风电齿轮箱轴承寿命计算方法的研究
风机轴承寿命预测算法研究

风机轴承寿命预测算法研究随着风机技术的不断进步,风机轴承作为关键部件之一也越来越受到重视。
对于风电场运营商来说,风机轴承的寿命是影响电站生产经济效益的重要因素之一。
因此,提高风机轴承的寿命是一个非常重要的研究方向。
随着信息技术的飞速发展和应用,利用数据采集和分析技术进行风机轴承寿命预测已成为当前研究的热点之一。
一、风机轴承寿命的重要性风机轴承是风力发电机的重要部件。
随着风电行业快速发展,风机轴承的工作状态要求不断提高,对于风电场运营商来说,风电机组的可靠性和经济性至关重要。
在风电机组运行过程中,轴承的损坏会严重影响风电机组的运行,并直接降低发电效率和电站经济效益。
因此,提高风机轴承的可靠性和寿命,对于提高风电机组的经济性和可靠性具有重要的意义。
二、风机轴承寿命预测算法的研究现状1. 基于统计模型的寿命预测算法基于统计模型的寿命预测算法,最基本的思路是通过对轴承寿命数据的统计分析,建立寿命模型,然后根据模型进行风机轴承寿命预测。
常见的统计模型包括最小二乘法回归分析、生存分析等。
这类算法不需要考虑轴承的具体工作环境和工况,仅仅基于统计数据进行预测,适用范围较窄。
2. 基于物理模型的寿命预测算法基于物理模型的寿命预测算法,是将轴承的工作环境和实际工况考虑进去,结合物理学和数学建立轴承寿命模型,进行寿命预测。
这类算法需要建立完整的轴承模型,将轴承的力学、热学、磨损等因素综合考虑进去,预测精度较高。
但是建模和参数标定等任务较为繁琐,对算法研究人员的专业素质和经验要求较高,应用范围较窄。
3. 基于深度学习的寿命预测算法基于深度学习的寿命预测算法,是近年来的研究热点之一。
深度学习的特点是通过大量数据的训练来建立模型,具有良好的自适应性和泛化能力。
该类算法适用于轴承寿命预测场景,可以通过大量轴承振动、温度等各种传感器数据的采集,训练出具有较高预测精度的模型。
三、风机轴承寿命预测的关键技术1. 数据采集数据采集是风机轴承寿命预测的关键技术之一。
风力发电机组轴承的寿命分析与优化设计
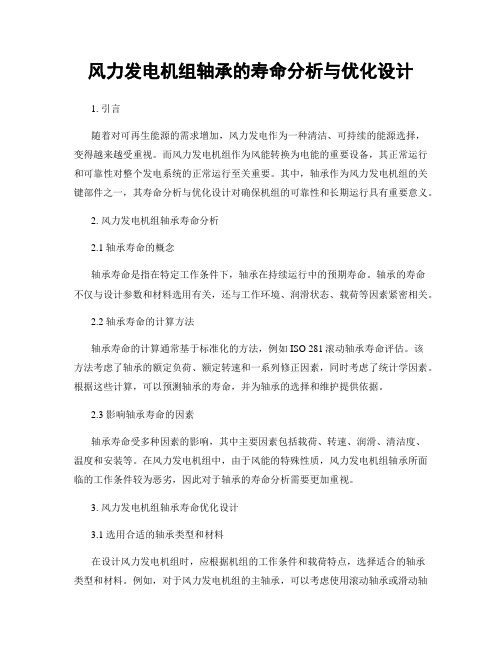
风力发电机组轴承的寿命分析与优化设计1. 引言随着对可再生能源的需求增加,风力发电作为一种清洁、可持续的能源选择,变得越来越受重视。
而风力发电机组作为风能转换为电能的重要设备,其正常运行和可靠性对整个发电系统的正常运行至关重要。
其中,轴承作为风力发电机组的关键部件之一,其寿命分析与优化设计对确保机组的可靠性和长期运行具有重要意义。
2. 风力发电机组轴承寿命分析2.1 轴承寿命的概念轴承寿命是指在特定工作条件下,轴承在持续运行中的预期寿命。
轴承的寿命不仅与设计参数和材料选用有关,还与工作环境、润滑状态、载荷等因素紧密相关。
2.2 轴承寿命的计算方法轴承寿命的计算通常基于标准化的方法,例如ISO 281滚动轴承寿命评估。
该方法考虑了轴承的额定负荷、额定转速和一系列修正因素,同时考虑了统计学因素。
根据这些计算,可以预测轴承的寿命,并为轴承的选择和维护提供依据。
2.3 影响轴承寿命的因素轴承寿命受多种因素的影响,其中主要因素包括载荷、转速、润滑、清洁度、温度和安装等。
在风力发电机组中,由于风能的特殊性质,风力发电机组轴承所面临的工作条件较为恶劣,因此对于轴承的寿命分析需要更加重视。
