配气机构整体系统仿真及优化
柴油机配气机构动力学仿真与分析
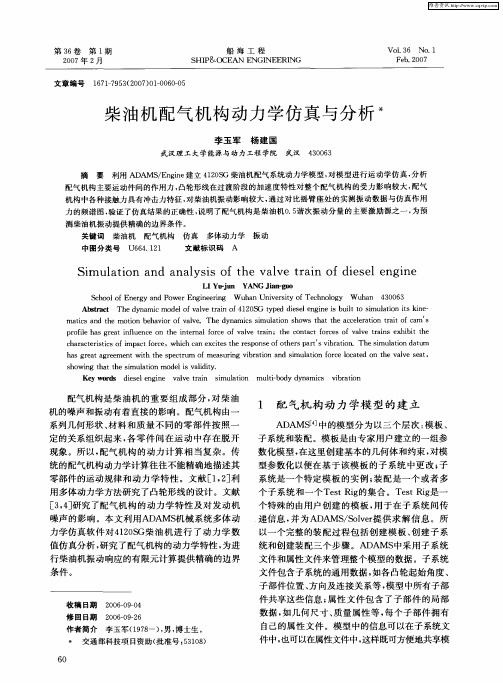
Ke r s de e n i e v l e t an smu a i n mu t b d y a c v b a i n y wo d i s le g n a v r i i lt o l - o y d n mis i ir t o
柴 油 机 配 气 机构 动力 学仿 真 与 分 析 *
李玉 军 杨建 国
武汉 4 0 6 303 武汉理 工大学能源与动力工程 学院 摘 要
利用 A DAMS E gn 建立 4 2 S / n ie 10 G柴油 机配气系统动力学模型 , 对模 型进 行运动学 仿真 , 分析
配气 机构主要运动件间 的作用力 , 凸轮形线在过渡 阶段 的加速度特 性对整个 配气机构 的受力影 响较大 , 配气 机构 中各种接触力具有 冲击 力特 征 , 对柴油机振 动影 响较大 , 通过对 比摇臂座处 的实测振 动数据与 仿真作用
力的频谱 图, 验证了仿真结果 的正确性 , 明了配气机构 是柴油机 0 5 次振动分量 的主要激 励源之一 , 说 .谐 为预
测柴油机振动 提供 精确的边界条件 。 关键 词 柴油机
中图分类号
配气机构
仿真
多体 动力学
A
振动
U6 4 1 1 6. 2
文献标识码
Si u a i n a na y i ft e vav r i fdis 1e g n m l to nd a l ss o h l e t an o e e n i e
维普资讯
第3卷 第 1 6 期 20 年 2 07 月
动力学配气机构试验分析仿真与优化

动力学配气机构试验分析仿真与优化【摘要】目前机械系统设计分析的有力手段是多体系统动力学运用到机械的仿真中,本文针对某发动机配气机构系统,建立参数化的多体系统动力学模型,以多体系统动力学分析软件ADAMS为仿真平台。
采用试验设计的方法进行动力学仿真试验,分析出对响应影响显著的因子,运用回归分析得到响应变量关于试验因子的响应面方程,以此作为优化目标进行寻优计算,实现了对配气机构的设计参数和局部凸轮型线的动力学优化。
【关键词】动力学;配气机构;参数;仿真与优化1.引言配气机构作为内燃机的重要组成部分,四冲程的内燃机都采用气门式配气构机构。
由于配气机构的设计又在很大程度上影响内燃机的动力性与可靠性,其性能好坏对内燃机的性能指标有着重要的影响。
配气机构系统动力学模型有很多种。
一般来说,低速系统配气机构,转速低、载荷小,进行运动学分析即可。
对于中速系统,转速和载荷较高,气门偏离理论运动规律较大,并出现构件在润滑、磨损、强度等方面问题,因此需要用动力学模型研究其动力学特性。
对于高速系统,转速和载荷很大,气门将显著偏离理论运动规律,并受到机构在开始和落座时的冲击反跳,在工作阶段的飞脱,以及润滑、磨损、强度等多方面问题制约,必须用动力学模型研究其特性,并尽可能考虑非线性因素的影响。
目前运用比较多的配气机构动力学模型有离散质量模型—包括单质量模型,多质量模型以及多体动力学模型,有限元模型等。
随着计算机技术、传感器技术以及信号处理相关方法和技术的发展,配气机构的实验也能更精确地反映配气机构工作情况下的实际情况和得到更精确的动力学数据。
实验的目的不仅仅是得到配气机构的动力特征,也可以通过实验得到模型的原始数据。
