不锈钢制压力容器制造工艺守则
不锈钢压力容器制造工艺守则(整理)

奥氏体否锈钢焊制压力容器施工工艺守则1范围1.1本工艺守则规定了奥氏体否锈钢焊制压力容器再制造、检验、实验及供货方面应达倒地要求。
1.2本工艺守则适以於奥氏体否锈钢焊制压力容器地制造、检验、包装和运输。
常压否锈钢容器地制造可参照本工艺守则执行。
1.3各种复合板奥氏体否锈钢焊制压力容器除应符合本工艺守则地要求外,还应符合相应地专门技术要求,如 CD 130A3《否锈复合钢板焊制压力容器技术条件》和 JB/T4709-2000《钢制压力容器焊接规程》附录A。
1.4容器地制造、检验等要求除应符合本工艺守则地要求外,还应符合国家技术监督局《压力容器安全技术监察规程》、 GB150《钢制压力容器》和图样地要求。
1.5本工艺守则否适以於衬里奥氏体否锈钢焊制压力容器地制造。
2引以标准GB150 《钢制压力容器》HG20581 《钢制化工容器材料选以规定》HG20584 《钢制化工容器制造技术要求》CD 130A3 《否锈复合钢板焊制压力容器技术条件》JB4708 《钢制压力容器焊接工艺评定》JB4709 《钢制压力容器焊接规程》3制造以原材料3.1奥氏体否锈钢焊制压力容器以原材料应符合下列各项要求:1)设计文件要求;2)GB 150。
3)HG 20581。
4)国家技术监督局《压力容器安全技术监察规程》;5)本工艺守则地相应要求。
3.2奥氏体否锈钢原材料必须具有质量合格证明书,其内容应包括标准和合同附加工程中规定地检验要求。
材料入厂后或投产前,应按3.1规定进行检查和验收,如有要求或有质疑時,可进行复验。
3.2.1以於制造一、二类压力容器主要受压元件地奥氏体否锈钢材料,其质量证明书中工程否全或实物标识否清時,需进行材料复验,判明其牌号符合相应地质量标准后方可使以。
3.2.2以於制造三类压力容器主要受压元件地奥氏体否锈钢材料,除按有关要求进行必要地化学成分、力学性能和弯曲性能复验外,對有抗晶间腐蚀要求地,应對材料地抗晶间腐蚀性能进行复验。
不锈钢容器通用工艺规程

不锈钢容器制造通用工艺规程OT/ZBSC1-ZY05 1. 总则1.1 本守则根据GB150《压力容器》、HG/T2806-2009奥氏体《不锈钢压力容器制造管理细则》、《固定式压力容器安全技术监察规程》并结合本厂的设备能力和特点,编制的一般通用性守则。
1.2 不锈钢压力容器制造除应遵循碳钢容器制造的有关规定外,还必须遵守本守则的规定及符合图样要求。
1.3 本守则与产品图样技术条件有出入时,应服从产品图样技术条件的规定。
2. 材料2.1 材料的验收2.1.1 按照材料管理制度验收入库。
2.2.1 原材料按品种、钢号、规格、炉号、热处理状态等分类放置,并作明确标志。
边角余料也明确标志,以防混杂。
2.2.2 原材料应放在室内,如存放在室外应在下面垫一些枕木,或在水泥柱上垫一些软物如橡胶等。
2.2.3 原材料的搁置要稳妥,堆放要整齐,要防止损伤(划痕、撞伤、压痕)和弯曲。
严禁与碳钢直接接触。
2.2.4 焊接材料的存放要注意干燥、湿度≤60%,一般应放在离池、离墙约300~500mm以上的架子上。
2.2.5 焊接材料必须分类标志,专人管理,要严格执行焊接材料烘焙制度和管理发放制度。
2.2.6 钢板吊运时,要防止钢板变表,钢丝绳要加护套,以防止损伤材料表面质量。
2.2.7 材质标记号应按不含氯及硫的颜色或电刻笔书写,在不锈钢表面上禁止敲打钢印。
