焊装夹具调试及验收技术要求
夹具预验收标准

试制车间焊装夹具预验收标准1.共性问题验收1.1 工艺文件验收1.1.1 工艺装备设计图纸1.1.2 所有工位工程图1.1.3 焊装作业指导书1.1.4 工艺装备清单1.1.5 工艺装备自检报告1.1.6 桁架系统的3D数据及图纸1.1.7 吊具与工位器具3D数据集图纸以上内容在验收前需检查落实1.2 夹具外观标准1.2.1 外观质量1.2.1.1 夹具外观颜色与要求一致,定位块、夹紧块需发黑处理1.2.1.2 夹具油漆喷涂均匀、美观、无锈蚀或油漆脱落1.2.2 夹具铭牌1.2.2.1 夹具铭牌为铜质板材,铆接固定方式,固定牢靠1.2.2.2 铭牌编号清晰,铭牌号与夹具名称一致1.2.3 气动管路1.2.3.1 进气管颜色为蓝色,出气管颜色为黑色,控制为红色,并采用双层阻燃气管1.2.3.2 管路布置要美观有序,且布置在BASE板的槽钢内1.2.4 叉车标识线1.2.4.1 较大夹具应有叉车标识线,标识线颜色合适1.2.5 推手和脚轮1.2.5.1 推手高度在800—900mm左右,符合人机工程学,管径合适,质量牢靠1.2.5.2 推手可折叠,不影响焊接工作1.2.5.3 脚轮要运动灵活,一端定向,一端万向,万向轮与推手在同侧,脚轮有自锁装置1.2.6 夹具焊缝质量1.2.6.1夹具与工位器具焊脚高度在3~5mm1.2.6.2所有焊缝不允许出现虚焊、脱焊,重要部位须采用连续焊缝1.2.6.3焊后清理焊渣,焊缝打磨平滑1.3 夹具精度1.3.1 三坐标检验1.3.1.1对部分夹具进行三坐标抽检1.3.2 BASE板1.3.2.1 BASE及连接板等结构件要求采用Q235-A板材和型材焊接而成。
1.3.2.2 BASE板面长度在1m以下时,板面厚度不低于20mm,型材采用14号槽钢;长度在1m~1.5m时要求面板厚度在25 mm以上,型材采用14号槽钢;BASE板面长度超过1.5m时,要求面板厚度在30mm以上,型材采用20号以上槽钢1.3.2.3 BASE应为一整体,其上平面为安装基准面,安装基准面上还应刻坐标网格线;坐标网格线的深度 0.3~0.4 mm,线距为100~200mm,坐标网格线的平行度误差:相邻单一间隔距0.10/100mm;累积间隔距0.30/全长。
焊装夹具技术要求

焊装夹具技术要求一、焊装夹具方案规划要求:1. 为了保证在产品加工过程中基准的统一,乙方在做夹具仕样书过程中需按照提供的RPS基准系统来确定夹具主定位基准(改造项目需延用原有基准,并保证统一),定位孔及销的圆菱性必须与RPS一致,定位面可在RPS同一基准面上进行适当调整(50mm以内),且必须保证前后工序定位基准统一。
夹具定位点需在RPS定位点的基础上进行适当增加,并保证钣件充分定位。
定位基准若乙方有其它方案的,会签时提出与RPS的差异清单,经书面同意后方可实施。
2. 夹具定位方案设计时,需充分考虑件的强度与定位精度,必要时可将RPS中的菱形定位销改为圆形以及可根据夹具的定位要求适当增加定位面,以保证件的精确、稳定定位。
3. 夹具定位方案设计时,需充分考虑夹具的作业性、结构设计的合理性,对提供的工艺文件中要求的夹具结构、工序的划分可根据实际情况提出合理建议,经书面同意后可进行适当的修改。
如乙方未提出异意的,乙方必须保证所设计、制造出来夹具的作业性、定位性完全满足生产要求。
4. 夹具定位方案设计时,需充分考虑每套夹具上钣件的防错措施,需充分有效的防止左右件、类似件装错;一个件不同方位的装反等情况的发生。
二、夹具材质及热处理要求1.夹具底座BASE要求采用Q235 A板材和槽钢或方钢焊接而成,槽钢或方钢规格要求如下:BASE底板的焊缝采用非连续焊缝,焊后经热处理退火消除应力(不允许采用机械消除应力)并喷砂处理,对于以上要求必须提供充分证明或在加工时将随时进行现场确认。
2.规制块(基准块、压块)必须采用45#钢,并经淬火处理,硬度值为(HRC30~35),表面应进行发黑处理。
