铝合金切削刀具加工参数分析与选用
6mm铣刀铣铝参数
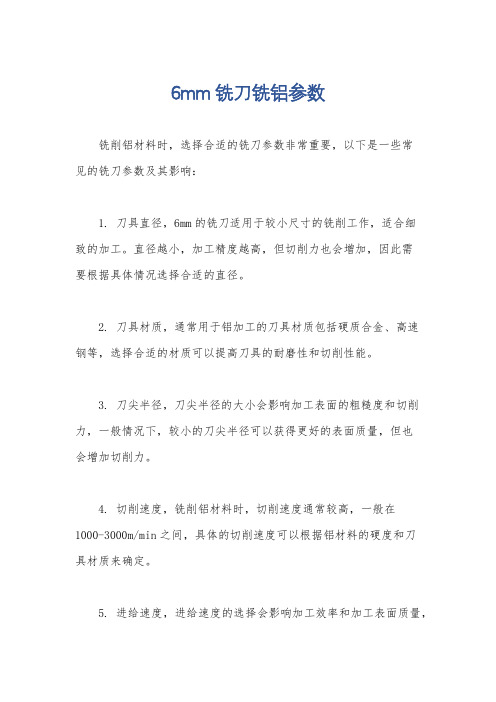
6mm铣刀铣铝参数
铣削铝材料时,选择合适的铣刀参数非常重要,以下是一些常
见的铣刀参数及其影响:
1. 刀具直径,6mm的铣刀适用于较小尺寸的铣削工作,适合细
致的加工。
直径越小,加工精度越高,但切削力也会增加,因此需
要根据具体情况选择合适的直径。
2. 刀具材质,通常用于铝加工的刀具材质包括硬质合金、高速
钢等,选择合适的材质可以提高刀具的耐磨性和切削性能。
3. 刀尖半径,刀尖半径的大小会影响加工表面的粗糙度和切削力,一般情况下,较小的刀尖半径可以获得更好的表面质量,但也
会增加切削力。
4. 切削速度,铣削铝材料时,切削速度通常较高,一般在
1000-3000m/min之间,具体的切削速度可以根据铝材料的硬度和刀
具材质来确定。
5. 进给速度,进给速度的选择会影响加工效率和加工表面质量,
通常情况下,较大的进给速度可以提高加工效率,但较小的进给速度可以获得更好的加工表面质量。
6. 切削深度,切削深度的选择需要考虑刀具的承受能力和加工的要求,一般情况下,较小的切削深度可以减小切削力,获得更好的加工表面质量。
总的来说,铣削铝材料时,6mm的铣刀可以适用于一些细致的加工,但在选择刀具参数时需要综合考虑加工的要求、材料的硬度和刀具的特性,以获得最佳的加工效果。
铝合金的高速切削加工技术研究
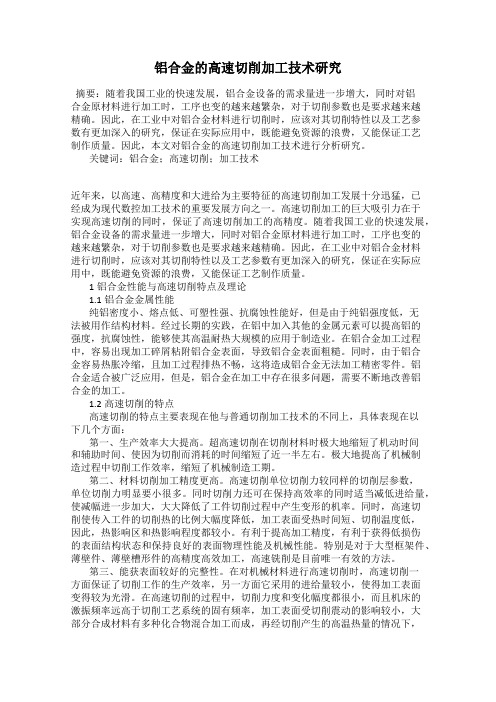
铝合金的高速切削加工技术研究摘要:随着我国工业的快速发展,铝合金设备的需求量进一步增大,同时对铝合金原材料进行加工时,工序也变的越来越繁杂,对于切削参数也是要求越来越精确。
因此,在工业中对铝合金材料进行切削时,应该对其切削特性以及工艺参数有更加深入的研究,保证在实际应用中,既能避免资源的浪费,又能保证工艺制作质量。
因此,本文对铝合金的高速切削加工技术进行分析研究。
关键词:铝合金;高速切削;加工技术近年来,以高速、高精度和大进给为主要特征的高速切削加工发展十分迅猛,已经成为现代数控加工技术的重要发展方向之一。
高速切削加工的巨大吸引力在于实现高速切削的同时,保证了高速切削加工的高精度。
随着我国工业的快速发展,铝合金设备的需求量进一步增大,同时对铝合金原材料进行加工时,工序也变的越来越繁杂,对于切削参数也是要求越来越精确。
因此,在工业中对铝合金材料进行切削时,应该对其切削特性以及工艺参数有更加深入的研究,保证在实际应用中,既能避免资源的浪费,又能保证工艺制作质量。
1铝合金性能与高速切削特点及理论1.1铝合金金属性能纯铝密度小、熔点低、可塑性强、抗腐蚀性能好,但是由于纯铝强度低,无法被用作结构材料。
经过长期的实践,在铝中加入其他的金属元素可以提高铝的强度,抗腐蚀性,能够使其高温耐热大规模的应用于制造业。
在铝合金加工过程中,容易出现加工碎屑粘附铝合金表面,导致铝合金表面粗糙。