由于配气机构组件在高速运动过程中表现出一定的柔性特征,部分组件产生一定的变形,导致组件的实际运动规律偏离凸轮型线。
而配气机构动力学特性实验可以测量机构组件的实际运动规律,分析配气机构参数对组件实际运动规律的影响。
常用机构优化设计及仿真系统的研发
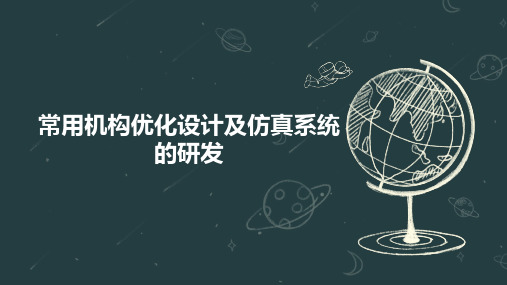
联合仿真及优化设计
1、数学模型的建立
根据曲柄摇杆扑翼机构的运动特征和动力学特征,我们建立了数学模型。该模 型包括运动学模型和动力学模型两个部分。其中,运动学模型描述了机构的运 动规律,而动力学模型则描述了机构在运动过程中所受到的各种力的作用。
常用机构优化设计及仿真系统 的研发
目录
01 一、机构优化设计
02 二、仿真系统研发
03 三、常用机构优化设 计及仿真系统的应用
04 四、机构优化设计及 仿真系统的未来发展
05 参考内容
在工程设计和制造领域,机构优化设计及仿真系统的研发具有重要的实际意义。 机构优化设计是提高机械设备效率、精度和可靠性的关键,而仿真系统的应用 则可以帮助我们在设计阶段预测和解决潜在的问题,降低试验成本,缩短产品 开发周期。本次演示将从机构优化设计、仿真系统研发、应用和未来发展等方 面进行详细介绍。
3)采用优化算法对曲柄摇杆扑翼机构进行优化设计,提高其性能指标; 4)对比分析优化前后的曲柄摇杆扑翼机构性能指标,验证优化设计的有效性。
研究方法
1)根据曲柄摇杆扑翼机构的运动特征和动力学特征,建立数学模型;
2)利用计算机仿真技术,对曲柄摇杆扑翼机构进行联合仿真,包括运动学仿 真和动力学仿真;
3)采用优化算法,如遗传算法、粒子群算法等,对曲柄摇杆扑翼机构进行优 化设计;
2、现代优化方法:如遗传算法、粒子群算法、模拟退火算法等,通过模拟自 然界的进化过程或物理现象,寻找最优解。
3、多学科优化方法:将多个学科领域的知识集成在一起,综合考虑多方面的 性能要求,进行优化设计。
二、仿真系统研发
燃气轮机控制系统的设计与优化

燃气轮机控制系统的设计与优化燃气轮机是一种重要的动力装置,广泛应用于发电、航空等领域。
燃气轮机控制系统的设计与优化是提高其性能和效率的关键。
本文将从控制系统的需求分析、设计原理与方法、系统优化等方面进行论述。
一、需求分析在设计燃气轮机控制系统之前,首先需要对系统的需求进行分析。
燃气轮机控制系统需要满足以下基本需求:1. 系统稳定性:控制系统应能够保持燃气轮机的稳定运行,确保其输出功率的稳定性。
2. 响应速度:控制系统应具备快速响应的能力,能够实时调整燃气轮机的输出功率,以适应外部负荷的变化。
3. 控制精度:控制系统应能够精确控制燃气轮机的输出功率,以满足设定的要求。
4. 安全性:控制系统应具备多重保护机制,及时检测和处理燃气轮机的故障状态,保证系统的安全运行。
基于以上需求,设计和优化燃气轮机控制系统需要考虑以下几个方面。
二、设计原理与方法1. 控制策略选择:燃气轮机控制系统可以采用PID控制器、模糊控制、神经网络控制等不同控制策略。
根据燃气轮机的特性和应用需求,选择合适的控制策略。
2. 信号采集与处理:通过传感器采集燃气轮机的运行状态、环境参数等信息,并进行信号处理和滤波,以获得准确可靠的系统反馈信息。
3. 控制算法设计:根据控制策略和系统需求,设计控制算法,实现对燃气轮机输出功率的调节和控制。
常用的算法包括PID控制算法、模糊控制算法、神经网络控制算法等。