3.支撑座采用焊接结构(或者采用铸钢件),不采用铸铁支撑座,支撑座板料厚应应≥15mm,焊后应作退火处理(铸钢件除外),消除应力;焊缝要求牢固、光滑平整、无缺陷;一般高度为150、200、250、300、350,能充分满足互换性要求。
夹具验收报告

夹具验收报告焊接夹具验收技术要求一、焊接夹具制造完成后,由乙方提出申请,甲方派出技术人员到乙方的现场进行焊接夹具预验收。
二、乙方必须提供以下记录,甲方才能进行预验收工作1、焊接夹具零部件质量检验记录:1)焊接工装外观质量检验。
1)尺寸精度检验。
2)焊接夹具材料及热处理检验。
3)表面粗糙度检验。
2、焊接夹具装配检验记录。
3、焊接夹具动态检验记录。
4、经过清点的焊接夹具清单。
5、焊接夹具与其对应的夹具仕样书的吻合情况自检清单。
乙方根据上述记录整理成焊接夹具自检报告提供给甲方。
三、焊接夹具的预验收1、预验收依据:1)乙方提供并由甲方确认的验收标准。
2)产品数模。
3)焊接夹具技术要求。
4)焊接夹具验收技术要求。
2、预验收程序:1)焊接夹具动、静检验见后附表。
2)焊接夹具动、静检验合格后,在乙方场地进行试焊接,利用合格的冲压件,焊接成一台总成,如符检验精度标准,则视为焊接夹具预验收合格。
四、对焊接夹具预验收过程中存在的问题及应采取的措施,乙方必须记录并形成文件,且经双方签字确认。
若没有形成文件,甲方视为夹具没有经过本次的预验收。
五、包装运输1、焊接夹具在乙方工厂预验收合格后包装发运,包装箱内附包装清单一份。
同时发运焊接夹具设计图纸资料。
2、焊接夹具应进行防水、防锈处理,焊接夹具应装箱,以防止在运输过程中磕碰。
六:焊接夹具在甲方验收时,乙方必须派出技术人员和调整工人到甲方现场进行调试,甲方技术人员配合,在甲方的验收为焊接夹具的最终验收。
七:乙方调试焊接夹具的时间不能影响合同总体进度。
八、焊接夹具的终验收1、终验收的前提是焊接夹具符合《XXX技术要求》。
2、乙方在甲方场地进行焊接夹具的安装、调试并进行焊接。
3、乙方提供了完整的、符合要求的焊接夹具技术资料。
4、能连续稳定地生产出20台合格的总成,则焊接夹具终验收合格。
九、本附件与合同具有同等法律效力。
十、本附件未尽事宜,双方通过协商解决。
甲方代表签字:乙方代表签字:年月日年月日附表:焊接夹具动、静态检查表附件九XXX设计图纸会签确认书NO:01注:图纸确认依据焊接生产线技术要求及验收技术要求焊接夹具及检具自检报告NO:022、此项目报告由乙方在预验收前全部提供。
焊装夹具类生产技术要求-2023标准
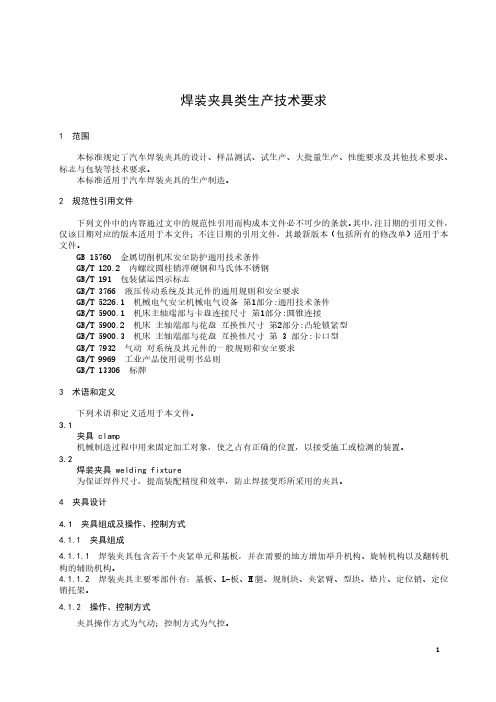
焊装夹具类生产技术要求1范围本标准规定了汽车焊装夹具的设计、样品测试、试生产、大批量生产、性能要求及其他技术要求、标志与包装等技术要求。
本标准适用于汽车焊装夹具的生产制造。
2规范性引用文件下列文件中的内容通过文中的规范性引用而构成本文件必不可少的条款。
其中,注日期的引用文件,仅该日期对应的版本适用于本文件;不注日期的引用文件,其最新版本(包括所有的修改单)适用于本文件。
GB15760金属切削机床安全防护通用技术条件GB/T120.2内螺纹圆柱销淬硬钢和马氏体不锈钢GB/T191包装储运图示标志GB/T3766液压传动系统及其元件的通用规则和安全要求GB/T5226.1机械电气安全机械电气设备第1部分:通用技术条件GB/T5900.1机床主轴端部与卡盘连接尺寸第1部分:圆锥连接GB/T5900.2机床主轴端部与花盘互换性尺寸第2部分:凸轮锁紧型GB/T5900.3机床主轴端部与花盘互换性尺寸第3部分:卡口型GB/T7932气动对系统及其元件的一般规则和安全要求GB/T9969工业产品使用说明书总则GB/T13306标牌3术语和定义下列术语和定义适用于本文件。
夹具clamp机械制造过程中用来固定加工对象,使之占有正确的位置,以接受施工或检测的装置。