同时,由于铝合金容易热胀冷缩,且加工过程排热不畅,这将造成铝合金无法加工精密零件。
铝合金适合被广泛应用,但是,铝合金在加工中存在很多问题,需要不断地改善铝合金的加工。
1.2高速切削的特点高速切削的特点主要表现在他与普通切削加工技术的不同上,具体表现在以下几个方面:第一、生产效率大大提高。
超高速切削在切削材料时极大地缩短了机动时间和辅助时间、使因为切削而消耗的时间缩短了近一半左右。
极大地提高了机械制造过程中切削工作效率,缩短了机械制造工期。
铝合金加工参数

铝合金加工参数
由于在加工过程中发现工件刀纹不致影响表面质量,查找了一些资料,作了一些摘要:
1.由于铝合金强度和硬度相对较低,塑性较小,对刀具磨损小,且热导率较高,使切削温度较低,所以铝合金的切削加工性较好,属于易加工材料,切削速度较高,适于高速切削.但铝合金熔点较低,温度升高后塑性增大,在高温高压作用下,切削界面摩擦力很大。
容易粘刀;特别是退火状态的铝合金,不易获得低的表面粗糙度。
2.与钢材和黄铜相比,铝合金的特点,一是材质软,刚性差,二是弹性模量低,这两个因素显著影响了铝合金的切削加工性。
因此,在加工铝合金工件时,必须充分地夹紧和支撑工件,并保持刀具锋利;否则,工件往往会有离开切削刀具的倾向。
有时工件的表面出现不规则的槽痕和光亮的挤压斑,一种可能是由于刀具对工件的压力不正常引发的,还有一种可能是由于夹持不牢固而引起振颤时,刀具在工件的表面作间隙式的磨蹭,发生挤压现象和粉状切削;然后,当间隙或弹性消失时,刀具就咬人工件的表面,啃出槽痕。
3.为了获得光洁的工件表面,尽可能采用粗切削和精切削的组合,因为各种合格的工件毛坯总会有一些氧化层,致使刀具受到相当程度的磨损。
如果最后切削工序采用抛光过的锋利刀具进行精细切削,就能达到以上要求。
4.通常把铝合金的切削性分为两类:1类是指工业纯铝和硬度小于80HB的退火状态铝合金;2类是指淬火时效状态的变形铝合金。
而铝合金的切削加工工艺参数与此类别有关。
金钢石刀具的典型切削参数
铝合金的典型铣削参数
铝合金攻螺纹前的钻孔的典型参数
铝合金的典型铰孔参数
注:冷却剂为煤油-松节油(5:4)混合物;或用约33°E的矿物油, 或优质油.干铰孔的质量不高。
pcd加工铝合金参数

pcd加工铝合金参数
PCD(聚晶金刚石)是一种高性能切削工具材料,常用于加工硬
质材料,包括铝合金。
在PCD加工铝合金时,需要考虑一些参数,以确保高效、精确的加工过程。
1. 切削速度
切削速度是指刀具切削材料的速度,通常用米/分钟(m/min)表示。
对于铝合金,建议切削速度为200-400 m/min。
当切削速度过高时,可能会导致切削工具损坏或铝合金表面产生热裂纹,而过低的切削速度则会导致加工效率低下。
2. 进给速度
进给速度是指刀具在切削中移动的速度,通常用毫米/转(mm/rev)表示。
对于铝合金,建议进给速度为0.05-0.15 mm/rev。
进给速度
