钢材热处理说明
钢的五种热处理工艺

钢的五种热处理工艺热处理工艺——表面淬火、退火、正火、回火、调质工艺:1、把金属材料加热到相变温度(700度)以下,保温一段时间后再在空气中冷却叫回火。
2、把金属材料加热到相变温度(800度)以上,保温一段时间后再在炉中缓慢冷却叫退火。
3、把金属材料加热到相变温度(800度)以上,保温一段时间后再在特定介质中(水或油)快速冷却叫淬火。
◆表面淬火•钢的表面淬火有些零件在工件时在受扭转和弯曲等交变负荷、冲击负荷的作用下,它的表面层承受着比心部更高的应力。
在受摩擦的场合,表面层还不断地被磨损,因此对一些零件表面层提出高强度、高硬度、高耐磨性和高疲劳极限等要求,只有表面强化才能满足上述要求。
由于表面淬火具有变形小、生产率高等优点,因此在生产中应用极为广泛。
根据供热方式不同,表面淬火主要有感应加热表面淬火、火焰加热表面淬火、电接触加热表面淬火等。
感应表面淬火后的性能:1.表面硬度:经高、中频感应加热表面淬火的工件,其表面硬度往往比普通淬火高2~3单位(HRC)。
2.耐磨性:高频淬火后的工件耐磨性比普通淬火要高。
这主要是由于淬硬层马氏体晶粒细小,碳化物弥散度高,以及硬度比较高,表面的高的压应力等综合的结果。
3.疲劳强度:高、中频表面淬火使疲劳强度大为提高,缺口敏感性下降。
对同样材料的工件,硬化层深度在一定范围内,随硬化层深度增加而疲劳强度增加,但硬化层深度过深时表层是压应力,因而硬化层深度增打疲劳强度反而下降,并使工件脆性增加。
一般硬化层深δ=(10~20)%D。
较为合适,其中D。
为工件的有效直径。
◆退火工艺退火是将金属和合金加热到适当温度,保持一定时间,然后缓慢冷却的热处理工艺。
退火后组织亚共析钢是铁素体加片状珠光体;共析钢或过共析钢则是粒状珠光体。
总之退火组织是接近平衡状态的组织。
•退火的目的①降低钢的硬度,提高塑性,以利于切削加工及冷变形加工。
②细化晶粒,消除因铸、锻、焊引起的组织缺陷,均匀钢的组织和成分,改善钢的性能或为以后的热处理作组织准备。
常用钢材热处理参数
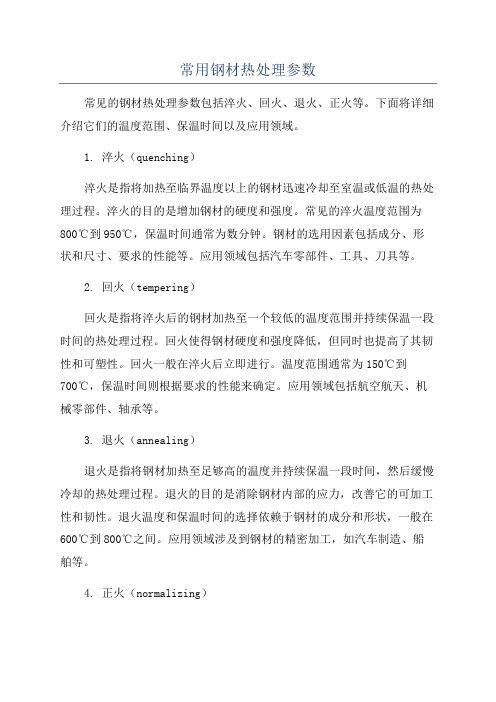
常用钢材热处理参数常见的钢材热处理参数包括淬火、回火、退火、正火等。
下面将详细介绍它们的温度范围、保温时间以及应用领域。
1. 淬火(quenching)淬火是指将加热至临界温度以上的钢材迅速冷却至室温或低温的热处理过程。
淬火的目的是增加钢材的硬度和强度。
常见的淬火温度范围为800℃到950℃,保温时间通常为数分钟。
钢材的选用因素包括成分、形状和尺寸、要求的性能等。
应用领域包括汽车零部件、工具、刀具等。
2. 回火(tempering)回火是指将淬火后的钢材加热至一个较低的温度范围并持续保温一段时间的热处理过程。
回火使得钢材硬度和强度降低,但同时也提高了其韧性和可塑性。
回火一般在淬火后立即进行。
温度范围通常为150℃到700℃,保温时间则根据要求的性能来确定。
应用领域包括航空航天、机械零部件、轴承等。
3. 退火(annealing)退火是指将钢材加热至足够高的温度并持续保温一段时间,然后缓慢冷却的热处理过程。
退火的目的是消除钢材内部的应力,改善它的可加工性和韧性。
