浅谈塑料产品设计中需考虑的模具因素
塑料制品模具设计影响因素探讨

工业技术科技咨询导报在我国塑料工业发展中,计算机的应用起到了很好的作用。
而计算机技术在模具设计领域的应用,大大缩短了模具设计时间, 尤其计算机辅助工程 (CAE 技术的大规模推广, 解决了塑料产品开发、模具设计及产品加工中的薄弱环节, 更在提高生产率、保证产品质量、降低成本等方面体现出现代科技的优越性。
但是现代技术并不能替代专业设计人员的经验,在塑料模具设计时制品材料的选择、及制品结构大小、壁厚的设计是决定模具设计、模具材料选用的重要因素。
而怎样选用合适的材料,就成为模具设计中一个重要的问题。
1 塑料制品材料种类用对模具设计的影响一般来说,并没有不好的材料,只有在特定的领域使用了错误的材料。
因此,设计者必须要彻底了解各种可供选择的材料的性能,并仔细测试这些材料,研究其与各种因素对成型加工制品性能的影响。
本文只就传统的热塑性材料进行分析以说明问题。
在注射成型中最常用的是热塑性塑料,它又可分为无定型塑料和半结晶性塑料。
这两类材料在分子结构和受结晶化影响的性能上有明显不同。
一般来说,半结晶型热塑性塑料主要用于机械强度高的部件,而无定型热塑性塑料由于不易弯曲,则常被应用于外壳,这是材料选用的大框。
另外,为改善热塑性塑料的使用性能和工艺性能,往往在制品原料中加入各种填料,因此,根据所加填料来选用就显得尤为重要了。
1.1 根据填料和增强材料进行选择的分析热塑性塑料可分为未增强、玻璃纤维增强、矿物及玻璃体填充等种类产品,不同产品的成型工艺性能是不相同的。
玻璃纤维主要用于增加强度、坚固度和提高应用温度; 矿物和玻璃体则具较低的增强效果,主要用于减少制品的翘曲。
例如,实际应用中玻璃纤维会影响到成型加工,使制品在成型后产生收缩和翘曲。
所以,玻璃纤维增强材料就不能被未增强热塑性塑料或低含量增强材料来替代,不然就会使制品的尺寸与设计尺寸发生不符。
此外,玻璃纤维在成型时的流动取向将引起制品机械强度的改变。
试验(从注射成型片的横向和纵向截取了 10个测试条,并在同一个拉力测试仪上对它们的机械性能进行了比较表明,对添加了 30%玻璃纤维增强的热塑性聚酯树脂,其横向的拉伸强度比纵向(流动方向低了 32%,挠曲模量和冲击强度分别减少了 43%和53%。
塑胶模具设计概述

塑胶模具设计概述塑胶模具设计是指通过计算机辅助设计软件对塑胶制品的实物模型进行数值分析、虚拟制造等技术手段,设计出合理的塑胶模具,在压制塑胶制品时使用,从而使得塑胶制品的生产工艺得到优化完善。
因此,塑胶模具设计是塑料制品生产中至关重要的一环。
一、塑胶模具设计思路塑胶模具设计,需要从整体上考虑塑料制品的结构、要求、生产工艺等多方面因素,进行全面综合的设计。
具体来说,设计思路应该包括以下方面:1. 塑料制品的形状和尺寸:首先,要了解塑料制品的形状和尺寸,根据产品的轮廓线和尺寸,完成上模和下模的设计。
2. 塑料制品的材质要求:考虑到不同塑料材料对模具、生产工艺的影响,应该综合考虑材料性能、加工工艺、成本等因素,选择合适的材料,对模具进行合理的热处理和表面处理,提高模具的耐磨性和使用寿命。
3. 塑料制品的表面要求:考虑到塑料制品表面的光洁度、平整度、尺寸稳定性等因素对产品外观质量的影响,设计师要在模具表面处理和抛光方面下功夫,使得产品表面光洁度达到要求,使产品的质量得以确保。
