鞋子样品制作标准流程
鞋样设计的工作程序及阶段性要求

分析鞋样设计的工作程序及阶段性要求一、构思阶段1、要求设计者必须具备一定的制鞋专业知识,包括楦、底、跟、饰、材、人体工程学、力学、脚型规律、楦型规律、制鞋工艺等。
2、要求设计者必须了解各种鞋靴类的基本特点及用途。
3、要求设计者必须了解时代社会背景、经济基础、工业条件、人类生活水平、文明程度及各阶层对物质、精神方面的需求标准。
4、要求设计者必须掌握鞋服流行趋势,必须把握适时社会的意识流、时尚流、色彩流。
5、要求设计者必须具备一定的产品策划能力和市场行销策划能力。
6、要求设计者的设计能力必须与企业现实生产能力相结合,必须与社会认识相结合,必须与市场购买能力相结合,必须与现实相结合。
7、要求设计者的设计思想必须顺应国情民意。
8、要求设计者的设计目的必须服务于人类的工作、生活和健康。
点评:鞋样设计工作的构思阶段是体现设计能力和构思能力的阶段。
是体现设计师自我价值的阶段,是对设计师的综合素质的考核阶段。
设计者是否具备设计能力在此得到验证。
二、确定思路阶段1、对于设计者来说,无论能力大小,在构思阶段的思路可能不止一条。
但必须以最大的努力来判断出其中一条最佳思路来确定设计目标。
2、要求设计者必须具备搜集各种信息情报能力,必须具备处理、整合、利用有效信息和情报的能力。
确保设计资源不被浪费。
3、要求设计者必须具备对市场的分析能力和判别能力。
力求设计思路和设计目标的正确性。
4、要求设计者必须对自己的设计能力、设计行为给予肯定,坚信设计理念,树立信心,大胆果断地作出决定。
点评:正确的思路确定是决定设计作品实用性价值的关键步骤。
在这一阶段设计者的设计能力、构思能力、策划能力、综合素质能够得以充分的体现。
在大胆果断地作出正确决定的那一刹那间就已经同时决定了设计者的存在价值、作品价值、作品的实用价值、市场效益和连锁效益等。
设计者是否可以称得上是是为真正的设计师,在此阶段可以得到验证。
三、表现与展示阶段1、要求设计者必须具备一定的鞋样设计基础、样板基础、各种鞋类或单项鞋类设计要素知识、美学知识。
制鞋的工艺流程

制鞋的工艺流程制鞋的工艺流程制鞋是一项复杂的工艺,需要经过多道工序才能完成,下面我将介绍一下制鞋的主要工艺流程。
首先,制鞋的第一步是设计。
设计师会根据时尚潮流和市场需求,设计出款式独特、符合人体工学原理的鞋子。
接下来是制作鞋样。
根据设计师的设计图纸,制鞋师傅会按照比例将鞋样放大或缩小,然后用木板或泡沫等材料制作出鞋样。
然后是制作鞋楦,鞋楦是制鞋的重要工具,它影响着鞋子的舒适度和外观。
制作鞋楦需要一些木材或塑料等材料,制鞋师傅会根据设计师提供的尺寸和要求制作出鞋楦。
接下来是裁剪材料。
制鞋需要不同材质的面料、皮革或合成革等材料,制作鞋面和鞋底。
裁剪工人会根据鞋样的尺寸,将面料或皮革等材料按照设计要求裁剪成各个部分。
然后是上机。
上机是将裁剪好的鞋面和鞋底通过缝纫机缝合在一起。
这个过程需要熟练的缝纫工人和高精度的缝纫机。
他们会根据设计要求,将鞋面和鞋底的各个部分缝合在一起。
缝合好的鞋子需要经过打平、固定、贴衬等工序。
这些工序通常需要运用热压机、水泡机、蒸汽等设备,使鞋子的形状更加美观。
然后是鞋底的制作。
鞋底通常由橡胶、EVA等材料制作而成。
