生产过程控制和检验
浅谈检验在生产过程中的质量控制
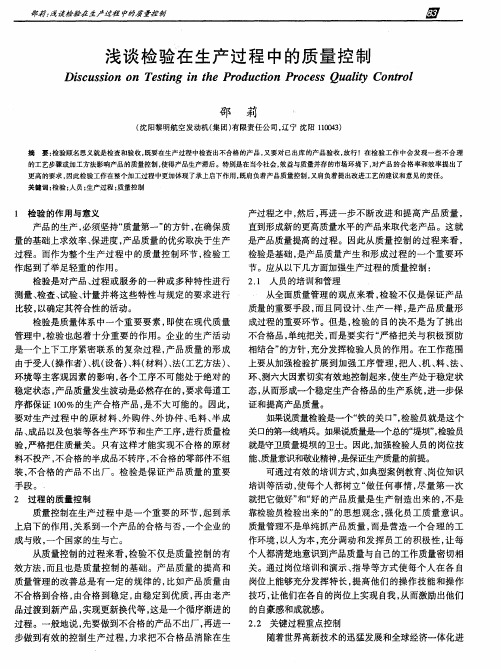
浅谈 检 验在 生产 过 程 中的质 量控 制
Di s c u s s i o n o n T e s t i n g i n t h e P r o d u c i t o n P r o c e s s Q u a l i t y C o n t r o l 邵 莉
关键词 : 检验 ; 人员 ; 生产过程 ; 质量控制
l 检 验 的作 用与 意义
产过程之中, 然后 , 再进一步不 断改进和提高产品质量 ,
直到形成新的更高质量水平 的产品来取代老产品。这就 是产品质量提高的过程。因此从质量控制 的过程来看 ,
检验是基 础 , 是 产 品质 量产 生 和形 成 过 程 的 一个 重 要 环
料不 投 产 , 不合格 的半成 品不转 序 , 不 合格 的零部 件不 组 装, 不 合 格 的产 品不 出厂 。检 验 是保 证 产 品 质量 的重 要
手段。 2 过 程 的 质量控 制
可通过有效的培训方式 , 如典型案例教育、 岗位知识 培训等活动 , 使每个人都树立“ 做任何事情 , 尽量第一次 就把它做好” 和“ 好 的产品质量是生产制造出来的 , 不是 靠检验员检验出来的” 的思想观念 , 强化员工质量意识 。 质量管 理不 是单纯 抓 产 品质 量 , 而 是 营造 一 个 合 理 的 工
品过渡到新产品, 实现更新换代等 , 这是一个循序渐进 的 过程 。一般地说 , 先要做到不合格的产品不出厂 , 再进一
步做到有效的控制生产过程 , 力求把不合格 品消除在生
的自豪感和成就感。
2 . 2 关键过程重点控制
随着世界高新技术 的迅猛发展和全球经济一体化进
生产过程控制和检验
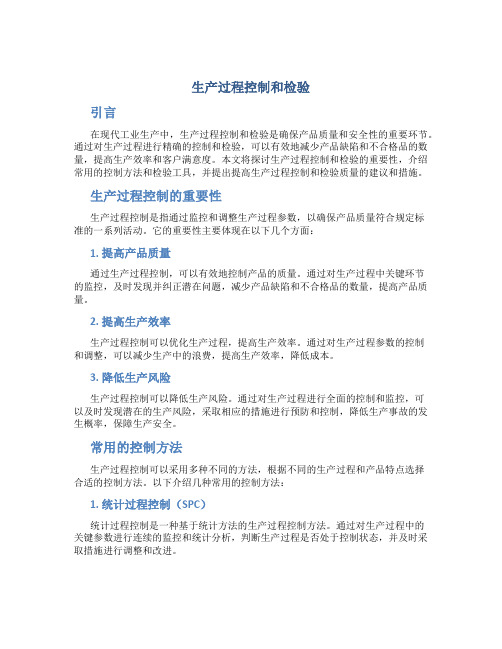
生产过程控制和检验引言在现代工业生产中,生产过程控制和检验是确保产品质量和安全性的重要环节。
通过对生产过程进行精确的控制和检验,可以有效地减少产品缺陷和不合格品的数量,提高生产效率和客户满意度。
本文将探讨生产过程控制和检验的重要性,介绍常用的控制方法和检验工具,并提出提高生产过程控制和检验质量的建议和措施。
生产过程控制的重要性生产过程控制是指通过监控和调整生产过程参数,以确保产品质量符合规定标准的一系列活动。
它的重要性主要体现在以下几个方面:1. 提高产品质量通过生产过程控制,可以有效地控制产品的质量。
通过对生产过程中关键环节的监控,及时发现并纠正潜在问题,减少产品缺陷和不合格品的数量,提高产品质量。
2. 提高生产效率生产过程控制可以优化生产过程,提高生产效率。
通过对生产过程参数的控制和调整,可以减少生产中的浪费,提高生产效率,降低成本。
3. 降低生产风险生产过程控制可以降低生产风险。
通过对生产过程进行全面的控制和监控,可以及时发现潜在的生产风险,采取相应的措施进行预防和控制,降低生产事故的发生概率,保障生产安全。
常用的控制方法生产过程控制可以采用多种不同的方法,根据不同的生产过程和产品特点选择合适的控制方法。
以下介绍几种常用的控制方法:1. 统计过程控制(SPC)统计过程控制是一种基于统计方法的生产过程控制方法。
通过对生产过程中的关键参数进行连续的监控和统计分析,判断生产过程是否处于控制状态,并及时采取措施进行调整和改进。