4. 塑料制品的生产效率要求:考虑到企业的生产效率问题,设计上模和下模时,应充分考虑压力、温度等控制因素,从而提高塑料制品的生产效率。
二、塑胶模具设计的主要步骤1. 模具设计的准备工作:首先,对于塑胶模具设计者而言,应该通过多方面了解产品的基本情况,确定产品要求,以及了解市场情况,明确用户的具体需求。
同时,根据产品的尺寸、形状、材料选择等多种因素,确定模具的工艺方案。
2. 模具设计方案的确定:在进行模具设计时,需要整合不同的信息资源,形成具体的设计方案。
在确定设计方案的过程中,需要充分考虑塑料产品的生产工艺、模具制作的技术、模具使用寿命等多种因素,从而设计出合理的模具。
3. 模具零件设计:模具设计的核心是模具零件的设计。
在进行模具零件设计时,需要考虑到气动元件、油压系统、电器控制系统等多种因素,确定模具零件的结构、材料、尺寸以及配合精度等要求。
塑料梳子注塑模具设计
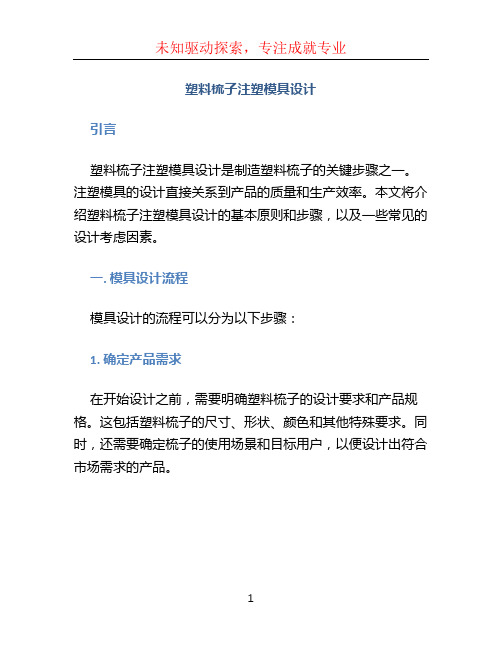
塑料梳子注塑模具设计引言塑料梳子注塑模具设计是制造塑料梳子的关键步骤之一。
注塑模具的设计直接关系到产品的质量和生产效率。
本文将介绍塑料梳子注塑模具设计的基本原则和步骤,以及一些常见的设计考虑因素。
一. 模具设计流程模具设计的流程可以分为以下步骤:1. 确定产品需求在开始设计之前,需要明确塑料梳子的设计要求和产品规格。
这包括塑料梳子的尺寸、形状、颜色和其他特殊要求。
同时,还需要确定梳子的使用场景和目标用户,以便设计出符合市场需求的产品。
2. 绘制产品草图根据产品需求,使用CAD软件或手绘草图绘制塑料梳子的三维图。
草图应包括梳子的各个部分,如梳齿、手柄和支撑结构。
草图的准确性和细节决定了后续模具设计的成功与否。
3. 模具结构设计根据产品草图,确定模具的结构和组成部分。
模具通常包括模具座、模芯、模腔和顶针等。
模具的结构设计应保证产品的精度和外观,并考虑到模具加工的可行性和生产的效率。
4. 水路和冷却系统设计在模具设计中,水路和冷却系统是非常重要的组成部分。
良好的水路和冷却系统可以有效提高塑料梳子的成品率和质量。
水路的设计应保证塑料材料在注塑过程中能够充分冷却,确保产品的尺寸稳定性和表面光洁度。
5. 进行模流分析模流分析是模具设计的关键步骤之一。
通过模流分析,可以评估塑料在模具中的填充情况和冷却效果,从而优化模具的设计。
模流分析还可以帮助预测可能出现的缺陷,如气泡、短斑和翘曲等,并采取相应的改进措施。
6. 模具加工和装配在完成模具设计之后,需要进行模具的加工和装配。
模具加工包括零件的加工和表面处理,如镜面抛光、喷砂等。
模具的装配包括各个零件的组装和调试。
模具加工和装配的质量和精度直接影响注塑工艺的稳定性和产品的质量。
二. 模具设计考虑因素在进行塑料梳子注塑模具设计时,需要考虑以下因素:1. 材料选择模具的材料选择直接影响到模具的寿命和稳定性。
常见的模具材料包括优质合金钢、不锈钢和铝合金等。
材料的选择应综合考虑模具的使用寿命、制造成本和加工难度。
塑料产品设计原则

塑料产品设计原则
1.结构设计原则
2.材料选择原则
在塑料产品的设计中,需要根据产品的使用要求和工艺要求选择合适的塑料材料。
