机加工车间危险源识别
机械加工行业危险源辨识与控制清单
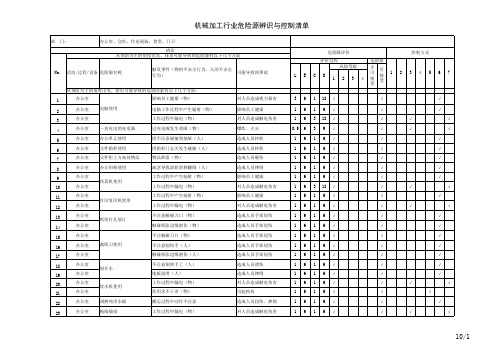
对人员造成伤害
作业现场 79
80
作业现场
清理金属切屑时用手拉或用嘴吹(人) 对人员造成伤害
没戴护目镜(人)
辐射
危险源评价
控制方式
评价过程
危险级
L
E
C
D
风险等级 1234
不 可 接 受
可 接 受
1
2
3
4
5
6
7
1 6 3 18 √ 1 6 3 18 √ 1 6 3 18 √ 1 6 3 18 √ 1 6 3 18 √ 1 6 3 18 √
造成职业病
造成人员伤害及财产损失 发生紧急情况增大损失与 应急救援难度 发生火灾时增加灭火难度 发生火灾时无法确保及时 灭火 造成人员滑倒伤害
造成人员砸伤
作业现场 50
设备接地不良,漏电,发生触电(物) 造成人员伤害
作业现场 51
转动部位楔子突出,无防护罩(物)
绞伤人体
作业现场 52
清洗铁屑无专用工具,操作者未戴护目镜 造成人员眼睛伤害
√
1 6 4 24
√
1 3 1 3√
1 6 1 6√
1 6 7 42
√
1 6 7 42
√
3 6 3 54
√
1 6 7 42
√
1 6 7 42
√
1 6 7 42
√
1 6 7 42
√
1 6 7 42
√
1 6 7 42
√
1 6 3 18 √
√ √ √ √ √ √ √ √ √
√
√
√
√ √ √ √ √ √
√
√
√
√
√
√
√
机加工危险源辨识

车床危险源辨识1、防护用品使用不当(戴手套操作,衣袖、衣襟不紧)易发生绞手,缠卷衣袖危险。
2、安全防护装置有缺陷或被拆卸产生不安全隐患。
3、用手直接抓砂布在工件上磨光;隔着正在加工的工件拿取物体;在加工过程中清理刀具上的铁屑、在切削过程中测量工件,擦试机床等,易发生碾、碰、割伤害事故。
4、加工细长件超过主轴后200mn没有加设防护装置,可发生甩击伤害。
5、卡具装卡不牢或卡压方法不合理。
转动的工、卡具、工件飞出导致事故。
6、加工偏心工件时,没有做好平衡配重,致使工件飞出,造成物体打击事故。
7、卡盘保险销子没有锁紧,工、卡具、工件飞出伤人。
8工、卡、量具摆放顺序交叉,混放不符合要求产生隐患。
9、吊卸工卡具、工件时不符合起重作业安全要求,发生起重伤害。
10、高速切削时未戴防护眼镜、工件未夹紧、用砂布光内孔时,将手指或手臂伸进工件打磨、切断小料时用手接、戴手套操作、切大料时直接切断、一手扶攻丝架(后扳牙架)一手开车会造成机械伤害。
11、机床接地不好,照明灯线裸露,照明未采用安全电压均易生触电事故。
立式车床危险源辨识1、卡具装卡不牢或卡压方法不合理,卡盘上有浮动物件,浮动物件甩出造伤害。
2、未调整工件与刀架间距,刀架与工件相撞造成伤害。
3、卡盘爪或压板超出卡盘,发生刮衣将人绞入。
4、没有穿戴好防护用品或操作不当,易伤人。
5、防护用品使用不当(戴手套操作,衣袖、衣襟不紧)易发生绞手,缠卷衣袖危险。
