第四章拉刀的设计及应用
拉刀课件
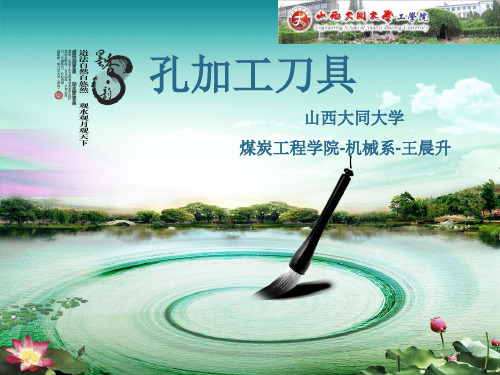
孔加工刀具
二、拉削方式 分层式、分块式和综合式 组 成 分层式是每层加工余量各由一个刀齿切除,但根据工件表面 与 最终轮廓的形成过程不同又可以分为同廓式与渐成式两种 拉 削 方 式
孔加工刀具
组 成 与 拉 削 方 式
同廓式是指各齿的廓形与加工表面的最终廓形相似,最 终廓形是由最后一个切削齿拉削形成的
孔加工刀具
拉刀设计主要内容:
工作部分和非工作部分结构参数设计;拉刀强度和拉床拉 圆 孔 力校验;绘制拉刀工作图
拉 刀 的 设 计
孔加工刀具
圆 孔 拉 刀 的 设 计
孔加工刀具
一 、工作部分设计
主要考虑生产效率和加工质量。同时要控制拉刀制造成本。
圆 孔 拉 刀 的 设 计
1. 确定拉削图形
目前我国圆孔拉刀多采用综合式拉削,并已列为专业工具 厂的产品
2. 确定拉削余量A
拉削余量应保证去除前道工序的加工误差和表面破坏层的 前提下,拉削余量尽量小的原则。 具体确定拉削余量应根据拉前孔的状态来定。 1)按经验公式计算 拉前孔为钻孔或扩孔时按公式A = 0.005Dm +(0.1 ~0.2) L mm 拉前孔为镗孔或铰孔时按公式A = 0.005Dm + (0.05 0.1) L mm ~ L─拉削长度,mm;
孔加工刀具
孔加工刀具
山西大同大学 煤炭工程学院-机械系-王晨升
孔加工刀具
(一) (二)
拉刀的种类与用途
拉刀的组成与拉削方式
教 学 内 容
(三) (四)
圆拉刀设计
矩形花键拉刀的结构特点
(五)
拉刀的合理使用和刃磨
孔加工刀具
拉削特点:
拉削过程是用拉刀进行的,它是靠拉刀的后一个(或一 组)刀齿高于前一个(或一组)刀齿,一层一层地切除余量, 以获得所需要的加工表面。 1、生产效率高 2、加工精度和表面质量高 3、拉刀耐用度高 4、拉床结构简单 5、封闭式容屑 6、加工范围广 7、拉削力大
内齿圈一次拉削成型大拉刀的设计制造技术及应用

[ ] h i L C i W 8 C u K , hu K,Y uK M.DrC i t e 5一 ai to pt eeao x l ahgnrt n so - i
f r e,r u h a dቤተ መጻሕፍቲ ባይዱf ih d b h a o t ee c p c c a g b e a s mby sr cu e oc o g n n s e us d p s tls o i h n a l s e l tu t r . i Ke wo d y r s:On —t r c i g;S cin Br a h n e i Bo a h n me e to o c i g;Ase l s mb y
( h zo erC . t. Z uh u4 2 0 , H Z uh uG a o ,Ld , h zo 1 0 0 C N)
A b t a t:Th sp p rpr s n st esr cur e in frb o c n o l pi ie h a a t r ,b ln e r a h n sr c i a e e e t h tu t e d sg o r a hig to ,o tm z ste p r mee s aa c sb o c i g
