聚烯烃类塑料注塑成型故障得成因及对策
塑料注塑成型不良现象的原因与处理办法
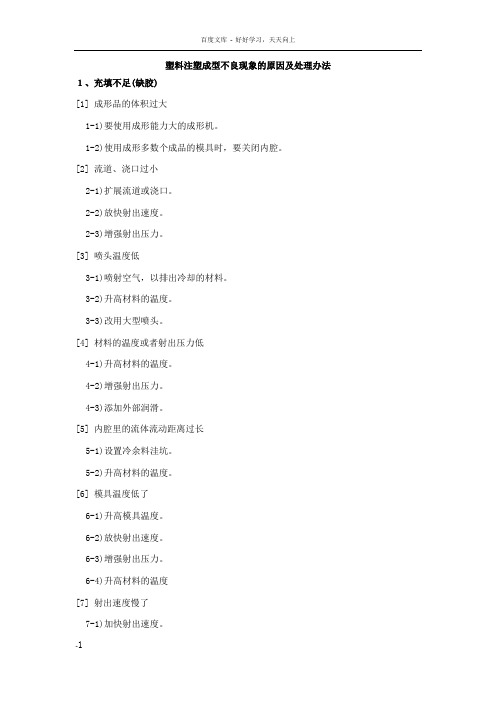
塑料注塑成型不良现象的原因及处理办法1、充填不足(缺胶)[1] 成形品的体积过大1-1)要使用成形能力大的成形机。
1-2)使用成形多数个成品的模具时,要关闭内腔。
[2] 流道、浇口过小2-1)扩展流道或浇口。
2-2)放快射出速度。
2-3)增强射出压力。
[3] 喷头温度低3-1)喷射空气,以排出冷却的材料。
3-2)升高材料的温度。
3-3)改用大型喷头。
[4] 材料的温度或者射出压力低4-1)升高材料的温度。
4-2)增强射出压力。
4-3)添加外部润滑。
[5] 内腔里的流体流动距离过长5-1)设置冷余料洼坑。
5-2)升高材料的温度。
[6] 模具温度低了6-1)升高模具温度。
6-2)放快射出速度。
6-3)增强射出压力。
6-4)升高材料的温度[7] 射出速度慢了7-1)加快射出速度。
7-2)升高材料的温度[8] 材料的供给量过少8-1)如属螺桨式装置,增加增塑量;而采用柱塞方式时,则增加从料斗落下的数量。
8-2)减少外部润滑,改进螺桨的加工条件[9] 排气不良9-1)放慢射出速度。
9-2)将填充不良的位置改为镶件结构或在模具上加设排气槽。
9-3)改变胶口的位置9-4)改变成形品的厚度2、溢料(飞边)[1]锁模力不足1-1)加强锁模力。
1-2)降低射出压力。
1-3)改用大型成形机。
1-4)确实调整好连杆。
[2]模具不好2-1)补修导推杆或导钉梢的部位2-2)修正模具安装板。
增加支撑柱。
2-3)使用轨距联杆的强度足够的成机2-4)确实做好模具面的贴合。
[3]模具面的杂质3-1)除去杂物[4]成形品的投影面积过大4-1)使用大型成形机。
[5]材料的温度过高5-1)降低材料的温度。
5-2)放慢射出速度。
[6]材料供给量过剩6-1)调整好供给量。
[7]射出压力高7-1)降低射出压力。
7-2)降低材料的温度。
3气孔在材料为充分干燥时,是挥发物或空气所致;大多时候发生在产品胶厚的位置,实际是材料的收缩引起的真空气泡[1] 流道或浇口过小1-1)将流道或浇口扩展。
注塑缺陷原因分析与解决方案
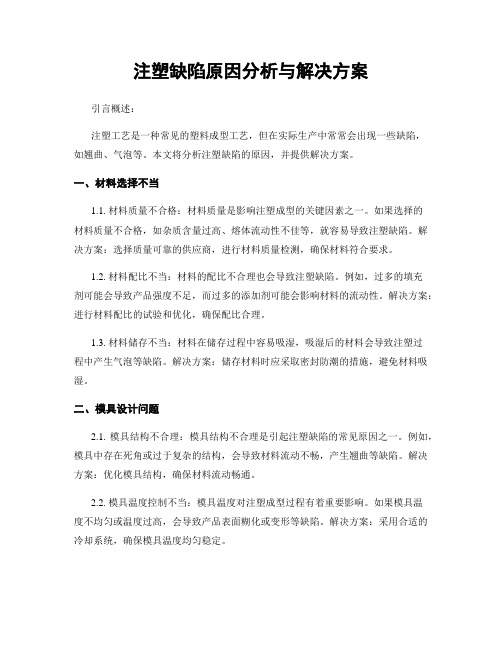
注塑缺陷原因分析与解决方案引言概述:注塑工艺是一种常见的塑料成型工艺,但在实际生产中常常会出现一些缺陷,如翘曲、气泡等。
本文将分析注塑缺陷的原因,并提供解决方案。
一、材料选择不当1.1. 材料质量不合格:材料质量是影响注塑成型的关键因素之一。
如果选择的材料质量不合格,如杂质含量过高、熔体流动性不佳等,就容易导致注塑缺陷。
解决方案:选择质量可靠的供应商,进行材料质量检测,确保材料符合要求。
1.2. 材料配比不当:材料的配比不合理也会导致注塑缺陷。
例如,过多的填充剂可能会导致产品强度不足,而过多的添加剂可能会影响材料的流动性。
解决方案:进行材料配比的试验和优化,确保配比合理。
1.3. 材料储存不当:材料在储存过程中容易吸湿,吸湿后的材料会导致注塑过程中产生气泡等缺陷。
