利用TQC原理解决摩托车发动机凸轮轴磨损
摩托车凸轮轴珠光体含量的电磁法检测技术

摩托车凸轮轴珠光体含量的电磁法检测技术
1 简介
摩托车发动机凸轮轴是发动机中的一个关键部件,它通过不断运动带动摩托车发动。
凸轮轴材质一般是高强度的合金钢,它在长时间的高速摩擦下,表面易产生疲劳、龟裂等微结构损伤,因此需要定期检测凸轮轴表面是否存在问题。
2 检测方法
传统的检测方法一般采用人工外观观察和超声波检测,然而这些方法都有一定的缺陷。
人工外观观察难以发现微小的龟裂,而超声波只能检测到表面伤痕,无法检测到深层缺陷。
因此,采用电磁法检测凸轮轴表面珠光体的含量可以成为一种更高效、准确的方法。
3 原理
在摩托车凸轮轴表面压制珠光体时,由于其电导率和磁导率的差异,凸轮轴表面和珠光体之间会产生不同的磁场响应。
通过加热凸轮轴,使珠光体断裂后释放出的磁场信号被接收,通过信号的强度和时间来判断凸轮轴表面上珠光体的含量和深度。
4 应用
电磁法检测技术已经广泛应用于汽车、飞机、铁路等交通运输工具的零件检测中。
在摩托车凸轮轴的检测中,电磁法检测技术可以快
速准确地检测出凸轮轴表面的微小损伤,有助于及早排除安全隐患和故障,提高摩托车性能和使用寿命。
5 结论
电磁法检测技术是一种可靠、高效、非破坏性的检测方法,可以用于检测摩托车凸轮轴表面珠光体含量,有效避免了传统检测方法的缺陷。
同时,电磁法检测技术的推广应用将有助于提高摩托车的安全性和可靠性。
凸轮磨削表面烧伤产生原因

凸轮磨削表面烧伤产生原因及消除方法探析(五羊-本田摩托(广州)有限公司,广东广州510260)摘要:磨削表面烧伤是磨削过程的瞬时高温使工件金属表面产生一层很薄的氧化层,它会影响工件的耐磨性和使用寿命.以WY125摩托车发动机凸轮轴磨削加工时凸轮表面产生烧伤现象为实例,分析凸轮表面磨削烧伤产生的原因,并从减少磨削热产生和加速磨削热传出两个方面介绍了消除磨削表面烧伤的方法.关键词:凸轮轴;磨削;表面烧伤笔者所在公司采用日本近腾(KONDO)公司制造的数控磨床精加工WY125摩托车发动机凸轮轴.该设备以机械靠模加工方式成形凸轮,其原理是通过工件传动轴和摇架摆动轴的联动关系,使得凸轮在磨削过程中实现远离和靠近砂轮的运动从而实现凸轮轮廓成形,该设备采用立方氮化硼CBN砂轮,砂轮修正器为金刚轮,砂轮高速旋转并由数控程序控制,其横向进给分粗磨、精磨、微磨3个阶段.凸轮轴是发动机内的重要零件,直接影响到发动机的使用性能.在加工凸轮轴时,在磨削凸轮表面工序中发现在凸轮轴进、排气凸轮的平面段表面出现淡黄色的表面烧伤现象,同时在亮光下观察到磨削表面有微细的裂纹.磨削作为精加工,在加工时必须具有较高的切削速度,才能使工件达到较高的尺寸精度、粗糙度等项要求,因此被磨削的金属在磨削力的作用下机械能转化为热能,在磨削区短时间地、大量地发热,瞬时温度可达1 000℃.磨削过程的瞬时高温引起被磨削金属表面产生一层很薄的氧化层磨削表面烧伤.磨削烧伤表面所呈现的颜色是磨削热在工件表面上产生的氧化膜的干涉颜色,相当于回火颜色.回火是在较低温度、长时间加热的条件下形成的,而磨削烧伤则是在瞬时高温加工中产生的.磨削烧伤会破坏工件表层组织,严重时会产生裂纹,使工件表面质量恶化,严重影响工件的耐磨性和使用寿命.1 凸轮磨削表面烧伤的原因分析磨削是用分布在砂轮表面上的磨粒通过砂轮和被磨工件的相对运动进行的切削.