力 , 、 刀套 均采 用可换套 简式 的装配 结构 。 粗 精 分段 拉 削 装 配式
关键词 : 一次成 形
中图分 类号 : G 1 T 75
文 献标识码 : B
拉刀设计
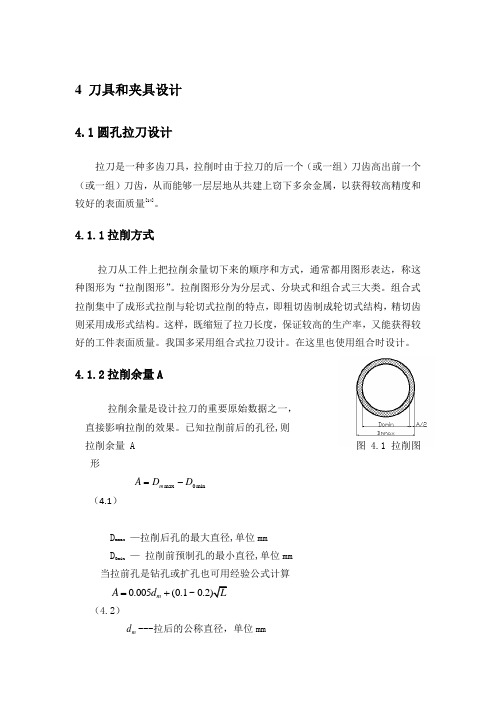
4 刀具和夹具设计4.1圆孔拉刀设计拉刀是一种多齿刀具,拉削时由于拉刀的后一个(或一组)刀齿高出前一个(或一组)刀齿,从而能够一层层地从共建上窃下多余金属,以获得较高精度和较好的表面质量[14]。
4.1.1拉削方式拉刀从工件上把拉削余量切下来的顺序和方式,通常都用图形表达,称这种图形为“拉削图形”。
拉削图形分为分层式、分块式和组合式三大类。
组合式拉削集中了成形式拉削与轮切式拉削的特点,即粗切齿制成轮切式结构,精切齿则采用成形式结构。
这样,既缩短了拉刀长度,保证较高的生产率,又能获得较好的工件表面质量。
我国多采用组合式拉刀设计。
在这里也使用组合时设计。
4.1.2拉削余量A拉削余量是设计拉刀的重要原始数据之一, 直接影响拉削的效果。
已知拉削前后的孔径,则拉削余量 A 图 4.1 拉削图形max 0minm A D D =-(4.1)D mmax —拉削后孔的最大直径,单位mm D 0min — 拉削前预制孔的最小直径,单位mm 当拉前孔是钻孔或扩孔也可用经验公式计算0.005(0.1~m A d =+(4.2)m d ---拉后的公称直径,单位mmL -- 拉削长度,单位mm查表A=0.7,所以扩孔达到D=41.3mm4.1.3拉刀材料拉刀材料常用W6Mo5CrV2高速工具钢整体制造,一般不焊接柄部。
也有整体硬质合金作为环齿,经过精磨后套装于9SiCr 或40Cr 刚作的刀体上。
4.1.4齿升量成形式结构的拉刀,其齿升量是指相邻两个刀齿高度之差;轮切式结构拉刀是指相邻两组刀齿高度之差。
圆孔拉刀齿升量大小对拉削过程和拉刀寿命有很大的影响。
齿升量越大,切削厚度越大,拉削长度越短,拉削生产率越高。
但齿升量过大,拉削力越大,拉刀使用寿命越短,加工表面质量降低。
齿升量不能太小,不然难以切下很薄的金属层而造成滑行和挤压现象,反而加剧大刀齿的磨损。
粗切齿切去整个拉削余量的80%左右,每个齿升量相等。
为了使拉削过程平稳和提高加工表面质量,齿升量应有粗切齿经过渡齿递减到精切齿。
拉刀课件

特点:分块式拉削时,工件的每层金属都由一组刀齿切除,一组中的每 个刀齿仅切除该层金属的一部分,因此,切削厚度大,切削宽度小,刀 齿数量可减少,拉刀长度可缩短,效率较高,表面粗糙度较大。
分块式又称为轮切式,可以用三个刀齿为一组,交错排列,分别切去 同一层金属的一部分,可以加大切削厚度,提高刀具使用寿命。
性。
孔加工刀具
二、拉削方式 组 分层式、分块式和综合式 成 分层式是每层加工余量各由一个刀齿切除,但根据工件表面 与 最终轮廓的形成过程不同又可以分为同廓式与渐成式两种 拉 削 方 式
孔加工刀具
组 同廓式是指各齿的廓形与加工表面的最终廓形相似,最
成 与
终廓形是由最后一个切削齿拉削形成的
拉
削
方
式
孔加工刀具
孔加工刀具
孔加工刀具
山西大同大学 煤炭工程学院-机械系-王晨升
孔加工刀具
(一) (二)
拉刀的种类与用途 拉刀的组成与拉削方式
教
