水泥熟料设计与烧成实验
新型节能环保水泥熟料烧成技术的研发及应用(上)
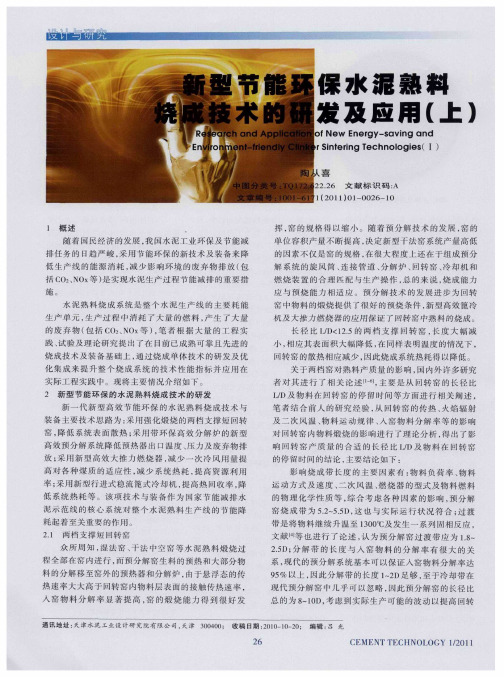
解 系 统 的旋 风 筒 、 接 管 道 、 连 分解 炉 、 回转 窑 、 冷却 机 和 燃 烧 装 置 的合 理 匹 配 与 生 产 操 作 , 的 来 说 , 成 能 力 总 烧
应 与 预 烧 能 力 相 适 应 。预 分 解 技 术 的 发 展 进 步 为 回转 窑 中物 料 的 煅 烧 提 供 了 很 好 的 预烧 条 件 , 型 高 效 篦 冷 新 机 及 大 推 力燃 烧 器 的 应用 保 证 了 回转 窑 中熟 料 的烧 成 。 长 径 比 LD< 25的 两 档 支 撑 回 转 窑 , 度 大 幅 减 / 1. 长 小 , 应 其 表 面 积 大 幅 降低 , 同样 表 明温 度 的情 况 下 , 相 在
程 全 部 在 窑 内进 行 , 预 分 解 窑 生料 的预 热 和 大 部 分 物 而
系 , 代 的 预 分 解 系统 基 本 可 以保 证 人 窑 物 料 分 解率 达 现 9 % 以上 , 此 分 解带 的 长度 1 2 5 因 ~ D足 够 , 于 冷 却带 在 至
现 代 预 分 解 窑 中 几 乎 可 以忽 略 , 因此 预 分 解 窑 的 长 径 比
带 是将 物 料继 续 升温 至 1 0 ℃及 发 生 一 系 列 同相 反 应 , 30
文 献 等 也 进 行 了论 述 , 为 预 分 解 窑过 渡 带 应 为 1 ~ 认 . 8
25 分 解 带 的 长 度 与 人 窑 物 料 的 分 解 率 有 很 大 的 关 .D;
众 所 周 知 , 法 窑 、 法 中空 窑 等 水 泥 熟 料 煅 烧 过 湿 干
磊
料 I 【 = 上
nd
(I)
l 概 述
.
挥 , 的规 格 得 以缩 小 。 随 着 预 分 解 技 术 的 发 展 , 的 窑 窑
水泥熟料烧成的变化过程

水泥熟料烧成的变化过程一、干燥与脱水1.干燥入窑物料当温度升高到100~150℃时,生料中的自由水全部被排除,特别是湿法生产,料浆中含水量为32~40%,此过程较为重要。
而干法生产中生料的含水率一般不超过1.0%。
2.脱水当入窑物料的温度升高到450℃,粘土中的主要组成高岭土(Al2O3·2SiO2·2H2O )发生脱水反应,脱去其中的化学结合水。
此过程是吸热过程。
Al2O3·2SiO2·2H2O== Al2O3 (无定形) + 2SiO2 (无定形) + 2H2O脱水后变成无定形的三氧化三铝和二氧化硅,这些无定形物具有较高的活性。
二、碳酸盐分解当物料温度升高到600℃时,石灰石中的碳酸钙和原料中夹杂的碳酸镁进行分解,在CO2分压为一个大气压下,碳酸镁和碳酸钙的剧烈分解温度分别是750℃和900℃。
MgCO3=MgO+CO2CaCO3=CaO+CO2碳酸钙分解反应的特点碳酸钙的分解过程是一个强吸热过程(1645 kJ/kg ),是熟料形成过程中消耗热量最多的一个工艺过程;该过程的烧失量大,在分解过程中放出大量的CO2气体,使CaO疏松多孔,强化固相反应。
三、固相反应1.反应过程从原料分解开始,物料中便出现了性质活泼的游离氧化钙,它与生料中的SiO2、Al2O3、Fe2O3进行固相反应,形成熟料矿物。
2.影响固相反应的主要因素⑴生料细度及其均匀程度;⑵温度对固相反应的影响;四、熟料烧结水泥熟料主要矿物硅酸三钙的形成需在液相中进行,液相量一般在22~26%。
2 CaO·SiO2 + CaO=3 CaO·SiO2该反应称为烧结反应,它是在1300~1450~1300℃范围进行,故称该温度范围为烧成温度范围;在1450℃时反应迅速,故称该温度为烧成温度。