4. 控制系统实现:将设计的控制算法实施到实际的硬件平台上,通过控制器对燃气轮机进行控制。
同时,需要实现对燃气轮机其他相关部件的控制,如燃料供给系统、鼓风系统等。
三、系统优化对燃气轮机控制系统进行优化能够提高系统的性能和效率,实现更好的控制效果。
以下是一些常用的系统优化方法:1. 参数整定优化:通过调整控制系统的参数,如PID控制器的比例、积分、微分系数等,优化控制算法的性能。
2. 系统动态响应优化:通过改变控制算法中的控制参数和结构,优化系统的动态响应速度和稳定性。
汽车发动机配气机构设计思路分析

汽车发动机配气机构设计思路分析摘要:随着我国汽车工业的不断发展,汽车在使用过程中可能遇到的问题种类也在不断增加。
本文重点描述了汽车发动机配气机构的故障,并简要列举了处理和分析方法。
关键词:发动机;配气机构;故障;处理分析;积炭;气门间隙0引言随着汽车数量的不断增加,人们对汽车的质量提出了更高的要求。
配气机构在汽车零部件中非常重要。
配气机构主要通过控制进气量来影响发动机功率。
随着汽车自身油路、温度环境和压力环境的日益复杂,配气机构的安全系数面临着巨大的挑战。
配气机构主要是按照一定的时限自动开启和关闭各缸的进排气门。
空气通过进气阀提供可燃气体混合物,燃烧做功后形成的废气从排气阀排出,实现气缸通风。
在实际使用中,由于多种因素的影响,汽车的配气机构变得脆弱,精密的配气机构受到影响后非常容易发生故障,其故障将直接影响发动机的性能。
1汽车发动机配气机构对发动机性能的影响为了让发动机获得更好的性能,就需要发动机有更高的充电效率。
为了提高发动机的充气效率,有必要降低进气通道的阻力。
通过扩大空气过滤器,加厚化油器,拉直进气管,并将其增加到进气阀的直径。
增大进气阀的直径,使进气口平直,可以大大提高充气效率。
随着汽车工业的发展,近年来双顶置凸轮轴四气门配气机构受到广泛关注,大大提高了汽车发动机的性能。
这种气门机构可以大大增加进气的有效流通面积,从而提高充气效率。
阀门的流通面积与进气口的直径成正比,而与阀头的面积不成正比。
对于每个气缸都有进气门和排气门的双气门发动机,当直径增加时,上限是进气门和排气门的直径之和低于气缸直径,因此不可能在尺寸上安装更大的气门。
在四气门发动机中,两个进气门直径之和可能大于两个气门的一个进气门直径。
当采用每缸4个气门的结构时,每个排气门的直径越小,气门受热面积就会越小,其机械负荷和热负荷也会相应降低,从而改善配气机构的动态性能,提高转速。
采用DOHC四气门机构可以有效提高发动机的充气效率、压缩比和功率。
燃气轮机系统的建模与仿真

燃气轮机系统的建模与仿真燃气轮机是一种高效可靠的能源转换设备,可以广泛应用于发电、飞行、航海等领域。
燃气轮机系统由多个部件组成,包括压气机、燃烧室、涡轮机等。
为了更好地设计、优化和控制燃气轮机系统,建立燃气轮机系统的模型并进行仿真是非常重要的。
一、燃气轮机系统的建模方法1. 基于物理学原理的建模方法这种建模方法基于燃气轮机系统的物理特性,通过对控制方程和能量平衡方程的建立,得出燃气轮机系统的数学模型。
这种方法的优点是能够准确地反映燃气轮机系统的物理特性,但是需要大量的计算和模型参数的确定,适用于研究燃气轮机系统的基本特性。
2. 基于统计方法的建模方法这种建模方法基于大量的实验数据,通过对实验数据的分析和处理,建立燃气轮机系统的统计模型。