选择塑料材料时需要考虑其物理、力学和化学性能,以及经济性和可塑性等因素。
3.成型工艺设计原则
塑料产品的成型工艺设计是塑料产品设计中的一个重要环节。
在设计过程中,需要考虑产品的形状、尺寸、壁厚等因素,以及成型工艺的选用和操作方法,确保产品成型质量和成本的控制。
4.模具设计原则
塑料产品的模具设计是影响塑料产品质量和生产效率的关键因素。
在模具设计过程中,需要考虑产品的形状、尺寸、壁厚等因素,以及模具的结构、材料和制造工艺等因素,确保产品的成型质量和生产效率。
5.附加工艺设计原则
6.人机工程学设计原则
7.环境保护设计原则
8.可维修性设计原则
9.创新设计原则
10.可持续发展设计原则
在实际的塑料产品设计中,需要根据具体的产品要求和设计目标,综合应用以上原则,灵活地进行设计。
只有在不断实践和总结的基础上,才能不断提高塑料产品设计的水平和效果。
塑料模具设计常见问题及改进方法

塑料模具设计常见问题及改进方法塑料模具是塑料制品生产的关键工具,其设计质量直接影响着产品的成型质量和生产效率。
在塑料模具设计过程中,常会遇到一些常见问题,例如设计不合理、成型不良等。
本文将介绍塑料模具设计常见问题及改进方法。
一、常见问题1.设计不合理在塑料模具设计过程中,设计不合理是最常见的问题之一。
设计不合理会导致模具结构复杂、易损件过多、成本增加等问题。
这些问题都会影响模具的使用寿命和生产效率。
2.成型不良成型不良也是常见的问题之一。
成型不良可能是由于模具设计不合理、材料选择不当、成型参数设置不正确等原因导致的。
成型不良会影响产品的质量,甚至导致生产事故。
3.模具寿命短模具寿命短是塑料模具常见问题之一。
模具寿命短可能是由于材料选择不当、表面处理不到位、使用条件不合理等原因导致的。
模具寿命短会增加生产成本,降低生产效率。
4.技术水平低一些塑料模具设计人员技术水平低也是常见问题。
技术水平低会导致设计不合理、制造精度低、模具寿命短等问题。
5.应力集中在塑料模具设计中,应力集中也是一个常见问题。
应力集中可能导致模具开裂、损坏等问题,从而影响模具的使用寿命和生产效率。
二、改进方法为了解决设计不合理的问题,可以通过优化设计来改进。
优化设计可以减少模具结构复杂度、减少易损件、降低成本等。
优化设计可以采用CAD软件进行模拟分析,找出设计不合理的地方并进行改进。
2.增加冷却系统成型不良的问题可以通过增加冷却系统来改进。
增加冷却系统可以有效降低成型温度、缩短成型周期、提高产品质量。
合理的冷却系统设计可以通过有限元分析和实验验证。
3.优化材料选择模具寿命短的问题可以通过优化材料选择来改进。
优化材料选择可以选择抗磨损、抗腐蚀、高强度的材料,从而提高模具的使用寿命。
还可以采用表面处理技术来提高模具的使用寿命。
为了解决技术水平低的问题,可以通过提高技术水平来改进。
提高技术水平可以通过培训、学习、实践等方式来进行。
提高技术水平可以提高设计水平、精度水平、制造工艺水平等。
塑料模具设计常见问题及改进方法

塑料模具设计常见问题及改进方法塑料模具设计在实际应用中,常常会遇到一些问题,影响生产效率和产品质量。
下面将介绍一些常见的问题,并提出改进的方法。
