氧气炉炼钢的冶金计算
炼钢部分各种计算公式汇总

炼钢部分各种计算公式汇总1、转炉装入量装入量=钢坯(锭)单重×钢坯(锭)支数+浇注必要损失钢水收得率(%)-合金用量×合金收得率(%)2、氧气流量Q=V tQ-氧气流量(标态),m 3min 或 m 3hV-1炉钢的氧气耗量(标态),m 3;t-1炉钢吹炼时间,min 或h 3、供氧强度 I=Q TI-供氧强度(标态),m 3t ·min ;Q-氧气流量(标态),m 3min;T-出钢量,t注:氧气理论计算值仅为总耗氧量的75%~85%。
氧枪音速计算 α=(κgRT)1/2m/sα—当地条件下的音速,m/s ;κ—气体的热容比,对于空气和氧气,κ=1.4;g —重力加速度,9.81m/s 2;R —气体常数,26.49m/κ。
马赫数计算 M=ν/αM —马赫数;ν—气体流速,m/s ;α—音速,m/s 。
冲击深度计算h 冲=K P 00.5·d 00.6ρ金0.4(1+H 枪/d c ·B)h 冲—冲击深度,m ;P 0—氧气的滞止压力(绝对),㎏/㎝2;d 0—喷管出口直径,m ;H 枪—枪位,m ;ρ金—金属的密度,㎏/m 3;d c —候口直径,m ;B —常数,对低粘度液体取作40;K —考虑到转炉实际吹炼特点的系数,等于40。
在淹没吹炼的情况下,H=0,冲击深度达到最大值,即 h max =P 00.5·d 00.6ρ金0.4有效冲击面积计算 R=2.41×104(h νmax)2R —有效冲击半径,m ;νmax —液面氧射流中心流速,m/s ;νmax =ν出d 出H ·P 00.404ν出—氧射流在出口处的流速,m/s 。
金属-氧接触面积计算 在淹没吹炼时,射流中的金属液滴重是氧气重量的3倍,吹入1m3氧气的液滴总表面积(金属-氧气的接触面积): S Σ=3G 金r 平均·ρ金G 金—1标米3氧气中的金属液滴重量=3×1.43㎏;r 平均—液滴的平均半径,m ;ρ金—金属液的密度,7×103㎏/m 3。
冶金工程 课程设计

17.58×0.002%×2/3=-0.0004
0.032
0.008
0.251
0.055
0.00
0.0002
-0.0002
0.056
0.011
0.471
0.243
0.00
-0.0004
0.0009
合计
0.434
0.346
17.58-0.434=17.146
为铁水量得1.5%(其中ω (FeO)为75%, (Fe2O3)为20%)
为铁水量得1%
渣中铁损(铁珠)
氧气纯度
炉气中自由氧含量
气化去硫量
金属中[C]的氧化产物
废钢量
为渣量的6%
99%,余者为N2
0.5%(体积比)
占总去硫量得1/3
90%C氧化成CO,10%C氧化成CO2
由热平衡计算确定,本计算结果为铁水量得17.58%,即废钢比为14.95%
0.042
0.058
82.11
16.47
0.05
0.18
0.50
0.69
合计
11.511
8.413
100.00
①炉气中O2的体积为8.413×0.5%=0.042m3;质量为0.042×32÷22.4=0.060kg。
②炉气中N2的体积系炉气总体积与其他成分的体积之差;质量为0.058×28÷22.4=0.072kg。
0.008
0.005
0.001
0.440
0.005
生白云石
2.5(表4)
0.910
0.640
0.020
0.025
0.905
《钢冶金学》_第6章 氧气底吹转炉和顶底复合吹炼转炉炼钢

