凹印联线复合剥离过程控制要求及检测方法
塑料凹版印刷中常见问题及处理办法
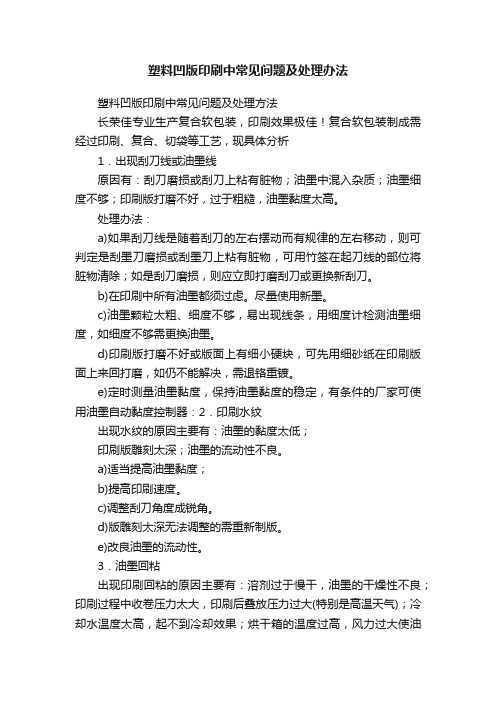
塑料凹版印刷中常见问题及处理办法塑料凹版印刷中常见问题及处理方法长荣佳专业生产复合软包装,印刷效果极佳!复合软包装制成需经过印刷、复合、切袋等工艺,现具体分析1.出现刮刀线或油墨线原因有:刮刀磨损或刮刀上粘有脏物;油墨中混入杂质;油墨细度不够;印刷版打磨不好,过于粗糙,油墨黏度太高。
处理办法:a)如果刮刀线是随着刮刀的左右摆动而有规律的左右移动,则可判定是刮墨刀磨损或刮墨刀上粘有脏物,可用竹签在起刀线的部位将脏物清除;如是刮刀磨损,则应立即打磨刮刀或更换新刮刀。
b)在印刷中所有油墨都须过虑。
尽量使用新墨。
c)油墨颗粒太粗、细度不够,易出现线条,用细度计检测油墨细度,如细度不够需更换油墨。
d)印刷版打磨不好或版面上有细小硬块,可先用细砂纸在印刷版面上来回打磨,如仍不能解决,需退铬重镀。
e)定时测量油墨黏度,保持油墨黏度的稳定,有条件的厂家可使用油墨自动黏度控制器:2.印刷水纹出现水纹的原因主要有:油墨的黏度太低;印刷版雕刻太深;油墨的流动性不良。
a)适当提高油墨黏度;b)提高印刷速度。
c)调整刮刀角度成锐角。
d)版雕刻太深无法调整的需重新制版。
e)改良油墨的流动性。
3.油墨回粘出现印刷回粘的原因主要有:溶剂过于慢干,油墨的干燥性不良;印刷过程中收卷压力太大,印刷后叠放压力过大(特别是高温天气);冷却水温度太高,起不到冷却效果;烘干箱的温度过高,风力过大使油墨出现假干现象;印刷非印刷面表面张力大(或双面电晕的情况),膜非印刷面与油墨的亲和力大,油墨发生转j处理办法:a)更换为快干溶剂,使油墨充分干燥。
b)调整收卷压力,尽量放小。
收卷的卷{要太大,堆积重量要小。
c)检查印刷机的冷却水是否打开,水温{符合要求。
b)在印刷中所有油墨都须过滤。
尽量使用新宜。
墨。
d)调整烘箱温度及风力,一般在50~65 ℃为宜。
e)印刷前检测薄膜的表面张力,印刷面的表面张力要大于非印刷面,双面电晕的薄膜最好不要使用。
4.印刷色差出现印刷色差的原因主要有:刮墨刀的位置、角度、压力发生变化引起印刷色差;油墨度变化引起印刷色差;油墨色浓度的变化引走刷色差;印刷版印到一定量后已变浅;印刷版版引起印刷色差;多色混合配置专色时,如果合油墨中各颜料的比重相差较大,在印刷过中,如油墨循环不良易发生油墨沉淀从而引起刷色差。
凹版印刷工艺过程质量控制

凹版印刷工艺过程质量控制资料来源:《广东印刷》2006年第3期作者:黄军马艳红胡更生一、套印系统优化设置随着电子技术和计算机技术的飞速发展,现代凹印机与计算机技术之间的结合越来越紧密。
特别是现代先进的高速凹印机,其套印系统大都采用微电脑进行控制处理,通过信号反馈来调整印刷图像的套印偏差。
1. 根据印刷图案的形状进行套印色标的位置设置套印识别色标一般采用的是一种梯形图案,为了套印系统能更有效地进行识别,在设置色标的位置时,应尽可能地避开印刷图案中类似形状的图案,即:不要让印刷图案中类似的形状与色标相邻地出现在同一条扫描区域内,否则,容易引起操作人员对显示屏上的波形误认,给套准调节带来一系列不必要的麻烦,造成不必要的浪费,情况严重时,还会导致套印系统无法稳定地进行工作。
