化肥厂合成氨岗位操作规程
小型合成氨厂的基本工艺

二、冷鼓车间
•目的和任务: • 除去焦炉气中残余粉尘 微粒及焦油后,再经煤气鼓 风机升压后送往洗氨脱萘为 后工序提供洁净的焦炉气。
三、压缩工段
目的和任务: 是把气体输送到各工序
并提供过程进行所需要的压力, 以使这些过程按工艺要求得以 顺利进行。
四、变换岗位
合成岗位
目的和任务:
将经甲烷化后送来的氢氮比合格的气体导入 系统,在一定的温度、压力下在氨催化剂的 作用下使氢氮气合成氨,热后经过水冷、氨 冷使混合气中的大部分气氨冷凝成液氨而分 离出来,并送往氨贮槽。分离出液氨的氢氮 混合气经循环机赠压后与补充的新鲜气在一 起送入合成塔内进行反应,如此循环。
小型化肥厂的工艺简介
小型氮肥厂的整体工艺流程
焦化车间
冷鼓车间
原料气压缩工段
变脱工段
PSA一段
碳化车间
氨回收工段
合成车间
合成压缩工段
PSA二段 精脱工段硫 工段甲烷化
CO2压缩
碳化车间 化肥
一、焦化车间
•主要的工作原理及目的 •原理:原煤经过焦化炉高温干熘后, 产出煤气,并留下了其付产品焦Βιβλιοθήκη 炭、焦油等产品。精脱硫岗位
目的与任务: 除和去有变机脱硫后,原保料证气 气中体少中量硫的化H物2S 总含量小于0.1PPm,满足甲烷 化工艺对硫的要求,同时消除 硫化物对管道和设备的腐蚀。
甲烷化岗位
除<1去.0脱%)碳,气在少适量当的的C温O和度C、O压2(共力 下,通过甲烷化催化剂的作用 将成残触余媒的无C害O的和甲CO烷2转,化出为口对气合体 (CO+CO2<20PPm)。
目的和任务: 将压缩工段送来的焦炉气中
的CO加入水蒸气并在催化剂的作 用 后下工转段化提成供较CO合2,格同的时原获料得气H2。,为
合成氨生产安全
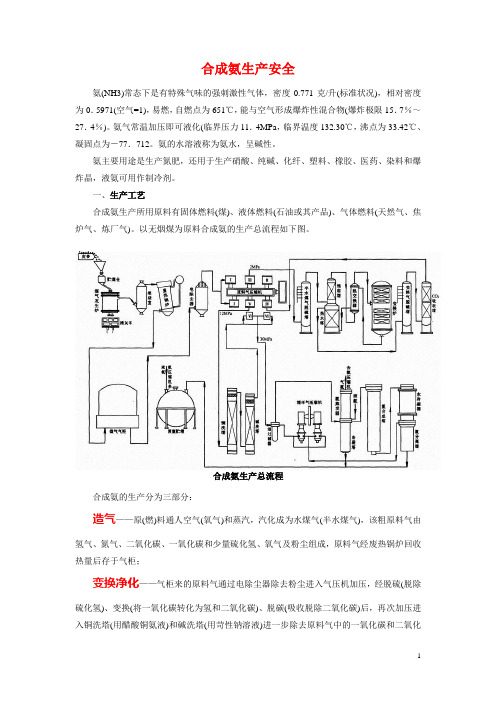
合成氨生产安全氨(NH3)常态下是有特殊气味的强刺激性气体,密度0.771克/升(标准状况),相对密度为0.5971(空气=1),易燃,自燃点为651℃,能与空气形成爆炸性混合物(爆炸极限15.7%~27.4%)。
氨气常温加压即可液化(临界压力11.4MPa,临界温度132.30℃,沸点为33.42℃、凝固点为-77.712。
氨的水溶液称为氨水,呈碱性。
氨主要用途是生产氮肥,还用于生产硝酸、纯碱、化纤、塑料、橡胶、医药、染料和爆炸晶,液氨可用作制冷剂。
一、生产工艺合成氨生产所用原料有固体燃料(煤)、液体燃料(石油或其产品)、气体燃料(天然气、焦炉气、炼厂气)。
以无烟煤为原料合成氨的生产总流程如下图。
合成氨生产总流程合成氨的生产分为三部分:造气——原(燃)料通人空气(氧气)和蒸汽,汽化成为水煤气(半水煤气),该粗原料气由氢气、氮气、二氧化碳、一氧化碳和少量硫化氢、氧气及粉尘组成,原料气经废热锅炉回收热量后存于气柜;变换净化——气柜来的原料气通过电除尘器除去粉尘进入气压机加压,经脱硫(脱除硫化氢)、变换(将一氧化碳转化为氢和二氧化碳)、脱碳(吸收脱除二氧化碳)后,再次加压进入铜洗塔(用醋酸铜氨液)和碱洗塔(用苛性钠溶液)进一步除去原料气中的一氧化碳和二氧化碳(含量降至十万分之三以下),获得纯氮气和氢气混合气体;合成——净化后的氢氮混合气(H:N2=3:1)经压缩机加压至30~32MPa进入合成塔,2在铁触媒存在下高温合成为氨。
生产是在密封、高压、高温下连续进行的。