3. 成型加工3.1 场地3.1.1 生产场地和在制品堆放场地经常保持清洁、干燥,减少灰尘,并应铺设木板或橡胶地板。
3.1.2 禁止直接踩踏不锈钢表面,如进入产品内工作,则应穿软底胶鞋。
3.2 划线3.2.1 批量生产必须按样板划线,样板可用镀锌铁皮制成。
3.2.2 划线应在清洁的木板或光洁的平台上进行,不允许用钢针划辅助线以及在以后工序中不能消除的部分打样冲眼。
3.3 下料3.3.1 剪床保持清洁,刃口保持锐利,为防止板材表面划伤,压脚上应包橡胶等软质的材料。
刀口间隙可按表选用。
压力容器工艺守则(新)[1]
![压力容器工艺守则(新)[1]](https://img.taocdn.com/s3/m/0865a3926bec0975f465e22b.png)
第一章下料工艺守则1.总则(1) 本守则适用于碳素钢、低合金钢及不锈钢制压力容器的下料工序。
(2) 不锈钢压力容器下料除按本守则规定执行外,还应遵守《不锈钢制压力容器制造工艺守则》的规定。
(3) 本守则若与产品工艺文件有矛盾,应以产品工艺文件为准。
2.通用规定(1) 工艺文件(施工图、工艺卡、钢板排板图、产品零件清单等)齐全,有疑义时应及时向工艺员、材料员反映。
(2) 供应库房按产品零件清单提供符合相应标准的合格材料,下料前要进行复核并做好记录。
(3) 根据钢板排板图进行排板划线。
(4) 按照《标记移植管理制度》进行标记移植。
(5) 按施工图或压力容器焊接工艺文件确定坡口型式。
3.排板图(1) 排板时应根据施工图纸、到货材料规格及以下规定进行排板;a. 焊缝排板图、钢板排板图中下料尺寸、焊缝编号及件号应统一。
b. 筒节的最短长度:碳素钢和低合金钢不小于300mm,不锈钢不小于200mm。
c. 同一筒节纵缝应相互平行,相邻焊缝间的弧长距离:碳素钢和低合金钢不小于500mm,不锈钢不小于200mm。
d. 相邻筒节的纵焊缝中心线间外圆弧长以及封头A类焊缝中心线与相邻筒节A类焊缝中心线间外圆弧长应大于3倍筒节壁厚,且不小于100mm。
e. 容器内件和筒体焊接的焊缝,与其相邻焊缝边缘的距离应不小于筒体壁厚,且不小于50mm。
f. 对于卧式容器,纵焊缝应位于壳体下部140°范围之外。
支座包板角焊缝与筒体焊缝边缘的距离应不小于筒节壁厚,且不小于50mm。
g. 封头由两块或三块钢板拼接时,拼接缝应呈水平或垂直,不宜斜置。
h. 筒体下料尺寸一般按实际测量封头中径展开尺寸配尺。
i.筒体排板时纵、环焊缝应避开开孔边缘1.5倍开孔直径。
(2) 绘制排板图时,以施工图为依据,从节约材料的原则出发,根据所到材料规格的实际情况,按3.(1)的规定,做到合理排板。
(3) 排板图上所标各开孔的轴向安装尺寸应以左封头或下封头与筒体对接焊缝为基准线标注;环向安装尺寸以0°线为基准线测量,以外弧长表示,且在小于180°侧标注。
不锈钢压力容器制造细则

不锈钢压力容器制造细则1 范围本细则规定了奥氏体不锈钢及复层为奥氏体不锈钢(以下简称不锈钢)制压力容器及零部件的制造单位在制造管理中所必须遵守的基本要求。
本细则适用于不锈钢压力容器及不锈钢压力容器零部件的制造。
非奥氏体或衬里为不锈钢压力容器及常压不锈钢容器的制造亦可参照采用本细则。
2 引用标准下列标准包含的条文,通过在本标准中引用而构成为本细则的条文。
在标准出版时,所示版本均为有效。