制鞋师傅会根据设计要求,经过模具成型、注模、烘烤等工艺,制作出符合设计要求的鞋底。
接下来是鞋底的胶接。
将制作好的鞋底用胶水或热熔胶粘合到鞋面上,使鞋底与鞋面紧密结合。
最后的工序是修饰和检验。
这个阶段的工人会对鞋子进行修饰,如刷漆、打磨等,使鞋子的表现更加完美。
然后,质检工人会对鞋子进行检验,确保鞋子的质量合格,并将合格的鞋子进行包装。
以上就是制鞋的主要工艺流程。
当然,鞋子的生产过程还可能包括鞋垫、鞋垫、鞋面绣花等特殊工艺,以及工艺的细节可能因不同鞋款而有所不同。
制鞋的工艺需要经过熟练的技术和经验,确保最终生产出的鞋子质量优良、符合人们的需求。
鞋子鞋样结构设计样板制作步骤及名词解析

鞋⼦鞋样结构设计样板制作步骤及名词解析⼀、鞋靴样板制作步骤制作鞋靴样板主要包括四套样板:半⾯板、做帮样板、划料样板和⾥样板。
另外有些鞋款还需要制作组合样板、衬布样板。
(⼀)、半⾯板从楦侧⾯揭下画有款式的美纹纸,并展平所得到的侧⾯样板称为半⾯板。
其楦侧⾯展平过程指的是多向弯曲的楦表⾯在外⼒的作⽤下,通过空间⾓的变化被展成⼀个形状相似、⼤⼩相近的展平⾯。
(⼆)、组合样板组合样板是由半⾯板制作⽽成的,其主要作⽤是帮助制作其它样板和帮⾯的精确制作。
(三)、做帮样板做帮样板是鞋样板中的核⼼样板,是制取划料样板和⾥样板的基准样板。
是在⾯部车间中⽤于镶接、折边、标画定针点等操作的样板。
在经验设计时,常⽤制取做帮样的⽅法有:⽐楦剪样法;贴楦剪样法;分解法;拷贝纸临摹法;扎点法。
* 做帮样板轮廓=部件设计轮廓+绷帮量+定针点+跷度+合缝量(需要合缝的位置)+翻缝量(需要翻缝的位置)1、部件设计轮廓⽆论是在设计图上,还是在楦⾯上,每个部件都应有⼀个完整的轮廓,即部件的设计轮廓。
2、绷帮量(绷帮做法)凡是与底⼝相连的部件,在制取做帮样板时都应加上相应的绷帮量,包括内、外腰底⼝上的区别(在内腰底⼝上打上⽛剪“∨”)。
如果内、外腰样板有区别时,每⼀单独部件上都应该在内腰⼀侧作出标记。
3、合缝量采⽤合缝时,⼀般留出1.5mm--2mm的合缝量(后跟处的合缝量⼀般不另外加出,因材料的延伸性能可以将其抵消,若遇材料较厚或伸缩性能较差将其抵消不掉可适当放出)。
4、翻缝量在鞋⼝、鞋⾆等部位翻缝时,要留出2mm--4mm的翻缝量。
如果翻缝部位要填充发泡材料,要留出3mm--5mm的翻缝量。
5、定针点定针点是指帮部件进⾏加⼯时的位置标记。
做帮样板上的定针点⼀般⽤直径1mm的⼩钺⼑打孔。
定针点包括组合点,中点标记、鞋眼位置等。
压茬标记、假线位置标记可⽤割线槽⽅式来表现,有了定针点,线槽位置线,做出的样品才规范。
6、跷度跷度是样板复原的条件,也是取样板时不可缺少的环节。
制作鞋的工艺流程介绍

制作鞋的工艺流程介绍一、原辅材料仓库管理1、每日原辅材料进出库须做好材料帐及库存帐,并用微机管理;2、进料和发料须专人管理,以免出错;3、进料时须有质检人员在场,检验品质是否正确,颜色是否正确。
二、裁断车间管理1、领料须由专人负责,由组长统一分配给员工;2、真皮类裁切时,因只能单层裁切,用GSB-2C液压摆臂式下料机或XCLP2-250液压平面下料机较好;3、裁切尼龙布、特多龙布、帆布及较薄PVC革时,因材料较软,同时可一次多层裁切,故应用XCLP2-250液压平面下料机或XCLL2-250液压龙门下料机。