二、职业危害合成氨生产的物料(易燃易爆、有毒)和工艺条件决定其具有极大固有危险性,事故统计表明,化工系统爆炸中毒事故最集中的就是合成氨生产。
爆炸——合成氨生产中的化学爆炸可归成三类。
一是高温高压使可燃气体爆炸极限扩宽,气体物料一旦过氧(亦称透氧),极易在设备和管道内发生爆炸;二是高温高压气体物料从设备管线泄漏时会迅速膨胀与空气混合形成爆炸性混合物,遇到明火或因高流速物料与裂(喷)口处摩擦产生静电火花引起着火和空间爆炸;三是气压机等转动设备在高温下运行会使润滑油挥发裂解,在附近管道内造成积炭,可导致积炭燃烧或爆炸。
鲁南化肥厂合成氨系统综合技术改造

・22・ 2006年第1期石油和化工节能鲁南化肥厂合成氨系统综合技术改造 吴萍 吕运江 (兖矿鲁南化肥厂 山东滕州277252) 摘要 本文介绍了兖矿鲁南化肥厂合成氨装置净化系统、合成系统进行的技术改造。
通过技术改造,使合成氨吨氨能耗降到44.09GJ,比目前中型合成氨装置吨氨能耗平均水平60.7GJ降低27%,取得了明显的节能效果。
关键词 合成氨 装置 节能 技术改造 兖矿鲁南化肥厂目前有两套合成氨装置,合成氨总生产能力为200kt/a,其中合成氨分厂的产能由原始设计的60 kt/a提高到了90 kt/a。
为进一步提高产量、降低成本、增加效益,对合成氨分厂合成氨系统进行了一系列的技术改造,使其生产能力达到了120 kt/a。
氨合成系统进行的综合技术改造情况总结如下。
1 净化系统 1.1 存在的问题 兖矿鲁南化肥厂合成氨分厂净化系统原设计为中变→低变→甲烷化流程,1998年进行全低变改造后,变换系统的吨氨高压蒸汽消耗降低到1.4 t,净化系统存在的主要问题在脱碳系统。
脱碳系统工艺落后,吸收和再生系统设备能力偏小,不能满足年产120 kt氨的需要。
具体表现在溶液的再生能力不足,一方面蒸汽消耗高,另一方面一次出口CO2含量长期在3%-5%,造成二次出口CO2和低变出口CO含量高,甲烷化温差大,消耗了大量的氢气,同时精制气中甲烷含量高,增加了合成的放空量,使合成氨产量降低,成本升高。
1.2 改造方案 经过反复考察和论证,决定采用南化院开发设计的脱碳变压再生工艺。
实施双塔变压再生,需增加加压再生塔、变煮器、蒸汽煮沸器、喷射器及冷却分离器、贫液闪蒸槽等设备,并更换贫液泵。
经论证,决定将原来的一次吸收塔改为二次吸收塔,新增1台φ3200 mm的一次吸收塔,原再生塔作为常压再生塔,加压再生塔由原来的一次吸收塔改造而成。
新增主要设备情况见表1。
表1 脱碳系统新增主要设备一览表 设备名称 规 格 一次吸收塔 φ3200 mm H=32784 mm 内装φ50×25×1双边阶梯环填料三层,每层6 m 二次吸收塔 φ2600 mm/φ2200 mm δ=24 mm H=33 260 mm 上部φ2200 mm装有φ50×50×2 mm碳钢填料18.5 m3 下部筛板为27层 加压再生塔 H=43100 mm 上部φ4200 mm δ=16 mm 下部φ2600 δ=22mm 上部扩大段为加压再生塔闪蒸段,内装Y125型不锈钢规整填料 下部筒体高约26950 mm,为原一次吸收塔筒体,内装两层φ50×20×1 mm碳钢阶梯环填料,每层6.8 m 常压再生塔 φ3200 mm H=39000 mm 贫液闪蒸槽 φ3000 mm H=6800 mm 卧式 加压再生塔 变换气煮沸器 φ1100×8763 mm,换热面积435 m2 加压再生塔低 变蒸汽煮沸器 φ1200×10742 mm,换热面积680 m2 贫液泵 TC 200-125×2 H=250 m Q=300 m3/h 1.3 改造的关键技术及创新点 选择了湖北省化学研究所的全低温变换工艺以及南化院的低供热源变压再生脱碳工艺,使净化装置的处理能力达到了国内中氮企业最高水平,消耗达到了国内最低水平,该净化工艺具有以下优点: (1)操作弹性大。
