品质部作业流程图
品质部作业流程图
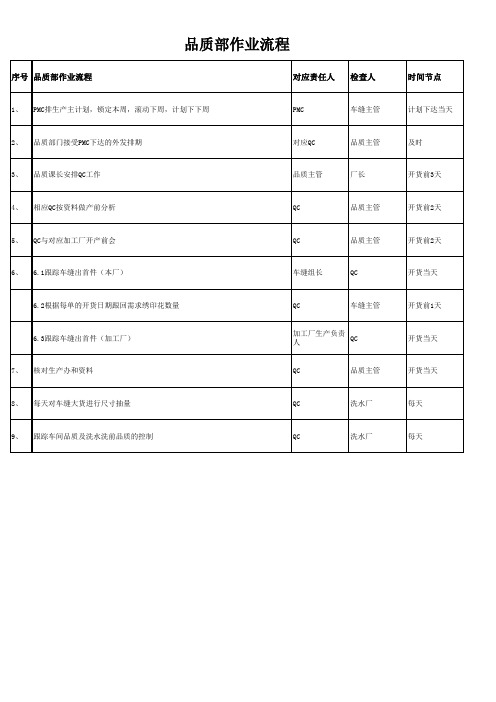
每天
9、
跟踪车间品质及洗水洗前品质的控制
QC
洗水厂
每天
品质部作业流程图
客 户
1\PMC计 划
业 务
2\查看排 期
计 划
3\接受订 单资料
技 术
4\产前分 析
5\开产 前会
6.1跟踪车 缝出首件 6\分配 QC工作 6.2绣、印 花品质、 进度跟踪 6.3外发车 缝出首件 7\核对首件资 料及品质检查
品质部作业流程
序号 品质部作业流程 对应责任人 检查人 时间节点
1、
PMC排生产主计划,锁定本周,滚动下周,计划下下周
PMC
车缝主管
计划下达当天
2、
品质部门接受PMC下达的外发排期
对应QC
品质主管
及时
3、
品质课长安排QC工作
品质主管
厂长
开货前3天
4、
相应QC按资料做产前分析
QC
品质主管
开货前2天
5、
QC与对应加工厂开产前会
QC
品质主管开货前2天来自6、6.1跟踪车缝出首件(本厂)
车缝组长
QC
开货当天
6.2根据每单的开货日期跟回需求绣印花数量
QC
车缝主管
开货前1天
6.3跟踪车缝出首件(加工厂)
加工厂生产负责 QC 人
开货当天
7、
核对生产办和资料
QC
品质主管
开货当天
8、
每天对车缝大货进行尺寸抽量
QC
洗水厂
生 产
8\洗前尺 寸的抽查
洗 水
9\跟踪车缝品质 及洗前尺寸的控 制
非标门品质部流程图
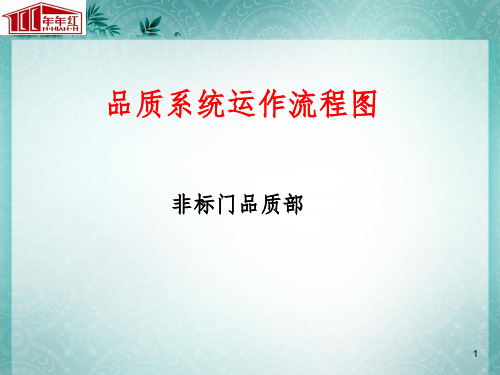
非标门检验流程----钣金车间
•剪板对角线检验
12
非标门检验流程----钣金车间
• 门面冲孔尺寸检验
13
非标门检验流程----钣金车间
• 门面冲孔尺寸检验
14
非标门检验流程----钣金车间
• 门面冲孔尺寸检验
15
非标门检验流程----钣金车间
• 门面冲孔尺寸检验
16
非标门检验流程----钣金车间
• 门面折弯尺寸检验
17
• 门面折弯尺寸检验
非标门检验流程----钣金车间
18
非标门检验流程----钣金车间
• 门面折弯尺寸检验
19
• 门架拉管检验
非标门检验流程----钣金车间
20
非标门检验流程----钣金车间
• 门架折弯尺寸检验
21
非标门检验流程----钣金车间
• 门架冲孔尺寸检验
22
1、原材料按公司要求进行检测,门面材料厚±0.03mm,门架材料厚度 ±0.04mm。 2、花型内部轮廓完好清晰,上下、左右不偏倚;表面无划伤、破损、褶 皱、裂缝、压痕、鼓包、波浪、等不良现象。 3、无特殊要求时压花花型位于门板正中心位置,花型距门板边缘上、下 距离尺寸偏差不大于1mm、左右距离偏差不大于1mm。 4、油漆用秒表和漏斗检测,时间12 ㏕ ±3 ㏕ 5、五金配件主要检验表面外观及孔位尺寸,抗腐蚀及老化程度做盐雾试 验、紫外线老化实验。
38
• 配门检验
非标门检验流程----钣金车间
39
非标门检验流程----喷漆车间
打磨检验要求 1、表面打磨后不能残留胶水、标签、锈迹、焊点、水笔印。 2、表面有凹凸不平的地方,经检验判定须批灰处理的应处理平
品质异常处理作业流程图

对异常品处置确 定意见。
对异常品处置进 行评审签字。
30分钟内不能对 异常排除,汇报 车间主任.