4、裁切中底板时,因材料较硬,同时可一次多层裁切,应用XCLP2-250液压平面下料机或XCLL2-250液压龙门下料机。
5、任何裁出的部件、特别是有色皮料、布类应同时做质检、配色、配双及数量清点等工作,以免到针车部门时做重复工作;6、裁切主管人员应辅导员工做好机器及刀模的日常保养工作;7、管理人员须随时巡视员工使用斩是否按指令单的刀号操作并教导员工如何自我检验。
8、教导员工对材料的认识,须适材适用,并注意斩刀排列方式,减少不必要的材料浪费。
三、调配中心管理1、调配中心依据订单情况,将裁切好的部件排列整齐,等待加工;2、已裁切好的部件如需印刷、削皮、贴内里、烫印等,均由调配中心负责;3、加工好的材料交付给中仓备料组,由中仓备料组发料至针车车间加工。
4、裁切好的部件如中底板、鞋垫等,如果不需要特别车缝加工的,可在完成必要处理后送半成品仓库5、在调配中心,待所有部件完成后,一定要将鞋面所有部件质量及统计数字妥善整理,准备交付给针车车间;四、针车车间管理1、针车车间的车帮及做帮的工艺流程和员工配置,依据鞋面设计的不同而变化,一般一条针车流水线,如果每8小时能生产1500双时,须各种针车约70-80台,手工人员约10-15人,共计80-95人;2、车缝时必须注意车线边距,针距是否控制良好,与要求的标准是否相符;3、车缝时必须注意鞋面部件上各记号点的正确性,如车缝时未按正确的记号,鞋面完成后将会不正,造成夹帮困难,影响成品鞋的品质。
鞋样板制作

后片为10mm搭位) ➢ 15mm以下(不含15mm)的条带,特殊搭位放8mm,15mm以
上的放10mm. ➢ 浅口门的羊皮夹里一律在外脚断帮做8mm特殊搭位,且搭位一律
单鞋
(7) 单鞋夹里做法: ➢ 反里夹里帮脚分三段收:前段收6mm,中间收8mm,
后段收10mm; ➢ 口门转弯处顺修2mm,并做三个与帮面车线的对应点,
以免反里起皱和夹里车歪; ➢ 其它夹里帮脚分两段收;前段收6mm,后段收8mm,
后缝上口以净线收0.5mm,以下净线收3.5mm,从 0.5mm处拉直线至后跟最凸处交叉,口门放6mm铲里 量,搭位放5mm。 ➢ 大身夹里是羊皮的需在外脚处段开(浅口鞋)做特殊 搭位,放8 mm并刻槽画线; ➢ 布里的后跟里做光,前片做8mm搭位,反里大身口门 夹里多放2mm余量;
单鞋
(12) 凡是过大机捏皱的,过大机位置需刻槽画线,并按 槽位线出相应过大机纸样
15mm以上的放10mm. ➢ 浅口门的羊皮夹里一律在外脚断帮做8mm特殊搭位,
且搭位一律为后搭前(即前片断带做8mm搭位,后片 为光) ➢ 凡是口门位的镶边条,滚边条,包口条有断帮做特殊 搭位的,其搭位一律为后搭前,其特殊搭位放8mm。 (11) 合缝的做法: ➢ 单鞋腰档合缝一律合3mm; ➢ 后缝有尾皮的一律放1.5mm,没尾皮的后缝一律放 3mm合缝。(深口门的加方形尾皮;浅口门的加半圆 形尾皮)
反里以及特殊反里、在开料样不收不放); ➢ 合逢以边线放3 mm; ➢ 皮面衬布样距帮脚收5 mm,布面、牛二层、PU、裂
面牛与帮脚平齐; ➢ 车人字线有固定装饰,衬布不收不放,无固定装饰的
鞋子样品成型制作流程
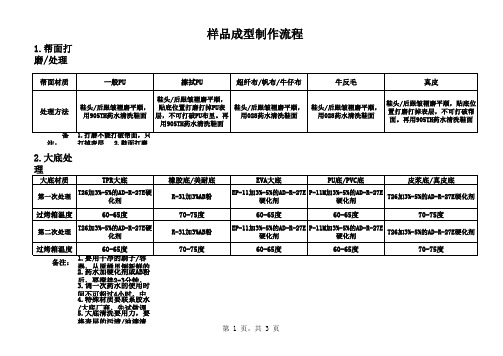