(三)
圆拉刀设计
学
内
(四) 矩形花键拉刀的结构特点
容
(五) 拉刀的合理使用和刃磨
孔加工刀具
拉削特点:
拉削过程是用拉刀进行的,它是靠拉刀的后一个(或一组) 刀齿高于前一个(或一组)刀齿,一层一层地切除余量,以获 得所需要的加工表面。 1、生产效率高 2、加工精度和表面质量高 3、拉刀耐用度高 4、拉床结构简单 5、封闭式容屑 6、加工范围广 7、拉削力大
式
孔加工刀具
组 渐成式是指加工表面 成 最终廓形是又各齿拉 与 削后衔接形成的。即 拉 由各刀齿的副切削刃 削 逐渐切成 方 式
拉刀工作原理
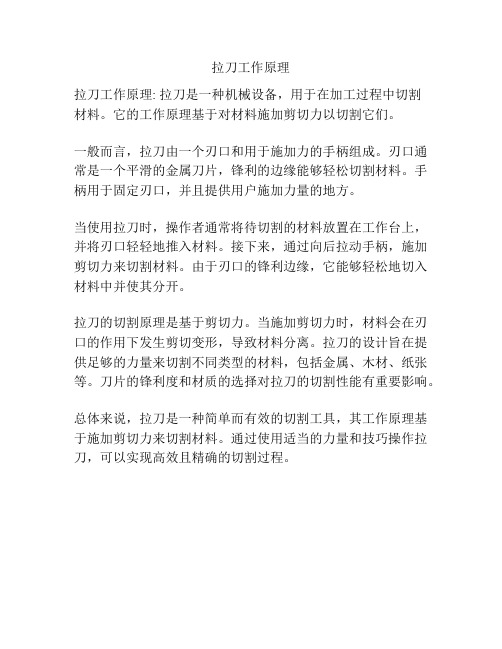
拉刀工作原理
拉刀工作原理: 拉刀是一种机械设备,用于在加工过程中切割
材料。
它的工作原理基于对材料施加剪切力以切割它们。
一般而言,拉刀由一个刃口和用于施加力的手柄组成。
刃口通常是一个平滑的金属刀片,锋利的边缘能够轻松切割材料。
手柄用于固定刃口,并且提供用户施加力量的地方。
当使用拉刀时,操作者通常将待切割的材料放置在工作台上,并将刃口轻轻地推入材料。
接下来,通过向后拉动手柄,施加剪切力来切割材料。
由于刃口的锋利边缘,它能够轻松地切入材料中并使其分开。
拉刀的切割原理是基于剪切力。
当施加剪切力时,材料会在刃口的作用下发生剪切变形,导致材料分离。
拉刀的设计旨在提供足够的力量来切割不同类型的材料,包括金属、木材、纸张等。
刀片的锋利度和材质的选择对拉刀的切割性能有重要影响。
总体来说,拉刀是一种简单而有效的切割工具,其工作原理基于施加剪切力来切割材料。
通过使用适当的力量和技巧操作拉刀,可以实现高效且精确的切割过程。
拉刀设计

复杂刀具设计
拉刀容屑槽的形状和尺寸可参阅有关资料。 根据选定的齿距p,即可查出容屑槽的各尺寸参数。 容屑槽的尺寸必须在对其容屑空间进行校验后才能最后确定。 为了保证刀齿容屑槽有足够大的容屑空间,又因切屑在容屑 槽中卷曲不紧密,故容屑槽的有效容积 V槽 必须大于切屑的 体积 V屑。它们在法平面内的比值称为容屑槽的容屑系数 K
l切削部=z粗 p+z过 p过+z精 p精
复杂刀具设计
二、校准齿 校准齿没有齿升量,只起校准和修光孔的作用,它们均不开分屑槽 1.前角与后角 (1)前角γog 由于校准齿不起切削作用, γog可取0º ~5º ,但为了制造方 便,也可取与切削齿相同的前角。 (2)后角 αog和刃带宽度b α1g 为了使拉刀重磨后直径变化小,延长拉刀使用寿命,校准齿 的后角比切削齿取得小些,一般取αog=30’~ 20º30’。 在校准齿上后面的刃带bα1g做得比切削齿的刃带宽得多。但 根据生产经验,刃带过宽易使金属粘附在刀齿顶部(尤其是 对韧性大的钢料),故近年来刃带宽度偏于取得较小。
复杂刀具设计
5)拉削的加工范围广。拉削可加工内表面,也可加工外表 面。但盲孔或表面有挡碍的工件不能加工。 6)切削条件差。拉削属于封闭式切削,排屑困难,因此容 屑、冷却和润滑都受到很大影响。 7)拉刀结构复杂,制造成本较高。
根据拉削上述特点,故在成批和大量生产中广泛使用。 在加工零件要求有一定精度的小批生产,如花键孔、键 槽等也都采用拉削加工。在现代化的自动线上,拉削工 艺也得到了应用。
复杂刀具设计