2. 6σ (Six Sigma)6σ 是一种通过减少产品或过程的变异性,从而实现产品质量提高的方法。
它是一种以数据为基础的管理方法,通过准确定义目标、测量当前绩效、分析数据、改进过程和控制过程,以实现质量的持续改进。
3. 过程流程管理(PPM)过程流程管理是一种通过对生产过程的全面管理和优化,实现产品质量和生产效率提高的方法。
它通过对整个生产过程进行细致的划分和管理,控制关键环节,提高生产过程的稳定性和可控性。
过程、成品和出厂质量检验管理方案
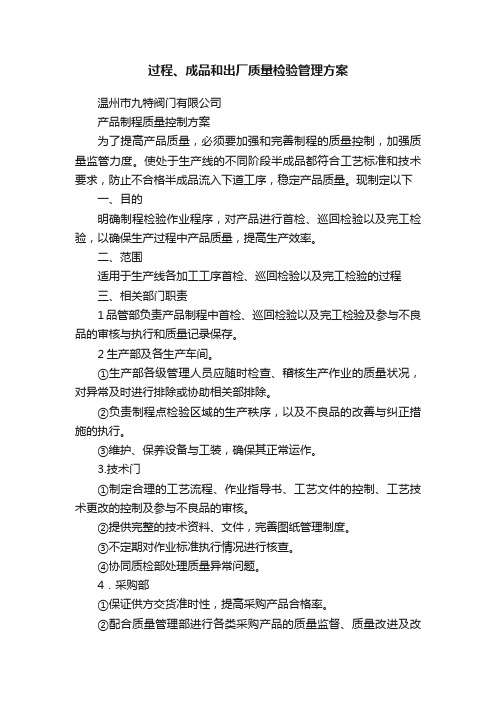
过程、成品和出厂质量检验管理方案温州市九特阀门有限公司产品制程质量控制方案为了提高产品质量,必须要加强和完善制程的质量控制,加强质量监管力度。
使处于生产线的不同阶段半成品都符合工艺标准和技术要求,防止不合格半成品流入下道工序,稳定产品质量。
现制定以下一、目的明确制程检验作业程序,对产品进行首检、巡回检验以及完工检验,以确保生产过程中产品质量,提高生产效率。
二、范围适用于生产线各加工工序首检、巡回检验以及完工检验的过程三、相关部门职责1品管部负责产品制程中首检、巡回检验以及完工检验及参与不良品的审核与执行和质量记录保存。
2生产部及各生产车间。
①生产部各级管理人员应随时检查、稽核生产作业的质量状况,对异常及时进行排除或协助相关部排除。
②负责制程点检验区域的生产秩序,以及不良品的改善与纠正措施的执行。
③维护、保养设备与工装,确保其正常运作。
3.技术门①制定合理的工艺流程、作业指导书、工艺文件的控制、工艺技术更改的控制及参与不良品的审核。
②提供完整的技术资料、文件,完善图纸管理制度。
③不定期对作业标准执行情况进行核查。
④协同质检部处理质量异常问题。
4.采购部①保证供方交货准时性,提高采购产品合格率。
②配合质量管理部进行各类采购产品的质量监督、质量改进及改进结果的验收,以及质量索赔及其他日常管理工作。
③合格供应商协作配套能力调查评价的组织与实施。
四、工作程序1制程自主检验制程中每一位操作者均应对所生产的制品实施自主检查,遇质量异常时应即予挑出,如系重大或特殊异常应立即报告质检人员和车间主任,共同分析原因及处理对策。
车间主任或主管均有督促所属员工实施自主检查的责任,随时抽验所属员工各制程质量,一旦发现有不良或质量异常时应立即处理外,并追究相关人员疏忽的责任,以确保产品质量水准,降低异常重复发生。
2首件检验操作者要严格按《首件检验制度》执行,对所生产的首件零件实施自主检查,认为符合要求后,送检验员检验。
这对于加工中心、数控机床、线切割等设备靠编程和刀具来保证加工质量的,以及冲床等靠模具保证质量的批量产品,尤为重要。
CCC生产过程控制和过程检验

CCC生产过程控制和过程检验1 目的对生产服务过程特别是关键生产工序进行有效控制,以确保满足顾客的需求和期望。
2 范围适用于对产品的形成、过程的确认、标识和可追溯性、产品的防护及放行。
3 职责3.1 生产经营部负责生产设备的管理,并对整个生产过程进行监督、协调,负责产品的防护。
3.2 车间负责产品的生产和基本质量的控制。
3.3 生产经营部及车间等相关部门负责实施各类产品状态的标识。
3.4 技术检验部负责监视和测量装置的管理,过程的识别、编制相应的工艺规程。