1. 精度不够:在塑料模具的设计和制造过程中,如果精度不够,会导致产品尺寸和形状的不一致,影响产品的质量。
改进方法可以通过使用高精度加工设备和工艺,并进行严格的质量控制来提高精度。
2. 成型件表面质量不良:塑料模具中常常会出现成型件表面出现纹痕、气泡、疤痕等问题,影响产品的外观和质量。
改进方法可以选择适合的模具材料,提高模具表面光洁度,调整模具温度和冷却系统等。
3. 模具寿命短:塑料模具在长时间使用过程中容易出现磨损、疲劳断裂等问题,导致模具寿命较短。
改进方法可以选择耐磨性好的材料制作模具,增加模具的强度和硬度,正确使用和维护模具等。
4. 模具结构复杂:一些塑料模具的结构比较复杂,设计和制造难度大,容易出现问题。
改进方法可以使用先进的设计软件和CAD/CAM技术,优化模具结构,简化模具制造过程,提高生产效率和产品质量。
5. 生产周期长:一些塑料模具的设计和制造周期较长,影响生产进度和交货时间。
改进方法可以使用模具快速制造技术,如快速加工和快速制造等,缩短模具的设计和制造周期。
6. 模具排气不畅:在塑料模具制造过程中,如果模具的排气不畅,容易产生气泡等缺陷,影响产品质量。
改进方法可以优化模具的设计和加工过程,设置合适的排气口和排气系统,并通过模具试验和调整来改善排气效果。
7. 模具变形:一些大尺寸或复杂结构的塑料模具在使用中容易发生变形,影响产品的尺寸精度和外观。
改进方法可以通过增加模具的刚性和稳定性,使用优质的模具材料,控制模具温度和冷却系统等来减少模具变形。
塑料模具设计常见问题的改进方法主要包括提高精度、改善表面质量、增加模具寿命、简化结构、缩短生产周期、优化排气系统和控制模具变形等。
通过不断改进和优化,可以提高塑料模具的生产效率和产品质量。
塑料注塑成型中的模具设计与优化
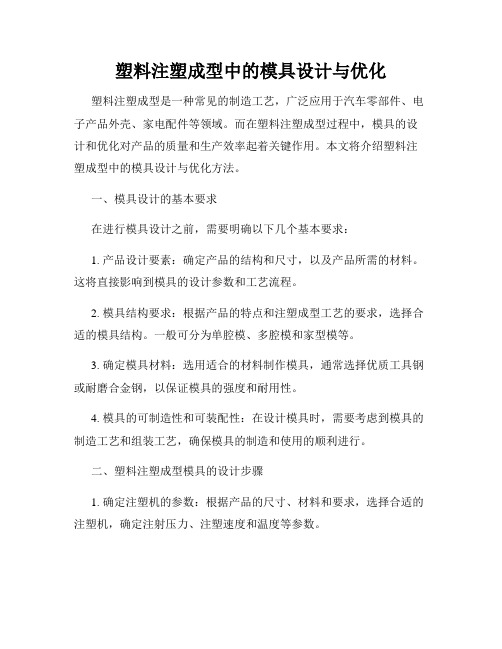
塑料注塑成型中的模具设计与优化塑料注塑成型是一种常见的制造工艺,广泛应用于汽车零部件、电子产品外壳、家电配件等领域。
而在塑料注塑成型过程中,模具的设计和优化对产品的质量和生产效率起着关键作用。
本文将介绍塑料注塑成型中的模具设计与优化方法。
一、模具设计的基本要求在进行模具设计之前,需要明确以下几个基本要求:1. 产品设计要素:确定产品的结构和尺寸,以及产品所需的材料。
这将直接影响到模具的设计参数和工艺流程。
2. 模具结构要求:根据产品的特点和注塑成型工艺的要求,选择合适的模具结构。
一般可分为单腔模、多腔模和家型模等。
3. 确定模具材料:选用适合的材料制作模具,通常选择优质工具钢或耐磨合金钢,以保证模具的强度和耐用性。
4. 模具的可制造性和可装配性:在设计模具时,需要考虑到模具的制造工艺和组装工艺,确保模具的制造和使用的顺利进行。
二、塑料注塑成型模具的设计步骤1. 确定注塑机的参数:根据产品的尺寸、材料和要求,选择合适的注塑机,确定注射压力、注塑速度和温度等参数。
2. 模具整体结构设计:根据产品的结构和尺寸,设计模具的整体结构,包括模具的型腔、型芯、导向机构等,并保证模具的生产效率和质量要求。
3. 流道系统设计:流道系统是模具中传递熔融塑料的管道系统,需要根据产品的结构和注塑工艺的要求进行设计,确保熔融塑料能够顺利注入模腔中。