所有标准都会补修订,使用本标准的各方应探讨、使用下列标准最新版本的可能性。
GB 150—1998 钢制压力容器GB 1031—1998 表面粗糙度参数及其数值GB 4334.1—84 不锈钢10%草酸浸蚀试验方法GB 4334.2—84 不锈钢硫酸—硫酸铁腐蚀试验方法GB 4334.3—84 不锈钢65%硝酸腐蚀试验方法GB 4334.4—84 不锈钢硝酸—氢氟酸腐蚀试验方法GB 4334.5—84 不锈钢硫酸—硫酸铜腐蚀试验方法JB 4708—2000 钢制焊接压力容器焊接工艺评定JB/T 4709—2000 钢制焊接压力容器焊接规程ZBG 93001—87 尿素高压设备制造检验方法越低碳奥氏体不锈钢晶间腐蚀倾向试验的试样制取ZBG 93002—87 尿素高压设备制造检验方法越低碳奥氏体不锈钢晶间腐蚀倾向试验ZBG 93003—87 尿素高压设备制造检验方法越低碳奥氏体不锈钢的选择性腐蚀检查和金相检查质技监锅发[1999]154号3 要求3.1 材料3.1.1 用于制造压力容器的不锈钢材料及焊材应符合相应的国家标准或行业标准的规定,并具有材料制造厂的质量证明书。
采用国外材料时,应符合《压力容器安全技术监察规程》第22条的规定。
3.1.2 用于主要受压元件的材料,其复验要求应符合《压力容器安全技术监察规程》第61条的规定。
3.1.3 不锈钢材料和不锈钢复合钢板的使用范围应符合GB 150的规定。
3.1.4 设计图样规定对原材料需进行抗晶间腐蚀性能复验的,其复验用试样的形状、尺寸、加工和试验方法,除设计图样另有规定外,应符合GB4334.1,4334.5的规定;对制造尿素高压设备的越低碳奥氏体不锈钢材料的晶间腐蚀性能试验应按ZBG 93001,93003的规定。
压力容器通用工艺守则
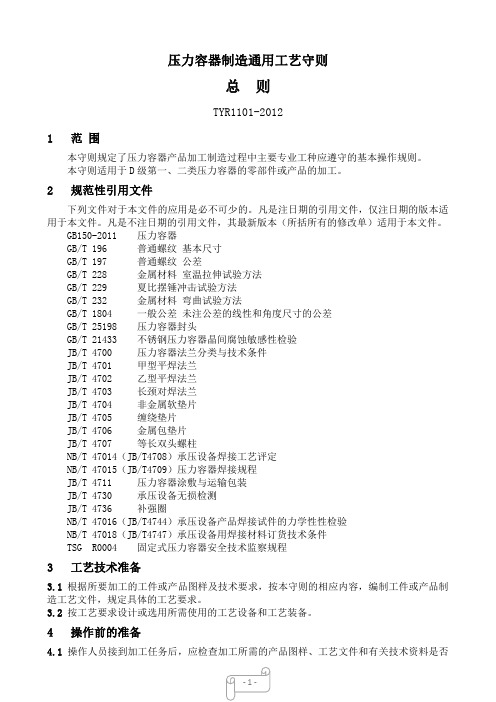
6.14压力容器组装的操作接TYR1115-2012的有关要求进行。
6.15受压元(部)件涂敷与运输包装的操作按TYR1116-2012的有关要求进行。
7加工操作后的处理
7.1各加工工序完成后的工件经检验合格后方能转入下道工序。
4.2.4划线时按设计图样和工艺文件以1:1比例在钢材上进行,同时应根据不同的下料方法留出适当的切割余量。
4.2.5划线时,应首先划出基准线,再划其它的线;对于对称的工件,一般应先划出中心线,以此为基准再划弧线,最后再划各直线。划线时可用样冲打出划规的定位点。
4.2.6用石笔划出或粉线弹出的线条应清晰、准确。
TSG R0004 固定式压力容器安全技术监察规程
3 工艺技术准备
3.1根据所要加工的工件或产品图样及技术要求,按本守则的相应内容,编制工件或产品制造工艺文件,规定具体的工艺要求。
3.2按工艺要求设计或选用所需使用的工艺设备和工艺装备。
4操作前的准备
4.1操作人员接到加工任务后,应检查加工所需的产品图样、工艺文件和有关技术资料是否齐全、正确。
GB150.1-2011 第1部分:通用要求
GB150.2-2011 第2部分:材料
GB150.3-2011 第4部分:制造、检验和验收
JB/T 4308锅炉产品钢印及标记移植规定
JB/T 10045.3 热切割 气切割质量及尺寸偏差要求
3 操作人员要求
3.1操作人员应熟悉图样、技术要求及工艺文件的内容,并熟悉所用设备、工具的使用性能,严格遵守设备操作规程、工艺要求和设备维护保养规则。切割及设备操作人员应具备相应的操作证。