1.帮面打磨/处理备注:1.打磨不能打破帮面,只打掉表层 2.鞋面打磨的灰尘要清理干净 3.鞋面和中底粘着要牢固,不能开口备注: 1.要用干净的刷子/容器,从原桶里倒新鲜的药水2.药水加硬化剂或AB粉后,要搅拌2-3分钟,充分溶解后再使用3.调一次药水的使用时间不可超过4小时,中间停止使用时,要用PU膜盖紧封存,以免表层结膜,挥发失效。
4.特殊材质要联系胶水/大底厂商,先试做调好药水再做样品5.大底清洗要用力,要将表层的污渍/油漆清洗干净6.大底和沿条是两种材质的时候,要分开洗两种药水,沿条药水不可洗到大底上,大底药水也不可洗到沿条上,要用小刷子仔细清洗备注:1.要用干净的刷子/容器,从原桶里倒新鲜的胶水2.胶水加硬化剂后,要搅拌3-5分钟,充分溶解后再使用3.调一次胶水的使用时间不可超过4小时,中间停止使用时,要用PU膜盖紧封存,以免表层结膜,挥发失效。
4.刷胶要均匀到位,不可欠胶/溢胶,也不能积胶/死胶5.过烤箱鞋面和大底不可变色,缩水,起泡,大底的组合位置不能烤开4.贴底1.按照胶水线贴底,切记不可开胶,贴底要平顺,鞋子要正不能前后踢2.用正确的压底模压底,(压力22-25KG,时间7-8秒),要有二次压3.冷冻时间要够4.按照鞋跟形状和制作说明打钉5.做号的鞋子放置48小时再做拉力和曲折/剥离测试。
重点要求:1.所有步骤严格/仔细的操作,按标准,按要求作业,不能偷工减料2.所有化学品不能违反客人的环保规定。
例如:不能含笨,不能含铅等3.在没有把握保证拉力的情况下,先用一块面料贴在大底做测试,检验OK再做样品4.所有调配好的药水/胶水,要用塑料膜封好,防止结膜/挥发,要在4小时内用完5.同类材质也有性质差别,在拉力通不过的情况下,要及时与胶水厂商技术人员联系。
★ 6.底部人员要跟胶水厂技术人员学习,对不同材质的处理方法和实际操作经验,做详细记录/总结制表:夏 进2015/4/11。
鞋子生产制造流程
标准:严格、及时。
22、试做 要求:新款试做组长亲自操作1双,注意点位,印线、大小问题,并及时参加试做报告会,和其他部门主任达成共识,确认无误后才签字投产,如以后发现问题将追究责任。
带冲仔 革4层 皮1层
带针 革6层 皮1层
后方海绵 2.0CM以下 冲6层
鞋舌海绵 2.0CM以下 冲12层
冲裁管理规定
冲裁管理工作概述:
核对刀模,检验材料,安排生产,协调进度,现场控制,成本核算。
冲裁管理的重要性:发的溃裁管理,可以降低材料消耗,节约产品成本为企业的生产发展作出贡献。
冲裁作业标准
2.1 每次投产前先检查刀模是否变形、掉针,并熟悉排刀方法。
2.2 领料前先领到样品鞋,并和所领材料核对颜色、花纹、材质。
2.3 皮料存在以下问题应用记号笔画出,利用率太低应退回仓库处理,暗伤处给予剪开:
①刀伤②破洞③血筋④痧孔⑤鸡爪纹⑥毛绒过长⑦不透心⑧厚薄
2.4 作业前应调好机台压力深浅以防损坏发模。
2.5 作业时样料应注意接头色差、花纹、厚薄、宽窄是否一致,数量是否足够。
3、冲裁操作规定
3.1 每捆(反绒皮)都贴流水标。
10、车反领口内里 要求:领口内里的边缘与鞋口的边缘要对齐,车护眼重叠处要放松内里,车领口处要拉紧内里,车对接时边距3mm,边距一定要保持一致,不能大小针,塑料袋要车牢固。
标准:边缘平齐,不爆口,圆顺。