2. 根据不同类型的原稿进行套印参照物的优化选择下面对两类有代表性的原稿分别进行讨论。
第一类原稿:印刷主体为线条和实地。
此类原稿的特点在于其图文以实地和线条为主,图像与图像间的套印关系简单,要求并不高。
该类原稿又可分为两类:①各专色版图案只与某一种色版图案之间存在着套印关系,那么该印件色标的设置就可以是各色版只与关键色版进行套印,即各色版套印的参考色标为关键版色标。
②两种实地版(A版、B版)存在着较高要求的套印关系且与关键色版(C版)也存在套印关系,而其他色版(D版、E版)只与关键色版(C版)存在套印关系,而与前两种实地版不存在套印关系,那么此类原稿的套印关系就可以设置为:A→B→C;D→C;F→C (“A→B”代表“A”参照“B”进行套印,其余以此类推)。
第二类原稿:图像、线条和实地共存的原稿。
此类原稿的特点在于,图像部分层次丰富,并且色彩再现是通过多个色组的彩色叠合而成,图像与图像之间存在着高精度的套印关系,如果套印精度不够,图像部分便会出现不清晰、重影等一系列套印问题。
假设图像部分是由A、B、C、D四种专色版所印的图案叠合而成,E为线条文字版,与图像部分不存在明显的套印关系,F版为实地基准版,与其他各版之间均存在套印关系,那么它们之间的套印关系就可以设置为A→B→C→D→F;E→F。
凹印生产线的分散控制与集中控制

影 响联线 设备后加工精度的关
快 捷得 多 。 一 个人 时 , 大脑 指 挥 右 凹 印机 与 联 线 设 备之 间 的 控 制连 键 是 跟 踪 承 印物 的 印刷线 速 度 精
手释放 纸张的同时, 已向左 手发出 接 ,除操作控制上必要 的互动 、连 度 。利 用 上 述 手 段 得 到 的 计 算 线 速 接纸 的指令 ,不存在 时滞 。而两个 锁 外 , 由 凹 印 机 提 供 一 个 转 速 信 度 与 实 际线 速度 存 在着 一 定
以八 色 机 为 例 ,第 一 色 组 与 最 问题,究其原因,在主驱动 上,除 安 装 调 试 和 日常 维 护 的 难度 。 后一 色 组 印版 滚 筒直 径 的误 差 :
P N N RI TI G FEL 0 .1 I D 2 1 0 0
陆 维 强
分 散控制与集 中控制
模切 )生产线 ,印刷部分 套印精度
一
笔者 曾看到过这 样一个现场表 大利等 国的多条 凹印联线 ( 横切 、
演 :一 人 右 手 两 手 指 捏 住 一 张 纸 ,
、
主 驱 动 的分 散 控 制
必然 结果 。
人 员输 入 的印版周 长数据L 引起 。
一
仔 细分析一下 ,这类设备分散
般 操 作 人 员输 入 的印版 周 长 数
这个表演使笔者联想 到凹印生 控制有两大部分 :一是主驱动 的控 据£ 为版 面设 计 的 “ 标称 周长 ” , 产线 的控制 。国内曾进 口美 国、意 制,二是套准装置 。 而并非实测 周长 ,特 别是与后加工
认真分析研 究这类 设备 ,可发 比Ⅳ 及操 作人 员输入 的 印版 周长数
