夹具设计规范
夹具基准设计标准要求有哪些
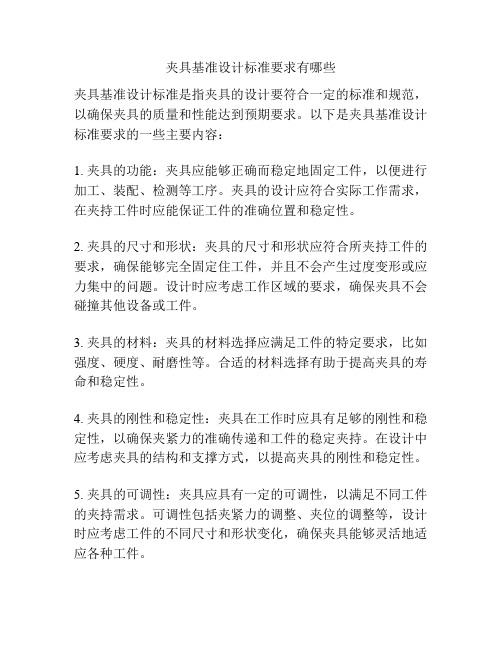
夹具基准设计标准要求有哪些夹具基准设计标准是指夹具的设计要符合一定的标准和规范,以确保夹具的质量和性能达到预期要求。
以下是夹具基准设计标准要求的一些主要内容:1. 夹具的功能:夹具应能够正确而稳定地固定工件,以便进行加工、装配、检测等工序。
夹具的设计应符合实际工作需求,在夹持工件时应能保证工件的准确位置和稳定性。
2. 夹具的尺寸和形状:夹具的尺寸和形状应符合所夹持工件的要求,确保能够完全固定住工件,并且不会产生过度变形或应力集中的问题。
设计时应考虑工作区域的要求,确保夹具不会碰撞其他设备或工件。
3. 夹具的材料:夹具的材料选择应满足工件的特定要求,比如强度、硬度、耐磨性等。
合适的材料选择有助于提高夹具的寿命和稳定性。
4. 夹具的刚性和稳定性:夹具在工作时应具有足够的刚性和稳定性,以确保夹紧力的准确传递和工件的稳定夹持。
在设计中应考虑夹具的结构和支撑方式,以提高夹具的刚性和稳定性。
5. 夹具的可调性:夹具应具有一定的可调性,以满足不同工件的夹持需求。
可调性包括夹紧力的调整、夹位的调整等,设计时应考虑工件的不同尺寸和形状变化,确保夹具能够灵活地适应各种工件。
6. 夹具的安全性:夹具的设计应考虑安全性因素,防止夹具在使用过程中对操作人员造成伤害。
夹具应避免尖锐边缘和突出部分,且在夹紧力过大时应有安全保护措施,如紧急停止装置等。
7. 夹具的可维护性:夹具设计应方便夹具的维护和保养。
夹具的关键部件应易于拆卸和更换,设计时应充分考虑维护人员的工作需求,以便及时进行维护和修理。
8. 夹具的标准化:夹具的设计应尽量符合标准化要求,以便于制造和使用。
标准化设计有助于降低制造成本、提高夹具质量和效率,并便于夹具的更换和升级。
综上所述,夹具基准设计标准要求包括夹具的功能、尺寸和形状、材料、刚性和稳定性、可调性、安全性、可维护性以及标准化等方面。
这些要求有助于确保夹具能够可靠地夹持工件,提高加工质量和效率,减少操作人员的劳动强度。
夹具设计方案及使用规范
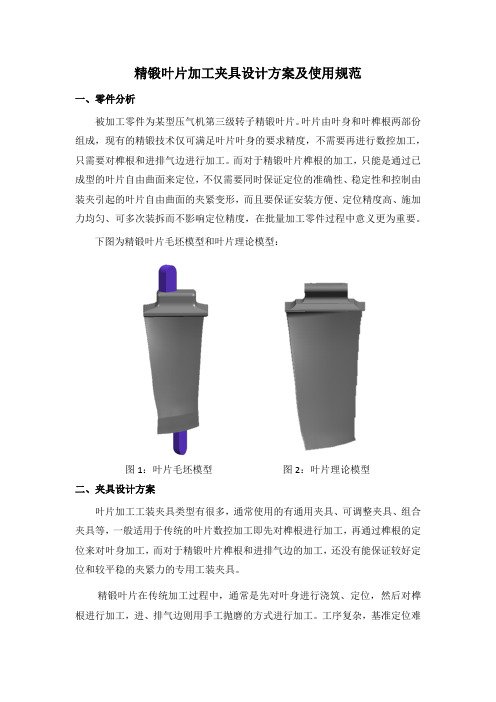
精锻叶片加工夹具设计方案及使用规范一、零件分析被加工零件为某型压气机第三级转子精锻叶片。
叶片由叶身和叶榫根两部份组成,现有的精锻技术仅可满足叶片叶身的要求精度,不需要再进行数控加工,只需要对榫根和进排气边进行加工。
而对于精锻叶片榫根的加工,只能是通过已成型的叶片自由曲面来定位,不仅需要同时保证定位的准确性、稳定性和控制由装夹引起的叶片自由曲面的夹紧变形,而且要保证安装方便、定位精度高、施加力均匀、可多次装拆而不影响定位精度,在批量加工零件过程中意义更为重要。
下图为精锻叶片毛坯模型和叶片理论模型:图1:叶片毛坯模型图2:叶片理论模型二、夹具设计方案叶片加工工装夹具类型有很多,通常使用的有通用夹具、可调整夹具、组合夹具等,一般适用于传统的叶片数控加工即先对榫根进行加工,再通过榫根的定位来对叶身加工,而对于精锻叶片榫根和进排气边的加工,还没有能保证较好定位和较平稳的夹紧力的专用工装夹具。
精锻叶片在传统加工过程中,通常是先对叶身进行浇筑、定位,然后对榫根进行加工,进、排气边则用手工抛磨的方式进行加工。
工序复杂,基准定位难度较大,手工抛磨的方式也不利于大批量生产,效率低、稳定性差。
因而亟需设计新型精锻叶片加工夹具。
设计方案如下:1、由于精锻叶片的榫根加工是通过叶身的自由曲面来定位的,存在定位误差大、稳定性不足、夹紧变形大、难以多次重复使用的问题,提出一种精锻叶片榫根加工夹具,夹具由精锻叶片叶身曲面定位带进行定位和夹紧,保证曲面定位的精确性和稳定性。