6、吊卸工卡具、工件时不符合起重作业安全要求,发生起重伤害。
7、机床接地不好;照明灯线裸露,照明未采用安全电压,易发生触电伤害。
钻床危险源辨识1、防护用品使用不当(戴手套操作,衣袖、衣襟不紧)易发生绞手,缠卷衣袖危险。
2、用手扶工件、用手清除铁屑划伤手指;3、在旋转的刀具下,翻转、卡压或测量工件会造成机械伤害。
4、工卡具装卡不牢,飞出伤人;5、员工操作不当或操作失误,造成设备损坏或人身伤害。
7、工件超出操作平台尺寸时支撑架要平稳牢靠,如有摆动或滑移现象易造成重物伤害。
危险源辨识和风险评价清单(机加)
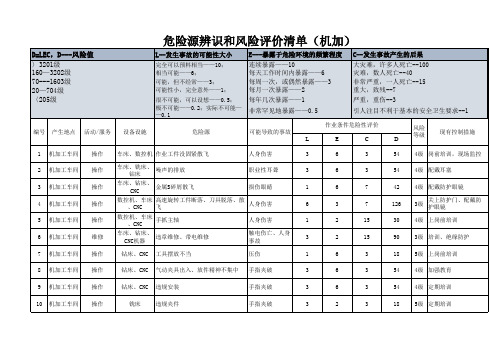
物品掉落 搬运撞伤 搬运撞伤 搬运撞伤 伤人
3
6
3
6
3
6
3
6
0.2
6
33 装配车间
操作
流水线 流水线接口处
易伤手
3
6
34 装配车间 35 装配车间 36 装配车间
操作 操作 操作
流水线 输送带变形 包装机 包装机堵塞时员工用手排除 打包机 打包机漏电
伤人,损坏产品 0.5
1
包装机温度很 高,易伤手
0.1
刀片
使用戒刀片、飞鹰刀片造成人员割 伤
锋利物切割伤
6
6
55 各车间 车间环境
地面
车间地面不平整、有杂物或较滑造 成人员摔倒
摔伤
3
6
56 各车间 车间环境
噪音
车间内机器设备产生的噪音造成听 力下降
噪音
3
6
57
各车间
车间环境
设备设施
车间内摆放的机器设备、办公设施 造成碰伤
碰伤
3
6
58 各车间 车间环境
化学品 使用饮料瓶装化学品
损伤眼睛
15
物品搬运
物料内部转 移
人工搬运
新上架的5G产品过重,搬运时会造 成身体损伤
职业病
16
物品搬运 出入库搬运
机动叉车
机动叉车行駛过快或超重驾驶;叉 运时未看清周边人及物
车辆伤害
17
物品搬运 出入库搬运
机动叉车
机动叉车所叉运物料未作防护,升 降时滑落
车辆伤害
18
物品搬运 出入库搬运
机动叉车
机动叉车驾驶人员没有驾驶证操作 不当
引人注目不利于基本的安全卫生要求--1
机加工车间危险源识别
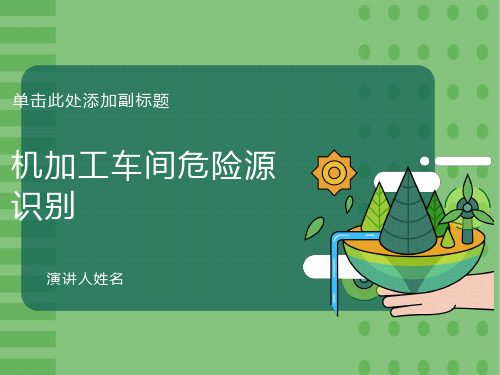
活动内容
物的状态 人的行为 人的行为 安全管理
物的状态
危险源 描 述
机床电器箱柜线路不符合要求
设备维修未切断电源或未采取有 效防护措施
设备维修时配合不当
机床照明未采用安全电压或利用 床身载流导电
金切机床限位、联锁等安全保护 装置无效
系统名称
实训金属切 削机床
活动内容
危险源 描 述
物的状态
金切机床夹具卡具松动,防脱落 装置缺陷
金切机床操作手柄、开关失灵
设备维修未采取有效防护措施或 误操作
系统名称
实训金属切 削机床
活动内容
危险源 描 述
物的状态
未正确穿戴劳动防护用品和正 确使用工具
人的行为
隔着运转、传动部位传递或拿 取物品
人的行为 机床运转时打开机箱或防护罩
人的行为
不用专用工具夹装工件,用手 拿或嘴吹
系统名称
实训金属切 削机床
人的行为
