缺陷种类图
常见的焊接缺陷与缺陷图片

常见的焊接缺陷(1)常见的焊接缺陷(1)未焊透:母体金属接头处中间(X坡口)或根部(V、U坡口)的钝边未完全熔合在一起而留下的局部未熔合。
未焊透降低了焊接接头的机械强度,在未焊透的缺口和端部会形成应力集中点,在焊接件承受载荷时容易导致开裂。
(2)未熔合:固体金属与填充金属之间(焊道与母材之间),或者填充金属之间(多道焊时的焊道之间或焊层之间)局部未完全熔化结合,或者在点焊(电阻焊)时母材与母材之间未完全熔合在一起,有时也常伴有夹渣存在。
(3)气孔:在熔化焊接过程中,焊缝金属的气体或外界侵入的气体在熔池金属冷却凝固前未来得及逸出而残留在焊缝金属部或表面形成的空穴或孔隙,视其形态可分为单个气孔、链状气孔、密集气孔(包括蜂窝状气孔)等,特别是在电弧焊中,由于冶金过程进行时间很短,熔池金属很快凝固,冶金过程中产生的气体、液态金属吸收的气体,或者焊条的焊剂受潮而在高温下分解产生气体,甚至是焊接环境中的湿度太大也会在高温下分解出气体等等,这些气体来不及析出时就会形成气孔缺陷。
尽管气孔较之其它的缺陷其应力集中趋势没有那么大,但是它破坏了焊缝金属的致密性,减少了焊缝金属的有效截面积,从而导致焊缝的强度降低。
某钢板对接焊缝X射线照相底片V型坡口,手工电弧焊,未焊透某钢板对接焊缝X射线照相底片V型坡口,手工电弧焊,密集气孔(4)夹渣与夹杂物:熔化焊接时的冶金反应产物,例如非金属杂质(氧化物、硫化物等)以及熔渣,由于焊接时未能逸出,或者多道焊接时清渣不干净,以至残留在焊缝金属,称为夹渣或夹杂物。
视其形态可分为点状和条状,其外形通常是不规则的,其位置可能在焊缝与母材交界处,也可能存在于焊缝。
另外,在采用钨极氩弧焊打底+手工电弧焊或者钨极氩弧焊时,钨极崩落的碎屑留在焊缝则成为高密度夹杂物(俗称夹钨)。
W18Cr4V(高速工具钢)-45钢棒对接电阻焊缝中的夹渣断口照片钢板对接焊缝X射线照相底片V型坡口,手工电弧焊,局部夹渣钢板对接焊缝X射线照相底片V型坡口,手工电弧焊,两侧线状夹渣钢板对接焊缝X射线照相底片V型坡口,钨极氩弧焊打底+手工电弧焊,夹钨(5)裂纹:焊缝裂纹是焊接过程中或焊接完成后在焊接区域中出现的金属局部破裂的表现。
塑胶件的24种常见不良缺陷图片PPT课件

缩水(凹痕)
缩水(凹痕)
•1
二、气纹:
气纹
•2
三、缺料(走胶不足):
走胶不足
缺料
•3
四、水口不平:
水口不平
•4
五、披锋(毛边):
披锋
夹线(结合线)
•6
七、黑点:
黑点NG!
•7
八、变形:
平面中间拱起变形
柱子弯曲变形
•8
九、混色(异色):
混色
混色(杂色料)
上盖色偏哑
下盖色偏亮
•19
二十、披锋丝(拉丝):
披锋丝(拉丝)NG
•20
二十一、应力痕:
应力痕:因注射时内应力过大而在产品表面形成的光影;
•21
二十二、进胶位发蓝:
进胶点发蓝
•22
二十三、多胶:
多胶 NG
•23
•9
十、划伤(刮伤):
划伤
刮花
•10
十一、烧焦:
烧焦
•11
十二、拖花(拉伤):
拖花(拉伤)
•12
十三、顶高(顶白):
顶高(顶针印)
•13
十四、料花:
料花
•14
十五、油污:
油污NG!