这种方法的优点是不需要精确的物理特性和模型参数,可以通过实验数据进行建模,但是需要大量的实验数据和数据分析技能。
3. 基于神经网络的建模方法这种建模方法基于神经网络的模式识别能力,通过对燃气轮机系统的输入和输出数据进行学习,建立燃气轮机系统的神经网络模型。
这种方法的优点是能够学习系统的复杂非线性关系,但是需要大量的学习数据和神经网络模型的优化。
二、燃气轮机系统的仿真方法1. 基于模型的仿真方法这种仿真方法基于燃气轮机系统的数学模型,通过数值模拟的方法,进行燃气轮机系统的仿真。
这种方法的优点是可以对燃气轮机系统进行全面的仿真和测试,但是需要精确的物理模型和大量的计算资源。
2. 基于实验数据的仿真方法这种仿真方法基于实验数据的统计模型,通过对实验数据的模拟和处理,进行燃气轮机系统的仿真。
这种方法的优点是可以通过实验数据进行仿真,但是需要大量的实验数据和数据分析技能。
3. 基于混合方法的仿真方法这种仿真方法综合使用基于模型和基于实验数据的方法,通过建立精确的数学模型和处理实验数据,进行燃气轮机系统的仿真。
这种方法的优点是综合了两种方法的优点,可以比较准确地进行燃气轮机系统的仿真。
气动系统动力学建模与仿真分析
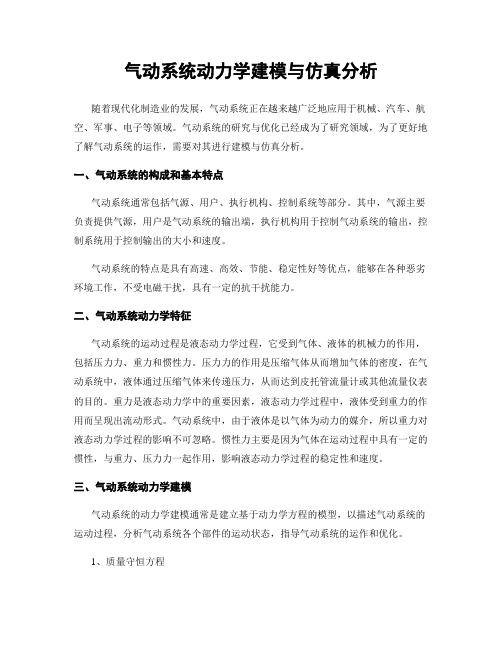
气动系统动力学建模与仿真分析随着现代化制造业的发展,气动系统正在越来越广泛地应用于机械、汽车、航空、军事、电子等领域。
气动系统的研究与优化已经成为了研究领域,为了更好地了解气动系统的运作,需要对其进行建模与仿真分析。
一、气动系统的构成和基本特点气动系统通常包括气源、用户、执行机构、控制系统等部分。
其中,气源主要负责提供气源,用户是气动系统的输出端,执行机构用于控制气动系统的输出,控制系统用于控制输出的大小和速度。
气动系统的特点是具有高速、高效、节能、稳定性好等优点,能够在各种恶劣环境工作,不受电磁干扰,具有一定的抗干扰能力。
二、气动系统动力学特征气动系统的运动过程是液态动力学过程,它受到气体、液体的机械力的作用,包括压力力、重力和惯性力。
压力力的作用是压缩气体从而增加气体的密度,在气动系统中,液体通过压缩气体来传递压力,从而达到皮托管流量计或其他流量仪表的目的。
重力是液态动力学中的重要因素,液态动力学过程中,液体受到重力的作用而呈现出流动形式。
气动系统中,由于液体是以气体为动力的媒介,所以重力对液态动力学过程的影响不可忽略。
惯性力主要是因为气体在运动过程中具有一定的惯性,与重力、压力力一起作用,影响液态动力学过程的稳定性和速度。
三、气动系统动力学建模气动系统的动力学建模通常是建立基于动力学方程的模型,以描述气动系统的运动过程,分析气动系统各个部件的运动状态,指导气动系统的运作和优化。
1、质量守恒方程气动系统的质量守恒方程是表示气体在气动系统内流动的质量守恒方程,可以用来描述气体的流量变化情况。
守恒方程可以写成下列形式:其中,ρ表示气体密度,u表示气体速度,S表示面积,t表示时间,Q表示面积S内的质量流量。
2、动量守恒方程气动系统的动量守恒方程描述了各个部分在气流过程中的速度和压力变化情况。
动量守恒方程可以写成下列形式:其中,ρ表示气体密度,u表示气体速度,p表示气体压力,F表示面积,n表示或其他物质量,g表示重力加速度,t表示时间。
基于ADAMS的柴油机配气机构动力学仿真分析

基 于 AD AMS的柴 油机 配 气机 构 动力 学仿真 分析
