主要半干法脱硫工艺机理分析
半干法脱硫方案
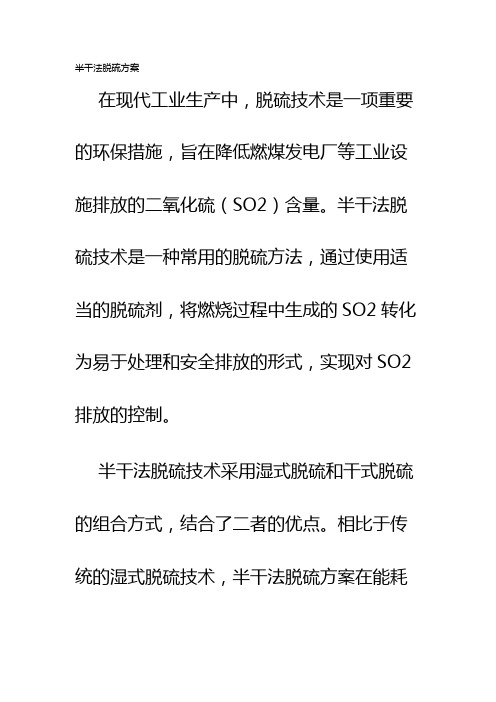
半干法脱硫方案在现代工业生产中,脱硫技术是一项重要的环保措施,旨在降低燃煤发电厂等工业设施排放的二氧化硫(SO2)含量。
半干法脱硫技术是一种常用的脱硫方法,通过使用适当的脱硫剂,将燃烧过程中生成的SO2转化为易于处理和安全排放的形式,实现对SO2排放的控制。
半干法脱硫技术采用湿式脱硫和干式脱硫的组合方式,结合了二者的优点。
相比于传统的湿式脱硫技术,半干法脱硫方案在能耗和脱硫产物处理上具有一定的优势。
下面将详细介绍半干法脱硫方案的原理、工艺和应用。
一、半干法脱硫方案的原理半干法脱硫方案的原理是在燃烧过程中将煤粉与适当的脱硫剂混合,通过加入脱硫剂,使SO2在燃烧过程中与脱硫剂发生反应,生成易于处理的脱硫产物。
脱硫产物经过除尘设备处理后,可以达到国家标准的排放要求。
半干法脱硫方案主要有两个关键步骤:煤炭预处理和脱硫剂喷射。
首先,煤炭经过破碎、干燥、磨碎等预处理工艺,使其适合于半干法脱硫的使用。
然后,脱硫剂通过喷射系统均匀地喷洒到煤粉中,与煤粉一起进入锅炉进行燃烧。
在燃烧过程中,脱硫剂与SO2发生反应生成脱硫产物。
二、半干法脱硫方案的工艺流程半干法脱硫方案的工艺流程主要包括煤炭预处理、脱硫剂喷射、燃烧和脱硫产物处理等几个关键步骤。
1. 煤炭预处理:煤炭经过破碎、干燥、磨碎等工艺处理,使其适合于半干法脱硫的使用。
2. 脱硫剂喷射:脱硫剂通过喷射系统均匀地喷洒到煤粉中,与煤粉一起进入锅炉进行燃烧。
3. 燃烧和脱硫:在锅炉中,煤粉和脱硫剂发生燃烧和反应,生成脱硫产物。
其中,脱硫剂参与了SO2的吸收和转化过程。
4. 脱硫产物处理:脱硫产物通过除尘设备进行分离和处理,得到符合排放要求的脱硫产物。
这个工艺流程中的每个步骤都需要精确的控制和操作,以确保脱硫效果和设备的安全运行。
同时,该方案的关键在于选择适当的脱硫剂和调整脱硫剂的用量,以最大程度地提高脱硫效率。
三、半干法脱硫方案的应用半干法脱硫方案广泛应用于燃煤发电厂等工业设施中,用于控制SO2的排放。
半干法脱硫
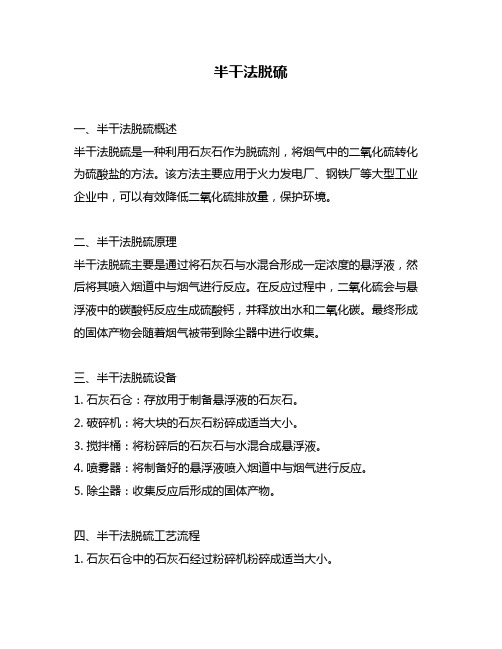
半干法脱硫一、半干法脱硫概述半干法脱硫是一种利用石灰石作为脱硫剂,将烟气中的二氧化硫转化为硫酸盐的方法。
该方法主要应用于火力发电厂、钢铁厂等大型工业企业中,可以有效降低二氧化硫排放量,保护环境。
二、半干法脱硫原理半干法脱硫主要是通过将石灰石与水混合形成一定浓度的悬浮液,然后将其喷入烟道中与烟气进行反应。
在反应过程中,二氧化硫会与悬浮液中的碳酸钙反应生成硫酸钙,并释放出水和二氧化碳。
最终形成的固体产物会随着烟气被带到除尘器中进行收集。
三、半干法脱硫设备1. 石灰石仓:存放用于制备悬浮液的石灰石。
2. 破碎机:将大块的石灰石粉碎成适当大小。
3. 搅拌桶:将粉碎后的石灰石与水混合成悬浮液。
4. 喷雾器:将制备好的悬浮液喷入烟道中与烟气进行反应。
5. 除尘器:收集反应后形成的固体产物。
四、半干法脱硫工艺流程1. 石灰石仓中的石灰石经过粉碎机粉碎成适当大小。