•15
十六、碰伤:
碰伤
•16
十七、削伤:
削缺(削伤)
•17
十八、气泡:
气泡(透明件中央白泡状)
•18
十九、色差(上下盖阴阳色):
铸件外观缺陷图

铸件常见缺陷常见缺陷缺陷的分类:铸件常见缺陷分为孔眼、裂纹、表面缺陷、残缺类缺陷、形状及尺寸和重量不合格、成份及组织和性能不合格六大类。
1孔眼类缺陷孔眼类缺陷包括气孔、缩孔、缩松、渣眼、砂眼、等。
1.1.1气孔:别名气眼,气泡、由气体原因造成的孔洞。
铸件气孔的特征是:其表面一般比较光滑,主要呈梨形\圆形和椭圆形.一般在铸件表面露出,大孔常孤立存在,小孔则成群出现。
(如图)产生的原因是:来源于气体,炉料潮湿或绣蚀、表面不干净、炉气中水蒸气等气体、炉体及浇包等修后未烘干、型腔内的气体、浇注系统不当,浇铸时卷入气体、铸型等。
1.1.2缩孔缩孔别名缩眼,由收缩造成的孔洞。
缩孔的特征是:形状不规则,孔壁粗糙并带有技状晶,常出现在铸件最后凝固的部位,广义的缩孔包括缩松。
(如图)产生的原因是:金属在液体及凝固期间由于补缩不良而产生的孔洞,主要有以下几点:铸件结构设计不合理,浇铸系统不适当,冷铁的大小、数量、位置不符实际、铁水化学成份不符合要求,如含磷过高等。
浇注温度过高浇注速度过快等。
1.1.3缩松缩松别名疏松、针孔蜂窝、由收缩耐造成的小而多的孔洞。
缩松的特征是:铸件断面上出现的分散而细小的缩孔.助高倍放大镜才能发现的缩松称为显微缩松,铸件有缩松的部位,在气密性实验时易渗漏。
(如图)产生的原因同以上缩孔。
1.1.4渣眼渣眼别名夹渣、包渣、脏眼、铁水温度不高、浇注挡渣不当造成。
渣眼的特征是:铸件浇注位置上表面的非金属夹杂物。
通常在加工后发现与气孔并存,孔径大小不一,成群集结。
(如图)产生的原因是:铁水纯净度差、除渣不净、浇注时挡渣不好,浇注系统挡渣作用差、浇注时浇口未充满或断流。
1.1.5砂眼砂眼是夹着砂子的砂眼。
砂眼的特征是:铸件内部或表面带有砂粒的孔洞(如图)。
产生的原因是:型砂损坏脱落,型腔内的散砂或砂块未清除干净、型砂紧实度差、浇注时冲坏型芯、浇注系统设计不当、型芯表面涂料不好等。
1.1.6铁豆铁豆是夹着铁珠的孔眼、别名铁珠、豆眼、铁豆砂眼等。
常见的焊接缺陷缺陷图片
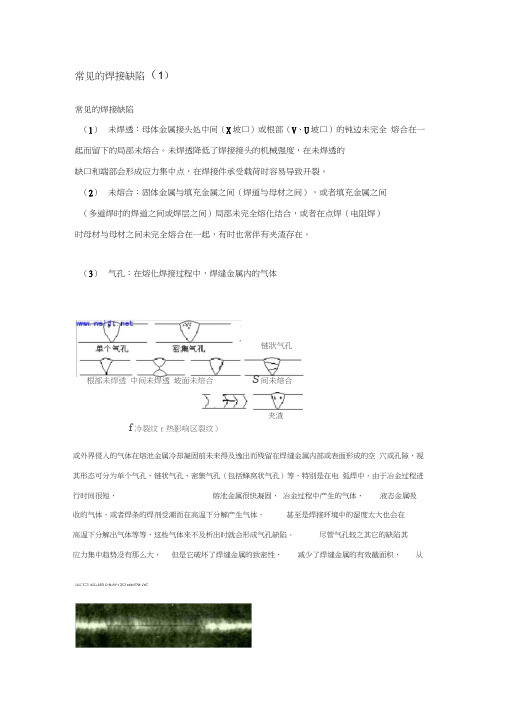
常见的焊接缺陷(1)常见的焊接缺陷(1)未焊透:母体金属接头处中间(X坡口)或根部(V、U坡口)的钝边未完全熔合在一起而留下的局部未熔合。
未焊透降低了焊接接头的机械强度,在未焊透的缺口和端部会形成应力集中点,在焊接件承受载荷时容易导致开裂。
(2)未熔合:固体金属与填充金属之间(焊道与母材之间),或者填充金属之间(多道焊时的焊道之间或焊层之间)局部未完全熔化结合,或者在点焊(电阻焊)时母材与母材之间未完全熔合在一起,有时也常伴有夹渣存在。
(3)气孔:在熔化焊接过程中,焊缝金属内的气体f冷裂纹r热影响区裂纹)或外界侵入的气体在熔池金属冷却凝固前未来得及逸岀而残留在焊缝金属内部或表面形成的空穴或孔隙,视其形态可分为单个气孔、链状气孔、密集气孔(包括蜂窝状气孔)等,特别是在电弧焊中,由于冶金过程进行时间很短,熔池金属很快凝固,冶金过程中产生的气体、液态金属吸收的气体,或者焊条的焊剂受潮而在高温下分解产生气体,甚至是焊接环境中的湿度太大也会在高温下分解出气体等等,这些气体来不及析出时就会形成气孔缺陷。