了根 本 变 化 。虽 然 都 是 经 挑 选 的动 现一个共 同特 点:凹印机与联线用 据 乘积的结果: 手 敏 捷 选 手 进 行 接 纸 ,五 人 每 人 五 的横切机或模切 设备分 别 由不同厂 次 ,结 果 只 有 二 人 共 三 人 次 取 得 成 商 生 产 ,联 线 组 合 采 用 自成 系 统 的
凹版印刷复合片材的注意要点

书山有路勤为径;学海无涯苦作舟
凹版印刷复合片材的注意要点
与柔性印刷复合片材不同,凹版是先印刷在PE膜上,然后再同铝箔
复合,做成复合软管料的。
因此,凹版在复合片材上的印刷实际上就是凹
版在单层PE上的印刷。
1.注意PE印刷膜的纵横向的拉伸强度
常用的PE印刷膜,是二层共挤吹胀膜,其纵向拉伸强度的大小同
吹膜时的牵引比有关。
牵引比是薄膜牵引速度与管坯挤出速度之比,增大
牵引比,薄膜的纵向强度提高。
薄膜的横向拉伸强度同吹膜时的吹胀比有关。
吹胀比是膜管直径与口模直径之比,增大吹胀比,薄膜的横向强度提高。
凹印在印单层PE膜时,由于凹印每个色组间的距离在6-7m ,且干燥时加热温度一般达50-60℃,这样就特别容易将PE拉伸变形。
虽然有可靠的自动套色跟踪器在保障,但自动套色跟踪器的调整范围跟不上单层PE
膜在受热拉伸时变形的范围,因此,经验的凹印工艺在印刷PE 时总会发现套印不准。
其实,只要控制住吹膜时的MD,CD,即纵横向的拉伸强度,注意不使其过大,此时,注意牵引速度与检测速度之比不可太大,注意膜
管直径与口模直径之比不可太大。
2.根据PE印刷膜的MD、CD调整凹印印版
控制得再好的MD、CD,单层膜在印刷过程中仍然还会拉伸变形,此
时就必须把这种变形参数调整到印版中去。
凹印印版在每一色组印刷时,
有一个直径上的递增量,根据在特定MD、CD参数下,调整纵向的递增量与横向的收缩量,是保证印刷机上自动套色跟踪可靠工作的前提。
3.注意印刷时张力的调整与干燥单元温度的控制
为了不使纵向拉伸过大,从而妨碍套版精度,要十分注意张力的调
专注下一代成长,为了孩子。
凹印常见问题分析与解决

第二节凹印常见问题分析及解决一、凹印问题的成因二、凹印常见问题(一)、堵版在凹版印刷中,油墨从印版滚筒网穴中的转移率通常在50%-70%,大约还有1/2-1/3左右的油墨总是残留在印版滚筒网穴中。
该残留率如果保持一定尚可,但在印刷过程中由于种种原因,网穴中的油墨残留率逐步提高,油墨的转移率也就随之下降,造成堵版故障。
发生堵版以后,会引起印刷图案和文字的模糊不清、印刷颜色的变化,严重时基至无法继续进行印刷。
特别是浅网层次部位容易发生堵版。
1、赌版产生原因:(1)、油墨干固于版面印版滚筒网穴中油墨的转移率通常是由油墨的类型、粘度、印刷速度等因素决定的,总有1/2-1/3的油墨残留在网穴中。
当这些残余油墨在某些因素影响下发生干固(粘度增高)后,印版滚筒再次进入油墨槽时其也难以完全溶解,油墨转移率随之降低。
久而久之,网穴越来越浅,转移率越来越低,最后形成堵版。
此类堵版故障当然与油墨类型、溶剂配比、干燥速度等因素有关,而且印刷机的构造也有很大影响。
(2)、油墨中混入杂质在印刷时,印刷薄膜由于高速运行往往会产生静电,吸附周围的尘埃及基材碎屑等杂质并带人油墨中。
(3)、制版质量低下在腐蚀或雕刻过程中网穴内壁生成小毛刺,镀铬后表面不平滑;研磨时产生的毛刺以及Ω型网穴等,对油墨的转移率也有一定的影响,情况严重时也往往造成转移率低下而成为堵版的原因。