4. 冷却系统设计:冷却系统是模具中的关键部分,可以通过冷却系统的设计合理调节模具温度,确保产品的质量和生产效率。
一般采用水冷却方式,需要在模具设计中合理布置冷却水路。
5. 塑料料斗和顶出机构设计:根据注塑成型的要求,设计合适的塑料料斗和顶出机构,以保证熔融塑料能够顺利注塑和产品能够从模具中顺利脱模。
三、模具设计的优化方法在塑料注塑成型过程中,模具设计的优化可以提高产品的质量和生产效率,降低生产成本。
以下是一些常用的模具设计优化方法:1. 流道长度和直径优化:流道的长度和直径对产品的注塑过程有着重要影响,应根据产品的尺寸和注塑机的要求进行合理设计,以减少产品的缩水和留痕。
模具设计原理及考虑

制件设计的一般考虑工程塑料制品大部分是用注射成型方法加工而成的,制件的设计必须在满足使用要求和符合塑料本身的特性前提下,尽可能简化结构和模具、节省材料、便于成型。
制件设计中应分别考虑如下因素:一、制件的形状应尽量简单、便于成型。
在保证使用要求前提下,力求简单、便于脱模,尽量避免或减少抽芯机构,如采用下图例中(b)的结构,不仅可大大简化模具结构,便于成型,且能提高生产效率。
二、制件的壁厚确定应合理。
塑料制件的壁厚取决于塑件的使用要求,太薄会造成制品的强度和刚度不足,受力后容易产生翘曲变形,成型时流动阻力大,大型复杂的制品就难以充满型腔。
反之,壁厚过大,不但浪费材料,而且加长成型周期,降低生产率,还容易产生气泡、缩孔、翘曲等疵病。
因此制件设计时确定制件壁厚应注意以下几点:1.在满足使用要求的前提下,尽量减小壁厚;2.制件的各部位壁厚尽量均匀,以减小内应力和变形;3.承受紧固力部位必须保证压缩强度;4.避免过厚部位产生缩孔和凹陷;5.成型顶出时能承受冲击力的冲击。
国外的一些常用塑料的推荐壁厚如下表:三、必须设置必要的脱模斜度为确保制件成型时能顺利脱模,设计时必须在脱模方向设置脱模斜度,其大小与塑料性能、制件的收缩率和几何形状有关,对于工程塑料的结构件来说,一般应在保证顺利脱模的前提下,尽量减小脱模斜度。
下表为根据不同材料而推荐的脱模斜度:具体确定脱模斜度时应考虑以下几点:1.对于收缩率大的塑料制件应选用较大的脱模斜度;2.对于大尺寸制件或尺寸精度要求高的制件应采用较小的脱模斜度;3.制件壁厚较厚时,成型收缩增大,因此脱模斜度应取大;4.对于增强塑料脱模斜度宜取大;5.含自润滑剂等易脱模塑料可取小;6.一般情况下脱模斜度不包括在制件公差范围内。
四.强度和刚度不足可考虑设计加强筋为满足制件的使用所需的强度和刚度单用增加壁厚的办法,往往是不合理的,不仅大幅增加了制件的重量,而且易产生缩孔、凹痕等疵病,在制件设计时应考虑设置加强筋,这样能满意地解决这些问题,它能提高制件的强度、防止和避免塑料的变形和翘曲。
- 1、下载文档前请自行甄别文档内容的完整性,平台不提供额外的编辑、内容补充、找答案等附加服务。
- 2、"仅部分预览"的文档,不可在线预览部分如存在完整性等问题,可反馈申请退款(可完整预览的文档不适用该条件!)。
- 3、如文档侵犯您的权益,请联系客服反馈,我们会尽快为您处理(人工客服工作时间:9:00-18:30)。
© 1994-2010 China Academic Journal Electronic Publishing House. All rights reserved.