尽管气孔较之其它的缺陷其应力集中趋势没有那么大,但是它破坏了焊缝金属的致密性,减少了焊缝金属的有效截面积,从根部未焊透中间未焊透坡面未焙合链狀气孔S间未焙合夹渣而导致焊缝的强度降低。
某钢板对接焊缝X射线照相底片V型坡口,手工电弧焊,未焊透某钢板对接焊缝X射线照相底片V型坡口,手工电弧焊,密集气孔(4 )夹渣与夹杂物:熔化焊接时的冶金反应产物,例如非金属杂质(氧化物、硫化物等)以及熔渣,由于焊接时未能逸出,或者多道焊接时清渣不干净,以至残留在焊缝金属内,称为夹渣或夹杂物。
视其形态可分为点状和条状,其外形通常是不规则的,其位置可能在焊缝与母材交界处,也可能存在于焊缝内。
另外,在采用钨极氩弧焊打底+手工电弧焊或者钨极氩弧焊时,钨极崩落的碎屑留在焊缝内则成为高密度夹杂物(俗称夹钨)。
W18Cr4V(高速工具钢)-45钢棒对接电阻焊缝中的夹渣断口照片钢板对接焊缝X射线照相底片V型坡口,手工电弧焊,局部夹渣钢板对接焊缝X射线照相底片V型坡口,手工电弧焊,两侧线状夹渣钢板对接焊缝X射线照相底片V型坡口,钨极氩弧焊打底+手工电弧焊,夹钨(5)裂纹:焊缝裂纹是焊接过程中或焊接完成后在焊接区域中出现的金属局部破裂的表现。
产品质量缺陷排列图
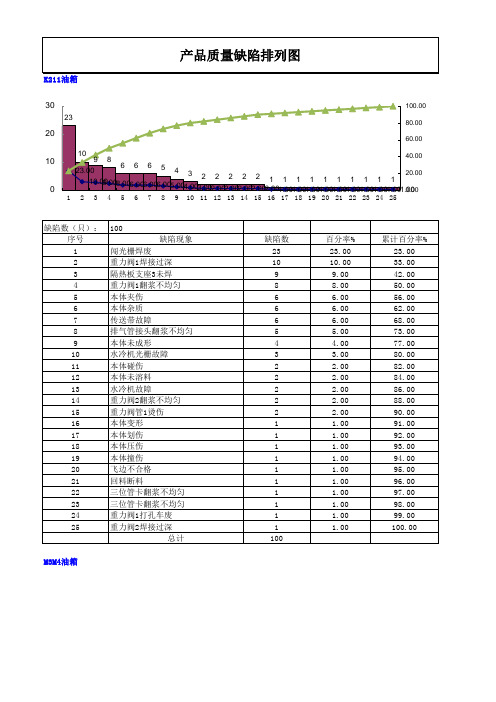
累计百分率% 36.21 44.83 51.72 56.90 60.69 64.48 67.59 70.34 72.76 75.17 77.59 79.66 81.72 83.45 85.17 86.55 87.93 89.31 90.34 91.38 92.41 93.10 93.79 94.48 95.17 95.86 96.21 96.55 96.90 97.24 97.59 97.93 98.28 98.62 98.97 99.31 99.66 100.00
总计
M44EP6油箱
缺陷数 105 25 20 15 11 11 9 8 7 7 7 6 6 5 5 4 4 4 3 3 3 2 2 2 2 2 1 1 1 1 1 1 1 1 1 1 1 1 290
百分率% 36.21 8.62 6.90 5.17 3.79 3.79 3.10 2.76 2.41 2.41 2.41 2.07 2.07 1.72 1.72 1.38 1.38 1.38 1.03 1.03 1.03 0.69 0.69 0.69 0.69 0.69 0.34 0.34 0.34 0.34 0.34 0.34 0.34 0.34 0.34 0.34 0.34 0.34
1 2 3 4 5 6 7 8 9 10 11 12 13 14 15 16 17 18 19 20 21 22 23 24 25 26 27 28 29 30 31 32 33 34 35 36 37 38
缺陷数(只): 序号 1 2 3 4 5 6 7 8 9 10 11 12 13 14 15 16 17 18 19 20 21 22 23 24 25 26 27 28 29 30 31 32 33 34 35 36 37 38