4 程序4.1 生产提供过程的控制4.1.1 生产流程图见产品相关设计文件。
4.1.2 关键生产工序4.1.2.1 关键生产工序包括:a) 对成品的质量、性能、功能、寿命、可靠性及成本等有直接影响的工序;b) 产品重要质量特性形成的工序;c) 工艺复杂,质量容易波动,对工人技艺要求高或问题发生较多的工序。
4.1.2.3 本公司生产的关键生产工序是装配;对些过程应进行确认,证实它们的过程能力。
适用时,这些确认的安排应包括:(1)生产车间操作者应依照工艺流程操作,按照设计图纸生产;车间主任要指导车间操作者工作,及时解决制造过程中出现的工艺难题。
及时解决制造过程中出现的工艺难题。
(2)当实际作业不能满足工艺文件和技术图纸要求时,由车间主任提出改进方案,征得主管领导同意后付诸实施;当本部门不能独立解决时,可请设计者一并商议解决。
(3)操作者在制造过程中若发现有不合格的采购物资时,应将其隔离并及时的通知检验员,由检验员按《进货检验规程》负责重检,执行《不合格品控制程序》。
(4)生产车间操作者在完成每一工序制造工作后,都要认真进行自检,遇质量不合格时应立即处理;经车间主任复核确认合格后,在产品过程检验单上的相应项目栏内签字确认,签字人必须是两人,即操作者和复核人。
(5)自检、复核完成后,车间主任应及时的通知检验员予以验证;检验员验证合格后在《装配过程检验记录》的相应项目栏内签字确认,确认后转入下道工序。
07生产过程控制和过程检验控制程序
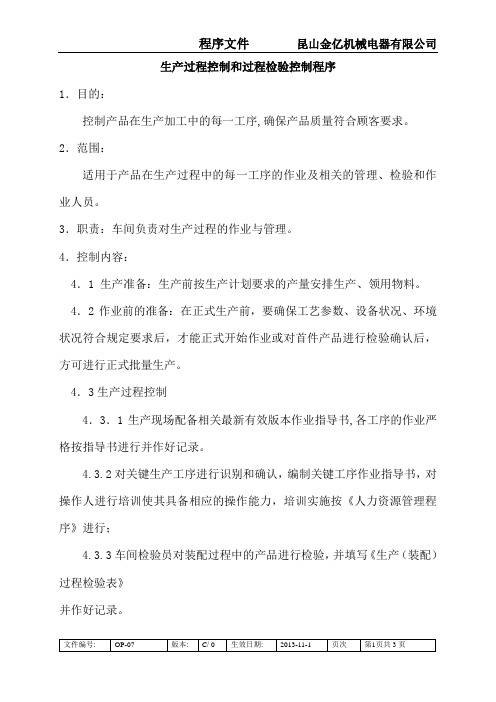
生产过程控制和过程检验控制程序1.目的:控制产品在生产加工中的每一工序,确保产品质量符合顾客要求。
2.范围:适用于产品在生产过程中的每一工序的作业及相关的管理、检验和作业人员。
3.职责:车间负责对生产过程的作业与管理。
4.控制内容:4.1 生产准备:生产前按生产计划要求的产量安排生产、领用物料。
4.2作业前的准备:在正式生产前,要确保工艺参数、设备状况、环境状况符合规定要求后,才能正式开始作业或对首件产品进行检验确认后,方可进行正式批量生产。
4.3生产过程控制4.3.1生产现场配备相关最新有效版本作业指导书,各工序的作业严格按指导书进行并作好记录。
4.3.2对关键生产工序进行识别和确认,编制关键工序作业指导书,对操作人进行培训使其具备相应的操作能力,培训实施按《人力资源管理程序》进行;4.3.3车间检验员对装配过程中的产品进行检验,并填写《生产(装配)过程检验表》并作好记录。
4.3.4在生产过程中保持生产现场的环境卫生条件,要按照设备的安全操作规程的要求操作;4.3.5车间负责对生产设备进行日常的维护保养,并定期的进行维修;日常的维护保养及其维修后,要认真填写《设备维护记录单》。
4.3.3过程中发现的不合格品按《不合格品控制程序》的相关条款进行标识与处理。
4.4所有相关的记录按《记录控制程序》以有关规定保存。
5 相关文件:5.1不合格品控制程序5.2记录控制程序5.3 《人力资源管理程序》6 使用表单:6.1生产(装配)过程检验表6.2《设备维护记录单》6.3 《设备台账》昆山金亿机械电器有限公司编号:RD015昆山金亿机械电器有限公司年月设备名称:设备维护记录表表单编号:RD016批准:检查人:昆山金亿机械电器有限公司设备管理台账表单编号:RD017批准:制表:。