钢冶金学重庆科技学院王宏丹◆氧气底吹转炉炼钢氧气底吹转炉炼钢OBM法和LWS法吹炼高磷铁水时的成分变化Q-BOP法吹炼过程中钢水和炉渣成分的变化Q-BOP法吹炼过程炉渣成分的变化吹炼终点[C]和[O]的关系图终点[C]和[Mn]的关系Q-BOP和LD炉内渣中(FeO)6.2.1 顶底复吹转炉炼钢工艺类型6.2 顶底复合吹炼转炉的冶金特点6.2.2 顶底复吹转炉的底吹供气和供气元件6.2.3 顶底复吹转炉内的冶金反应6.2.4 冶金效果氧气顶底复吹转炉炼钢在复吹转炉中,了解和掌握底吹气体的性质、冶金行为、合理地确定底吹气体比例,选择和控制底吹供气强度,是复吹转炉获得良好的技术经济指标的重要因素。
底吹气体的冶金行为主要表现在三个方面: 强化熔池搅拌,使钢水成分,温度均匀;加速炉内反应,使渣钢反应界面增大,元素间化学反应和传质过程更加趋于平衡;冷却保护供气元件,使供气元件使用寿命延长。
底吹气体底吹O:需用冷却介质来保护供气元件,会与熔2池中碳发生反应,产生较大的搅拌力。
:可不用冷却剂,会与熔池中碳发生反 底吹CO2应搅拌力较强的气体;会使熔池CO分压增加,不利于超低碳钢冶炼。
、Ar和CO:属中性或惰性气体,供入铁 底吹N2水中不参与熔池内的反应,只起搅拌作用。
底吹气体比例在复吹转炉中,底吹气体量的多少决定熔池内搅拌的强弱程度。
,其底吹 在冶炼超低碳钢种时,即使用底吹O2供气量也要达20%左右;对一些具有特殊功能的复吹工艺(如喷石灰粉、煤粉等),其底吹供气量可达40%。
就一般复吹转炉而言,为了保证脱硫、脱气和渣-钢间反应趋于平衡,在吹炼结束前,也要采用较大的底吹供气来搅拌熔池。
底吹供气强度获得最佳搅拌强度,使熔池混合最均匀。
大量实验研究表明,熔池的混匀程度与搅拌强度有关,而搅拌强度受供气量和底吹元件布置影响。
根据吹炼过程调节供气强度。
复吹转炉的特点是能有效地把熔池搅拌与炉渣氧化性有机统一起来,而实现手段就是控制底吹供气强度。
炼钢过程中的冶金气体和热力学模拟计算

炼钢过程中的冶金气体和热力学模拟计算钢铁是现代社会建设的基本材料之一,而钢铁的炼制过程中,冶金气体和热力学模拟计算都是至关重要的环节。
本文将从这两个方面进行探讨。
一、冶金气体在钢铁冶炼过程中,关于冶金气体的应用和控制是非常重要的。
常见的冶金气体如氧气、氮气、氢气、氩气等,它们的主要作用有以下几个方面:1. 氧气氧气在钢铁炼制过程中是最为常见的冶金气体,主要用于促进氧化反应和定量控制炉温。
炉料和炉渣中的一部分物质可以通过氧化反应将其转化为更容易熔化和分离的形态,比如氧化碳和氧化硫等。
此外,氧气的流量调节可以直接影响炉温的变化,保证炉温稳定有助于优化冶炼过程,提升钢材质量。
2. 氮气氮气主要用于对钢铁液的保护和保温,同时可以排除炉膛内的空气,以避免氧化反应的发生。
在连铸过程中,氮气还可以通过挤压作用对坯料进行压制,提高钢材的密度和均匀性。
3. 氢气氢气主要用于气体保护焊接和去除钢铁中的氧化物、硫化物等杂质。
通过向钢铁中注入氢气,可以将其中的杂质还原成低毒、易挥发的化合物,随炉渣一起从铁液中排出。
4. 氩气氩气作为一种惰性气体,在冶金炉中主要用于保护钢铁液,避免其遭受氧化。
氩气的对冶金过程的干扰极小,而且可以减少钢铁液中的杂质,保证钢材质量。
通过对冶金气体的合理运用和控制,可以帮助冶炼工人更好地掌握钢铁炼制过程,提升其工作效率和钢材质量。