磨削过程是磨粒在工件表面进行滑擦、耕犁和切屑的时间延续,磨削过程所产生的能量部分转化为热,而大部分的热能均被传入工件中,使工件升温.磨粒磨削点的温度是磨粒与切屑接触部分的温度,是磨削中温度最高的部位,也是磨削热的热源.砂轮磨削区的温度是砂轮与工件接触区的平均温度,它与磨削烧伤、裂纹的产生有密切关系.根据相关理论,砂轮磨削区的温度可表示为式中:V,V W---砂轮及工件的线速度,m/s;fr---径向进给量,mm;由上式可见,径向进给量fr增加将使砂轮与工件接触区域增加,它对磨削温度θ的影响最大.由于凸轮是由不同形状的表面构成,而根据所使用凸轮轴磨床的工作原理,加工时各段表面的磨削厚度相同,因此,在对各段表面磨削过程中,相应的各段砂轮与工件的接触区域是不同的,如图1所示.加工平面段或曲面段时,各加工表面的磨削厚度均为ap,加工平面段时砂轮与工件接触区域为ab段,加工曲面段时砂轮与工件接触区域为cd段,由图1可见,ab段等于de段,de段大于cd段,即ab段大于cd段.由此可以说明,在加工平面段时砂轮与工件的接触区域大于加工曲面段时砂轮与工件的接触区域.因此,在加工平面段时单位时间内进入磨削区的工件材料增加,从而使每个磨粒的切削厚度增加,即在磨削平面段过程中磨削力和能量的消耗增加,并且磨削区的温度增加较高,因而导致被加工的平面段表面比曲面段表面更易产生磨削烧伤和磨削裂纹.这就是为什么被磨削的凸轮表面平面段有烧伤现象而曲面段无烧伤现象的主要原因.影响磨削表面烧伤的主要因素是磨削热的产生和磨削热的传出,根据磨削工件凸轮表面被烧伤的现象,笔者从磨削热的产生和传出这两个方面,对其产生的具体因素进行了调查.影响磨削热产生的主要因素是砂轮和磨削参数.1 砂轮其影响因素为:砂轮硬度太硬,磨粒磨钝后仍不脱落;合理选择砂轮的粒度、结合剂,使其不易引起堵塞;砂轮定期修整,保持砂轮在锋利条件下进行磨削.调查结果为:磨床使用的立方氮化硼CBN砂轮是人工合成的一种高硬度材料,硬度HV7 300~9 000,仅次于金刚石,能耐1 300~1 500℃的高温,与铁族金属的亲和力小.砂轮修整频次300个/次,投产以来一直使用该种砂轮,使用效果良好.2 磨削参数其影响因素为;不合理的磨削参数,将使磨削过程的磨削力和能量消耗增加,增大磨削过程中塑性变形和磨削热.调查结果为:对磨床设定的径向进给速度为1.0mm/min,粗磨深度为A=0.45mm,精磨深度为B=0.10mm,微磨深度为C=0.05mm.影响磨削热传出的主要因素是切削液和凸轮轴材料.1 切削液其影响因素为:加工时切削液流量不足,使用不当;所选用的切削液冷却效果不好.调查结果为:现场检测所使用的切削液浓度为4%,符合切削液浓度2%~4%的工艺要求.但切削液起泡,水箱底沉积物较多,影响了切削液的冷却效果,使磨削区的热量不能及时转出;同时,发现砂轮修正器冷却管堵塞,修正砂轮时无冷却液流出,影响了砂轮的修正效果.2 凸轮轴材料其影响因素为:材料的碳或合金含量越高,导热性越差.调查结果为:所加工的凸轮轴毛坯材料为珠光体可锻铸铁,含碳量不高,磨削前采用整体淬火,硬度要求为HRC50~60;以往使用该材料加工,产品性能良好,经材料和金相检测,符合技术要求.