2、该夹具解决其技术问题所采用的技术方案是:包括转动台、夹具箱体、箱盖、夹紧垫片、紧固螺钉、工艺台定位块、紧固螺栓、锥形定位销、定位销、固定销、定位块等,夹具设计满足六点定位原理。
3、夹具箱体与转动台固定连接,转动台安装在机床工作台上。
气动快换装置连接,方便自动化生产线中机器人手臂进行装卸。
4、夹具上有拉紧装置,在叶片加持过程中,起到定位拉紧作用。
5、夹具箱体与叶片接触面试根据叶片的叶盆、叶背型面加工而来,叶片的叶身试不需要加工的,因而起到很好的贴合和加持作用。
通用夹具方案设计规范最新版

通用夹具方案设计规范最新版通用夹具方案设计规范最新版一、设计原则1. 经济性:夹具设计应尽可能实现低成本和高效益的原则。
2. 通用性:夹具设计应具有一定的通用性,能够适用于多种工件的加工和装配。
3. 稳定性:夹具设计应具有足够的稳定性,能够确保工件在夹具中的位置和姿态不变。
4. 便捷性:夹具设计应便于使用和调整,能够快速完成夹具的装夹和拆卸。
5. 安全性:夹具设计应保证操作人员的安全,并避免对设备和工件造成损坏。
二、设计要求1. 结构设计:夹具结构应简单紧凑,易于制造和组装,各部件之间应具有良好的协调性。
2. 强度设计:夹具的关键部件应具备足够的强度和刚度,能够承受工作负荷和外部冲击。
3. 精度设计:夹具设计应考虑工件的精度要求,确保夹具对工件的定位和固定不会产生误差。
4. 自动化设计:夹具设计应考虑自动化生产的需求,提高生产效率和质量。
5. 维修性设计:夹具设计应考虑维修和更换部件的便捷性,降低维修成本和停机时间。
三、设计流程1. 确定夹具设计的目标和要求,包括工件的类型、加工过程、精度要求等。
2. 选择合适的夹具结构和原理,根据工件的特点和要求确定夹具的工作方式和定位方式。
3. 进行夹具零部件的设计和选型,根据夹具结构和工作原理确定各个部件的尺寸和材料。
4. 进行夹具的装配和试验,验证夹具的设计是否符合要求,并进行必要的调整和改进。
5. 编写夹具使用和维护手册,记录夹具的结构、使用注意事项和维护方法。
四、设计审核1. 设计部门应对夹具设计进行审核,确保夹具设计符合规范要求。
2. 生产部门和质量部门应对夹具的性能和精度进行测试和评估,确保夹具能够满足生产要求。
3. 进行实际生产试验,并根据生产情况对夹具进行改进和调整。
五、设计评估1. 根据夹具的成本、性能、稳定性和可靠性等指标对夹具的设计进行评估,确定是否满足设计要求。
2. 根据评估结果进行修正和改进,以提高夹具的效率和质量。
六、设计文件1. 夹具设计应包括夹具总图、零件图、装配图和BOM表等。
夹具设计标准标准
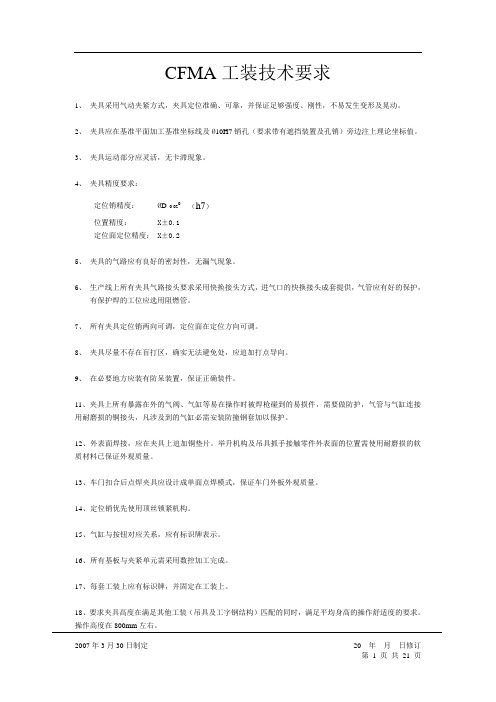
CFMA工装技术要求1、夹具采用气动夹紧方式,夹具定位准确、可靠,并保证足够强度、刚性,不易发生变形及晃动。
2、夹具应在基准平面加工基准坐标线及Ø10H7销孔(要求带有遮挡装置及孔销)旁边注上理论坐标值。
3、夹具运动部分应灵活,无卡滞现象。
4、夹具精度要求:定位销精度:ØD-0.020 (h7)位置精度:X±0.1定位面定位精度: X±0.25、夹具的气路应有良好的密封性,无漏气现象。
6、生产线上所有夹具气路接头要求采用快换接头方式,进气口的快换接头成套提供,气管应有好的保护,有保护焊的工位应选用阻燃管。
7、所有夹具定位销两向可调,定位面在定位方向可调。
8、夹具尽量不存在盲打区,确实无法避免处,应追加打点导向。
9、在必要地方应装有防呆装置,保证正确装件。
11、夹具上所有暴露在外的气阀、气缸等易在操作时被焊枪碰到的易损件,需要做防护,气管与气缸连接用耐磨损的铜接头,凡涉及到的气缸必需安装防撞钢套加以保护。
12、外表面焊接,应在夹具上追加铜垫片。
举升机构及吊具抓手接触零件外表面的位置需使用耐磨损的软质材料已保证外观质量。
13、车门扣合后点焊夹具应设计成单面点焊模式,保证车门外板外观质量。