2. 粉碎后的石灰石与水在搅拌桶中混合成悬浮液。
3. 制备好的悬浮液通过喷雾器喷入烟道中与烟气进行反应。
4. 反应后形成的固体产物被带到除尘器中进行收集。
五、半干法脱硫优缺点1. 优点:(1)适用于高含硫量和高湿度的废气处理,效果显著;(2)设备简单,易于维护;(3)可以实现无二氧化硫排放或排放量显著降低。
2. 缺点:(1)对于低含硫量和低湿度的废气处理效果不理想;(2)需要大量使用石灰石作为脱硫剂,造成资源浪费;(3)在反应过程中会产生大量二氧化碳,对环境造成一定影响。
六、半干法脱硫的应用前景半干法脱硫技术具有较高的脱硫效率和经济性,已经被广泛应用于火力发电厂、钢铁厂等大型工业企业中。
随着环保意识的不断提高,半干法脱硫技术将会得到更广泛的应用和推广。
同时,随着科技的不断进步和发展,该技术也将会不断完善和优化。
半干法脱硫原理

半干法脱硫原理
半干法脱硫是一种常用的烟气脱硫技术,主要通过喷射干石灰粉末或半干石灰乳液来吸收烟气中的二氧化硫。
其基本原理是将石灰喷射到烟气中,石灰与二氧化硫发生化学反应形成石膏,将二氧化硫从烟气中去除。
半干法脱硫的主要过程包括喷射设备、石灰粉末输送系统和石膏排放系统等。
烟气经过除尘设备去除粉尘后,进入脱硫塔,同时喷射石灰粉末或半干石灰乳液。
石灰与二氧化硫反应生成石膏,石膏颗粒随石灰粉末一同沉积在脱硫塔底部的石膏池中。
经过脱硫后的烟气由脱硫塔顶部排出,排放到大气中。
半干法脱硫具有处理烟气中二氧化硫的效果好、适用于小颗粒煤粉燃烧、脱硫效率高等优点。
在半干法脱硫过程中,石灰粉末或半干石灰乳液通过喷射形成细小的液滴或粉末,增大了石灰颗粒与烟气接触的有效面积,提高了脱硫效率。
此外,脱硫过程中形成的石膏还可以作为一种有价值的资源,用于建筑材料、水泥生产等。
总之,半干法脱硫通过喷射石灰粉末或半干石灰乳液吸收烟气中的二氧化硫,从而实现了脱硫的效果。
该技术具有高效、适用范围广等特点,在工业生产中得到了广泛应用。
半干法烟气脱硫性能实验及其机理分析

第19卷第1期 电 站 系 统 工 程 Vol.19 No.1 2003年1月Power System EngineeringJan., 2003文章编号:1005-006X(2003)01-0049-04半干法烟气脱硫性能实验及其机理分析浙江大学 魏恩宗 程世庆 王乃华 高 翔 骆仲泱摘 要:选用富阳石灰作为实验研究的脱硫剂,研究了石灰浆液雾化粒径、反应产物进行再循环对半干法烟气脱硫效率的影响,并进行了机理分析。
还研究分析了增湿水对脱硫的强化作用以及脱硫塔轴向中心温度分布等情况。
关键词:半干法;烟气脱硫;性能实验中图分类号:TK411+.5 文献标识码:AExperiment on Performance of Semi-dry FGD Technology and Mechanism AnalysisWEI En-zong, CHENG Shi-qing, WANG Nai-hua, et al .Abstract: Fuyang lime is selected as the desulfurizing agent for