,其机械部分主要由注塑部件和合模部件组成。
注塑部件主要由料筒和螺杆及注射油缸组成示意如图1-19所示。
注塑成型是用塑性 的热物理性质,把物料从料斗加入料筒内,料筒外由加热圈加热,使物料熔融。
在料筒内装有在外动力油马达作用下驱动旋转的螺杆。
物料在螺杆的作用下,沿着螺槽向前输送并压实。
物料在外加热和螺杆剪切的双重作用下逐渐的塑化、熔融和均化。
当螺杆旋转时,物料在螺槽摩擦力及剪切力的作用下把已熔融的物料推到螺杆的头部,与此同时,螺杆在物料的反作用力作用下向后退,使螺杆头部形成储料空间,完成塑化过程。
然后,螺杆在注射油缸活塞杆推力的作用下,以高速、高压,将储料室的熔融料通过喷嘴注射到模具的型腔中。
型腔中的容料经过保压、冷却、固化定型后,模具在合模机构的作用下,开启模具,并通过顶出装置把定型好的制件从模具顶出落下。
塑料从固体料经料斗加入到料筒中,经过塑化熔融阶段,直到注射、保压、冷却、启模、顶出制品落下等过程,全是按着严格地自动化工作程序操作的,如图1-20所示。
1-模具 2-喷嘴 3-料筒 4-螺杆 5-加热圈6-料斗 7-油马达 8-注射油缸 9-储料室 10-制件 11-顶杆图1-19 注塑成型原理图注射座动作选择第二节 注塑机组成注塑机根据注塑成型工艺要求是一个机电一体化很强的机种,主要由注塑部件、合模部件、机身、液压系统、加热系统、冷却系统、电气控制系统、加料装置等组成,如图1-21所示。
第二节注 塑 机 结 构注塑机总体结构公司目前主力机型为HTFX 系列,该机型主要可分为注射部分(01注塑机注塑部件塑化装置 注射座 注射油缸 螺杆驱动装置 注射座油缸 螺杆 料筒 螺杆头 喷嘴合模部件合模装置 调模装置 制品顶出装置机身液压系统泵、油马达、阀蓄能器、冷却器、过滤装置 管路、压力表冷却系统 入料口冷却、模具冷却 润滑系统 润滑装置、分配器电器控制系统动作程序控制;料筒温度控制;泵电机控制安全保护;故障监测、报警;显示系统机械手加料装置图1-21 注塑机组成示图部分)、合模部分(02部分)、安全防护门(03部分)、液压传动部分(04部分)、润滑部分(05部分)、电器控制部分(06部分)和机身部分(07部分),括号内为公司内部简称。
注塑机三件套工作原理

注塑机三件套工作原理注塑机三件套是指模板、射出系统和开合模机构这三个部分,它们共同工作以完成塑料制品的注塑加工。
下面我将从多个角度详细解释注塑机三件套的工作原理。
首先,让我们从模板开始。
模板是注塑机的重要部件之一,它由上模板和下模板组成。
在注塑加工过程中,模板的主要作用是固定模具,使其能够承受注塑过程中的压力和温度。
上模板和下模板之间的空间称为模腔,塑料熔融物质在模腔内得以成型。
模板的工作原理是通过开合模机构控制上下模板的运动,使其在注塑过程中能够完成闭合和开启的动作。
其次,射出系统也是注塑机三件套中至关重要的部分。
射出系统主要由螺杆、筒筒和加热系统组成。
在工作时,塑料颗粒被螺杆推进到筒筒内,并在高温和高压下熔化。
一旦达到一定的熔融状态,螺杆会向前推动,将熔融的塑料注入模腔中。
射出系统的工作原理是通过螺杆的旋转和推进,将固态塑料颗粒加热熔化,并在一定的压力下将其注入模腔,完成塑料制品的成型。
最后,开合模机构是注塑机三件套中起到连接和控制模板运动的部分。
开合模机构通过液压系统或机械系统控制上下模板的开合动作,使得模具能够在注塑过程中完成闭合和开启的动作。