陈仲 海 ,魏 玉 娜 , 白峭 峰
( 中北 大 学 机 械 工 程 与 自动化 学院 , 山西 太 原 0 3 0 0 5 1 )
摘 要 :利 用 P r o / E n g i n e e r 和 AD AMS软 件 建 立 某 柴 油 机 配 气 机 构 系 统 的 动 力 学 模 型 , 并对 其进 行 多 体 动 力 学 仿 真分 析 ,得 到 了配 气机 构 进 气 门的运 动规 律 和 关 键 运 动 件 间 的 作 用 力 , 以及 不 同 转速 对 气 门的 影 响 , 为
移 动 副 气 门垫 块 与气 门杆 平 面 一平 面 i 约 束
图 1 配 气 机构 多刚 体 动 力学 模 型
2 . 1 进 气 门运 动 规 律
图2 、 图 3和 图 4分别为 3种转 速 下进 气 门位移 、 速 度和加 速度 曲线 。由图 2 、 图 3和 图 4可 见 , 随着 发 动机转 速的提 高 , 气 门的速度不 断增 大 , 进气 门在 开启 与关闭 时加速度 冲击 较 大 , 这 与 实 际现 象 吻合 。 当发 动机 转 速 为 2 i 0 0 r / mi n时 , 进 气 门 的 落 座 速 度 为 0 . 1 8 m/ s ; 当发动 机转 速为 2 3 1 0 r / mi n时 , 进 气 门的 落座速度 为 0 . 2 1 m/ s ; 当发 动机 转 速 为 2 5 2 0 r / mi n
作 者 简 介 : 陈仲 海 ( 1 9 8 8 一 ) ,男 , 山西 运 城人 .在 凑硕 士研 究生 , 主要 从 事 发动 机 总 体 技 术及 结 构 动 态 设计 方 面 的学 习 与研 究 。
- 1、下载文档前请自行甄别文档内容的完整性,平台不提供额外的编辑、内容补充、找答案等附加服务。
- 2、"仅部分预览"的文档,不可在线预览部分如存在完整性等问题,可反馈申请退款(可完整预览的文档不适用该条件!)。
- 3、如文档侵犯您的权益,请联系客服反馈,我们会尽快为您处理(人工客服工作时间:9:00-18:30)。
配气机构整体系统仿真及优化
康黎云司庆九
(重庆长安集团汽车工程研究院CAE所)
摘要:通过A VL EXCITE Timing Drive的仿真,对某机型的配气机构进行动力学计算以了解存在的问题和优化方向。
拟定重新设计凸轮型线和调整弹簧参数的优化措施,并用EXCITE Timing Drive进行对比计算,结果表明凸轮型线的设计和弹簧参数的更改达到了优化目的。
关键词:配气机构;动力学;凸轮型线;气门弹簧
主要软件:A VL EXCITE Timing Drive;MSC/NASTRAN
1. 前言
某发动机的配气机构采用四气门单顶置凸轮轴摇臂驱动,其中进、排气侧分别为两同形式的指形从动件摇臂。
摇臂驱动形式的配气机构刚度一般比挺柱直接驱动的配气机构要弱,相应其动力性也要差些。
现实的问题是:如何从优化配气机构的角度出发,在不提高发动机转速的情况下增加该发动机的功率,同时还必须使配气机构的动力性也满足设计要求,如不出现飞脱、反跳及弹簧并圈等问题。
2. 分析过程
2.1 总体流程
为解决问题,制订以下分析流程,如图1所示:
图1 配气机构分析及优化流程图
2.2 优化前仿真分析
机构的主要全局参数如表1所示:
表1 配气机构主要技术参数
进气侧排气侧
15.5mm
基圆半径 15.5mm