浅谈塑料产品设计中需考虑的模具因素
哈尔滨哈轻塑胶有限公司 季晓冬
摘 要 本文简单地说明了在设计塑料产品的过程中,应注意到的有关模具的因素。
关键词 设计 模具 结构
塑料产品的设计与其它材料如钢、铜、铝、木材等的设计有部分是类似的,但是由于塑料材料组成的多样性,结构、形状的多变性,使得它比起其它材料更具设计特性,特别是它的形状设计、材料选择、加工方法的选择,更是其它大部分材料无可比拟的。
目前,我国绝大多数的塑料产品都采用注塑成型,注塑成型模具是这种生产方式中的关键设备,这就要求在设计塑料制品的同时要考虑其中的模具因素。
一、产品壁厚
产品的壁厚会直接影响到成型周期和生产效率,通常产品必须有均匀的壁厚,不均匀的壁厚会造成严重的翘曲以及尺寸控制问题,因此在设计产品壁厚时应注意:
11产品在满足机械强度的条件下应尽可能的使壁厚均匀一致,以防止缩痕产生。
21尽可能使产品不要出现尖角、大角度拐角,尽量多设计倒圆,以减少流动阻力。
31在产品外表面上有圆柱结构时,将其设计为空心,并且其厚度与高度应遵循:T =015-0175W ,H <5W (T 为圆柱壁厚,H 为圆柱高度,W 为产品壁厚)。
二、开模方向和分型线设计
每个注塑产品在开始设计时,首先要确定其开模方向和分型线,以保证尽可能的减少抽芯机构和消除分型线对外观的影响。
开模方向确定以后,产品的加强筋、卡扣、凸起等结构尽量设计成与开模方向一致,以避免抽芯减少拼缝线,延长模具寿命。
在符合产品功能的同时,尽量使产品的分型线简单化,易操作化,在产品不外露的地方,避免影响外观。
三、抽芯机构设计
在满足产品功能的条件下,尽量减少产品侧壁凸凹等卡勾的设计,或者是将卡勾设计成便于模具的出模。
当塑件按开模方向不能顺利脱模时,模具就需要增加抽芯结构,抽芯结构虽然能成型复杂产品结构,但易引起拼缝线、缩痕等缺陷,并增加模具成本,缩短模具寿命。
所以,如无特殊要求,应尽量避免抽芯结构。
例如,孔轴向和筋的方向改为开模方向,利用型腔型芯碰穿等方法成型。
见图1、图2所示。
四、变形设计
在塑件产品设计过程中,尽量避免平直结构,可
在产品上面做出凸凹形状,合理设置翻边、加强筋等,这样可以减少由应力产生的变形,还可增加产品强度,见图3、图
4所示。
图1
设计不合理
图2 设计合理
图3 设计不合理
图4 设计合理
五、脱模斜度
脱模斜度在产品设计的过程中是不可缺少的,因为塑件冷却收缩后多附在凸模上。
为了使产品壁厚平均及防止产品在开模后附在较热的凹模上,脱模斜度对应于凹模及凸模应该是相等的。
脱模斜度的大小没有一定的准则,多数凭借经验和依照产品深度来决定。
但是产品壁厚及材料的选择也应在考虑之中。
在产品设计中有很多误区,很多设计者在设计的时候没有想到过实际操作的可行性,等到真正加工的时候才发现很多错误。
所以说,一个好的产品设计者,是一定要从模具设计开始学起的,只有把将来实际操作中可能发生的问题都考虑进去,才能最大限度的减少错误的发生,才能设计出好的产品。
(02)
6
11 农 机 使 用 与 维 修
2009年第1期。