Inspection Maintenance and Repair of Deepwater Pipelines
故障和缺陷的处理流程和案例英文
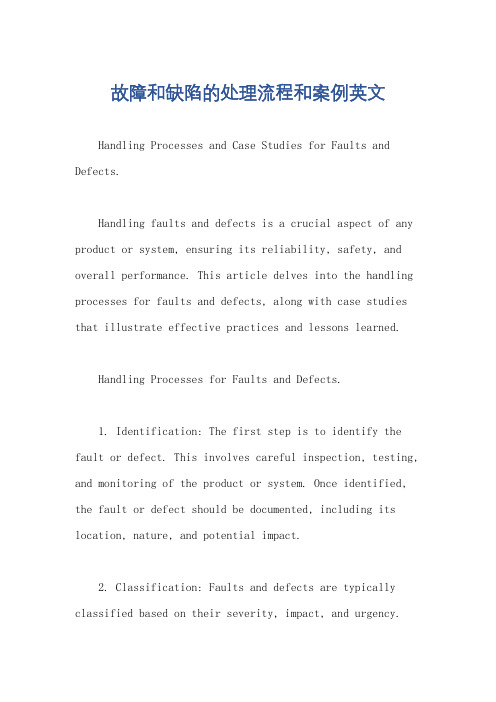
故障和缺陷的处理流程和案例英文Handling Processes and Case Studies for Faults and Defects.Handling faults and defects is a crucial aspect of any product or system, ensuring its reliability, safety, and overall performance. This article delves into the handling processes for faults and defects, along with case studies that illustrate effective practices and lessons learned.Handling Processes for Faults and Defects.1. Identification: The first step is to identify the fault or defect. This involves careful inspection, testing, and monitoring of the product or system. Once identified, the fault or defect should be documented, including its location, nature, and potential impact.2. Classification: Faults and defects are typically classified based on their severity, impact, and urgency.This classification helps prioritize the handling andrepair efforts.3. Isolation: Once classified, the fault or defect needs to be isolated to prevent it from affecting other components or systems. This may involve shutting down certain parts or redirecting flows.4. Repair or Replacement: Depending on the nature of the fault or defect, it may be repaired or replaced. Repairs may involve replacing damaged components, adjusting settings, or recalibrating systems. Replacement, on the other hand, involves swapping out the faulty component with a new one.5. Testing and Verification: After repair or replacement, the product or system needs to be tested and verified to ensure that the fault or defect has been addressed. This may involve functional testing, stress testing, or performance evaluation.6. Documentation and Reporting: Detailed documentationof the fault or defect, its handling, and the results of testing and verification is crucial. This information is essential for future reference, troubleshooting, and improving product or system design.Case Studies.Case Study 1: Aircraft Engine Fault.An airline noticed a decrease in performance and efficiency in one of its aircraft engines. After careful inspection and testing, it was identified that a compressor blade was damaged. The fault was classified as severe dueto its potential impact on flight safety and performance.To isolate the fault, the affected engine was shut down, and the aircraft was ferried to a maintenance facility. The damaged compressor blade was replaced with a new one, and the engine underwent rigorous testing to ensure its safety and performance. The aircraft was then cleared for flight, and the incident was documented for future reference.Lessons Learned: Regular inspection and maintenance of aircraft engines are crucial. Prompt identification and handling of faults can prevent major incidents and ensure flight safety.Case Study 2: Software Bug in a Healthcare System.A healthcare system experienced frequent crashes and slowdowns, affecting patient care and operations. After analyzing the system logs, it was discovered that asoftware bug was causing the issues.The bug was isolated, and a patch was developed to address it. The patch was then deployed to the system, and extensive testing was conducted to ensure its effectiveness. Once verified, the patch was rolled out to all affected systems, resolving the crashes and slowdowns.Lessons Learned: Continuous monitoring and updating of software systems are essential. Quick response andeffective handling of software bugs can minimize downtime and ensure smooth operations.In conclusion, effective handling of faults and defects is paramount for the reliability, safety, and performance of any product or system. By following the outlined handling processes and learning from case studies, organizations can ensure prompt and effective resolution of faults and defects, minimizing downtime and maximizing operational efficiency.。
生产流程的英文专业术语

生产流程的英文专业术语Certainly, I will provide you with an English essay on the topic of "Technical Terminology in Production Processes" that meets your requirements.The production process is a complex and intricate series of steps that transform raw materials into finished products. Each stage of the production process involves specialized terminology that is essential for effective communication and understanding among industry professionals. These technical terms are crucial for describing the various components, equipment, and procedures involved in the manufacturing of goods.One of the fundamental concepts in production is the raw material. Raw materials are the unprocessed natural or synthetic substances that serve as the starting point for the manufacturing process. These materials can include metals, plastics, textiles, chemicals, and a wide range of other substances. The term "feedstock" is often used interchangeably with raw materials, referring to the input materials that are fed into the production system.The next step in the production process is the procurement of theseraw materials. Procurement involves the acquisition and delivery of the necessary raw materials to the manufacturing facility. This process may involve negotiating contracts with suppliers, arranging for transportation, and