从以上调查结果可以看出,影响磨削热产生和传出的主要因素是磨削参数设定的不合理以及切削液的冷却效果差.2 凸轮磨削表面烧伤的消除方法要控制和避免磨削烧伤的产生,就必须减少磨削热的产生和加速磨削热的传出.根据对影响磨削热产生和传出的因素分析和调查结果,经多次试验和反复摸索比较,我们采取了以下措施来消除凸轮轴表面的磨削烧伤现象.1 定期清理磨床的冷却系统定期清理磨床的冷却系统是为了确保切削液流动顺畅、流量充足.同时选用另一种磨粉与水分离性较好的切削原液,以提高切削液的冷却效果.2 调整磨削参数主要采用了以下两种方法.一是减少磨削深度.根据凸轮表面烧伤原因分析,减少磨削深度可减少磨削产生的热量,有效控制磨削表面的烧伤现象,但是根据凸轮轴加工工艺,凸轮磨削前需经粗铣凸轮、凸轮轴整体热处理等加工工序,考虑到前工序的加工公差、工件热处理变形以及加工时的定位基准误差等因素的影响,故减少磨削深度将使许多工件不能磨出完整的凸轮轮廓,这将大大增加废品率,批量生产中不宜采用此方法.二是降低径向进给速度.根据对凸轮表面的烧伤原因分析,径向进给速度降低,将减少单位时间内砂轮与工件的接触区域,从而减少磨削热的产生.从磨削的3个阶段看,粗磨和精磨两个阶段由于磨削深度较深,磨削量大,故降低粗磨和精磨的进给速度可有效控制凸轮表面烧伤现象,但这样做将使该工序的生产节拍大大延续.磨凸轮工序是凸轮轴生产线的瓶颈工序,大幅度延缓生产线节拍将无法满足生产线生产能力的要求.鉴于以上因素,我们经过多次试验,采用降低微磨进给速度的方法来控制凸轮表面的烧伤程度,试验数据见表1.由试验数据可见,在确保凸轮轴生产线加工合格率和生产能力要求的前提下,通过将微磨进给速度由1.0 mm /min调整至0.1mm/min,可消除凸轮表面的烧伤现象.在实施了上述措施后,凸轮轴磨削表面无烧伤现象,表面粗糙度、尺寸精度等检测项目均符合技术要求,经质量加工验证,凸轮轴加工质量稳定.3 结束语本文依据磨削加工原理,对于生产现场出现的凸轮轴磨削表面的烧伤现象产生的部位和原因进行了分析,并探讨了控制和消除磨削表面烧伤的方法,从而有效地保证了凸轮轴磨削加工的表面质量.地址:广州市增城新塘镇永和新新六路1号总机:(020)32989888 邮编:511356。
某型柴油机凸轮异常磨损原因分析
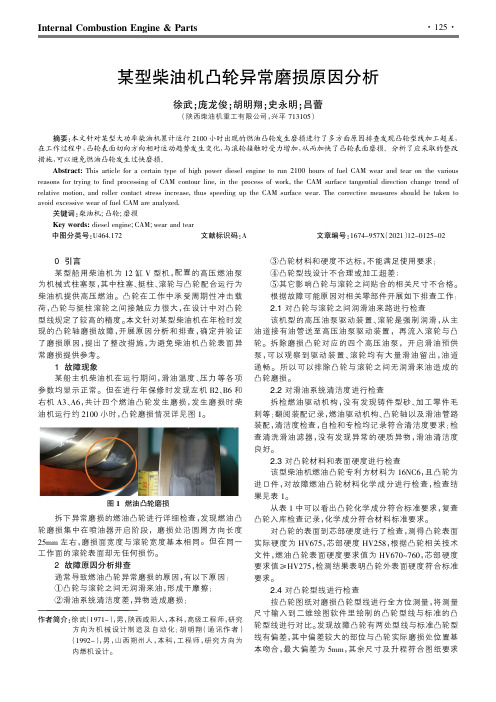
图1燃油凸轮磨损拆下异常磨损的燃油凸轮进行详细检查,发现燃油凸轮磨损集中在喷油器开启阶段,磨损处沿圆周方向长度25mm左右,磨损面宽度与滚轮宽度基本相同。
但在同一工作面的滚轮表面却无任何损伤。
2故障原因分析排查通常导致燃油凸轮异常磨损的原因,有以下原因:①凸轮与滚轮之间无润滑来油,形成干摩擦;②滑油系统清洁度差,异物造成磨损;———————————————————————作者简介:徐武(1971-),男,陕西咸阳人,本科,高级工程师,研究方向为机械设计制造及自动化;胡明翔(通讯作者)(1992-),男,山西朔州人,本科,工程师,研究方向为内燃机设计。
(具体见图2),图中阴影曲线部分为故障件凸轮型线。
所以不排除凸轮型线偏差造成凸轮磨损的可能。