14、定位销优先使用顶丝锁紧机构。
15、气缸与按钮对应关系,应有标识牌表示。
16、所有基板与夹紧单元需采用数控加工完成。
17、每套工装上应有标识牌,并固定在工装上。
18、要求夹具高度在满足其他工装(吊具及工字钢结构)匹配的同时,满足平均身高的操作舒适度的要求。
操作高度在800mm左右。
19、要求伸缩销机构需带有气缸内置或外置的THK导轨,且要求引出外置直线导轨的润滑加油嘴已便维护。
20、夹具设计时的定位需严格执行CFMA提供的定位Locator-drawing信息,需要改动的需与LAM相应工程师确认。
21、原则要求定位销采用MISUMI品牌,对于个别标准无法统一的定位销,需供应商列出清单并清晰不同点,与CFMA讨论一致后确定方案。
工装夹具的要求 -回复
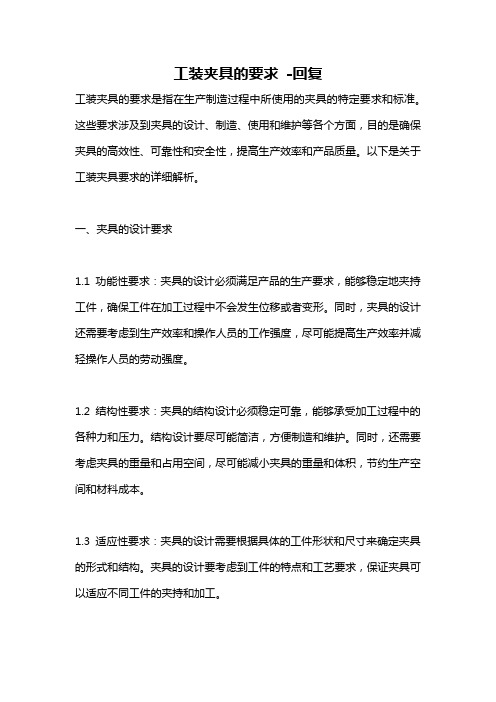
工装夹具的要求-回复工装夹具的要求是指在生产制造过程中所使用的夹具的特定要求和标准。
这些要求涉及到夹具的设计、制造、使用和维护等各个方面,目的是确保夹具的高效性、可靠性和安全性,提高生产效率和产品质量。
以下是关于工装夹具要求的详细解析。
一、夹具的设计要求1.1 功能性要求:夹具的设计必须满足产品的生产要求,能够稳定地夹持工件,确保工件在加工过程中不会发生位移或者变形。
同时,夹具的设计还需要考虑到生产效率和操作人员的工作强度,尽可能提高生产效率并减轻操作人员的劳动强度。
1.2 结构性要求:夹具的结构设计必须稳定可靠,能够承受加工过程中的各种力和压力。
结构设计要尽可能简洁,方便制造和维护。
同时,还需要考虑夹具的重量和占用空间,尽可能减小夹具的重量和体积,节约生产空间和材料成本。
1.3 适应性要求:夹具的设计需要根据具体的工件形状和尺寸来确定夹具的形式和结构。
夹具的设计要考虑到工件的特点和工艺要求,保证夹具可以适应不同工件的夹持和加工。
1.4 安全性要求:夹具设计要符合安全操作的要求,确保操作人员在夹具使用过程中不会受到伤害。
夹具的各个部件要具备足够的强度和刚度,避免因夹具失效导致工件脱离夹持造成伤害。
二、夹具的制造要求2.1 材料选用:夹具的制造要选用材质适当的材料,如高强度合金钢、工程塑料等。
材料的选择要考虑夹具在使用过程中的承载能力、耐磨性、耐腐蚀性等因素。
2.2 加工精度:夹具的加工精度直接影响到夹具的使用效果和工件的加工精度。
夹具的各个部件的加工精度要求较高,以保证夹具的工作精度和稳定性。
夹具的加工精度通常要求在±0.02mm以内。
2.3 表面处理:夹具的表面处理可以有效地提高夹具的耐磨性和耐腐蚀性。
常见的表面处理方式包括镀铬、喷涂、氮化等。
表面处理要符合环保要求,确保无害于操作人员和产品质量。
2.4 装配要求:夹具的装配要求严格,各个部件的装配要正确无误,保证夹具的正常工作。
装配时要注意夹具各部分之间的匹配精度,以及各紧固件的紧固力,确保夹具的稳定性和可靠性。
专用夹具设计的基本要求

一、专用夹具设计的基本要求1.夹具设计应满足零件加工工序的精度要求;2.应能提高加工生产率;3.操作方便、省力、安全;4.具有一定使用寿命和较低的夹具制造成本;5.夹具元件应满足通用化、标准化、系列化的“三化”要求;6.具有良好的结构工艺性:便于制造、检验、装配、调整、维修。
二、专用夹具设计的方法步骤1、已知条件:工艺人员提出的夹具设计任务书,内容主要包含:工序加工尺寸、位置精度要求、定位基准、夹紧力作用点、方向;机床、刀具、辅具;所需夹具数量。