测试线生产过程与检验控制程序

测试线生产过程与检验控制程序1.目的对测试线生产环境、半成品包装,切割工艺、测试项目,测试治具、仪器,产品质量进行控制,确保产品符合客户要求。
2.适用范围适用于测试线生产过程与检验控制。
3.职责1.根据测试线的组织架构合理的配置人员,并培训其相关技能。
2.根据PMC下发的《工作令》及《每日生产计划》安排生产.3.将影响生产的异常问题及时反馈给PMC以便PMC调整生产计划.4.规范测试线仪器,测试安全操作流程,强化员工的安全意识.5.工单生产完成及时入库。
4.定义4.1 首件确认:在试产,批量生产前对所贴物料进行一次全面确认,验证产品是否可生产的一项活动。
4.2 IPQC检查:生产中IPQC对测试产品进行测试项目检查。
4.5 QA:依规定的抽样频率、抽样数量、时间、标准或规格检查制程中的在制品,确保产品质量满足客户需求。
5.程序5.1 测试线生产环境管理5.1.1 测试线生产环境5.1.1.1 测试线生产管理人员对测试车间生产环境条件进行管理,温度:21℃~27℃;湿度:40%~75%,并担当2次/天的频率进行工作环境的确认,并通过温/湿度测试仪收集车间的温度和湿度,将结果记录于《车间温湿度记录表》中。
5.1.1.2 测试线所有人员每天测量静电并记录《防静电点检记录表》。
5.1.1.4当上述项目确认发生异常时须及时反馈车间负责人并给予改善。
5.1.2 测试线半成品保存条件51.1.23 半成品测试后需贴条码,条码内容需有:生产日期,编号,软件版本,条码,机型。
并用防静电胶盒装入周转。
5.2 SMT的部品管理5.2.1 测试半成品包装后,QA贴外包装条码纸,盖PASS印章,生产管理人员填写《入库单》,发送成品仓。
5.2.2 不良品,经过维修部,品质部,生产部确认后,填写《报废申请单》,由生产副总签名入成品仓。
5.2.3 由外部门转入的半成品需用周转车,插板架,或包装箱进行。
5.4生产过程管理5.4.1 测试5.4.1.1转线生产提前30分钟发出并填写《测试转机通知记录表》,生产,技术,品质按记录表内容进行作业执行。
生产过程控制制度与出厂检验记录制度

不合格品处理与追溯
不合格品定义:不符合质量标准或技术要求的产品 不合格品处理:隔离、标识、记录、处理、销毁等 追溯制度:记录不合格品的来源、去向、处理情况等信息 追溯目的:确保产品质量,提高产品质量管理水平
制度宣传与培训
制度宣传:通过各种渠道,如会议、邮 件、公告等,向员工宣传生产过程控制 制度与出厂检验记录制度的重要性和具 体要求。
培训与考核:对员工 进行培训,确保其掌 握操作规程和安全要 求,并进行考核
监督与检查:定期对 生产过程进行检查, 确保操作规程和安全 要求的执行情况
定期检查:定期对设备进行检查, 确保设备正常运行
设备维护与保养
定期保养:定期对设备进行保养, 延长设备使用寿命
添加标题
添加标题
添加标题
添加标题
及时维修:发现设备故障,及时进 行维修,避免影响生产
检验方法与流程
检验方法:采用抽样检验、全数检验等方法 检验流程:从原材料到成品,每个环节都要进行检验 检验标准:按照国家标准、行业标准或企业标准进行检验 检验记录:记录检验结果,包括检验时间、检验人员、检验项目、检验结果等
记录要求与保存期限