ensuring the timely delivery of the materials. The term "sourcing" is commonly used to describe the process of identifying and securing reliable suppliers of raw materials.Once the raw materials have been procured, they must be prepared for the manufacturing process. This preparation stage is known as preprocessing, and it may involve activities such as cutting, shaping, or mixing the materials to meet specific requirements. The term "pretreatment" is often used to describe the various processes that are performed on the raw materials before they enter the main production line.The actual manufacturing process is where the transformation of raw materials into finished products takes place. This stage is often referred to as the "production line" or the "assembly line," and it involves a series of carefully orchestrated steps. Each step in the production process is known as an "operation," and these operations may include activities such as molding, casting, welding, painting, or packaging.To ensure the efficient and consistent execution of these operations, manufacturers often employ various production control techniques.One such technique is known as "process control," which involves the monitoring and adjustment of process parameters to maintain the desired product quality and consistency. Another important concept in production control is "quality assurance," which encompasses the systematic procedures and activities that are implemented to ensure that the final product meets the required standards and specifications.In addition to the production process itself, there are also various supporting systems and infrastructure that are essential for the smooth operation of a manufacturing facility. One such system is the "material handling system," which is responsible for the movement and storage of raw materials, work-in-progress, and finished goods within the production environment. This system may include conveyors, cranes, forklifts, and other specialized equipment.Another important aspect of production is the maintenance of the manufacturing equipment and machinery. This is known as "preventive maintenance," and it involves the scheduled inspection, servicing, and repair of equipment to prevent breakdowns and ensure optimal performance. The term "predictive maintenance" is also used to describe the use of advanced monitoring and analysis techniques to predict and prevent equipment failures.Finally, the successful management of a production process requiresthe integration of various information systems and data-driven decision-making. This is where the concept of "production planning and control" comes into play. Production planning and control involves the use of sophisticated software and algorithms to optimize the production schedule, inventory management, and resource allocation based on real-time data and forecasting models.In conclusion, the technical terminology used in the production process is a critical component of effective communication and efficient manufacturing operations. From raw materials to production control, maintenance, and information systems, each stage of the production process is characterized by specialized terminology that is essential for industry professionals to understand and apply effectively.。
T12528

GB/T12528IntroductionGB/T12528 is a Chinese national standard that provides guidelines for the design, manufacturing, and installation of general valves. It covers various aspects of valve technology including terminology, standards, testing methods, and requirements for valves used in different industries.ScopeThe scope of GB/T12528 includes the following aspects:1.Definitions and terminology related to valves.2.Classification and types of valves.3.Materials and component requirements.4.Design and manufacturing requirements.5.Valve performance specifications.6.Testing methods for valves.7.Installation and operation guidelines.8.Inspection and maintenance requirements.Definitions and TerminologyGB/T12528 provides a comprehensive list of definitions and terminology related to valves. This ensures clear communication and understanding between manufacturers, designers, and users of valves.Some of the key definitions provided in GB/T12528 include:1.Valve: A device used to control or regulate the flow of fluids or gases.2.Gate valve: A valve that uses a sliding gate to control the flow of fluids.3.Globe valve: A valve that uses a plug or disc to control the flow offluids.4.Ball valve: A valve that uses a rotating ball to control the flow of fluids.5.Butterfly valve: A valve that uses a disc mounted on a spindle tocontrol the flow of fluids.6.Check valve: A valve that allows the flow of fluids in one direction only.7.Plug valve: A valve that uses a cylindrical or tapered plug to controlthe flow of fluids.8.Pressure rating: The maximum pressure that a valve can withstandwithout failure.Classification and Types of ValvesGB/T12528 provides a systematic classification and categorization of valves based on their design and function. It includes various types of valves used indifferent applications such as gate valves, globe valves, ball valves, butterfly valves, check