2、设计方法步骤夹具设计生产过程一般可简单表示成下面框图⑴准备阶段:明确设计要求、掌握第一手资料①收集各种图纸和技术资料②了解生产批量和夹具需要量③收集有关机床的资料④收集有关刀具方面的资料⑤收集有关夹具零部件标准⑥了解有关本单位制造和使用夹具的情况⑦收集国内外同类夹具的资料⑵ 设计阶段①定位方案②夹紧方案③对刀、导引、分度方案④典型夹具结构借鉴⑶ 绘图阶段①比例尽量1∶1;②主视图尽量选与操作者正对的位置;③被加工工件用双点划线画出外形轮廓和主要表面(定位面、夹紧面、加工面),可视为透明体,可对其剖视表示,其加工余量用网纹线表示;④在夹具体显眼位置画出“◆”标记,表示该处打夹具编号。
⑷标注尺寸、技术条件⑸编写零件明细表⑹绘制非标准夹具零件图三、夹具总图上公差配合的制订⑴ 夹具标准件与相关零件的配合参照《夹具设计手册》选取。
⑵ 与工件加工尺寸公差无关的夹具公差:一般参照下表选择⑶ 与工件加工尺寸公差δH有关的夹具公差δHJ,参照下表选取四、夹具总图上技术条件的制订夹具总图上的技术条件包括:装配过程中的注意事项;装配后应满足的位置精度要求;本夹具的操作要求等。
装配后应满足的位置精度要求主要归纳为如下框图:框与框之间有连线,表明有相互位置要求,箭头指向框为相互位置的基准。
H1:① 多件装夹时,相同定位元件之间的位置要求;② 组合定位时,多个定位元件之间,次要定位元件对主要定位元件的位置要求。
夹具基准设计标准要求是什么
夹具基准设计标准要求是什么夹具基准设计标准是指夹具设计中需要满足的一系列要求,以确保夹具能够满足使用要求并保证工艺生产的质量和效率。
下面是夹具基准设计标准的一般要求:1. 强度和刚度:夹具需要具有足够的强度和刚度,能够承受并保持工件的正确位置和姿态。
夹具的材料选择和结构设计需要满足所要加工工件的特殊要求。
2. 精度和稳定性:夹具需要满足加工工件的精确要求,保持工件的稳定位置和姿态,以确保加工过程中的精度和一致性。
夹具在长时间使用后也需要保持稳定性,不产生变形或松动。
3. 可调性:夹具需要具有可调性,以适应不同尺寸和形状的工件,并且能够快速和准确地进行调整。
夹具的调整方式要方便实用,并且能够保持调整后的位置和姿态。
4. 安全性:夹具设计需要考虑到操作人员的安全,避免产生危险的部件、夹紧力过大或不均匀等问题。
夹具需要能够保护工件和夹具本身,防止工件损坏或夹具磨损。
5. 便于制造和维护:夹具的设计需要考虑到制造和维护的便捷性,避免过于复杂的结构和工艺要求,以减少制造成本和维护成本。
6. 标准化和规范化:夹具的设计应符合相关的标准和规范,以确保夹具与其他设备和工艺的兼容性,并便于技术交流和设备替换。
7. 经济性:夹具的设计需要考虑到经济性,包括材料成本、制造成本和维护成本等方面。
夹具的设计应尽量简化结构,节约材料,并提高生产效率和使用寿命,以降低总体成本。
8. 可靠性和耐久性:夹具需要具有足够的可靠性和耐久性,能够在长时间使用和重复使用时保持稳定性和性能。
夹具的制造质量和材料选择需要确保其长时间使用的可靠性。
综上所述,夹具基准设计标准要求包括强度和刚度、精度和稳定性、可调性、安全性、便于制造和维护、标准化和规范化、经济性、可靠性和耐久性等方面。
这些要求旨在确保夹具能够满足工艺生产的需求,提高加工质量和效率,并降低成本和风险。
焊装夹具设计技术规范
6.4.5 手动夹紧,气动打开的标准机构:
EC—J 02 001—2008
12
每天进步一点点
PDF 文件使用 "pdfFactory Pro" 试用版本创建
6.4.6 手动夹紧,气动打开机构气动原理图的构成:
EC—J 02 001—2008
1.此种类型气缸下部进气口处安装消声器;
2500≥A+B≥1800 采用 12#槽钢 (超大型) 基板厚度 C=25
A+B≥2500
采用 20#槽钢 (超大型) 基板厚度 C=30
注:A 或 B≥1400 时采用中间加强筋,且间距不大于 700mm。周边槽钢设计开口向外;
6.3.3 精度 l 基准面平面度0.1/1000; l 基准槽公差±0.05mm; l 栅格线位置相对基准的误差:0.15/1000; l 基准面粗糙度Ra1.6。
