缺陷的种类及产生的原因
钢构件中常见缺陷的种类及产生的原因

钢构件中常见缺陷的种类及产生的原因一、钢焊缝中常见缺陷及产生的原因1、外观缺陷(1)咬边:由于焊接参数选择不当,或操作方法不正确,沿焊趾的母材部位产生的沟槽或凹陷。
(2)焊瘤:焊接过程中,熔化金属流淌到焊缝之外未熔化的母材上所形成的金属瘤。
(3)、凹坑:焊后在焊缝表面或焊缝背面形成的低于母材表面的局部低洼部分。
(4)、未焊满:由于填充金属不足,在焊缝表面形成的连续或断续的沟槽。
(5)、烧穿:焊接过程中,熔化金属自坡口背面流出,形成穿孔的缺陷。
(6)、其他表面缺陷①表面成形不良②错边③塌陷④弧坑⑤焊接变形2、气孔:焊接时,熔池中的气泡在凝固时未能逸出而残留下来所形成的空穴。
气孔可分为密集气孔、条虫状气孔和针状气孔等。
3、夹渣:焊后残留在焊缝中的焊渣。
4、焊接裂纹:在焊接应力及其他致脆因素共同作用下,焊接接头中局部地区的金属原子结合力遭到破坏而形成的新界面所产生的缝隙。
它具有尖锐的缺口和大的长宽比的特征。
5、未焊透:焊接时接头根部未完全熔透的现象,对对接焊缝也指焊缝深度未达到设计要求的现象。
6.未熔合:熔焊时,焊道与母材之间或焊道与焊道之间,未完全熔化结合的部分,电阻点焊指母材与母材之间未完全熔化结合的部分。
二、铸件中常见缺陷及产生的原因序缺陷名称缺陷特征1 气孔在铸件内部、表面或近于表面处,有大小不等的光滑孔眼,形状有圆的、长的及不规则的,有单个的,也有聚集成片的。
颜色有白色的或带一层暗色,有时覆有一层氧化皮。
2 缩孔在铸件厚断面内部、两交界面的内部及厚断面和薄断面交接处的内部或表面,形状不规则,孔内粗糙不平,晶粒粗大。
3 疏松在铸件内部微小而不连贯的缩孔,聚集在一处或多处,晶粒粗大,各晶粒间存在很小的孔眼,水压试验时渗水。
4 密集气孔在铸件内部或表面形状不规则的孔眼。
孔眼不光滑,里面全部或部分充塞着熔渣。
5 热裂在铸件上有穿透或不穿透的裂纹(注要是弯曲形的),开裂处金属表皮氧化。
6 冷裂在铸件上有穿透或不穿透的裂纹(主要是直的),开裂处金属表皮氧化。
第七章缺陷的种类及产生的原因
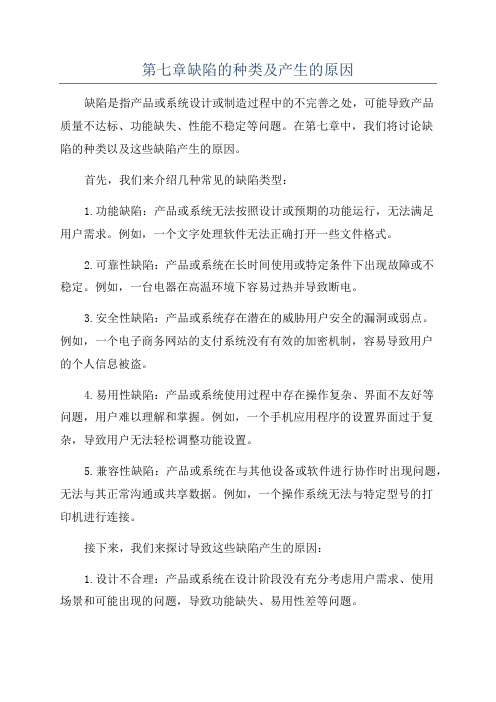
第七章缺陷的种类及产生的原因缺陷是指产品或系统设计或制造过程中的不完善之处,可能导致产品质量不达标、功能缺失、性能不稳定等问题。
在第七章中,我们将讨论缺陷的种类以及这些缺陷产生的原因。
首先,我们来介绍几种常见的缺陷类型:1.功能缺陷:产品或系统无法按照设计或预期的功能运行,无法满足用户需求。
例如,一个文字处理软件无法正确打开一些文件格式。
2.可靠性缺陷:产品或系统在长时间使用或特定条件下出现故障或不稳定。
例如,一台电器在高温环境下容易过热并导致断电。
3.安全性缺陷:产品或系统存在潜在的威胁用户安全的漏洞或弱点。
例如,一个电子商务网站的支付系统没有有效的加密机制,容易导致用户的个人信息被盗。
4.易用性缺陷:产品或系统使用过程中存在操作复杂、界面不友好等问题,用户难以理解和掌握。
例如,一个手机应用程序的设置界面过于复杂,导致用户无法轻松调整功能设置。