experiment research. Influences of lime slurry size and product recycling on desulfurizing efficiency are investigated, and the mechanism is analyzed. Also, the enhancement on desulfurizing efficiency by added moisture and axial central temperature distribution of desulfurizing tower are detailed. Key words: semi-dry way; FGD; performance experiment由于以煤为主的一次能源构成,以及煤发热量低、含硫量高的特点,使我国二氧化硫污染日益严重。
半干法脱硫原理
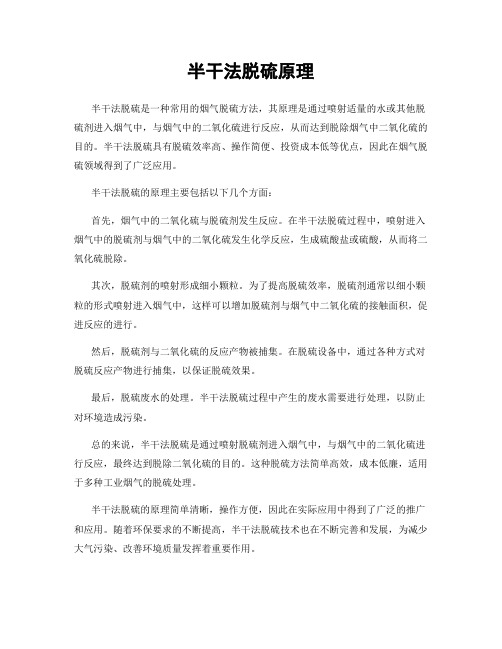
半干法脱硫原理
半干法脱硫是一种常用的烟气脱硫方法,其原理是通过喷射适量的水或其他脱硫剂进入烟气中,与烟气中的二氧化硫进行反应,从而达到脱除烟气中二氧化硫的目的。
半干法脱硫具有脱硫效率高、操作简便、投资成本低等优点,因此在烟气脱硫领域得到了广泛应用。
半干法脱硫的原理主要包括以下几个方面:
首先,烟气中的二氧化硫与脱硫剂发生反应。
在半干法脱硫过程中,喷射进入烟气中的脱硫剂与烟气中的二氧化硫发生化学反应,生成硫酸盐或硫酸,从而将二氧化硫脱除。
其次,脱硫剂的喷射形成细小颗粒。
为了提高脱硫效率,脱硫剂通常以细小颗粒的形式喷射进入烟气中,这样可以增加脱硫剂与烟气中二氧化硫的接触面积,促进反应的进行。
然后,脱硫剂与二氧化硫的反应产物被捕集。
在脱硫设备中,通过各种方式对脱硫反应产物进行捕集,以保证脱硫效果。
最后,脱硫废水的处理。
半干法脱硫过程中产生的废水需要进行处理,以防止对环境造成污染。
总的来说,半干法脱硫是通过喷射脱硫剂进入烟气中,与烟气中的二氧化硫进行反应,最终达到脱除二氧化硫的目的。
这种脱硫方法简单高效,成本低廉,适用于多种工业烟气的脱硫处理。
半干法脱硫的原理简单清晰,操作方便,因此在实际应用中得到了广泛的推广和应用。
随着环保要求的不断提高,半干法脱硫技术也在不断完善和发展,为减少大气污染、改善环境质量发挥着重要作用。
浅谈半干法脱硫技术问题及脱硫效率

浅谈半干法脱硫技术问题及脱硫效率半干法脱硫技术是一种将干法脱硫和湿法脱硫的优点结合在一起的高效脱硫技术。
相比于传统的湿法脱硫技术,半干法脱硫技术具有投资和运行成本低、脱硫效率高、废水处理量小等优点。
在实际应用中,半干法脱硫技术还存在一些问题,如脱硫效率不稳定、除硫副产物处理难题等。
本文着重从技术原理、问题分析及优化措施等方面进行讨论,以期为半干法脱硫技术的进一步发展和应用提供一些参考。
一、半干法脱硫技术原理半干法脱硫技术是将气态二氧化硫通过一个特殊的干法吸收剂(通常是石灰石或者石膏)进行吸收,形成硫酸钙或者硫酸钙镁等固体产物。
这一过程是在少量水蒸气的存在下进行的,因此称为“半干法”。