记录内容:包括产品名称、规格、数量、检验项目、检验结果、检验日期、检验人员等 记录格式:统一格式,便于查阅和管理 保存期限:根据产品特性和法律法规要求,一般保存3-5年 保存方式:纸质或电子形式,确保数据安全和可追溯性
生产过程控制制度与出厂 检验记录制度
目录
单击此处添加文本 生产过程控制制度 出厂检验记录制度 制度实施与监督
生产流程规范
生产计划:制定合理的生产计划,确保生产进度和质量 生产过程:严格按照生产工艺流程进行生产,确保产品质量 质量控制:在生产过程中进行质量控制,及时发现和解决质量问题 生产记录:详细记录生产过程中的各项数据,便于追溯和分析
生产过程控制和检验

生产历程控制和查验4.1 工场应对要害生产工序进行识别,要害工序操纵人员应具备相应的能力,如果该工序没有文件划定就不能包管产物质量时,则应制定相应的工艺作业指导书,使生产历程受控。
理解要点:1) 历程控制(Process control),指从要害元器件、质料的采购,直到加工出制品的全历程中对半制品、产物的质量进行监督、修正和控制的运动;2) 历程查验(Process testing),在历程控制中对要害元器件、质料,半制品,制品的划定参数进行的检测和验收;3) 工场应以明确的表达方法指明,哪些生产历程工序对认证产物的要害特性(宁静、环保、EMC)起着重要的作用;4) 工场应对在要害工序岗亭的人员能力提出具体要求,并包管在岗人员的能力切合划定的要求;5) 并非所有的工序都需要工艺作业指导书。
工艺作业指导书是否需要及其详略水平与操纵人员的能力、作业运动的庞大水平等有关。
只有在确认没有文件划定就不能包管认证产物质量时,工艺作业指导书才是必须的;6) 通常,工艺作业指导书应明确工艺的步调、要领、要求等,须要时,可包罗对工艺历程监控的要求。
审查要点:1) 通过查阅相关文件和现场视察,确认工场是否明确了要害生产工序;2) 通过查阅要害工序操纵人员的培训记载,并结合现场视察的情况,判断操纵人员是否具备相应的能力;3) 在现场审查时,注意在划定有工艺作业指导书的工序上,工艺作业指导书是否为有效版本,是否明确了控制要求。
操纵人员是否按工艺作业指导书进行操纵。
4.2 产物生产历程中如对情况条件有要求,工场应包管事情情况满足划定的要求。
理解要点:1) 情况条件包罗:温度、湿度、噪声、振动、磁场、照度、洁净度、无菌、防尘等;2) 工场应识别认证产物生产历程中为到达其切合要求所需的事情情况,应提供和治理相应的资源以确保事情情况满足划定要求。
工场还应对这些条件作出明确的划定,包罗具体的参数及控制要求(如果有);3) 在认证产物生产历程中,必须确认划定的条件已得到满足,不然不能进行生产运动。
- 1、下载文档前请自行甄别文档内容的完整性,平台不提供额外的编辑、内容补充、找答案等附加服务。
- 2、"仅部分预览"的文档,不可在线预览部分如存在完整性等问题,可反馈申请退款(可完整预览的文档不适用该条件!)。
- 3、如文档侵犯您的权益,请联系客服反馈,我们会尽快为您处理(人工客服工作时间:9:00-18:30)。
生产过程控制和检验4.1 工厂应对关键生产工序进行识别,关键工序操作人员应具备相应的能力,如果该工序没有文件规定就不能保证产品质量时,则应制定相应的工艺作业指导书,使生产过程受控。