开合模机构的工作原理是通过控制液压缸或机械传动装置,使上下模板能够在注塑过程中保持稳定的运动轨迹和速度,确保塑料制品的成型质量。
总的来说,注塑机三件套的工作原理是通过模板、射出系统和开合模机构三个部分的协同作用,完成塑料制品的注塑加工。
模板固定模具、射出系统将塑料熔融物质注入模腔、开合模机构控制模板的运动,三者紧密配合,确保注塑加工过程的顺利进行。
希望这个回答能够全面地解释注塑机三件套的工作原理。
注塑机的工作原理

注塑机的工作原理注塑机是一种常用的塑料加工设备,它通过将熔化的塑料注入模具中,经过冷却和凝固,最终得到所需的塑料制品。
注塑机的工作原理可以分为四个主要步骤:给料、熔化、注射和冷却。
1. 给料给料是注塑机工作的第一步。
在给料阶段,塑料颗粒被输送到注塑机的进料斗中。
通常,给料系统由一个螺杆或者一个活塞驱动的注塑机进料机构组成。
这些机构将塑料颗粒从储料仓中输送到注塑机的熔融室。
2. 熔化熔化是注塑机工作的第二步。
在熔化阶段,塑料颗粒通过加热和压力逐渐熔化成为可注射的熔融塑料。
熔融室通常由一个加热器和一个螺杆组成。
加热器将塑料颗粒加热到熔点以上,使其熔化成为粘稠的熔融塑料。
螺杆则通过旋转将熔融塑料向前推进,同时也起到搅拌和混合的作用。
3. 注射注射是注塑机工作的第三步。
在注射阶段,熔融塑料被注入到模具中,填充模具的腔室。
注射过程由注射缸、注射活塞和注射嘴组成。
注射缸内的熔融塑料被注射活塞推动,通过注射嘴进入模具腔室。
注射速度和压力可以根据产品要求进行调节,以确保注射过程的准确性和稳定性。
4. 冷却冷却是注塑机工作的最后一步。
在冷却阶段,注入到模具中的熔融塑料开始冷却和凝固,最终形成所需的塑料制品。
冷却时间和温度可以根据不同的塑料材料和产品要求进行调节。
通常,模具会通过冷却系统来加速冷却过程,例如通过循环的冷却水或者冷却气体。
总结:注塑机的工作原理可以简单概括为给料、熔化、注射和冷却四个步骤。
在给料阶段,塑料颗粒被输送到注塑机的进料斗中。
在熔化阶段,塑料颗粒通过加热和压力逐渐熔化成为可注射的熔融塑料。
在注射阶段,熔融塑料被注入到模具中,填充模具的腔室。
最后,在冷却阶段,注入到模具中的熔融塑料开始冷却和凝固,最终形成所需的塑料制品。
注塑机的工作原理是实现塑料制品生产的关键,通过掌握和优化这一原理,可以提高生产效率和产品质量。
注塑机工作原理

注塑机工作原理注塑机的动作程序合模→预塑→倒缩→喷嘴前进→注射→保压→喷嘴后退→冷却→开模→顶出→开门→取工件→关门→合模.注塑机操作项目注塑机操作项目包括控制键盘操作、电器控制柜操作和液压系统操作三个方面。
分别进行注射过程动作、加料动作、注射压力、注射速度、顶出形式的选择,料筒各段温度及电流、电压的监控,注射压力和背压压力的调节等。
注射结束、冷却计时器计时完毕后,预塑动作开始.螺杆旋转将塑料熔融料挤送到螺杆头前面。
由于螺杆前端单向阀的作用,熔融塑料积存在机筒的前端,将螺杆向后迫退。
当螺杆退到预定的位置时(此位置由行程开关确定,控制螺杆后退的距离,实现定量加料),预塑停止,螺杆停止转动.紧接着是倒缩动作,倒缩即螺杆做微量的轴向后退,此动作可使聚集在喷嘴处的熔料的压力得以解除,克服由于机筒内外压力的不平衡而引起的“流涎”现象。
若不需要倒缩,则应把倒缩停止,开关调到适当位置,让预塑停止。
开关被压上的同一时刻,倒缩停止开关也被压上。