3. 风力发电机组轴承寿命优化设计3.1 选用合适的轴承类型和材料在设计风力发电机组时,应根据机组的工作条件和载荷特点,选择适合的轴承类型和材料。
例如,对于风力发电机组的主轴承,可以考虑使用滚动轴承或滑动轴承。
对于滚动轴承,需要选择适当的密封结构和润滑方式,以减少污染和磨损。
同时,轴承的材料也应考虑其抗疲劳和抗腐蚀性能,以提高寿命。
3.2 轴承运维管理风力发电机组轴承的运维管理是保证轴承寿命的关键。
应建立完善的维护管理制度,包括定期检查和维保计划、润滑管理、载荷监测等。
定期检查可以及时发现轴承的异常情况并采取相应的维修措施。
合理的润滑管理可以减少轴承的摩擦和磨损,延长寿命。
同时,通过载荷监测,可以了解轴承的实际工作状况,及时调整运行参数,以降低轴承的负荷,延长寿命。
海上风力发电用轴承的寿命评估方法研究

海上风力发电用轴承的寿命评估方法研究近年来,海上风力发电作为一种清洁、可再生的能源形式,在全球范围内得到了广泛的关注和推广。
而在海上风力发电项目中,轴承作为重要的机械元件之一,负责支撑转子和风轮等关键部件的运动,其寿命评估成为了提高发电系统可靠性和运行效率的关键因素。
轴承的寿命评估是指预测轴承在特定工况下的使用寿命,并根据寿命评估结果制定相应的维修和更换计划。
海上风力发电场的运行环境复杂,风速、波浪、腐蚀等因素都可能对轴承寿命产生影响,因此,对于海上风力发电用轴承寿命评估方法的研究具有重要意义。
一种常用的海上风力发电用轴承寿命评估方法是基于标准化的建模和试验数据。
通过收集和分析大量的实验数据,结合标准化的计算模型,可以得出轴承在特定工况下的寿命预测。
这种方法的优点是可靠性较高,可以较为准确地评估轴承的使用寿命。
然而,由于海上风力发电场环境复杂多变,单纯依靠标准化模型进行寿命评估可能存在偏差,需要结合实际运行数据进行修正。
另一种海上风力发电用轴承寿命评估方法是基于振动和温度监测的故障预测。
通过安装振动传感器和温度传感器,实时监测轴承的振动和温度情况,利用数据分析方法识别出轴承存在的故障特征,并根据这些特征预测轴承的寿命。
这种方法能够及时发现轴承故障,并进行相应的维修和更换,可以有效提高海上风力发电系统的可靠性和运行效率。
此外,还有一种基于物理模型的海上风力发电用轴承寿命评估方法。
通过建立轴承的物理模型,考虑各种载荷和环境因素对轴承的影响,使用数值分析方法预测轴承的寿命。
这种方法可以更加精确地评估轴承的寿命,但对于模型参数的准确性和确定性要求较高,需要进行大量的实验验证和数据分析工作。
综上所述,海上风力发电用轴承寿命评估方法是提高风力发电系统可靠性和运行效率的重要环节。
标准化建模和试验数据、振动和温度监测的故障预测,以及基于物理模型的评估方法都具备各自的优势和适用范围。
未来的研究可以继续深入探索这些方法的应用和改进,同时结合实际海上风力发电场数据,提高轴承寿命评估的准确性和实用性,为海上风力发电行业的发展贡献力量。
风力发电机组轴承的磨损机理与寿命预测模型研究

风力发电机组轴承的磨损机理与寿命预测模型研究1. 引言在可持续能源发展的背景下,风力发电作为一种环保和可再生的能源形式,逐渐受到世界各国的关注与重视。
风力发电机组作为风力发电系统的核心部件之一,其稳定运行对于实现高效发电至关重要。