氨化拉料岗位安全操作规程范本
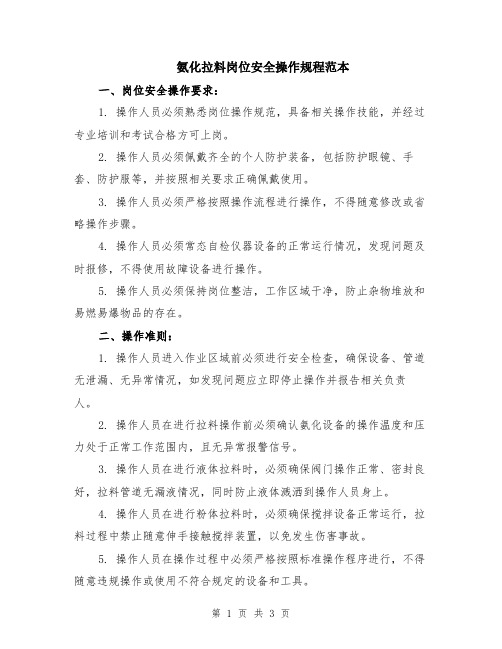
氨化拉料岗位安全操作规程范本一、岗位安全操作要求:1. 操作人员必须熟悉岗位操作规范,具备相关操作技能,并经过专业培训和考试合格方可上岗。
2. 操作人员必须佩戴齐全的个人防护装备,包括防护眼镜、手套、防护服等,并按照相关要求正确佩戴使用。
3. 操作人员必须严格按照操作流程进行操作,不得随意修改或省略操作步骤。
4. 操作人员必须常态自检仪器设备的正常运行情况,发现问题及时报修,不得使用故障设备进行操作。
5. 操作人员必须保持岗位整洁,工作区域干净,防止杂物堆放和易燃易爆物品的存在。
二、操作准则:1. 操作人员进入作业区域前必须进行安全检查,确保设备、管道无泄漏、无异常情况,如发现问题应立即停止操作并报告相关负责人。
2. 操作人员在进行拉料操作前必须确认氨化设备的操作温度和压力处于正常工作范围内,且无异常报警信号。
3. 操作人员在进行液体拉料时,必须确保阀门操作正常、密封良好,拉料管道无漏液情况,同时防止液体溅洒到操作人员身上。
4. 操作人员在进行粉体拉料时,必须确保搅拌设备正常运行,拉料过程中禁止随意伸手接触搅拌装置,以免发生伤害事故。
5. 操作人员在操作过程中必须严格按照标准操作程序进行,不得随意违规操作或使用不符合规定的设备和工具。
6. 操作人员在操作过程中应保持操作平稳,避免过度拉料造成设备损坏或事故发生。
7. 操作人员在操作过程中应随时关注设备运行情况和仪表数据,如发现异常应及时处理,确保设备安全运行。
8. 操作人员在操作结束后必须及时关闭设备、清理作业区域,保持岗位整洁,并将设备、工具归位存放。
9. 操作人员在操作过程中必须随时保持沟通交流,如遇到异常情况及时报告相关负责人,并按照紧急情况处理措施进行操作。
三、安全意识和应急能力要求:1. 操作人员必须具备良好的安全意识,严格遵守操作规程,不得进行违规操作和违章行为。
2. 操作人员必须熟悉紧急情况处理流程,能够迅速反应并采取正确应对措施,保证人员安全和设备安全。
合成氨的工艺流程

合成氨工艺流程氨是重要的无机化工产品之一,在国民经济中占有重要地位.除液氨可直接作为肥料外,农业上使用的氮肥,例如尿素、硝酸铵、磷酸铵、氯化铵以及各种含氮复合肥,都是以氨为原料的.合成氨是大宗化工产品之一,世界每年合成氨产量已达到1亿吨以上,其中约有80%的氨用来生产化学肥料,20%作为其它化工产品的原料.德国化学家哈伯1909年提出了工业氨合成方法,即“循环法",这是目前工业普遍采用的直接合成法.反应过程中为解决氢气和氮气合成转化率低的问题,将氨产品从合成反应后的气体中分离出来,未反应气和新鲜氢氮气混合重新参与合成反应。
合成氨反应式如下:N2+3H2≒2NH3合成氨的主要原料可分为固体原料、液体原料和气体原料。
经过近百年的发展,合成氨技术趋于成熟,形成了一大批各有特色的工艺流程,但都是由三个基本部分组成,即原料气制备过程、净化过程以及氨合成过程。