为使反应完全,还需有一定的时间,一般为15~25分钟。
五、熟料冷却熟料冷却时需急速冷却,其目的和作用是:1、为了防止C3S在1250℃分解出现二次游离氧化钙(对水泥安定性没大影响),降低熟料的强度;2、为了防止C2S在500℃时发生晶型转变,产生“粉化”现象;3、防止C3S晶体长大而强度降低且难以粉磨;4、减少MgO晶体析出,使其凝结于玻璃体中,避免造成水泥安定性不良;5、减少C3A晶体析出,不使水泥出现快凝现象,并提高水泥的抗硫酸盐性能;6、使熟料产生应力,增大熟料的易磨性。
日产5000吨水泥熟料新型干法生产线烧成系统窑头工艺设计
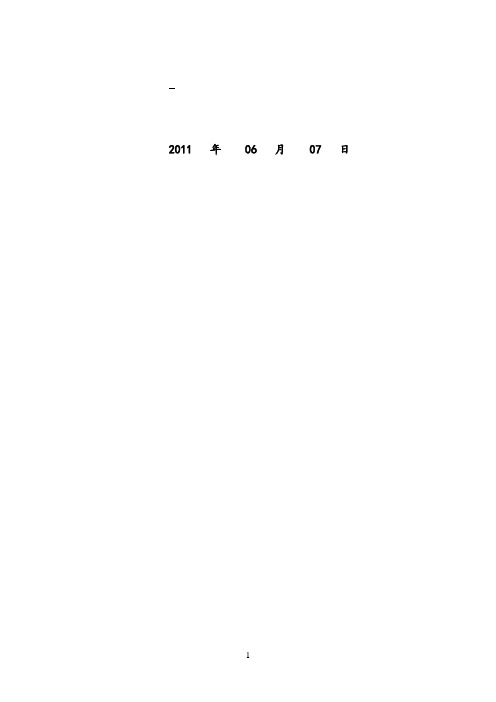
关键词:物料平衡、新型干法生产、篦冷机、电收尘、
ABSTRACT
This designisone 5000tons of cementclinkerproductionlines burningdrykilnsystem ofsome ofthe design.In order todesign morereasonable and perfect,I revieweda lot of information, andcombined with the currentdaily output of5,000 tons ofcement clinkerproduction line ofnew drykilnsystempractical examplesto makehis owndesign results.But has very many Shortcoming existence, therefore looks forgiveness. Under I introduce my design mentality. 1.Kiln choice:in the selection process of Kiln, Icalculate thetheoretical formulausedkiln, and I alsofindthe actualmanufacturerof thesituation, finally, Isetmycombination;2.Mass balance computation:According to the empirical formula(limestone saturation coefficient, silicic acid rate, alumina rate)calculates, obtains the appropriate rate value.Determinethe finalratio of raw materials;3.Material balancecalculationsbased on previousresults, combined withtheoretical formulaand the application ofselectedmodelsderivedinstance;4.Appurtenance shaping: The appurtenance includes,Clinkercrusher,clinkerzippermachines,centrifugal fans,pulverized coal burner.The equipment although is small, but in the production process also is essential.