二、热力学模拟计算热力学模拟计算是一种钢铁冶炼中常用的理论计算手段。
通过对冶炼过程中的炉温、炉内气体组成等参数进行模拟和预测,可以帮助冶炼工人更好地掌握和控制整个冶炼过程,比如优化炉况设计、控制温度分布和气体通量等。
下面我们来看看具体的应用场景:1. 炉况优化炉况优化是指通过调整炉内参数,比如炉温、气体组成等,来实现钢材质量的升级和冶炼效率的提高。
通过热力学模拟计算,可以对炉温分布、气体流动、反应速率等进行定量分析,找到最佳的炉况状态,从而提高生产效率和钢材质量。
2. 坩埚设计坩埚在钢铁炼制中起到了非常重要的作用,其选材、设计和使用都会严重影响冶炼效果。
第七章氧气转炉炼钢

•⑵ 氧化剂 •① 氧气 •转炉炼钢的主要氧源,氧气纯度,超过98%;氧气压力要稳 定,0.6~1.5MPa之间。 •② 铁矿石和氧化铁皮 •氧化铁有利于化渣和冷却作用
•⑶ 冷却剂 作用:准确命中转炉终点温度。 种类:废钢、氧化铁皮、铁矿石、烧结矿、球团矿、石灰 石等。 •⑷ 增碳剂 •种类:木炭、电极粉、焦炭粉、生铁等。
第七章氧气转炉炼钢
第七章氧气转炉炼钢
•⑵ 吹炼过程熔池内金属、炉渣成分和温度变化 整个吹炼过程分为三期来描述,碳的氧化过程明显的分为 三个阶段: ➢ 吹炼前期:脱碳速度缓慢,其速度随吹炼时间的延长而几 乎成直线增加; ➢ 吹炼中期:脱碳迅速,其速度达最大值,且几乎不变; ➢ 吹炼后期:脱碳反应衰弱,其速度随吹炼时间而直线下降。
第七章氧气转炉炼钢
•⑤ 吹炼中期脱碳反应激烈,渣中(%FeO)降低,致使炉渣熔 点增高和粘度加大,并可能出现稠渣(“返干“)现象。此时应 适当提高枪位,并可加入第二批料(氧化铁皮或矿石),可考 虑加入萤石,但要防止“喷溅”。 •⑥ 吹炼末期,[%C]降低,脱碳反应减弱,火焰变短而透明。 确定吹炼终点,并提枪停止供氧,倒炉测温取样,若碳温合 适,则出钢,否则补吹后出钢。 •⑦ 出钢前挡渣帽,出钢程中加入脱氧剂和铁台金进行脱氧 合金化,在出钢末期加挡渣塞。
第七章氧气转炉炼钢
7.3 氧气转炉炼钢工艺
特点 •① 完全依靠铁水氧化带来的化学热及物理热; •② 生产率高(冶炼时间在35分钟左右); •③ 质量好(气体含量少,CO的反应搅拌,将N、 H除去)可 以生产超纯净钢,有害成份(S、P、N、H、O)<80ppm; •④ 冶炼成本低,耐火材料用量比平炉及电炉用量低; •⑤ 原材料适应性强,高P、低P都可以。 •⑥ 冶炼品种多达400个。
整合版转炉炼钢计算部分

整合版转炉炼钢计算部分转炉炼钢是一种常用的工业炼钢方法,通过氧气吹炼可以去除钢中的杂质,得到高品质的钢材。
在转炉炼钢中,有一些重要的计算部分,包括吹炼时间、温度控制、钢水负荷等。
接下来将详细介绍这些计算部分。
1.吹炼时间的计算:吹炼时间是指从氧气吹入开始到钢水净化结束的时间。
吹炼时间的长短直接影响到钢水净化的效果和转炉的生产能力。
一般来说,吹炼时间可以通过下式计算:吹炼时间=钢水重量/(氧气流量×氧气纯度×铁素量)其中,钢水重量是指待净化的钢水的质量,氧气流量是指进入转炉的氧气的流量,氧气纯度是指进入转炉的氧气的纯度,铁素量是指待净化的钢中的铁含量。
2.温度控制的计算:在转炉炼钢过程中,温度的控制非常重要。
温度的过高或过低都会对钢水的成分和性能产生负面影响。
温度的控制主要通过加入适量的生铁和废钢来实现。