1。
合成氨的工艺流程(1)原料气制备将煤和天然气等原料制成含氢和氮的粗原料气。
对于固体原料煤和焦炭,通常采用气化的方法制取合成气;渣油可采用非催化部分氧化的方法获得合成气;对气态烃类和石脑油,工业中利用二段蒸汽转化法制取合成气。
(2)净化对粗原料气进行净化处理,除去氢气和氮气以外的杂质,主要包括变换过程、脱硫脱碳过程以及气体精制过程。
① 一氧化碳变换过程在合成氨生产中,各种方法制取的原料气都含有CO,其体积分数一般为12%~40%。
合成氨需要的两种组分是H2和N2,因此需要除去合成气中的CO。
变换反应如下:CO+H2OH→2+CO2 =—41.2kJ/mol 0298HΔ由于CO变换过程是强放热过程,必须分段进行以利于回收反应热,并控制变换段出口残余CO含量.第一步是高温变换,使大部分CO转变为CO2和H2;第二步是低温变换,将CO含量降至0.3%左右.因此,CO变换反应既是原料气制造的继续,又是净化的过程,为后续脱碳过程创造条件。
② 脱硫脱碳过程各种原料制取的粗原料气,都含有一些硫和碳的氧化物,为了防止合成氨生产过程催化剂的中毒,必须在氨合成工序前加以脱除,以天然气为原料的蒸汽转化法,第一道工序是脱硫,用以保护转化催化剂,以重油和煤为原料的部分氧化法,根据一氧化碳变换是否采用耐硫的催化剂而确定脱硫的位置。
化肥厂实习报告

15、除办公室、控制室、值班室和检修班组室外,(任何)人进入生产现场,必须戴(安全帽)。
16、“四不放过”事故处理原则:事故原因未查清不放过;责任人未受到处理不放过;群众未受到教育不放过;整改措施未落实不放过,
项目总投资近30亿元人民币,预计2012年底正式投产。项目达产后,年均销售收入为8.94亿元,年均税后利润为3.7亿元。
本项目投产后,公司将陆续启动二期和下游新产品两个新项目,力争三年内新项目落地实施。
工作地点为内蒙古自治区鄂尔多斯市准格尔旗大路工业园区。该园区位于准格尔旗东北部,是准格尔旗为推进工业化、城市化进程,于2004年高起点、高标准规划建设的集产业摆布与城市建设于一体的城市新区,控制面积230平方公里,规划“一区两基地”(市政区、煤化工基地、东工业基地),拟打造世界一流煤化工基地,建成中国一流县域城市,作为规划内的准格尔旗旗政府所在地,该园区将成为准格尔旗未来的政治、经济与文化中心。准格尔旗2009年经济综合实力在全国百强县(市)中排名第47位,是典型的依托煤炭资源发展的县域经济模式。
利用甲醇在低温下对酸性气体溶解度极大的优良特性,脱除原料气中的酸性气体。该工艺气体净化度高,选择性好,气体的脱硫和脱碳可在同一个塔内分段、选择性地进行。
天润化肥有限公司变换工序采用变换炉,合成氨原料气中均有一氧化碳,一氧化碳不是合成氨的直接原料,而且能使催化剂中毒,,因此在送往合成工序之前必须脱除,一般分两步:首先进行一氧化碳的变换,即用一氧化碳与水蒸气作用,生成氢气和一氧化碳。经变换大部分一氧化碳转化为以除去的二氧化碳,并获得氮气,。少量一氧化碳将在后继工序中除掉。
合成氨工艺

合成氨工艺————————————————————————————————作者:————————————————————————————————日期:合成氨工艺流程(1)原料气制备将煤和天然气等原料制成含氢和氮的粗原料气。