而轴承作为风力发电机组的关键元件之一,其寿命与性能对整个风力发电系统运行的可靠性和稳定性具有重要影响。
因此,理解风力发电机组轴承磨损机理以及通过寿命预测模型对其进行管理和维护具有重大的现实意义。
2. 风力发电机组轴承磨损机理风力发电机组轴承磨损主要包括疲劳磨损和润滑脱层两种形式。
疲劳磨损是指轴承在长时间高速旋转下由于循环应力超过其疲劳极限而产生的磨损。
润滑脱层是指轴承润滑层由于摩擦、热量和化学因素的作用而逐渐脱落导致的轴承磨损。
而风力发电机组的运行环境恶劣、工作负荷大以及长时间的连续运行等因素,进一步加剧了轴承的磨损情况。
3. 轴承寿命预测模型研究轴承寿命预测模型的研究旨在通过数学模型和统计分析方法来估计轴承的寿命,从而提前预测轴承的失效时间,以便及时进行维护和更换。
目前,常用的轴承寿命预测模型包括基于经验模型、基于物理模型和基于统计模型等多种方法。
其中,基于统计模型的方法是当前研究的热点之一。
3.1 基于统计模型的轴承寿命预测方法基于统计模型的轴承寿命预测方法主要通过收集和分析大量历史数据,建立数学模型并应用统计方法来预测轴承的寿命。
常用的统计模型包括Weibull模型、Cox比例风险模型等。
这些模型通过拟合实验数据,得到轴承失效的概率分布函数,进而进行寿命预测。
3.2 参数估计方法参数估计方法是基于统计模型的轴承寿命预测中的关键一步。
常用的参数估计方法包括极大似然估计、最小二乘估计以及贝叶斯估计等。
这些方法可以通过优化算法来估计模型中的参数,以获得更准确的轴承寿命预测结果。
4. 轴承寿命预测模型的优化为了提高轴承寿命预测模型的准确性和可靠性,研究者们提出了一系列的优化方法。
风力发电机组轴承寿命预测方法的综合研究

风力发电机组轴承寿命预测方法的综合研究引言风力发电已成为全球范围内最主要的可再生能源之一,然而,由于风力发电机组风环境的不确定性以及复杂的工作条件,其轴承寿命预测一直是一个关键问题。
本文将对风力发电机组轴承寿命预测方法进行综合研究,旨在为可靠性评估和维护管理提供科学依据。
一、轴承寿命预测方法的概述风力发电机组的轴承寿命预测方法可以分为传统统计学方法和基于机器学习的方法两大类。
传统统计学方法主要基于轴承寿命统计数据进行参数估计,如Weibull分布函数、韦伯分布函数等。
基于机器学习的方法则根据大量数据样本进行模型训练,通常采用支持向量机、神经网络等算法。
二、轴承寿命预测方法的优缺点传统统计学方法具有计算简单、理论基础牢固的优点,但在预测精度上常常存在较大误差。
机器学习方法则可以通过模型训练不断优化,具有更高的预测精度,但对数据量和计算资源的要求较高。
三、基于特征提取的轴承寿命预测方法在轴承寿命预测中,特征提取是一个关键环节,合理的特征提取能够提高预测模型的准确性。
常用的特征包括振动信号的时域特征、频域特征和小波时频特征等。
通过提取轴承振动信号的特征,可以对其进行故障诊断和寿命预测。
四、基于机器学习的轴承寿命预测方法基于机器学习的轴承寿命预测方法通常分为监督学习和无监督学习两类。
监督学习方法需要事先标注好的训练样本,常用的算法包括支持向量机、随机森林等;无监督学习方法则不需要标注样本,常用的算法包括聚类分析、自编码器等。
这些方法可以根据实际需求选择合适的算法进行模型训练和预测。
五、综合预测方法的应用及效果评估综合预测方法将传统统计学方法与机器学习方法相结合,通过充分利用各种数据源和特征提取技术,提高轴承寿命预测的准确性和可靠性。