解决方案:储存材料时应采取密封防潮的措施,避免材料吸湿。
二、模具设计问题2.1. 模具结构不合理:模具结构不合理是引起注塑缺陷的常见原因之一。
例如,模具中存在死角或过于复杂的结构,会导致材料流动不畅,产生翘曲等缺陷。
解决方案:优化模具结构,确保材料流动畅通。
2.2. 模具温度控制不当:模具温度对注塑成型过程有着重要影响。
如果模具温度不均匀或温度过高,会导致产品表面糊化或变形等缺陷。
解决方案:采用合适的冷却系统,确保模具温度均匀稳定。
2.3. 模具磨损严重:模具长时间使用后会出现磨损,磨损严重的模具会导致产品尺寸不准确或表面粗糙等缺陷。
解决方案:定期检查和维护模具,及时更换磨损严重的模具部件。
三、注塑工艺参数设置不当3.1. 注射压力过高或过低:注射压力是影响注塑成型的关键参数之一。
如果注射压力过高,会导致产品变形或开裂,而注射压力过低则会导致产品表面光洁度不高。
解决方案:根据产品要求和材料特性,合理设置注射压力。
3.2. 注射速度不合理:注射速度对产品的充填和冷却过程有着重要影响。
如果注射速度过快,会导致产品内部产生气泡或短射,而注射速度过慢则会导致产品表面瑕疵。
注塑缺陷原因分析与解决方案
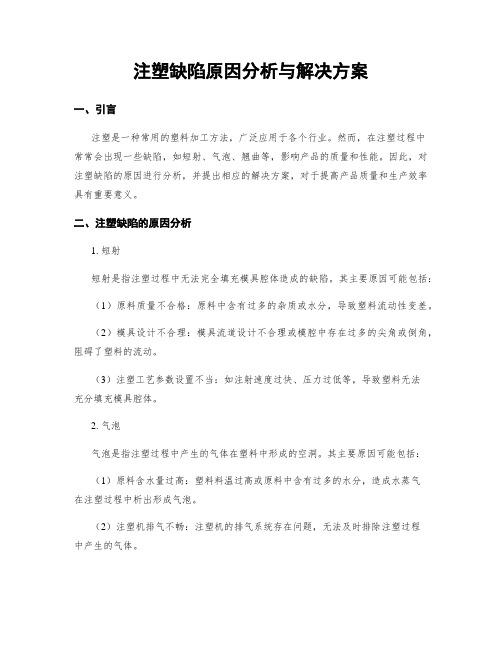
注塑缺陷原因分析与解决方案一、引言注塑是一种常用的塑料加工方法,广泛应用于各个行业。
然而,在注塑过程中常常会出现一些缺陷,如短射、气泡、翘曲等,影响产品的质量和性能。
因此,对注塑缺陷的原因进行分析,并提出相应的解决方案,对于提高产品质量和生产效率具有重要意义。
二、注塑缺陷的原因分析1. 短射短射是指注塑过程中无法完全填充模具腔体造成的缺陷。
其主要原因可能包括:(1)原料质量不合格:原料中含有过多的杂质或水分,导致塑料流动性变差。
(2)模具设计不合理:模具流道设计不合理或模腔中存在过多的尖角或倒角,阻碍了塑料的流动。
(3)注塑工艺参数设置不当:如注射速度过快、压力过低等,导致塑料无法充分填充模具腔体。
2. 气泡气泡是指注塑过程中产生的气体在塑料中形成的空洞。
其主要原因可能包括:(1)原料含水量过高:塑料料温过高或原料中含有过多的水分,造成水蒸气在注塑过程中析出形成气泡。
(2)注塑机排气不畅:注塑机的排气系统存在问题,无法及时排除注塑过程中产生的气体。
(3)注塑工艺参数设置不当:如注射速度过快、压力过高等,造成塑料内部气体无法顺利排出。
3. 翘曲翘曲是指注塑制品在冷却后出现变形的现象。
其主要原因可能包括:(1)模具温度不均匀:模具温度不均匀导致注塑制品冷却不均匀,从而引起翘曲。
(2)注塑过程中的应力积累:注塑过程中,塑料在注射后会受到冷却和收缩的影响,如果释放不及时,会导致应力积累引起翘曲。
(3)注塑工艺参数设置不当:如注射速度过快、冷却时间过短等,造成塑料冷却不充分,引起翘曲。
三、注塑缺陷的解决方案1. 短射的解决方案(1)优化原料质量:选择质量合格的原料,避免杂质和水分的存在。
(2)优化模具设计:合理设计模具流道,避免尖角和倒角的存在,保证塑料的顺畅流动。