5.兼容性缺陷:产品或系统在与其他设备或软件进行协作时出现问题,无法与其正常沟通或共享数据。
例如,一个操作系统无法与特定型号的打印机进行连接。
接下来,我们来探讨导致这些缺陷产生的原因:1.设计不合理:产品或系统在设计阶段没有充分考虑用户需求、使用场景和可能出现的问题,导致功能缺失、易用性差等问题。
2.编程错误:在软件开发过程中,程序员可能会犯错或存在逻辑错误,导致功能异常、安全漏洞等问题。
3.制造过程缺陷:在产品制造过程中,可能存在材料不合格、工艺不标准等问题,导致产品质量缺陷。
4.管理不善:项目管理不善,导致定义不清晰的需求、进度控制不足等问题,从而导致缺陷的产生。
5.版本控制不当:软件开发过程中,管理人员未能正确管理和控制不同版本的代码,导致错误的代码被部署到生产环境中。
总结起来,缺陷的种类和产生原因是多种多样的,包括设计不合理、编程错误、制造过程缺陷等。
为了减少和避免这些缺陷,企业应加强项目管理、进行有效的质量控制,并投入足够的时间和资源进行测试和验证工作,以确保产品或系统达到用户的要求和期望。
技能培训资料:常见的焊接缺陷

1、焊接夹渣焊接夹渣缺陷是指焊后熔渣残留在焊缝中的情况。
夹渣主要有金属夹渣即夹铝或夹铜和非金属夹渣即焊条药皮、焊剂、硫化物、氧化物或氮化物留存在焊缝中。
夹渣产生的主要原因是破口清理不彻底、坡口尺寸不符合设计要求、焊条质量不合格等。
2、焊接凹坑焊接凹坑是指在收弧和断弧时操作不当而在焊道末端形成的凹陷部分。
主要产生的原因是焊接材料在焊接过程中停留时间不够,填充金属不够导致的。
其危害是导致焊缝的横截面减少,凹坑处容易产生偏析或杂质汇集,从而易形成气孔、灰渣或裂纹。
3、焊接裂纹焊接裂纹主要是指焊缝中金属原子结合遭到破坏,从而形成新的界面而形成的裂缝。
焊接裂纹按温度可分为热裂纹、再热裂纹、冷裂纹、层状撕裂。
裂纹再焊接工艺里是最严重的一种缺陷,也是导致焊接结构失效而引发事故的主要原因。
4、焊接气孔焊接气孔主要是在熔池中的气泡在金属凝固时未能及时逸出而形成的空穴。
其主要产生原因是电弧保护不到位,弧太长或者焊接材料有锈,气体保护介质不纯以及坡口处理不到位。
5、焊接咬边焊接咬边是指沿着焊趾,在焊件部分形成凹陷或者沟槽。
主要形成原因是焊接参数选择不正确、焊速太慢、电弧拉得太长、电流过大、焊枪位置不准确导致。
其危害导致焊件工作截面减小,咬边处应力集中。
6、焊接焊瘤焊瘤是指金属溢流到加热不足的焊件或焊缝上,未能与焊件和金属熔合在一起而堆积的金属缺陷。
主要形成原因是焊接参数选择不符合设计要求、焊接坡口清理不到位、焊接速度太慢等。
7、焊接局部烧穿焊接局部烧穿是指焊接过程中,焊接部位熔透至坡口背面,形成穿孔现象。
主要产生原因是焊接电流太大、焊件加热过高、坡口对接空隙太大、焊接速度太慢、电弧停留时间太长等8、焊接未焊透焊接未焊透是指焊缝的熔透深度小于板厚时形成的。
在单面时,焊缝熔透到达不了焊件底部;双面焊时两道焊缝熔深总厚度小于焊件厚度而形成的。
主要形成原因有焊条位置不准确,偏离中心位置;坡口角度太小,焊接空隙小钝边太大;电流太小等。
缺陷的种类及产生的原因
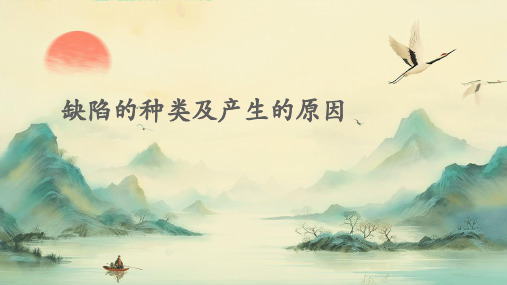
性能缺陷