11、贴后衬 要求:将鞋身后方需贴后方衬处擦胶和后衬的贴合面擦胶,贴后衬从中间开始,后衬的中线与鞋向的的方拼缝线对齐粘贴,要贴紧,不留空隙。再将两侧平顺粘贴,后衬两侧边缘与后方的网脚边对齐(套楦),如攀帮鞋要留0.8mm(杂交鞋)。
制鞋工艺操作规程
工艺操作规程裁断车间一、手工划料1:按流程卡指定的货号、尺码和规格取划料样,分清内外脚,了解各部件的片数。
2:领取皮料后先检查与确认样是否相符。
包括厚度、表面色泽、手感、有无掉漆、皮炸、松面等现象。
3:按不同款式部件要求选皮分类,先算后用。
4:顶验皮疤,并用银笔作上记号(画圈)。
5:样板互套,寻求最佳互套方法,合理利用。
8:每张皮划完要点数、配双并在包脚底或其它部件适当部位贴上对码贴,不缺料、缺片。
9:头排部件要再次检查是否有皮疤漏验。
10:注意1里皮口条横流划料冲料(特殊除外)2小件按不同款要求划料3填写质量卡。
二、手工剪料1:使用合适剪刀,剪口要锋利。
2:需上手做包修毛边部位线外留有0.5-1mm,不需要上手做包修剪的部位,剪去划线,不得线内吃料,光滑流畅。
3:拥边、搭地按线剪(划走样除外)。
4:改划或吃料部件先看清后剪。
包脚地可以少量缺料(2-3mm)。
搭地部位可以少量吃料(小弯角2mm)。
拥边,毛边不得缺料。
5:里皮外搭接头要剪去线位。
6:按顺序剪料,分类摆放、点数。
7:缺片少块及时拼包,多余返回,不得代码混装。
8:整手鞋包(包括小件)要配齐,分类捆绑。
9:注意1发现疲疤等缺陷要返回划料2不同码不得混杂3对码贴脱落要及时补上4大皮冲料参照裁断和手工剪料。
三、验收点数1:验皮疤采用不同大小的铁球顶验。
A大件、硬件剪料或冲料后分部件按顺序顶验B 小件、软条形件应先划料剪成小块(多部件)顶验,后冲料或剪料。
C顶验皮疤不得将部件拉变形。
2:验花纹、粗细按对码贴,头排、机心、明口舌、横档等要逐双检验,后排可分片检验(花皮除外)3:不良品要及时拼包,对码、对双补齐。
4:分部件摆放点数,填写质量卡。
5:革鞋按部件分刀点数抽查。
6:注意1不良品处置要及时2不良品的处理要先控制后处置、追踪。
四、冲料1:机心、边排、后跟条直流排刀。
2:头排布没复EV A直流排刀,复EV A可以任意排刀,特殊除外。
3:后里、边里排横刀,口舌可任意排刀。
制鞋工艺流程与步骤详解
制鞋工艺流程与步骤详解鞋子是我们日常生活中不可或缺的一部分,而制鞋工艺则是鞋子产生的重要环节。
无论是手工制鞋还是机器制鞋,都需要经过一系列的步骤和流程。
本文将详细介绍制鞋的工艺流程和步骤。
1. 设计与样板制作制鞋的第一步是设计与样板制作。
设计师根据市场需求和流行趋势,设计出鞋子的款式和样式。
然后,制鞋师傅根据设计图纸制作出样板,以便后续的制作工作。
2. 材料准备在制鞋的过程中,材料的选择非常重要。
一般来说,鞋子的材料包括鞋面、鞋底、鞋垫、鞋垫等。
制鞋师傅会根据设计要求,选择合适的材料,并进行裁剪和准备。
3. 鞋面制作鞋面是鞋子的外部部分,它的制作需要经过多道工序。
首先,将选好的鞋面材料裁剪成合适的形状和尺寸。
然后,使用缝纫机或手工缝制,将鞋面的各个部分拼接在一起。
最后,进行整理和修饰,使鞋面看起来平整、美观。
4. 鞋底制作鞋底是鞋子的底部部分,它的制作也需要经过多个步骤。