(3)优化注塑工艺参数:合理设置注射速度和压力,确保塑料能够充分填充模具腔体。
2. 气泡的解决方案(1)控制原料含水量:确保塑料料温适宜,原料中的水分含量符合要求。
注塑成型常见不良现象及处理措施

注塑成型常见不良现象及处理措施注塑成型常见的不良现象有以下几种:
1. 短射:指注塑料进模型中未充满模腔,导致产品缺陷。
处理措施:增加注射
压力、延长注射时间、增加料缸温度、增加模具温度、增加模具出料口直径等。
2. 气泡:指产品表面或者内部浮现气泡,影响产品质量。
处理措施:增加注射
压力、延长注射时间、增加模具温度、增加料缸温度、增加模具出料口直径、增加模具排气孔等。
3. 热熔线:指产品表面浮现细小的线状缺陷,通常是由于注射速度过快导致的。
处理措施:减小注射速度、增加模具温度、增加模具出料口直径等。
4. 毛刺:指产品表面浮现细小的凸起,通常是由于模具设计不合理或者模具磨
损导致的。
处理措施:修复模具、修改模具设计、增加模具温度、增加模具出料口直径等。
5. 缩水:指产品尺寸缩小,通常是由于注射压力不足或者冷却时间不足导致的。
处理措施:增加注射压力、延长冷却时间、增加模具温度等。
6. 毛洞:指产品表面或者内部浮现凹陷,通常是由于注射速度过快或者模具设
计不合理导致的。
处理措施:减小注射速度、修改模具设计、增加模具温度等。
处理不良现象的关键是找到问题的根源,然后针对性地采取相应的处理措施。
同时,注塑成型过程中的参数控制和模具维护也是关键的因素,需要进行定期检查和调整。
塑料注塑成型故障排除

塑料注塑成型故障排除注塑成型是一种广泛应用于各种产品制造过程中的一种技术,它可以将塑料材料通过高温高压下注于模具中,并在冷却后保持原来的形状,形成各种各样的塑料制品。
但是在注塑成型过程中也会出现各种故障,特别是塑料注塑成型故障,因为塑料材料特性的不同,会导致不同的故障原因和对应的解决办法。
今天,我们将重点讨论一下塑料注塑成型中可能出现的故障及其排除方法。
1. 塑料材料不充分塑料注塑成型过程中最常见的故障之一是塑料材料不充分。
当注塑机在注入模具时,塑料材料未能充分注入模具的所有角落和隙缝,这可能导致制品表面上出现缺陷,例如气泡、白点和空洞。
解决这个问题的方法包括:增加注塑机的注塑速度、增加熔融态的体积、调整模具温度和检查射嘴。
2. 模具温度不同模具温度不均是注塑成型过程中另一个常见的问题。
如果模具的温度太高或太低,会导致塑料材料的凝固不均,使成品外观和性能下降。
解决这个问题的方法包括:检查模具的温度设定、调整水温控制阀和增加或减少模具循环时间。
3. 熔体进入模具时速度不同熔体进入模具时速度不同也会导致注塑成型的故障。
如果熔体进入模具的速度过快,可能会导致痕迹和缺陷,而如果速度过慢,则会导致模具中的熔融材料减少,从而使成品缺陷严重。
解决这个问题的方法包括检查注塑机的压力、调整注塑机的压力、检查注塑机的速度和调整塑料温度。
4. 模具中的熔体流动模具中的熔体流动也是注塑成型过程中的一个常见问题。
当模具处于运行状态时,如果熔融材料的流动速度不均,可以导致产品表面崩裂,甚至可能损坏模具。