日产5000吨水泥熟料新型干法生产线烧成系统窑头工艺设计
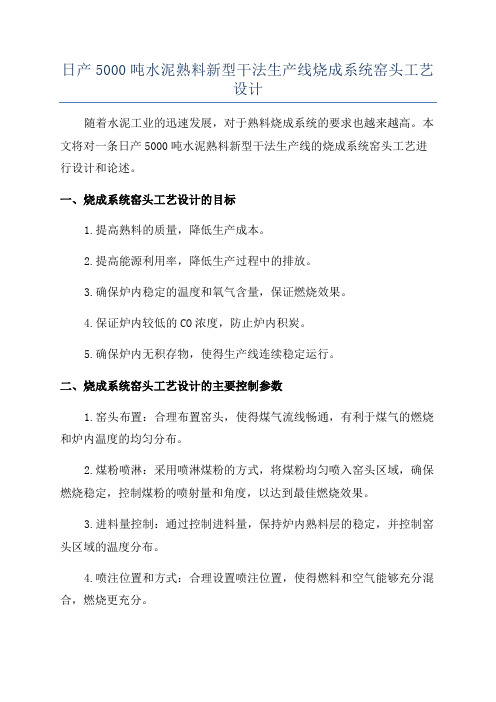
日产5000吨水泥熟料新型干法生产线烧成系统窑头工艺设计随着水泥工业的迅速发展,对于熟料烧成系统的要求也越来越高。
本文将对一条日产5000吨水泥熟料新型干法生产线的烧成系统窑头工艺进行设计和论述。
一、烧成系统窑头工艺设计的目标1.提高熟料的质量,降低生产成本。
2.提高能源利用率,降低生产过程中的排放。
3.确保炉内稳定的温度和氧气含量,保证燃烧效果。
4.保证炉内较低的CO浓度,防止炉内积炭。
5.确保炉内无积存物,使得生产线连续稳定运行。
二、烧成系统窑头工艺设计的主要控制参数1.窑头布置:合理布置窑头,使得煤气流线畅通,有利于煤气的燃烧和炉内温度的均匀分布。
2.煤粉喷淋:采用喷淋煤粉的方式,将煤粉均匀喷入窑头区域,确保燃烧稳定,控制煤粉的喷射量和角度,以达到最佳燃烧效果。
3.进料量控制:通过控制进料量,保持炉内熟料层的稳定,并控制窑头区域的温度分布。
4.喷注位置和方式:合理设置喷注位置,使得燃料和空气能够充分混合,燃烧更充分。
确保炉内氧气浓度达到规定要求,提高熟料的烧结质量。
三、烧成系统窑头工艺设计的具体内容1.窑头布置合理设置窑头区域的布置,使得煤气在该区域内流线畅通,有利于煤气的燃烧和炉内温度的均匀分布。
窑头区域应尽量避免死角和室外风向相对应的通风口。
2.煤粉喷淋采用喷淋煤粉的方式,将煤粉均匀喷入窑头区域,使得燃烧更加均匀稳定。
喷淋方式可以采用多角度喷淋或者环形喷淋,根据窑头区域的具体设计来决定。
3.进料量控制通过控制进料量,保持炉内熟料层的稳定,并控制窑头区域的温度分布。
进料量可以通过控制进料设备的运行速度和进料口的开启程度来实现。
4.喷注位置和方式根据窑头区域的特点和煤粉的喷射角度,合理设置喷注位置,使得燃料和空气能够充分混合,燃烧更加充分。
喷射方式可以采用立喷、横喷或者斜喷等方式。
5.空气供给浓度达到规定要求。
炉内的氧气浓度可以通过调节空气进口阀门的开启程度来实现。
四、总结通过对日产5000吨水泥熟料新型干法生产线的烧成系统窑头工艺设计的详细论述,我们可以看到,合理布置窑头、控制煤粉喷淋、控制进料量、合理设置喷注位置和方式,以及调节空气供给量等因素,对于烧成系统的燃烧效果、熟料质量和生产成本具有重要影响。
水泥熟料的煅烧
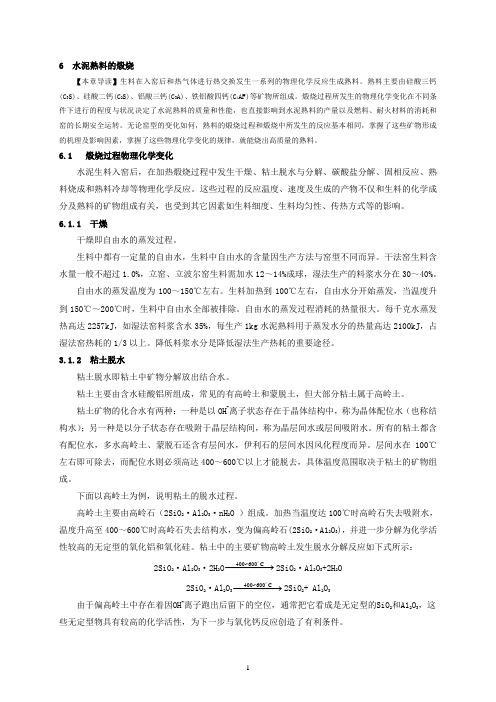
6 水泥熟料的煅烧【本章导读】生料在入窑后和热气体进行热交换发生一系列的物理化学反应生成熟料。
熟料主要由硅酸三钙(C 3S)、硅酸二钙(C 2S)、铝酸三钙(C 3A)、铁铝酸四钙(C 4AF)等矿物所组成。
煅烧过程所发生的物理化学变化在不同条件下进行的程度与状况决定了水泥熟料的质量和性能,也直接影响到水泥熟料的产量以及燃料、耐火材料的消耗和窑的长期安全运转。
无论窑型的变化如何,熟料的煅烧过程和煅烧中所发生的反应基本相同,掌握了这些矿物形成的机理及影响因素,掌握了这些物理化学变化的规律,就能烧出高质量的熟料。
6.1 煅烧过程物理化学变化水泥生料入窑后,在加热煅烧过程中发生干燥、粘土脱水与分解、碳酸盐分解、固相反应、熟料烧成和熟料冷却等物理化学反应。
这些过程的反应温度、速度及生成的产物不仅和生料的化学成分及熟料的矿物组成有关,也受到其它因素如生料细度、生料均匀性、传热方式等的影响。
6.1.1 干燥干燥即自由水的蒸发过程。
生料中都有一定量的自由水,生料中自由水的含量因生产方法与窑型不同而异。