操作时带手套、围巾或敞开衣服
环境因素
工作时高速旋转的钻头、飞溅的 铁屑伤人
人的行为
夹装工件不稳固
人的行为
切削时,手接近切削面
系统名称
活动内容
危险源 描 述
物的状态
刀具的锁紧装置出现故障
物的状态
脚踏板护板出现损坏
实பைடு நூலகம்金属切削机床
物的状态 机床卡盘的锁紧装置出现故障
物的状态
电器柜主电源无挡板
物的状态 现场设备的安全操作规程缺失
金切机床PE连接失效或缺损、电 源线老化破损
在机床头、小刀架、床面上放置 工、量具或其他东西
系统名称
实训金属切 削机床
活动内容
物的状态 物的状态 人的行为 物的状态 物的状态
机加工车间危险源识别课件

其他伤害包括噪声、振动、 辐射等。
01
1. 噪声伤害:高噪声环境可
能导致听力受损。
02
03
2. 振动伤害:长时间接触振 动工具可能导致手臂振动症。
04
05
3. 辐射伤害:紫外线、X射 线等辐射源可能对皮肤和眼
睛造成损伤。
03
危险源的识别方法
直观识别法
总结词
基于经验和直观判断,对危险源 进行初步识别。
管理措施
详细描述
制定并执行安全操作规程,确保 员工正确操作设备设施,防止误 操作引发事故。
总结词:通过制定和执行一系列 安全管理制度和操作规程,规范 员工行为,降低危险源的风险。
建立健全安全管理体系,包括安 全生产责任制、安全检查制度、 隐患排查治理制度等。
加强安全培训和教育,提高员工 的安全意识和技能水平,确保员 工能够自觉遵方安全法规 的要求,确保企业合法合 规生产。
危险源的定义与分类
定义
危险源是指在特定条件下可能产生危 险或危害的根源或条件,包括物理、 化学、生物等方面的因素。
分类
危险源可以根据不同的标准进行分类, 如按性质可分为物理性、化学性、生 物性危险源;按触发条件可分为常温、 高温、高压、静电等危险源。
详细描述
制定安全检查表,列出各项安全要求和标准,对机加工车间 的设备和操作过程进行检查,以发现潜在的危险源。
04
危险源的风险评估
风险评估的方法
风险矩阵法
将危险源的发生概率和可能导致 的后果进行综合评估,形成风险
等级。
概率-后果法
根据危险源发生概率和可能产生的 后果进行评估,确定风险等级。
历史数据法
详细描述
通过观察机加工车间的设备和操 作过程,判断是否存在潜在的危 险源,如机械伤害、触电、火灾等。
机加工车间危险源识别课件
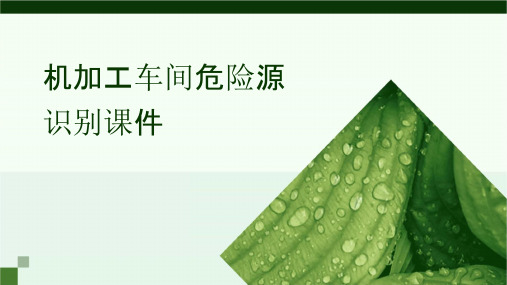
温度和湿度危险源识别
温度危害
机加工车间中,设备的运行会产生大量热量,加上夏季车间内温度往往较高,可能导致操作者中暑、 脱水等健康问题。
湿度危害
机加工车间的湿度过低可能导致操作者皮肤干燥、口鼻喉干燥等不适;湿度过高则可能引发霉菌等微 生物滋生,影响产品质量和操作者健康。
照明和通风危险源识别
要点一
照明危害
不正确的使用机器
不正确的使用机器可能导致机器故 障或工件损坏。
04
操作规程和安全操作规程危险源识别
缺乏安全意识