二、拉刀切削部分要素
复杂刀具设计
1.几何角度
2.结构参数
复杂刀具设计
第三节 拉削方式(图形)
复杂刀具设计
拉削方式是指用拉刀逐齿把加工余量从工件表面切下来 的方式,它决定拉削时每个刀齿切削截面形状,因此又 称拉削方式为拉削图形。
第四章拉刀的设计及应用
2、齿升量的选取
• 齿升量 拉刀两相邻刀齿在半径方向上的尺寸差称 为拉刀的齿升量。齿升量也是拉刀每齿的切削厚 度和进给量,拉刀齿升量的大小直接影响着拉削 表面的质量、拉削力和拉刀的结构,是拉刀的最 重要的参数之一。齿升量的数值通常根据被加工 材料的性质、拉刀的类型、被拉削工件表面的质 量和精度要求等因素而确定,一般情况下拉刀的 齿升量不超过0.15,若有被拉削表面粗糙度要求 较小、被加工材料的加工性能差、用于高速拉削 的拉刀、加工刚性差的零件(薄壁和软金属)、 小截面低强度的拉刀等情况,齿升量应取小一些。
图5 拉刀切削部份 的主要切削参数
三、拉削方式
• (1)分层式拉(也称为成形式拉削) • 特点:刀齿的刃形与被加工表面相同,它们一层层
地切下加工余量,最后由拉刀的最后一个刀齿和校 准齿切出工件的最终尺寸和表面。这种方式可获得 较高的表面质量,但拉刀长度较长,生产率较低。
图6 成形式拉削图 形
三、拉削方式
• 外拉刀用于加工各种开放的外表面,如平面、成型表面、 槽纹、汽轮机中的复杂榫槽和榫头以代替这些零件的铣、 刨、磨等加工,特别适用与汽车、摩托车、拖拉机等大批 量生产中的某些零件表面。
• 拉刀按机构分可分为整体式和组合式(装配式)两大类, 中小规格的内拉刀都做成整体式,大规格的内拉刀和大部 分外拉刀多做成组合式。
• (2)分块式拉削(也称为轮切式拉削) 将加工余量分为若干层,每层金属不是由一个刀
齿切去,而是由几个刀齿分段切除,每个刀齿切去 该层金属中的相互间隔的几块金属。
优点是切屑窄而厚,在同一拉削余量下所需的刀 齿总数较分层式少,故拉刀长度大大缩短,生产率 也大大提高。这种方式还可用来加工带有硬皮的铸 件和锻件。其缺点是拉刀结构复杂,加工表面质量 较差。
拉 刀-机械制造
3 . 拉削特点
拉削加工与其他金属切削加工方法相比较,具有以下主要特点: 1 生产率高。虽然拉削速度较低,一般为0.04~0.13 m/s(约2~8
m/min),但拉刀同时工作的齿数多,切削刃长,且一次行程就能够完 成粗、半精及精加工,所以生产率高。
切齿、过渡齿和精切齿组成。
6 校准齿 校准齿是几个尺寸、形状相同,起校准及储备作用的刀齿。它可以
提高工件的加工精度和降低表面粗糙度,还可作为精切齿的后备齿。
7 后导部 后导部是保证拉刀的最后刀齿正确切离工件的导向部分,可防止拉
刀因工件下垂而损坏已加工表面或刀齿。
8 后柄 后柄是拉刀后端用于夹持或支承的柄部。若在自动拉床上拉削,则
2)颈部 颈部是前柄与过渡锥之间的连接部分,也是打烙拉刀标记(拉刀材
料、尺寸、规格等)的部位。
3)过渡锥 过渡锥是引导拉刀前导部进入工件预加工孔的过渡部分。
4)前导部 前导部是引导拉刀切削齿正确地进入工件待加工表面的部分,并检
查工件预加工的孔径是否过小,以免拉刀第一个刀齿因负荷太大而损坏。
5 切削齿 切削齿担负全部切削工作,可切除工件上全部的加工余量。它由粗
1.3
—
0.5 0.6 0.7