对于固体原料煤和焦炭,通常采用气化的方法制取合成气;渣油可采用非催化部分氧化的方法获得合成气;对气态烃类和石脑油,工业中利用二段蒸汽转化法制取合成气。
(2)净化对粗原料气进行净化处理,除去氢气和氮气以外的杂质,主要包括变换过程、脱硫脱碳过程以及气体精制过程。
①一氧化碳变换过程在合成氨生产中,各种方法制取的原料气都含有CO,其体积分数一般为12%~40%。
合成氨需要的两种组分是H2和N2,因此需要除去合成气中的CO。
变换反应如下:CO+H2OH→2+CO2 =-41.2kJ/mol 0298HΔ由于CO变换过程是强放热过程,必须分段进行以利于回收反应热,并控制变换段出口残余CO含量。
第一步是高温变换,使大部分CO转变为CO2和H2;第二步是低温变换,将CO含量降至0.3%左右。
因此,CO变换反应既是原料气制造的继续,又是净化的过程,为后续脱碳过程创造条件。
②脱硫脱碳过程各种原料制取的粗原料气,都含有一些硫和碳的氧化物,为了防止合成氨生产过程催化剂的中毒,必须在氨合成工序前加以脱除,以天然气为原料的蒸汽转化法,第一道工序是脱硫,用以保护转化催化剂,以重油和煤为原料的部分氧化法,根据一氧化碳变换是否采用耐硫的催化剂而确定脱硫的位置。
工业脱硫方法种类很多,通常是采用物理或化学吸收的方法,常用的有低温甲醇洗法(Rectisol)、聚乙二醇二甲醚法(Selexol)等。
粗原料气经CO变换以后,变换气中除H2外,还有CO2、CO和CH4等组分,其中以CO2含量最多。
CO2既是氨合成催化剂的毒物,又是制造尿素、碳酸氢铵等氮肥的重要原料。
因此变换气中CO2的脱除必须兼顾这两方面的要求。
一般采用溶液吸收法脱除CO2。
合成氨 工艺流程

合成氨工艺流程
《合成氨工艺流程》
合成氨是一种重要的化工原料,广泛应用于化肥、塑料、药品等行业。
它的工艺流程一直以来都备受关注,因为合成氨的生产需要高温、高压和复杂的催化反应。
下面我们来了解一下合成氨的工艺流程。
首先,合成氨的工艺流程主要分为两步:氮气和氢气的制备、氮氢气混合气的合成。
氮气一般来自空气中的分离,氢气则通常是通过蒸汽重整、乙烷裂解等方式制备。
其次,氮氢气混合气的合成是合成氨的关键步骤。
这一步通常使用哈勃-波希过程,即在高温高压下,利用铁、铁钾、铁钼等金属作为催化剂,使氢气和氮气在反应器中发生化学反应,生成合成氨。
在这个过程中,需要对反应温度、压力和催化剂进行精确控制,以确保合成氨的产率和质量。
最后,合成氨的后续处理包括冷凝、脱碳、洗涤等步骤,以去除反应器中产生的杂质和副产物,使得合成氨的纯度达到要求。
这样就得到了可供工业生产和应用的合成氨。
综上所述,《合成氨工艺流程》涉及氮气和氢气的制备、氮氢气混合气的合成和合成氨的后续处理等关键步骤,通过精确控制各项参数和操作条件,才能产生高质量的合成氨,为化工行业提供了重要的原料。
- 1、下载文档前请自行甄别文档内容的完整性,平台不提供额外的编辑、内容补充、找答案等附加服务。
- 2、"仅部分预览"的文档,不可在线预览部分如存在完整性等问题,可反馈申请退款(可完整预览的文档不适用该条件!)。
- 3、如文档侵犯您的权益,请联系客服反馈,我们会尽快为您处理(人工客服工作时间:9:00-18:30)。
1.循环机的开停机操作:
㈠正常开车
①检查曲轴箱油位油质情况应正常良好,开启氨冷阀,并调节到0.4Mpa左右。
②关闭进出口阀门,开启近路阀和放空阀。
③盘车两圈以上若无异常情况,微开进口阀,置换两次后,关闭放空阀。