综合预测方法通常包括数据预处理、特征提取、特征选择和模型训练等步骤。
通过对实际案例的应用和效果评估,可以验证综合预测方法的有效性和可行性。
六、预测模型的优化和改进为进一步提高轴承寿命预测模型的准确性,可以进行模型的优化和改进。
风力发电增速齿轮箱的材料疲劳寿命预测和寿命管理

风力发电增速齿轮箱的材料疲劳寿命预测和寿命管理随着可再生能源的重要性日益凸显,风力发电作为一种清洁能源逐渐被广泛应用。
在风力发电系统中,齿轮箱是连接风机和发电机的关键组件之一。
然而,由于齿轮箱工作环境的复杂性和高负荷工况的要求,其材料疲劳寿命成为一个值得研究的重要问题。
齿轮箱的材料疲劳寿命预测是评估其可靠性和寿命管理的关键。
通过预测齿轮箱的材料疲劳寿命,可以及时发现并解决潜在的问题,从而提高齿轮箱的性能和可靠性,延长其使用寿命。
本文将介绍一种常见的预测材料疲劳寿命方法,并探讨如何进行齿轮箱的寿命管理。
材料疲劳寿命预测是通过分析材料的疲劳性能,预测其在特定工况下的寿命。
在风力发电系统中,齿轮箱的工作环境复杂,包括高速旋转、重载和不断变化的工况等。
因此,齿轮箱材料的疲劳寿命预测需要综合考虑多种因素。
一种常见的方法是使用应力-寿命(S-N)曲线,即疲劳强度与寿命的关系曲线。
通过对齿轮箱进行应力分析,确定其工作状态下的应力水平,然后利用S-N曲线预测材料的疲劳寿命。
除了S-N曲线方法外,还可以使用有限元分析(FEA)方法进行材料疲劳寿命预测。
有限元分析可以对复杂的齿轮箱结构进行精确建模,并模拟其在不同工况下的应力分布。
通过对应力分布进行疲劳强度计算,可以预测齿轮箱的材料疲劳寿命。
FEA方法的优势在于可以考虑更多的因素,如应力集中、材料非均匀性和应力历史等,从而提高预测的准确性。
齿轮箱的材料疲劳寿命预测是寿命管理的基础。
寿命管理是指通过定期检测、监测和评估,及时发现齿轮箱的问题并采取相应措施,以延长其寿命和保持其正常运行。
寿命管理包括以下几个方面:1. 定期检测和监测:定期对齿轮箱进行检测,包括振动检测、噪声检测和温度检测等。
通过检测和监测可以及时发现齿轮箱的故障迹象,避免由于故障引起的停机和损失。
2. 材料疲劳监控:通过监测齿轮箱的材料疲劳状态,包括应力水平、疲劳损伤和裂纹扩展等,可以预测齿轮箱的寿命,并制定相应的维护和修复策略。
风力发电增速齿轮箱的寿命评估与健康监测方法

风力发电增速齿轮箱的寿命评估与健康监测方法引言风力发电作为一种清洁能源,正逐渐成为全球能源结构调整的重要组成部分。
在风力发电系统中,齿轮箱是传动系统的核心部件之一。
然而,由于受到其特殊工作环境的影响,风力发电增速齿轮箱往往面临着严峻的工作条件,其寿命评估和健康监测显得尤为重要。
一、风力发电增速齿轮箱寿命评估方法风力发电增速齿轮箱的寿命评估旨在预测其使用寿命及剩余寿命,为运维工作提供依据。
以下是几种常见的风力发电增速齿轮箱寿命评估方法:1. 经验法经验法是根据历史数据和经验模型进行寿命评估的方法。
通过统计风力发电增速齿轮箱的故障数据和运行状况,建立对应的经验模型,预测齿轮箱的寿命。
然而,该方法主观性较强,可靠性有待提高。
2. 物理模型法物理模型法是基于齿轮箱的物理特性模型进行寿命评估的方法。
通过建立齿轮箱的运动方程和磨损模型,对齿轮箱进行剩余寿命预测。