(4)、油墨溶解不良(劣化)油墨变质或溶剂平衡发生变化时引起溶解力下降,或者混入不同类型的油墨、误用溶剂等导致油墨溶解劣化,造成转移率低下,同时也会直接造成堵版。
(5)、化学变化两液型油墨或反应型油墨随着印刷的进行会逐步发生交联等化学反应,流动性变差,粘度增高,转移率随之降低,也可能成为堵版的原因之一。
2、解决方法:(1)、塑料凹印生产过程中发生堵版故障时,应使用溶剂或专用的清洗剂进行清洗,并针对发生堵版的原因加以解决。
(2)、调整适当的环境温湿度、选择与印刷速度、印刷环境相适应的溶剂配比。
AG24-2012凹印操作规程

前言为了规范本企业联机凹印机组、自动捆扎机、凹印清废、印版安装(含墨缸滚筒清洗)、凹印模切排刀、凹印机组刀(含模具安装)作业人员的安全操作要求,特制订本标准。
本标准由上海烟草包装印刷有限公司、上海金鼎印务有限公司标准化委员会提出。
本标准是对原企业标准QG/SYY·AG24(A)-2009《凹印作业安全操作规程》的修订,本标准代替QG/SYY·AG24(A)-2009。
与前版标准相比,除编辑性修改外主要技术变化如下:——细化凹印机组安全生产操作规程内容;——明确设备防静电装置以及墨泵电线维护要求。
本标准由安全保卫科负责起草并归口管理。
本标准主要起草人:聂明、杜心渭、郭新钢、季晓、张思宁。
本标准2009年6月首次发布。
本标准2011年12月第2次修改。
本标准2012年2月6日正式实施。
凹印作业安全操作规程1 范围本规程规定了联机凹印机组、自动捆扎机、凹印清废、印版安装(含墨缸滚筒清洗)、凹印模切排刀、凹印机组刀(含模具安装)等生产专用设备在生产过程中安全操作的要求。
本规程适用于上海烟草包装印刷有限公司、上海金鼎印务有限公司凹印作业安全生产管理。
2 规范性引用文件下列文件中的条款通过本标准的引用而成为本标准的条款,属于不注日期的引用文件,其最新版本适用于本标准。
《劳动保护管理规定》《员工守则及奖惩规定》《废弃物管理规定》《职业健康安全绩效测量和监视程序》3 凹印机组安全生产操作规程3.1 本安全操作规程适用于凹印机组上机操作人员。
3.2 本岗位的重点危险源、主要的一般危险源和重要环境因素,参见本岗位操作人员签约的安全承诺书。
3.3 凹印机组安全生产操作规程内容:3.3.1 基本要求3.3.1.1 机组操作人员必须通过职工三级安全教育和上岗培训,全面了解机组性能,掌握操作技能,经考试合格后方可上岗操作。
3.3.1.2 开机前应进行班前一分钟安全教育,认真检查机器安全联锁装置和防护罩部位、设备润滑系统是否正常和紧急停止开关是否应急可靠。
凹版印刷操作规程完整

凹版印刷操作规程完整一、凹版印刷操作规程的目的和范围(100字以内)二、凹版印刷操作规程的组织与管理1.管理人员的职责-确保凹版印刷操作规程的有效执行;-对操作人员进行岗前培训,提供必要的安全防护设备;-定期检查操作人员的工作情况,提出合理化改进建议。
2.操作人员的职责-遵守操作规程,确保操作的安全、规范;-维护和保养印刷设备,确保设备正常工作;-及时向管理人员报告设备故障和危险情况。