对异常内容调查 同时进行异常排 除.
组织专业人员,对 现场异常处理.
对异常品处置进 行评审签字。
在60分钟内异常 不能排除,汇报生 产部长.
生产部长
异常停线2H上报 公司副总经理.
项目
发现者
发现异常品时, 立即停止作业;
对异常品进行隔
作
离\标志,联络检
业
流
程
作业者在10分钟 内向班长汇报.
检验员 检验员对隔离 的异常品确认.
填写异常处理 联络单。
品质异常处理作业流程图
工程师
组织相关人员, 进行再发防止对 策的确立和实施
班长
车间主任
异常品处置损失 超过500元 ,汇 报质量部长批准.
异常现象排除在 2个小时内不能 解决时,换线组 织生产。
现场组织资源, 对异常现场处理.
NO.
质量部长
对损失大于500元 的异常品处置, 进行评审
异常品处置损失 超过2000元 ,上 报副总批示.
标记
更改内容
更改人
更改日期
批准
审核
编制
品质部各岗位职责与流程
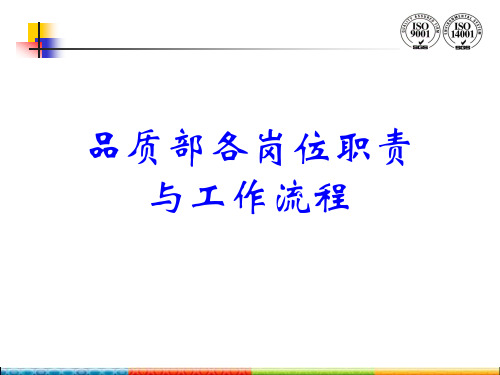
IQC 来料检验
来料检验工作流程
供应商送货 仓库暂收 放置待检区 IQC检查
发出来料检验报告 纠正预防措施报告
组织评审
评审同意使用
评审单位: 业务/PMC/工程/采购; 由品质做最终判定。
评审判退
不合格品区
PASS入库
退货供应商
OQC出货检验
OQC:即出货检验, Outgoing Quality Control 的英文缩写简称
IPQC制程检验
1.首件确认
制程检验的工作职责
生产部提交首件确认单,IPQC对比相关标准依据,对产品结构、外观、
尺寸等进行检查,对所检验的产品填写《首件报告》。首件合格即量产,不合
格即要求改善。首件未合格之前,生产不得量产;否则发出《品质异常通知单》
2.巡回检查
在既定的时间范围对自己所负责的机台产品,进行巡回检查(5-10啤产
4.品质异常的清仓确认
当生产现场发生异常或遭到客诉异常时,OQC需协助清查在库品状 态,是否存在类似异常的产品;结果汇报并处理、跟进;
OQC出货检验
出货检验工作流程
出货指令单
发出不合格 品处理报告
仓库备料 放置待检区
组织评审
OQC检查
评审同意出货
PASS出货
评审单位: 业务/PMC/工程/生产; 由品质做最终判定。
出货检验的目的:
产品在出货之前为保证出货产品满足客户品质要求。
出货检验的工作职责
1.出货检查:
负责成品出货前的检验工作,出货产品符合相关检验标准,进行最 终的成品检验;并对于所检验的产品或批次需填写《OQC检验报告》
2. 检验标示
做好出货检验状态(合格、不合格)的标示。
机械加工品质控制流程图
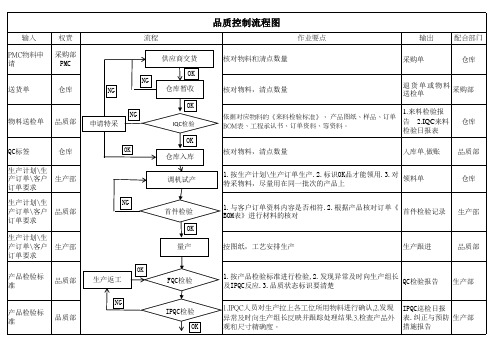
输入 PMC物料申 请 权责 采购部 PMC NG 送货单 仓库 NG