退火温度和保温时间的选择依赖于钢材的成分和形状,一般在600℃到800℃之间。
应用领域涉及到钢材的精密加工,如汽车制造、船舶等。
4. 正火(normalizing)正火是指将加热至临界温度以上的钢材空气冷却至室温的热处理过程。
正火可以消除钢材内部的应力,改善它的可加工性和韧性。
正火温度范围一般为800℃到950℃,保温时间通常为数分钟。
应用领域包括汽车零部件、轴承、机械零件等。
此外,还有其他钢材热处理方法如奥氏体化退火、球化退火等针对不同的钢材类型和应用需求的热处理方法。
具体的热处理参数应根据材料的成分、形状和要求的性能来确定,并结合实际生产条件进行调整。
因此,在进行钢材热处理时,需要进行一系列的试验和分析,以确定最佳的处理参数。
第6章 钢的热处理
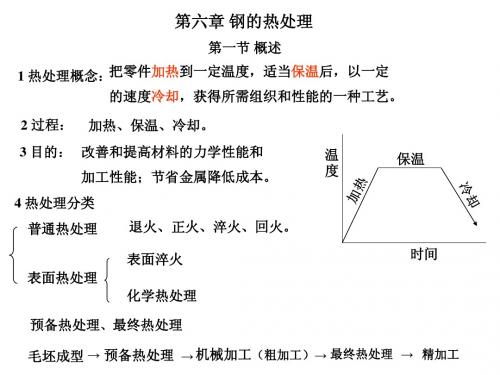
保温
普通热处理
退火、正火、淬火、回火。
表面淬火
表面热处理
时间
化学热处理
预备热处理、最终热处理 毛坯成型 → 预备热处理 → 机械加工(粗加工)→ 最终热处理 → 精加工
5 状态图中三条重要线及加热和冷却速度对线的位置的影响
A3 A1 0 0.77 2.11 4.3 6.69
硬度650HB,塑性和韧性差
原因:碳过饱和程度大,晶格畸变大,
淬火内应力大,存在显微裂纹,
容易导致脆性断裂的出现,微 细孪晶存在破坏了滑移系使脆 性增大,塑性和韧性差。
孪晶M
M的硬度主要取决于含碳量
M 转变是在 Ms ~ Mf 进行。
残余A量随含碳量的增多而增多,即C↑ → A残↑
(三)影响C曲线的因素
1 碳的影响
亚共析钢和过共析钢C曲线上部
多出一条先共析相析出线。
A过转变前,亚共析钢析出F,过共析钢析出Fe3C 剩下的A过达到共析成分,再发生P类型转变。
共析钢C曲线最靠右,所以:共析钢A过最稳定。
亚共析钢随含碳量↑, C曲线向右移, A过稳定性↑。
过共析钢随含碳量↑, C曲线向左移, A过稳定性↓。
A+F F+P
A + Fe3CⅡ P+ Fe3CⅡ
2 冷却介质的选择
保证有足够的冷却速度V冷>Vk;
V冷↑→ 热应力和组织应力↑ 650 ℃~ 400℃: V冷要快
650℃ 550℃ 400℃
vk
常用淬火介质:水、盐水、矿物油
水:在650℃~400℃冷速很大,对A稳定性较小的碳钢非常有利。 但300 ℃~200 ℃冷速仍很大,组织应力大,易变形和开裂。 盐水:由于NaCl晶体在工件表面析出和爆破,破坏包围在工件表面的 蒸 汽膜,使冷速加快,而且可以破坏加热产生的氧化皮,使其 剥落。盐水淬火容易得到高硬度和光洁表面。但300 ℃~200 ℃ 冷速仍很大,组织应力大,易变形和开裂。 适用于形状简单、硬度要求高、表面要求光洁、变形要求不严格 的碳钢零件,如:螺钉、销钉、垫圈等。 矿物油:冷却能力弱:650℃~550℃,18℃水的冷却强度为1, 则50℃
钢材技术要求-钢材热处理
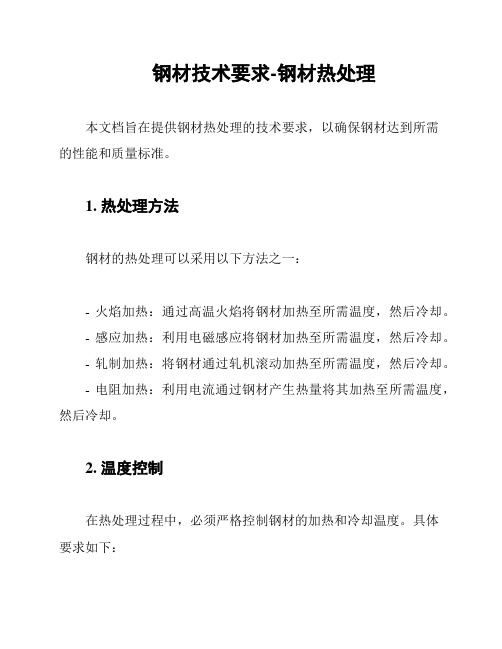
钢材技术要求-钢材热处理本文档旨在提供钢材热处理的技术要求,以确保钢材达到所需的性能和质量标准。
1. 热处理方法钢材的热处理可以采用以下方法之一:- 火焰加热:通过高温火焰将钢材加热至所需温度,然后冷却。
- 感应加热:利用电磁感应将钢材加热至所需温度,然后冷却。