1.5
—
0.6 0.6 0.7
1.6
—
—
0.7 0.8
>80 ~120
— — — 0.7 0.7 0.8 0.8
2)齿升量 拉刀的齿升量是前后相邻两刀齿(或齿组)的高度差或半径差,
它等于切削厚度,常用符号 表示,单位为mm。 粗切齿的齿升量 是根据工件材料、拉刀类型来选取的,具体
拉刀课程设计
直径d6=护送托架衬套孔径 3 拉刀总长度L0
拉刀直径d0 拉刀总长度L0
12~15 >15~20 >20~25
600
800
1000
>25~ 30
1200
>30~50 >50 1300 1600
三、拉刀强度及拉床拉力校验
1 拉削力 综合式圆孔拉刀的最大拉削力:
• 16. 中心孔
• 两端选用带护准中心孔
• d=2 d1= 6.3 t1 = 2.54 t =2
• 17. 材料与热处理硬度
• 材料:W6Mo5CrV2
•
刀齿与后导部 63~66HRC
•
前导部 60~66HRC
•
柄部 40~52HRC
• 18.技术条件
• 参考国标确定。(GB3831-83
JB/T6457-92 )
•
= 30.6 kN
• FQ = 100×0.75 kN =75 kN
•
Fc< FQ
• 检验拉刀强度: σ< [σ]
•
[σ] =350 MPa
•
σ= Fc / Amin
•
Amin =π(Dz1-2h)2/4 = 3.1416(19-8)2/4= 942 mm
•
σ = 30615 N/94 Mpa =325 Mpa < 350 MPa
• 10. 分屑槽尺寸
• 弧形槽:n=6、R=25
• 角度槽:n=8、bn =7、ω=90°
• 槽底后角:αn =5°
• 11.检验
• 检验拉削力:Fc< FQ
•
Fc = Fc’ × bD × Ze × k
第四章拉刀设计..
15
2)渐成式: 如图8-31所示,图中工件最后要求是方孔, 拉刀刀齿与被加工表面形状不同,被加工工件表面形状 和尺寸是由各刀齿的副刃所切成。这时拉刀可制成简单 的直线形或弧形。
它的优点是,复杂形状的 工件,拉刀制造却不太复 杂。 缺点是在工件已加工表面 上可能出现副切削刃的交 接痕迹,因此被加工表面 较粗糙。
第二节
拉刀的结构
拉刀的类型不同,其结构上虽各有特点,但他们的组 成部分仍有共同之处。下面以圆孔拉刀为例介绍其组 成部分。如图8--28所示。
10
圆孔拉刀由头部、 颈部、过渡锥部、 前导部、切削部、 校准部、后导部及 尾部组成,其各部 分功用如下:
头部——用于将拉刀装夹在拉床的夹头中以传送运动 和拉力。 颈部——用于连接头部与刀体,一般在颈部上刻印拉刀的 标记。一般颈部和头部的尺寸较小,如果拉刀强度不够, 希望在头部或颈部折断,这样拉刀的修复较容易。 过渡锥部——使前导部能顺利进入初孔(工件上予先加工 的孔),起对准中心的作用。
26
齿距可按下列经验公式计算:
其中,1.25~1.5用于分层拉削,1.5~1.9用于轮式拉削 式中,L为拉削长度。
精切齿和校准齿的齿距应适当减小,约为粗切齿的 0.6~0.9倍。
同时参加切削工作的拉刀齿数ze可用下式计算:
ze =L/p+1
注意:ze不宜少于2~3个,否则拉削工作就不平稳, 可能发生振动,并将降低加工质量。一般应使ze为 4~5个。最多不要超过8个.