NG
流
输出 采购单
配合部门 仓库
OK 仓库暂收 OK 物料送检单 品质部 申请特采
IQC检验
核对物料,清点数量
退货单或物料 采购部 送检单 1.来料检验报 告 2.IQC来料 检验日报表 入库单.做账
依据对应物料的《来料检验标准》、 产品图纸、样品、订单 BOM表、工程承认书、订单资料、等资料。
仓库
OK
QC标签
仓库
OK
仓库入库 调机试产 NG
首件检验 OK
核对物料,清点数量
品质部
生产计划\生 产订单\客户 生产部 订单要求 生产计划\生 产订单\客户 品质部 订单要求 生产计划\生 产订单\客户 生产部 订单要求 产品检验标 准
OK
1.按生产计划\生产订单生产.2.标识OK品才能领用.3.对 领料单 特采物料,尽量用在同一批次的产品上 1.与客户订单资料内容是否相符.2.根据产品核对订单《 首件检验记录 BOM表》进行材料的核对
仓库
生产部
量产
按图纸,工艺安排生产
生产跟进
品质部
品质部
生产返工 NG
FQC检验
1.按产品检验标准进行检验,2.发现异常及时向生产组长 QC检验报告 及IPQC反应.3.品质状态标识要清楚 1.IPQC人员对生产拉上各工位所用物料进行确认,2.发现 异常及时向生产组长反映并跟踪处理结果.3.检查产品外 观和尺寸精确度。
生产部
产品检验标 准
品质部
IPQC检验 OK
IPQC巡检日报 表.纠正与预防 生产部 措施报告
品质控制流程图
输入 权责 流程 作业要点 输出 配合部门
质量管理流程图表

确认产品的包装 清晰正确,数量
入成品库 出货
备注: 在检查过程中,如果遇到比较难判定的检查项目或异常情况,可以上报给质量主管王xx,让她作出判断.
量具管理工作
量具购回 量具登记、编号、标识, (担当者:张xx,
新量具校验并记录, (担当者:王xx,
量具存放到固定的地方,妥善保管 (担当者:张xx,
担当者:王xx 监督者:张x 工作内容: 1.按照计划将本司 所有除卡尺、千分 尺、螺纹规、塞规 以外的其它内校量 具在规定的环境下, 参照校验说明书, 进行校验,并作好 相应的记录. 2.将校验德出的 “降级、停用、报 废”结果的情况反 馈给检验主管和相 关量具使用的部门
担当者:王xx 工作内容: 1.按照计划定期将 需要外校的量具送 外校正,并确认其 校验结果,作好相 关记录. 2.将外校得出的 “降级、停用、报 废”结果的情况通 知到相关量具使用 部门或个人.
担当者:张x 工作内容: 1.按照标准抽 样比例将每批 加工好的成品 进行抽检,并 作好检验记录 报告.将检验 结果反馈给检 验主管.
担当者:王xx ( 张x协助) 工作内容: 1.根据出货 通知单对出货 产品进行出货 检验,并作好相 应的检验记录.