- 轧制加热:将钢材通过轧机滚动加热至所需温度,然后冷却。
- 电阻加热:利用电流通过钢材产生热量将其加热至所需温度,然后冷却。
2. 温度控制在热处理过程中,必须严格控制钢材的加热和冷却温度。
具体要求如下:- 加热温度:根据钢材类型及所需性能确定加热温度范围。
- 保温时间:根据钢材的尺寸和厚度,以及所需性能,确定保持所需温度的时间。
- 冷却速率:根据钢材的组织结构和性能要求,确定合适的冷却速率。
3. 热处理工艺热处理工艺是指采用特定的加热、保温和冷却方法来改变钢材的性能和组织结构。
具体工艺应根据钢材的类型和性能要求来确定。
- 淬火工艺:通过迅速冷却钢材以获得高硬度和高强度。
- 回火工艺:在淬火后将钢材加热至适当温度并保持一段时间,以减轻内应力并提高韧性。
- 规定温度回火:在回火时严格控制温度,以确保钢材达到特定的硬度要求。
4. 检测和验收完成热处理后,应对钢材进行检测和验收,以确保其满足技术要求。
可采用以下检测方法:- 硬度测试:通过测量钢材硬度来评估其机械性能。
- 组织观察:通过金相显微镜观察钢材的组织结构来评估其质量。
- 化学成分分析:对钢材的化学成分进行分析以确保其符合规定标准。
以上就是钢材热处理的技术要求。
通过遵循这些要求,您可以确保钢材达到所需的性能和质量标准。
钢的热处理方法

钢的热处理方法钢是一种重要的金属材料,在工业生产和日常生活中得到广泛应用。
为了提高钢的性能和使用寿命,需要对钢进行热处理。
热处理是指通过控制钢材的加热和冷却过程,使钢材的组织和性能发生变化,从而达到预期的效果。
本文将介绍几种常见的钢的热处理方法。
第一种热处理方法是退火。
退火是将钢材加热到一定温度,保持一定时间后,缓慢冷却的过程。
退火可以消除钢材中的应力,改善钢材的塑性和韧性,提高加工性能。
退火分为全退火和局部退火两种。
全退火是将整个钢材进行退火处理,局部退火是只对钢材的某一部分进行退火处理。
退火的温度和时间需要根据钢材的成分和要求来确定。
第二种热处理方法是淬火。
淬火是将钢材加热到临界温度以上,然后迅速冷却的过程。
淬火可以使钢材的组织转变为马氏体组织,从而提高钢材的硬度和强度。
淬火的冷却介质可以是水、油或气体,不同的冷却介质会对钢材的硬度和组织产生影响。
淬火后的钢材通常需要进行回火处理,以提高其韧性和减少内应力。
第三种热处理方法是正火。
正火是将钢材加热到临界温度,然后在空气中冷却的过程。
正火可以使钢材的组织转变为珠光体组织,从而提高钢材的韧性和塑性。
正火的温度和时间需要根据钢材的成分和要求来确定,通常需要多次进行正火处理。
第四种热处理方法是回火。
回火是将淬火后的钢材加热到一定温度,保持一定时间后,缓慢冷却的过程。
回火可以降低钢材的硬度和脆性,提高其韧性和塑性。
回火的温度和时间需要根据钢材的成分和要求来确定,通常需要多次进行回火处理。
第五种热处理方法是表面处理。
表面处理是通过加热和冷却的方式改变钢材表面的组织和性能。
常见的表面处理方法包括渗碳、氮化、镀层等。
渗碳是将钢材加热到高温,使其表面吸收碳元素,从而提高表面的硬度和耐磨性。
氮化是将钢材加热到高温,使其表面吸收氮元素,从而提高表面的硬度和耐腐蚀性。
镀层是将钢材表面涂覆上一层金属或非金属材料,以改变其表面的性质和外观。