valves, and plug valves.Each type of valve is described in detail, highlighting its unique features, advantages, and limitations. The standard also provides guidelines for selecting the appropriate type of valve based on the specific requirements of the application.Materials and Component RequirementsGB/T12528 specifies the materials and component requirements for valve construction. It outlines the standards and specifications for materials such as cast iron, cast steel, stainless steel, bronze, and other alloys commonly used in valve manufacturing.The standard also provides guidelines for the selection of components such as valve bodies, stems, seats, seals, and actuators. It emphasizes the importance of using high-quality materials and components to ensure the reliability and performance of valves.Design and Manufacturing RequirementsGB/T12528 establishes the design and manufacturing requirements for valves. It includes guidelines for the design of valve bodies, seats, seals, and other critical components. The standard also provides specifications for manufacturing processes such as casting, forging, machining, and assembly.The design and manufacturing requirements outlined in GB/T12528 are aimed at ensuring the structural integrity, functional efficiency, and long-term durability of valves.Valve Performance SpecificationsGB/T12528 specifies the performance requirements for valves. It includes parameters such as pressure rating, temperature rating, flow capacity, leakage rate, and operating torque. These specifications ensure that valves can operate safely and efficiently under different operating conditions.The standard also provides guidelines for testing the performance of valves using various methods such as pressure testing, flow testing, and leakage testing. It specifies the acceptance criteria for performance tests, ensuring that valves meet the required standards.Testing Methods for ValvesGB/T12528 describes the testing methods for valves. It includes procedures for testing the performance, durability, and safety of valves. The standard provides guidelines for various types of testing such as hydrostatic testing, pneumatic testing, fire resistance testing, and emission testing.The testing methods outlined in GB/T12528 are designed to assess the performance and reliability of valves under simulated operating conditions. These tests help in identifying potential defects or shortcomings in valve design and manufacturing.Installation and Operation GuidelinesGB/T12528 provides guidelines for the installation and operation of valves. It includes instructions for valve installation, alignment, connection, and sealing. The standard also provides guidelines for valve operation, including opening and closing procedures, maintenance requirements, and troubleshooting guidelines.The installation and operation guidelines outlined in GB/T12528 help ensure the proper functioning and longevity of valves. It provides valuable information for operators and maintenance personnel, enabling them to handle valves correctly and perform necessary maintenance tasks.Inspection and Maintenance RequirementsGB/T12528 specifies the inspection and maintenance requirements for valves. It includes guidelines for routine inspection, preventive maintenance, and repair procedures. The standard also provides guidelines for the replacement of worn-out components and troubleshooting common issues.The inspection and maintenance requirements outlined in GB/T12528 help ensure the continued performance and reliability of valves throughout their service life. It emphasizes the importance of regular inspection and maintenance to prevent unexpected failures or malfunctions.ConclusionGB/T12528 is a comprehensive standard that provides guidelines for the design, manufacturing, testing, installation, and maintenance of valves. It covers various aspects of valve technology, ensuring the safety, reliability, and performance of valves used in different industries. Adhering to the requirements of GB/T12528 can help manufacturers and users of valves to achieve consistent quality and compliance with national standards.。
飞机维修作文英语

飞机维修作文英语Aircraft Maintenance。
Aircraft maintenance is a crucial aspect of theaviation industry. It ensures the safety and airworthiness of the aircraft, as well as the comfort and well-being of the passengers. In this essay, we will discuss the importance of aircraft maintenance, the different types of maintenance, and the role of aircraft maintenance technicians.Aircraft maintenance is essential to ensure the safety and airworthiness of the aircraft. It involves the inspection, repair, and servicing of various components of the aircraft, including the engine, avionics, and airframe. Regular maintenance helps to identify and rectify any potential issues before they become a safety hazard. This is especially important in the aviation industry, where safety is of utmost importance.There are different types of maintenance that are carried out on aircraft. The most common type is line maintenance, which involves routine checks and servicing of the aircraft between flights. This includes tasks such as refueling, visual