总计
常见的焊接缺陷及缺陷图片
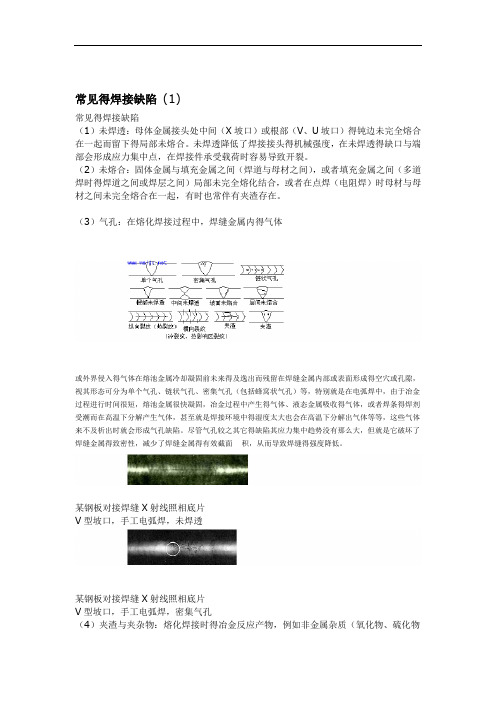
常见得焊接缺陷(1)常见得焊接缺陷(1)未焊透:母体金属接头处中间(X坡口)或根部(V、U坡口)得钝边未完全熔合在一起而留下得局部未熔合。
未焊透降低了焊接接头得机械强度,在未焊透得缺口与端部会形成应力集中点,在焊接件承受载荷时容易导致开裂。
(2)未熔合:固体金属与填充金属之间(焊道与母材之间),或者填充金属之间(多道焊时得焊道之间或焊层之间)局部未完全熔化结合,或者在点焊(电阻焊)时母材与母材之间未完全熔合在一起,有时也常伴有夹渣存在。
(3)气孔:在熔化焊接过程中,焊缝金属内得气体或外界侵入得气体在熔池金属冷却凝固前未来得及逸出而残留在焊缝金属内部或表面形成得空穴或孔隙,视其形态可分为单个气孔、链状气孔、密集气孔(包括蜂窝状气孔)等,特别就是在电弧焊中,由于冶金过程进行时间很短,熔池金属很快凝固,冶金过程中产生得气体、液态金属吸收得气体,或者焊条得焊剂受潮而在高温下分解产生气体,甚至就是焊接环境中得湿度太大也会在高温下分解出气体等等,这些气体来不及析出时就会形成气孔缺陷。
尽管气孔较之其它得缺陷其应力集中趋势没有那么大,但就是它破坏了焊缝金属得致密性,减少了焊缝金属得有效截面积,从而导致焊缝得强度降低。
某钢板对接焊缝X射线照相底片V型坡口,手工电弧焊,未焊透某钢板对接焊缝X射线照相底片V型坡口,手工电弧焊,密集气孔(4)夹渣与夹杂物:熔化焊接时得冶金反应产物,例如非金属杂质(氧化物、硫化物等)以及熔渣,由于焊接时未能逸出,或者多道焊接时清渣不干净,以至残留在焊缝金属内,称为夹渣或夹杂物。
视其形态可分为点状与条状,其外形通常就是不规则得,其位置可能在焊缝与母材交界处,也可能存在于焊缝内。
另外,在采用钨极氩弧焊打底+手工电弧焊或者钨极氩弧焊时,钨极崩落得碎屑留在焊缝内则成为高密度夹杂物(俗称夹钨)。
W18Cr4V(高速工具钢)-45钢棒对接电阻焊缝中得夹渣断口照片钢板对接焊缝X射线照相底片型坡口,手工电弧焊,局部夹渣V.钢板对接焊缝X射线照相底片型坡口,手工电弧焊,两侧线状夹渣V钢板对接焊缝X射线照相底片手工电弧焊,夹钨型坡口,钨极氩弧焊打底+V(5)裂纹:焊缝裂纹就是焊接过程中或焊接完成后在焊接区域中出现得金属局部破裂得表现。
常见焊接缺陷及图示

常见焊接缺陷及图示
常见的缺陷有:裂纹、焊瘤、烧穿、弧坑、气孔、夹渣、咬边、未熔合、未焊透等,以及焊缝尺寸不符合要求、焊缝成形不良(如:长度不足,高度不足,未满焊)等。
1.气孔:
修复方法:打磨去除该段焊缝,重新焊接。
修复方法:打磨去除该段焊缝,重新焊接。
2.砂眼(焊接时气体或杂质在焊接构件内部或表面形成的小孔)
修复方法:打磨去除所有影响焊缝,重新焊接。
3.缩孔(焊接后在冷凝过程中收缩而产生的孔洞,形状不规则,孔壁粗糙,一般位于铸件的热节处。
)
修复方法:打磨去除所有影响焊缝,重新焊接。
4.焊瘤(金属物在焊接过程中,通过电流造成金属焊点局部高温熔化,液体金属凝固时,在自重作用下金属流淌
形成的微小疙瘩)