在脱硫过程中,通过合适的温湿条件,将硫酸钙或硫酸钙镁溶解成废水,再对废水进行处理,回收利用,实现资源的综合利用。
半干法脱硫技术的主要优点在于,一方面能够避免传统湿法脱硫过程中大量废水的产生,减轻了对环境的影响,由于脱硫产生的固体废物质量相对较小,更易于处理。
半干法脱硫技术还具有无需混合器、不易粘结、脱硫效率高等特点,使其在工业应用中具有很强竞争力。
二、半干法脱硫技术存在的问题和挑战尽管半干法脱硫技术有很多优点,但在实际应用中还是存在一些问题和挑战,需要引起重视。
脱硫效率不稳定和除硫副产物处理难题是最为突出的两个问题。
1. 脱硫效率不稳定半干法脱硫技术的脱硫效率受到影响的因素较多,包括进口烟气的温度、湿度、SO2浓度、吸收剂的性质和粒度等。
这些因素的变化都可能导致脱硫效率的波动,特别是在烟气条件较差的情况下,脱硫效率常常较低。
如何稳定提高半干法脱硫技术的脱硫效率成为了亟待解决的问题。
2. 除硫副产物处理难题在半干法脱硫技术中,除硫副产物是一种固体固化废物,处理问题一直受到人们的关注。
目前的处理方法主要是将硫酸钙或硫酸钙镁进行干态固化处理,然后再进行回收或综合利用。
由于硫酸钙或硫酸钙镁在干态下易形成结块,降低了其再利用的可能性,导致了一定的资源浪费。
半干法脱硫原理
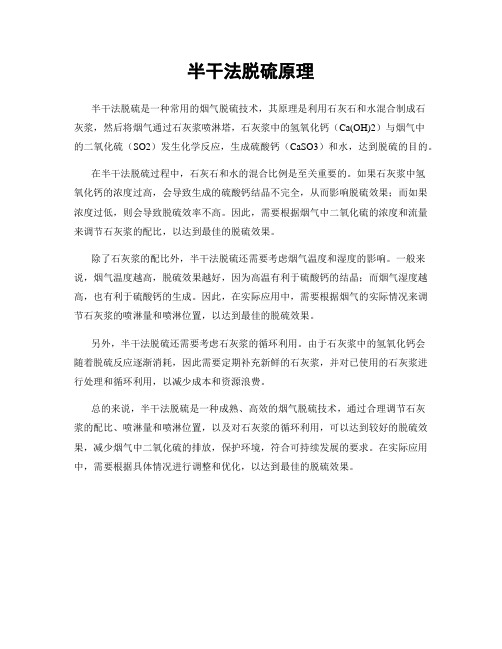
半干法脱硫原理
半干法脱硫是一种常用的烟气脱硫技术,其原理是利用石灰石和水混合制成石
灰浆,然后将烟气通过石灰浆喷淋塔,石灰浆中的氢氧化钙(Ca(OH)2)与烟气中
的二氧化硫(SO2)发生化学反应,生成硫酸钙(CaSO3)和水,达到脱硫的目的。
在半干法脱硫过程中,石灰石和水的混合比例是至关重要的。
如果石灰浆中氢
氧化钙的浓度过高,会导致生成的硫酸钙结晶不完全,从而影响脱硫效果;而如果浓度过低,则会导致脱硫效率不高。
因此,需要根据烟气中二氧化硫的浓度和流量来调节石灰浆的配比,以达到最佳的脱硫效果。
除了石灰浆的配比外,半干法脱硫还需要考虑烟气温度和湿度的影响。
一般来说,烟气温度越高,脱硫效果越好,因为高温有利于硫酸钙的结晶;而烟气湿度越高,也有利于硫酸钙的生成。
因此,在实际应用中,需要根据烟气的实际情况来调节石灰浆的喷淋量和喷淋位置,以达到最佳的脱硫效果。
另外,半干法脱硫还需要考虑石灰浆的循环利用。
由于石灰浆中的氢氧化钙会
随着脱硫反应逐渐消耗,因此需要定期补充新鲜的石灰浆,并对已使用的石灰浆进行处理和循环利用,以减少成本和资源浪费。
总的来说,半干法脱硫是一种成熟、高效的烟气脱硫技术,通过合理调节石灰
浆的配比、喷淋量和喷淋位置,以及对石灰浆的循环利用,可以达到较好的脱硫效果,减少烟气中二氧化硫的排放,保护环境,符合可持续发展的要求。
在实际应用中,需要根据具体情况进行调整和优化,以达到最佳的脱硫效果。
半干法脱硫工艺流程和原理

半干法脱硫工艺流程和原理今天来聊聊半干法脱硫工艺流程和原理。
你看啊,在日常生活里,我们想要去除东西上的污垢,总会有不同的办法。
就像要洗一块油渍渍的布,有的时候我们会用干的东西先吸一吸油,有时候会用水加一些清洁剂来洗,半干法脱硫呢,就有点像这两者的结合。