焊装夹具welding fixture为保证焊件尺寸,提高装配精度和效率,防止焊接变形所采用的夹具。
4夹具设计夹具组成及操作、控制方式4.1.1夹具组成4.1.1.1焊装夹具包含若干个夹紧单元和基板,并在需要的地方增加举升机构、旋转机构以及翻转机构的辅助机构。
4.1.1.2焊装夹具主要零部件有:基板、L-板、H腿、规制块、夹紧臂、型块、垫片、定位销、定位销托架。
4.1.2操作、控制方式夹具操作方式为气动;控制方式为气控。
数据建模4.2.1夹具在设计前应开展实地测绘,获取实车数据,并建立数据模型。
4.2.2夹具应根据白车身建模实际结果,结合开孔位置及用户需求,精准定位以确定白车身开孔位置,从而得出定位点的支撑点及限位点等数据。
焊接工装夹具使用及管理规定
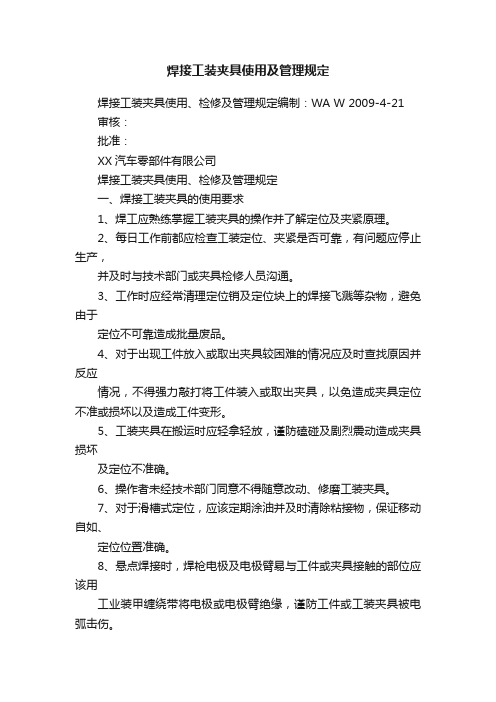
焊接工装夹具使用及管理规定焊接工装夹具使用、检修及管理规定编制:WA W 2009-4-21审核:批准:XX汽车零部件有限公司焊接工装夹具使用、检修及管理规定一、焊接工装夹具的使用要求1、焊工应熟练掌握工装夹具的操作并了解定位及夹紧原理。
2、每日工作前都应检查工装定位、夹紧是否可靠,有问题应停止生产,并及时与技术部门或夹具检修人员沟通。
3、工作时应经常清理定位销及定位块上的焊接飞溅等杂物,避免由于定位不可靠造成批量废品。
4、对于出现工件放入或取出夹具较困难的情况应及时查找原因并反应情况,不得强力敲打将工件装入或取出夹具,以免造成夹具定位不准或损坏以及造成工件变形。
5、工装夹具在搬运时应轻拿轻放,谨防磕碰及剧烈震动造成夹具损坏及定位不准确。
6、操作者未经技术部门同意不得随意改动、修磨工装夹具。
7、对于滑槽式定位,应该定期涂油并及时清除粘接物,保证移动自如、定位位置准确。
8、悬点焊接时,焊枪电极及电极臂易与工件或夹具接触的部位应该用工业装甲缠绕带将电极或电极臂绝缘,谨防工件或工装夹具被电弧击伤。
9、修改或调整过的焊接工装夹具,必须经过首件检验合格才能批量生产,不能盲目焊接。
共3页,第1页10、每日工作后应清理工装夹具上的脏物,保持工装清洁。
11、工装夹具上应禁止溅上水及其它液体,以防工装锈蚀。
12、气保焊焊接时不得随意在工装夹具上引弧。
13、气动夹具应保证压力表读数调整在规定范围,气动三联件应定期放水及注油,经常检查管路是否漏气。
二、焊接工装夹具的检修1、所有悬点及气保焊工装夹具均应每半年检修一次,并填写检修记录。
2、操作者应陪同检修人员一同完成检修工作。
3、检修内容包括如下:1)定位销是否牢固以及是否弯曲变形,定位销磨损量是否过大,一般定位销与工件孔直径不大于0.25mm。
2)定位块是否牢固,定位面磨损是否过大,一般不大于0.3mm。
3)压钳能否可靠压紧,压头磨损是否严重,如果压头面积太小易将工件压出凹坑则必须修磨或更换。
焊装夹具调试及验收技术要求精编版
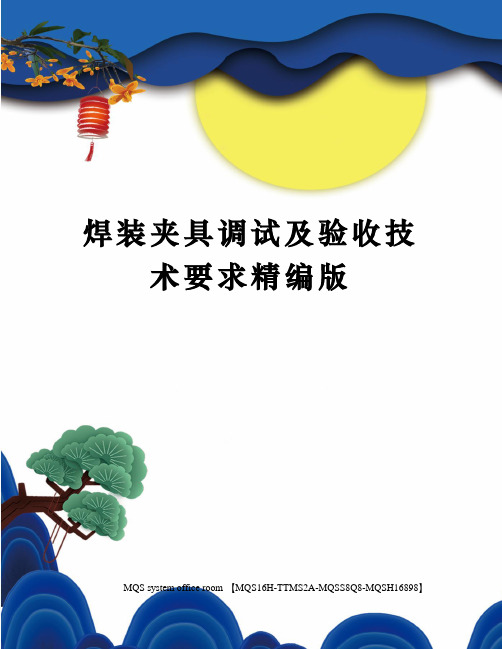
焊装夹具调试及验收技术要求精编版MQS system office room 【MQS16H-TTMS2A-MQSS8Q8-MQSH16898】+8AT项目焊装夹具招标要求项目名称:+8AT项目夹具新增/改造重庆力帆乘用车有限公司目录+8AT项目焊装夹具招标要求1.简述该项目承担重庆力帆乘用车有限公司(甲方)+8AT项目夹具新增/改造(详见附件一清单,但不限于清单内容)。
乙方对以上工程负全面责任,以满足工艺、安全、可靠等方面要求。
本项目为“交钥匙”工程。
双方共同确认技术方案、工艺装备要求、供货范围及施工工程等,乙方须在该方案基础上进行完善并满足纲领和焊车需求;若后续发生工艺变更,双方协商解决或交付商务处理。
本招标要求书主要针对该设备技术要求、功能描述、责任范围等进行明确,作为甲、乙双方履行合同的技术依据。