当螺杆做倒缩动作后退到压上停止开关时,倒缩停止。
接着注座开始后退.当注座后退至压上停止开关时,注座停止后退。
若采用固定加料方式,则应注意调整好行程开关的位置。
一、注塑机的工作原理注塑成型是利用塑料的热物理性质,把物料从料斗加入料筒中,型料筒外由加热圈加热,使物料熔融,在料筒内装有在外动力马达作用下驱动旋转的螺杆,物料在螺杆的作用下,沿着螺槽向前输送并压实,物料在外加热和螺杆剪切的双重作用下逐渐地塑化,熔融和均化,当螺杆旋转时,物料在螺槽摩擦力及剪切力的作用下,把已熔融的物料推到螺杆的头部,与此同时,螺杆在物料的反作用下后退,使螺杆头部形成储料空间,完成塑化过程,然后,螺杆在注射油缸的活塞推力的作用下,以高速、高压,将储料室内的熔融料通过喷嘴注射到模具的型腔中,型腔中的熔料经过保压、冷却、固化定型后,模具在合模机构的作用下,开启模具,并通过顶出装置把并通过顶出装置把定型好的制品从模具顶出落下。
塑料注塑成型工艺(3篇)
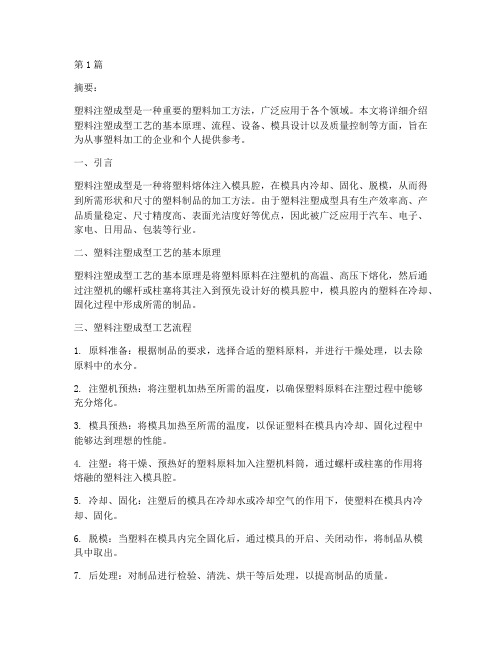
第1篇摘要:塑料注塑成型是一种重要的塑料加工方法,广泛应用于各个领域。
本文将详细介绍塑料注塑成型工艺的基本原理、流程、设备、模具设计以及质量控制等方面,旨在为从事塑料加工的企业和个人提供参考。
一、引言塑料注塑成型是一种将塑料熔体注入模具腔,在模具内冷却、固化、脱模,从而得到所需形状和尺寸的塑料制品的加工方法。
由于塑料注塑成型具有生产效率高、产品质量稳定、尺寸精度高、表面光洁度好等优点,因此被广泛应用于汽车、电子、家电、日用品、包装等行业。
二、塑料注塑成型工艺的基本原理塑料注塑成型工艺的基本原理是将塑料原料在注塑机的高温、高压下熔化,然后通过注塑机的螺杆或柱塞将其注入到预先设计好的模具腔中,模具腔内的塑料在冷却、固化过程中形成所需的制品。
三、塑料注塑成型工艺流程1. 原料准备:根据制品的要求,选择合适的塑料原料,并进行干燥处理,以去除原料中的水分。
2. 注塑机预热:将注塑机加热至所需的温度,以确保塑料原料在注塑过程中能够充分熔化。
3. 模具预热:将模具加热至所需的温度,以保证塑料在模具内冷却、固化过程中能够达到理想的性能。
4. 注塑:将干燥、预热好的塑料原料加入注塑机料筒,通过螺杆或柱塞的作用将熔融的塑料注入模具腔。
5. 冷却、固化:注塑后的模具在冷却水或冷却空气的作用下,使塑料在模具内冷却、固化。
6. 脱模:当塑料在模具内完全固化后,通过模具的开启、关闭动作,将制品从模具中取出。
7. 后处理:对制品进行检验、清洗、烘干等后处理,以提高制品的质量。
四、注塑设备注塑设备是塑料注塑成型工艺的核心,主要包括注塑机、模具、冷却系统、控制系统等。
1. 注塑机:注塑机是注塑成型工艺的关键设备,主要包括料筒、螺杆、液压系统、控制系统等部分。
2. 模具:模具是注塑成型工艺的重要部件,其质量直接影响到制品的形状、尺寸、表面质量等。
3. 冷却系统:冷却系统主要用于控制模具温度,确保塑料在模具内冷却、固化过程中达到理想的性能。
注塑机的工作原理
注塑机的工作原理一、概述注塑机是一种用于制造塑料制品的机械设备,它通过将熔化的塑料注入模具中,经过冷却固化后得到所需的塑料制品。
注塑机工作原理主要包括塑料熔化、注射、冷却和开模等步骤。
二、工作原理1. 塑料熔化首先,将塑料颗粒或粉末放入注塑机的料斗中,通过螺杆传动将塑料送入加热筒中。