解决这个问题的方法包括检查模具的设计、融材料的温度、注射压力、喷嘴位置和模具温度。
5. 塑料材料气泡塑料材料中出现气泡也是注塑成型中常见的故障。
当塑料材料中存在饱和的空气或其他气体时,会在塑料成型过程中形成气泡,这可能影响制品的美观,同时还会影响其物理性能。
解决这个问题的方法包括颗粒制造商解决、高压注入气体、在模具中放置真空和减少塑料材料中的空气含量。
注塑制品产生缺陷的原因及其处理方法
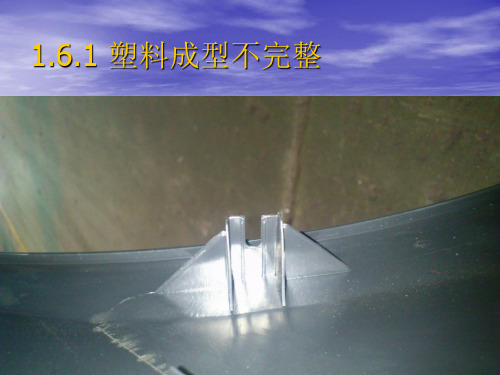
(3)模具的关键部位应有效地设置冷却水道。
(4)整个模具应不带毛刺且具有可靠的合模密 封性 。
三 工艺方面【凹痕】
(1)增加注射压力,保压压力,延长注射时间。
(2)提高注射速度可以较方便地使制件充满并 消除大部分的收缩。
(3)薄壁制件应提高模具温度,保证料流顺畅; 厚壁制件应减低模温以加速表皮的固化定型。
道入口配合不良,塑料炭化沉积物等堵塞; 喷嘴或主流道入口球面损伤、变形,影响 与对方的良好配合;
(4)塑料熔块堵塞加料通道这种情况只 有在凿通通道,排除料块后才能得到根本 解决。
(5)喷嘴冷料入模,应降低机筒前端和喷嘴的 温度以及减少机筒的储料量,减低背压压力避 免机筒前端熔料密度过大。
(6)注塑周期过短。由于周期短,料温来不及跟上 也会造成缺料。延长料粒在机筒内的预热时间。
总结处理方法
流道和螺杆料温太高,射出和储料速度太快, 背压太小,烘干不足,有混料,模温低,未打 保备方面【熔接痕】 塑化不良,熔体温度不均,可延长模塑周期。
二 模具方面【熔接痕】
(1)模具温度过低。 (2)流道细小、过狭或过浅,冷料井小。 (3)扩大或缩小浇口截面,改变浇口位置。 (4)排气不良或没有排气孔
三 工艺方面【飞边】
(1)注射压力过高或注射速度过快。由于高压 高速,对模具的张开力增大导致溢料。 (2)加料量过大造成飞边。值得注意的是不要 为了防止凹陷而注入过多的熔料,这样凹陷未 必能“填平”,而飞边却会出现。这种情况应 用延长注射时间或保压时间来解决。
(3)机筒、喷嘴温度太高或模具温度太高都会 使塑料黏度下降,流动性增大,在流畅进模的 情况下造成飞边。
(2)对流动性差或热敏性高的塑料适当添加润 滑剂及稳定剂,必要时改用流动性好的或耐热性 高的塑料。
注塑成型缺陷的成因及解决方法

注塑成型缺陷的成因及解决方法注塑成型缺陷的成因及解决方法空隙往往发生在壁相对较厚的制品内并且是在最厚的地方。
一物理原因当制品内有泡产生时,经常认为是模具内的空气被流入模腔的熔料裹入。
另一个解释是料筒内的水气和气泡会想方设法进入到制品的内部。
所以说,这样的“泡”的产生有多方面的根源。
一开始,生产的制品会形成一层坚硬的外皮,并且视模具冷却的程度往里或快或慢的发展。
然而在厚壁区域里,中心部分仍继续保持较长时间的粘性。
外皮有足够强度抵抗任何应力收缩。
结果,里面的熔料被往外拉长,在制品内仍为塑性的中心部分形成空隙。