这种方法相对较为精确,但需要准确的齿轮箱结构参数和工作参数。
3. 统计学方法统计学方法是利用统计学原理和方法对大量数据进行分析,预测寿命的方法。
通过统计齿轮箱的运行数据,建立统计模型并进行预测。
这种方法可以提高寿命评估的准确性,但依赖于大量的数据和统计分析能力。
二、风力发电增速齿轮箱健康监测方法风力发电增速齿轮箱的健康监测旨在实时监测齿轮箱的状况,及时发现故障并采取相应的维修措施。
以下是几种常见的风力发电增速齿轮箱健康监测方法:1. 声音监测通过对风力发电增速齿轮箱发出的声音进行监测分析,可以判断齿轮箱是否存在异常磨损或故障。
这种方法无需停机,实施便捷,但需要对声音信号进行复杂的分析处理。
2. 振动监测振动监测是通过对风力发电增速齿轮箱振动信号进行监测分析,以判断齿轮箱的运行状况和故障情况。
振动监测可实时获取齿轮箱的振动特征参数,可以较准确地判断齿轮箱是否需要维修或更换。
3. 温度监测温度监测是通过监测风力发电增速齿轮箱的各个部位温度变化,来判断齿轮箱是否存在异常情况。
风力发电机组的轴承寿命分析与优化

风力发电机组的轴承寿命分析与优化随着全球对可再生能源需求的不断增加,风力发电作为一种清洁、可持续的能源来源受到越来越多的关注。
在风力发电机组中,轴承作为关键部件,对整个系统的可靠性和性能起着至关重要的作用。
轴承寿命的分析与优化对于提高风力发电机组的运行效率、降低维护成本具有重要意义。
首先,我们需要了解什么是轴承寿命。
轴承寿命是指在特定运行条件下,轴承在无故障的情况下能够正常运行的时间。
轴承寿命的长短直接关系到风力发电机组的维护周期和使用寿命。
因此,分析轴承寿命并采取优化措施,对于延长风力发电机组的使用寿命、提高经济效益至关重要。
在分析轴承寿命方面,了解轴承的工作原理和运行特点是关键。
风力发电机组中常用的轴承有滚动轴承和滑动轴承两种类型。
滚动轴承由内圈、外圈、滚动体、保持架等组成,其工作原理是通过滚珠或滚子在内外圈之间传递负载,并减小摩擦。
滑动轴承则是通过润滑剂的润滑,使轴承轴承内外圈之间形成无润滑膜,降低摩擦系数。
针对滚动轴承,分析寿命的关键指标是疲劳寿命。
疲劳寿命是指轴承在一定载荷、速度和润滑条件下能够承受的周期次数。
常见的寿命评估方法有L10寿命、L50寿命、L90寿命等。
其中,L10寿命表示在统计意义下,轴承10%的寿命不低于某个指定容限。
L50寿命同样表示在统计意义下,轴承50%的寿命不低于某个指定容限。
L90寿命则是轴承90%的寿命不低于某个指定容限。
对于滑动轴承而言,寿命评估的关键指标是润滑膜磨损量。
润滑膜磨损量是指滑动轴承在特定工作条件下,润滑膜的磨损程度。
润滑膜磨损量的大小直接影响轴承的寿命。
常用的寿命评估方法包括B10寿命和B50寿命,类似于滚动轴承的L10寿命和L50寿命。
在优化轴承寿命方面,以下几点是需要考虑的重要因素:1. 选用合适的轴承材料和设计。
轴承材料是影响轴承寿命的关键因素之一。
选择适合工作条件的材料,如高强度、耐磨损和耐腐蚀的材料,能够提高轴承的寿命。
此外,合理的轴承设计也对寿命有重要影响,如设置适当的负荷分配、减小应力集中区域等。
- 1、下载文档前请自行甄别文档内容的完整性,平台不提供额外的编辑、内容补充、找答案等附加服务。
- 2、"仅部分预览"的文档,不可在线预览部分如存在完整性等问题,可反馈申请退款(可完整预览的文档不适用该条件!)。