④关闭进口阀,启动循环机调节好油压,带运转正常后逐渐开进口阀,并根据生产负荷大小调节近路阀。
㈡正常停车
①开启回路阀,关闭进出口阀。
②开启放空阀卸压,待压力卸完后,停循环机,关闭放空阀油冷水阀和放氨阀。
㈢紧急停车(如遇断电或严重故障时,立即按停车按钮停循环机
①迅速关闭进出口阀,开启回路阀(如停车时回路阀未完全关闭,应先关闭回路阀,再按停车按钮以防止气体倒流)
②开启放空阀卸压,关闭放氨阀油冷水阀。
㈣倒循环机要点
①按正常开机步骤启动备用机。
②逐渐开启备用机的进口阀,当出口压力与系统压力相等全开出口阀,同时开启在用机回路阀,关闭进出口阀。
按正常停车步骤停在用机。
③在倒机过程中注意两机相互配合,防止工艺波动太大。
2.氨合成的反应机理
氨合成的反应过程是典型的气固相催化反应,一般有以下步骤:
①气体反应物(H2、N2)自气体主相扩散到催化剂外表面。
②催化剂外表面的反应物绝大多数继而扩散到催化剂毛细孔的内表面。
③反应物被催化剂表面(主要内表面)活性吸附,即反应物与催化剂发生表面反应:
N2+2Fe↔2N(Fe)
H2+2Fe↔2H(Fe)
④吸附态的氢氮在表面发生反应,生成一系列中间化合物,最后形成吸附态的氨
N(Fe)+H(Fe)↔NH(Fe)+(Fe)
NH(Fe)+H(Fe)↔NH2(Fe)+(Fe)
NH2(Fe)+H(Fe)↔NH3(Fe)+(Fe)
⑤吸附态的氨(产物)在催化剂表面解析
NH3(Fe)↔NH3+(Fe)
⑥产物氨从催化剂毛细孔的内表面向孔外表面扩散
⑦产物从催化剂外表面扩散至气体主相。
以上步骤中①、⑦是外扩散过程;②、⑥为内扩散过程;③、④、⑤为化学动力学过程。
即合成氨反应速率包括扩散速率和化学反应速率。
3.合成岗位操作要点:
①触媒层温度控制
②废锅液位及水质控制
③氨冷温度调节
④循环气体中惰性气体含量控制
⑤按时排油,认真巡检
⑥防止跑气漏气。
⑦循环水水质的控制。
4.系统升温前为什么要充氨
①氨水的气相分压较低,可以降低系统中水蒸气的含量。
②氨水的冰点较低,不易结冰。
5.触媒层温度突然升高的原因及处理
原因:①补充气量突然增加或循环气量突然减小。
②气质突然好转。
③操作不当调节不及时。
④循环机跳车⑤测温表假。
处理: ①迅速开大副阀防止超温。
②联系电工迅速开备用机。
③联系仪表校对温度。
6.名词解释
①空速:单位时间内1m³体积的触媒表面所通过气体的体积数。
单位m³/m³·h
②氨净值:出塔氨含量与进塔氨含量差值。
③催化活性:物质的催化能力,是催化剂重要性质之一。
④微量:补充气体中CO2+CO≦20ppm
⑤铁比:氨合成催化剂未被还原氧化亚铁和三氧化二铁中二价铁,三价铁的比值。
7.断电停机岗位职责:
①迅速关闭放氨阀和加氨阀后放去提氢阀。
②关闭补进阀和废锅上水阀。
③关闭合成塔主副阀各冷激阀、蒸汽阀。
④正常停循环机,使其处于备用状态。
⑤注意气氨压力变化,如压力过高,联系冰机岗位。
⑥坚守岗位以便送电恢复生产。
注意事项:①注意压力和触媒层温度变化。
②注意塔壁温度变化。
8.循环机跳车原因及处理
①停电②油压低③超压超电流。
处理:①如有备用机迅速开启备用机,与调度及其他相关岗位联系。
②若无备用开大冷激阀和副阀注意触煤层温度及压力,防止超压超温等安全事故发生。
③如跳车时近路阀未关死,立即关闭近路阀。
④联系人员查明原因修复后,使其备用。