加热筒内设置有加热器,通过加热器的加热作用,将塑料加热至熔化温度。
螺杆的旋转将熔化的塑料推送到注射缸中。
2. 注射注射缸内装有活塞,当螺杆将熔化的塑料推送到注射缸时,活塞向前移动,将塑料推入模具中。
注射过程中,注塑机通过控制系统控制注射速度、压力和时间等参数,确保塑料注入模具的质量和精度。
3. 冷却在注塑过程中,模具内的塑料会受到冷却水的冷却。
冷却水通过模具中的冷却通道流过,将热量带走,使塑料迅速冷却固化。
冷却时间根据塑料的种类和厚度等因素进行调节,以确保塑料制品的质量。
4. 开模当塑料冷却固化后,注塑机通过控制系统控制模具的开合动作,将成型的塑料制品从模具中取出。
开模过程中,注塑机通常采用机械、液压或气动方式,根据模具的结构和大小选择合适的开模方式。
三、工作原理的优势1. 生产效率高:注塑机具有高速注射和快速冷却的特点,可以快速制造大批量的塑料制品。
2. 制品精度高:注塑机通过控制系统精确控制注射过程的参数,可以获得高精度的塑料制品。
3. 适用范围广:注塑机可以生产各种形状和尺寸的塑料制品,满足不同行业的需求。
4. 自动化程度高:注塑机的控制系统可以实现自动化操作,提高生产效率和降低人力成本。
四、工作原理的应用领域注塑机的工作原理被广泛应用于各个行业,包括汽车制造、电子电器、日用品、医疗器械等。
例如,汽车制造中的车灯、仪表盘、车身零部件等都可以通过注塑机生产。
电子电器行业中的塑料外壳、插座等也是通过注塑机制造的。
此外,注塑机还可以制造塑料瓶、塑料容器、塑料玩具等日用品。
总结:注塑机的工作原理包括塑料熔化、注射、冷却和开模等步骤。
注塑机工作原理、结构及维护
•
• •
螺杆类型 通用型
加料段(L1) 45~50%
压缩段(L2) 20~30%
均化段(L3) 20~30%
8
8
(一)注塑部件的典型结构
• (2)螺杆头 • 在注射螺杆中,螺杆头的作用是:预塑时,能将塑化好的熔体放流 到储料室中,而在高压注射时,又能有效地封闭螺杆头前部的熔体, 防止倒流。 • 螺杆头分为两大类,带止逆环的和不带止逆环的,对于带止逆环的, 预塑时,螺杆均化段的熔体将止逆环推开,通过与螺杆头形成的间 隙,流入储料室中,注射时,螺杆头部的熔体压力形成推力,将止 逆环退回流道封堵,防止回流。 • 对螺杆头的要求: • 螺杆头要灵活、光洁; • 止逆环与料筒配合间隙要适宜,即要防止熔体回流,又要灵活; • 既有足够的流通截面,又要保证止逆环端面有回程力,使在注射时 快速封闭; • 结构上应拆装方便,便于清洗; • 螺杆头的螺纹与螺杆的螺纹方向相反,防止预塑时螺杆头松脱。
9
9
(一)注塑部件的典型结构
• (3)料筒 • (ⅰ)、料筒的结构 • 料筒是塑化部件的重要零件,内装螺杆外装加热圈,承受复合应力 和热应力的作用,结构如图7:
• 图7 料筒结构 • 1-前料筒;2-电热圈;3-螺孔;4-加料口 • 螺孔3装热电偶,要与热电偶紧密地接触,防止虚浮,否则会影 响温度测量精度。
• • • • • • • • • •
• 工作原理是:预塑时,在塑化部件中的螺杆通过液压马达驱动主轴旋转,主轴一端 与螺杆键连接,另一端与液压马达键连接,螺杆旋转时,物料塑化并将塑化好的熔 料推到料筒前端的储料室中,与此同时,螺杆在物料的反作用下后退,并通过推力 轴承使推力座后退,通过螺母拉动活塞杆直线后退,完成计量,注射时,注射油缸 的杆腔进油通过轴承推动活塞杆完成动作,活塞的杆腔进油推动活塞杆及螺杆完成 注射动作。