以上是几种常见的钢的热处理方法。
钢材热处理的四种方法
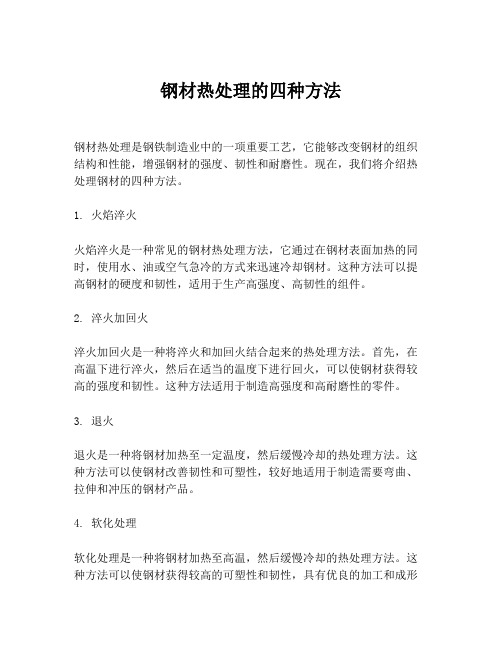
钢材热处理的四种方法
钢材热处理是钢铁制造业中的一项重要工艺,它能够改变钢材的组织结构和性能,增强钢材的强度、韧性和耐磨性。
现在,我们将介绍热处理钢材的四种方法。
1. 火焰淬火
火焰淬火是一种常见的钢材热处理方法,它通过在钢材表面加热的同时,使用水、油或空气急冷的方式来迅速冷却钢材。
这种方法可以提高钢材的硬度和韧性,适用于生产高强度、高韧性的组件。
2. 淬火加回火
淬火加回火是一种将淬火和加回火结合起来的热处理方法。
首先,在高温下进行淬火,然后在适当的温度下进行回火,可以使钢材获得较高的强度和韧性。
这种方法适用于制造高强度和高耐磨性的零件。
3. 退火
退火是一种将钢材加热至一定温度,然后缓慢冷却的热处理方法。
这种方法可以使钢材改善韧性和可塑性,较好地适用于制造需要弯曲、拉伸和冲压的钢材产品。
4. 软化处理
软化处理是一种将钢材加热至高温,然后缓慢冷却的热处理方法。
这种方法可以使钢材获得较高的可塑性和韧性,具有优良的加工和成形
性能。
总的来说,这四种方法是钢材热处理中较为基础和常见的方法。
每种方法都有其特定的优缺点和适用范围,因此在选择热处理方法时,需要结合不同的钢材类型和使用条件来进行选择。
钢材热处理的四种方法

钢材热处理的四种方法钢材热处理是指通过加热、保温和冷却等一系列工艺,改变钢材的组织和性能,以达到一定的技术要求。
在工程实践中,钢材热处理是非常重要的一环,可以有效提高钢材的硬度、强度、韧性和耐磨性等性能。
下面将介绍钢材热处理的四种常见方法。
首先,淬火是一种常见的钢材热处理方法。
淬火是指将钢材加热至临界温度以上,然后迅速冷却到室温或低温,使其组织发生相变,从而获得高硬度和高强度。
淬火是通过快速冷却来固溶过饱和的碳元素,形成马氏体组织,从而提高钢材的硬度。
淬火后的钢材具有较高的表面硬度和内部强度,适用于制作刀具、弹簧等工件。
其次,回火是钢材热处理的另一种重要方法。
回火是指将淬火后的钢材加热至较低的温度,保温一定时间后再冷却,目的是消除淬火产生的残余应力和改善硬度。
回火可以使钢材获得适当的硬度和韧性,提高其耐磨性和抗断裂性能,适用于制作各种机械零件和工具。
另外,正火是一种钢材热处理方法,也称为退火。
正火是将钢材加热至适当温度,保温一定时间后缓慢冷却,目的是使钢材内部组织发生均匀的晶粒再结晶和析出碳化物,从而获得较好的韧性和塑性。
正火后的钢材具有较低的硬度和较高的韧性,适用于制作焊接零件和需要较高韧性的零件。
最后,固溶处理是一种钢材热处理方法,主要用于不锈钢和高温合金等特殊钢材。
固溶处理是将钢材加热至固溶温度,然后保温一定时间后迅速冷却,目的是溶解钢材中的合金元素和固溶相,从而提高钢材的塑性和加工性能。
固溶处理后的钢材具有较好的塑性和韧性,适用于制作航空发动机零件和化工设备等高温高压工件。
综上所述,钢材热处理的四种方法分别是淬火、回火、正火和固溶处理。
每种方法都有其适用的钢材和工件类型,通过合理选择和控制热处理工艺参数,可以使钢材获得理想的组织和性能,满足不同工程要求。