- 3、如文档侵犯您的权益,请联系客服反馈,我们会尽快为您处理(人工客服工作时间:9:00-18:30)。
图1 FAG 轴承寿命修正系数计算流程图
除寿命外 , AG MA6006 标准还对轴承当量静负荷 时的最大接触应力作了规定 ( 见表 3 ) , 并给出了 pmax 的计算方法 。
表3 轴承的最大接触应力 轴承位置 最大接触应力/ MPa 高速轴 高速中间轴低速中间轴行星轮轴
( 2) 工作黏度 ν, 润滑剂在工作温度下的黏度 , 由
幅度降低 。
2 轴承寿命修正系数的计算及影响因
素分析
2. 1 修正系数计算方法
工作温度 t 和 40 ℃ 时的公称黏度按黏温曲线确定 。 黏度比 κ是一个表示油膜形成能力的指标 , 它以 量化的方式确定轴承工作的润滑条件 , 是计算轴承寿 命的一个基础系数 , 由定义可知要使轴承得到较好的 润滑条件 ,κ 应大于等于 1 , 但黏度比又不能过大 , 否 则黏度的增加可能会使轴承的工作温度升高 。 当 κ< 1 时应采用含极压添加剂 ( EP) 的润滑油 ,κ
TIMKEN
L nm = a1 a2 a3 da3 ka3 l a3 ma3 pa4 L 10
a3 k :载荷区域修正系数 a3 l :润滑修正系数 a3 m :偏心修正系数 a3 p :低载荷修正系数 a4 :有效寿命修正系数 。
ln
100RΒιβλιοθήκη a1 = (ln100 90
)
1
e
( 1)
式中 , R 为可靠度 , e 为韦布尔指数 。 G B/ T 6391 和 ISO281 都没有给出 axyz 的具体计算 方法 , SKF 和 INA 的计算方法基本相同 , 通过给定的条 件 , 可以得到数值不超过 50 的修正系数 ; FAG 给出的 方法与 SKF 类似 , 但修正系数由基本值乘以清洁度系 数得到 , 并限制基本值不超过 3 . 8 ; TIMKEN 提出的计
第 31 卷 第 5 期 风电齿轮箱轴承寿命计算方法研究 9
文章编号 :1004 - 2539 (2007) 05 - 0009 - 04
风电齿轮箱轴承寿命计算方法研究
( 郑州机械研究所 研发中心 , 河南 郑州 450052)
基本额 定寿命
修正额定寿命
L nm = a1 a xyzL 10 L nm = a1 a xyzL 10 L nm = a1 aS KFL 10 L nm = a1 a23 L 10 L nm = a1 avcL 10
系数说明
a xyz :寿命修正系数 a xyz :寿命修正系数 aS KF :寿命修正系数 a23 :材料和工作条件系数 avc :运行条件修正系数 a2 :材料修正系数 a3 d :清洁度修正系数
< 0 . 4 时必须使用含极压添加剂的润滑油。
本文仅对 FAG 和 SKF 的计算方法进行分析对比 。 为分析影响修正系数的各种因素 , 图 1 和图 2 分别为
FAG 和 SKF 寿命计算中修正系数的计算流程图 ( 图中
符号意义见相应的参考文献) 。 : 从图 1 和图 2 可以看出 FAG 轴承和 SKF 轴承的 计算方法中都考虑了运行条件 ( 工作温度 、 转速 、 载荷 大小) 、 润滑状况 ( 润滑油黏度 、 污染物水平 ) 等对轴承 寿命的影响 , 所不同的是 FAG 计算方法中通过载荷对 润滑和污染条件的影响进而影响修正系数 a23 ; SKF 将 载荷 、 润滑和污染条件一起作为影响修正系数 aS KF 的 基本因素考虑 , 但两者都将润滑条件量化为一个修正