inspections, and minor repairs. Another type of maintenance is base maintenance, which is more extensive and involves the overhaul and repair of major components of the aircraft. This type of maintenance is usually carried out at a maintenance facility and requires the aircraft to be out of service for a longer period of time.Aircraft maintenance technicians play a crucial role in ensuring the airworthiness of the aircraft. They are responsible for carrying out routine inspections, identifying any issues, and performing necessary repairs. These technicians undergo rigorous training andcertification to ensure that they are capable of performing their duties to the highest standard. Their attention to detail and dedication to safety are essential in maintaining the reliability and safety of the aircraft.In conclusion, aircraft maintenance is a critical aspect of the aviation industry. It is essential for ensuring the safety and airworthiness of the aircraft, as well as the comfort and well-being of the passengers. Different types of maintenance, such as line maintenance and base maintenance, are carried out to keep the aircraft in top condition. Aircraft maintenance technicians play a crucial role in performing these tasks and upholding the highest standards of safety and reliability in the aviation industry.。
模具维修检验流程

模具维修检验流程The process of mold maintenance and inspection is a crucial aspectof ensuring the quality and efficiency of manufacturing. 模具维修检验流程是确保制造质量和效率的关键方面。
It involves a series of stepsthat require attention to detail, technical expertise, and adherence to safety protocols. 这涉及一系列步骤,需要注意细节、技术专长和遵守安全协议。
From identifying the need for maintenance to the actual repair and inspection, each stage plays a vital role in upholding the integrity of the molds. 从识别维修需求到实际修理和检验,每个阶段在维护模具的完整性上都发挥着至关重要的作用。
The first step in the mold maintenance and inspection process is the identification of the need for repairs. 模具维修检测流程的第一步是确认维修需求。
This can be determined through regular monitoring of the molds during production and identifying any signs of wear and tear. 这可以通过定期监控模具在生产过程中的情况,识别任何磨损迹象来确定。
It is also essential to have a clear understanding of the performance standards of the molds and any deviations from these standards. 对模具的性能标准以及与这些标准的任何偏差都有清晰的理解也是非常重要的。
检测维修保养中级证工作范围要求

检测维修保养中级证工作范围要求1.检测维修保养中级证工作范围要求包括机械设备的维修和保养。
The scope of work requirements for the intermediate certificate of inspection, maintenance and repair includesthe maintenance and repair of mechanical equipment.2.专业技能包括设备故障排除和维护。
Professional skills include equipment troubleshooting and maintenance.3.需要具备机械工程方面的知识和技能。
Mechanical engineering knowledge and skills are required.4.要求具备电气设备的维修和保养能力。
Ability to maintain and repair electrical equipment is required.5.必须能够独立完成相关维修任务。
Must be able to independently complete the related maintenance tasks.6.需要能够识别和解决设备故障。
Ability to identify and resolve equipment malfunctions is required.7.必须遵守相关的安全操作规程。
Must adhere to relevant safety operational procedures.8.要求具备使用标准工具进行维修的能力。
Ability to use standard tools for repairs is required.9.需要了解机械设备的润滑和清洁要求。
Knowledge of lubrication and cleaning requirements for mechanical equipment is necessary.10.要求具备相关设备的安装和调试能力。
CP50技术资料6278

1.2. Inspection, Maintenance and Repair for Major Areas1.2.1. Head Assembly 1.2.1.1.WooriAlignInspectionAligner may not function properly if the align windows are contaminated. Use soft not-abrasive cloth to clean the windows in case of contamination.Figure 1-1. Align Windows of AlignerSolutionw Gently wipe off the dust with a camel hairbrush to remove dust.w Clean the windows with a foam swab or lens cleaning tissue slightly dampened with aisopropyl alcoholw In case the WooriAlign needs to be replaced, contact the service center.w Unscrew the screw from the bottom section of the WooriAlign to remove the Aligner. w Should calibrate the WooriAlign after replacing it.Warning If you need to approach the major areas for maintenance, Be sure to turn off the main power switch for safety.The malfunction caused by manual moving of the gantrymay cause damage to the machine or injury of the operator. Don't move the gantry manually.Caution The Aligner system windows should be cleaned like a highquality lens. Fingerprints and dust on these windows willdegrade the performance of the system.Align Window1.2.1.2. Compliance AssemblyInspectionThe compliance assembly could be damaged or bent. Check the compliance assembly to make sure the spring is moving properly and there is no bent.Figure 1-2. Compliance AssemblySolutionUnscrew the compliance assembly from the ball spline and replace it with a new one.Disassembling the Compliance Assembly from the Head ¨ç Grip the groove (A) on the upper side of head spline using a spanner.¨è Insert the compliance assembling tool(B) into the compliance assembly.¨é Loose the compliance assembly until it can be unscrewed manually using the compliance assembling tool. ¨ê Disassemble the compliance assembly manually.Assembling the Compliance Assembly into the Head¨ç Insert the compliance assembly into the head and screw it manually.