在实际生产中,需要根据具体情况选择合适的热处理方法,以确保钢材具有良好的性能和可靠的使用寿命。
钢材热处理说明模板
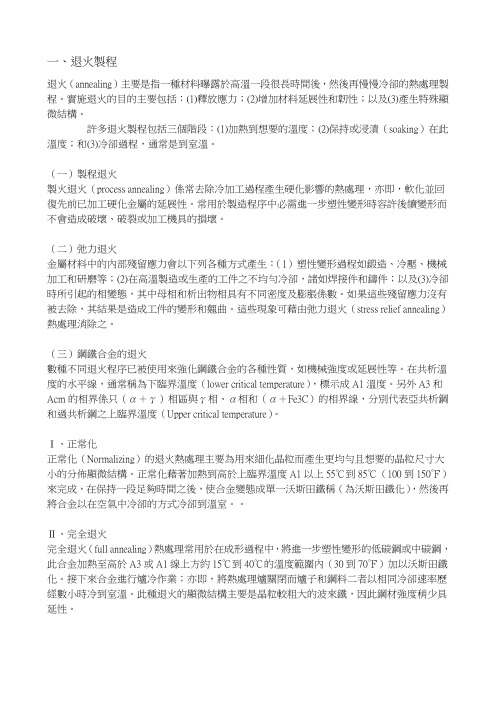
一、退火製程退火(annealing)主要是指一種材料曝露於高溫一段很長時間後,然後再慢慢冷卻的熱處理製程。
實施退火的目的主要包括:(1)釋放應力;(2)增加材料延展性和韌性;以及(3)產生特殊顯微結構。
許多退火製程包括三個階段:(1)加熱到想要的溫度;(2)保持或浸漬(soaking)在此溫度;和(3)冷卻過程,通常是到室溫。
(一)製程退火製火退火(process annealing)係常去除冷加工過程產生硬化影響的熱處理,亦即,軟化並回復先前已加工硬化金屬的延展性。
常用於製造程序中必需進一步塑性變形時容許後續變形而不會造成破壞、破裂或加工機具的損壞。
(二)弛力退火金屬材料中的內部殘留應力會以下列各種方式產生:(1)塑性變形過程如鍛造、冷壓、機械加工和研磨等;(2)在高溫製造或生產的工件之不均勻冷卻,諸如焊接件和鑄件;以及(3)冷卻時所引起的相變態,其中母相和析出物相具有不同密度及膨脹係數。
如果這些殘留應力沒有被去除,其結果是造成工件的變形和翹曲。
這些現象可藉由弛力退火(stress relief annealing)熱處理消除之。
(三)鋼鐵合金的退火數種不同退火程序已被使用來強化鋼鐵合金的各種性質,如機械強度或延展性等。
在共析溫度的水平線,通常稱為下臨界溫度(lower critical temperature),標示成A1溫度。
另外A3和Acm的相界係只(α+γ)相區與γ相、α相和(α+Fe3C)的相界線,分別代表亞共析鋼和過共析鋼之上臨界溫度(Upper critical temperature)。
Ⅰ、正常化正常化(Normalizing)的退火熱處理主要為用來細化晶粒而產生更均勻且想要的晶粒尺寸大小的分佈顯微結構。
正常化藉著加熱到高於上臨界溫度A1以上55℃到85℃(100到150℉)來完成,在保持一段足夠時間之後,使合金變態成單一沃斯田鐵稱(為沃斯田鐵化),然後再將合金以在空氣中冷卻的方式冷卻到溫室。
- 1、下载文档前请自行甄别文档内容的完整性,平台不提供额外的编辑、内容补充、找答案等附加服务。
- 2、"仅部分预览"的文档,不可在线预览部分如存在完整性等问题,可反馈申请退款(可完整预览的文档不适用该条件!)。
- 3、如文档侵犯您的权益,请联系客服反馈,我们会尽快为您处理(人工客服工作时间:9:00-18:30)。
一、退火製程退火(annealing)主要是指一種材料曝露於高溫一段很長時間後,然後再慢慢冷卻的熱處理製程。
實施退火的目的主要包括:(1)釋放應力;(2)增加材料延展性和韌性;以及(3)產生特殊顯微結構。
許多退火製程包括三個階段:(1)加熱到想要的溫度;(2)保持或浸漬(soaking)在此溫度;和(3)冷卻過程,通常是到室溫。
(一)製程退火製火退火(process annealing)係常去除冷加工過程產生硬化影響的熱處理,亦即,軟化並回復先前已加工硬化金屬的延展性。
常用於製造程序中必需進一步塑性變形時容許後續變形而不會造成破壞、破裂或加工機具的損壞。