总结词
性能缺陷是指程序运行缓慢或资源消耗过大,如响应时间过长、内存泄漏等。
详细描述
性能缺陷可能是由于算法效率低下、资源管理不当或系统资源不足导致的。性能缺陷会影响程序的可用性和效率, 降低用户体验和工作效率。
安全缺陷
总结词
安全缺陷是指程序存在安全漏洞,可能导致未陷相关标准的制定和完善,规范缺 陷的检测、处理和预防等方面的操作流程 ,提高行业整体水平。
THANKS
感谢观看
展望
未来研究方向
技术创新
针对现有缺陷研究的不足,未来的研究应 更加注重缺陷的早期发现、快速处理和预 防措施的有效性评估等方面。
鼓励技术创新,开发更加高效、准确的缺 陷检测和处理方法,提高产品质量和可靠 性。
跨学科合作
标准化建设
加强跨学科合作,借鉴其他领域的先进理 论和技术,促进缺陷研究领域的整体发展 。
缺陷的种类及产生的原因
• 引言 • 缺陷的种类 • 缺陷产生的原因 • 预防和解决缺陷的方法 • 结论
01
引言
目的和背景
缺陷管理在现代软件开发中的重要性
随着软件开发的复杂性和规模的增加,缺陷管理成为确保软件质量和可靠性的关 键因素。
缺陷对软件质量的影响
缺陷可能导致软件运行不稳定、功能失效或数据丢失,严重影响用户体验和企业 的声誉。
在项目完成后进行验收测试,确保项目满足 用户需求。
持续维护和更新
维护
在程序运行过程中,定期进行维护,修复发 现的缺陷。
更新
及时更新软件版本,修复已知的缺陷和漏洞。
文档
编写详细的文档,记录程序运行情况和修复 的缺陷,方便后期维护。
05
结论
总结
产品缺陷的概念和种类

产品缺陷的概念和种类概念产品缺陷指的是产品在设计、制造或售后服务过程中出现的错误或缺陷。
它可能导致产品无法正常使用、功能不完善或存在安全隐患等问题。
产品缺陷在市场经济中非常常见,消费者购买产品后发现问题时,他们常常会寻求售后维权或者要求退货。
产品缺陷的种类1. 设计缺陷:设计缺陷指的是产品在设计阶段就存在的问题,导致产品无法满足消费者需求或者容易出现故障。
设计缺陷可能源自于设计师对产品功能的理解错误、抄袭他人设计或者不同厂家间技术差异等。
比如,某个家电公司生产的电饭锅在设计时忽略了实际需求,导致加热不均匀或者小心烧焦食物。
2. 制造缺陷:制造缺陷指的是产品在制造过程中出现的错误,导致产品无法正常工作或者存在安全隐患。
制造缺陷可能来自于工艺不当、原材料选择有误、生产设备老化或者操作失误等。
比如,某个汽车制造商在生产过程中没有严格控制质量,导致汽车零部件容易断裂或者接缝易开裂。
3. 包装缺陷:包装缺陷指的是产品在包装过程中出现的问题,导致产品容易损坏或者影响产品使用。
包装缺陷可能产生于包装材料的质量问题、包装设计的不合理或者包装过程中的操作失误等。
比如,某个食品生产企业在包装产品时使用了低质量的塑料袋,导致产品在运输过程中易破裂,影响食品的安全性。
4. 表示缺陷:表示缺陷指的是产品在市场营销过程中表述失误或者虚假宣传等问题,导致消费者对产品性能、功能或者质量有误解。
表示缺陷可能来自于企业在广告宣传中的夸大其词、销售人员对产品性能的不正确说明或者标签贴错等。
比如,某个化妆品公司在产品广告中宣称可以即时祛皱,吸引了很多消费者购买,但实际效果却非常有限。