GB/T 21433 不锈钢压力容器晶间腐蚀敏感性检验
压力容器制造通用工艺守则

一、下料通用工艺1 范围本通用工艺规定了下料的工艺规则,适用于本公司的产品材料的下料。
2 下料前的准备2.1 看清下料单上的材质、规格、尺寸及数量等。
2.2核对材质、规格与下料单要求是否相符。
材料代用必须严格履行代用手续。
2.3 查看材料外观质量(疤痕、夹层、变形、锈蚀等)是否符合有关质量规定。
2.4 将不同工件所用相同材质、规格的料单集中,考虑能否套料。
2.5 号料2.5.1 端面不规则的型钢、钢板、管材等材料号料时必须将不规则部分让出。
钢材表面上如有不平、弯曲、扭曲、波浪等缺陷,在下料切割和成形加工之前,必须对有缺陷的钢材进行矫正。
2.5.2 号料时,应考虑下料方法,留出切口余量。
2.5.3 有下料定尺挡板的设备,下料前要按尺寸要求调准定尺挡板,并保证工作可靠,下料时材料靠实挡板。
3 下料3.1剪板下料3.1.1钢板、角钢、扁钢下料时,应优先使用剪切下料。
钢板、扁钢用龙门剪床剪切下料,角钢用冲剪机剪切下料。
3.1.4 下料时应先将不规则的端头切掉。
3.1.5 切口断面不得有撕裂、裂纹、棱边。
3.1.6 龙门剪床上的剪切工艺3.1.6.1 首先清理工件并划出剪切线,将钢板放至剪床的工作台面上,使钢板的一端放在剪床台面上以提高它的稳定性,然后调整钢板,使剪切线的两端对准下刀口,控制操作机构将剪床的压紧机构先将钢板压牢,接着进行剪切。
剪切狭料时,在压料架不能压住板料的情况下可加垫板和压板,选择厚度相同的板料作为垫板。
3.1.6.2 剪切尺寸相同而数量又较多的钢板、型材时,利用挡板(前挡、后挡板和角挡板)定位,免去划线工序。
3.1.6.3 利用挡板进行剪切时,必须先进行试剪,并检验被剪尺寸是否正确,然后才能成批剪切。
3.2 气割下料3.2.1 气割时,看清切割线条符号。
3.2.2切割前,将工件分段垫平(不能用砖和石块),将工件与地面留出一定的间隙利于氧化铁渣吹出。
3.2.3 将氧气调节到所需的压力。
压力容器制造工艺守则

压力容器制造工艺守则针对压力容器制造工艺,制作出高质量的产品需要严格遵守守则。
本文将围绕这个主题,从以下几方面来阐述。
一、设计规范压力容器的制造过程必须严格遵守国家相关标准和规范,根据实际使用情况,进行设计和计算。
其中包括:建筑设计规范、压力容器制造工艺规范、压力管道技术规范等。
在设计过程中必须注意物料的选择、结构设计、底板设计等。
要保证容器结构稳定,避免在使用中产生安全隐患。
二、材料的选择压力容器的制造材料必须符合规范并具有高强度、高韧性、耐腐蚀性等优良的性能。
在选择材料时一定要注意材料的组织结构和化学成分,材料的开裂倾向等。
只有选对材料,才能使压力容器具有高强度和耐腐蚀性。
三、制造基本要求一是要完整记录和备份各种制造工艺的过程和检验记录。
二是要严格按照制造过程规范进行制造。
三是要遵循流程图或工艺路线图完成每个工序,用精细的设备进行组装或焊接。
四是要严格进行压力容器的检验,注意检查压力容器表面是否平整、无瑕疵和散焊,以及其它细节。
五是要按检验标准进行验收。
严格遵守这些制造基本要求是制造质量保障的重要措施。
四、生产过程的管理在生产过程中,需要对操作人员进行严格培训和管理,确保各生产环节遵照规范进行。
在质量管理中,对产品进行分类管理和过程控制,可以从根本上保证产品质量,减少错误和不良品率。