¨è Tighten the compliance assembly using the compliance assembling tool.1.2.1.3. Compliance O-RingInspectionAfter a long running of Component Placer, some residue or wear can occur on the tip ofthe compliance assembly where the o-ring is located. In this case, leakage or errors can beexpected while nozzle changes. Should check the o-ring for contamination or wear.SolutionApply grease or replace it with a new one.1.2.1.4. NozzleInspectionCheck the nozzle to see if excessive wear or if the tip of the nozzle has been altered dueto impact. In addition, check to see if any contamination, such as solder paste is cloggingthe nozzle.Figure 1-3. Nozzle inspectionSolutionClean the nozzle with alcohol in case of contamination, or replace the nozzle if anexcessive wear was detect.1.2.1.5. Vacuum FilterInspectionProblem to the vacuum can occur when the vacuum filter has been contaminated by dust in the air or due to solder paste. Check the vacuum filter regularly to make sure the filter is free from contamination.Figure 1-4. Vacuum Filter InspectionSolutionOpen the filter cap and replace the inside filter. In addition, clean the inside of the spindle at the same time.Figure 1-5. Replacing the filter1.2.1.6. SpindleInspectionContamination (such as solder paste, etc.) in the spindle can cause pickup problems. The inside of the spindle must be cleaned in case of contamination. Solutionw Remove the rotary joint.w Place a soft cloth beneath the spindle and pour a small amount of alcohol from the topof the spindle.w Using an air gun, completely blow out any residue or alcohol that may be inside thespindle.Caution Using the air gun without putting on goggles may causeinjury to the eyes of the operator. Be sure to wear goggleswhen using the air gun.Vacuum Filter1.2.1.7. Vacuum GeneratorInspectionw Check to see if the filter element within the vacuum generator has changed in color. w Check to see if there are any leakages within the vacuum generator.Figure 1-6. Vacuum GeneratorSolutionw If the filter element has changed color, remove the screw from the top of the filter andreplace the filter element.w If the vacuum generator has to be replaced due to leakage, be sure to contact theservice center and receive proper service.Figure 1-7. Replacing the filter element of vacuum generatorCaution Make sure the alcohol does not spill out from the spindlewhen pouring the alcohol into the spindle and make sure toblock the bottom of the spindle with a piece of cloth.Filter1.2.2. X-Y Frame Section1.2.2.1. X-axis L/M Guide RailInspectionw Check the rail for discoloration or dust.w Check the lubricants on the rails. Insufficient lubricants on the rails could causeunusual noise during operation of the machine.Figure 1-8. X-axis L/M Guide Rail & BlockSolutionw Clean the rail of any contamination or dust, and apply grease if necessary.1.2.2.2. Y-axis L/M Guide RailInspectionw Check the rail for discoloration or dust.w Check the lubricants on the rails. Insufficient lubricants on the rails could causeunusual noise during operation of the machine.CautionIt may shorten the average life span of a machine if grease not specified by our company is applied on the machine. Use the grease specified by our company.X-axis L/M Guide Rail & BlockL/M Guide RailL/M Guide BlockFigure 1-9. Y-axis L/M GuideSolutionw Clean the rail of any contamination or dust, and apply grease if necessary.1.2.2.3. X-axis Ball ScrewInspectionw Check the ball screw for discoloration or dust.w Check the lubricants on the ball screw. Insufficient lubricants on the rails could cause unusual noise during operation of the machine.SolutionClean the ball screw of any contamination or dust, and apply grease if necessary.1.2.2.4. Y-axis Ball ScrewInspectionw Check the ball screw for discoloration or dust.w Check the lubricants on the ball screw. Insufficient lubricants on the rails could cause unusual noise during operation of the machine.Y axis ball screw grease nippleFigure 1-10. Y axis ball screw grease nippleSolutionw Clean the ball screw of any contamination or dust, and apply grease if necessary.w Apply grease through the grease nipple.1.2.2.5. X-axis Belt and PulleyInspectionw Check the tension on the belt to see if it is too loose or too tight.w Check the belt for abnormal wear.w Check the pulley for abnormal wear.Tension ScrewsFigure 1-11. X-axis Belt and PulleySolutionw Adjusting the tension of the belt can cause some problem to motors. When it is necessary to adjust the tension of the belt or an abnormal wears was found on the beltand pulley, contact the service center.1.2.2.6. Y-axis Belt and PulleyInspectionw Check the tension on the belt to see if it is too loose or too tight.w Check the belt for abnormal wear.w Check the pulley for abnormal wear.Tension ScrewFigure 1-12. Y-axis Belt and PulleySolutionw Adjusting the tension of the belt can cause some problem to motors. When it is necessary to adjust the tension of the belt or an abnormal wears was found on the beltand pulley, contact the service center.1.2.3. Conveyor System1.2.3.1. PCB Conveyor BeltInspectionw Check the tension of the belt to see if it is too tight or too loose.w Check the belt for abnormal wear.w Check the driving motor pulley for abnormal wear.w Check the support idler for abnormal wear.w