1.目的
EC—J 02 001—2008
为在夹具设计制造过程中,提供设计依据及验收标准;在与夹具厂家进行技术交流以
本标准作为依据。
2.范围
本标准规定了夹具设计制造过程中设计规则和部分标准件的适用范围。
本标准适用于长城汽车股份有限公司的夹具设计制造及夹具验收和招标技术文件依
据。
3.规范性引用文件
下列文件中的条款通过本标准的引用而成为本标准的条款,本标准等效采用以下标
准,所示标准均为有效版本,所有标准均会被修订,如有修订将及时变更。
GB/T1804-1992 一般公差、线性尺寸的未注公差;
GB/T1800.4-1999 孔与轴的极限偏差数值;
GB/T4458.4-1984 尺寸标注;
GB/T4458.5-1984 尺寸公差与配合的标注;
机床夹具的设计要求
机床夹具的设计要求
机床夹具的设计要求会根据具体的应用和工作要求而有所不同。
以下是一些常见的机床夹具设计要求:
稳定性:机床夹具必须具备足够的稳定性和刚性,以确保工件在加工过程中不会产生过大的振动和变形。
精度:夹具的设计应考虑到工件的精度要求,并提供合适的定位和固定方式,确保工件在夹具中的位置和姿态的准确性。
可靠性:夹具设计应具备足够的可靠性和耐久性,以确保长时间稳定地夹持工件,并能经受重复的使用和加工过程中的力和压力。
切削润滑:对于涉及切削加工的夹具,设计应考虑切削润滑的供给和排除,以保持切削表面的清洁和顺畅。
操作便捷性:夹具的设计应便于操作和调整,以提高操作员的工作效率,并确保安全性。
工艺优化:夹具的设计应考虑到工艺流程的优化,减少加工时间、提高生产效率,并最大程度地满足工艺要求。
适应性:夹具的设计应具备一定的适应性,能够夹持不同形状、尺寸和材料的工件,并且具备一定的调整和适应范围。
安全性:夹具的设计应考虑到操作员的安全,防止夹具在工作过程中产生危险或造成伤害。
经济性:夹具的设计应尽量简化和优化结构,以降低成本,并在保证功能的前提下提高制造效率。
以上是一些常见的机床夹具设计要求,具体的要求可能会因不同的应用、工艺和工件而有所不同。
在进行机床夹具设计时,需要综合考虑这些要求,并根据具体情况进行合理的设计和优化。
焊接夹具设计规范
焊接夹具设计规范篇一:焊接夹具的设计的要求焊接夹具的设计的要求焊接工装是摩托车车架制作过程中的关键设备,其设计质量不仅直接影响车架的精度,而且也决定生产效率和工人的作业条件。
1 焊接工艺方案的确定1.1 准备工作主要研究原始资料,明确设计任务和进行必要的调查研究。
一般应具备下列原始资料。
a)车架的生产纲领(年产量)、生产性质与类型。
b)车架图纸、技术要求及其他相关件的装配关系。
c)车间的生产条件,如作业面积、动力供应及技术水平等。
d)相关技术标准、法规和本企业的发展目标。
1.2 工艺方案的设计在调查研究和对资料综合分析的基础上拟定车架的工艺方案(包括焊接工艺规程、工程计划表和结构草图等)。
需对下列内容进行构思和选择。
a)根据生产纲领等确定车架的生产节拍。
b)根据车架零部件的装配顺序、焊接方法、焊缝的位置及质量要求、生产节拍和各工序工时的均衡来规定生产组织形式和工艺路线的安排,包括划分车架零部件组焊的工序和所需焊接工装的数量及其在车间的布局。
c)实现某种功能拟采用的原理和相应的机构。
如定位与夹紧的方式和机构、焊件的翻转或回转等。
d)各工序所需工装的基本构成、车架零部件的定位、夹紧位置和总体布局,主要零部件的基本结构。
2 焊接工装的设计2.1 焊接工装的设计原则首先是焊接工装满足工艺技术要求,并应便于操作、安全、可靠及满足外观和经济上的要求。
2.2焊接工装的设计要求a)焊接工装应具有动作迅速、操作方便,操作位置应处在工人最容易接近、最易操作的部位。
特别是手动夹具,其操作力不能过大,操作高度应设在工人最易用力的部位,当夹具处于加紧状态时应能自锁,一般操作高度应控制在800~900mm。