三、凹版印刷操作规程的安全操作要求1.操作前的准备工作-确保印刷机的电源接地良好;-检查印版、油墨、纸张等材料的质量,确保无损坏和过期情况;-确保纸张的尺寸和摆放位置正确。
2.操作中的安全要求-穿戴劳动防护用品,如手套、眼镜、口罩等;-注意操作规程中的操作顺序和要点,确保操作的准确性和稳固性;-防止触碰旋转件和运动件,以免发生危险;-配置灭火器材和紧急救援设备,并了解其使用方法。
3.操作后的安全措施-清理和整理操作台和周边区域,排除杂物和危险物;-关闭印刷机的电源,确保设备停止运行;-报告设备故障和危险情况,及时进行维修和处理。
四、凹版印刷操作规程的生产效率要求1.准备工作的时间控制-合理安排生产计划,确保准备工作的时间不超过规定时间;-提前准备好所需材料,避免因准备工作不及时导致生产延误。
2.操作过程的时间控制-熟悉印刷机的操作流程,确保操作的高效准确性;-配合其他操作人员的工作,互相配合,提高工作效率。
3.故障排除和维修的时间控制-及时报告设备故障,减少设备维修和更换的时间;-做好设备的日常保养工作,延长设备的使用寿命。
五、凹版印刷操作规程的质量控制要求1.检查印版和油墨的质量-严格按照规程要求检查印版和油墨的质量,确保印刷品的图文清晰、颜色鲜艳;-对不合格的印版和油墨及时更换或调整,保证印刷品质量。
2.检查印刷品的质量-定期抽检印刷品的质量,包括颜色、位置、图案清晰度等方面;-对不合格的印刷品及时进行返工或淘汰,确保产品合格率。
CYT 202—2019《凹印联线复合剥离过程控制要求及检验方法》标准文本

应为 7.0 ~ 8.0。 4.1.3.4 黏度
原料黏度应为 100 mPa·s ~ 900 mPa·s,上机黏度应为 10 s ~ 40 s(察恩 4 号杯)。
2
CY/T 202—2019
4.2 过程控制
4.2.1 涂布 4.2.1.1 环境温度应为 (25±8) ℃,相对湿度应为 (60±10)% RH。 4.2.1.2 涂布时,纸张幅宽应大于膜的幅宽,膜的幅宽应大于压印辊轴向宽度,压印辊轴向宽度应大 于印版的有效涂布宽度。 4.2.1.3 应选择合适的涂布辊,通过网线数、网穴深度、网穴形状控制涂布量。 4.2.1.4 应至少每半小时检测胶黏剂黏度一次 , 黏度偏差不大于 2 s。 4.2.1.5 应调整刮刀角度、压力,检查刮刀磨损情况,确保涂布均匀平整。 4.2.2 粘合 4.2.2.1 膜放卷张力应小于膜收卷张力,纸卷放卷张力应小于印刷张力。 4.2.2.2 定位转移膜粘合前,应通过调整膜面张力,使膜面版距符合生产要求。 4.2.2.3 应调整粘合辊线压力,使转移膜与卷筒纸面充分贴合。 4.2.2.4 应通过纠偏装置,使转移膜在卷筒纸居中位置。 4.2.3 干燥 4.2.3.1 烘箱温度应分段设置,先设置初始温度,逐步升温到与胶黏剂干燥匹配的温度再逐步降温到 易于分离的温度。 4.2.3.2 应调节烘箱进出风量,确保干燥充分。 4.2.4 剥离 4.2.4.1 冷却水辊温度应为(20±2)℃。 4.2.4.2 分离后功能层、镀层应完全转移,基材表面无残留斑点。 4.2.4.3 转移后纸张表面的转移层附着牢固。 4.2.5 表面处理 4.2.5.1 纸张表面转移层表面润湿张力应不小于 3.8×10-2 N/m2。 4.2.5.2 印刷后油墨附着牢固。