半干法脱硫一般是把石灰等碱性物质制成浆液(这里像我们弄的类似小清洁剂一样的东西),然后把这浆液喷到含硫的烟气里。
这里的硫啊,就好比是我们说的污垢。
石灰浆液中的主要成分氢氧化钙会和烟气里的二氧化硫发生反应。
这个反应就像是两个小伙伴见面了,然后紧紧抱在一起,变成了新的东西。
二氧化硫和氢氧化钙反应生成亚硫酸钙,这个过程就把有害的硫元素给抓住了,使它不再在烟气里捣乱。
打个比方吧,这就像是在一个满是小虫子(二氧化硫就像小虫子)的房间里,我们用一张带有魔力胶水(石灰浆液)的网,那些虫子一碰到网就被黏住了(发生化学反应)。
那半干法脱硫的流程是怎样的呢?首先含硫的烟气会进到反应器里,然后从底部或者侧向喷入石灰浆液。
在反应器里啊,二者充分混合进行反应。
这里面有个很重要的点就是温度的控制,就像我们做菜一样,火候很重要。
温度控制不好,可能反应就不完全。
一般在这个过程中还要确保有一定的水分存在,这样才能让反应更顺利,但是又不能太多水,不然就成湿法脱硫了,所以才叫半干法。
实际应用案例非常多,像一些中型的火力发电厂就常用半干法脱硫。
因为这种方法既不像湿法脱硫会产生很多的废水需要处理(处理废水就像收拾一大堆残局,很麻烦),又比单纯的干法脱硫效率要高很多。
说到这里,你可能会问,那怎么保证这个反应能持续有效地进行呢?这就要说到这个系统里还有一些尾气监测和调节环节,如果发现脱硫效果不好,像如果没黏住足够多的“小虫子”,那就会调节浆液的喷入量或者其他参数。
有意思的是,一开始我也不明白为啥一定要半干呢,直接干的或者湿的不是更简单?后来啊,发现这真的是一个权衡各方面利弊的好办法。
干的虽然简单,但是效率不高,湿的效率高但是废水多麻烦。
- 1、下载文档前请自行甄别文档内容的完整性,平台不提供额外的编辑、内容补充、找答案等附加服务。
- 2、"仅部分预览"的文档,不可在线预览部分如存在完整性等问题,可反馈申请退款(可完整预览的文档不适用该条件!)。
- 3、如文档侵犯您的权益,请联系客服反馈,我们会尽快为您处理(人工客服工作时间:9:00-18:30)。
几种半干法脱硫工艺机理的探讨葛介龙张佩芳戴永阳周钓忠李文勇张永(浙江菲达环保科技股份有限公司诸暨311800)摘要:本文总结循环半干法、烟道流化床、炉内喷钙炉后增湿活化、喷雾半干法等脱硫工艺的工程应用,就反应时间、操作温度、钙硫比、可靠性、燃料适应性、装置占地、性价比等进行了综合比较分析,并对上述四种主要半干法脱硫工艺进行了脱硫机理的探讨。
关键词:半干法、脱硫、性价比、机理、研究图1 NID 反应系统示意图 图2 CFB 反应系统示意图C 1、C 0分别为NID 和CFB 工艺反应器中的活性Ca(OH)2的浓度。
因为两种工艺都具有灰高倍比循环的特征,因此原烟气进入反应器后的0.3秒内,烟气温度即降到要求的75℃左右。
CFB 工艺的阻力降主要来自喉部及扩大段,系统总阻力较高,通常设计值为1800Pa 左右,而NID 工艺在反应器中的压力降分配则相对均匀,通常设计值为1200Pa 。
从图1、2中可以看出,两者的最明显区别在于工艺水加入位置的不同,正是由于这原理的区别,造成两技术以下性能上的明显差异。