理解要点:1) 过程控制(Process control),指从关键元器件、材料的采购,直到加工出成品的全过程中对半成品、产品的质量进行监视、修正和控制的活动;2) 过程检验(Process testing),在过程控制中对关键元器件、材料,半成品,成品的规定参数进行的检测和验收;3) 工厂应以明确的表达方式指明,哪些生产过程工序对认证产品的关键特性(安全、环保、EMC)起着重要的作用;4) 工厂应对在关键工序岗位的人员能力提出具体要求,并保证在岗人员的能力符合规定的要求;5) 并非所有的工序都需要工艺作业指导书。
工艺作业指导书是否需要及其详略程度与操作人员的能力、作业活动的复杂程度等有关。
只有在确认没有文件规定就不能保证认证产品质量时,工艺作业指导书才是必需的;6) 通常,工艺作业指导书应明确工艺的步骤、方法、要求等,必要时,可包括对工艺过程监控的要求。
审查要点:1) 通过查阅相关文件和现场观察,确认工厂是否明确了关键生产工序;2) 通过查阅关键工序操作人员的培训记录,并结合现场调查的情况,判断操作人员是否具备相应的能力;3) 在现场审查时,注意在规定有工艺作业指导书的工序上,工艺作业指导书是否为有效版本,是否明确了控制要求。
操作人员是否按工艺作业指导书进行操作。
4.2 产品生产过程中如对环境条件有要求,工厂应保证工作环境满足规定的要求。
理解要点:1) 环境条件包括:温度、湿度、噪声、振动、磁场、照度、洁净度、无菌、防尘等;2) 工厂应识别认证产品生产过程中为达到其符合要求所需的工作环境,应提供和管理相应的资源以确保工作环境满足规定要求。
工厂还应对这些条件作出明确的规定,包括具体的参数及控制要求(如果有);3) 在认证产品生产过程中,必须确认规定的条件已得到满足,否则不能进行生产活动。
审查要点:1) 通过询问或查阅相关文件的方式确认工厂是否识别出生产过程中对环境的要求;2) 按照规定的要求,采用查阅记录和现场观察的方法,确认环境条件是否得到满足。
4.3 可行时,工厂应对适宜的过程参数和产品特性进行监控。
理解要点:1) 在以下两种情况时,工厂应对适宜的过程参数和产品特性进行监控:a) 过程的结果不能通过以后的检验和试验完全验证,或者加工后无法测量或需实施破坏性测量才能得出结果;b) 过程对最终产品的安全质量、主要性能有重大影响。
2) 当过程参数和产品特性失控会使认证产品的质量失去保障时,应对此种可能做出相应的补救规定;3) 当过程参数和产品特性是以特定的软件进行监控时,生产厂应有相应的措施或规定,保持软件的正确使用,防止非正常使用。
审查要点:1) 通过查阅相关规定和调查询问的方式,确定有无需要进行监控的过程参数和产品特性;2) 通过查阅相关记录和现场观察的方式,了解对过程参数和产品特性进行监控的情况,确认其实施的符合性和有效性。
4.4 工厂应建立并保持对生产设备进行维护保养的制度。
理解要点:1) 凡是和生产认证产品相关的生产设备都须进行维护和保养;2) 维护和保养制度中的规定应确保生产设备正常运转,处于完好的技术状态,并能生产出符合要求的认证产品。
审查要点:1) 查阅与生产设备维护保养相关的文件,了解维护保养的要求;2) 按文件规定的要求,抽查维护保养计划和记录,确认其计划实施的符合性和有效性;3) 在现场通过观察和询问的方式了解生产设备的运行状态。
4.5 工厂应在生产的适当阶段对产品进行检验,以确保产品及零部件与认证样品一致。