拉削余量一定时,齿升量增加,刀齿的齿数可减少,拉刀长 度可短些,不仅使拉刀制造容易,而且可提高拉削生产率; 但齿升量增加,拉削力增加,拉刀耐用度和加工质量将受到 不良影响。因此,齿升量的确定必须考虑到拉刀强度、机床 拉力以及工件表面质量等要求。
- 1、下载文档前请自行甄别文档内容的完整性,平台不提供额外的编辑、内容补充、找答案等附加服务。
- 2、"仅部分预览"的文档,不可在线预览部分如存在完整性等问题,可反馈申请退款(可完整预览的文档不适用该条件!)。
- 3、如文档侵犯您的权益,请联系客服反馈,我们会尽快为您处理(人工客服工作时间:9:00-18:30)。
3、拉削速度的选取
• 拉削速度一般在1~18m/min。当拉刀齿升 量大时拉削速度应取小一些,拉削较硬材 料(280~320HB)或较软材料硬度<170HB 时,拉削速度应相应降低。拉削硬度大于 320HB时,拉削速度更应该降低。拉削粗 糙度低于Ra1.6时,拉削速度应控制在 2m/min以下。
4、拉削加工中常见缺陷产生的原因及消除方法 •
• • • • • •
三、拉刀的合理使用
• 1、对被拉削工件的要求
• •
•
2、拉削时注意事项 3、拉削速度的选取
4、拉削加工中常见缺陷产生的原因及消除 方法
1、对被拉削工件的要求
• 拉削时的加工表面质量和尺寸精度与拉削前工件的工艺准 备状况有着密切的关系,对内孔的拉削来说工件预制孔不 仅是待加工表面而且也是定位基准,它的尺寸和几何精度, 与工件基准端的垂直度,以及工件材料的切削加工性能等, 对拉削的质量和拉削过程的正常进行都起着重要作用。 拉削前的工件应满足下列要求 1) 拉前的预制孔,应进行半精加工; 2) 拉削时的基面必须平整光滑,如果预制孔与定位基面精 度较差,则应采用球面支承夹具; 3) 对于较短的工件。其长度小于拉刀两个齿距时,可用夹 具把几个工件紧固在一起拉削; 4) 钢件应经过正火或退火及调制处理,其硬度在 180~240HB时拉削性能最好,粗糙度最容易达到,拉刀耐 用度也较高。因此,应尽可能将被加工工件预先热处理在 这一范围;
图5 拉刀切削部份 的主要切削参数
三、拉削方式
• (1)分层式拉(也称为成形式拉削) • 特点:刀齿的刃形与被加工表面相同,它们一层层 地切下加工余量,最后由拉刀的最后一个刀齿和校 准齿切出工件的最终尺寸和表面。这种方式可获得 较高的表面质量,但拉刀长度较长,生产率较低。
图6 成形式拉削图 形
三、拉削方式
• • •
5、容屑槽的形状与尺寸
• 拉刀的容屑槽应能保证容纳切下的全部切屑和切屑的 自由卷曲,并应保证刀齿有足够的强度和一定的重磨 次数。常用的容屑槽形状有直线齿背型和曲线齿背型 两种,直线齿背型易于制造,多用于拉削脆性材料, 曲线齿背有利于切屑的卷曲和拉削结束后切屑从容屑 槽中落下来,适用于拉削韧性材料。 容屑槽各部分尺寸与齿距t的关系如下: h=(0.38~0.45)t g=(0.3~0.35)t R=(0.65~0.7)t R=0.5h 在设计和生产中应遵循尽量减小容屑槽规格尺寸,又 能满足生产需要的原则。
二、 拉刀的结构(主要组成部份)
• 头部--与机床连接,传递运动和拉力。