- 1、下载文档前请自行甄别文档内容的完整性,平台不提供额外的编辑、内容补充、找答案等附加服务。
- 2、"仅部分预览"的文档,不可在线预览部分如存在完整性等问题,可反馈申请退款(可完整预览的文档不适用该条件!)。
- 3、如文档侵犯您的权益,请联系客服反馈,我们会尽快为您处理(人工客服工作时间:9:00-18:30)。
《凹印联线复合剥离过程控制要求及检测方法》
新闻出版标准编制说明
一、工作简况
(一)任务来源
随着环保理念的深入人心,凹印设备全息膜避版缝的专利技术的结束以及无版缝全息膜技术的进步,转移介质层与凹版印刷连线完成工艺日渐成熟,但目前国内尚无同类凹印连线转移过程控制标准,如果该工艺能形成规范,将无疑将使需要参照此规范的企业减少摸索工艺的时间,节约大量的人力、物力。
由全国印刷标准化技术委员会(SAC/TC 170)组织筹备制定的《凹印联线复合剥离过程控制要求及检测方法》新闻出版行业标准于2015年8月经新闻出版总署批准正式启动立项。
(二)标准的起草单位及起草人
标准的起草单位:江苏劲嘉新型包装材料有限公司、深圳劲嘉集团股份有限公司、安徽安泰新型包装材料有限公司、北京印刷学院、贵州劲嘉新型包装材料有限公司、昆明彩印有限责任公司、江西丰彩丽印刷包装有限公司、江苏中印印务有限公司、浙江美浓世纪集团有限公司、中丰田光电科技(珠海)有限公司、陕西北人印刷机械有限责任公司、云南侨通包装印刷有限公司、常德金鹏印务有限公司、天津长荣印刷设备股份有限公司、中山松德印刷机械有限公司、广州市恒远彩印有限公司、中山松德印刷机械有限公司。
标准起草人:侯立伟、徐静彦、许文才、吕伟、吴净土、曹国荣、朱国良、易元锋、王倩倩、庞锟、张辉、徐斯伦、陆俊、习大润、文杰、欧立国、王玉信、贺志磐、王文娜
(三)主要工作过程
2014年12月深圳劲嘉集团股份有限公司与SAC/TC 170就《凹印联线复合剥离过程控制要求及检测方法》行业标准起草工作进行了协商,并确定由深圳劲嘉集团股份有限公司牵头承担标准起草任务;
2015年8月深圳劲嘉集团股份有限公司为主负责联系标准起草组成员单位,并报SAC/TC 170备案同意;
2015年10月,深圳劲嘉集团股份有限公司就“凹印联线复合剥离过程控制要求及检测方法”撰写了“中华人民共和国新闻出版总署新闻出版印刷科研项目开题报告”;
2017年7月6日于北京市召开了“凹印联线复合剥离过程控制要求及检测方法”新闻出版行业标准起草组成立会议暨第一次工作会议,讨论与确定了标准起草的框架、内容、工作任务与分工,形成了第一次工作会议纪要。
第一次工作会议确定由深圳劲嘉集团股份有限公司作为牵头单位,执笔组成员为吴净土、吕伟、易元锋、朱国良。
确定吴净土为组长,易元锋为副组长。
会上讨论了标准适用范围,确定了《凹印联线复合剥离过程控制要求及检测方法》标准由范围、规范性引用文件、术语和定义、技术要求、检验方法五个内容组成,确定了转移、转移膜、凹印联线转移3个重要术语和定义。
2017年9月18日在北京召开了标准起草组第2次工作会议,会议对执笔组根据第一次会议纪要完成的《凹印联线复合剥离过程控制要求及检测方法》标准草案第1稿内容进行了讨论与研究,修改了标准的适用范围,反复讨论了转移、转移膜、凹印联线转移3个术语的定义,并提出应增加“定位膜”和“膜面版距”这2个术语。