过高可能导致刀具寿命缩短,而进给速度过低则会导致加工效率低下。
3. 切削深度
切削深度是指刀具在每个工作循环中切削材料的深度,通常用毫米(mm)表示。
对于铝合金,建议切削深度为1-3 mm。
切削深度过
大可能导致切削力和热量增加,从而影响刀具寿命和加工质量。
4. 刀具半径
刀具半径是指刀具切削部分的半径大小,通常用毫米(mm)表示。
对于铝合金,建议使用较小的刀具半径,以便更好地控制切削质量和表面光洁度。
5. 刀具材料
PCD刀具是PCD加工铝合金的最佳选择,因为它具有高硬度、高热稳定性和良好的耐磨性。
此外,还可以选择具有涂层的PCD刀具,以提高刀具寿命和加工效率。
总之,PCD加工铝合金需要仔细考虑各个参数,以确保高效、高质量的加工过程。
铝合金7系列和6系列加工参数
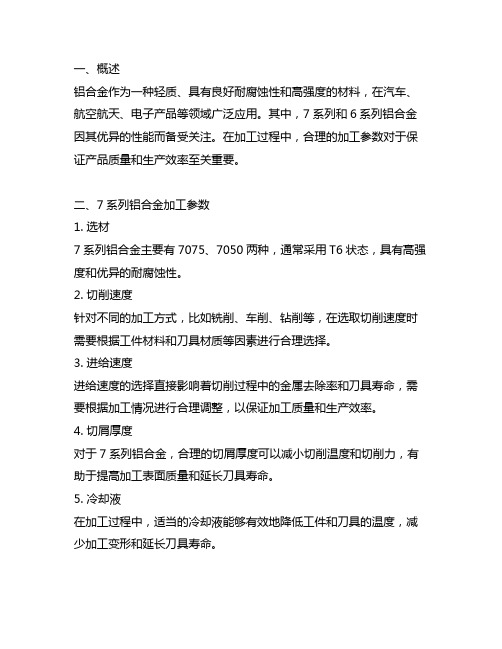
一、概述铝合金作为一种轻质、具有良好耐腐蚀性和高强度的材料,在汽车、航空航天、电子产品等领域广泛应用。
其中,7系列和6系列铝合金因其优异的性能而备受关注。
在加工过程中,合理的加工参数对于保证产品质量和生产效率至关重要。
二、7系列铝合金加工参数1. 选材7系列铝合金主要有7075、7050两种,通常采用T6状态,具有高强度和优异的耐腐蚀性。
2. 切削速度针对不同的加工方式,比如铣削、车削、钻削等,在选取切削速度时需要根据工件材料和刀具材质等因素进行合理选择。
3. 进给速度进给速度的选择直接影响着切削过程中的金属去除率和刀具寿命,需要根据加工情况进行合理调整,以保证加工质量和生产效率。
4. 切屑厚度对于7系列铝合金,合理的切屑厚度可以减小切削温度和切削力,有助于提高加工表面质量和延长刀具寿命。
5. 冷却液在加工过程中,适当的冷却液能够有效地降低工件和刀具的温度,减少加工变形和延长刀具寿命。
三、6系列铝合金加工参数1. 选材6系列铝合金主要有6061、6063两种,广泛应用于航空航天和轨道交通领域。
同样需要根据实际加工情况选择不同的状态和硬度。
2. 切削速度由于6系列铝合金具有较高的塑性,因此在选择切削速度时需要根据工件材料和刀具材质等因素进行合理调整,以避免刀具损坏和加工表面质量下降。
3. 进给速度进给速度的选择需要兼顾加工质量和生产效率,在实际加工中需要根据不同的工件和刀具情况进行合理调整。
4. 刀具材质对于6系列铝合金,选择合适的刀具材质能够有效地提高加工效率和保证加工质量。
5. 切削温度6系列铝合金的切削温度控制尤为重要,合理的切削温度能够避免刀具损坏和工件表面质量下降的问题。
四、结论7系列和6系列铝合金在实际加工中需要根据具体情况选择合适的加工参数,以保证产品质量和生产效率。
合理的切削速度、进给速度、切屑厚度等加工参数对于提高加工效率和延长刀具寿命都具有重要作用。
加工过程中的冷却液和刀具材质选择也同样重要。
数控车床加工铝件技巧

数控车床加工铝件技巧数控车床加工铝件是一种常见且重要的加工工艺,在很多行业中都得到了广泛的应用。