2.生产线设计及建设基本条件电源:电压380V±10%、220V±10%、频率50Hz±2%;冷却水压力:;设备正常工作;压缩空气压力:;设备正常工作;焊装生产线使用寿命为8年或总产量50万台。
3.生产线信息生产节拍:288秒/台;生产纲领:5万/年;251天。
生产班次:双班;设备开动率:85%。
项目夹具新增/改造管理要求乙方负责+8AT焊装SE分析(输出:时序图、焊接流程图,MCP/MCS,焊点分析及优化,焊接通过性分析,搭接性分析,焊接避让,干涉性审查等)、文件输出、工艺方案及布局图的详细设计,并反应出乙方的工艺规划及流程的合理性及可行性。
项目总计划时间大纲要求30日前制定《项目计划》及项目组织架构图发送甲方确认,《项目计划》需体现甲方在该项目的管理流程中。
⑴焊接总成的组成件;⑵装入件名称、数量、零部件号;⑶装件顺序;⑷定位点、辅助定位、支撑点、压紧点的坐标位置;⑸定位及压紧形式;⑹操作高度700mm~800mm;⑺焊接形式(是电阻焊还是二氧化碳焊);⑻所用设备的规格、型号及数量;⑼前后工序,定位基准应统一;⑽所装件的名称及件数;未特殊说明部分按照行业通用规则进行提供。
夹具、检具技术要求
焊接夹具、焊接检具技术要求一、夹具的设计与制造要求1、焊接夹具上各种定位、夹紧、翻转及回转等动作采用手动。
焊接夹具定位面及定位销均独立可调整。
2、夹具应有完善的装配定位基准,便于夹具制造、装配、检测、调试和维修。
3、夹具设计应充分考虑操作方便和安全可靠、维护修理方便,应保证焊接装卸方便,使焊接件处于最佳焊接位置,并应防止机构压手和松开打手。
4、夹具设计在保证工艺要求和刚性的情况下结构应简单合理,降低制造成本。
5、夹具结构设计时,应充分考虑保证夹具具有足够的强度和刚度。
6、夹具的工作环境条件:(1)室温:-50℃~42℃(2)湿度:80%(3)电源:三相380V;单相220V;频率50HZ(4)汽源:0.5Mpa(5)水压:0.25 Mpa7、夹具的定位装置和夹紧装置应便于操作,同时不应使焊接作业处于不恰当的姿态8、手动夹紧装置都应可靠、压紧状态时,制件不能松动,不能产生相互偏移,制件不能有被压的痕迹或变形,在动作时不能伤害操作人员的身体。
9、旋转和运动机构应确保灵活、轻便、稳定。
10、制件在夹具内装配过程的定位,其相对位置应确保稳定性、可靠性。
11、应充分考虑易磨损件的拆换方便,以利于夹具修理。
12、应保证制件在夹具内能以最有利的顺序组焊,并保证焊接时防止制件的变形,包括热影响造成的变形。
13、尽量能以一次安装装配一定的制件以及回转数达到最少,同时便于取出焊接好的制件。
14、定位装置和夹紧装置以及支承板型面的配置应考虑所装配制件由于自重而引起的变形。
15、如有可能发生变形的部位,快速夹必须要装置上或下支承面。
16、夹具内压紧机构的动力开关或手柄应尽量配置在夹具的边侧,受力方向也应尽量以从下到上、从右到左的习惯性原则。
17、夹具零件与工件接触面、定位销承受装卸频繁、转动频繁的部位应采用淬火钢或渗碳钢。
18、夹具结构的零部件要求标准化、规格化、统一化。
19、夹具作业高度(工作面)要求距地0.8~0.85M范围内。
焊装夹具技术要求
附件:焊装夹具技术要求一、焊装夹具方案规划要求:1. 为了保证在产品加工过程中基准的统一,乙方在做夹具式样书过程中需按照甲方提供的RPS基准系统来确定夹具主定位基准(改造项目需延用原有基准,并保证统一),定位孔及销的主、副性必须与RPS一致;定位面可在RPS同一基准面上进行适当调整(50mm以内,不可切换定位型面;型面变化较大的位臵移动控制在20mm以内),且必须保证前后工序定位基准统一。
如乙方定位基准有其它方案的,会签时提出与甲方RPS的差异清单(详见附件一),经甲方书面同意后方可实施。
甲方提供夹具式样书的,完全按照夹具式样书进行夹具设计与商务报价。
2. 夹具定位方案设计时,需充分考虑件的强度与定位精度,必要时可将RPS中的菱形定位销改为圆形,以及可根据夹具的定位要求在甲方提供的RPS基础上增加定位面,以保证件的精确、稳定定位。
