第一章车工
车工(中级)_第一章56
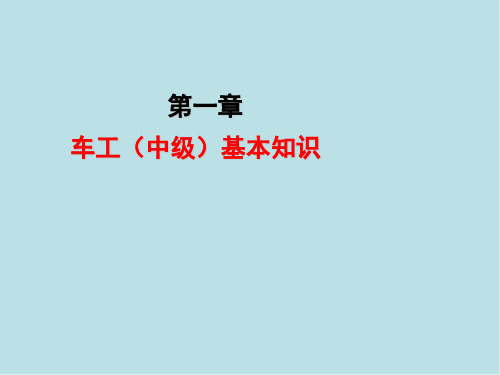
(1)安装 工件经一次装夹后所完成的那一部分工序称为安装。在一 道工序中可以有一次或几次安装。 (2)工位 为了完成一定的工序内容,一次安装工件后,工件与夹具或 设备的可动部分一起相对刀具或设备的固定部分所占据的每一个位置 称为一个工位。
第一节 工艺规程概述
3.工步与进给
工
在加工表面和加工工具不变的情况下,所连续完成的那一
②车φ19、φ12js6外圆放0.5~0.6放磨量,φ25js6
车至φ36
③倒角 端面钻φ2中心孔
2)调头软爪夹φ36外圆
①取总长至74
②车φ32外圆至
320.5 0.6
③钻φ10×32孔 孔口倒角1×60°
第二节 典型零件的工艺分析
工序 4 5
6
7 8 9
工序名称 磨 车
步 部分工序。
进
在一个工步中,若切除的金属层较厚,应分几次切削,每
给 一次切削称为依次进给(走刀),在一个工步中包含一次或几次
进给。
三、生产类型及其工艺特征
单
生产的产品种类很多,而数量不多,只制造一个或几个,
件 生
制造完以后就不再制造,即使再制造也不定期的,这种生产
产 叫做单件生产。
单件生产时,应尽量利用一切现有的通用设备和工具。
四、工序的集中与分散
所谓工序集中是在加工零件的每道工序中,尽可能地多加工 几个表面。
工序分散法是使每个工序中所包含的工作量尽量减少。
第一节 工艺规程概述
五、机械加工工艺规程
1.工艺规程的内容
机械加工工艺规程是规定产品或零部件制造工艺过程和操作 方法的工艺文件。
2.工艺文件
(1)工艺过程卡 即在加工过程中的工艺路线。
《大学车工教案》

《大学车工教案》word版第一章:车工基本概念与安全操作1.1 车工定义与分类介绍车工的定义、分类及应用范围解释车工的基本原理和操作方法1.2 车床结构与功能介绍车床的主要结构部件及其功能解释各种车床的类型和特点1.3 车工安全操作规程讲解车工操作中的安全注意事项分析常见的安全事故原因及预防措施第二章:车工工具与量具2.1 车工工具的分类与使用介绍车刀的类型、用途及使用方法解释刀具的安装和调整方法2.2 量具的分类与使用介绍量具的类型、用途及使用方法讲解量具的校准和维护方法2.3 工具的选用与维护讲解选择合适工具的原则和方法介绍工具的维护和保养方法第三章:车工基本技能训练3.1 车外圆讲解车外圆的原理和方法分析外圆加工中常见问题及解决方法3.2 车内孔讲解车内孔的原理和方法分析内孔加工中常见问题及解决方法3.3 车螺纹讲解车螺纹的原理和方法分析螺纹加工中常见问题及解决方法第四章:车工高级技能训练4.1 车床上孔讲解车床上孔的原理和方法分析上孔加工中常见问题及解决方法4.2 车床端面讲解车床端面的原理和方法分析端面加工中常见问题及解决方法4.3 车床上轴肩讲解车床上轴肩的原理和方法分析轴肩加工中常见问题及解决方法第五章:车工工艺与质量控制5.1 车工工艺流程讲解车工工艺流程的制定和执行分析工艺流程中的关键环节和控制方法5.2 车工质量控制讲解车工质量控制的方法和手段分析质量控制中的常见问题和解决方法5.3 车工精度检验讲解车工精度检验的方法和工具分析精度检验中的常见问题和解决方法第六章:车工自动化与数控技术6.1 车工自动化简介介绍车工自动化的概念、发展历程和应用领域解释自动化车床的组成和原理6.2 数控车床与编程讲解数控车床的定义、特点和应用介绍数控编程的基本知识和方法6.3 数控车工操作与维护讲解数控车工的操作步骤和注意事项分析数控车床维护保养的重要性和方法第七章:车工在制造业中的应用7.1 车工在汽车制造业的应用讲解车工在汽车制造业中的关键作用分析车工技术在汽车零部件加工中的应用7.2 