(二)弛力退火金屬材料中的內部殘留應力會以下列各種方式產生:(1)塑性變形過程如鍛造、冷壓、機械加工和研磨等;(2)在高溫製造或生產的工件之不均勻冷卻,諸如焊接件和鑄件;以及(3)冷卻時所引起的相變態,其中母相和析出物相具有不同密度及膨脹係數。
如果這些殘留應力沒有被去除,其結果是造成工件的變形和翹曲。
這些現象可藉由弛力退火(stress relief annealing)熱處理消除之。
(三)鋼鐵合金的退火數種不同退火程序已被使用來強化鋼鐵合金的各種性質,如機械強度或延展性等。
在共析溫度的水平線,通常稱為下臨界溫度(lower critical temperature),標示成A1溫度。
另外A3和Acm的相界係只(α+γ)相區與γ相、α相和(α+Fe3C)的相界線,分別代表亞共析鋼和過共析鋼之上臨界溫度(Upper critical temperature)。
Ⅰ、正常化正常化(Normalizing)的退火熱處理主要為用來細化晶粒而產生更均勻且想要的晶粒尺寸大小的分佈顯微結構。
正常化藉著加熱到高於上臨界溫度A1以上55℃到85℃(100到150℉)來完成,在保持一段足夠時間之後,使合金變態成單一沃斯田鐵稱(為沃斯田鐵化),然後再將合金以在空氣中冷卻的方式冷卻到溫室。
Ⅱ、完全退火完全退火(full annealing)熱處理常用於在成形過程中,將進一步塑性變形的低碳鋼或中碳鋼,此合金加熱至高於A3或A1線上方約15℃到40℃的溫度範圍內(30到70℉)加以沃斯田鐵化。
接下來合金進行爐冷作業;亦即,將熱處理爐關閉而爐子和鋼料二者以相同冷卻速率歷經數小時冷到室溫。
此種退火的顯微結構主要是晶粒較粗大的波來鐵,因此鋼材強度稍少具延性。
Ⅲ、球化熱處理經球化熱處理後的鋼料具有相當良好的柔軟性和延展,因此且易於切割或變形加工。
球化(Spheroidizing)熱處理包括在剛好低於共析溫度下(即相圖之α+ Fe3C區域)加熱。
如果先前顯微結構包括波來鐵與肥粒鐵或片狀雪明碳鐵,則球化時間通常約介15 到25小時之間。
此一退火期間,片狀(或層狀)Fe3C碳化物將產生凝集而形成球化顆粒。
二、鋼之熱處理介紹鋼鐵熱處理的方法很多,各種熱處理的目的也不盡相同,但包含加溫、淬火急回火等熱處理技巧卻頻多相同之處。
本節先部隊熱處理技術作深入探討,先從其基本面的硬化能觀念作一說明。
產生麻田散鐵鋼之傳統熱處理程序,通常包含將已沃斯田鐵化試片急速冷卻到低溫的淬火介質中,如水、油或空氣。
鋼料整個截面產生主要是麻田散鐵顯微結構,主要視三個因素而定:(1)合金的成分;(2)淬火介質的型式和特性;以及(3)試片的尺寸和形狀。
(一)硬化能概念對一已知特殊淬火處理而言,合金元素對鋼鐵材料變態成麻田散鐵之能力的影響,與硬化能(hardenability)的參數有關。
常被用來決定硬化能的標準程序是Jominy端面淬火試驗。
使用此一程序時,除了合金成分外,所有會影響試片硬化深度的因素,包括試片尺寸和形狀、以及淬火處理條件)等均需固定,才能決定其硬化能曲線。
(二)硬化能曲線典型硬化能曲線,因淬火端冷得最快而擁有最大硬度;對大部份的鋼材而言,在此位置的顯微結構為100%麻田散鐵。
冷卻速率與由淬火端算起之距離成反比,其硬度也跟著減低由於減小冷卻速率使得碳有更多時間進行擴散,因而產生大部份為柔軟的波來鐵,當然可能混有麻田散鐵和變韌鐵。