二与加工参数有关的原因与改良措施:1、保压太低提高保压压力2、保压时间太短提高保压时间3、模壁温度太低提高模壁温度4、熔料温度太高降低熔体温度三与设计有关的原因与改良措施:1、浇口横截面太小增加浇口横截面,缩短浇道2、喷嘴孔太小增大喷嘴孔3、浇口开在薄壁区浇口开在厚壁区注塑成型各种缺陷及解决方法2017-03-22 16:02 | #2楼一、龟裂龟裂是塑料制品较常见的一种缺陷,产生的主要原因是由于应力变形所致。
主要有残余应力、外部应力和外部环境所产生的应力变形。
(-)残余应力引起的龟裂残余应力主要由于以下三种情况,即充填过剩、脱模推出和金属镶嵌件造成的。
作为在充填过剩的情况下产生的龟裂,其解决方法主要可在以下几方面入手:(1)由于直浇口压力损失最小,所以,如果龟裂最主要产生在直浇口附近,则可考虑改用多点分布点浇口、侧浇口及柄形浇口方式。
(2)在保证树脂不分解、不劣化的前提下,适当提高树脂温度可以降低熔融粘度,提高流动性,同时也可以降低注射压力,以减小应力。
(3)一般情况下,模温较低时容易产生应力,应适当提高温度。
但当注射速度较高时,即使模温低一些,也可减低应力的产生。
(4)注射和保压时间过长也会产生应力,将其适当缩短或进行th 次保压切换效果较好。
(5)非结晶性树脂,如as树脂、abs树脂、pmma树脂等较结晶性树脂如聚乙烯、聚甲醛等容易产生残余应力,应予以注意。
塑料注塑成型不良现象原因及处理办法

塑料注塑成型不良现象原因及处理办法一、气泡气泡是一种常见的注塑不良现象,造成气泡的原因可以分为产品设计、原料选择和注塑工艺三个方面。
1.产品设计问题:设计中未考虑到壁厚梯度过大、封闭空腔、通孔无曲线等情况,导致气泡无法排除。
处理办法:合理优化产品设计,减小壁厚梯度、增加封闭空腔的通气孔。
2.原料选择问题:原料中含有过多的挥发性成分、水分或杂质,或者原料中添加了过多的促进剂。
处理办法:使用质量可靠的原料,并严格控制原料中的水分和杂质含量。
3.注塑工艺问题:温度、压力、注射速度等工艺参数设置不合理,导致气泡无法排除。
处理办法:合理调整注塑工艺参数,保持合适的温度、压力和注射速度,防止气泡产生。
二、热缩痕热缩痕是注塑过程中产生的一种表面缺陷,常见于产品壁厚不一致、结构复杂的部分。
1.壁厚不一致问题:在产品设计中,壁厚过大或过小的部分易产生热缩痕。
处理办法:调整产品结构,减小壁厚梯度,避免热缩痕的产生。
2.注塑工艺问题:注塑过程中温度、压力不稳定,或者注射速度过快,都会导致热缩痕的产生。
处理办法:优化注塑工艺参数,保持合适的温度、压力和注射速度,避免热缩痕的产生。
三、翘曲变形翘曲变形是注塑成型中常见的一种现象,主要是由于材料流动不均匀或受力不平衡造成的。
1.部件结构问题:产品设计中存在壁厚不均匀、结构不合理等问题,易导致翘曲变形。
处理办法:优化产品结构设计,减小壁厚梯度,增加强度和刚度。
2.注塑工艺问题:注塑过程中温度、压力、注射速度等参数设置不合理,也会导致翘曲变形。
处理办法:调整注塑工艺参数,保持合适的温度、压力和注射速度,控制注塑过程中的变形。
四、色差色差是指注塑成型产品的颜色不均匀或与要求的颜色不符,主要由原料或工艺引起。
1.原料问题:原料中的色母粒质量不好、色母粒加入不均匀等原因,导致产品的色差问题。