干法窑生料含水量一般不超过1.0%,立窑、立波尔窑生料需加水12~14%成球,湿法生产的料浆水分在30~40%。
自由水的蒸发温度为100~150℃左右。
生料加热到100℃左右,自由水分开始蒸发,当温度升到150℃~200℃时,生料中自由水全部被排除。
自由水的蒸发过程消耗的热量很大。
每千克水蒸发热高达2257kJ ,如湿法窑料浆含水35%,每生产1kg 水泥熟料用于蒸发水分的热量高达2100kJ ,占湿法窑热耗的1/3以上。
降低料浆水分是降低湿法生产热耗的重要途径。
3.1.2 粘土脱水粘土脱水即粘土中矿物分解放出结合水。
粘土主要由含水硅酸铝所组成,常见的有高岭土和蒙脱土,但大部分粘土属于高岭土。
粘土矿物的化合水有两种:一种是以OH -离子状态存在于晶体结构中,称为晶体配位水(也称结构水);另一种是以分子状态存在吸附于晶层结构间,称为晶层间水或层间吸附水。
实验一水泥熟料制备与分析
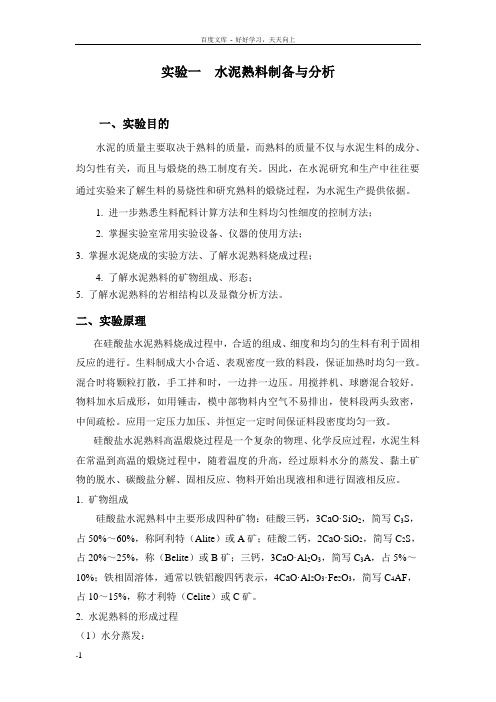
实验一水泥熟料制备与分析一、实验目的水泥的质量主要取决于熟料的质量,而熟料的质量不仅与水泥生料的成分、均匀性有关,而且与煅烧的热工制度有关。
因此,在水泥研究和生产中往往要通过实验来了解生料的易烧性和研究熟料的煅烧过程,为水泥生产提供依据。
1. 进一步熟悉生料配料计算方法和生料均匀性细度的控制方法;2. 掌握实验室常用实验设备、仪器的使用方法;3. 掌握水泥烧成的实验方法、了解水泥熟料烧成过程;4. 了解水泥熟料的矿物组成、形态;5. 了解水泥熟料的岩相结构以及显微分析方法。
二、实验原理在硅酸盐水泥熟料烧成过程中,合适的组成、细度和均匀的生料有利于固相反应的进行。
生料制成大小合适、表观密度一致的料段,保证加热时均匀一致。
混合时将颗粒打散,手工拌和时,一边拌一边压。
用搅拌机、球磨混合较好。
物料加水后成形,如用锤击,模中部物料内空气不易排出,使料段两头致密,中间疏松。
应用一定压力加压、并恒定一定时间保证料段密度均匀一致。
硅酸盐水泥熟料高温煅烧过程是一个复杂的物理、化学反应过程,水泥生料在常温到高温的煅烧过程中,随着温度的升高,经过原料水分的蒸发、黏土矿物的脱水、碳酸盐分解、固相反应、物料开始出现液相和进行固液相反应。
1. 矿物组成硅酸盐水泥熟料中主要形成四种矿物:硅酸三钙,3CaO·SiO2,简写C3S,占50%~60%,称阿利特(Alite)或A矿;硅酸二钙,2CaO·SiO2,简写C2S,占20%~25%,称(Belite)或B矿;三钙,3CaO·Al2O3,简写C3A,占5%~10%;铁相固溶体,通常以铁铝酸四钙表示,4CaO·Al2O3·Fe2O3,简写C4AF,占10~15%,称才利特(Celite)或C矿。
2. 水泥熟料的形成过程(1)水分蒸发:自由水分随物料温度而逐渐蒸发,当温度升高至100~150℃时,生料中自由水分全部被排除。
湿法生产中,料浆可达32%~40%,故此干燥过程对产量、质量及热耗影响极大。
第6章 水泥熟料的烧成2-形成热计算
( ) q0 = q − q' = (q1 + ⋅⋅⋅⋅⋅⋅ +q6 ) − q1' + ⋅⋅⋅⋅⋅⋅ +q5'
式中,q0—形成 1kg 熟料理论热耗量,kJ/kg-clinker;
q—熟料形成过程中吸收热量之和,kJ/kg-clinker; q' —熟料形成过程中放出热量之和,kJ/kg-clinker。 上述计算比较麻烦,可用下列简易公式进行计算,即
q1'
= mr AS2 H 2