修复方法:打磨去除该段重新焊接5.咬边(烧筋)
修复方法:重新焊接
6.弧坑(在焊接收尾处形成低于焊缝高度的凹陷坑)
修复方法:打磨去除该段重新焊接7.焊缝不均匀
修复方法:重新焊接
8.焊接裂缝
修复方法:打磨去除该段重新焊接
9.未焊透(未焊透指母材金属未熔化,焊缝金属没有进入接头根部的现象)
修复方法:打磨去除该段重新焊接10.未满焊(未焊满是指焊缝表面上连续的或断续的沟槽)
修复方法:打磨去除该段重新焊接11.简易示意图。
缺陷的种类和产生原因

图4
未焊满
(5) 烧穿——烧穿是指焊接过程中,熔深超过工件厚度,熔 化金属自焊缝背面流出,形成穿孔性缺陷,见图5。 焊接电流过大,速度太慢, 电弧在焊缝处停留过久,都 会产生烧穿缺陷。工件间隙太大,钝边太小也容易出现烧 穿现象。 烧穿是绝大多数产品上不允许存在的缺陷。它破坏了焊 缝,使接头丧失连接及承载能力。 选用较小电流和合适的焊接速度,减小装配间隙,在焊缝 背面加设垫板或药垫,使用脉冲焊,能有效地防止烧穿。
图8
夹渣
(3) 夹渣产生的原因 1)坡口尺寸不合理。 2) 坡口有污物。 3) 多层焊时,层间清渣不彻底。 4) 焊接线能量小。 5) 焊缝散热太快,液态金属凝固过快。 6) 焊条药皮,焊剂化学成分不合理,熔点过高,冶金反应 不完全,脱渣性不好。 7) 钨极性气体保护焊时,电源极性不当,电流密度大,钨 极熔化脱落于熔池中。 8) 手工焊时,焊条摆动不正确,不利于熔渣上浮。 可根据以上原因分别采取对应措施,以防止夹渣的产生。 (4) 夹渣的危害——点状夹渣的危害与气孔相似,带有尖角的 夹渣会产生尖端应力集中,尖端还焊缝表面上连续的或断续的沟 槽,见图4。 填充金属不足是产生未焊满的根本原因。规范太弱,焊条 过细,运条不当等均会导致未焊满。 未焊满同样减小了焊缝的有效截面积,削弱了焊缝,也会 产生应力集中。同时,由于规范太弱使冷却速度增大,容 易产生气孔、裂纹等缺陷。 防止未焊满的措施:加大焊接电流,加焊盖面焊缝。
(3) 凹坑——凹坑指焊缝表面或 背面局部的假于母:材的部 分,见图3。 凹坑多是由于收弧时焊条(焊 丝)未作短时间停留造成的 (此时的凹坑称为弧坑)。仰、 立、横焊时,常在焊缝背面 根部产生内凹。
图3
凹坑
凹坑减小了焊缝的有效截面积,弧坑常带有弧坑裂纹和弧 坑缩孔。 防止凹坑产生的措施:施焊时尽量选用平焊位置,选用合 适的焊接规范,收弧时让焊条在熔池内短时间停留或环形 摆动,填满弧坑。
- 1、下载文档前请自行甄别文档内容的完整性,平台不提供额外的编辑、内容补充、找答案等附加服务。
- 2、"仅部分预览"的文档,不可在线预览部分如存在完整性等问题,可反馈申请退款(可完整预览的文档不适用该条件!)。
- 3、如文档侵犯您的权益,请联系客服反馈,我们会尽快为您处理(人工客服工作时间:9:00-18:30)。
压铸产品缺陷图示
缺陷种类图例1.流痕
其他名称:条纹
特征:铸件表面上呈现与金属液流动方向相
一致的,用手感觉得出的局部下陷光滑纹路。
此缺陷无发展倾向,用抛光法能去除。
2.冷隔
其他名称:冷接
特征:温度较低的金属流互相对接但未熔合
而出现的缝隙。
呈现不规则的线形,有穿透