Check the belt to see if it has shifted in position or is coming off.Figure 1-13. PCB Conveyor BeltSolutionw Use the support idler for the motor to adjust the tension of the belt if it seems tootight or too loose.wContact the service center to acquire replacement for the belt if an abnormal wear hasbeen found.w Contact the service center to acquire replacement for the driving pulley and supportidler if abnormal wears have been found.1.2.3.2. Lead Screw for Adjusting Conveyor WidthInspectionw Look for components, dust or discoloration of the lead screw.w Insufficient lubricant on the lead screw can cause difficulty in adjusting the width ofthe conveyor. Check the lubricant condition.Figure 1-14. Lead Screw for Adjusting Conveyor WidthSolutionw Eliminate the dust and contamination and apply grease to the lead screw if necessary.Support IdlerLead Screw Chain L/M Guide Rail1.2.3.3. L/M Guide Rail for Adjusting Conveyor WidthInspectionw Look for components, dust or discoloration of the rails.w Insufficient lubricant on the rails can cause difficulty in adjusting the width of the conveyor. Check the lubricant condition.Solutionw Eliminate the dust and contamination from the rails and apply grease to the lead screw if necessary.w Apply grease through the grease nipple.1.2.3.4. Chain for Adjusting Conveyor WidthInspectionw Check for contamination on the chain.w Insufficient lubricant on the chain could cause difficulties in adjusting the conveyor width. Check the condition of the lubrication.Solutionw Eliminate the contamination and apply grease if necessary.1.2.3.5. PCB Detect SensorInspectionw Check to see if the sensor window has been contaminated.w Check the sensor's firmness in location to see whether it has moved out of position.w Check the sensor's performance to see whether it is functioning or not.Sensor WindowFigure 1-15. PCB Detect SensorSolutionw Eliminate the contamination and clean the sensor window with a soft cloth.w Check the sensitivity of sensor.w If the sensor is found defective, contact the service center for a replacement.1.2.3.6. Adjusting Belt SpeedInspectionw Check to see if there is a production problem caused by the speed of the conveyor system.Figure 1-16. Conveyor Speed Control VolumeSolutionwThe speed of the conveyor system can be adjusted by adjusting the conveyor speedcontrol volume located in the rear of the machine where the controller is.1.2.3.7. Stopper(Hard Stop) InspectionInspectionw Check the upper section of the stopper (or hard stop) to see if excessive wear hasoccurred (inspect the area where it contacts the PCB).Figure 1-17. Stopper Inspection PointsSolutionw If excessive wear is detected, replace the upper section of the stopper.Caution Inaccurate speed control may deteriorate the accuracy of component placement. Speed control must be performed by a skilled person who received C/S training or contact ourdesignated C/S company(STS). Conveyor Speed Control Volume1.2.3.8. Conveyor Cylinder OperationInspectionw Check the operation of each cylinder. w Check the detect sensor of each sensor. Solutionw The operation of each cylinder can be checked using <Setup/Manual Control>command or <Setup/Diagnostics/Self Diagnosis> command on the MMI application. § Please refer to "Operations Manual-Programming Guide, 10.5 Manual Control[Ctrl+M] (page 10-80)" on <Setup/Manual Control> command.§ Please refer to "Operations Manual-Programming Guide, 10.6.3 Self Diagnosis(page 10-87)" on <Setup/Diagnostics/Self Diagnosis> command. w If the cylinder is found defective, contact the service center for a replacement.1.2.4. Electric DeviceInspectionw Check abrasive wear in each area of the device.w Check if the machine generates errors when the switch is operated.w Check if the corresponding Input IO on the MMI IO window operates.(EmergencySwitch , Door Switch)w Check if power is disconnected when the Current Breaker is operated. Solutionw Contact our C/S center for service when severe abrasive wear is present or themachine does not work properly.1.2.5. Feeder Station Section 1.2.5.1.Feeder BaseInspectionw Make sure the feeder base is clear of any stray components or residue beforeinstalling the feeders onto the feeder base.w Check to see if any wear is found on the securing slots. SolutionWarning Adjusting the sensor or correcting an error while themachine is ready could result in personal injury. Be sure toadjust the sensor or correct an error in the stop status (idlemode) after cancelling the ready status. Caution Before checking abrasive wear, be sure to turn off power,lock, and check.1.2.5.2. Adjustment of Multi Cylinder SpeedInspectionw Check to see if inadequate setting of the speed control is causing problems to feedersoperation when presenting components.Figure 1-18. Speed Control ValvesSolutionw Adjust using the speed control valve for the multi -cylinders.1.2.6. Upward Vision UnitFigure 1-19. Upward Vision UnitCautionEliminate or remove any components or contamination on the feeder base and clean with a soft cloth.In case of wear is found, it could lead to reliability problems with the component pickups. Contact the service center for service or replacement.Speed Control