处理办法:选用质量可靠的色母粒,并加入均匀进行混合。
2.注塑工艺问题:注塑过程中温度控制不当,熔融状态不稳定,颜色出现偏差。
- 1、下载文档前请自行甄别文档内容的完整性,平台不提供额外的编辑、内容补充、找答案等附加服务。
- 2、"仅部分预览"的文档,不可在线预览部分如存在完整性等问题,可反馈申请退款(可完整预览的文档不适用该条件!)。
- 3、如文档侵犯您的权益,请联系客服反馈,我们会尽快为您处理(人工客服工作时间:9:00-18:30)。
(3)浇口位置设置不合理。应改变浇口位置。
(4)原料中易挥发物含量太高或模具排气不良。应去处原料内挥发
物及改善模具排气系统。
(5)模具内未设冷料穴。应增设冷料穴。
(6)模腔表面有异物杂质。应进行清洁处理。
(7)浇注系统设计不合理。应改善浇注系统的充模性能,使熔料在
模腔中流动顺畅。
(5)保压时间太长。应适当缩短。
(6)模具温度不均匀。应合理设置模具冷却系统和流量。
(7)浇口截面尺寸太小。应适当放大。
(8)顶出装置设置不合理。应尽量增加顶出截面积及顶出点。
(9)模具强度不足。应尽量提高模具刚性。
竖浇口粘着
(1)料筒温度太高。应适当降低料筒温度。
(2)注射压力太低。应适当提高。
(3)喷嘴温度太低。应适当提高喷嘴温度。
银丝纹
(1)熔料温度太高。应适当降低料筒温度。
(2)模具温度偏低。应适当提高。
(3)原料内混入异物杂质。应进行清除。
(4)原料干燥不良。应提高干燥温度及延长干燥时间。
表面划痕
(1)Байду номын сангаас射压力太高。应适当降低。
(2)保压时间偏长。应适当缩短。
(3)模具温度太低。应适当提高。
(4)顶出装置设置不合理。应尽量增加顶出截面积及顶出点。
(4)竖浇口套表面光洁度太低。应提高其光洁度。
聚丙烯注塑成型故障得成因及对策
故障名称
成因及对策
欠注
(1)工艺条件控制不当。应适当调整。
(2)注射机注射量不足。应更换较大规格的注射机。
(3)浇注系统结构尺寸偏小。应适当放大浇口和流道截面。
(4)模腔内熔料的流动距离太长或有薄壁部分。应设置冷料穴。
(5)模具排气不良。应改善模具排气。
色泽不均
(1)料筒温度太高。应适当降低料筒温度。
(2)成型周期太长。应适当缩短。
(3)螺杆背压太低。应适当提高。
(4)原料着色不均匀。应使原料着色均匀。
脆弱
(1)料筒温度太高。应适当降低料筒温度。
(2)模具温度较高。应适当降低。
(3)原料内混入异物杂质。应进行清除或更换原料。
(4)浇口位置设置不当。应将浇口设置在壁厚处。
(3)不同品种的原料混用,会产生银条痕。应防止异种树脂混用。
(4)原料中水分及易挥发物含量太高。应对原料干燥处理。
(5)银条痕总是在一定的部位出现时,应检查对应的模腔表面是否
有表面伤痕。如果有表面伤痕的复映现象,应采用机加工方法去除模
腔表面伤痕。
龟裂及白化
(1)注射压力和注射速度太高。应适当降低。
(2)冷却时间太短。应适当延长。
气泡
(1)注射压力太低。应适当提高。
(2)浇口及流道尺寸太小。应适当放大。
(3)制品壁厚变化太大。应合理设计制品形体结构,避免壁厚急变。