CFB 工艺的特点是因喷嘴埋在流态不稳定、湿度不均匀的反应灰堆中,循环灰表面含水不均匀,且有游离的直径较大液滴浆团,易造成喷嘴及吸收塔惭扩段的粘堵,装置不能长周期稳定运行。
而NID 的特点是在一个外置的专有设备中对反应循环灰进行雾化增湿,灰表面水分呈均匀的薄膜状,且大量的循环物料具有巨大的蒸发表面,灰表面的水分蒸发很快,在1m 左右的反应器床层高度内使烟气温度降到75℃左右,达到理想的脱硫工况,达到90%以上的脱硫效率。
两种工艺的脱硫效率与反应时间的分布梯度见下图:烟气停留时间与脱硫效率关系2040608010000.40.8 1.2 1.62 2.4 2.8 3.2 3.64烟气停留时间t (秒)脱硫效率(%)图3反应时间与效率关系示意图 在整个脱硫反应过程中,NID 工艺的脱硫效率与反应时间的变化速率K 理论上说约是CFB 工艺的6倍。
因为脱硫反应可以理解为基元反应,根据化学反应碰撞理论,有效碰撞的机率与反应器中的反应物有效浓度成正相关:r=K ×C Ca(OH)2(l)×C SO2 (l)×e -RTCFB 工艺反应器喉部流速远高于NID ,但由于喉部无吸收剂,对提高脱硫效率无贡献。
NID 垂直反应段中的烟气流通截面积是CFB 的1/5,两种工艺需喷入的冷却水量几乎是相等的,循环灰量也几乎一样,因而NID 工艺反应器中的C Ca(OH)2是CFB 工艺反应器中的5倍。
在其它参数都一样时,NID 反应器中的脱硫速率(去除SO 2的摩尔数/单位时间)是CFB 工艺的5倍,即达到同样85~95%的脱硫效率,NID 工艺需的反应时间仅需CFB 工艺的1/5。
NID 工艺利用高度浓相的C Ca(OH)2浓度,可以理解为SO 2通过一个具有优良活性的Ca(OH)2(l)固体床层,在非常短的时间内即可实现快速的离子化脱硫,达到90%以上的脱硫效率。
在菲达公司已投运行十多套的采用浓相的循环半干脱硫工艺中,只要保证烟气在反应器中有0.9~1.3秒左右的停留时间,就足以保证90%以上的脱硫效率。
高且大直径的反应塔对于脱硫系统吸收平衡后进一步提高脱硫效率意义不大,设计的目的是为了尽可能干燥因内置式喷嘴造成湿度均匀性不稳定的增湿灰,减少在反应器内壁、除尘器内件及极板上的粘结。
脱硫的主反应式是:SO 2(l)+Ca(OH)2(l) →CaSO 3·1/2H 2O(s)+1/2H 2O (l )+Q ①反应式①是一个气液“双膜”控制的放热反应,除了Ca(OH)2(s)表面雾化水使之成为Ca(OH)2(l)是发生快速离子化脱硫反应的前提之外,加强气、固两相之间的相对流速,减少气、液两相间的传质阻力;另外,适当低的反应器操作温度也同样重要。
脱硫反应的关键是SO 2(g)的扩散并溶解,见下式:SO 2(g)→SO 2(l) ②SO 2(l)+H 2O(l) →H ++HSO 3- (l) ③步骤 ②的扩散阻力主要在气相中,步骤③的扩散阻力主要在液相中。
大直径吸收塔的边界滞流区及整个塔中3~3.5m/s 的低流速,烟气没有充分的紊流,气固两相之间没有较高的相对速率,不利于SO 2(g)的扩散并溶解成SO 2(l),也不利于在Ca(OH)2(l)小颗粒内部的扩散溶解,还将制约被生成物CaSO 3·1/2H 2O(s)覆盖的Ca(OH)2表面的更新,因而对提高脱硫效率效果有限。