铝合金具有良好的可塑性和加工性能,但由于其热导率高、切削削具极易磨损,所以在加工过程中需要注意一些技巧,以保证加工质量和效率。
以下是一些数控车床加工铝件的技巧:1.选择合适的切削参数:铝合金的切削应力和热导率较高,加工过程中容易产生较大的热量。
因此,应降低切削速度和进给量,以避免过高的切削温度。
同时,要注意选择合适的刀具和切削液,以提高刀具寿命和加工质量。
2.使用合适的刀具:在数控车床加工铝件时,应选择合适的刀具。
通常情况下,采用硬质合金刀具效果较好。
硬质合金刀具具有较高的硬度和耐磨性,能够较好地抵抗铝合金的切削热和磨损。
3.控制刀具磨损:铝合金的磨损对刀具寿命和加工质量影响较大。
因此,要及时检查和更换磨损的刀具,以保持加工质量和效率。
此外,应注意刀具的冷却条件,避免切削温度过高引起刀具磨损。
4.优化切削路径和进给方向:在数控车床加工铝件时,应优化切削路径和进给方向,以减小切削阻力和提高切削效率。
通常情况下,采用螺旋切削和斜切削技术,能够有效地减小切削阻力和热量。
5.控制加工精度:在数控车床加工铝件时,要注意控制加工精度。
铝合金具有较大的热膨胀系数,加工时易出现变形,从而影响加工精度。
因此,要采取合适的工艺措施,如加工温度控制、合理的夹紧方式和切削力控制,以保证加工精度。
6.加工后处理:在加工完铝件后,应注意进行适当的后处理。
例如,进行热处理、表面处理或抛光等,以提高铝件的表面质量和性能。
总之,数控车床加工铝件需要注意切削参数、选择合适的刀具、控制刀具磨损、优化切削路径和进给方向、控制加工精度和进行适当的后处理。
这些技巧可以帮助提高加工效率和质量,确保铝件的精度和表面质量。
数控机床加工铝合金的最佳切削参数选择方法
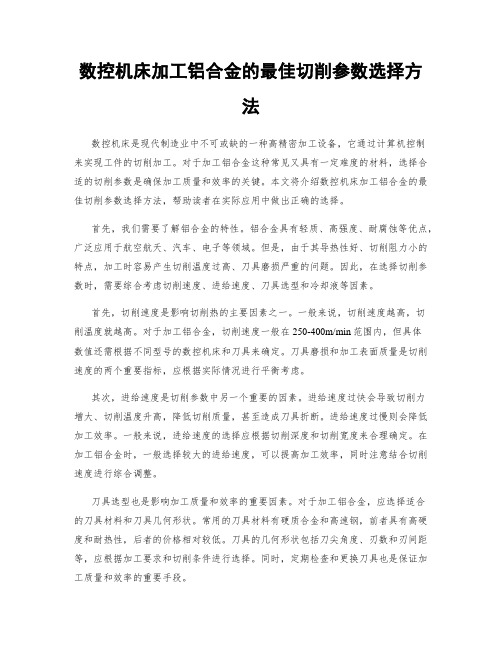
数控机床加工铝合金的最佳切削参数选择方法数控机床是现代制造业中不可或缺的一种高精密加工设备,它通过计算机控制来实现工件的切削加工。
对于加工铝合金这种常见又具有一定难度的材料,选择合适的切削参数是确保加工质量和效率的关键。
本文将介绍数控机床加工铝合金的最佳切削参数选择方法,帮助读者在实际应用中做出正确的选择。
首先,我们需要了解铝合金的特性。
铝合金具有轻质、高强度、耐腐蚀等优点,广泛应用于航空航天、汽车、电子等领域。
但是,由于其导热性好、切削阻力小的特点,加工时容易产生切削温度过高、刀具磨损严重的问题。
因此,在选择切削参数时,需要综合考虑切削速度、进给速度、刀具选型和冷却液等因素。
首先,切削速度是影响切削热的主要因素之一。
一般来说,切削速度越高,切削温度就越高。
对于加工铝合金,切削速度一般在250-400m/min范围内,但具体数值还需根据不同型号的数控机床和刀具来确定。
刀具磨损和加工表面质量是切削速度的两个重要指标,应根据实际情况进行平衡考虑。
其次,进给速度是切削参数中另一个重要的因素。