表1 轴承寿命计算方法对比 计算方法
G B/ T 6391 ISO281 SKF FAG INA
L 10 = ( C 2 ) P
引言 随着现代材料和制造技术的提高 , G B/ T 6391 2003 《滚动轴承额定动载荷和额定寿命》 标准提出的轴
承寿命计算方法已难以适应需对轴承寿命进行精确计 算的场合 。在某些应用中 , 轴承实际工作寿命远远偏 离传统寿命计算公式得到的结果 , 某些应用场合下国 外先进轴承的实际使用寿命已是计算寿命的数倍乃至 数十倍以上 。由于轴承寿命的影响因素很多 , 目前的 轴承寿命计算方法仍在完善之中 , 国内外轴承寿命计 算并没有一个统一的为行业所接受的计算方法 , 国外 各大轴承生产厂商根据各自的研究成果和现场经验提 出了不同的轴承寿命计算方法 。 由于风电机组工作的特殊性和载荷的复杂性 , 轴 承是风电齿轮箱中一个相对薄弱的环节 。统计数据表 明 ,早期风电齿轮箱故障大多是由轴承引起的 ,随着现 场经验的增多 ,目前轴承引起的故障明显降低 ,但仍约 有 50 %的故障与轴承的选型 、 润滑或使用有关 。因 此 ,较为精确的轴承寿命计算方法对风电齿轮箱的设 计尤为重要 ,对影响风电齿轮箱轴承寿命的各种因素 进行深入分析也是十分必要的 。
L 10 m =
1
U1 L 10 m1
+
U2 L 10 m2
+
U3 L 10 m3
( 2)
+ …
图3 粘度比 κ的影响因素
其中 , L 10 m 为额定寿命 , L 10 m1 , L 10 m2 …… 为工作条件不 变的各时间段 U1 , U2 ……的分段寿命 。且满足 6 Ui
i =1 n
2. 2. 2 污染水平
( 温度上升 、 转速降低 、 污染物增多 ) , 轴承寿命可能大
图2 SKF 轴承寿命修正系数计算流程图
2. 2 轴承寿命影响因素分析
通过分析表 1 、 图 1 和图 2 , 可以得出轴承寿命影 响的主要因素 2. 2. 1 润滑条件 ( 1) 参考黏度 ν 1 , 它的涵义为在滚动接触面之间 形成一个足够把两个表面分开的润滑膜 , 润滑剂在正 常工作温度时必须保持一定的最小黏度以减少轴承摩 擦 , 提高轴承寿命 , 影响的主要因素为轴承平均直径 dm 和工作转速 n 。
1300 1650 1650 1450
表 2 和表 3 中的数值是基于 20 年寿命得到的 , 设 计寿命不同时 , 表中数据应相应调整 。 由于国家标准未提供切实可用的修正额定寿命计 算方法 , 而各公司提供的计算方法一般设计人员难以 掌握 , 而且计算表明绝大多数轴承的基本额定寿命很 难达到 130000 小时 , 因此国家标准提供的轴承计算方 法的可操作性不如 AG MA6006 标准 。此外 ,AG MA6006 标准指出轴承的运行温度 、 润滑油的黏度和清洁度及 转速等因素对轴承寿命有很大影响 , 运行状态变差时
董进朝 刘忠明