Valve1.2.6.1. Cover GlassInspectionw Check to see if there are any dust, components or contamination on or near the cover glass.Solutionw Remove the LED assembly by removing the four screws to the sides of the assembly.w Clean the cover glass using a soft cloth.w Assemble the LED assembly by screwing the four screws.Caution The cover glass is fragile. Take precautions.1.2.6.2. Reflector MirrorInspectionw Check to see if there are any dust or contamination on the reflector mirror.Solutionw Remove the LED assembly by removing the four screws to the sides of the assembly.w Clean the reflector mirror by using a soft cloth.w Assemble the LED assembly by screwing the four screws.1.2.6.3. Camera LensInspectionw Check to see if there are any dust or contamination on the camera lens.Solutionw Remove the LED assembly by removing the four screws to the sides of the assembly.w Clean the camera lens by using a soft cloth.w Assemble the LED assembly by screwing the four screws.1.2.7. Pneumatics 1.2.7.1.Pressure SettingsInspectionw Check to see if the supplied pneumatics is appropriate for the configured pressure.Figure 1-20. Inspection for PneumaticsSolutionw Adjust the pneumatics setting by rotating the regulator CW(Clockwise) orCCW(Counter Clockwise).1.2.7.2. Air Filter & Auto DrainerInspectionw Check to see if there are any moisture or water inside the air filter. w Check to see if the filter element is clogged. w Check for discoloration of the filter element.w Check to see if moisture is being properly drained out through the drainer. w Check to see if the tube is properly connected to the drainer.Caution Setting the pressure incorrectly could harm the machine performance. Set the pressure correctly. Warning Changing the air filter without cutting off the air pressurecould result in personal injury.Be sure to cut off air pressure before changing the air filter.Solutionw Lower the locking mechanism or handle for the air filter tray and turn it sideways toremove the tray. w Remove the contaminated filter element.w Install the new filter element reversing the above procedures.w Reassemble the tray.1.2.7.3. Gauge and Pressure SwitchInspectionw Check to see if the pressure switch has been automatically activated by low pressure.Solutionw If it does not function properly, contact the service center for service.1.2.7.4. Connections and FittingsInspectionw Check for unusual wear in the tubes.w Check to see if any tubes and fittings are loose, and make sure there are no leaks.Solutionw Replace the tube if unusual wear is discovered.w Tighten any loose fitting.1.2.8. Component Feeding Sub-Systems (Feeders)w Please refer to the manuals for information on each component feeding sub-systems.。
汽车检测与维修总结月报范文

汽车检测与维修总结月报范文英文回答:Car Inspection and Maintenance Monthly Report.Introduction:This monthly report aims to summarize the activities and findings of the car inspection and maintenance department for the month of [Month]. It provides an overview of the number of cars inspected, the types of issues identified, and the actions taken for maintenance and repair.1. Number of Cars Inspected:During the month of [Month], a total of [Number] cars were inspected by our team. This includes both scheduled inspections and those brought in for specific issues.2. Types of Issues Identified:The inspections revealed various types of issues in the cars. The most common problems identified were related to engine performance, electrical systems, brakes, and suspension. Additionally, we also found issues with tires, fluids, and overall vehicle safety.3. Actions Taken for Maintenance and Repair:Upon identifying the issues, our team took prompt actions to address them. We conducted necessary repairs, replaced faulty parts, and performed routine maintenance tasks such as oil changes and filter replacements. We also provided recommendations to the car owners for any additional repairs or maintenance required.4. Customer Satisfaction:Customer satisfaction is a key priority for our department. We ensured that all car owners were provided with detailed reports of the inspection findings and theactions taken. We also sought feedback from customers to assess their level of satisfaction with our services. The feedback received was mostly positive, with customers appreciating our professionalism, expertise, and timely completion of repairs.Conclusion:In conclusion, the car inspection and maintenance department has successfully carried out inspections on a significant number of cars during the month of [Month]. We have identified and addressed various issues, ensuring that the cars are safe and in optimal condition. The positive feedback received from customers reflects our commitment to providing quality services.中文回答:汽车检测与维修月报。
- 1、下载文档前请自行甄别文档内容的完整性,平台不提供额外的编辑、内容补充、找答案等附加服务。
- 2、"仅部分预览"的文档,不可在线预览部分如存在完整性等问题,可反馈申请退款(可完整预览的文档不适用该条件!)。
- 3、如文档侵犯您的权益,请联系客服反馈,我们会尽快为您处理(人工客服工作时间:9:00-18:30)。
Deep and Ultra-deepwater Pipelines Conference 27 - 28 September 2011, Novotel Paris Les Halles
Inspection Maintenance and Repair of Deepwater Pipelines
Routine inspections may indicate a requirement for more specific investigations involving detailed or specialist techniques.