b)焊接工装应有足够的装配、焊接空间,不能影响焊接操作和焊接观察,不妨碍焊件装卸。
所有定位元件和夹紧机构的执行元件应可调,即能伸缩和转位。
同时必须保证焊接机头的焊接可达性。
c)夹紧可靠,刚性适当。
加紧时不能破坏焊接件的定位位置和几何形状(如变形、凹陷、划伤等),且要保证夹紧后不能使焊件松动滑移,可以采取压头行程限位、加大压头接触面积或在压头上安装铜、铝、硬塑料衬垫等措施。
- 1、下载文档前请自行甄别文档内容的完整性,平台不提供额外的编辑、内容补充、找答案等附加服务。
- 2、"仅部分预览"的文档,不可在线预览部分如存在完整性等问题,可反馈申请退款(可完整预览的文档不适用该条件!)。
- 3、如文档侵犯您的权益,请联系客服反馈,我们会尽快为您处理(人工客服工作时间:9:00-18:30)。
焊接夹具设计制造技术规范根据国外先进汽车车身装焊夹具公司对夹具设计的经验,并结合国内的具体情况,大连奥托技术有限公司制定了装焊夹具的设计制造技术规范,设计者应严格遵循。
1..装焊夹具的设计依据以汽车产品零部件图(数模最佳)、装焊工艺图、设计技术任务书、厂标件标准为设计依据,进行规范化、模块化设计。
2..装焊夹具设计通则2.1装焊夹具设计采取模块化方式,按照装焊工艺图进行,以满足焊接工艺要求,夹具设计图画法应贯彻国家机械制图标准。
2.2夹具操作方便,设计完成后的工装系统必须符合人机工程学的要求。
2.3夹具应有足够的装配、焊接空间,焊点在布置时应易接近。
2.4夹具本身必须有良好的制造工艺性和较高的机械效率。
3..装焊夹具设计规范及要求3.l总图设计总图上应标注:夹具轮廓尺寸、操作高度、坐标线(尽量与汽车坐标线统一),坐标基准刻线或坐标基准孔、各部件的安装位置、气缸位置、所有定位尺寸坐标基准孔应相对于坐标线标注,在图中按汽车产品件在汽车中的实际位置建立汽车坐标,其基准线用○>符号表示;同时按夹具的基础建立坐标系,其基准线用○=符号表示。
在夹具上有产品图的摆放位置,并用细双点划线绘出。
焊点位置用○+表示。
设计时应注意焊点的坐标位置,必须留有充分的焊钳工作空间位置,便于施焊。
用双点划线表示焊钳的外形。
总图上还应包括夹具的操作步骤,并且特殊步骤必须详细说明。
对总拼及较复杂的工装、带有自动焊的工装等,其设计必须采用三维设计。
3.2定位块、压块的设计定位块尽量采用标准精铸ZG45#L形毛坯件加工,其厚度规定16mm,特殊情况及厂家有要求例外。
与定位板装配的结合面为基准面用○基表示,要求表面粗糙度为Ra3.2,定位面表面粗糙度为Ra3.2,定位面局部火焰淬火HRC40~45,安装挡片面加工表面粗糙度为Ra6.3,通常挡片安装在L板垂直面一侧定位板上,定位块为AB面情况下,安装在高面一侧,加工后表面喷漆处理,安装面定位面不喷漆,安装孔表面粗糙度为Ra12.5其余表面不加工。
压块尽量采用标准精铸ZG25L形毛坯件加工,其厚度规定16mm,特殊情况及厂家有要求例外。
与压杆装配的结合面为基准面用○基表示,要求表面粗糙度为Ra3.2,压紧面表面粗糙度为Ra3.2,安装挡片面加工表面粗糙度为Ra6.3加工后表面喷漆处理,安装面夹紧面不喷漆,安装孔表面粗糙度为Ra12.5其余表面不加工。
定位块、压块应绘制出车系和夹具坐标系,并标注出其基准面至汽车坐标和夹具坐标的尺寸。
定位块的定位面、压块的压紧面尺寸相对于基准标注,并留出1~5mm加工余量,要求NC加工,定位块的定位方向、压块的压紧方向应设有调整垫片。
定位块、压块应尽量选用总长45mm,65mm两种。
间隙调整垫片长度规定为25、30、45、50、60、65、80、100mm,常规范围里一般长度不超过100mm。
采用冷扎Q235薄钢板,厚度允差为±0.1。