注塑机的工作原理
注塑机的工作原理注塑机是一种常见的塑料加工设备,它的工作原理是通过将塑料颗粒加热熔化后注入模具中,经过冷却固化后得到所需的塑料制品。
下面将详细介绍注塑机的工作原理。
1. 注塑机的组成部分注塑机主要由注射系统、熔融系统、冷却系统、液压系统和控制系统等几个主要部分组成。
2. 注射系统注射系统是注塑机的核心部分,它由注射缸、螺杆和喷嘴等组成。
首先,塑料颗粒被放入注射缸中,并通过加热和旋转的螺杆将颗粒加热熔化。
当螺杆向前推进时,熔融的塑料被注射缸内的压力推送到喷嘴。
喷嘴在注塑机的模具中形成一个注射道,将熔融的塑料注入模具中。
3. 熔融系统熔融系统主要由加热器和温控器组成。
加热器通过加热注射缸中的加热带,将塑料颗粒加热到熔融状态。
温控器能够监测和控制注射缸的温度,确保塑料能够达到适宜的熔融状态。
4. 冷却系统冷却系统主要由冷却水管和冷却器组成。
当塑料注入模具中后,冷却水通过冷却器流经模具,将熔融的塑料迅速冷却固化。
冷却系统的效果直接影响到注塑制品的质量和成型周期。
5. 液压系统液压系统主要由液压泵、液压缸和液压阀组成。
液压泵通过压力传递给液压缸,使其产生足够的压力推动注射缸、模具和模板等部件的运动。
液压阀能够控制液压系统的压力和流量,确保注塑机的正常运行。
6. 控制系统控制系统主要由电气控制柜、触摸屏和PLC等组成。
通过控制系统,操作人员可以设置注塑机的工作参数,如温度、压力和注射速度等。
控制系统还可以监测注塑机的运行状态,并进行故障诊断和报警。
总结:注塑机的工作原理主要包括注射系统、熔融系统、冷却系统、液压系统和控制系统等几个主要部分。
注射系统通过将塑料颗粒加热熔化后注入模具中,经过冷却固化后得到所需的塑料制品。
熔融系统负责加热和控制塑料的熔融状态,冷却系统通过冷却水迅速冷却固化塑料,液压系统提供运动所需的压力,控制系统对注塑机的工作参数进行设置和监测。
注塑机的工作原理是塑料加工行业中非常重要的一环,它的高效、精确和稳定的工作状态对于塑料制品的生产具有重要意义。
典型注塑模具结构、工作原理及维护保养
2.按模具功能结构划分为八大部分
1)成型部分:与塑件表面接触,直接成型塑料件的模具零 件,如型芯:成型塑料件内表面的外凸模具零件(大部分 在动模,故称动模型芯)。型腔:成型塑件外表面的内凹 模具零件(大部分在定模,因此称定模型腔,有时动模也 存在有型腔)。
2) 先闭合模具后注塑塑料 。塑料制品材料不同,成型时模具 温度也不同,有的模具需要冷却降温,有的模具则需要加热 升温。 通常模具升温是由高温塑料传导而得,当模温超过所需温度 范围时,则需冷却降温。需要时可在模具中设置加热或冷却 系统。
3) 注塑模生产适应性强,大、小塑件及简单、复杂塑件均可生 产,且生产效率高,容易实现自动化。
第三章 典型注塑模具结构、工作原理及维护保 养
塑料模具分类:
注塑模 压注模 压缩模 挤出模 气动成形模 发泡成型模 空气辅助成型模
大型、复杂、精密、 超级镜面模具
注塑 模具 高度 3米 重量 20顿
世界上最大的注塑模具,重量160吨,注塑 机重量超过2000吨。
3.1 注塑模组成和特点
1. 注塑模按组成分类(或分型面分)
1.浇注系统的组成和分类
如图a)、b)所示的侧浇口、点浇口应用实例。
2.浇注系统的设计原则