3. 夹具定位方案设计时,需充分考虑夹具的作业性、结构设计的合理性,对甲方提供的工艺文件中要求的夹具结构、工序的划分可根据实际情况提出合理建议,经甲方书面同意后可进行适当的修改。
如乙方未提出异意的,乙方必须保证所设计、制造出来夹具的作业性、定位性完全满足甲方生产要求。
4. 夹具定位方案设计时,需充分考虑每套夹具上增加钣件的防错、防漏装装臵(如左右件、类似件装错,同一个零件不同方位的装反,在总成件下方小零件漏装等),以有效避免错漏装。
5. 夹具在定位方案设计时,补焊夹具根据甲方的焊点布局进行夹具设计,满足焊点在夹具夹紧状态下能够焊接完成。
二、夹具材质及热处理要求1.夹具底座BASE要求采用Q235 A板材和槽钢或方钢焊接而成,槽钢或方钢规格要求如下:ArrayBASE底板的焊缝采用非连续焊缝(焊缝总长度不得小于制件总长的1/2),焊后经热处理退火消除应力(不允许采用机械消除应力)并喷砂处理,退火处理须提供残余应力检测报告。
2.规制块(基准块、压块)采用45#钢,表面淬火处理后硬度值达HRC40~45,表面应进行发黑处理。
焊装夹具调试及验收技术要求
焊装夹具调试及验收技术要求前言焊装夹具是生产过程中不可或缺的一个环节,它直接影响着产品的质量。
为了保证焊装夹具的可靠性和精度,在生产过程中需要进行一系列的调试和验收工作。
本文将从以下几个方面介绍焊装夹具调试及验收技术要求,希望能够对读者提供一定帮助。
焊装夹具调试技术要求1.准备工作在调试之前必须对焊装夹具所使用的设备进行必要的检查和维护工作,确保设备的正常运转。
同时,还需要对夹具的各部位进行检查,发现问题及时处理。
2.组装和安装在组装和安装焊装夹具时,必须按照制造商的装配要求和程序进行操作。
如有需要,要进行试装,确保加工精度符合要求。
在安装过程中,也要注意检查夹具的配合情况,以保证夹具各个部位的平行度和垂直度。
3.调试过程在进行焊装夹具的调试过程中,需要注意以下几个方面:3.1 合模精度夹具的合模精度必须达到要求,以保证工件的加工精度。
调试时要精确调整夹具的机构,使工件能够按照要求正确定位,同时与夹具配合的各个部件也必须精确调整。
3.2 夹具的牢固程度在实际使用中,夹具必须有一定的刚度和稳定性,以避免工件在加工时发生变形或位移。
在调试过程中,要注意夹具的牢固程度,并及时发现和处理夹具发生松动、变形等问题。
对于夹具的加固部位,要加强加固措施,确保夹具在使用过程中的安全性。
3.3 校正夹具的各个部位夹具的各个部位的正确度对于工件的加工效果有着至关重要的影响。
在调试过程中,要对夹具的各个部位进行校正,以保证夹具各个部位的角度和位置都符合要求。
4.调试结果的评估在焊装夹具的调试过程中,要注意记录各个部位的调试结果,并及时评估夹具的使用效果。
对于不符合要求的部位,要及时进行修正和改进工作。
焊装夹具的验收技术要求1.技术文件的审查焊装夹具在出厂之前,需要经过一系列的设计、制造和调试工作。
在验收过程中,首先要对焊装夹具相关的技术文件进行审查,以确认设计和制造过程是否规范合理,夹具是否满足使用要求。
2.焊装夹具的外观检查外观检查主要是对焊装夹具的外形、表面质量等进行检查,目的是检测或发现夹具表面裂痕、脱落、变形等不良情况。
微型车车身焊装夹具的调试和验证_杨旭磊
车身焊接夹具的调试与验证是一项涉及到夹具 设计、机械制造、焊接技术、车身焊接工艺制定、 三坐标检测等多方面综合性很强的技术工作,因此 调试人员必须具备一定的理论知识和丰富实践经 验,否则会出现花费很多的时间和精力解决了一个
2010年第3期
汽 车 工 艺 与 材 料 AT&M 15
AT & M
2 夹具调试的流程和样件的准备
夹具调试的顺序见图2。 检查调试与验证工装的焊接样件是否合格的内容
汽 车 工 艺 与 材 料 AT&M 13
AT & M
AT & M 视 界
FIELD
OF
VISION
图2 夹具调试的顺序 如下。