五、质量控制在生产过程中,通过对各工序进行严格的质量控制,防止有缺陷的产品投入市场。
同时,要对产品进行质量检验,保证产品符合国家标准和用户要求的各种性能指标。
要做好检验标准、校验和检定等工作,以确保产品性能监控和产品质量的稳定。
六、售后服务售后服务是一项重要的工作,也是压力容器企业竞争力的体现。
企业需要完善售后服务流程,为用户提供及时、周到的服务。
对于用户遇到的问题要及时回应并提供解决方案,对于有质量问题的产品,要快速处理,及时维修或更换产品,以维护客户的利益。
总之,严格遵守压力容器制造守则,保障制造质量和产品安全,同时在售后服务上与客户建立长期信任。
压力容器工艺守则

压力容器工艺守则压力容器是在许多行业中使用的重要设备,如化工、石油、天然气等。
为了确保压力容器的安全性能和可靠性,需要遵守严格的工艺守则。
下面就是关于“压力容器工艺守则”的一些详细介绍。
一、压力容器的设计标准根据不同的行业和用途,压力容器有着不同的设计标准和规范。
在设计压力容器时,必须遵守所采用的国家或行业标准,例如ASME(美国机械工程师协会)规范、JIS(日本工业标准)或GB(国家标准)等。
在进行设计的过程中,还要考虑到容器的适用环境和使用条件,并应遵循安全性、可靠性、经济性和节能减排等原则。
二、材料的选择在压力容器的设计中,材料的选择是至关重要的。
选择材料时,需要考虑其抗腐蚀性能、强度、塑性、热膨胀系数、裂纹敏感性等因素。
钢制品是最常用的压力容器材料,而不锈钢、镍合金、合金钢等也是常见的选择。
必须严格遵照标准要求,选择具有合适化学成分和相应耐蚀性的材料。
三、焊接工艺的要求焊接是压力容器制造的重要环节之一。
焊接质量的好坏直接影响着容器的结构安全和产生不良事故的概率。
焊接前需要进行充分的预备工作,如清洁焊接部位、选用适当的焊接工艺、应用合适的焊接辅材、保障佳的焊接温度、施加正确的焊接加压力等。
必须注意对焊接部位进行可靠性测试,进行X光或者超声波探伤等测试手段,以确保数据真实有效。
四、检测和检验在压力容器的制造中,将涉及很多不同的检测和检验程序和设备,以确保容器的质量和安全性。
例如,涉及到材料金相检测、焊接断面金相检测、压力试验、超声波探伤等等。
每一项检测和检验都必须符合国家或行业标准的要求,并由专业的检验人员进行操作。
在检测和检验过程中,如出现任何问题,都应及时进行排除和修复,确保容器构件可以满足标准要求和安全性能。
总的来说,压力容器工艺守则是非常重要的,必须遵循标准要求,确保容器的安全性和可靠性。
只有符合标准,压力容器才可以发挥其最大的作用,为我们的生产和生活提供更加稳定的保障。
在制造压力容器时,合理选材、科学自变量规、精选接径合和高质量检测是非常必要的。
- 1、下载文档前请自行甄别文档内容的完整性,平台不提供额外的编辑、内容补充、找答案等附加服务。
- 2、"仅部分预览"的文档,不可在线预览部分如存在完整性等问题,可反馈申请退款(可完整预览的文档不适用该条件!)。
- 3、如文档侵犯您的权益,请联系客服反馈,我们会尽快为您处理(人工客服工作时间:9:00-18:30)。