理解要点:1) 工厂应针对认证产品的特点,在其形成的适当阶段设立检验/试验点,并明确其要求;2) 在检验/试验点上,须用明确的表示方法(如图纸、图片、模型、描述说明等)标明认证样品的特点(如名称、规格、型号、尺寸等);3) 检验的目的是为了确保认证产品的一致性。
审查要点:1) 通过查阅相关文件和询问的方式,明确检验/试验的工位(或类似检验/试验点);2) 通过在现场查阅记录和观察的方式,确认其实施结果可否达到检验的目的;3) 当无法实现检验目的时,请生产厂给出合理的解释,并确认其为实现检验目的所采用的保证方式。
5 例行检验和确认检验工厂应制定并保持文件化的例行检验和确认检验程序,以验证产品满足规定的要求。
检验程序中应包括检验项目、内容、方法、判定等,并应保存检验记录。
具体的例行检验和确认检验要求应满足相应产品的认证实施规则的要求。
例行检验是在生产的最终阶段对生产线上的产品进行的100%检验,通常检验后,除包装和加贴标签外,不再进一步加工。
确认检验是为验证产品持续符合标准要求进行的抽样检验。
理解要点:1) 例行检验(Routine test),在生产的最终阶段对产品的关键项目进行的100%检验,例行检验后除进行包装和加贴标签外,一般不再进一步加工。
在有些认证机构的文件中称为生产线试验(Production Line Test)是产品认证工厂审查时普遍要求的项目,也是与其他认证制度的工厂审查不同的项目。
其目的是剔除产品在加工过程中可能对产品产生的偶然性损伤,以确保成品的质量满足规定的要求;2) 确认检验(Verification test), 作为质量保证措施的一部分,为验证产品是否持续符合标准要求而由工厂计划和实施的一种定期抽样检验。
其目的是考核认证产品质量的稳定性,从而验证工厂质量保证能力的有效性;3) 认证实施规则中对例行检验、确认检验的要求有明确规定。
工厂应按认证实施规则的要求制定文件化的例行检验和确认检验程序并执行;4) 工厂制定的例行检验的项目应不少于认证实施规则的要求,确认检验的频次应不低于认证实施规则的要求。
确认检验可由工厂进行,也可由工厂委托具备能力的组织来完成;5) 例行检验和确认检验的记录应予以保存,其控制应符合2.3条的要求。
审查要点:1) 是否制定文件化的例行检验和确认检验程序,其规定是否适宜;2) 是否按程序要求进行例行检验和确认检验;3) 是否保存相关记录。
6 检验试验仪器设备用于检验和试验的设备应定期校准和检查,并满足检验试验能力。
检验和试验的仪器设备应有操作规程,检验人员应能按操作规程要求,准确地使用仪器设备。
理解要点:1) 生产厂应根据规定的检验试验要求来配备检验和试验设备,并确保这些设备的能力应能满足检验试验的要求(如量程、精度、数量等);2) 生产厂应针对检验和试验设备制定并执行相关规定;3) 生产厂配备的检验和试验设备及检验人员应能适应检验试验的需要。
审查要点:1) 查阅有关检验和试验设备的相关规定,并确认其能否保证检验和试验设备满足检验试验能力要求;2) 在现场审查时,注意观察检验人员是否按操作规程使用仪器设备;3) 通过现场观察和抽查检验人员培训记录等方式确认检验人员是否有能力准确使用仪器设备。
6.1 校准和检定用于确定所生产的产品符合规定要求的检验试验设备应按规定的周期进行校准或检定。
校准或检定应溯源至国家或国际基准。
对自行校准的,则应规定校准方法、验收准则和校准周期等。
设备的校准状态应能被使用及管理人员方便识别。