能高度硬化的鋼在相對長的距離,將能保持高硬度值,因此可加深硬化層厚度及熱處理性能。
舉例說明1040鋼的硬化能很低,因為其硬度在相對短的Jominy距離就很陡峭地下降。
藉著曲線間的相對結果,大部分合金鋼的硬度之下降明顯地較為和緩。
在Jominy距離50mm(2in)試驗中,4340和8640合金鋼的硬度大約分別為50HRC和32HRC;因此,對此二種合金而言4340合金鋼是較能硬化的。
1040普通碳鋼之水淬試片只能硬化到表面下很淺薄的深度,但對其它具有高淬火硬度的四種合金鋼而言,其具有較的硬化深度。
(三)淬火介質前面硬化能部份主要探討合金成分以及淬火速率對硬度、硬化能及硬化深度的影響。
試樣的冷卻速率需視被吸收熱量的速率而定,而收吸熱量的速率除與材料特性有關外,亦與接觸試樣表面之淬火介質的特性,以及試樣尺寸與幾何形狀有關。
常用為淬火的三種介質包括水、油和空氣,其中水產生最激烈的淬火現象,其冷卻速率最快。
其次為油,比空氣之淬火更有效。
當然每種介質的攪拌程度也會影響熱量被移走的速率。
三、選材及問題探討(一)高洲波表面淬火硬化1.選材:*中碳剛、中碳低和金剛、鑄鋼、鑄鐵等均可施予高週波表面硬化處理。
2.加工程序:*粗加工→應力消除退火→精加工→淬火→高溫回火→粗磨→預熱→高週波加熱淬火→低溫回火→精磨3.淬火—高溫回火(俗稱〝調質〞):*常用鋼種及其調質硬度*S45C:HRC26±2,SCM440:HRC28±2,SNCM439:HRC30±2*母材硬度不宜太軟—易產生硬化層剝裂。
*母材硬度也不宜太軟—易產生高週波加熱破裂。
4.預熱:常用鋼種之預熱溫度*S45C(低限碳當量)免預熱*S45C(高限碳當量或大型件)100℃以上*SCM440 150℃以上*SNCN439 200℃以上*碳當量較高之剛種,預熱溫度需較高,但最高以350℃為限。
*母材較硬(HRC30以上)者,必須充分預熱。
*若以加熱線圈預熱,宜分數次加熱,且勿使其表面溫度超出母材之回火溫度(或應力消除退火溫度)—否則可能產生變形。
5.高週波頻率:*是所需要有效硬化層厚度選擇是當之頻率。
頻率越高,硬化層越薄。
6.高週波淬冷停止溫度:*高週波淬火,需是母材鋼種而在適當之溫度停止淬冷,以免產生淬裂。
*S45C:約100℃,SCM440:約150℃,SNCM439:約200℃7.回火:*淬火後,必須適時(50~60℃)施予150~200℃之低溫回火。
*切勿放冷過度,以免產生延遲回火破裂。
*也不宜太早(溫度太高)回火,否則其表層硬度會較低。
8.硬度測定:HRC測定其硬度,那只能估計母材內部硬度及有效硬化層厚度,而不是該處理件之表面硬度。
9.精磨:*高週波表面硬化處理件之表面硬度高達約HRC60(碳鋼)或HRC60以上(合金鋼),故研磨處理件表層時,進刀量每道以約.005㎜~0010㎜為度,且必須充分冷卻,並適時削銳砂輪面,以免產生研磨表面龜裂。
(二)滲碳表面硬化處理:1.選材:低碳鋼或低碳低合金鋼*低碳鋼:S09CK、S15CK、S20CK*合金鋼:SCr415、420;SCM415、418、420、421、822;SNCM220、415、420、616、815 *含碳量.15%之鋼種,滲碳—淬火後母材內部硬度在HRC30以下,韌性較佳,含強度稍低。