• 颈部--头部和过渡锥连接部分,也是打标记的地方 • 过渡锥部分--起引导作用,使拉刀容易进入工件的预制孔。 • 前导部分--引导拉刀平稳地、不发生歪斜地过渡到切削部分。 • 切削部分--担任全部加工余量的切除工作。它由粗切齿、过渡齿 和精切齿组成。 • 校准部分--最后几个无齿升量和分屑槽的刀齿,起修光、校准作 用。以提高孔的加工精度和表面质量,并可作为精切齿的后备齿。 • 后导部分--用来保持拉刀最后几个刀齿的正确位置,防止拉刀在 即将离开工件时,因工件下垂而损坏已加工表面质量及刀齿。 • 尾部--当拉刀长而重时,可以用托架支托拉刀的尾部,防止拉力 因自重而下垂,一般重量较轻的拉刀则不需要尾部。
4、容屑系数K和容屑槽深度h的选取
• • • • 在拉削中,拉刀每一刀齿所切下的切屑都 必须完全纳在容屑槽内。 容屑系数应满足以下条件 Ac/Aj≥K K>1 式中 Ac——容屑槽的有效面积 Ac=π*h²/4 Aj——切削面积 Aj=Sz*L 所以 π*h²/4*Sz*L≥K 则 h≥1.13(K*Sz*L)1/2
3、齿距t的选取
• • 齿距t及同时工作的齿数Zi
齿距是拉刀两相邻刀齿间的轴向距离,其大小一 般由工件的被拉削长度确定。拉削一般材料时齿距 t=(1.25~1.5)L*1/2(L——工件的被拉削长度) 短工件和脆性材料选小值,长工件或韧性材料选大 值。拉削高温合金材料时齿距为t=(1.9~2.0) *L1/2同时工作齿数Zi=L/t+1(取整数)。由此可知, 拉刀的齿距越小,拉刀的工作齿数就越多,工作过 程就越平稳,拉削表面粗糙度就越小,但相应会增 加拉削力,减小容屑空间,而拉刀齿距太大,则会 减小同时工作齿数,使拉削过程不平稳。所以在设 计时拉刀的同时工作齿数一般取3≤Zi≤8,齿距和同 时工作齿数时相互联系的必须综合考虑拉削平稳性, 拉削力,拉削长度,容屑空间和拉刀强度等情况。
•
• • •
2、拉削时注意事项
•
• • • •
•
• •
1)拉削过程中,冷却润滑液不仅应有力的喷在刀齿上,最好在 工件外表面也要有足够的冷却。工件表面粗糙度要求较低时,建 议采用浓度较高的乳化液; 2)对于长而重的拉刀,从拉削开始到行程一半左右为止都应有 托架扶托进行拉削。当拉刀细而长有不够扶托条件时,可用手扶 托拉刀尾部,可减小摆尾现象; 3)在拉削即将结束时,要防止工件因自重下垂; 4)拉削过程中,要经常观注工件拉削表面质量及拉刀磨损情况。 一般来说,工件粗糙度较高时,拉刀振动和拉削异声加剧,都标 志着拉刀已经磨钝,需要进行修磨; 5)拉完一个工件后,应用铜丝刷顺着切削刃方向将附在容屑槽 内的切屑刷去,严禁用钢丝刷,也不能用棉纱揩擦,以免棉纱纤 维钩缠在刀齿上。当刀齿上粘附着的切屑用铜丝刷很难去除时, 可用油石轻轻打磨掉,但要注意保持刀齿原先的几何形状和锋口; 6)拉削过程中,要经常注意拉床上的压力表指针的变化情况, 若发现指针直线上升时应停车检查,防止损坏拉刀; 7)由于拉床拉力不够或工件偏斜等原因,造成拉床发生沉重负 荷的响声,甚至溜板停止移动,应立即停车检查; 8)拉刀用毕,应垂直悬挂,严防拉刀刀齿与金属物相碰(包括 与其他拉刀相碰)。
• (2)分块式拉削(也称为轮切式拉削) 将加工余量分为若干层,每层金属不是由一个刀 齿切去,而是由几个刀齿分段切除,每个刀齿切去 该层金属中的相互间隔的几块金属。 优点是切屑窄而厚,在同一拉削余量下所需的刀 齿总数较分层式少,故拉刀长度大大缩短,生产率 也大大提高。这种方式还可用来加工带有硬皮的铸 件和锻件。其缺点是拉刀结构复杂,加工表面质量 较差。 (2)综合式拉削 集中了分层式与分块式拉削的优点,拉刀的粗切 齿及过渡齿制成轮切式结构(分块拉削),精切齿 则采用分层式结构,分层拉削,最终完成零件表面 的加工。