担当者:王xx 工作内容: 1.分配量具管 理工作,监督其作 好量具统计和量 具发放记录. 2.按计划分配 量具校正工作,并 作好校正记录. 3.监督其作好 量具保养和维修 工作,并作好记录
首 检
巡 检
入库检
样品首检
量产首检
工作内容: 1.对新产品调 试样品进行检 验,并作好首检 记录. 2.首件检查合 格,开机前将样 品封存至机床 边. 3.待样品加工 完,对样品进行 全数检验,并将 检验结果反馈 给车间主任:王
品质异常处理作业流程图(精)
.客诉不良品的返工退货
1.品质接到客户的投个诉,一个工作日完成围堵措施;
2.品质窗口为定品质工程师来确认,具体的人员田丽兼职,5月19日之前定具体的人员
3.DOA,RMA,客诉由该品质工程师来处理;
4.对于功能的确认品质会做初步的检测与;
5.批量返工,由工程给出返工SOP;PMC直接下单进行批量返工;
6.对于客诉的严重性,将召开不同等级的品质会议;
1.来料产品规格书是工程承认后,给到IQC;
2.品质将主导MRB会议的召开;
1.首检由生产送检,生产,工程,品质签字确认;
2.合同评审的评审时必须对客制化信息进行确认,工程下达SOP给到生产,品质;;
3.品质根据客制化信息制定检验标准
4.品质对应只是生产部门,工程部门对生产部门的工艺,产品异常负责;
生产的变更
1.客户的变更及客户的客制化信息变更工程必须下达给到生产,品质人员;
2.品质设置白板,品质主导把每天的异常记录到白板上,现场对问题进行检讨与改善;品质人员
3.不能解决的问题,直接上升到各自领导层面
4.一码多料问题,由PMC整理后,在总监会议进行检讨;
的人员
,品质;;
与改善;品质人员:翟红云。
品质部检验流程图总表
[品质部管理流程图]1:品质管控流程图2:QA成品检验流程图3:IPQC巡检流程图4:IQC来料检验流程图品质管控流程图 厂商交货IQC 检验生产计划IPQC 首件检IPQC 巡回检生产安排 发现不合格品QC 测试发现不 合格品发现不 合格品QA 检验joK 品贴绿色标标 识预防改善______________. _____处置1 T异常开案1 r隔离发现不 合格品QA成品检验流程图流程说明1:生产线把做好的成品送检至QA o2:QA根据《产品规格书、图纸》《样品》《生产指令单》《AQL抽样计划》对送检成品进行外观和功能性检验,有必要时需进行可靠性试验。
3:检验完成时填写《QA检验报告》记录存档。
4:产品合格后贴绿色合格标识并通知入库,产品不合格则贴红色标识,注明不良原因,并开出《QA检验不良报告》。
5:由品质部,研发中心,业务部,生产部门,计划部共同确认不良产品处理方式。
6:处理方法确认后对不良产品进行处理,并跟进。
流程说明1:生产线领料后按《作业指导 书》进行首件制作。
2:生产线制作首件交于IPQC 进行首件确认。
3:IPQC 根据《作业指导书》 《产品规格图纸》《产品规格 书》《样品》对首件的性能, 外观,尺寸进行确认,并填写 《首件确认表》。
4:首件合格后交由生产并开 始生产作业,首件不合格则要 求生产分析并作出改善措施, 重做首件进行确认。
5:正常生产开始后IPQC 进行 巡回检验,作业员需按照《生 产SOP 》进行作业,注意电 子产品的防护。
6:巡检未发现异常,生产持续 作业至产品完工,如巡检过程 发现异常,开出《生产异常报 告》通知生产,品质部,研发 中心。
7:生产,品质部,研发中心分 析不良原因,给出改善措施。
确定是否需要停止生产。
8:确定改善措施后,IPQC 进 行监督性检验,跟进措施实行 效果。
9:产品生产完工,生产移交产 品或入库。
10:IPQC 填写《每日巡检报 告》IPQC 巡检流程----首件检验kt !1!重做首样不合格 合格生产移交或入库供应商/外协厂送货至仓库仓库收料打单送检IQCIQC检验流程图IQC进行物料检验(根据承认书.样板.规格书等)填写?IQC检验报告?流程说明1:供应商/外协厂送货至仓库,仓库确认数量,型号,合格放置待检区并打单送至IQC,不合格退货至供应商。