会上对标准草案第4章的内容从文字表达简洁性和准确性角度进行了认真讨论,提出由中丰田光电科技(珠海)有限公司张辉核实水基胶黏剂黏度的具体要求和检测方法。
会上对标准草案第5章“剥离性能”的检验方法进行讨论,有专家提出草案第1稿的检验方法有误,需进一步查证。
2018年4月10日在东莞市召开了标准起草组第3次工作会议,会议对执笔组根据第2次会议纪要完成的《凹印联线复合剥离过程控制要求及检测方法》标准草案第2稿内容进行了讨论与研究,会议对第3章中的“定位膜”和“膜面版距”两个术语的定义进行了反复商讨。
会上专家一致认为原定术语“转移”太过口语化,从而引入术语“复合剥离”取代原术语并给出了定义。
会上决定原料粘度暂定为60~1000mpa·s,上机粘度暂定应为10s~50s(察恩4号杯),
会后中丰田光电科技(珠海)有限公司张辉进一步核实。
会议确定,会后由执笔组依据第3次工作会议纪要求补充和完善标准草案第2稿,而后提交至印刷标委会秘书处修改,修改后的版本可作为《凹印联线复合剥离过程控制要求及检测方法(征求意见稿)》,同时执笔组要完成标准编制说明编写。
2018年8月8日,印刷标委会在全体委员中,并在印刷标委会网站()上征集印刷业对《凹印联线复合剥离过程控制要求及检测方法(征求意见稿)》文件的意见和建议。
二、标准编制原则与确定标准主要内容的依据
(一)标准编制原则
严要求与适宜性、可操作性相结合的原则。
严要求即标准的编制应严格遵循GB/T1.1-2009《标准化工作导则第1部分:标准的结构和编写》及相关法规的要求进行;适宜性既要充分考虑行业内各单位都能依照本标准有所指引,体现标准应用于凹印联线复合剥离过程控制及检测,方便各单位在生产实际中能根据本标准来指导日常工作的开展,从而提高标准贯彻实施的可操作性。
(二)本标准主要内容
本标准规定了凹印联线复合剥离工艺的术语与定义、过程控制指标及检测方法。
(三)本标准制定参考的主要依据
参考国内外标准制定的一般规则。
同时考虑到本标准需要对凹印联线复合剥离具有指导性与可操作性,故起草组成员依据各自单位的实际情况结合相关标准规范共同商讨制定了《凹印联线复合剥离过程控制要求及检测方法》。
三、主要试验(或验证)的分析及技术经济效益评估
(一)主要试验验证的样品及其测试数据的分析
共收集胶黏剂品牌4种、每个品牌6个批次的样品。
4种胶黏剂品牌均为转移膜生产厂家常用品牌,具体测试数值见附件1。
根据该测试数据设定《凹印联线复合剥离过程控制要求及检测方法》标准草案中胶黏剂来料管控应满足的指标值大小。
(二)试验项目和方法评估
24个样品的测试项目包括原料黏度(mpa·s)、杂质颗粒度(μm)和固含量(%),其中原料黏度采用GB/T 2794—1995《胶粘剂粘度的测定》规定的旋转黏度计法进行测量,杂质颗粒度采用GB/T 6753.1《色漆、清漆和印刷油墨研磨细度的测定》规定的方法进行测量,固含量采用GB/T 2793《不挥发物含量的测定》规定的方法进行测量。
(三)技术经济评估
本标准的贯彻实施经济效益是显著的。
本标准的贯彻实施将对我国凹版印刷包装工艺改进、提升企业的市场竞争力与市场占有份额都具有重要意义。