操作人员缺乏安全意识,不 遵守操作规程,可能导致事
故发生。
1
不明确的安全规定
安全规定不明确或未及时更 新,能导致操作人员无法
正确操作机器。
不安全的机器
机器存在不安全因素,如过 热、磨损等,可能导致事故 发生。
不安全的操作环境
操作环境存在不安全因素, 如噪音、振动等,可能导致 操作人员疲劳或受伤。
04
机加工车间环境危险源识 别
噪声和振动危险源识别
噪声危害
机加工车间中,机床等设备的运行往往会产生高噪声,长期处于这种噪声环境中,可能导致操作者听力下降、心 血管疾病等健康问题。
振动危害
机床运转时产生的振动可能会引起操作者手部疲劳、不适,甚至导致长期的肌肉骨骼损伤。
危险部位,如设计安全装置、使用安全离合器、提供自动停车功能等。
02
操作区域的设计
操作区域应合理布局,留出足够的安全通道和安全出口,避免人员拥挤
和交通阻塞。
03
电器设施的设计
电器设施应符合国家电气安全标准,避免漏电、短路等故障引发火灾或
触电事故。
合理安排工艺流程
工艺流程的优化
机加工危险源辨识、风险评价

机加工危险源辨识、风险评价控制清单
状态:正常-Δ 异常-○ 紧急-∧ 时态:过去-□ 现在-▽ 将来-◇ 辨识方式:直接辨识-☆ 工具仪器仪表-♀ L-发生事故可能性大小(分值:0.1、0.2、0.5、1、3、6、10) E-处危险环境的频繁程度(分值:0.5、1、2、3、6、10) C-救护轻微伤害或经济损失(分值:1、3、7、15、40、100)D-风险性分值=L×E
机加工危险源辨识、风险评价控制清单
状态:正常-Δ 异常-○ 紧急-∧ 时态:过去-□ 现在-▽ 将来-◇ 辨识方式:直接辨识-☆ 工具仪器仪表-♀ L-发生事故可能性大小(分值:0.1、0.2、0.5、1、3、6、10) E-处危险环境的频繁程度(分值:0.5、1、2、3、6、10) C-救护轻微伤害或经济损失(分值:1、3、7、15、40、100)D-风险性分值=L×E
机加工危险源辨识、风险评价控制清单
状态:正常-Δ 异常-○ 紧急-∧ 时态:过去-□ 现在-▽ 将来-◇ 辨识方式:直接辨识-☆ 工具仪器仪表-♀ L-发生事故可能性大小(分值:0.1、0.2、0.5、1、3、6、10) E-处危险环境的频繁程度(分值:0.5、1、2、3、6、10) C-救护轻微伤害或经济损失(分值:1、3、7、15、40、100)D-风险性分值=L×E。
危险源辨识和风险评价记录
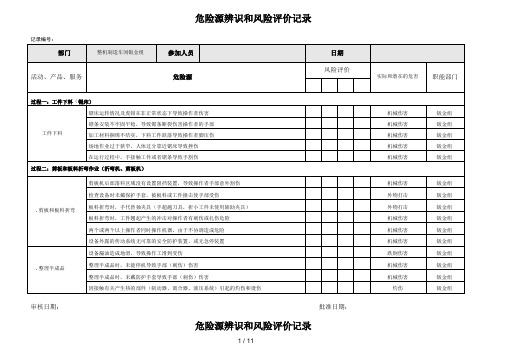
危险源辨识和风险评价记录
审核日期:批准日期:
危险源辨识和风险评价记录
1 / 11
批准日期:
危险源辨识和风险评价记录
审核日期:
批准日期:
危险源辨识和风险评价记录
记录编号:
审核日期:
批准日期:审核日期:
危险源辨识和风险评价记录
记录编号:
批准日期:
危险源辨识和风险评价记录
记录编号:
审核日期:
审核日期:批准日期:
危险源辨识和风险评价记录