• • • • •
1、对被拉削工件的要求
• 5) 拉削前预制孔必须保证一定的几何精度(如同 轴度、垂直度、尺寸精度为H8、H9~H11,粗糙度 Ra6.3~3.2)拉刀前导部分应能完全穿入孔内,穿 不进去或只穿过一半时是不能进行拉削的; • 6) 拉削前预制孔两端应进行倒角,以免毛刺影响 拉刀的通过及工件的定位; • 7) 拉刀使用前必须将防锈油用汽油洗净,并检查 刀齿是否锋利,刀齿有无碰伤,崩刃或其他损伤, 绝对不能用刀齿已损伤的拉刀进行拉削; • 8) 孔加工拉刀的拉削长度是有严格规定的,不能 任意超过拉刀规定的范围,否则会造成拉刀强度不 够而崩刃或折断,但拉削长度也不宜过短,要保证 拉削时同时工作的齿数不少于三个,以保证拉削过 程的平稳;
(1)拉刀结构图
头部
颈部
过渡锥部
前导部
切削部
校准部
后导部
尾部
•
图4
(2) 刀齿几何参数
• 齿升量αf--前、后两刀齿(或 齿组)半径或高度之差。粗切齿 af=0.02~0.20mm,精切齿 af=0.005~0.015mm。 齿距p--相邻两刀齿之间的轴 向距离。齿距根据孔的拉削长度 计算,拉刀同时工作齿数可取 3~8个。 前角γo--前角根据工件材料选 择。一般高速钢拉刀切削齿的前 角γo=5°~20°,硬质合金拉刀 的前角γo=0°~1.0°,校准齿 前角γog与切削齿前角相同。 刃带ba1--为了增加拉刀的重 磨次数,提高切削过程的平稳性 和便于制造时控制刀齿的直径, 在刀齿后刀面上留有一后角为 0°的棱边。
•
图2拉刀工作示意图
图3 几种常用拉刀的结构型式
键槽拉刀
矩型花键拉刀
圆孔拉刀 渐开线花键拉刀
平面拉刀
一、 拉刀的种类和用途
• 内拉刀用于加工各种廓形的内孔表面,其拉刀名称一般都 有被加工孔的形状来确定,如圆孔拉刀、四、六方拉刀、 键槽拉刀、花键拉刀等。内拉刀还可以加工螺旋内花键, 内齿轮。内拉刀可加工的孔径通常为10~120mm,在特殊 情况下可加工到5~400mm,拉削的槽宽一般为3~100mm, 孔的长度一般不超过直径的3倍,特殊情况下可达到2m。 • 外拉刀用于加工各种开放的外表面,如平面、成型表面、 槽纹、汽轮机中的复杂榫槽和榫头以代替这些零件的铣、 刨、磨等加工,特别适用与汽车、摩托车、拖拉机等大批 量生产中的某些零件表面。 • 拉刀按机构分可分为整体式和组合式(装配式)两大类, 中小规格的内拉刀都做成整体式,大规格的内拉刀和大部 分外拉刀多做成组合式。 • 根据拉刀刀齿材料又分为高速钢拉刀和硬质合金拉刀。 • 根据拉刀工作时的受力情况又分为拉刀和推刀。
三. 拉刀主要切削要素选取
• 1、前角γ、后角α的选取 • 2、齿升量Sz的选取 • 3、齿距t的选取 • 4、容屑系数K和容屑槽深度h的选取
• 5、容屑槽的形状与尺寸
1、前角γ、后角α 的选取
• 前角γ 拉刀的前角主要根据被拉削材料的性能选 取。当拉削韧性材料时,应选用较大的前角,拉 削脆性材料时,应选用较小的前角。 后角α 拉刀的后角是根据拉刀的类型和工件所需 的加工精度而确定的。增大后角可以减少拉刀后 刀面与工件的摩擦,但在重磨时会很快减小拉刀 的尺寸,使其丧失精度。通常拉削IT7~IT8级精 度的圆孔拉刀、花键拉刀、四六方拉刀以及其他 类型的拉刀切削齿后角为2°~3°30′,拉削IT9精 度和更低精度的上述拉刀切削齿后角为3°~4°, 单面有齿的槽拉刀、平面拉刀和外拉刀切削齿后 角为4°~7°,校准齿的后角为0°30′~1°30′。
一、概述