首先,根据鞋子的款式和要求,选择合适的鞋底材料,如橡胶、塑料等。
然后,使用模具或机器将鞋底制作成所需的形状和尺寸。
最后,进行修整和打磨,使鞋底光滑、耐磨。
5. 鞋垫制作鞋垫是鞋子内部的一部分,它的制作也需要一定的工艺。
首先,选择合适的鞋垫材料,如海绵、皮革等。
然后,根据鞋子的尺寸和要求,裁剪出合适的鞋垫形状。
最后,将鞋垫缝制或粘贴到鞋子内部,使鞋子更加舒适。
6. 组装和装饰在完成鞋面、鞋底和鞋垫的制作后,就需要将它们组装在一起。
首先,将鞋面和鞋底进行粘合或缝制,使它们紧密结合。
然后,将鞋垫放置在鞋子内部,使鞋子更加舒适。
最后,根据设计要求,进行一些装饰工艺,如绣花、打孔等,使鞋子更加美观。
7. 质量检验和包装在制鞋的最后阶段,需要对鞋子进行质量检验。
制鞋师傅会仔细检查鞋子的每一个部分,确保没有瑕疵和缺陷。
如果发现问题,会及时进行修复和调整。
最后,将制作好的鞋子进行包装,以便运输和销售。
以上就是制鞋的工艺流程和步骤的详细介绍。
制鞋虽然看似简单,但其中涉及到的工艺和技术是非常复杂的。
鞋工艺流程
鞋工艺流程鞋工艺流程是制鞋过程中的重要环节,它关系到鞋子的品质和制作效率。
下面将详细介绍一下鞋工艺流程。
第一步,设计绘图。
鞋工艺流程的第一步是根据客户需求和市场需求进行设计绘图。
设计师首先根据鞋子的功能和定位确定鞋型设计,并绘制出初步的设计图。
然后通过手工或计算机辅助设计软件进行修改和精修,最终确定鞋子的设计。
第二步,打样。
在确定了设计图之后,需要制作鞋样。
首先,将设计图拆解成各个鞋部件的零件图,然后选择合适的材料进行切割和缝制,制作出初样。
然后根据初样的试穿效果进行修改,直到满足设计要求。
第三步,鞋面加工。
鞋面加工是指将各个鞋面部件经过裁剪、缝合和拼贴等工艺处理,制作成成品鞋面。
首先,根据鞋面零件图进行裁剪,然后使用缝纫机进行缝制,将各个鞋面部件拼接成整体鞋面。
最后,对鞋面进行粘合、搭接和压花等加工,使鞋面具有良好的质感和外观效果。
第四步,鞋底制作。
鞋底是鞋子的重要组成部分,影响着鞋子的舒适度和耐磨性。
制作鞋底的工艺通常包括橡胶挤压、橡胶注塑和大底压制等。
首先,根据鞋底的设计图制作模具,并选择合适的鞋底材料进行加工。
然后,将鞋底材料放入模具中,通过挤压、注塑或压制等工艺,使鞋底成型。
最后,对鞋底进行修整和磨光等处理,使其具备良好的质量和外观效果。
第五步,组装与检验。
鞋子的组装是将鞋面和鞋底进行结合,形成最终的成品。
首先,将鞋面和鞋底放置在组装台上,进行粘合或缝制等工艺处理。
然后,对鞋子进行整体修整和磨光,使其具备统一的外观效果。
最后,对鞋子进行质量检验,检查鞋子的粘合、缝制和外观等方面是否符合要求。
第六步,包装和发货。
在鞋子制作完成后,需要进行包装和发货。
首先,根据鞋子的类型和市场需求选择合适的包装方式,例如盒装、袋装或纸箱包装等。
然后将鞋子放入包装盒中,并添加相关的包装材料和标识。
最后,将包装好的鞋子进行静态检验和数目核对,并安排发货。
鞋工艺流程的每一个环节都需要精心操作和严格控制,以确保鞋子的质量和交货期。
- 1、下载文档前请自行甄别文档内容的完整性,平台不提供额外的编辑、内容补充、找答案等附加服务。
- 2、"仅部分预览"的文档,不可在线预览部分如存在完整性等问题,可反馈申请退款(可完整预览的文档不适用该条件!)。