高且大直径的反应塔的唯一作用仅是延长因雾化不均匀或团聚产生的粗大液滴的蒸发干燥时间,因为埋在灰堆中的回流或双流喷嘴,很难产生如喷雾半干法工艺一样相对均匀的中位径约为80μm 的小液滴,不可避免出现浆滴的团聚,出现湿灰团及浆团,国内已建成采用此类烟道流化床脱硫技术(CFB )的工程应用也表明:这种因粗大湿浆团不能及时干燥而出现系统设备的粘堵是不可避免的, 国内采用此技术出现装置不能长期期运行的主要症结都是这种未充分干燥的脱硫终产物不断粘堵造成的。
反应器中的浆滴的干燥图见下:浆液粒径与干燥时间关系12345678910102030405060708090100浆液粒径(μm)干燥时间(S )图4消石灰浆液滴直径与干燥时间关系图从图4可知,最大粒径100μm的消石灰浆雾滴,在70~80℃反应条件下,需12秒才能干燥到含水低于3%的水平,对于平均粒径100μm的水雾滴,需5秒充分蒸发,才不至于对后续的除尘器、引风机等设备造成粘堵等问题。
所以为使反应塔内喷浆的CFB脱硫系统设备及所配电除尘器不间断运行,设计烟气在反应器内的停留时间最好大于8秒。
但实际工程设计时,出于经济性考虑,一般按6秒左右设计。
荷电干法由于脱硫的环境相对较干,脱硫机理属慢速的亚硫化反应,在工业装置应用中,因受场地及经济性的限制,一般设计反应时间2秒,脱硫效率只能达到50~70%,目前几乎已退出市场。
喷雾半干法及炉内喷钙炉后活化两种脱硫工艺,保证装置能稳定运行的前提是保证脱硫终产物平均含水低于3%,所以工业装置设计的总脱硫时间都不低于8秒。
2.2.钙硫比就化学反应的本真动力学而言,影响反应速率的主要因素有温度、活化能、各反应物的有效浓度等,对于脱硫反应式①,在相同的反应温度状态下,其反应活化能是一样的,对此反应速率影响最大的因素是反应器不同床层高度中的SO2(l)和Ca(OH)2(l)的浓度。
就NID与CFB两种脱硫工艺而言,系统的温度控制原理及灰的循环比值基本一样,但因NID工艺反应器中的烟气流速明显高于CFB工艺,所以NID对高倍率的循环比具有更好的适应性。
NID工艺由于在反应器外设有特有的灰/水混合装置,反应产物中平衡的消石灰几乎100%的表面都被均匀增湿,在较小截面积的反应器中与溶解的HSO3-快速完成离子化脱硫反应。
而CFB工艺则由于喷嘴是埋在灰堆中,喷出的水对灰表面的增湿是不均匀的,尽管其循环灰量与NID差不多,但由于表面未被增湿的Ca(OH)2(s)几乎是没有脱硫活性的,与SO2(g)发生的是慢速的亚硫化反应。
据国外的研究:优质Ca(OH)2(s)在荷电弥散的状态下,反应5秒后的脱硫效率约50%。
另一方面,CFB工艺为保证粗大浆团在有限的脱硫时间内(5~6s)尽可能干燥,减小对后续收尘器的影响,反应器操作温度只能控制得高一些,一般为75~85℃,但这需要较高的钙硫比作为代价。
而NID工艺则不受此约束,根据脱硫效率及经济性的需要,反应器操作温度可任意选取并控制在65~85℃,在同样90%的脱硫效率下,钙硫比可同比下降0.1,因而具有的性价比优势。