a.定位面的形状和尺寸,夹具所用焊接样件上的 定位面应该表面光滑、成形到位。
问题,又导致出现另外一个问题。总之,车身焊接 夹具的调试与验证,必须依据具体的产品结构特点、 工艺特点、夹具结构特点、零件受力特点去寻求一
16 汽 车 工 艺 与 材 料 AT&M
种综合的调试状态。
AT &M
2010年第3期
长春工业大学 陈 军 于 燕 长春工程学院 贾坤宁 中国第一汽车集团公司技术中心 宋起峰
当前,在全球面临能源匮乏和环境污染的严重形 势下,汽车轻量化已成为汽车发展的主要方向;而采 用先进的高强度钢板是在保证汽车安全性前提下实现 汽车轻量化的最有效途径。双相钢因具有强度高、加 工性能好等优良的综合性能而得到世界各国的大力开 发和研究,成为车用钢板的热门材料;而在汽车制造 业中,电阻点焊是主要的连接技术。由于电阻点焊具 有生产效率高、易于实现自动化等优点,已经在汽车 工业中广泛采用,并将继续成为汽车工业中高强度钢 板的主要焊接方法
- 1、下载文档前请自行甄别文档内容的完整性,平台不提供额外的编辑、内容补充、找答案等附加服务。
- 2、"仅部分预览"的文档,不可在线预览部分如存在完整性等问题,可反馈申请退款(可完整预览的文档不适用该条件!)。
- 3、如文档侵犯您的权益,请联系客服反馈,我们会尽快为您处理(人工客服工作时间:9:00-18:30)。
焊装夹具调试及验收技术要求IMB standardization office【IMB 5AB- IMBK 08- IMB 2C】+8AT项目焊装夹具招标要求项目名称:+8AT项目夹具新增/改造重庆力帆乘用车有限公司目录+8AT项目焊装夹具招标要求1.简述该项目承担重庆力帆乘用车有限公司(甲方)+8AT项目夹具新增/改造(详见附件一清单,但不限于清单内容)。
乙方对以上工程负全面责任,以满足工艺、安全、可靠等方面要求。
本项目为“交钥匙”工程。
双方共同确认技术方案、工艺装备要求、供货范围及施工工程等,乙方须在该方案基础上进行完善并满足纲领和焊车需求;若后续发生工艺变更,双方协商解决或交付商务处理。
本招标要求书主要针对该设备技术要求、功能描述、责任范围等进行明确,作为甲、乙双方履行合同的技术依据。
2.生产线设计及建设基本条件电源:电压380V±10%、220V±10%、频率50Hz±2%;冷却水压力: mpa;设备正常工作;压缩空气压力:;设备正常工作;820焊装生产线使用寿命为8年或总产量50万台。
3.生产线信息生产节拍:288秒/台;生产纲领:5万/年;251天。
生产班次:双班;设备开动率:85%。
4.+8AT项目夹具新增/改造管理要求乙方负责+8AT焊装SE分析(输出:时序图、焊接流程图,MCP/MCS,焊点分析及优化,焊接通过性分析,搭接性分析,焊接避让,干涉性审查等)、文件输出、工艺方案及布局图的详细设计,并反应出乙方的工艺规划及流程的合理性及可行性。
项目总计划时间大纲要求该项目的管理流程中。
⑴焊接总成的组成件;⑵装入件名称、数量、零部件号;⑶装件顺序;⑷定位点、辅助定位、支撑点、压紧点的坐标位置;⑸定位及压紧形式;⑹操作高度700mm~800mm;⑺焊接形式(是电阻焊还是二氧化碳焊);⑻所用设备的规格、型号及数量;⑼前后工序,定位基准应统一;⑽所装件的名称及件数;未特殊说明部分按照行业通用规则进行提供。
所有焊装夹具设计任务书的内容都必须经过甲方的认可。
5.+8AT项目焊装夹具主要技术总则+8AT项目焊装夹具由乙方方案规划、设计、制作、改造、安装、调试、陪产等,主要包括:820焊接生产线、吊具、输送机构、电气控制等。
焊装线/产品输送要求平稳、安全、可靠、准确。
重复定位精度±。
包边后的补焊夹具需考虑铰链装配的实现。
乙方须选型确定在线设备所涉及的品种、数量,如:CO2保护焊机、螺柱焊机、涂胶机、悬点焊机及焊钳等的数量和安装位置。
焊装夹具设计、制造需满足本协议中第6条:焊装夹具设计和制造技术要求。
+8AT项目夹具新增/改造乙方责任范围。