车工在机械制造业的应用介绍车工在机械制造业中的广泛应用分析车工技术在各种机械零件加工中的重要性7.3 车工在其他行业中的应用探讨车工技术在其他行业(如航空、航天、医疗器械等)中的应用和潜力第八章:车工技术创新与发展趋势8.1 车工技术创新的重要性强调车工技术创新对提高生产效率和产品质量的作用分析车工技术创新的驱动力和影响因素8.2 新型车工工具与设备介绍新型车工工具和设备的发展趋势分析其对车工技术的影响和挑战8.3 车工技术的发展趋势预测车工技术未来的发展方向和趋势探讨车工技术如何适应智能制造和工业4.0的发展需求第九章:车工项目实践与案例分析9.1 车工项目实践流程讲解车工项目实践的流程和步骤分析项目实践中的关键环节和注意事项9.2 车工项目案例分析分析具体车工项目案例的成功经验和挑战解决方案从中总结经验教训,为实际操作提供参考9.3 车工项目实践与案例研究的意义强调车工项目实践与案例研究对提高车工技能和经验的重要性探讨如何将实践经验和案例研究应用于实际工作第十章:车工职业规划与发展10.1 车工职业规划讲解车工职业规划的重要性和方法分析车工职业发展的前景和路径10.2 车工技能提升与培训介绍车工技能提升的途径和方法分析车工培训的内容和效果评估10.3 车工职业生涯案例分享分享成功车工职业生涯的经验和故事激励学生制定自己的职业规划并追求车工事业的成就第十一章:车工模拟与CAD/CAM技术11.1 车工模拟技术介绍车工模拟技术的概念和应用解释车工模拟软件的工作原理和操作方法11.2 CAD/CAM技术在车工中的应用讲解CAD/CAM技术在车工过程中的应用分析CAD/CAM技术对提高车工效率和精度的影响11.3 车工模拟与CAD/CAM技术的实践应用探讨车工模拟与CAD/CAM技术在实际车工操作中的应用案例分析实践应用中的经验和挑战第十二章:车工与智能制造12.1 智能制造概述介绍智能制造的概念、特点和应用领域解释智能制造对车工技术的影响和挑战12.2 车工与智能制造的融合讲解车工与智能制造的结合方式和应用案例分析车工在智能制造背景下的发展趋势12.3 智能制造在车工领域的挑战与机遇探讨智能制造在车工领域中面临的挑战和解决方案分析智能制造为车工行业带来的机遇和前景第十三章:车工环境保护与可持续发展13.1 车工对环境的影响讲解车工过程中产生的环境污染和安全隐患分析车工对环境和可持续发展的重要性13.2 车工环境保护措施介绍车工环境保护的方法和手段解释实施环境保护措施对车工企业和员工的好处13.3 车工可持续发展战略讲解车工可持续发展战略的制定和实施分析车工可持续发展对企业和行业的影响第十四章:车工安全与紧急处理14.1 车工安全知识与防护措施讲解车工安全知识,包括个人防护装备的使用、机械安全等分析车工安全事故的原因和预防方法14.2 车工紧急处理与救援介绍车工紧急情况的处理方法和救援措施解释事故发生时的紧急应对和事故调查的重要性14.3 车工安全文化与教育强调车工安全文化的重要性讲解车工安全教育和培训的方法和效果评估第十五章:车工的未来与挑战15.1 车工技术的未来发展趋势预测车工技术的未来发展趋势和应用领域分析车工技术面临的挑战和机遇15.2 车工行业的挑战与应对策略探讨车工行业面临的挑战,如技术革新、市场竞争等讲解应对挑战的策略和方法,以保持车工行业的竞争力15.3 车工教育与培训的改革与发展分析车工教育与培训的现状和问题讲解车工教育与培训的改革和发展方向,以适应未来车工行业的需求重点和难点解析本文主要介绍了《大学车工教案》,涵盖车工基本概念、安全操作、工具与量具、基本技能训练、高级技能训练、工艺与质量控制、自动化与数控技术、制造业中的应用、技术创新与发展趋势、项目实践与案例分析、职业规划与发展等十五个章节。