*含碳量020%之鋼則硬度在HRC30以上,強度較高而韌性稍差。
兩者必須視其用途而區分,切勿混用。
2.加工程序:*粗加工→應力消除退火→精加工→滲碳→淬火→低溫回火→精磨3.滲碳—淬火處理及回火處理:*滲碳後必須擴散處理,將最表層含碳量降至約08%,並將滲入之碳往內部擴散,以期緩和硬度分佈曲線之陡度,增加有效硬化層厚度。
滲碳,擴散後,宜降溫至800~850℃出爐油淬至100~150℃(碳鋼)或150~200℃(合金鋼),然後空冷至50~60℃,適時送入回火爐(150~200℃)回火。
4.滲碳處理時間、厚度及硬化層性質:*滲碳處理時間視所需有效硬化層度而定,通常處理1~10小時,有效厚度0.3㎜~㎜,最表層硬度均在HRC60以上(合金鋼HRC61~62)。
與滲氮處理比較,處理溫度較高,且須淬冷,故變形量較大,表面硬度也較低,耐磨耗性,耐熱性,耐蝕性及耐熔蝕性等均較差;但其處理時間短,有效硬化層叫厚,能承受較大之負載。
(三)滲氮(氮化)處理1.選材:中碳合金鋼或高碳合金鋼。
*最常用之中碳合金鋼為SACM645及SKD61,高碳合金鋼則為SKD11、DC53、SKH51等。
SCM440或SNCM439等中碳低合金鋼也可以滲氮,但效果不佳。
*碳鋼除了離子滲氮,不能作滲碳處理。
2.加工程序:3.淬火—高溫回火(調質):*滲氮處理件必須先施予調質(至該鋼種合理之使用硬度),其回火溫度必須高於滲氮處理溫度。
*SACM645:HRC32~35、SKD61:HRC45~49、SKD11:HRC56~58,DC53:HRC58~61、SKH51:HRC62~64。
4.滲碳處理溫度、時間、厚度及硬化層性質:*滲氮處理通常在500~600℃溫度範圍進行,但必須稍低於母材調質時之回火溫度,以免變形量加大。
常見之滲氮時間為40~100小時,可獲有效硬化層厚度0.02~0.3㎜。
*滲氮層之最表層為氮化物層,硬度高達HV1000以上,但厚度僅為.010㎜(10μm)以下。
最外層為ε—氮化鐵Fe2-3N,較硬且脆;次層為γ’—氮化鐵Fe4N,較軟較韌。
氮化物層之內部為擴散層,最高硬度達HRC60以上。
*滲氮層之硬度高、耐磨耗性、耐蝕性、耐熱性(500℃以上才分解)、耐熔蝕性等均優於滲碳處理層,處理溫度較低且不需淬冷,故其變形量甚微;唯其處理時間較長,且有效硬化層厚度很薄,故不能承受較大之負載。
(四)鍍硬鉻處理1.選材:*中碳鋼、中碳低合金鋼、中碳合金鋼、高碳鋼、或高碳合金鋼等,只要能以淬火—回火或高週波表面硬化處理將表層淬硬之鋼種均不施予鍍硬鉻。
2.加工程序:*粗加工→應力消除退火→精加工→淬火—回火精磨→研磨→高週波處理前處理→鍍硬鉻→除氫處理→拋光3.高週波處理:*工、模具鋼鐵淬火—回火後即可施予鍍硬鉻,但中碳鋼或中碳低合金鋼類則淬火—回火(高溫)後,須在作高週波表面硬化處理提高處理件表層之硬度,始能鍍硬鉻。
4.前處理:*鍍硬鉻前必須以酸洗清除處理件表面之油脂及污垢,酸洗必須以軟水清洗,切勿殘留碳酸鈣等於處理件表面。
不良之前處理,將引起鍍層內部鼓泡現象。
5.鍍硬鉻:*鍍硬鉻時之電流密度不宜過大。
過大之電流密度會使鍍槽溫度升高,鍍層成長太快,會成為多孔質層(硬度測定值較低),鍍層品質不佳。