- 3、如文档侵犯您的权益,请联系客服反馈,我们会尽快为您处理(人工客服工作时间:9:00-18:30)。
鞋子样品制做流程
一.备料
1.收到样品材料,先根据来料清单,核对数量/配件是否齐全,有没有在运输途中损坏或者丢
失,再和样鞋仔细对照。
2.材料颜色车线颜色加工方法
大底颜色拉链饰扣松紧织带
包边条喇叭布标印刷网板
3.有些特殊材料不能挤压,不能褶皱,如镜面PU/贴膜金属PU等,存放的时候要注意
二.开料
1. 样品材料要单独存放,不要和大货放在一起,以免用错材料。
2.有些特殊材料不能挤压,不能褶皱,如镜面PU/贴膜金属PU等,裁断的时候要注意
3. 样品材料都比较少,特别是有些特殊材料或小配件,材料可能只有一点点。
有些材料是样
品室用剩下的部分,材料会不规则。
裁断冲裁的时候不要浪费材料,不规则或有瑕疵的材料要单片冲裁,剩下的样品材料要按指令装好写上标签,方便下次再用。
(有瑕疵的材料也不能扔掉)
4. 样品没有刀模的时候要手工开料,手工开料的时候要先比对纸板和样鞋,不要用错纸板,
也不要用错材料
常用纸板名称
开料板和刀模纸板一样大的纸板,包含有折边位置,组合位置,反车位置
实板和折完边的部件一样大,不包含折边位置(比开料板少了一个折边位)
比板有些小部件会有比板,即不包含折边位置,也不包含组合和反车位置(像组合好鞋头剩下的鞋头中片大小,鞋身饰片大小,条带宽度比对等)组合板像凉鞋和有扣带组合的鞋子,一般都会有组合板,用来比对扣带组合的角度翘度板有需要定型的鞋子,用来比对部件定型后的翘度
5.做到鞋头要定型的鞋子,鞋头要先定一片看效果,再定剩下的鞋头。
如果是手工开料,要
先剪一片鞋头试定型效果,和翘度板比对,没有问题再开剩下的鞋头,避免有鞋头定型后太小,鞋子做不起来的现象。
三.针车
1.按照样鞋组合位/折边位削皮,削皮要顺薄,不能有痕迹。
港薄削10MM宽,顺薄到0.1MM
2.按照样鞋和样品单要求位置,印刷样品指令号,印刷中皮
3.先比对样鞋的车线颜色/粗细,再车在材料上看效果,再试一下车线打油和不打油的效果,
和样鞋一样再车样品
4.比对样鞋的针距/边距/行距,车线效果要同样鞋。
线路要调好,不能爆线,不能浮线跳针,
也不能太紧车皱鞋面,鞋面不能有线头,不能露针孔,车出来不能有车破的感觉
5.折边位置,先折一片看效果,比对样鞋看厚度是否一样,如果削皮不到位,退回削皮组重
削
6.反车位置,先反车一片看效果,比对样鞋看厚度是否一样,如果削皮不到位,退回削皮组
重削
7.中心点位要对齐,鞋面各部件的大小/高低要和样鞋一样,鞋面冲孔大小同样鞋。
8.有反口的鞋子,要注意反口的高低,内里外露的多少,都要同样鞋。
9.有泡棉的位置,泡棉厚度要同样鞋
10.双线/饰线的宽度要同样鞋
11.有后包拼车万能组合后跟条的结构,都要加后包布,后包布用(18P+单股)材料,后包
布要和鞋面刷胶贴死,不能空
12.锁口位置车线要调紧一点,锁口的高底,锁口车几针都要照样鞋
13.鞋眼不能有高低,要平顺
14.切边的位置不能毛边,不能露白,需要涂边的位置不能污染到鞋面其它地方
15.长纤,双“U”位补强,鞋口补强,等常用补强要贴到位,要贴牢固
16.扣子要打牢固,不能打开花,不能掉漆
17.扣带穿扣子的位置要加尼龙补强,增加拉力