由于凸轮在使用过程中发生磨损,为查明原因,对同一批次的库存燃油凸轮进行测量得到同样不符合图纸要求的型线尺寸,非同批次检查结果表明凸轮型线符合图纸要求,见图3。
2.5对其它影响凸轮与滚轮之间贴合的相关尺寸进行检查根据凸轮专利方图纸进行其它相关尺寸的检查,检测结果如表2。
从检测结果看,全部合格,可以排除影响凸轮与滚轮之间贴合的尺寸超差引起凸轮工作面异常磨损。
凸轮材料、尺寸及表面硬度直接影响柴油机的可靠性,对于设计定型的柴油机,机需要重点针对凸轮材料、过程的监管,特别是加强对原材料采购的质量控制和凸轮型线加工及热处理的过程检验,类故障的发生。
参考文献:[1]柴油机排烟异常的分析与诊断(11):28.[2]韩自朴.8240ZJ[J].内燃机车,1993:[3]张河.CAT-C9备管理与维修,2019图2故障件凸轮型线图3库存件凸轮型线序号检测项目要求值实测值1 2 3 4 5 6 7 8凸轮工作面与内孔轴线的平行度凸轮基圆表面圆柱度凸轮工作面的表面粗糙度凸轮哈夫面平面度凸轮工作面的直线度起始点和终点的角度误差凸轮基圆内径凸轮基圆外径0.005mm0.050mm0.40μm0.020mm0.005mm±30′Φ125K6+0.04-0.021mmR95±0.5mm0.002mm0.025mm0.25μm0.015mm0.005mm18′X向Φ124.99mmY向Φ124.99mmR95.05mm表2检测结果图4正常凸轮受力图5故障凸轮受力F1F3F2F1。
利用TYCON软件优化摩托车发动机配气凸轮型线

轮 型线优 化实例 来介 绍优化 过程 。
42 6 MS发动机是 一款并列 4缸 顶置 凸轮 驱动式
发动机 ,首先在 T C Y ON软件 中建立运动 留有一 定 间隙 ,以保证 气门在任
何情 况 下都能 完全 闭合 。 另外 ,配 气机构 各零件 都不是 绝对 刚性 的 ,当
Me h nc l p e n Stm c a ia Ta p t dVa a e
受到压 缩时 ,在凸轮 驱动下 ,零 件会产生弹性变形 , 气门并 没有立 即升起 ,直 到 克服 了弹性变 形 引起 的 压 缩量 后 ,气门才 开始升 起 。 因此 ,应使 气 门在 设
图 1 建 立 的4 2 6 M9发 动机 运 动学 模 型
维普资讯
维普资讯
D s n・ eerh设计 ・ ei R sac g 研究
加 ∞ 如
门对 凸轮运 动机 构进行运 动学 和动 力学 分析 、 设计
的功能强大的软件 ,可用 它进行 凸轮型线的设计 、分
门接近 全开位 置 ,即获 得较大 的丰 满度 。
l t r l x le c v v r n . .  ̄ u a f  ̄ u n y of al e t ai a . 1axi 4 mum ca■ t o t appet cont act st re豁 1 x m  ̄ a 4 i u a  ̄ l e al e of a ut v u c ■ t r u o q e 1i mum f 4 ni or∞ f act o ̄ .. ..... ..... ...
.
.
.
.
.
Fl w o ef i i nt ( ot 1) . . . . . . o o fce t a . . + .
摩托车发动机凸轮磨削动态特性影响的快捷排除方法

j —
?