M AS2 M AS2H2
×
301
=
mr AS2 H 2
× 301× 0.86
式中, q1' —黏土脱水后无定形物质结晶放热,kg/kg-clinker;
0.86—脱水高岭土(Al2O3·2SiO2)和高岭土(Al2O3·2SiO2·2H2O)相
对分子质量之比;
301—脱水高岭土的结晶热,kJ/kg-AS2。 ⑵ 熟料矿物形成放出热量,与各矿物的含量有关,其矿物含量可根据
⑷ 碳酸盐分解吸收热量
q4
=
Mr CaCO3
×1660 +
Mr MgCO3
× 1420
式中,q4—碳酸盐分解吸收的热量,kJ/kg-clinker;
1660—碳酸钙分解热效应,kJ/kg-CaCO3;
1420—碳酸镁分解热效应,kJ/kg- MgCO3。
⑸ 物料由 900℃加热到 1400℃时吸收的热量
C4 AF = 3.04Fe2O3k ( P > 0.64)
式中,C3S,C2S,C3A,C4AF—熟料各种矿物的含量,%; CaOk,SiO2k,Al2O3k,Fe2O3k—熟料中各化学成分含量,%。
熟料实验报告单
熟料实验报告单实验目的本实验的目的是研究不同条件下熟料的性质和成分变化,通过实验结果,探究熟料的制备过程及其对水泥品质的影响。
实验原理熟料是水泥的主要成分,其主要由矿渣和烧成熟料组成。
矿渣是通过冶炼和燃烧工业废料得到的,而烧成熟料则是通过在高温下将原料进行反应得到的。
根据实验需求,我们将研究烧成熟料的成分变化和其对水泥品质的影响。
实验中,我们将采用不同烧成温度和反应时间的条件下制备熟料,并进行物理性能测试和化学成分分析。
实验步骤1. 准备实验所需材料,包括不同比例的原料和控制变量条件下的装置。
2. 按照实验条件,将原料投入烧结炉中,并控制好烧成温度和反应时间。
3. 熟料烧结完成后,取出样品进行外观观察。
4. 对烧结样品进行物理性能测试,包括密度、抗压强度等。
5. 对烧成样品进行化学成分分析,包括主要元素的含量、氧化物的比例等。
实验结果及分析经过实验,我们得到了不同烧成温度下的烧结样品。
我们观察到随着烧成温度的升高,熟料的颜色逐渐变深,且质地更加致密。
这说明烧成温度对熟料的成分和性质有一定的影响。
通过物理性能测试,我们发现烧成温度较高的样品具有较高的密度和抗压强度。
这是因为高温有利于原料的熔化和反应,使得熟料更加致密、结晶度更高,从而提高了水泥的品质。
化学成分分析的结果表明,随着烧成温度的升高,熟料中氧化物的含量减少,而硅酸盐和氧化铁含量增加。
这是因为在高温下,矿物质的熔融和反应速度加快,使得不稳定的化合物转变为稳定的硅酸盐、氧化铁等成分。
结论通过实验结果分析,我们得出以下结论:1. 烧成温度对熟料的成分和性质有重要影响,高温有利于提高熟料的密度、抗压强度和品质。
2. 高温下熟料中的氧化物含量减少,硅酸盐和氧化铁含量增加。
实验总结本实验主要研究了烧成温度对熟料的影响。
通过实验,我们了解了熟料的制备过程和成分的变化。
在实验过程中,我们还发现了一些实验技巧,如控制烧成温度和反应时间等。
然而,本实验还存在一些局限性,如样品数量较少、实验条件有限等,这些因素可能会对实验结果产生一定影响。
水泥熟料节能降氮烧成技术-2019年节能技术应用案例
水泥熟料节能降氮烧成技术技术适用范围适用于水泥行业新型干法水泥熟料煅烧领域。
技术原理及工艺分解炉系统采用“分解炉鹅颈管”结构的“再循环”技术和分级燃烧技术,提升煤粉燃尽率及出分解炉物料的分解率,降低回转窑内的热负荷,强化分解炉内的热稳定性,降低有害气体的排放量;通过戴“非金属材质拢焰罩”的低氮燃烧器及纵向控制流固定床,提高熟料的质量和整机的冷却效率,采用精密系统优化控制技术,使各项工艺结构的性能得到充分发挥,实现系统稳定运行。