5. 效能缺陷:效能缺陷指的是产品在正常使用时无法满足消费者的期望或者功能不完善的问题。
效能缺陷可能源自于产品设计时对市场需求的误判、制造工艺的不完善或者未发现的技术难题等。
比如,某个电子公司生产的智能手机屏幕显示效果不清晰,导致用户体验差。
6. 安全缺陷:安全缺陷指的是产品在使用过程中存在安全隐患或者对用户造成伤害的问题。
缺陷种类及产生原因

淄博特检院
徐长业
第七章
缺陷种类及产生原因
无损检测最主要的用途是探测缺陷。了解材料 和焊逢中的缺陷种类和产生原因,有助于正确的 选择无损检测方法,正确判断和分析检测结果。
第七章
缺陷种类及产生原因
一、钢焊缝中常见缺陷及产生原因 1,外观缺陷 外观缺陷(表面缺陷):不借助仪器,从工件表面肉眼可以 发现的缺陷 (1)咬边:沿着焊趾,在母材部分形成的凹馅或沟槽。 产生原因:是因为电弧热量太高,电流太大,运条速度太 小,焊条与工件角度不正确,摆动不合理,电弧过长,焊 接次序不合理;直流焊时磁偏吹;焊接位置会加剧咬边。 产生的电弧将焊逢边缘的母材熔化没有得到熔敷金属的充 分补充所留下的缺口。 危害:咬边减小了母材的有效截面积,降低构件的承载能 力,同时造成应力集中,发展裂纹源。
第七章 缺陷的种类及产生原因
谢谢
第七章 缺陷的种类及产生原因
危害:焊瘤常伴未熔合、夹渣缺陷。焊瘤改变了焊缝 的实际尺寸,应力集中。 管子内部焊瘤减小了内径,可能造成堵塞。
Hale Waihona Puke 第七章 缺陷种类及产生原因
(3)凹坑:焊缝表面或背面局部的低于母材的部分。 产生原因是由于收弧时焊条未作短时间停留造成的。横, 立,仰焊位置常常在焊缝背面根部产生内凹。 危害 减小了焊缝的有效截面积,应力集中,弧坑常带有 裂纹 (4)未焊瞒:焊缝表面上连续的或断续的沟槽。 填充金属不足是产生未焊瞒的根本原因。规范太弱,焊条过 细,运条不当等均会容易产生未填瞒。 危害 减小了焊缝的有效截面积,消弱了焊缝,应力集中 规范弱,增大冷却速度,易产生气孔。裂纹缺陷
缺陷及其特征
焊接缺陷及其特征
产生原因: (1)坡口尺寸不合理。 (2)坡口有污物。 (3)焊接线能量过小。 (4)多层焊时,层间清渣不彻底。 (5)焊缝散热太快,液态金属凝固过快。 (6)药皮,焊剂化学成分不合理,熔点过高,冶金 反应不完全,脱渣性不好等。 (7)钨极焊时电流过大,钨极融化脱落焊缝内。 (8)手工焊时焊条摆动不真确,熔渣不利于上浮。 夹渣危害:点状夹渣与气孔相同,带有尖端夹渣易形 成应力集中,可能形成裂纹,危害比较大。 防止措施
缺陷种类及产生原因
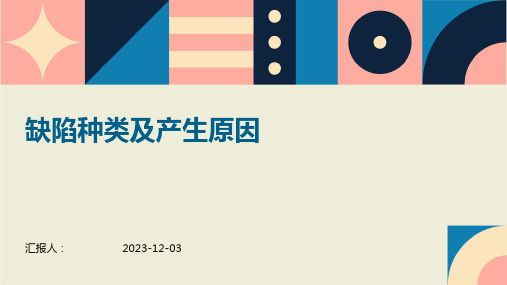
环境因素
如温度、湿度、清洁度等环境条件对产品质量产生影响。
要点二
管理因素
如质量管理体系不完善、质量控制不严格等管理问题导致 产品质量问题。
04
针对不同缺陷种类的预防措施
外观缺陷预防措施
严格控制原材料质量
对进厂的原材料进行严格的检验,确保其质 量符合标准。
优化生产工艺
改进生产工艺,降低产品外观缺陷的发生率 。
随着人工智能和机器学习技术的发展,未来将有更多智能 化检测工具用于发现和修复缺陷,提高软件质量和开发效 率。