:
圈口团
摩托 车发动机 凸轮磨 削动态特性 影响 的快捷排 除方法
刘兴 富 ( 广 州威而信精 密仪 器有 限公 司西安 分公 司)
刘瑞 玲 ( 陕 西五 环 ( 集 团 ) 实 业 有 限 责任 公 司)
摘要 : 在 磨削 凸轮时 ,影响 凸轮精度 的 因素有很 多,如原始 靠模 ( 标 准 凸轮)、工作靠模等 系统本
Abs t r a c t : Ma n y f a c t o r s a f f e c t t h e a c c u r a c y o f t he c a m g r i n d i n g,s uc h a s t h e e r r o r s i n t h e d e s i g n a n d
L i u Xi n g f u ( Gu a n g z h o u Wi l s o n P r e c i s i o n I n s t r u me n t C o . , L t d . )
L i u Ru i l i n g ( S h a n x i R i n g s( Gr o u p ) I n d u s t r y C o . , L t d . >
ma n u f a c t u r i n g o f d e s i g n e d mo d e l ( f o r s t a n d a r d c a m) a n d r e a l mo d e l , t h e d i s t o r t i o n e r r o r c a u s e d b y t h e c l e a r a n c e
精度 误差 及 被磨 削 凸轮形 状 引起 的磨 削动 态特 性造 成 的形
发动机凸轮轴磨损原因分析及修复方案
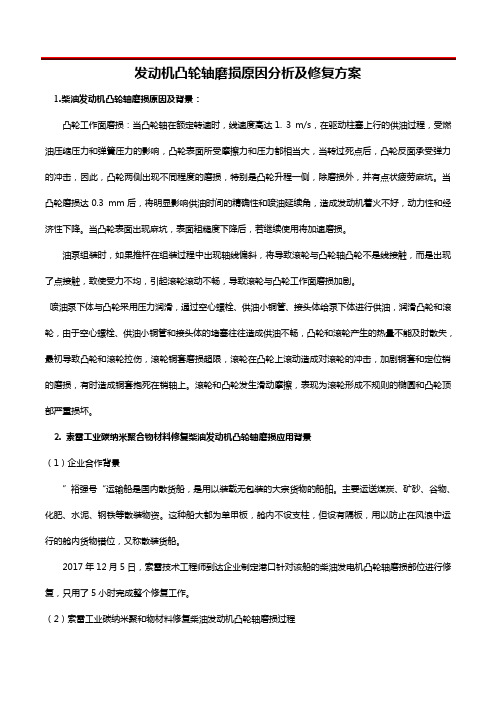
发动机凸轮轴磨损原因分析及修复方案1.柴油发动机凸轮轴磨损原因及背景:凸轮工作面磨损:当凸轮轴在额定转速时,线速度高达1. 3 m/s,在驱动柱塞上行的供油过程,受燃油压缩压力和弹簧压力的影响,凸轮表面所受摩擦力和压力都相当大,当转过死点后,凸轮反面承受弹力的冲击,因此,凸轮两侧出现不同程度的磨损,特别是凸轮升程一侧,除磨损外,并有点状疲劳麻坑。
当凸轮磨损达0.3 mm后,将明显影响供油时间的精确性和喷油延续角,造成发动机着火不好,动力性和经济性下降。
当凸轮表面出现麻坑,表面粗糙度下降后,若继续使用将加速磨损。
油泵组装时,如果推杆在组装过程中出现轴线偏斜,将导致滚轮与凸轮轴凸轮不是线接触,而是出现了点接触,致使受力不均,引起滚轮滚动不畅,导致滚轮与凸轮工作面磨损加剧。
喷油泵下体与凸轮采用压力润滑,通过空心螺栓、供油小铜管、接头体给泵下体进行供油,润滑凸轮和滚轮,由于空心螺栓、供油小铜管和接头体的堵塞往往造成供油不畅,凸轮和滚轮产生的热量不能及时散失,最初导致凸轮和滚轮拉伤,滚轮铜套磨损超限,滚轮在凸轮上滚动造成对滚轮的冲击,加剧铜套和定位销的磨损,有时造成铜套抱死在销轴上。
滚轮和凸轮发生滑动摩擦,表现为滚轮形成不规则的椭圆和凸轮顶部严重损坏。
2. 索雷工业碳纳米聚合物材料修复柴油发动机凸轮轴磨损应用背景(1)企业合作背景”裕强号“运输船是国内散货船,是用以装载无包装的大宗货物的船舶。
主要运送煤炭、矿砂、谷物、化肥、水泥、钢铁等散装物资。
这种船大都为单甲板,舱内不设支柱,但设有隔板,用以防止在风浪中运行的舱内货物错位,又称散装货船。