************************文件编号:SN—SZ—02版本: 1修改状态: 0奥氏体不锈钢制压力容器制造工艺守则编制:****** 日期:****年**月**日审核:****** 日期:****年**月**日批准:****** 日期:****年**月**日发布日期:****年**月**日实施日期:****年**月**日受控状态受控□非受控分发号持有人**********************************作业指导书奥氏体不锈钢制压力容器制造工艺守则文件编号:******** 版本: 1 修改状态: 0文件审批修改记录1材料1.1材料的验收1.1.1用于制造容器的不锈钢板(包括不锈钢复合钢板)、钢管、圆钢、钢丝等原材料和焊条、焊丝、焊剂等焊接材料应符合相应的国家标准、行业标准的规定。
入厂时,须经检验部门根据材料生产单位提供的质量证明书(原件或复印件)按照标准,原材料入厂验收规则验收后,方准入库。
严禁使用标志(记)不明,未经检验科验收的各种材料。
1.1.2原材料和焊接材料的验收要求:原材料和焊接材料必须符合下列标准或规定。
不锈钢材料使用温度及许用应力符合GB150 中第二章及附录A15的规定。
1.1.2.1热轧和热锻不锈钢棒应符合:GB1220《不锈钢棒》。
1.1.2.2不锈钢管应符合GB/T14976 《流体输送用不锈钢无缝钢管》。
1.1.2.3不锈钢板应符合GB3280 《不锈钢冷轧钢板》、GB4237 《不锈钢热轧钢板》、GB8165《不锈钢复合钢板》。
1.1.2.4不锈钢焊接材料,焊丝应符合GB4242《焊接用不锈钢丝》、焊条应符合GB983《不锈钢焊条》、焊剂按“焊接材料产品样本”规定(1997年第一机械工业部编)。
1.1.2.5压力容器用不锈钢锻件应符合JB4728《压力容器用不锈钢锻件》的要求。
1.1.2.6原材料的入厂验收按写上公司文件编号《原材料入厂验收制度》的规定进行,用于制造第三类压力容器主要受压元件的材料必须复验,同批同牌号、同规格的材料抽验1件,复验内容:力学性能和弯曲性能,每个炉号的化学成份抽验1件。
1.1.2.7压力容器用不锈钢锻件的验收按JB4728《压力容器用不锈钢锻件》、图样或合同及写上公司文件编号《外协件质量管理制度》进行。
1.1.2.8进口的不锈钢原材料和焊接材料,应是国外压力容器规范允许使用的材料,其使用范围应符合相应规范的规定,并有该材料的质量证明书。
一般可按出口国的规范检验。
1.1.2.9进口的不锈钢原材料首次使用前,应进行试验和验证,满足技术要求后才能投料。
1.2材料的管理材料的保管按写上公司文件编号《材料采购、保管管理制度》的规定执行。
1.2.1原材料按品种、钢号、规格、炉号、热处理状态分类放置,并作出明确标志,以防止混放。
1.2.2原材料应存放在干燥、清洁的仓库内,严格控制灰尘。
不允许与黑色金属和水泥地、砂石直接接触。
1.2.3原材料的搁置要稳妥,堆放要整齐,要防止损坏(划痕、撞伤、压痕)和弯曲,散装的光亮板应放在15°斜度的货架上。
1.2.4焊接材料的存放按写上公司文件编号《焊接材料一级库管理制度》的规定。
1.2.5焊接材料的焙烘、保温、发放按写上公司文件编号《焊接材料二级库管理制度》的规定。
1.2.6钢板吊运时,要防止钢板变形。
钢丝绳要加护套,以防损伤材料表面。
2成型加工2.1场地2.1.1应有专用车间或专用场地,经常保持清洁、干燥、严格控制灰尘,并应铺设木质或橡胶垫板。
2.1.2不得与黑色金属制品或其他产品混杂生产。
2.1.3禁止直接踩踏不锈钢表面。
进入工作场所;应穿无钉鞋。
2.2划线2.2.1指生产必须按样板划线,样板可用镀锌铁皮制成。