主要装备工艺图如下:技术指标(1)熟料热耗在原有指标下降低10-15kgce/tcl;(2)熟料综合电耗降低3-5 kW·h /tcl;(3)氨水用量比原来减少50-70%。
技术功能特性低NO x排放,通过较低的一次风量(6%以下)和减少火焰的最高温度点,通常一般的低氮燃烧器可以降低氮氧化物生成量4-10%。
应用案例中国建材集团中材甘肃水泥有限公司改造项目。
技术提供单位为淄博科邦热工科技有限公司。
(1)用户用能情况简单说明改造前,实际产量5100t/d,喂料量350t/h ,窑头耗煤量12~14t/h 、窑尾耗煤量21~24t/h ,氮氧化物排放浓度645~775mg/m3。
(2)实施内容及周期新增分解炉外循环、分解炉优化改造、窑头更换低氮燃烧器、优化热器、采用配套的操控技术。
改造后,喂料量352.4t/h,窑头耗煤量11-13t/h、窑尾耗煤量19-21t/h,氮氧化物排放浓度332~365mg/m3。
实施周期3 个月。
(3)节能减排效果及投资回收期改造后年可以节约标煤15900t,按每吨标准煤700 元估算,节约费用为1113 万元。
该项目节能效益合计为1113 万元,总投入为790 万元,投资回收期约9 个月。
熟料烧制方案
关于生料烧制熟料的方案为了寻求所产出的经过提碱、提铝的末次赤泥和其他几种废料的利用途径,根据领导安排我们自己初步对几种废料通过干燥机烘干、研磨、合理比例组合进行生料烧制,进行前期经验的积累,现对初步考虑的方案进行粗略罗列,有不当之处领导指出。
废料明细:电厂:渣脱碱赤泥、脱铝渣(产品)、粉煤灰、脱硫石膏原赤泥(含碱高)、煤气站碳芒硝、电石泥、盐泥、铝渣石灰粉、除尘粉。
烧制熟料名称:重点是硫铝酸盐为主,普通硅酸盐为辅。
一、原料分析:二、化验设备:101B干燥机、制样研磨机、盘式三头研磨机、1300度电阻炉、1600度电阻炉(附带不带釉的陶瓷坩埚、坩埚钳)三、配料计算:烧制熟料需要关注熟料的三个率值:硅率SM、铝率IM、石灰饱和系数KH1、硅率:硅率又称硅酸率,它表示熟料中Si02 的百分含量与AI2O3和Fe203百分含量之比,用SM 表示:通常硅酸盐水泥的硅率在 1.7-2.7 之间。
但白色硅酸盐水泥的硅率可达 4. 0 甚至更高。
硅率除了表示熟料的Si02 与A1203 和Fe2O3 的质量百分比外,还表示了熟料中硅酸盐矿物与溶剂矿物的比例关系,相应地反映了熟料的质量和易烧性。
2、铝率:铝率又称铁率,以IM 表示。
其计算式为:铝率通常在0. 9-1. 7 之间。
抗硫酸盐水泥或低热水泥的铝率可低至0. 7 。
铝率表示熟料中氧化铝与氧化铁的质量百分比,也表示熟料中铝酸三钙与铁铝酸四钙的比例关系,因而也关系到熟料的凝结快慢。
同时还关系到熟料液相粘度,从而影响熟料的锻烧的难易。
3、石灰饱和系数:石灰饱和系数KH :,是熟料中全部氧化硅生成硅酸钙(C3S-I-CzS) 所需的氧化钙含量与全部二氧化硅理论上全部生成硅酸三钙所需的氧化钙含量的比值,也即表示熟料中氧化硅被氧化钙饱和成硅酸三钙的程度。
硅酸盐水泥熟料KH 值在0. 82-0. 94 之间,我国湿法回转窑KH 值一般控制在0. 89 士0. 0l 左右。
- 1、下载文档前请自行甄别文档内容的完整性,平台不提供额外的编辑、内容补充、找答案等附加服务。