记录编号:
批准日期:
危险源辨识和风险评价记录
记录编号:
审核日期:
批准日期:
危险源辨识和风险评价记录
记录编号:
审核日期:
审核日期:批准日期:
危险源辨识和风险评价记录
记录编号:
批准日期:
审核日期:
危险源辨识和风险评价记录
批准日期:审核日期:。
- 1、下载文档前请自行甄别文档内容的完整性,平台不提供额外的编辑、内容补充、找答案等附加服务。
- 2、"仅部分预览"的文档,不可在线预览部分如存在完整性等问题,可反馈申请退款(可完整预览的文档不适用该条件!)。
- 3、如文档侵犯您的权益,请联系客服反馈,我们会尽快为您处理(人工客服工作时间:9:00-18:30)。
系统 名称
活动内容 物的状态
危 险 源 描 述 刀具的锁紧装置出现故障 脚踏板护板出现损坏 机床卡盘的锁紧装置出现故障
实训 金属 切削 机床
物的状态 物的状态
物的状态
物的状态
电器柜主电源无挡板
现场设备的安全操作规程缺失
系统 名称 实训 金属 切削 机床
活动内容 物的状态
危 险 源 描 述 无砂轮机环境监测,所有开关 保持完好 机床安全标识缺陷 在机床头、床面上放置工、量 具或其他物品
物的状态
物的状态
系统 名称
活动内容
危 险 源 描 述
实训 砂轮 机
物的状态 砂轮机护罩缺失 砂轮机无挡屑板或未及时调整 物的状态 间隙 物的状态 砂轮机除尘设施缺陷 物的状态 砂轮机挡屑板、托架间隙过大 物的状态 砂轮片缺陷或选型错误,使用 时碎裂弹出
系统 名称
活动内容 人的行为
危 险 源 描 述 由于在砂轮机上磨削用力过度 或侧面磨削等使用不当,砂轮 碎裂飞出 砂轮机开机没有空转2-3分钟就 立即使用 在砂轮机上磨削用力过度或侧 面磨削 砂轮损伤、受潮、变质、裂纹 等原因碎裂
危 险 源 描 述 漏电保护器失效 违反操作规程带电作业 私自进行电气线路的改动
物的状态
超负载使用
系统 名称
活动内容
危 险 源 描 述
人的行为 磨胶皮,木材等非金属零部件 人的行为 实训 砂轮 机 物的状态 砂轮机上1.8米以下照明未用安 全电压 砂轮片有缺陷或使用时选用型 号错误,造成伤害 砂轮损伤、受潮、变质等原因 碎裂 砂轮机托架失效
活动内容 物的状态
危 险 源 描 述 未正确穿戴劳动防护用品和正 确使用工具 隔着运转、传动部位传递或拿 取物品 机床运转时打开机箱或防护罩 不用专用工具夹装工件,用手 拿或嘴吹
实训 金属 切削 机床
人的行为
人的行为
人的行为
系统 名称
活动内容 物的状态 人的行为
危 险 源 描 述 机床电器箱柜线路不符合要求 设备维修未切断电源或未采取 有效防护措施 设备维修时配合不当 机床照明未采用安全电压或利 用床身载流导电
实训 金属 切削 机床
人的行为 安全管理
物的状态
金切机床限位、联锁等安全保 护装置无效
系统 名称
活动内容
物的状态
危 险 源 描 述
金切机床夹具卡具松动,防脱 落装置缺陷 操作时带手套、围巾或敞开衣 服
实训 金属 切削 机床