应保存设备的校准记录。
理解要点:1) 校准(Calibration),在规定的条件下,为确定测量仪器所指示的量值或实物量具的赋值与对应的由测量标准所复现值之间关系的一组操作。
校准一般不进行结果合格与否的判定;2) 检定(Verification),通过测量和提供客观证据,表明规定的要求已经得到满足的一组确认。
检定与测量仪器的管理有关,检定提供了一种方法,用来证明测量仪器的指示值与被测量已知值之间的偏差,并使其始终小于有关测量仪器管理标准、规程所规定的最大允差。
根据测量结果做出合格、降级使用、停用、恢复使用等决定;3) 溯源(Traceability),通过一条具有规定不确定度的不间断的比较链,使测量结果或测量标准的值能够与规定的参考标准(国家标准或国际标准)联系起来的可能性或过程;4) 生产厂应针对检验和试验设备的具体情况或特定要求,规定其校准或检定周期;5) 生产厂应选择具有相应资格的校准和/或检定机构(无论是本机构内部或外部的)对检验和试验设备进行校准和/或检定;6) 在检验和试验设备上使用表明校准状态的标识。
对于不能投入使用的检验和试验设备,一定要有醒目的标识,以防非预期使用。
审查要点:1) 查阅检验和试验设备一览表,确认其中的信息(包括校准或检定周期、校准或检定状态等)是否满足要求;2) 通过计量溯源图,计量机构的声明或类似文件了解溯源情况;3) 如有自行校准的情况,应查阅其规定,并确认是否合理、有效;4) 抽查现场使用的检验和试验设备是否有校准或检定记录,是否有易于识别的校准状态标识;5) 抽查保存的校准或检定记录,确认记录是否保存完好。
6.2 运行检查对用于例行检验和确认检验的设备除应进行日常操作检查外,还应进行运行检查。
当发现运行检查结果不能满足规定要求时,应能追溯至已检测过的产品。
必要时,应对这些产品重新进行检测。
应规定操作人员在发现设备功能失效时需采取的措施。
运行检查结果及采取的调整等措施应记录。
理解要点:1) 运行检查(Functional check),定期对检测仪器设备进行的功能性检查,以判断该仪器能否用于进行产品检测和质量判断;2) 当检验/试验仪器设备的好坏直接影响产品质量时,则不仅要求该仪器设备要按有关规定定期校准,确保仪器设备准确。
此外,还要求对仪器设备在两次校准期间以简单有效的方法确定设备功能是否正常;3) 需进行运行检查的设备限于进行例行检验和确认检验的设备;4) 工厂应明确需进行运行检查的设备,同时规定其检查的要求、内容、频次和方法,使能做到一旦发现设备功能失效时,可将上次检测过的认证产品追回重新检测;5) 当检测设备在使用或运行检查中发现失准或失效时,工厂应对以往检测结果的有效性进行评价,并采取必要的措施;6) 有关的运行检查、评价结果及采取的措施须有记录。
审查要点:1) 对用于例行检验和确认检验的设备是否规定了运行检查程序,其中的检查要求是否明确;2) 用于运行检查的样件是否进行了有效控制;3) 通过查阅运行检查记录和询问的方式,了解运行检查是否按要求得到实施,并保存了相应的记录;4) 通过查阅相关规定和询问设备操作人员的方式,了解操作人员在发现设备功能失效时,是否并如何采取措施;5) 工厂对发现设备失效时所采取的评价方法及相应措施是否适当;6) 抽查运行检查记录,并与现场调查的情况相比较;7) 设备失效时的结果评价及处理措施是否进行了记录。