浙江巨化热电厂的NID工程连续三年的运行表明:反应器出口温度每下降1℃,可节省消石灰约7kg。
NID和CFB在合理低的安全温度下运行,钙硫比都可以控制在1.2±0.1。
炉内喷钙炉后活化工艺,由于石灰石在最佳温度层的停留时间短,分解不彻底;在活化塔中活化不充分;脱硫灰没有再循环等因素,系统的钙硫比一般为2.3~2.5。
喷雾半干法脱硫在操作温度70℃左右运行时,钙硫比一般为1.4~1.6。
2.3.反应器操作温度反应器运行温度的设定要考虑设计脱硫效率、煤中的氯含量、钙硫比等诸多因素,当然也与选择的脱硫工艺有关。
反应温度越接近于烟气的酸露点,吸收剂表面的水分得以保持更长的时间,越有利于快速的离子化脱硫反应,脱硫效率可以更高,吸收剂的消耗量可以明显降低。
所以,对于循环灰是在反应器外的特有流态化混合器中预先均匀增湿的脱硫工艺来说,反应器的操作温度可选更宽的操作范围:65~85℃。
在燃用中硫煤(1.5~3.5%)时,控制适当低的操作温度,可明显降低吸收剂的消耗量。
浙江巨化热电厂的NID 脱硫工程正常燃煤含硫0.4~0.8%左右,设定反应器出口温度75℃,脱硫效率90~95%下运行,累计平均钙硫比为1.2左右;2001年9~10月期间,电厂试燃用平均含硫1.5%的中硫煤,在设定反应器出口温度70℃,脱硫效率90%下运行,累计平均钙硫比也为1.22左右,说明操作温度对脱硫效率及运行经济性的影响是非常明显的。
因为烟气的酸露点决定于三氧化硫浓度,在循环灰环境下,三氧化硫的去除率接近100%,故烟气的酸露点接近于水露点,约48~51℃。
所以在燃用高硫煤时,反应器和除尘器即使在65℃左右温度下运行,只要有合适的外保温,仍是安全的,不必担心出现腐蚀。
CFB 脱硫工艺由于受浆滴干燥因素的制约,操作温度只能控制得稍高些,一般为75~90℃,但钙硫比将比NID 时增加约0.1~0.2,经济性将受到较大的影响。
当然操作温度的选择与煤中的氯含量密切相关,因为烟气中的氯化氢先于SO X 与消石灰反应生成吸湿性极强的CaCl.2H 2O ,此时将不得不适当提高运行温度,以保证系统的稳定运行。
喷雾半干法和炉内喷钙炉后活化法工艺在加强吸收塔及出口烟道的防腐措施后,操作温度可降得更低,然后对塔出口烟气进行再加热,以此达到提高脱硫效率并降低物耗的目的。
2.4.燃料含硫的适应性循环半干法NID 和CFB 脱硫工艺都具有较宽的煤种变化适应性,在燃料中含硫低于2.5%或二氧化硫浓度低于7000 mg/Nm 3时仍有较好的经济性,对于NID 工艺,脱硫效率与入口烟气中的SO 2浓度关系如下:767880828486889092949630003500400045005000550060006500700075008000进口SO 2浓度(mg/Nm 3)脱硫效率(%)上图所示,当反应器入口SO 2浓度为5000mg/Nm 3左右,反应器操作温度为71℃左右时,脱硫效率仍达90%以上。
但燃用高硫份的燃料时,要注意区分达到脱硫效率和排放浓度的差别,达到设计的脱硫效率是相对较容易的,但同时达到较高要求的排放新标准就要难得多。