1)保证塑件外观质量 浇口在塑件表面会留下痕迹,影响表面质量,因此浇口应
设置在塑件隐蔽部位,且浇口容易切除、痕迹不明显。 2)避免熔料直接冲击细小型芯、嵌件或薄壁等薄弱环节,防 止模具型芯和其他成型零件的变形。 3)排气良好。
4)流程要短 5)尽可能采用平衡式布置使收缩均匀,尺寸精度高,塑件有
- 1、下载文档前请自行甄别文档内容的完整性,平台不提供额外的编辑、内容补充、找答案等附加服务。
- 2、"仅部分预览"的文档,不可在线预览部分如存在完整性等问题,可反馈申请退款(可完整预览的文档不适用该条件!)。
- 3、如文档侵犯您的权益,请联系客服反馈,我们会尽快为您处理(人工客服工作时间:9:00-18:30)。
(一) 注塑机结构分析及其工作原理 0…… 一、注塑机的工作原理
注塑成型机简称注塑机。 注塑成型是利用塑料的热物理性质,把物料从料斗加入料筒中,料筒外由加热圈加热,使物料熔融,在料筒内装有在外动力马达作用下驱动旋转的螺杆,物料在螺杆的作用下,沿着螺槽向前输送并压实,物料在外加热和螺杆剪切的双重作用下逐渐地塑化,熔融和均化,当螺杆旋转时,物料在螺槽摩擦力及剪切力的作用下,把已熔融的物料推到螺杆的头部,与此同时,螺杆在物料的反作用下后退,使螺杆头部形成储料空间,完成塑化过程,然后,螺杆在注射油缸的活塞推力的作用下,以高速、高压,将储料室内的熔融料通过喷嘴注射到模具的型腔中,型腔中的熔料经过保压、冷却、固化定型后,模具在合模机构的作用下,开启模具,并通过顶出装置把定型好的制品从模具顶出落下。 注塑机作业循环流程如图1所示。
图1 注塑机工作程序框图 二、注塑机的分类
按合模部件与注射部件配置的型式有卧式、立式、角式三种 (1)卧式注塑机:卧式注塑机是最常用的类型。其特点是注射总成的中心线与合模总成的中心线同心或一致,并平行于安装地面。它的优点是重心低、工作平稳、模具安装、操作及维修均较方便,模具开档大,占用空间高度小;但占地面积大,大、中、小型机均有广泛应用。 (2)立式注塑机:其特点是合模装置与注射装置的轴线呈一线排列而且与地面垂直。具有占地面积小,模具装拆方便,嵌件安装容易,自料斗落入物料能较均匀地进行塑化,易实现自动化及多台机自动线管理等优点。缺点是顶出制品不易自动脱落,常需人工或其它方法取出,不易实现全自动化操作和大型制品注射;机身高,加料、维修不便。 (3)角式注塑机:注射装置和合模装置的轴线互成垂直排列。根据注射总成中心线与安装基面的相对位置有卧立式、立卧式、平卧式之分:①卧立式,注射总成线与基面平行,而合模总成中心线与基面垂直;②立卧式,注射总成中心线与基面垂直,而合模总成中心线与基面平行。角式注射机的优点是兼备有卧式与立式注射机的优点,特别适用于开设侧浇口非对称几何形状制品的模具。
闭模 注射座前进 注射 保压 冷却 启模 制品顶出
退回塑化 塑化退回 固定塑化 三、注塑机的组成结构分析 注塑机根据注射成型工艺要求是一个机电一体化很强的机种,主要由注射部件、合模部件、机身、液压系统、加热系统、控制系统、加料装置等组成。如图2所示。
图2 注塑机组成示意图 (一)注塑部件的典型结构