自动化测试
自动化测试将在未来得到更广泛的应用,通过自动化工具 和框架实现测试用例的自动生成、执行和分析,提高测试 效率和质量。
全流程质量管理
未来软件开发将更加注重全流程质量管理,从需求分析、 设计、编码、测试到发布等各个环节进行严格的质量控制 。
改进开发流程
通过对缺陷产生原因的分析,可以发现开发流程中存在的问题和不足,从而针对性地改进开发流程,提 高开发效率和软件质量。
报告目的和结构
报告目的
本报告旨在对软件缺陷的种类及产生原因进行深入分析,为制定有效的预防和纠正措施提供依据,以提高软件的 质量和可靠性。
报告结构
本报告将首先介绍缺陷的定义和分类,然后分析缺陷产生原因的重要性,接着详细阐述各类缺陷的产生原因,最 后提出预防和纠正措施的建议。
05
案例分析:典型产品缺陷及产生原因
案例一:手机外观划痕问题
01 02 03 04
缺陷描述:手机外壳或屏幕上出现明显的划痕,影响外观和使用体验 。
产生原因
生产工艺问题:如外壳材料质量差、加工过程中操作不当等。
使用环境问题:如长时间接触钥匙、硬币等硬物,或在沙尘较多的环 境下使用。
常见焊接缺陷类型产生原因与防止措施
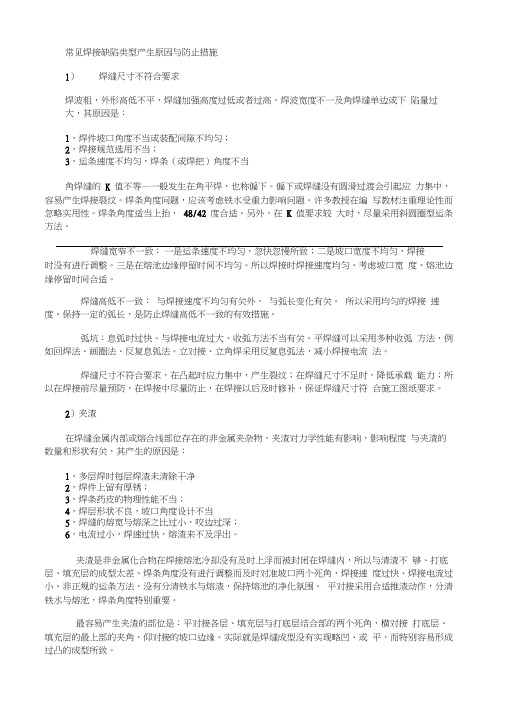
常见焊接缺陷类型产生原因与防止措施1)焊缝尺寸不符合要求焊波粗,外形高低不平,焊缝加强高度过低或者过高,焊波宽度不一及角焊缝单边或下陷量过大,其原因是:1,焊件坡口角度不当或装配间隙不均匀;2,焊接规范选用不当;3,运条速度不均匀,焊条(或焊把)角度不当角焊缝的K 值不等—一般发生在角平焊,也称偏下。
偏下或焊缝没有圆滑过渡会引起应力集中,容易产生焊接裂纹。
焊条角度问题,应该考虑铁水受重力影响问题。
许多教授在编写教材注重理论性而忽略实用性。
焊条角度适当上抬,48/42 度合适。
另外,在K 值要求较大时,尽量采用斜圆圈型运条方法。
时没有进行调整。
三是在熔池边缘停留时间不均匀。
所以焊接时焊接速度均匀、考虑坡口宽度、熔池边缘停留时间合适。
焊缝高低不一致:与焊接速度不均匀有关外,与弧长变化有关。
所以采用均匀的焊接速度、保持一定的弧长,是防止焊缝高低不一致的有效措施。
弧坑:息弧时过快。
与焊接电流过大、收弧方法不当有关。
平焊缝可以采用多种收弧方法,例如回焊法、画圈法、反复息弧法。
立对接、立角焊采用反复息弧法,减小焊接电流法。
焊缝尺寸不符合要求,在凸起时应力集中,产生裂纹;在焊缝尺寸不足时,降低承载能力;所以在焊接前尽量预防,在焊接中尽量防止,在焊接以后及时修补,保证焊缝尺寸符合施工图纸要求。
2)夹渣在焊缝金属内部或熔合线部位存在的非金属夹杂物,夹渣对力学性能有影响,影响程度与夹渣的数量和形状有关,其产生的原因是:1,多层焊时每层焊渣未清除干净2,焊件上留有厚锈;3,焊条药皮的物理性能不当;4,焊层形状不良,坡口角度设计不当5,焊缝的熔宽与熔深之比过小,咬边过深;6,电流过小,焊速过快,熔渣来不及浮出。
夹渣是非金属化合物在焊接熔池冷却没有及时上浮而被封闭在焊缝内,所以与清渣不够、打底层、填充层的成型太差、焊条角度没有进行调整而及时对准坡口两个死角,焊接速度过快、焊接电流过小、非正规的运条方法,没有分清铁水与熔渣,保持熔池的净化氛围。