间隙调整垫片压块应尽量选用45mm,65mm两种。
所有的间隙调整垫片应该是3mm厚度,即lmm×2片,0.5mm×2片,且不允许作任何增减。
3.3压杆的设计压杆应尽量采用标准结构形式,压杆的板厚应尽量选用16mm,允差上差+0.1,下差0。
压杆宽度应根据压杆的长短选用30、35、40mm,特殊情况例外。
连接板应选用宽38mm,厚9mm的板焊接在两侧。
压杆应绘制出车系和夹具坐标系,其基准为与定位板铰接的孔用○基表示,应标注出基准孔至汽车坐标和夹具坐标的尺寸,并标注出外形尺寸及基准孔至安装压块和气缸活塞杆铰接孔尺寸。
其中基准孔的允差应为H7,表面粗糙度为Ra1.6;压块安装面粗糙度为Ra3.2 ,其至基准孔的尺寸允差为±0.05mm;气缸活塞杆铰接孔尺寸允差为H7,表面粗糙度为Ra1.6,其余Ra12.5,周边应为Ra25。
3.4定位板的设计定位板的板厚应尽选用16mm厚,板厚允差上差为0mm,下差为-0.1mm;板面加工粗糙度Ra6.3;定位块安装面粗糙度Ra3.2;销孔为Φ10H7;表面粗糙度Ra1.6;铰接孔允差H7,表面粗糙度Ra1.6;其余Ra12.5,周边Ra25。
定位板应绘制出车系和夹具坐标系,其基准选为一个与L板或支座装配的销孔上用○基表示。
应标注出基准销孔至汽车坐标和夹具坐标的尺寸,并标注出外形尺寸;定位板上两销孔之间的距离为70mm,允差为±0.02mm;定位板安装面至基准销孔、铰接孔至基准销孔之间距离允差为±0.05mm。
如果是外来图纸须下通知说明。
3.5通用支座的设计支座的设计应标准化,系列化。
保证支承上、下平面的平行度允差0.05mm.支座焊后应作时效处理,消除应力。
焊缝应为连续焊缝,并要求牢固、光滑平整、无缺陷。
夹具所采用的支承座须满足系列化要求,尽可能选用厂标件,一般高度为150、200、250、300、350、400mm;且能满足互换性要求。
3.6 L座的设计L座的设计应标准化,系列化。
应保证安装底面与立面垂直度允差在0.02mm/100mm;其销孔应为Φ10H7表面粗糙度为Ra1.6,同一平面内的两销孔距离为70mm,允差±0.02mm;底面销孔至立面、立面销孔至底面距离允差为±0.05mm;底面、立面加工表面粗糙度为Ra3.2,其余Ra1.5,周边Ra25。
L座焊后应作时效处理,消除应力。
焊缝应为连续焊缝,并要求牢固、光滑平整、无缺陷。
夹具所采用的L座须满足系列化要求,尽可能选用厂标件,一般高度为100、150、200、250、300、350、400mm;且能满足互换性要求。
选用是时尽量用250mm以下,高度不够时可加支座。
3.7装焊夹具BASE板(底板)的设计BASE板应为一整体,其上平面为安装基准面,表面粗糙度为Ra3.2,平面度按7级形位公差处理,加工应达到7级以下;为测量方便下平面应加工,表面粗糙度为Ra6.3,上下面平行度按7级形位公差标注。
根据厂家要求不同可在安装基准加工两对Φ10H7基准孔,两对孔中心连线上刻上坐标号,或加工出相互垂直的基准槽,如用户没有要求均按基准槽处理。
基准槽10mm宽,3mm深,非基准线侧倒2×45度角,基准线侧表面粗糙度Ra3.2,其它为Ra12.5,基准孔或基准槽应要求装配时封盖。
安装基准面上还应在数控加工中刻坐标网格线,线距为200mm,坐标网格线的平行度允差0.05mm,垂直度允差0.05mm,并在刻线的两端刻上坐标号或用标牌标注,坐标号应与汽车产品图上的坐标号相一致,BASE板的焊接焊缝尽量采用连续焊缝,并要求牢固,光滑平整,无缺陷。
BASE扳焊接后应时效处理,消除内应力。
根据BASE板的大小上板应选20、25、30mm厚,最小不得低于15mm,下板15mm。
应绘制出车系和夹具坐标系,标注出夹具坐标系与车系坐标系的尺寸关系,并标注出基准刻线或基准孔基准孔的位置,以及BASE板各焊接件的外形尺寸及相对位置。