1.注射部件的组成 目前,常见的注塑装置有单缸形式和双缸形式。因不同的厂家、不同型号的机台其组成也不完全相同,下面就对常用的机台作具体分析。 立式机和卧式机注塑装置的组成图分别如图3和图4。 工作原理是:预塑时,在塑化部件中的螺杆通过液压马达驱动主轴旋转,主轴一端与螺杆键连接,另一端与液压马达键连接,螺杆旋转时,物料塑化并将塑化好的熔料推到料筒前端的储料室中,与此同时,螺杆在物料的反作用下后退,并通过推力轴承使推力座后退,通过螺母拉动活塞杆直线后退,完成计量,注射时,注射油缸的杆腔进油通过轴承推动活塞
注塑机 注射部塑化部螺杆 料筒 螺杆喷嘴 注射座 注射油缸 座移油缸 液压马达
合模部合模装置 调模装置 顶出装置 机
身 液压系泵、液压马达、
蓄能器、冷却器、管路等油加热系
冷却系
控制系统 动作程控
料筒温度控制 液压泵电机控故障检测报警控安全保护
加料装置 杆完成动作,活塞的杆腔进油推动活塞杆及螺杆完成注射动作。 图3 卧式机双缸注射注塑装置示意图 (a)是俯视图; (b)为注射座与导杆支座间的平视图 1-油压马达;2,6 -导杆支座;3-导杆;4-注射油缸;5-加料口; 7-推力座;8-注射座;9-塑化部件;10-座移油缸
角式注塑机的注射部件与卧式机注塑机一样。 图4 立式注塑机注射装置示意图 1- 液压马达;2-推力座;3-注射油缸;4-注射座;5-加料口;6-座移油缸;7-塑化部件;8-上范本
2.塑化部件 塑化部件有柱塞式和螺杆式两种,下面就对螺杆式做一下介绍。 螺杆式塑化部件如图5所示,主要由螺杆、料筒、喷嘴等组成,塑料在旋转螺杆的连续推进过程中,实现物理状态的变化,最后呈熔融状态而被注入模腔。因此,塑化部件是完成均匀塑化,实现定量注射的核心部件。
图5 螺杆式塑化部件结构图 1-喷嘴;2-螺杆头;3-止逆环;4-料筒;5-螺杆;6-加热圈;7-冷却水圈
螺杆式塑化部件的工作原理:预塑时,螺杆旋转,将从料口落入螺槽中的物料连续地向前推进,加热圈通过料筒壁把热量传递给螺槽中的物料,固体物料在外加热和螺杆旋转剪切双重作用下,并经过螺杆各功能段的热历程,达到塑化和熔融,熔料推开止逆环,经过螺杆头的周围通道流入螺杆的前端,并产生背压,推动螺杆后移完成熔料的计量,在注射时,螺杆起柱塞的作用,在油缸作用下,迅速前移,将储料室中的熔体通过喷嘴注入模具。 螺杆式塑化部件一般具有如下特点: ① 螺杆具有塑化和注射两种功能; ② 螺杆在塑化时,仅作预塑用; ③ 塑料在塑化过程中,所经过的热历程要比挤出长; ④ 螺杆在塑化和注射时,均要发生轴向位移,同时螺杆又处于时转时停的间歇式工作状态,因此形成了螺杆塑化过程的非稳定性。
(1) 螺杆 螺杆是塑化部件中的关键部件,和塑料直接接触,塑料通过螺槽的有效长度,经过很长的热历程,要经过3态(玻璃态、黏弹态、黏流态)的转变,螺杆各功能段的长度、几何形状、几何参数将直接影响塑料的输送效率和塑化质量,将最终影响注射成型周期和制品质量。 与挤出螺杆相比,注塑螺杆具有以下特点: ① 注射螺杆的长径比和压缩比比较小; ② 注射螺杆均化段的螺槽较深; ③ 注射螺杆的加料段较长,而均化段较短; ④ 注射螺杆的头部结构,具有特殊形式。 ⑤ 注射螺杆工作时,塑化能力和熔体温度将随螺杆的轴向位移而改变。