(4)原料内水分含量高。应对原料进行予干燥处理。
真空孔
(1)保压不足。应适当延长补料的注射时间。
(2)注射压力太低。应适当提高。
(3)模具温度太低,料筒温度太高。应适当降低料筒温度,提高模
烧焦及黑纹
(1)熔料温度太高,产生过热分解。应适当降低料筒温度。
(2)成型周期太长。应适当缩短。
(3)注射速度太快。应适当减慢。
(4)螺杆背压太高。应适当降低。
(5)浇口截面尺寸太小。应适当放大。
(6)模具排气不良。应增加模具排气。
(7)原料干燥不良。应提高干燥温度及延长干燥时间。
(8)脱模剂用量太多。应尽量减少其用量。
(6)供料不足。应增加供料量。
(7)螺杆背压偏低。应适当提高。
(8)浇注系统结构尺寸偏小。应适当放大浇口和流道截面。
(9)模具排气不良。应增加模具排气。
(10)模具强度不足。应尽量提高模具刚性。
溢料飞边
(1)熔料温度太高。应适当降低料筒及喷嘴温度。
(2)注射压力太高。应适当降低。
(3)注射速度太快。应适当减慢。
(6)原料流动性能太差。应换用流动性较好的原材料。
(7)料筒温度太低、注射压力不足或补料的注射时间太短。应相应
提高有关工艺参数。
溢料飞边
(1)成型温度太高或注射压力太高。应适当降低。
(2)锁模力不足。应更换规格较大的注射机。
(3)模具分型面有异物杂质。应进行清除。
(4)模具的销孔或导销磨损严重。应机械加工修复模具。
(3)注射速度太慢。应适当加快。
(4)模具温度太低。应适当提高。
(5)制品结构设计不合理或壁太薄。应在可能的情况下调整。
(6)浇注系统结构尺寸偏小。应适当放大浇口和流道截面。
(7)模具内的冷料穴太小。应适当放大。
(8)原料内混入异物杂质。应进行清除。
(9)脱模剂用量偏多。应尽量减少其用量。
(10)原料着色不均匀。应使原料着色均匀。
烧焦及黑纹
(1)注射机规格太大。应换用规格合适的注射机。
(2)树脂的流动性能较差。应使用适量的外部润滑剂。
(3)注射压力太高。应适当降低。
(4)浇口位置设计不合理。应改变浇口位置,使熔料在模腔中均
匀流动。
(5)模具排气不良。应增加模具排气。
银条痕
(1)模具与喷嘴接触不良。应调整两者的位置和尺寸。
(2)模具排气不良。应增加模具排气。
(3)熔料及模具温度太低。应适当提高。
(4)顶出装置设置不合理。应尽量增加顶出截面积及顶出点,最好
采用气动脱模装置。
(5)模具的浇注系统结构设计不合理。应改善浇口和流道尺寸,使
充模时不产生紊流。
弯曲变形
(1)模具温度太高或冷却不足。应适当降低模具温度或延长冷却时间,
对于细长制品可采取胎具固定后冷却的方法。
(5)保压时间偏短。应适当延长。
分层剥离
(1)熔料温度太低。应适当提高料筒及喷嘴温度。
(2)螺杆背压太高。应适当降低。
(3)原料内混入异物杂质。应进行彻底清除。
翘曲变形
(1)熔料温度太低。应适当提高料筒温度。
(2)成型周期偏短。应适当延长。
(3)注射压力太高。应适当降低。
(4)注射速度太快。应适当减慢。
(5)脱模斜度不足。应适当增加。
光泽不良
(1)熔料温度偏低。应适当提高料筒及喷嘴温度。