对基准刻线或基准孔从一边标注的,该边最好粗加工至Ra12.5作粗基准,周边Ra25,其余不加工。
地面到夹具安装基准面的高度一般为200mm,夹具基面到工件中心焊接面的高度一般定在700mm以内,总体原则要求符合人机工程要求。
BASE板打孔图应用细双点划线标注出每个单元的接触面及单元号,其尺寸标注应为:每个单元内销孔为2-Φ10H7,销孔间距允差为±0.02mm;单元中基准销孔BASE 板基准刻线或基准销孔尺寸,其允差为±0.05mm;还应标注每个单元内螺纹孔至单元内基准销孔的垂直距离。
3.8装焊夹具设计时应考虑汽车覆盖件的外表面有防止出现焊点压痕的保护措施。
保护板的材料选用CuCrlZr(铬锆铜),其板厚10~12mm,对刚性较差的大型零件应考虑工件抬起机构,对不便于施焊的焊点应设计焊钳导向机构,保证焊接点的准确位置。
3.9装焊夹具设计时,所有定位块、定位销、压块等件离焊点的距离<40mm时应考虑绝缘,绝缘件详见绝缘标准。
3.10气缸运动夹具设计时,气缸在压紧点处必须留有5~8mm运动间隙,防止运动到端点。
3.11采用手动与气动混合夹紧、纯气动夹紧的夹具,夹头打开有先后顺序要求的,动作应能互锁,防止误操作。
3.12其余部件设计要求结构简单可靠、维修方便,夹紧件,元器件的选择按选定标准设计。
3.13装焊夹具调整图的画法及要求调整图是测量和指导装配夹具的重要依据,在调整图上按汽车产品件在汽车中的实际位置建立汽车坐标系,其基准线用符号○>表示;同时按夹具的基础建立坐标系,其基准线用○=符号表示;在夹具图中应有4~Φ10H7基准孔。
如用户须采用ROMER三坐标测量仪,则图中还须有三个(或四个)测量基准块的图形及位置坐标,并在夹具测量基准座上钉上标牌,在标牌上标注测量基准块的实际测量汽车坐标值。
同时应将夹具上的定位件,支承块的外形及测量点反映到调整图中,并按概念图标上代号,与支承块贴合的产品件应有产品件号。
在定位件,支承块的图形上按测量点标上序号,按测量点在引出线上标坐标尺寸,在图纸的右侧按汽车坐标系(X、Y、Z)和夹具坐标系(X1、Y1、Z1)的理论值列表。
支承块测量点的确定原则:支承面是水平面,则选一个测量点;支承面有一个方向的倾斜角,则选二个测量点;支承面为弧面,则选三个测量点。
定位销测量点的原则:垂直销选一个测量点;斜销选一个点,并标一个角度。
3.14 A V导向间隙应可调,但不须定位销;D导向间隙应可调,但调整后打定位销。
3.15倾斜夹具的测量机支座上平面应保持水平位置。
3.16装焊夹具的地脚可设计成可调,其形式见TSG标准设备基础安装机构。
4.夹具基准4.1夹具基准的位置必须满足以下条件4.1.1与汽车坐标系的转换方便、直观;4.1.2便于设备的加工和检测;4.2设备基准的设置有以下方式4.2.1基准孔式:即在夹具的安装基面上加工出垂直于基面且不在同一直线上的三个基准孔(φ10H7),安装检测时通过1面(基面)、—线(其中2个基准孔中心的连线)、一点(第3个基准孔的中心)建立设备坐标系。
4.2.2基准槽式:即在夹具的安装基面上加工出垂直于基面且相互垂直的两条基准槽,安装检测时通过1面(基面)、一面(其中一条基准槽的基面)、一面(其中其一条基准槽的基面)建立设备坐标系。
4.2.3基准块式:在夹具的安装基面上安装不在同一直线上的但具有相同高度的三个基准块,且其中两个基准块与基准面共面,第三个基准块的基面与之垂直,安装检测时通过1面(三个基准块的上平面)、一面(其中2个基准块的共用面)、一面(第3个基准块的基面)建立夹具坐标系。
5.夹具精度5.1主定位销的位置精度为至基准±0.1,尺寸应比产品件孔小0.2mm,加工精度为上差0mm,下差-0.05;5.2夹具基准面至所有夹具垂直方向的测量点公差均为+0.2mm或者-0.2mm,不能土0.2mm。