≥90%,其余为100%)。
乙方主要承担+8AT项目焊装新增/改造夹具的方案及3D设计、制造、安装及调试完成合格后交付给甲方全过程。
生产线内人工工位辅助设备(焊机、焊钳、螺柱焊机、涂胶机等)由甲方负责采购、安装、调试,由乙方提供设备清单,经甲方签字确认提交。
+8AT项目焊装夹具总清单(详见附件一清单,但不限于清单内容)。
6.焊装夹具设计和制造技术要求结构要求:材质要求:×,要求板厚≥20mm,型材采用16号槽钢;夹具BASE板面尺寸≥×,要求板厚≥25mm,型材采用20号槽钢。
BASE焊后经热处理退火消除应力(不允许采用机械消除应力)并喷砂处理。
夹具需有叉车位置标识,位置要适宜夹具平稳的叉运,标识在夹具侧面的槽钢上,标识宽度为40mm,颜色工程黄,两条标识的总宽度不得小于300 mm。
对于以上要求必须提供充分证明或在加工时请甲方参与。
≥120mm,应采取增加加强筋,当支撑座及底板高度≥350mm,应制造专用的支撑座(料厚应≥18mm)以保证刚性。
≤μm。
≤μm,保证其硬度和耐磨性。
直径规范:产品孔径、螺纹孔径采用,加工公差+。
措施。
夹具BASE板面上的检测基准孔(不得采用基准沟)的坐标值应设定为一车身坐标的100、50整数值;基准孔孔径要求为10H7,并要加盖板保护;基准孔坐标值直接在BASE 面上进行机械打坐标号,并要加盖板保护(下图所示);坐标已旋转的夹具,基准孔坐标为A、B、C,且在夹具铭牌上注明旋转基准坐标与角度。
基准孔空间分布要合理(一组至少要3个,间距要大于BASE长、宽的3/4以上,对于大型夹具要考虑适当增加检测基准孔的组数),作为检测的主基准孔在坐标上要标注“主”字,有几个主基准孔的标注“H1”、“H2”,且BASE板面上要预留有一定的便携式三坐标摆放位置,便于后期检测基准沿用。
功能要求:夹具设计需保证操作的安全性和便捷性,符合人机工程学,平移、平面旋转、轴向翻转等动态机构应有到位锁死装置和安全防护装置;夹具设计规范及要求:焊点位置两层板用“●”表示,三层板用“▲”表示,重焊用“■”表示,保护焊用“━”表示,设计时应注意焊点的坐标位置,必须留有充分的焊钳操作空间,便于施焊。
调整垫片应进行表面镀锌或发蓝处理。
支撑座的设计应标准化、系列化,支撑座焊后应作退火处理,消除应力。
焊缝应为连续焊缝,并要求牢固、光滑、平整、无缺陷。
夹具所采用的支承座(即POST)须满足系列化要求,一般高度为150mm、200mm、250mm、300mm、350mm、400mm、450mm ,且能充分满足互换性要求。
坐标网格线的平行度误差:相邻单一间隔距为100mm;累积间隔距为全长,并在刻线的两端刻上坐标值,坐标值应与汽车产品图上的坐标值相一致,底板的焊接焊缝采用非连续焊缝,要求牢固、光滑、平整、无缺陷,底板焊接后应作完全退火处理。
≥的,要装有水平调整螺栓。
大型夹具(如前纵梁、后纵梁总成等)要求用8英寸铸铁滚轮,并且要有水平调整螺栓。
水平调整螺栓调整量需≥50mm,并且前后序调整量要一致。
水平调整螺栓布置间距控制在以内,并尽量均布。
),防止零件划伤到人。
若气缸超出BASE板外形,原则上应增加保护罩。
Ф10mm,磁铁外侧应嵌入铜套,装磁铁的零件上应开有方便磁铁更换的取出孔。
SMC\FESTO标准双导杆系列产品(详见附件二),为保证精度不允许自行加工。
注:材料为铝质,厚度,字体深度;字体为宋体,公司名称字高5,其他字高3;表格线宽度;底色为铝材本色,文字及表格线为黑色;公司图标为红色,底色为铝材本色;夹具需设置起吊机构精度要求:定位面的组合精度控制在±以内,定位销的组合精度控制在±以内。
主定位销的位置精度为±。
BASE板水平面上定位孔与定位孔之间的位置公差为±,粗糙度为,在加工、测量和组装时使用的基准必须统一,底座采用三销基准孔,具体结合夹具大小确定,甲方在会签时确认。
所有的定位孔与基准面的公差为±,定位孔粗糙度为。
基准面之间精度允许±,测量面之间的精度允许±。