2.2.2划线应在清洁的木板上或光洁的平台上进行,不允许用钢针划辅助线以及非切割线上敲洋冲印。
标记移植采用色笔,不准打钢印,做好记录。
2.2.3划线时要注意焊缝布置,焊缝布置要符合图纸或工艺规定。
一般要注意下列问题:2.2.3.1尽量避免在焊缝上开孔,如必须开孔,则以开孔中心为园心,1.5倍开孔直径为半径的圆中所包容的焊缝,需采用图样规定的探伤方法,进行百分之百射线或超声波探伤检查。
2.2.3.2组装时,避免十字焊缝,相邻圆筒A类焊缝的距离或封头A类焊缝的端点与相邻圆筒A类焊缝的距离应大于名义厚度S的三倍,且小于100mm,筒节长度应不小于300mm。
2.2.3.3封头各种不相交拼接焊缝之间的最小距离应不小于封头名义厚度S的三倍,且不小于100mm。
封头由瓣片和顶圆板拼接制成时,焊缝方向只允许是径向和环向的(见图1)。
2.3下料2.3.1剪床应保持清洁、刃口保持锐利润滑应良好。
为防止板材表面划伤;压脚上应包橡胶等软质材料。
刃口间隙可按下表选用:2.3.2剪切不锈钢板的剪床应尽量做到专用,当不能专用时,应在剪切不锈钢板前,把刃口台面揩擦干净。
2.3.3板材的剪口和边缘,不应有裂缝、压痕、撕裂等现象,剪口下塌δ1和倾斜δ2应小于板厚的10%(图2)δ1sδ2图22.3.5剪好的材料整齐地堆放在底架上,以便连同底架吊运,板间要垫橡胶木板,毯子等软质材料,以防损伤表面。
2.3.6圆钢和管子可用车床、锯床或砂轮切割机等方法下料,如还需焊接,则要除去割口处砂轮残屑及毛刺。
2.3.7厚板的下料或开孔,可用等离子切割或电弧切割进行。
板的周边或坡口用刨边机加工到图样、工艺文件要求。
孔边缘用砂轮机或锉刀除去割口的氧化物至显露金属光泽。
2.3.8施焊前将坡口表面的氧化物、油污、熔渣及其它有害杂质清除干净,清除的范围(以离坡口边缘的距离计)不得小于20mm。
2.3.9等离子切割的切口宽度和下料余量(尚需切削加工)参见下表:2.3.10进行钻、锪、车削等机械加工时,冷却液一般采用水基乳化液。
2.4成型2.4.1成型一般在冷态下进行,成型设备以及工装模具的工作表面,应干净清洁、无铁锈,碳钢屑及油污等脏物,表面粗糙度应符合图样及工艺文件要求。
2.4.2须使用不锈钢锤、木锤和铜锤,避免使用钢锤。
2.4.3筒体冷卷2.4.3.1 卷板机上下辊要清除油污及毛刺,必要时用纸覆盖轧辊,防止不锈钢板受损伤及污染。
复合钢板对口错边量b不大于钢板复层厚度的50%,且不大于2mm。
2.5焊接2.5.1焊前清除坡口及其两侧25mm范围内的油污等污物。
在不锈钢坡口两侧100mm范围内应涂白垩粉,防止沾附飞溅。
2.5.2选用尽可能小的线能量,特别是进行双层或多层焊时,除盖面层允许轻微摆动外,其余各层焊缝要求窄一些,焊条横向摆动范围按照焊条说明书要求,一般不超过焊条直径的2.5倍,要进行快速短弧焊,焊接结束或中断时,收弧要慢,弧坑要填满。
多道焊时,要严格控制层间温度不大于100℃。
2.5.3 与介质接触的焊缝一侧,尽可能最后进行焊接,以防重复加热。
2.5.4 每焊完一层焊缝可以浇冷水,使其快冷。
如条件允许,可以在焊缝背面浇冷水,或边焊边浇,但必须注意焊接熔池内不能有水。
亦可采用铜垫通水强制冷却。
2.5.5工艺上允许碳弧气刨清根时,刨槽应打磨直至露出金属光泽。
2.5.6 因焊接在环向形成的棱角E,用弦长等于1/6设计内直径D I,且不小于300mm的内样板或外样板检查(见图),其E值不得大于(0.1S+2)mm且不大于5mm(见图3)。