进给速度过快会导致切削力增大、切削温度升高,降低切削质量,甚至造成刀具折断。
进给速度过慢则会降低加工效率。
一般来说,进给速度的选择应根据切削深度和切削宽度来合理确定。
在加工铝合金时,一般选择较大的进给速度,可以提高加工效率,同时注意结合切削速度进行综合调整。
刀具选型也是影响加工质量和效率的重要因素。
对于加工铝合金,应选择适合的刀具材料和刀具几何形状。
常用的刀具材料有硬质合金和高速钢,前者具有高硬度和耐热性,后者的价格相对较低。
刀具的几何形状包括刀尖角度、刃数和刃间距等,应根据加工要求和切削条件进行选择。
同时,定期检查和更换刀具也是保证加工质量和效率的重要手段。
最后,冷却液的使用在加工铝合金时尤为重要。
冷却液不仅可以降低切削温度,还可以减少切削力和刀具磨损,提高加工质量和效率。
选择冷却液时应考虑其导热性、润滑性和抗腐蚀性等性能,同时要控制冷却液的喷射方式和压力,确保切削过程中刀具和工件始终处于良好的润滑和冷却状态。
关于铝合金材料PCD刀具加工应用的研究

关于铝合金材料PCD刀具加工应用的研究作者:刘源来源:《科教导刊·电子版》2017年第12期摘要铝合金材料被广泛运用于汽车、飞机等装备制造领域,有利于减轻机械动力负荷,实现机械设备的轻型化、小型化发展。
在铝合金材料的运用过程中,PCD切割工具以其硬度高、热膨胀系数低、与铝合金亲合小的特点被广泛运用于铝合金的切削加工领域。
本文对PCD刀具加工应用方法进行了研究,探索了PCD刀具钝化处理的技术,以及钝化处理后对于切削铝合金材料的影响。
关键词 PCD刀具钝化处理铝合金材料目前,PCD(金刚石)刀具已经大规模的运用铝合金等有色金属的切削加工中。
为提高PCD刀具的使用寿命和加工质量,笔者在工作实践的基础上,结合现有的研究成果,进行了PCD刀具钝化和铝合金材料切削实验,对PCD刀具钝化技术和要求,有针对性地进行了优化。
1 PCD刀具的钝化技术的原理PCD刀具的钝化技术是对PCD刀具进行深加工,提高刀具运用水平的重要方法。
笔者在实践中发现,PCD刀具在切削加工铝合金的过程中,使用初期会表现出加工质量不高、磨损较快等问题。
随着使用时间的延长,其加工的质量越来越高。
其实现的原理主要是:PCD刀具在刃磨后会出现一些毛刺和微缺口,但是在车削铝合金材料长时间磨损中,刀具刃口出现钝化,毛刺和微缺口被去除,切削刃变得光滑,提高刀具的使用寿命和加工质量。
2 PCD刀具的钝化和铝合金材料车削实验本文进行的实验主要由两个部分组成:一是PCD刀具的钝化实验;一是钝化PCD刀具对铝合金材料的切削实验。
2.1关于的PCD刀具的钝化实验在实验中,笔者采用了小型可转位刀片刃口钝化机,通过刀具与钝化机磨刷之间的磨损运动,对PCD刀具进行刃口钝化观察。
为了观察不同的磨刷与PCD刀具钝化的关系,笔者在试验中分别选用含400目、800目、1000目、1200目金刚石磨料的磨料刷,转速800r/min,切削刃和磨料刷接触长度为2mm进行实验。