9.带氨现象原因及处理
①触煤入口温度下降,进口氨含量升高
②塔壁温度降低。
③触煤层温度下降,系统压力升高。
④冷交换热器液位高。
原因:氨分液位高。
冷交上部换热器内漏。
冷交分离器损坏或油污堵塞。
①迅速放低氨分液位,如液位计有故障,及时联系仪表处理。
②关闭塔副阀减小循环量,抑制温度下降。
③根据情况开电炉。
10.循环机工作原理:
电机→连轴器→曲轴→连杆→活塞杆→活塞在汽缸内往复运动,使气体吸进压缩排出。
11.合成工段任务:
在适宜的温度压力等条件下,借助催化剂的作用将氢氮气合成氨,然后将所得气氨冷凝分离分离出来,液氨部分送氨罐加入氨冷器蒸发为气氨,进入冷冻系统压缩、冷凝、回收;一部分由氨罐送尿素制取尿素,过剩的液氨可做产品卖出,未合成的氢氮气继续循环使用。
12.氨冷温度高的原因和处理方法:
原因:①水冷器出口温度高②负荷重,增加了氨冷负荷③氨冷液位过低或气氨压力升高,影响氨冷效率。
④液氨纯度低,含水量大。
⑤氨冷器盘管表面有油污。
处理:①提高水冷降温效率。
②维持氨冷液位后,联系冰机吸收降低气氨压力。
③增开冰机。
④安排排污。
⑤停车时热洗。
13.循环机活塞杆等主要部件断裂的原因及处理方法
原因:①部分材质或加工质量不符合要求。
②螺栓或开口处拉动脱落未及时发现。
③安装检修质量不好。
④系统阻力大使循环机出口压差大,循环机超负荷。
⑤进出口活门装反气体无回路或汽缸内有异物发生撞击,造成活塞杆断裂。
处置:①迅速切断电源,按紧急停车处理。
②如果有高压气体迅速关闭进出口阀。
③维修循环机。
④当着火或爆炸,应联系有关岗位切断与合成的气源。
14.工艺流程(文字叙述):新鲜气经过氨冷器冷却后进入补给进气油分离器,分离器后与循环气氨冷器出来的气体混合,再进入氨分离器,分离液氨后,气体进入冷交经上部换热器换热后,进入循环机加压后,进入循环汽油分,此时气体分两路,一路进入合成塔塔桶的夹层冷却塔壁,后一路气体进入热交加热后,进入合成塔反应,之后进入废锅回收热量后进入热交,之后进入冷排降温后进入冷交上部,经过分离液氨后,气体进入循环气氨冷器,经冷却后出来和补给气混合进入下个循环。
15.循环机油路流程:机身油池→粗过滤网→油泵→抽油精过滤网→油冷→曲轴中心油孔→连杆大头瓦→连杆小头衬套→十字头滑道→油池
16.合成岗位的生产特点:
17.填空:
①合成工段的任务是在适宜的温度、压力、催化剂的作用下将氢氮气合成气氨,然后将气氨冷凝、分离出来送往氨库,未合成的氢氮气继续再系统循环使用。
②氨合成反应是可逆放热和体积缩小的反应,并在触媒存在下其化学反应方程式3H2+N2→2NH3+Q。
氨合成催化剂还原反应方程式FeO+H2→Fe+H2O-Q,Fe2O3+3H2→2Fe+3H2O—Q。
③催化剂主要成分α-Fe具有尖晶石的结构,促进剂成分K2O,CaO,Mg,Al2O3,SiO2密堆积2.5-3.0kg/L.内表明积4-16m3/g.
④循环机结构有曲轴,连杆,十字头,气缸,活塞,填料函密封,传动部件。
作用提高压力克服阻力,调节触媒层温度。
⑤本岗位循环机的型号DZW-12/275-300。
功率750kw,转速300rad/min,打气量12m3/min,活塞行程320mm,电压6000v出口压力30mpa,电流86A.
⑥氨储槽压力 2.25-2.35Mpa.氢气53%-58%氨储槽容量80%(夏)85%(冬),甲烷 19-21%.进氨≦3%。