因焊接在轴向形成的棱角E,用长度不小于300mm的检查尺检查,其E值不得大于(0.1S+2)mm,且大于5mm。
2.5.7不锈钢容器的表面如有局部伤痕,刻槽等影响耐腐蚀性能的缺陷应予修磨,修磨深度不应超过钢板厚度(复合钢板指复层厚度)的负偏差C1。
2.5.7.1筒体与封头对接时,筒体制造尺寸应与封头车削后的直段围圆尺寸配作。
2.6.2热冲压时,毛坯加热不得渗碳和过烧,接触毛坯的支承块表面也应是奥氏体不锈钢。
对于0Cr18Ni19Ti,热冲压加热温度为1130℃~1180℃,终压温度为820℃~850℃。
2.6.3冲压所用的工具、压模、工作台面,须清理干净,不允许有铁屑、氧化皮等杂物存在。
2.6.4经热冲的不锈钢零件,凡图纸有抗晶间腐蚀倾向性试验要求时,应做固溶化处理。
2.6.5不锈钢制封头压制时要做到:a)焊缝正面应位于封头外侧,封头外侧过渡区至直边部份的正反面焊缝在压制前须磨至和母齐平,封头内侧的焊缝在压制前须全部磨平。
c)椭圆形、碟形、球形及折边锥形封头的直边部份上的纵向皱折深度应不大于1.5mm。
2.6.6热冲压封头(包括其他热冲压件)应按图样要求附带试板,以便根据图纸要求进行力学性能试验,试板与封头同炉热处理。
2.6.7热冲压不锈钢封头在固溶化处理时,要采取防变形措施,如采用十字撑加固等方法。
2.6.8冷冲压的不锈钢材料要求为固溶状态交货。
2.6.9冲压速度不宜太大,以满足零件顺利成型。
2.6.10不锈钢封头压制后的弹性比碳钢封头大,若借用碳钢封头的压模时须注意。
2.6.11封头内外表面应光滑、过渡平滑、不允许有划痕,裂纹等缺陷。
外协件应按《外协件质量管2.7.3弯管后,弯头外侧不得有裂纹及较深的划痕,内侧不得有明显的皱折。
2.7.4受压管路弯管后,应能通过直径为85%管子内径的钢球。
2.7.5成品的管品内侧应将毛刺锉干净。
2.7.6U形管的弯制2.7.6.1U形管不宜热弯,否则须征得用户同意。
2.7.6.2U形管弯管段的圆度偏差,应不大于管子外径的10%。
2.7.6.3当有耐应力腐蚀要求时,冷弯U形管的弯管段及至少包括150mm的直管段应进行热处理。
2.7.6.4奥氏体不锈钢管可按供需双方商定的方法进行热处理。
2.7.6.5换热管拼接时,须符合以下要求:a)同一根换热管,其对接焊缝不得超过一条(直管)或二条(U形管);b)最短管长不得小于300mm。
c)包括至少50 mm直管段的U形管弯管段范围内不得有拼接焊缝;d)对口错边量应不超过管子壁厚的15%,且不大于0.5 mm;直线度偏差以不影响顺利穿管为限;e)f)对接接头应进行射线探伤,抽查数量应不少于接头总数的10%,年且不少于1条,符合JB4730-94《压力容器无损检测》的Ⅲ级为合格,如有1条不合格,应加倍抽查,再出现不合格时,应100%检查。
g)对接后的换热管,应逐根作液压试验,试验压力为设计压力的2倍。
2.8折边2.8.1与工件接触的折边模模腔应光滑,无铁锈、油污、模具接头处应平整。
2.8.2180°折边时,板材的抛光纹路应与折边的折边线方向垂直,以防裂开或折边后抛光。
2.9锻造不锈钢锻件,要编制锻造工艺卡,并注意以下事项:2.9.1为防止锻件加热的渗碳和过烧,不允许与碳素钢及低合金钢同炉加热。
加热宜采用电炉或反射炉,并应有自动时间-温度记录。
2.9.2为防止锻造裂纹,应严格控制始锻温度和终锻温度。