The normal physical inspection tasks undertaken on the Deepwater Pipelines can be split into locations internal and external to the pipeline. Internal and External locations are typically periodically inspected by Pigging and Remote Vehicle methods respectively. Permanent monitoring methods also exist and are becoming more commonplace.
Inspection Maintenance and Repair of Deepwater Pipelines
3
Ian Nash
Typical Characteristics of Deepwater Pipelines
• • • Water depths are beyond diver limits and all activity (IMR) is remote Wall thickness are typically high } Materials, Welding, buckling Operating pressures are typically very high or very low
1
Ian Nash
Introduction
• • • • •
Requirements for pipeline inspection: what, when and how Pipeline maintenance and routine inspection Pipeline damage during installation and operation in deepwater, causes and effects Understanding the risks and potential need for repair Repair systems & tools
Deep and Ultra-deepwater Pipelines Conference 27 - 28 September 2011, Novotel Paris Les Halles
Defects
Spanning/Burial Corrosion Dents Gouges leak CP Failure Coating Damage Hydrate Movement Buckle Vibration Cracking Fatigue Protection Integrity (mattresses/ Rock/Covers)
Deep and Ultra-deepwater Pipelines Conference 27 - 28 September 2011, Novotel Paris Les Halles
Inspection Maintenance and Repair of Deepwater Pipelines
Geohazards can be significant } Spanning, Buckling, Damage, Bend Stability, Turbitity and Debris flows Slugging within produced fluids is common } Spanning, Fatigue Greater tolerances – Survey inaccuracy, installation accuracy Metocean and environmental conditions tend to be benign } Stability Seabed mobility is less dominant } Scour, Spanning
Deep and Ultra-deepwater Pipelines Conference 27 - 28 September 2011, Novotel Paris Les Halles
Inspection Maintenance and Repair of Deepwater Pipelines
Permanent Monitoring
5
Ian Nash
INSPECTION STRATEGY (Monitoring)
Planned inspection campaigns are an integral part of the IMR strategy, the purpose of the inspections being: • to monitor pipeline system integrity over time • monitor the impact of the subsea and production environments on the pipeline. • Understanding and confirming design assumptions
6
Ian Nash
INSPECTION STRATEGY (Understanding the Design)
It is essential that in developing an inspection regime that the deign is understood and must include interaction with the designers: • deepwater lateral buckling and walking issues will have been solved with reference to the anticipatedpipeline operation response. Is that what really happened? If your system is anticipated to have multiple start up and shut down scenarios you will need to understand what the designers anticipated happening and how to monitor it. there may be need to reconfirm what has actually happened once the pipeline is in operation.
4
Ian Nash
BASELINE SURVEY
The ongoing assessment of inspection findings will involve comparison of data with that recorded during previous inspection campaigns. This will allow trends to be extrapolated and judgments made regarding the urgency of remedial action. This process necessarily commences with the acquisition of the measurement of internally and externally taken values at the commencement of pipeline service, known as a Baseline Survey.
2
pipeline inspection: what, when and how
Deep and Ultra-deepwater Pipelines Conference 27 - 28 September 2011, Novotel Paris Les Halles
•
• • • • •
repair is performed remotely
•
Corrosion coatings tend to be of very high quality } Corrosion, Damage
Deep and Ultra-deepwater Pipelines Conference 27 - 28 September 2011, Novotel Paris Les Halles Inspection Maintenance and Repair of Deepwater Pipelines
Inspection Maintenance and Repair of Deepwater Pipelines
DNV RP-F113 Deep and Ultra-deepwater Pipelines Conference 27 - 28 September 2011, Novotel Paris Les Halles Inspection Maintenance and Repair of Deepwater Pipelines
7
Ian Nash
INSPECTION METHODS