- 1、下载文档前请自行甄别文档内容的完整性,平台不提供额外的编辑、内容补充、找答案等附加服务。
- 2、"仅部分预览"的文档,不可在线预览部分如存在完整性等问题,可反馈申请退款(可完整预览的文档不适用该条件!)。
- 3、如文档侵犯您的权益,请联系客服反馈,我们会尽快为您处理(人工客服工作时间:9:00-18:30)。
3)危害性:
烧穿是锅炉压力容器压力管道产品上不允许存在的缺陷,它破坏了焊缝, 使接头丧失联接及承载能力。
4)预防措施:
(1)选用较小电流和合适的焊接速度。 (2)减小装配间隙,在焊缝背面加设垫板或药垫。 (3)使用脉冲焊,能有效地防止烧穿。
薛振林 陆志春
7.1.1外观缺陷
6、其他表面缺陷
熔合区裂纹
弧坑裂纹
热影响区裂纹
薛振林 陆志春
7.1.4 裂纹
④按产生的条件和时机不同可分为: 热裂纹(产生于Ac3线附近的裂纹)结晶裂纹
冷裂纹(产生于马氏体转变温度M3点200-300 ℃以下的裂
纹)延迟裂纹
再热裂纹(接头冷却后再加热至550~650℃时产生的裂纹) 层状撕裂(金属中杂质偏析在施焊过程中在焊接应力或外拘 束应力作用下沿金属轧制方向开裂
3)焊缝金属脱氧不足也会增加氧气孔。
薛振林 陆志春
7.1.2 气孔
5、气孔的危害性: 气孔减少了焊缝的有效截面积,使焊缝疏松,从面降低了 接头的强度,降低塑性,还会引起泄漏。气孔也是引起应力 集中的因素。氢气孔还可能促成冷裂纹。 6、防止气孔的措施: ① 清除焊丝,工作坡口及其附近表面的油污、铁锈、水分和 杂物。 ② 采用碱性焊条、焊剂时,要彻底烘干。 ③ 采用直流反接并用短电弧施焊。 ④ 焊前预热,减缓冷却速度。 ⑤ 用偏强的规范施焊。
4)预防措施:
(1)选用合理的规范, (2)采用正确的运条方式都有利于消除咬边。 (3)焊角焊缝时,用交流焊代替直流焊也能有效地防止咬边。
薛振林 陆志春
7.1.1外观缺陷
2、焊瘤
1)定义:焊缝中的液态金属流到加热不足未熔化的母材上或从焊缝根部溢出, 冷却后形成未与母材熔合的金属瘤即为焊瘤。
(1)电弧热量太高,即电流太大(2)运条速度太小而造成的(3)焊条 与工件间角度不正确,摆动不合理(4)电弧过长,焊接次序不合理等 (5)直流焊时电弧的磁偏吹也是产生咬边的一个原因(6)某些焊接位 置(立、横、仰)会加剧咬边。
3)危害性:
(1)咬边减小了母材的有效截面积,降低结构的承载能力 (2)同时还会造成应力集中,发展为裂纹源。
5、危害性:
点状与气孔相似,带有尖角的夹渣会产生应力集中,其尖端还会发展 为裂纹源,其危害远比气孔严重。
薛振林 陆志春
7.1.4 裂纹
1、定义:在焊接应力及其它致脆因素共同作用下,焊接接头中局部部位的金属 原子结合力遭到破坏而形成新的界面所产生的缝隙称之裂纹。 2、裂纹的分类 ①按尺寸大小可分为宏观裂纹、微观裂纹和超显微裂纹(指晶间或晶内裂纹)。
4、危害性:
(1)裂纹是焊接缺陷中危害性最大的一种。裂纹是一种面积型缺陷,它的出现 将显著减少承载面积。