本标准的制定为凹印联线复合剥离工艺的生产原材料以及生产过程控制等都提出了质量要求,这对提高印刷生产效率和产品质量,引领行业的技术发展,倡导绿色环保,减少职业病等方便均将产生良好的社会效益与经济效益。
同时也为行业新的生产工艺建立相关标准提供示范。
四、本标准参照采用的国际或国内法规及相关标准
本标准查阅的相关国家标准、行业标准和其他国家的标准, 见附件2。
五、与有关的现行法律、法规和强制性国家标准的关系
本标准内容符合国家现行法律、法规要求,并与参照采用的相关标准有一定的对应关系。
六、重大分歧意见的处理经过和依据
本标准的制定过程中出现的分歧意见, 主要集中在第3章术语“定位转移膜”等的定义、黏度、分离性能的检测标准以及胶黏剂指标杂质颗粒度与细度。
(一)第3章术语由第1次和第2次起草组确定的“转移”、“转移膜”、“凹印连线转移”、“定位膜”和“膜面版距”5个术语修改为“复合剥离”、“转移膜”、“定位转移膜”、“膜面版距”4个术语。
专家们对各术语以及术语的定义进行了长时间的讨论,尤其是针对“复合剥离”这一术语,深圳劲嘉集团股份有限公司的专家认为“复合剥离”描述了工艺过程,更为准确。
去掉了“转移”这一术语,标准名称也由原来的《凹印连线转移过程控制及检验方
法》改为《凹印联线复合剥离过程控制要求及检测方法》。
(二)有关转移膜剥离后有无残留镀层这一技术要求的检验方法争议点在于参考标准。
转移膜分离性能的检验方法可参考的标准有GB/T 25256《光学功能薄膜离型膜180°剥离力和参与黏着率测试方法》和GB/T 7122《高强度胶粘剂剥离强度的测定浮辊法》。
由于GB/T 7122范围规定该标准适用于刚性金属被粘物与绕性金属被粘物之间的剥离强度检测,而《凹印联线复合剥离过程控制要求及检测方法》中转移膜分离指的是金属镀层从塑料薄膜基材上剥离,GB/T 25256更为适用,最终专家组一致同意采用GB/T 7122《高强度胶粘剂剥离强度的测定浮辊法》作为分离性能检验方法。
(三)作为凹印联线复合剥离过程中重要辅料之一的胶黏剂,生产时经常由于黏度过大或过小等问题影响成品质量,故将黏度作为重要指标进行管控毫无争议。
但标准起草会议上有专家提出胶黏剂的黏度有来料时的黏度和上机使用时的黏度两种,来料时的黏度应作为胶黏剂的基本指标进行检验,而上机时的黏度应作为凹印联线复合剥离过程控制指标纳入检测指标,同时指出生产中胶黏剂时常因含有一些颗粒杂质等导致质量事故。
据此专家展开讨论认为应将“杂质颗粒度”作为胶黏剂的检测指标,也有专家提出应该用“细度”。
经商榷,最终检测指标为“杂质颗粒度”,但检测方法参考细度。
七、标准作为强制性标准或推荐性标准的建议
本标准建议为推荐性标准。
八、贯彻标准的要求措施建议(包括组织措施、技术措施、过渡办法等内容)
(一)组织措施:在SAC/TC 170的组织协调下,以标准起草组成员为主,成立标准宣贯小组。
(二)技术措施:组织撰写标准宣贯材料,组织标准宣贯培训,争取标准颁布实施后尽快在全行业推广。
九、废止现行有关标准的建议
不存在可废除的对应标准。
十、本标准编制说明的附件
附件1:胶黏剂样品测试数据表;
附件2:编制本标准所查阅的相关标准一览表;。