支架的垂直度,精度允许误差按国家7级精度执行。
参见《机械工程手册第二版》夹具定位块的安装需采用“调整垫片式”的结构,调整垫片厚度为3mm(1mm 、1mm 、、、)。
采用三坐标检测夹具的制造精度,并输出夹具检测报告,三坐标精度和测量平板精度必须能够满足测量要求(乙方提供检测结果)。
气动元器件要求:气动元器件品牌(详见附件二),在会签时需经甲方确认。
根据气动元件自身润滑的要求,气源处理元件乙方可以选择采用二联件,要求其上有防撞盖板。
夹具的气管要求布置在底板的槽钢内,管路布置和装配要有序、美观,气管两端要有标识牌/标签,在预验收时经甲方确认。
在气路设计时,必须充分考虑到安全性,特别是气路设计为“软启动”以防止“启动飞出”造成安全隐患。
在弧焊工位,气缸形式需要耐焊渣型气缸,以及增加相应的保护装置,避免焊渣直接掉到磁性开关上。
在有干扰信号地方,要有抗强磁抗干扰的措施。
衬套采用嘉善品牌,加强耐磨性和导向精度。
导杆材质采用40Cr模具钢,并作表面硬化处理,加强导杆耐磨性。
其它要求:合同签定后甲方提供设计所需的产品明细表、产品图(数模)以及相关的技术文件;乙方严格遵守相应的保密协议,所有资料不作他用,并不提供给其它厂家及个人。
乙方外购件应提供品牌名称、生产厂家技术规格图及主要技术图(一式两份)。
乙方应提供自制非标件的图纸的电子档,乙方所提供的技术资料及图纸应能够用于甲方的备件制作、更换、安装等要求。
乙方所提供的技术资料及图纸应能够用于甲方的备件制作、更换、安装等要求。
气动原理图上应标明各气动元件的型号。
夹具上的各气动元件要在气动原理图上进行统一编号。
乙方提供夹具工艺方案仕样书,由甲方确认能够满足甲方要求后才能进行夹具的3D图设计,夹具3D设计完成后必须经甲方会签同意后才能投入制造,甲方在夹具工艺方案仕样书会签确认时,只针对单套夹具图纸确认,对夹具的整套工艺方案、流程不承担责任。
整个设计、开发过程甲方有权进行全过程监控(设计会签—加工—装配—检测—调试的全过程中甲方根据需要进行监控)。
所有工装交付前应统一着色、编号,夹具颜色由甲方拟定色标,必要时乙方提供色标样卡并予甲方确定。
力帆厂的具体时间根据焊样件情况确定。
派出技术人员到乙方工厂进行有关图纸和资料的会签工作,会签确认后方可投入制造。
设计会签仅是甲方对图面的认可,不对夹具设计图纸及工艺方案的正确性承担责任,而乙方必须对夹具的最后结果负责。
7.焊装夹具调试及验收技术要求厂家调试甲方以乙方提供并经过甲方确认后的焊装夹具设计制造规范和验收标准作为焊装夹具验收标准(除甲方提出的特定要求外)。
预验收在乙方工作地进行静态和动态检查,甲方派人员参加,并填写《夹具验收报告》,并出具夹具预验收会议纪要。
预验收时乙方提供以下文件(以下文件预验收完成后随夹具发运到甲方):⑴三坐标检测报告电子档及纸质版各一份⑵工艺方案仕样书电子档及纸质版各一份⑶ 3D夹具数模电子档一份,要求CATIA 20版本⑷ 2D夹具图电子档及纸质版各一份⑸电气原理图电子档及纸质版各一份⑹平面布置图电子档及纸质版各一份⑺工艺流程图电子档(EXCEL格式,含工位名称、零部件名称和代码、材质、厚度等信息)及纸质版各一份⑻工艺卡电子档及纸质版各一份⑼合格证和其他相关的验收资料等甲方才予以预验收,预验收合格后才允许发货。
预验收标准及要求详见附件三:《焊装线-夹具预验收标准》。
焊装夹具运到甲方的工厂后,按装箱单进行开箱检查,如发现破损、缺陷或缺少零件,乙方应作出整改计划并按计划执行。
乙方派人员到甲方的工厂进行安装、调试和技术指导,此项工作要做出满足节点要求的执行计划。
焊装夹具的总协调工作由乙方负责,甲方予以充分配合。
终验收在甲方的工厂进行,焊装夹具达到批量生产满足产品要求或生产500台白车身后,甲方负责组织,乙方派人员参加进行终验收。
在焊装夹具的验收过程中,由于乙方设计或制造等原因而出现的质量问题,甲方有权提出请乙方返修,然后再次检查直至合格。