18.刷胶贴前后港宝,港宝距帮脚8-9MM,港宝和鞋面弧度要吻合,不能贴空。
港宝和鞋面/
内里要粘死,不能脱层。
港宝要削10MM宽顺薄到0.1MM。
削太厚的港宝退给削皮组反工好再贴
19.鞋面做好,要整理干净,不能有画线/线头/胶水,内里要平顺,鞋面不能有皱褶
20.将制作中发现的问题记录在试做报告上面
21.样鞋,鞋面,中皮,样品单,操作说明书,试做报告一起交给针车主管看过,再交到品管
室。
由品管/师傅一起看过后再成型
常用标准
鞋面针距合缝针
距
面线边距
双线宽
度
男鞋9-9.5针12针1.2-1.5M
M
1.8MM
女鞋10-10.5
针
12针 1.2MM 1.8MM
实际针距,边距要看样鞋,一般车线越粗,针距越少
部位折边宽
度
反车宽
度
合缝宽度
组合宽
度
松紧组合宽度
拉链齿距边宽
度
数据 4.5MM 1.5-2MM 1.5-2MM 8MM 14MM 2MM
以上是普通材料操作标准,实际生产会有变化,容易散边和有泡棉的材料,折边可以做到6MM,反车和合缝做到3MM,组合位可以做到10MM
四.成型
1.按照样鞋/样品单/操作说明书/试做报告,提前准备好中底/大底/楦头。
楦头要插干净,大
底不能有瑕疵,颜色/纹路都要和样鞋一样。
中底要按照操作说明书,看是前置还是后置。
2.按照操作说明书提供数据,画出楦头记号点
3.鞋头画出8MM前帮第一爪位置
4.根据样鞋类型,选则合适的定型模先定型。
定型温度不能太高,PU内里要防止被定型模
烫坏。
浅色内里要避免被定型模污染变色。
定型好要检查内里是否平顺,鞋面有没有皱。
5.先放一双样品码,攀起来比对数据/形状,看和样鞋是否一样。
没问题再接着往下放,有问
题退给师傅反工。
6.按照数据攀鞋,鞋头后包要正,腰帮要拉贴楦,鞋头后包不能有发角。
7.鞋面和中底要粘牢固,帮脚要均匀/平顺,不可有波浪,中底不能跑位
8.按照操作说明书比对鞋头/后包数据,没有问题再过加硫
9.先做一双样品码和样鞋比较
10.打磨要平顺,不能打破帮面,打完磨要把灰尘清理干净
11.按照样鞋和操作说明书画线贴底,要对到样鞋数据,也要方便大货操作。
发现问题要马上
反映。
样品码做好再做剩下的鞋子
12.按照材料选择药水/胶水
13.药水/胶水要刷到位,不能欠胶/溢胶,也不能积胶/死胶
14.烤箱温度要按照标准要求
15.贴底要平顺,鞋子要正,不能前后踢放不稳
16.用正确压低模压底,压力时间按标准,不可压变形
17.冷冻时间/温度要够
18.拔楦前要把鞋带松开,脚背楦盖要取下来
19.中皮要贴正,中皮刷胶不能污染到鞋面
20.把鞋子整理干净,不能有画线/线头/胶线。
大底要清洗干净,用PE袋装好。
样品码按照大
货要求包装一双。
21.把样品制作过程中发现的问题全部记录下来,写在试做报告上面。
22.把样鞋/样品单/操作说明书/试做报告和鞋子一起交到品管室,由NQC/成型主管/品管/师傅
一起看过,针对出现的问题,做修改意见指导。
并将修改方法和操作重点整理出来发给现场各单位。
样品制作流程
NQC发样品制作报告→裁断冲裁好,裁片和样鞋/试做报告一起给针车→针车把面做好交到品管室→品管和师傅看过后交给成型→成型做好鞋子再交到品管室→NQC/成型主管/品管/师傅/生产经理看过后再开试做会。