的和不穿透的两种,在外力作用下有发展趋
势。
3.擦伤
其他名称:拉伤、拉痕、粘模伤痕
特征:顺着脱模方向,由于金属粘附,模具
制造斜度太小而造成铸件表面的拉伤痕迹,
严重时称为拉伤面。
4. 凹陷
其他名称:缩凹、缩陷、憋气、塌边
特征:铸件平滑表面上出现凹瘪的部分,其
表面呈自然冷却状态。
5.气泡
其他名称:鼓泡
特征:铸件表皮下,聚集气体鼓胀所形成的
泡。
6.气孔
其他名称:空气孔
特征:卷入压铸件内部的气体所形成的形状较为规则,表面较为光滑的空洞。
7.缩孔
其他名称:缩空、缩眼
特征:压铸件在冷凝过程中,由于内部补偿不足所造成的形状不规则,表面较粗糙的孔洞。
8.花纹
特征:铸件表面上呈现的光滑条纹,肉眼可见,但用手感觉不出,颜色不同于基体金属的纹路,用砂布稍擦几下即可去除。
9.裂纹
特征:铸件上合金基体被破坏或断开形成细丝状的缝隙,有穿透的和不穿透的两种,有发展趋势。
裂纹可以分为冷裂纹和热裂纹两种,他们的主要区别是冷裂纹铸件开裂处金属未被氧化,热裂纹铸件开裂处金属被氧化。
10.欠铸
其他名称:浇不足、轮廓不清、边角残缺特征:金属液未充满型腔,铸件上出现填充不完整的部位。
11.印痕
其他名称:推杆印痕、镶块或活动块拼接印痕。
特征:铸件表面由于模具型腔磕碰及推杆、镶块、活动块等零件拼接所留下的凸出和凹下的痕迹。
12.网状毛刺
其他名称:网状痕迹、网状花纹、龟裂毛刺特征:由于模具型腔表面产生热疲劳而形成的铸件表面上的网状凸起痕迹和金属刺。
13.有色斑点
其他名称:油斑、黑色斑点、积炭
特征:铸件表面上呈现的不同于基体金属的斑点,一般由涂料碳化物形成。
14.麻面
特征:充型过程中由于模具温度或合金温度太低,在近似于欠压条件下铸件表面形成的细小麻点状分布区域。
15.飞边
其他名称:披缝
特征:铸件边缘上出现的金属薄片。
16.分层
其他名称:隔皮、夹层
特征:铸件上局部存在有明显的金属层次。
17.疏松
特征:铸件表面上 呈现松散不紧实的宏观组织。
18.错边(错扣)
其他名称:错缝
特征:铸件的一部分与另一部分在分型面上错开,发生相对位移(对螺纹称错扣)。
19.变形
其他名称:扭曲、翘曲
特征:铸件几何形状与设计要求不符的整体变形。
20.碰伤
特性:铸件表面因撞击而造成的伤痕。
21.缺料
其他名称:崩料、掉肉
特征:因铸件过脆,或去水口时拉(崩)掉过多的坯料,或机加工铣平面崩块,造成加工余量不足。
22.黑皮
特征:局部尺寸偏差造成机加工余量不足,加工面有颜色层次
23.起皮
特征:经抛丸后产品部分表层翻开,外观不光滑。
24.铁环包铝
特征:曲轴孔镶件机加工后有铝皮包住。
25.爆环
其他名称:铁环裂纹
特征:铁环上有细小裂纹
26.铁环砂眼
特征:铁环机加工后明显有气孔或缩孔27.硬质点
其他名称:氧化夹杂、夹杂
特征:铸件基体内存在有硬度高于金属基体的细小质点或块状物,使加工困难,刀具磨损严重,加工后铸件上常常显示出不同亮度的硬质点。
28.脆性
特征:铸件基本金属晶粒过于粗大或细小,铸件易断裂或碰碎。
29.化学成分不符合要求
特征:经化学分析,铸件合金元素不符要求或杂质过多。
30.机械性能不符合要求
特征:铸件合金的机械强度、延伸率低于要求标准。