2017年12月5日,索雷技术工程师到达企业制定港口针对该船的柴油发电机凸轮轴磨损部位进行修复,只用了5小时完成整个修复工作。
(2)索雷工业碳纳米聚和物材料修复柴油发动机凸轮轴磨损过程根据凸轮轴实际磨损尺寸及配合特性等,利用索雷《工装修复工艺》现场实施磨损部位修复,保证配合同轴度要求前提下同时避免补焊中常见的热应力、变形、断裂等问题。
F6L912发动机凸轮轴后座孔烧蚀磨损失圆的修复方法

F6L912发动机凸轮轴后座孔烧蚀磨损失圆的修复方法——附加零件法中国人民解放军65057部队戴金山刘晓斌我单位一台74式Ⅱ型挖掘机在使用中出现六缸气门与活塞顶撞现象,调整气门间隙后上述现象依然存在且该缸气门间隙错乱,再次调整气门间隙,故障依旧。
进一步拆检发动机时发现凸轮轴最后一道轴颈与缸体座孔烧蚀并产生严重磨损,缸体座孔与凸轮轴颈均已失圆,其间隙达2mm之多。
该故障若按通常的“换件法”修理,缸体及凸轮轴购置费用就达7000元左右。
为降低修理费用,我们决定在缸体座孔与凸轮轴之间增加一个铜套的“附加零件法”对其进行恢复性修理。
1 铜套的尺寸确定1)根据缸体座孔的磨损失圆程度,将座孔搪大5-8mm;将失圆的凸轮轴颈磨圆;测量缸体座孔搪大后的径向尺寸D1及凸轮轴颈磨后的径向尺寸d1。
2)铜套尺寸的计算D外=D1+(0.02~0.04mm);保证轴套与孔座的过盈量为0.02~0.04mm;D内=d1+(0.07~0.09mm);保证轴套压装后与轴径的间隙为0.03~0.07mm;L=凸轮轴径的配合长度;d=5~7mm(与机体座油道大小近似)。
2 铜套材料的选择与加工1)材质为ZH40(铸黄铜);2)附加零件结构,如图1所示。
3 装配要点1)铜套油孔应与缸体座孔的油孔对正;2)装配时应与防止油堵密封不严产生渗漏(见图2)。
按照上述方法修配并进行气门间隙调整后,该机一次性启动成功,前述现象也随之消失。
该机在近1000摩托小时的使用过程中,运转平稳,性能可靠。
前不久,我们对某单位一台同样故障的F6L912发动机采用同样的方法进行修理,也获得了同样的效果。
实践证明:采用“附加零件法”对失圆座孔的恢复性修理,其方法是合理可行的,经济效益也令人满意。
踏板车凸轮轴磨损解决方法

踏板车凸轮轴磨损解决方法1.引言1.1 概述概述踏板车的凸轮轴是发动机中重要的零部件之一,其作用是驱动气门进行开闭。
由于凸轮轴长期运转,常受到高温高压环境的影响,容易出现磨损现象。
凸轮轴的磨损不仅会影响发动机的正常工作,还会影响踏板车的性能和经济性。
为了解决凸轮轴磨损问题,本文将介绍一些有效的解决方法。
本文首先将介绍凸轮轴磨损的原因,包括使用时间长、润滑不良、材质品质差等方面的因素。
然后,将探讨凸轮轴磨损对踏板车的影响,如功率下降、油耗增加、噪音变大等方面的问题。
最后,将提出两种解决凸轮轴磨损问题的具体方法,包括定期维护保养和更换高品质的凸轮轴。
通过本文的介绍,读者将能够全面了解凸轮轴磨损问题,并学会采取适当的解决方法。
希望通过本文的参考,读者能够更好地保护踏板车的凸轮轴,延长其使用寿命,提高踏板车的性能和经济性。
1.2文章结构文章结构部分的内容可以包括以下内容:在本文中,将从两个方面探讨踏板车凸轮轴磨损的解决方法。
首先,将介绍凸轮轴磨损的原因,分析出导致凸轮轴磨损的主要因素。
其次,将分析凸轮轴磨损对踏板车的影响,包括车辆性能下降、燃油消耗增加等问题。