SMT作业详细流程图
刮刀准 备
PCB板
领物料
锡膏、红胶 准备
料架准 备
转机工 具准备
程序/排列表 /BOM/位置图 检查是否正 确、有效
确认PCB 型号/周 期/数量
物料分 机/站位
解冻
搅拌
清机前点数
清机前对料
转机开始
Page 6
SMT转机流程
接到转机通知
熟悉工艺指导卡及注意事项
领钢网
领PCB
领物料及分区
领辅助材料
产线QC与操作员确认签名
IPQC签名确认
开始首件生产
Page 8
SMT首件样机确认流程
工程部 品质部 SMT部
提供工程样机 N PE确认 Y
生产调试合格首部机芯
核对工程样机 Y 元件贴装效果确认 N N 通知技术员调试
IPQC元件实物 测量
Y
OQC对焊接质量进行复检
Y
N 回流焊接或固化并确认质量
SMT详细流程图
SMT总流程图
N PCB来料检查 Y 网印锡膏/红胶 印锡效果检查 Y 贴片 炉前QC检查 Y 过回流炉焊接/固化 焊接效果检查 Y 后焊(红胶工艺先进行波 峰焊接) 后焊效果检查 Y 功能测试 Y 成品机芯包装送检 N 交修理员进行修理 N 向上级反馈改善 N 通知技术人员改善 Y N 校正 夹下已贴片元件 N N 通知IQC处理
填写样机卡并签名
对照样机进行生产、检查
Page 9
SMT首件样机测量流程
SMT部
品质部
转机调试已贴元件合格机芯
N 通知技术员调整 检查所有极性元件方向 Y 参照丝印图从机芯上取下元件 将仪表调至合适档位进行测量
将实测值记录至首件测量记录表
品质部样件工作流程图
品质部样件工作流程1 目的规模具样件发货后至模具发货前各项工作均按流程进行操作。
2 围本程序适用于公司所有模具样件及模具发货的各相关部门。
3 归口管理部门品质部4 职责权限4.1项目部:传递模具样件及模具发货前相关顾客信息;4. 2技术部、装配部:负责对样件及模具异常信息进行书面的反馈和整改;4.3品质部:品质部负责检验、判定模具样件及模具的质量。
5 标准程序5.1检验部门对样件进行检验,同时对模具进行初检,产生《样件检验单》和《模具初检单》。
5.2检验部门召开会议,讨论整改时间节点,项目部将时间安排作为新的一列加入进度表。
5.3当对问题点有异议时,装配部及技术部第一时间将反馈意见以书面形式通知检验部,以取得检验部的确认。
如果没有反馈自行决定不整改,检验部将按未整改来处理。
产生《装配部整改反馈》及《技术部整改反馈》,同时检验部产生《未整改管理措施》。
6、工作流程生产过程管理程序1 目的本程序目的是对与生产过程有关质量的因素,包括人员、设备、材料、操作方法、作业环境进行有效的控制和管理。
确保生产过程的每个工序按规定的方法在受控状态下进行。
2 围本程序规定了过程控制的容和办法。
本程序适用于对生产过程进行有效的控制、产品标识与追溯、工作环境之管理。
3 引用文件LY-QP-023 《采购管理程序》LY-QP-030 《文件和资料控制程序》LY-QP-029 《不合格品控制程序》LY-QP-032 《产品搬运、贮存、包装与防护管理程序》LY-QP-009 《产品标识和可追溯性程序》4 术语和定义工作环境: 指影响员工作业或产品品质之设备条件,包含温度、湿度、防尘、空气污染、震动、安全卫生等要项,是无形的,其管制是通过新增或改善设施来达到改善、提高的。
5 职责5.1 生产部是本程序的归口管理部门,负责编制生产作业计划及其生产调度工作,负责设备维修和管理。
5.2 技质部工艺组负责编制各类工艺规程、技艺评定准则和必要的作业指导书.5.3 技质部品检组负责生产过程各工序制件的专检;并且对过程中不合格品进行标识和记录.5.4 采购部负责为生产过程提供合格的原材料和辅料。