(2)成型周期太长。应适当缩短。
(3)模具温度偏低。应适当提高。
(4)浇注系统结构尺寸偏小。应适当放大浇口和流道截面。
(5)模具排气不良。应增加模具排气。
(6)原料内混入异物杂质。应进行清除或更换原料。
(7)脱模剂用量太多。应尽量减少其用量。
(2)成型周期太长。应适当缩短。
(3)注射压力偏低。应适当提高。
(4)注射速度太快。应适当减慢。
(5)保压时间太短。应适当延长。
(6)模具温度不均匀。应合理设置模具冷却系统和流量。
(7)模具排气不良。应增加模具排气。
(8)制品结构设计不合理,壁太厚。应在可能的情况下调整。
(9)浇口截面太小。应适当放大。
具温度。
(4)原料的流动性能太好。应换用熔体流动速率较低的树脂。
表面气孔
(1)厚壁制品的模具流道及浇口较小时容易产生表面气孔。应放大
流道和浇口尺寸。
(2)制品壁太厚。在设计时应尽量减少壁厚部分。
(3)成型温度太高或注射压力太低,都会导致制品表面产生气孔.
应适当降低成型温度,提高注射压力。
熔接痕
(1)熔料及模具温度太低。应适当提高料筒及模具温度。
(3)冷却时间太短。应提高冷却效率或延长冷却时间。
(4)供料不足。应增加供料量。
(5)模具温度不均匀。应合理设置模具冷却系统和流量。
(6)制品壁太厚。应在可能的情况下调整。
(7)浇注系统结构尺寸偏小。应适当放大浇口和流道截面。
熔接痕及料流痕
(1)熔料温度太低。应适当提高料筒及喷嘴温度。
(2)注射压力太低。应适当提高。
(5)保压不足。应适当延长补料的注射时间。
脱模不良
(1)模具表面光洁度太差。应通过研磨或电镀提高其光洁度。
(2)注射压力或注射速度太高。应适当降低。
(3)模具温度及冷却条件控制不当。当制品在芯模处粘模时,应提
高模温及缩短冷却时间。当制品在型腔表面粘模时,应适当降低模温
和延长冷却时间。
(4)顶出装置设置不合理。应尽量增加顶出截面积及顶出点。
(4)保压时间偏长。应适当缩短。
(5)供料过多。应适当减少供料量。
(6)锁模力不足。应增加锁模力。
(7)模具强度不足。应尽量提高模具刚性。
(8)镶件设置不合理。应适当调整。
(9)浇口截面较大。应适当减小。
(10)模具安装不良,基准未对中。应重新装配模具。
气泡
(1)熔料温度偏高。应适当降低料筒及喷嘴温度。
应适当降低模具温度或延长冷却时间对于细长制品可采取胎具固定后冷却的方法
聚烯烃类塑料注塑成型故障得成因及对策
故障名称
成因及对策
欠注
(1)熔料温度太低。应适当提高料筒及喷嘴温度。
(2)成型周期太短。应适当延长。
(3)注射压力偏低。应适当提高。
(4)注射速度太慢。应适当加快。
(5)保压时间偏短。应适当延长。
收缩与凹陷
(1)熔料温度偏高。应适当降低料筒温度。
(2)注射压力太低。应适当提高。
(3)模具温度太高。应适当降低。
(4)制品壁太厚。应在可能的情况下调整。
(5)浇口截面尺寸太小。应适当放大。
(6)成型周期太短。应适当延长。
(5)保压时间太短。应适当延长。
缩痕
(1)注射压力太低。应适当提高。
(2)保压时间太短。应适当延长。
(2)冷却不均匀。应改善模具冷却系统,保证制品冷却均匀。