- 2、"仅部分预览"的文档,不可在线预览部分如存在完整性等问题,可反馈申请退款(可完整预览的文档不适用该条件!)。
- 3、如文档侵犯您的权益,请联系客服反馈,我们会尽快为您处理(人工客服工作时间:9:00-18:30)。
武汉理工大学
材料科学与工程学院水泥熟料设计与烧成实验
姓名:
班级:
组别:
实验时间:
一、前言
生产中会有许多工业废弃物,比如钢渣等,如果不能充分利用这些工业废弃物,则不仅给环境带来巨大压力,也会影响生产的可持续发展,因此需要多这些工业废弃物进行有效的利用。
当今的水泥生产,作为铁质原料提供铁的主要是铁矿石,考虑到铁矿石是不可再生的资源,因此需要找到一种铁质原料进行有效替代。
结合工业废弃物的利用与水泥工业的发展,我们提出可以采用工业废弃物中的钢渣作为铁质原料应用于水泥的工业生产。
二、实验方法
(1)方案设计
配料设计原材料化学分析
通过这些数据对水泥的配比进行设计,按一定的升温速率进行熟料烧成实验,分别对所得的水泥熟料测定游离氧化钙的含量和进行岩相分析,分析烧成制度对水泥的性能影响以及用钢渣代替铁矿石后对水泥性能的影响等,可与实际生产联系,判断其是否符合要求。
(2)制样
①原材料的选取:实验室用石灰石、页岩、砂岩、矿渣粉。
②破碎与粉磨:实验所以的原料以经过初步粉磨,为达到所需的细度,同时保证原料的成分,在取样之前还需要多原料进一步人工粉磨。
分别将一定量的石灰石、页岩、砂岩、矿渣粉放入不同的研磨盘里,用研磨棒进行研磨,之后过0.08mm 筛,分别收集筛下料。
③均化:研磨结束后,分别称取大约640g石灰石、160g页岩、80g砂岩,进行装袋,钢渣需要多少取多少。
每份原料总重800g,共需准备两。
之后按配料计算值准确称取石灰石、页岩、砂岩及钢渣(按铁矿石设计的配料,铁矿石的含量用钢渣代替),初步进行均化,然后每份试样分为300g、300g、200g放入球磨机中,打开球磨机,磨4min。
磨后的原料进行装袋,等待压片。
④压片:每次称取20~25g原料,放于压片所用的小罐子里,在液压机下进行压片。
(3)熟料烧成
每组生料片再细分为两组,分别进行1400℃和1450℃烧成。
硅酸盐水泥熟料煅烧化学过程
①水分蒸发100--150℃
②粘土矿物脱水层间吸附水约100℃以上
晶体配位水500-600℃
③碳酸盐分解600℃开始:
600℃:MgCO3→MgO+CO2
900℃: CaCO3→CaO+CO2
④固相反应(放热反应)
--800℃开始形成CA、C2F与C2S;
800--900℃开始形成C12A7;
900--1100℃C2AS形成并分解,开始形成C3A与
C4AF,CaCO3全部分解,f-CaO 含量达最大值
1100--1200℃大量形成C3A和C4AF,C2S含量达
最大值。
⑤烧成
1250-1280℃出现液相,熟料逐
渐烧结, 由疏松状转变为色泽黑、
结构致密熟料,体积收缩。
1280~1450℃
C2S+CaO→C3S
⑥冷却
< 1300℃,同时进行液相凝固
和相变两个过程:
C3S→C2S+CaO(水硬性降低)
β-C2S→γC2S(无水硬性)
烧成用仪器设备:
预烧用高温炉1000℃;煅烧用高温炉1600℃;电热干燥箱;称量天平;平底耐高温容器;坩埚夹钳;成型模具。
试验步骤
●将试体放在105-110℃电热干燥箱内烘60min以上。
●取相同试体为一组,均匀且不重叠地直立于平底耐
高温匣钵内。
●将匣钵放入恒温至试验温度的高温炉内,恒温煅烧
至规定时间。
容器尽可能放置在热电偶端点正下方。
煅烧时间从达到烧成温度起计到取样开门止。