(2)更严重的是裂纹端部形成尖锐缺口,应力高度集中,很容易扩展导致破坏。 (3)冷裂纹因为其延迟特性和快速脆断特性,带来的危害往往是灾难性的。世 界上的锅炉压力容器压力管道事故绝大部分是由于裂纹引起的脆性破坏。
薛振林 陆志春
7.1.1外观缺陷
5、烧穿 1)定义:烧穿是指焊接过程中,熔深超过工件厚度,熔化金属自焊 缝背面流出,形成穿孔性缺陷 。
烧穿示意图
焊缝烧穿实例
薛振林 陆志春
接管烧穿X影像
7.1.1外观缺陷
2)产生原因:
(1)焊接电流过大,速度太慢,电弧在焊缝处停留过久,都会产生烧穿 缺陷。 (2)工件间隙太大,钝边太小也容易出现烧穿现象。
的根部未焊透也位于焊缝表面。
薛振林 陆志春
7.1.1外观缺陷
1、咬边
1)定义:沿焊趾的母材被电弧熔化时所形成的沟槽或凹陷。它是由于电弧将焊缝 边缘的母材熔化后没有得到熔敷金属的充分补充所留下的缺口。
常见咬边形式示意图
接管咬边实例
薛振林 陆志春
焊缝咬边X片影像
7.1.1外观缺陷
2)产生原因:
承压类特种设备无损检测相关知识
第7章 缺陷的种类及产生的原因
目录
7.1 7.2 7.3 7.4 7.5 钢焊缝中常见缺陷及产生原因 铸件中常见缺陷及产生原因 锻件中常见缺陷及产生原因 轧件中常见缺陷及产生原因 使用中常见缺陷及产生原因
7.1 钢焊缝中常见缺陷及产生原因
缺欠与缺陷
按GB6417.1-2005,焊接接头中因焊接产生的金属不连续、 不致密或连接不良现象称为缺欠,而超过规定的缺欠称为 缺陷。 7.1.1外观缺陷(形状缺陷) 外观缺陷(表面缺陷)是指不用借助于仪器,从工件表面 肉眼可以发现的缺陷。常见的外观缺陷有咬边、焊瘤、凹 陷及焊接变形等,有时还有表面气孔和表面裂纹。单面焊
球状气孔
群状均匀分布气孔 条虫状气孔
密集气孔
链状气孔
薛振林 陆志春
典型气孔金相照片
薛振林 陆志春
气孔的X影像
链状气孔
球状气孔
条虫状气孔
均匀群状气孔
密集状气孔
群状气孔
薛振林 陆志春
7.1.2 气孔
3、形成机理: 熔池金属在凝固过程中,有大量的气体要从金属中逸出来, 当金属凝固速度大于气体逸出速度,就会形成气孔。 4、产生气孔的主要原因: 1)母材或填充金属表面有锈,油污等,焊条及焊剂未烘干 会增加气孔量,因为锈、油污及焊条药皮、焊剂中的水分在 高温下分解为气体,增加了高温金属中气体的含量。 2)焊接线能量过小,熔池冷却速度大,不利于气体逸出。
4)预防措施:
(1)使焊缝处于平焊位置,正确选用规范。 (2)选用无偏芯焊条,合理操作。
薛振林 陆志春
7.1.1外观缺陷
3、凹坑
1)定义:凹坑指焊缝表面或背面局部的低于母材的部分 。
凹坑示意图
焊缝凹坑实例
凹坑X片影像
薛振林 陆志春
7.1.1外观缺陷
2)产生原因: 凹坑多是由于收弧时焊条(焊丝)未作短时间停留造成的 (此时的凹坑称为弧坑),仰、立、横焊时,常在焊缝背面 根部产生内凹。 3)危害性: 凹坑减小了焊缝的有效截面积,弧坑常带有弧坑裂纹和弧坑 缩孔。 4)预防措施: (1)施焊时尽量选用平焊位置,选用合适的焊接规范, (2)收弧时让焊条在熔池内短时间停留或环形摆动,填满 弧坑。
链状夹渣
薛振林 陆志春
典型夹渣金相照片
薛振林 陆志春
夹渣的X影像
链状夹渣