具体的计算方法如下:温度=(钢水质量×钢水温度+生铁质量×生铁温度+废钢质量×废钢温度)/(钢水质量+生铁质量+废钢质量)其中,钢水质量是指待净化的钢水的质量,钢水温度是指待净化的钢水的温度,生铁质量是指加入的生铁的质量,生铁温度是指加入的生铁的温度,废钢质量是指加入的废钢的质量,废钢温度是指加入的废钢的温度。
3.钢水负荷的计算:钢水负荷是指转炉的产能,即单位时间内可以生产的钢水的质量。
钢水负荷的计算可以通过下式得到:钢水负荷=吹炼时间×钢水重量吹炼时间已经在第一部分进行了介绍,钢水重量是指待净化的钢水的质量。
4.吸收剂的计算:在转炉炼钢中,为了提高钢水中的硫含量,常常需要加入吸收剂。
吸收剂的计算可以通过如下方式进行:吸收剂重量=钢水重量×(目标硫含量-初始硫含量)/吸收剂含硫量其中,钢水重量是指待净化的钢水的质量,目标硫含量是希望得到的钢水的硫含量,初始硫含量是待净化的钢水的硫含量,吸收剂含硫量是吸收剂中的硫含量。
以上是转炉炼钢计算部分的详细介绍。
炼钢部分各种计算公式汇总
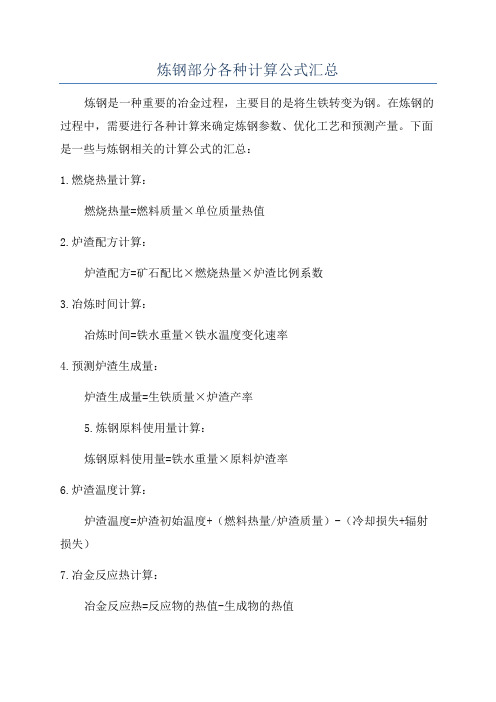
炼钢部分各种计算公式汇总炼钢是一种重要的冶金过程,主要目的是将生铁转变为钢。
在炼钢的过程中,需要进行各种计算来确定炼钢参数、优化工艺和预测产量。
下面是一些与炼钢相关的计算公式的汇总:1.燃烧热量计算:燃烧热量=燃料质量×单位质量热值2.炉渣配方计算:炉渣配方=矿石配比×燃烧热量×炉渣比例系数3.冶炼时间计算:冶炼时间=铁水重量×铁水温度变化速率4.预测炉渣生成量:炉渣生成量=生铁质量×炉渣产率5.炼钢原料使用量计算:炼钢原料使用量=铁水重量×原料炉渣率6.炉渣温度计算:炉渣温度=炉渣初始温度+(燃料热量/炉渣质量)-(冷却损失+辐射损失)7.冶金反应热计算:冶金反应热=反应物的热值-生成物的热值8.炉温控制计算:炉温控制=炉温目标值-炉温测量值9.耗氧量计算:耗氧量=氧气流量×氧浓度×燃烧公式系数10.炉渣替代率计算:炉渣替代率=炉渣替代量/炉渣生成量11.冷却水量计算:冷却水量=冷却热量/剪切热12.制氧气量计算:制氧气量=铁水含氧量×铁水重量×(氧气纯度/100)13.吹氧流量计算:吹氧流量=制氧气量/铁水供氧时间14.坩埚温度计算:坩埚温度=铁水温度+气氛温度15.炉水质量计算:炉水质量=炉水比例×矿石质量以上是一些与炼钢相关的计算公式的汇总。
当然,实际的炼钢过程非常复杂,还需要考虑其他因素如温度、压力、流量等等。
这些公式只是提供了一些基本的计算方法,实际应用中还需要根据具体情况进行适当的调整和修正。
2氧气转炉炼钢的基本原理
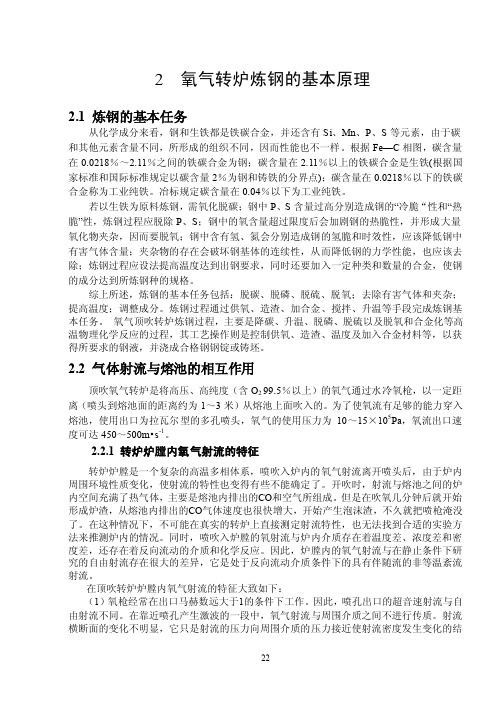
2氧气转炉炼钢的基本原理2.1 炼钢的基本任务从化学成分来看,钢和生铁都是铁碳合金,并还含有Si、Mn、P、S等元素,由于碳和其他元素含量不同,所形成的组织不同,因而性能也不一样。
根据Fe—C相图,碳含量在0.0218%~2.11%之间的铁碳合金为钢;碳含量在2.11%以上的铁碳合金是生铁(根据国家标准和国际标准规定以碳含量2%为钢和铸铁的分界点);碳含量在0.0218%以下的铁碳合金称为工业纯铁。
冶标规定碳含量在0.04%以下为工业纯铁。
若以生铁为原料炼钢,需氧化脱碳;钢中P、S含量过高分别造成钢的“冷脆“性和“热脆”性,炼钢过程应脱除P、S;钢中的氧含量超过限度后会加剧钢的热脆性,并形成大量氧化物夹杂,因而要脱氧;钢中含有氢、氮会分别造成钢的氢脆和时效性,应该降低钢中有害气体含量;夹杂物的存在会破坏钢基体的连续性,从而降低钢的力学性能,也应该去除;炼钢过程应设法提高温度达到出钢要求,同时还要加入一定种类和数量的合金,使钢的成分达到所炼钢种的规格。