车工基础工艺指导书
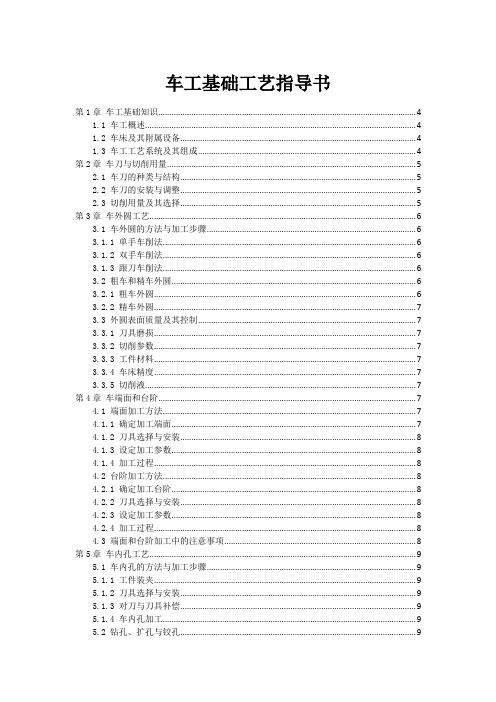
车工基础工艺指导书第1章车工基础知识 (4)1.1 车工概述 (4)1.2 车床及其附属设备 (4)1.3 车工工艺系统及其组成 (4)第2章车刀与切削用量 (5)2.1 车刀的种类与结构 (5)2.2 车刀的安装与调整 (5)2.3 切削用量及其选择 (5)第3章车外圆工艺 (6)3.1 车外圆的方法与加工步骤 (6)3.1.1 单手车削法 (6)3.1.2 双手车削法 (6)3.1.3 跟刀车削法 (6)3.2 粗车和精车外圆 (6)3.2.1 粗车外圆 (6)3.2.2 精车外圆 (7)3.3 外圆表面质量及其控制 (7)3.3.1 刀具磨损 (7)3.3.2 切削参数 (7)3.3.3 工件材料 (7)3.3.4 车床精度 (7)3.3.5 切削液 (7)第4章车端面和台阶 (7)4.1 端面加工方法 (7)4.1.1 确定加工端面 (7)4.1.2 刀具选择与安装 (8)4.1.3 设定加工参数 (8)4.1.4 加工过程 (8)4.2 台阶加工方法 (8)4.2.1 确定加工台阶 (8)4.2.2 刀具选择与安装 (8)4.2.3 设定加工参数 (8)4.2.4 加工过程 (8)4.3 端面和台阶加工中的注意事项 (8)第5章车内孔工艺 (9)5.1 车内孔的方法与加工步骤 (9)5.1.1 工件装夹 (9)5.1.2 刀具选择与安装 (9)5.1.3 对刀与刀具补偿 (9)5.1.4 车内孔加工 (9)5.2 钻孔、扩孔与铰孔 (9)5.2.2 扩孔 (10)5.2.3 铰孔 (10)5.3 内孔表面质量及其控制 (10)5.3.1 刀具磨损 (10)5.3.2 车削参数 (10)5.3.3 工件材料 (10)5.3.4 加工液 (10)5.3.5 车床精度 (10)第6章车螺纹工艺 (10)6.1 螺纹的种类与加工方法 (10)6.1.1 普通螺纹:用于一般的连接和固定作用,分为三角形螺纹、矩形螺纹和圆形螺纹等。
车工基本知识

背吃刀量的计算公式如下
ap
dw
dm 2
(1-1)
图1-9 背吃刀量和进给量
式中
ap——背吃刀量 (mm); dw——工件待加工表面的直径 (mm); dm——工件已加工表面的直径 (mm)。
.
第二节 工件加工的基本知识
2.进给量( f)
刀具在进给运动方向上相对工件的位移量。
3.切削速度 ( v c )
三、车床的型号
CM6140型卧式车床,型号中的代号及数字的含义如下:
.
第一节 车床基本知识
四、车床的润滑及常规保养方法
1. 车床的润滑
(1) 浇油润滑 (2) 溅油润滑 (3) 油绳润滑 (4) 弹子油杯润滑 (5) 黄油(油脂)杯润滑 (6) 油泵循环润滑
图1-6所示是CM6140A型卧式车床的润滑系统位置示意图。
第四节 车刀的基本知识 一、刀具材料 二、常用车刀材料的种类和用途 三、常用车刀的种类和用途 四、车刀的几何参数及其与切削性能的关系 五、车刀和麻花钻的刃磨方法
复习思考题
.
第一节 车床基本知识
一、车床的加工范围
卧式车床能进行内外圆柱面、圆锥面、环槽及成形面、端面、 螺纹、钻孔、扩孔、车孔、铰孔、滚花等,如图1-1所示。
.
第三节 工件定位与夹紧的基本知识
二、车床通用夹具的种类、结构与使用
1.拨动顶尖
(1) 内、外拨动顶尖
图1-17 内、外拨动顶尖 a)外拨动顶尖 b)内拨动顶尖
.
第三节 工件定位与夹紧的基本知识
(2) 端面拨动顶尖
图1-18 端面拨动顶尖 .
第三节 工件定位与夹紧的基本知识
2.弹簧夹头和弹簧心轴
.