最后,将提出两种解决凸轮轴磨损的方法,并对它们的可行性和效果进行评估。
通过本文的阐述,读者将能够了解踏板车凸轮轴磨损的原因和影响,并能够根据自身情况选择适合的解决方法,延长踏板车的使用寿命。
1.3 目的目的部分的内容可以写成以下这样:目的部分旨在介绍本文的主要目标和宗旨。
本文旨在探讨踏板车凸轮轴磨损的解决方法,并提供一些实用的指导和建议。
主要目的是帮助读者了解凸轮轴磨损的原因和影响,并提供有效的解决方法,让读者能够更好地维护和保养自己的踏板车,延长其使用寿命。
通过本文的阅读,读者将能够了解凸轮轴的重要性以及如何正确处理凸轮轴磨损问题。
同时,读者也可以根据本文的建议,采取一些预防措施,减少凸轮轴的磨损,提高踏板车的性能和稳定性。
总之,本文的目的是为读者提供相关知识和经验,解决凸轮轴磨损问题,确保踏板车的正常运行和使用。
- 1、下载文档前请自行甄别文档内容的完整性,平台不提供额外的编辑、内容补充、找答案等附加服务。
- 2、"仅部分预览"的文档,不可在线预览部分如存在完整性等问题,可反馈申请退款(可完整预览的文档不适用该条件!)。
- 3、如文档侵犯您的权益,请联系客服反馈,我们会尽快为您处理(人工客服工作时间:9:00-18:30)。
利用TQC原理解决摩托车发动机凸轮轴磨损
摘要:本文针对市场反馈发动机凸轮轴磨损现象,利用TQC原理,从几方面排除与查找产生发动机凸轮轴早期磨损的原因,对分析因素做实际验证,证明了磨损的主要原因为凸轮材质的选用欠佳及配偶件摇臂的精度不良导致。
关键词:TQC;凸轮轴;摇臂;异常磨损;工艺改善;验证
前言:
凸轮轴是发动机配气机构中的主要零件,它的主要作用是保证进排气阀按照一定的时间开启和关闭。
凸轮在工作过程中除受到一定的弯曲和扭转载荷外,主要是凸轮的型线表面承受交变的挤压应力和配偶的摇臂的相互运动摩擦。
凸轮轴的主要失效型式是凸轮表面因交变挤压应力作用产生的麻点或表面剥落现象。
所以要求凸轮轴具有较好的强度和刚度意外,更主要的是具有良好的耐接触和耐磨损性能。
搭载L YM149MG发动机的T110弯梁摩托车曾经荣获2007年度中国弯梁车年度车型,在摩托车领域享有较高的声誉,随着产量的不断扩大,市场反馈一定数量的发动机出现气缸头异响、凸轮轴和摇臂磨损异常的现象,影响到整车销售和企业的形象。
1.现状把握:对市场反馈做统计,故障发生期都为车辆行驶里程7000km以内,属于早期磨损。
2.原因查找与分析
针对凸轮轴早期磨损实施市场调查和要因讨论,按照TQC的原理,从人、机、料、法、环五个方面逐一进行排查分析:
人方面主要是检查:用户日常维护不当和使用劣质机油油品,通过市场用户走访,确定不是要因;
机方面主要是检查:凸轮、摇臂加工不良、凸轮、摇臂热处理金相组织不良、机油泵工作不良和油道堵塞,通过调查分析、试验再现和用户跟踪,发现凸轮和摇臂表面粗糙度检查,摇臂R面的直线度、平行度调查显示直线度超差会引起接触比压加大,易导致磨损故障发生;
料方面主要是检查:材质选用不良、缸头加工精度平行度差和气门弹簧弹力超大,发现凸轮材质有差异,不一样的材质使用的热处理方式导致金相硬度的不同,对耐磨性影响较大;
法方面主要是检查:未按照作业要求调整正时、气门间隙和油封装配不良,
导致供油压力不足,未发现成因;
环方面主要是检查:气候湿度较大、寒冷地区温差大,未发现成因。
通过对以上逐条确认,初步判断造成凸轮轴摇臂早期异常磨损的主要影响因素是:
2.1.摇臂加工不良
2.2.凸轮材质选用不适