综上所述,炼钢的基本任务包括:脱碳、脱磷、脱硫、脱氧;去除有害气体和夹杂;提高温度;调整成分。
炼钢过程通过供氧、造渣、加合金、搅拌、升温等手段完成炼钢基本任务。
氧气顶吹转炉炼钢过程,主要是降碳、升温、脱磷、脱硫以及脱氧和合金化等高温物理化学反应的过程,其工艺操作则是控制供氧、造渣、温度及加入合金材料等,以获得所要求的钢液,并浇成合格钢钢锭或铸坯。
2.2 气体射流与熔池的相互作用顶吹氧气转炉是将高压、高纯度(含O2 99.5%以上)的氧气通过水冷氧枪,以一定距离(喷头到熔池面的距离约为1~3米)从熔池上面吹入的。
为了使氧流有足够的能力穿入熔池,使用出口为拉瓦尔型的多孔喷头,氧气的使用压力为10~15×105Pa,氧流出口速度可达450~500m•s-1。
2.2.1 转炉炉膛内氧气射流的特征转炉炉膛是一个复杂的高温多相体系,喷吹入炉内的氧气射流离开喷头后,由于炉内周围环境性质变化,使射流的特性也变得有些不能确定了。
- 1、下载文档前请自行甄别文档内容的完整性,平台不提供额外的编辑、内容补充、找答案等附加服务。
- 2、"仅部分预览"的文档,不可在线预览部分如存在完整性等问题,可反馈申请退款(可完整预览的文档不适用该条件!)。
- 3、如文档侵犯您的权益,请联系客服反馈,我们会尽快为您处理(人工客服工作时间:9:00-18:30)。
氧气炉炼钢的冶金计算
概述
氧气炉炼钢是一种常见的冶金过程,用于生产高质量的钢材。
在这个过程中,氧气被用作燃烧剂来脱碳和脱硫炉料中的杂质。
本文提供了关于氧气炉炼钢的冶金计算的概述。
冶金计算
冶金计算在氧气炉炼钢过程中起着重要的作用。
以下是一些常见的冶金计算内容:
1. 需氧量计算:氧气炉炼钢的第一步是确定需要的氧气量。
这涉及到根据炉料中的杂质含量来计算氧气的需求量。
通常使用各种公式和指标来估计需要的氧气量。
2. 氧气吹炼时间计算:氧气炉炼钢过程中,吹炼时间也是一个重要的参数。
通过根据钢种和炉膛容量的不同,使用经验公式来计算吹炼时间。
吹炼时间的合理选择可以确保达到所需的冶金效果。
3. 炉料含硫量计算:在氧气炉炼钢过程中,确定炉料中的硫含
量也是非常重要的。
硫是钢材中的一个常见杂质,它对钢的性能有
很大的影响。
通过采样和化学分析,可以确定炉料中的硫含量,并
进行相应的计算。
4. 炉料含碳量计算:炉料中的碳含量也是冶金计算中的重要参数。
炼钢的目标之一就是减少炉料中的碳含量,以获得高质量的钢材。
通过化学分析和相应的计算,可以确定炉料中的碳含量,从而
进行适当的冶金操作。
5. 实时温度监测:在氧气炉炼钢过程中,实时温度监测非常关键。
通过使用温度计和其他传感器,可以监测炉内温度的变化,并
根据需要进行相应的调整。
结论
氧气炉炼钢的冶金计算是确保生产高质量钢材的重要一环。
通
过准确计算需要的氧气量、吹炼时间以及炉料中的硫和碳含量,可
以实现冶金过程的精确控制。
实时温度监测也是必不可少的工具,
以确保冶金过程的稳定性和可重复性。
熟练掌握这些冶金计算技术,可以提高钢材的质量和生产效率。
参考文献:
[1] 张三,钢铁冶金计算方法,冶金出版社,2010年。
[2] 李四,氧气炉炼钢工艺参数的计算与优化,钢铁科学研究,2005年。