人的行为
环境因素
人的行为 人的行为
工作时高速旋转的钻头、飞溅 的铁屑伤人
夹装工件不稳固 切削时,手接近切削面
机加工车间危险源识别
系统 名称
活动内容 环境因素
危 险 源 描 述 路面湿滑 道路照明缺失 人员奔跑经过实训中心大门口 时,被进出车辆碰伤
实训 环境 (道 路)
环境因素 安全管理
环境因素
人的行为
实训中心内道路堆放物料占道
实训中心内违规停放车辆
系统 名称
活动内容 人的行为 物的状态
危 险 源 描 述 机床照明未采用安全电压 金切机床PE连接不可靠、电源 线老化破损 金切机床加工长料没有采用防 弯装置或没有设置防护栏
活动内容
危 险 源 描 述
实训 砂轮 机
人的行为 操作时没有佩戴上防护眼镜 磨工件或刀具时用力过猛撞击 人的行为 砂轮 物的状态 砂轮机金属外壳PE线缺损 人的行为 磨削时未戴护目镜 砂轮机法兰盘与软垫不符合要 物的状态 求 人的行为 同一块砂轮上同时两人操作或 侧面磨削
注意: 1、若有同学发现以上危险源存在的,请立即 报告实习指导老师。
实训 金属 切削 机床
物的状态
人的行为
设备维修时人员配合不当,交 叉作业无人指挥或缺少信息沟 通
系统 名称
活动内容 人的行为 人的行为
危 险 源 描 述 设备维修未采取有效防护措施 设备维修未切断电源 扒、取铁屑未用专用工具或方 法不当
实训 金属 切削 机床
人的行为
人的行为
人的行为
不用专用工具夹装工件,用手 拿
实训 砂轮 机
人的行为
人的行为
物的状态
系统 名称
活动内容
危 险 源 描 述
实训 砂轮 机
物的状态 磨削时未戴防护眼镜 人的行为 安装或工作时站立位置不当 面对着砂轮圆周面进行磨削或 人的行为 在砂轮的侧面磨削 物的状态 砂轮机操作除尘设施缺陷 物的状态 砂轮机径向跳动,震动过大时, 继续使用
系统 名称
系统 名称
活动内容 物的状态
危 险 源 描 述 金切机床安全防护罩盖栏等装 置缺损
物的状态
实训 金属 切削 机床 人的行为 物的状态
金切机床旋转部位的楔、销、 键突出部位大于3毫米
未得到允许,开动别人的设备 或操作不熟练 金切机床操作手柄、开关失灵
物的状态
设备维修未采取有效防护措施 或误操作
系统 名称
隔着机床运转、传动部分传递 或拿取物品
系统 名称
活动内容
危 险 源 描 述
物的状态 实训 金属 切削 机床
安全管理 人的行为 物的状态 物的状态
上重下轻或重心不稳的设备未 安装地脚螺栓固定 无证操作或交无证人员操作
用砂布裹着工件砂光 金切机床PE连接失效或缺损、 电源线老化破损 在机床头、小刀架、床面上放 置工、量具或其他东西
物的状态
物的状态
系统 名称
活控人员私自清扫电控柜内灰 尘 配电箱(柜、板)无PE线 配电箱(柜、板)无盖、外露 带电部分无屏护 周围贮存易燃、易爆物品
实训 配电 箱柜 板
物的状态
物的状态 物的状态
物的状态
乱拉乱接临时线
系统 名称 实训 配电 箱柜 板
活动内容 物的状态 人的状态 人的行为