据此制定相应措施与对策,并将要因相关的问题点细化:
2.2.1.摇臂R30面直线度不良,图样要求:镀铬面直线度4um ,实测状况:两侧高出,中间低凹;直线度在10-20um;直线度符合图面要求,不应存在中间凹的形状,改进措施为:电镀电流参数调整,追加电镀前抛光处理和电镀后倒角处理。
2.2.2.凸轮轴材质适应性不良,现有材质QT600-3的金相组织耐磨性不及YFC250Cr,改进措施为:根据现有毛坯制作试制品并通过实验验证,并重新设计凸轮轴材质为YFC250Cr激冷处理。
3.对策措施
3.1. 摇臂--直线度不良:
检查中发现,实际零件直线度超差,且微观形状呈现中间凹边缘突起的不良形状,导致工作时对凸轮的比压急剧放大,产生凸轮偏磨。
对电镀工程的确认:摇臂R30弧面采用表面电镀硬铬方法,由于电流强度大,电镀时摇臂R30面两侧角处电流集中,铬层沉积速度远较平坦部位快,因此电镀后的产品R30平面铬层形状基本如图所示;
电镀后铬层采用布轮表面抛光,仅提高R30面表面粗糙度,并不能改善电镀后的R30面形状。
改善1:电镀工艺改善
电镀电流工艺改善,总电流从3600~3900A调整为2800~3000A
改善2:增加热处理前滚抛工艺
通过两次工艺调整,对样件做试作检查:直线度较之前有较大改善,但是还没有完全达到图面要求,产品直线度从原10-20um降低到6-9um,但仍超过图
样要求的4um范围;从图形来看,电镀后产品仍呈两侧高出,中间低凹状况,以上两项措施仅在数值上有所改善,但形状并未得到真正改善。
改善3:R30面两侧增加抛角工序
经过两侧抛角工序后,如上图所示,镀铬面形状已发生根本转变,由原两侧高出、中间低凹的形状转变为鼓形或直线形形状。
3.2. 凸轮轴材质更改
通过对现品QT600-3材质的凸轮和F8机型凸轮(YFC250Cr)以及CKD的凸轮(YFC250-Cr)进行材质金相的对比:比较结果:CKD和F8的金相组织比较接近,耐磨性明显优于L YM149MG的凸轮轴。
凸轮轴硬度的调查确认
表面硬度数据:
机种F8 CKD LYM
表面洛氏(桃尖部位) HRC49~50 HRC51.5~52.5 HRC46.5~47
显微硬度数据:(距表面0.15~0.20处)
CKD F8 LYM
序号显微硬度序号显微硬度序号显微硬度
1 510 1 53
2 1 439
2 508 2 538 2 427
3 509 3 573 3 433
4 564 4 574 4 443
5 501 5 59
6 5 479
6 502 6 580 6 447
7 484 7 605 7 477
8 512 8 578 8 473
9 475 9 514 9 463
平均HV507.22(HRC49.7)平均HV565.56(HRC53.2)平均HV453.44(HRC46.3)
硬度检查表明L YM149MG的凸轮桃尖硬度明显低于CKD和F8,也就是说现有材质QT600-3高频淬火得到的凸轮的硬度并没有YFC250-Cr材质的凸轮经过冷激处理来的高,耐磨性不佳。
4.改善效果的验证
从调查的结果及改善实绩的部品经过多次台架耐久及模拟用户的实车走行考核10000km,均没有再现异常磨损。
对策措施改进后的市场投诉也有明显改善。
今后进一步的工作:
4.1.加大对配套厂电镀工程的工艺执行情况管理,加大部品的受入检查力度。
4.2.对导致凸轮磨损的其他非主要因素也认真控制,特备是凸轮摇臂的面粗糙度的控制和缸头两孔平行度的控制也是非常关键的。