●煅烧后取出的试体置于空气中强制快速冷却。
●将冷却后的试体一起研磨至全部通过80um筛,装
入贴有标签的磨口小瓶内。
(4)岩相分析
方片状的为C3S;圆形或椭圆形的为C2S;
小圆点、脚趾状的为f-C a O;小菱形为MgO;
长片状、带尖的为C3A;混合的为中间相C4AF。
实验步骤:
①四份熟料,分别选取其中的一小块,在其中一面先进行打磨处理,然后放入
金镶试样镶嵌机里面,加入金相专用镶嵌料环氧树脂,在100多的温度下维持12min进行制片。
②含有熟料试片的面分别在一组砂纸上进行打磨(由上往下,磨得越细),每
次一片,沿一个方向打磨,下一片再沿与前一片成90°方向打磨,直至一组砂纸全部打磨完为止。
③在金丝绒抛光盘上进行进一步抛光,加入刚玉粉,以一定的速度开动抛光盘,
将试片抛光,直至试块表面呈镜面、光泽度良好为止。
④已抛光的试片,选择合适的侵蚀剂,将光面全部浸在侵蚀剂内,并不断晃动,
一定时间后把试片取出,迅速用吹风机吹干。
⑤将试片置于反光显微镜下进行观察,寻找清晰的岩相,并保存照片。
(5)游离氧化钙的测定
游离氧化钙测试原理:甘油-乙醇法
熟料试样与甘油-乙醇溶液混合后,在加热搅拌下,通过硝酸锶的催化作用,熟料中游离氧化钙与甘油化合,生产弱碱性的甘油酸钙,并溶于溶液中,酚酞指示剂使溶液呈现红色。
用苯甲酸-乙醇溶液滴定生成的甘油酸钙至微红色消失,由苯甲酸-乙醇溶液的消耗量可以求出游离氧化钙的含量。
游离氧化钙滴定用仪器
A.测定装置
B.玛瑙研钵、方孔筛
磁铁、干燥器。
C.盘式电炉。
D.滴定管等。
实验步骤
1.准确称取熟料约0.5克,置于150毫升干燥的锥形瓶中,加入15毫升甘油无水乙醇溶液,摇匀。
2.装上回流冷凝器,在放有石棉网的电炉上加热煮沸至溶液呈红色数分钟之后取下锥形瓶,立即以0.1mol苯甲酸无水乙醇标准
溶液滴定至微红色消失。
3.将锥形瓶继续装在冷凝器上,继续加热煮沸至红色出现,再取下滴定。
如此反复操作,直至在加热10分钟后不出现红色为
止。
记下苯甲酸无水乙醇标准溶液消耗的体积。
三、结果分析与讨论
(1)生料配比设计:a 石灰石、页岩、砂岩、铁矿石改为钢渣
b 石灰石、页岩、砂岩、钢渣
用试凑法进行计算生料配比,过程如下:
(2)熟料高温烧成
冷却为:风冷进行急冷
(3)熟料质量检测
游离氧化钙测定:实验数据T CaO=5.1728mg/ml
①
数据分析:
a、同一个小组里的高温烧成1450℃所形成的熟料游离氧化钙含量低于
1400℃烧成的熟料中游离氧化钙的含量,原因是熟料煅烧温度对
fCaO影响很大。
在生料成分比较均匀,熟料率值相对稳定的情况下,
较高的烧成温度,物料在烧成带又有足够的停留时间,则窑内物料的
化学反应完全,熟料中fCaO含量就低。
假如烧成温度偏低,形成的液
相量就少,液相粘度大,fCaO在液相中运动速度减慢,影响
C2S+CaO---C3S的反应速度,熟料中fCaO含量就增加。
因此要减少
熟料中fCaO的含量,必须适当提高熟料煅烧温度以避免熟料的欠烧。
b、1组与2组,在相同温度下,如1400℃,1组熟料中的游离氧化钙含量
高于2组,原因是1组的石灰石含量80%,大于2组中石灰石含量78%,最终在烧成时使游离氧化钙含量偏大。
以上数据说明游离氧化钙的含量结果符合水泥熟料烧成的温度变化规律。
由于生产中游离氧化钙会影响水泥安定性,因此在生产工艺里可以通过调节烧成温度来控制游离氧化钙的含量,也可以通过调节石灰石的配比来控制。
于是,测定游离氧化钙的含量显得尤为重要。
②岩相分析。