(ⅰ)、螺杆的分类 注塑螺杆按其对塑料的适应性,可分为通用螺杆和特殊螺杆,通用螺杆又称常规螺杆,可加工大部分具有低、中黏度的热塑性塑料,结晶型和非结晶型的民用塑料和工程塑料,是螺杆最基本的形式,与其相应的还有特殊螺杆,是用来加工用普通螺杆难以加工的塑料;按螺杆结构及其几何形状特征,可分为常规螺杆和新型螺杆,常规螺杆又称为三段式螺杆,是螺杆的基本形式,新型螺杆形式则有很多种,如分离型螺杆、分流型螺杆、波状螺杆、无计量段螺杆等。 常规螺杆其螺纹有效长度通常分为加料段(输送段)、压缩段(塑化段)、计量段(均化段),根据塑料性质不同,可分为渐变型、突变型和通用型螺杆。 ① 渐变型螺杆:压缩段较长,塑化时能量转换缓和,多用于PVC等热稳定性差的塑料。 ② 突变型螺杆:压缩段较短,塑化时能量转换较剧烈,多用于聚烯烃、PA等结晶型塑料。 ③ 通用型螺杆:适应性比较强的通用型螺杆,可适应多种塑料的加工,避免更换螺杆频繁,有利于提高生产效率。 常规螺杆名段的长度如下: 螺杆类型 加料段(L1) 压缩段(L2) 均化段(L3) 渐变型 25~30% 50% 15~20% 突变型 65~70% 15~5% 20~25% 通用型 45~50% 20~30% 20~30% (ⅱ)、螺杆的基本参数 螺杆的基本结构如图6所示,主要由有效螺纹长度L和尾部的连接部分组成。 图6 螺杆的基本结构 ds — 螺杆外径,螺杆直径直接影响塑化能力的大小,也就直接影响到理论注射容积的大小,因此,理论注射容积大的注塑机其螺杆直径也大。 L/ds — 螺杆长径比。L是螺杆螺纹部分的有效长度,螺杆长径比越大,说明螺纹长度越长,直接影响到物料在螺杆中的热历程,影响吸收能量的能力,而能量来源有两部分:一部分是料筒外部加热圈传给的,另一部分是螺杆转动时产生的摩擦热和剪切热,由外部机械能转化的,因此,L/ds直接影响到物料的熔化效果和熔体质量,但是如果L/ds太大,则传递扭矩加大,能量消耗增加。 L1—加料段长度。加料段又称输送段或进料段,为提高输送能力,螺槽表面一定要光洁,L1的长度应保证物料有足够的输送长度,因为过短的L1会导致物料过早的熔融,从而难以保证稳定压力的输送条件,也就难以保证螺杆以后各段的塑化质量和塑化能力。塑料在其自身重力作用下从料斗中滑进螺槽,螺杆旋转时,在料筒与螺槽组成的各推力面摩擦力的作用下,物料被压缩成密集的固体塞螺母,沿着螺纹方向做相对运动,在此段,塑料为固体状态,即玻璃态。 h1— 加料段的螺槽深度。h1深,则容纳物料多,提高了供料量和塑化能力,但会影响物料塑化效果及螺杆根部的剪切强度,一般h1≈(0.12~0.16)ds。 L3 — 熔融段长度。熔融段又称均化段或计量段,熔体在L3段的螺槽中得到进一步的均化,温度均匀,组分均匀,形成较好的熔体质量,L3长度有助于熔体在螺槽中的波动,有稳定压力的作用,使物料以均匀的料量从螺杆头部挤出,所以又称计量段。L3短时,有助于提高螺杆的塑化能力,一般L3=(4~5)ds。 h3 — 熔融段螺槽深度,h3小,螺槽浅,提高了塑料熔体的塑化效果,有利于熔体的均化,但h3过小会导致剪切速率过高,以及剪切热过大,引起分子链的降解,影响熔体质量,;反之,如果h3过大,由于预塑时,螺杆背压产生的回流作用增强,会降低塑化能力。 L2 — 塑化段(压缩段)螺纹长度。物料在此锥形空间内不断地受到压缩、剪切和混炼作用,物料从L2段入点开始,熔池不断地加大,到出点处熔池已占满全螺槽,物料完成从玻璃态经过黏弹态向黏流态的转变,即此段,塑料是处于颗粒与熔融体的共存状态。L2的长度会影响物料从玻璃态到黏流态的转化历程,太短会来不及转化,固料堵在L2段的末端形成很高的压力、扭矩或轴向力;太长则会增加螺杆的扭矩和不必要的消耗,一般L2=(6~8)ds。对于结晶型的塑料,物料熔点明显,熔融范围窄,L2可短些,一般为(3~4)ds,对于