气门正时 466°(曲轴转角) 258°(曲轴转角)
气门包角(含缓冲段) 170° 175°
气门倾角 16° 20°
0.25mm
气门间隙 0.15mm
弹簧预紧力 114N 工作段弹簧刚度 29N/mm 建立整个阀系的EXCITE Timing Drive模型:①. 从凸轮轴前端往后端看,凸轮的布置是排气门、两个进气门、排气门的形式;②. 由于发动机的点火顺序是1-3-4-2,所以对应缸的阀系相位要依次滞后90°;③. 忽略皮带传动对阀系的影响,而直接将转速加载到凸轮轴的最前段的SHPU单元上。
整个模型如图2所示:
图2 阀系模型
以下为发动机优化前6000rpm下的动力学计算结果(图3~图6所示),从各曲线图可以看出,该配气机构在高转速下出现反跳、飞脱和并圈,因此,有必要对该套系统进行优化。
优化的措施主要有以下几点:
(1) 重新设计进、排气凸轮型线,以避免飞脱和反跳的产生。
对于摇臂驱动的凸轮型线,使
用分段加速度函数(ISAC)方式设计型线是最为理想的。
(2) 加强摇臂刚度,从而提高整个系统的刚度。
(3) 优化气门弹簧参数,增加工作段长度及调节弹簧刚度,以消除并圈。
(4) 调节气门正时,通过GT-Power或Boost等软件工具进行计算,以检验功率是否提高。
图3 排气门升程
图4 进气门升程
图5 进气侧弹簧力曲线
图6 作用在凸轮上接触应力
2.3 具体优化实施
(1) 对于进、排气凸轮型线都重新设计,设计目的:在满足动力性要求的前提下,尽可能地
增大丰满度,以提高充气效率。
图7所示为进气凸轮的原始型线与新型线的对比,新型线与旧型线在局部升程最大差接近1.2mm,由于凸轮轴铸造件的余量有2mm,因此这种设计更改不存在增加重新开模的成本。
图7 进气凸轮新、旧型线对比
(2) 对摇臂结构的优化以提高其刚度。
摇臂结构的更改至少要满足配气机构各零件的空间布
置不会发生干涉,而且还要考虑到是否需要重新设计模具以及质量是否增加等等因素。
图8是排气侧摇臂设计前后的示意图。
更改后的摇臂质量增加,但刚度几乎没有多少提高,没有达到设计意愿,因此建议保持摇臂原有结构形式。
图8 排气侧摇臂更改前后示意图
(3) 气门弹簧参数的优化,包括弹簧预紧力、刚度、工作段长度、簧丝直径等参数都可以适
当调节,以满足动力性要求。
对消除弹簧并圈最有效的措施是增加弹簧的工作段长度,
但如果保持其他参数不变而增加工作段长度,那么气门锁夹及气门长度等也会受影响。
因此,减小簧丝直径是一个值得考虑的办法。
经过弹簧验证计算,将原来的直径3.1mm 减小至3.0mm,弹簧中径也相应减小,其他参数基本不变,从而达到增加弹簧工作段长度的目的,可以消除并圈。
(4) 气门正时调节对功率的影响在本文中就不赘述了。
2.3 优化后仿真分析
图9~图12为优化后的配气机构动力学计算结果:
图9 进气门升程
图10 排气门升程
图11 进气侧弹簧力曲线
图12 作用在凸轮上的接触应力
3. 结语
凸轮型线的重新设计成功地消除了飞脱和反跳的产生,弹簧参数的优化也解决了并圈的问题。
从仿真角度来说,该机构的优化已经达到了初始目的,但还需要进行发动机性能验算,确保优化后发动机的性能没有下降,如有可能应结合试验来共同检验优化效果。
参考文献
[1] 尚汉冀,内燃机配气凸轮机构-设计与计算,复旦大学出版社,1988
[2] AVL EXCITE Timing Drive用户培训手册。