摘要 介绍了滚动轴承最新寿命理论和计算方法 , 讨论了这些计算方法的特点 , 并结合风电齿轮 箱的特点详细分析了影响轴承寿命的几种主要因素 。 关键词 寿命计算 滚动轴承 齿轮箱 是一个多因素影响系数 , 除了轴承类型的影响外 , 还包 括材料 、 润滑 、 环境 、 杂质颗粒 、 套圈中内应力 、 安装方 式、 轴承载荷等因素 。TIMKEN 计算方法则引入材料 修正系数 a2 、 运行条件修正系数 a3 和有效寿命修正 系数 a4 ; SKF 计算方法引入寿命修正系数 aX KF ; FAG 则引入基本系数 a23 Ⅱ和清洁度系数 s 。表 1 为各种计 算方法的对比 。 表 1 中 , C 为轴承的基本额定动载荷 , P 为轴承当 量动载荷 ,ε 为寿命指数 。各计算方法中 , a1 为可靠 度寿命修正系数 , 是考虑当可靠度不是 90 % 时 , 对寿 命的修正 , 计算公式见式 ( 1) 。
1 轴承寿命计算方法
我国轴承额定寿命计算标准 G B/ T 6391 - 2003 等 同采用 ISO 281 :1990 , 标准提供了轴承基本额定寿命 和修正额定寿命的计算公式 。世界著名的轴承生产厂 家也根据各自的研究成果提出了不同的修正额定寿命 的计算方法 ,如 SKF 、 TIMKEN 、 FAG 等 。这些计算方法 采用的基本额定寿命计算方法完全相同 , 修正寿命计 算公式大同小异 , 但具体计算方法不尽相同 。当轴承 的可靠度要求不同 ,或者希望更精确 、 更完善考虑轴承 质量和运转条件对其寿命的影响时 , 应采用修正额定 寿命 。各种修正额定寿命计算方法中可靠性系数的计 算完全相同 , 但其它系数的计算方法有所差异 。G B/ T6391 - 2003 ( ISO281 :1990) 引入寿命修正系数 a XYZ , 它
轴承寿命的影响量化为一单独的系数来考虑 ,而 SKF 和 FAG 轴承寿命计算方法则将压力隐含到某一系数 中与其他因素一起考虑 。
算载荷的大小是轴承寿命计算的重要依据 , 是齿轮箱 设计阶段最重要的参数 。SKF 和 FAG 等都给出了阶 梯载荷下的轴承寿命计算方法 , 这些计算方法基本相 同 。AG MA6006 标准强调轴承等零部件的计算应以载 荷谱为基础 ,给定载荷谱时 ,通常按等效载荷作为设计 计算的依据 。SKF 等给出的计算公式为
机械传动 2007 年 10
算方 法 较 复 杂 , 一 般 技 术 人 员 难 以 完 成 计 算 过 程 。
G B/ T 19073 标准规定风电齿轮箱轴承的修正额定寿
命不小于 130000 小时 , 按 G B/ T 6391 或轴承制造商的 计算指南进行计算 。但由于 G B/ T6391 修正额定寿命 计算方法中并未给出 aXYZ 的具体计算方法 , 因此一般 设计人员无法完成轴承的修正额定寿命计算 。而 AG 2
MA6006 标准仍以轴承的基本额定寿命作为判据 , 但根
系数来修正轴承的计算寿命 , 尽管 ISO281 中未明确给 出计算方法 , 但这些算法中轴承寿命的影响因素是基 本一致的 。
据轴承位置不同 , 规定了齿轮箱各处轴承的最小基本 额定寿命 , 见表 2 。
表2 轴承的最小基本额定寿命 轴承位置 高速轴 高速中间轴 低速中间轴 行星轮轴 低速轴 寿命/ 小时
此外 , 滚动表面间的压力也会改变润滑油的黏度 , 当黏压特性对黏度比的影响较大时 , 应对黏度比 κ 进 行修正 。影响黏度比 κ的因素见图 3 。 由图 3 可知 , 压力 , 平均直径 , 转速等对黏度比的 影响比较明显 。TIMKEN 轴承寿命计算方法将压力对