条状夹渣
密集点状夹渣
薛振林 陆志春
7.1.3夹渣
3、形成机理:
熔池中熔化金属的凝固速度大于熔渣的流动速度,当熔化金属凝固时,
熔渣未能及时浮出熔池而形成。
4、产生原因:
① 坡口尺寸不合理;② 坡口有污物;③ 多层焊时,层间清渣不彻底;④ 焊 接线能量小;⑤ 焊缝散热太快,液态金属凝固过快;⑥ 焊条药皮,焊剂化 学成分不合理,熔点过高,冶金反应不完全,脱渣性不好;⑦ 钨极性气体保 护焊时,电源极性不当,电流密度大,钨极熔化脱落于熔池中⑧ 手工焊时, 焊条摆动不正确,不利于熔渣上浮。 可根据以上原因分别采取对应措施以防止夹渣的产生。
薛振林 陆志春
纵向裂纹
热裂纹
晶枝状裂纹
弧坑裂纹
典型热裂纹X影像
7.1.4 裂纹
②冷裂纹
A.特征:产生于较低温度,且大多数在焊后一段时间之后出现在焊热影响区 或焊缝上,并沿晶或穿晶、或是两者共存的开裂,又称延迟裂纹。
B.产生机理:这是因热影响区或焊缝局部存在淬硬组织(马氏体)减小了金
属的塑性储备,或是接头内有一定的含氢量,且接头有较大焊接残余应力使 接头处于较大的拉应力状态之下,淬硬组织会开裂,氢会发生氢致效应而产 生裂纹。
焊缝超高
表面粗糙
错边
塌陷
表面气孔
弧坑缩孔
薛振林 陆志春
7.1.2 气孔
1、定义:焊接时,熔池中的气泡在凝固时未能逸出而残留 下来所形成的空穴。 2、气孔的分类:从形态分有球状、针孔、柱孔、条虫状; 从分布状态有均匀分布状、密集群状和链状之分;按孔内成 分有氮气孔、氢气孔、二氧化碳和一氧纹
超显微裂纹
薛振林 陆志春
7.1.4 裂纹
②根据裂纹延伸方向,可分为: 纵向裂纹(与焊缝平行);横向 裂纹(与焊缝垂直);辐射状裂 纹等。
纵向裂纹
辐射状裂纹
横向裂纹
薛振林 陆志春
7.1.4 裂纹
③根据裂纹发生部位,可分为: 焊缝裂纹;热影响区裂纹;熔合 区裂纹;焊趾裂纹;焊道下裂纹; 弧坑裂纹等。
C.防止措施:采用低氢碱性焊条,及时后热消氢处理,以减小含氢量;选择 合理的焊接规范,提高预热温度,减慢冷却速度,防止出现淬硬组织;选择 科学的焊接工艺,采用合理的装配,焊接顺序,以减小焊接变形和焊接应力。
薛振林 陆志春
冷裂纹X影像
薛振林 陆志春
7.1.4 裂纹
③再热裂纹
A.特征:再热裂纹是在焊后的热处理等再次加热(其加热温度:碳钢 与合金钢是550~650℃,奥氏体不锈钢约是300℃)的过程中,主 要发生在热影响区的过热粗晶区,在焊接残余应力作用下沿晶界开裂, 沉淀强化的钢种最易产生再热裂纹。 B.产生机理:楔形开裂理论,近缝区金属在高温热循环作用下,强化 相碳化物(如碳化铬等)沉积于晶内的位错区上,使晶内强化强度大 大高于晶界强化强度,尤其是强化相弥散分布在晶粒内时,会阻碍晶 粒内部调整,又会阻碍晶粒内部的整体变形。这样,由于应力松弛而 带来的塑性变形就主要由晶界金属来承担,于是晶界区金属会产生滑 移,且在三晶粒交界处产生应力集中而导致沿晶开裂。 C.防止措施:热处理工艺应尽量避开再热裂纹的敏感温度或缩短在此 温度区停留时间,改善合金元素的强化作用和对再热裂纹的影响;采 用适当的焊前预热和焊后的后热处理,控制冷却速度,以降低焊接残 余应力;避免应力集中。