第一节 车床基本知识
《车工工艺学教案》

《车工工艺学教案》第一章:车工工艺学概述1.1 课程简介介绍车工工艺学的基本概念、课程目标和教学内容。
1.2 车工工艺的意义和发展解释车工工艺在制造业中的重要性。
探讨车工工艺的历史发展及其现状。
1.3 车工基本术语和概念解释车工行业中常用的专业术语和概念。
第二章:车工工具和设备2.1 车刀的类型和用途介绍不同类型的车刀及其适用场合。
2.2 车床的构造和工作原理解析车床的主要部件及其功能。
阐述车床的工作原理。
2.3 车工夹具和量具介绍车工夹具的类型和作用。
讨论量具的选用和使用方法。
第三章:车工基本工艺3.1 车外圆和端面介绍车外圆和端面的基本工艺方法。
3.2 车内孔和倒角解析车内孔和倒角的车削工艺。
3.3 车螺纹和螺纹加工阐述车螺纹的工艺方法和注意事项。
第四章:复杂零件的车削工艺4.1 车削曲线和曲面介绍车削曲线和曲面的方法和技巧。
4.2 车削组合件和装配解析车削组合件的车削工艺和装配过程。
4.3 车削精度控制和质量评估讨论车削精度控制的方法和质量评估指标。
第五章:车工安全生产和环境保护5.1 车工安全操作规程介绍车工安全操作规程和注意事项。
5.2 车床事故预防和处理解析车床事故的原因和预防措施。
讨论车床事故的处理方法。
5.3 车工环境保护和职业健康阐述车工过程中环境保护的重要性。
讨论车工职业健康问题及其预防措施。
第六章:车工编程与自动化6.1 车工编程基础介绍车工编程的基本概念、方法和常用指令。
6.2 车工自动化的应用探讨车工自动化技术的应用领域和实例。
6.3 CNC车床编程与操作解析CNC车床编程的基本步骤和操作方法。
第七章:车工工艺实验与操作训练7.1 车工工艺实验的组织与实施阐述车工工艺实验的目的、内容和步骤。
7.2 车工操作训练的要求与评价讨论车工操作训练的要求和评价标准。
7.3 车工工艺实验案例分析第八章:车工工艺案例分析与创新8.1 车工工艺案例分析8.2 车工工艺改进与创新探讨车工工艺的改进方法和创新途径。
《车工工艺学教案》

《车工工艺学教案》第一章:车工工艺概述1.1 车工工艺的定义与发展历程1.2 车工工艺的基本要素1.3 车工工艺的作用与地位第二章:车工工具与设备2.1 车工工具的分类与使用2.2 车床的构造与功能2.3 车床的安全操作规程第三章:车工基本技能3.1 车工的基本操作3.2 车外圆、内孔和端面3.3 车螺纹和螺母第四章:车工高级技能4.1 车复杂轴类零件4.2 车球形和圆锥形零件4.3 车非圆形零件第五章:车工工艺的优化与改进5.1 车工工艺的优化方法5.2 车工工艺的改进措施5.3 车工工艺的发展趋势第六章:车工工艺在实际生产中的应用6.1 车工工艺在机械制造中的应用6.2 车工工艺在汽车工业中的应用6.3 车工工艺在航空航天领域的应用第七章:车工工艺的质量和精度控制7.1 车工工艺质量控制的基本原理7.2 车工工艺精度控制的方法与技术7.3 车工工艺质量和精度控制的实践应用第八章:车工工艺的标准化和自动化8.1 车工工艺标准化的意义与作用8.2 车工工艺自动化的发展与现状8.3 车工工艺标准化和自动化的实施策略第九章:车工安全生产与环境保护9.1 车工安全生产的重要性9.2 车工安全生产的措施与方法9.3 车工环境保护的现状与对策第十章:车工工艺的未来发展趋势10.1 新材料在车工工艺中的应用10.2 新技术在车工工艺中的应用10.3 车工工艺发展的前景展望重点和难点解析一、车工工艺概述难点解析:理解车工工艺的内涵及其在制造业中的地位,掌握车工工艺的基本要素及其相互作用。
二、车工工具与设备难点解析:熟悉各种车工工具的用途及其正确使用方法,理解车床的复杂结构与基本功能,遵守车床操作的安全规程。
三、车工基本技能难点解析:掌握车工的基本操作步骤和技巧,精确加工外圆、内孔和端面,正确加工螺纹和螺母。
四、车工高级技能难点解析:处理复杂轴类零件的加工问题,掌握球形和圆锥形零件的加工技巧,应对非圆形零件的加工挑战。
车工工艺学课件第一章

精髓车削法
通过调整刀具的切削角度和切 削深度,使车刀的侧面同时参 与到切削中,适用于加工直径 较大、表面粗糙度要求较高的 工件。
三角刀车削法
三角刀具有三个切削刃,适用 于加工直径较小且深度较大的 工件。由于具有三个切削刃, 相对的工作效率也概述和工 艺路线
在进行车削加工之前,必须 理解加工方法和工艺路线, 以确保加工质量和加工效率。
车床及其构造
床身
车床的主要框架结构。通常由机床铸件制成,其 大小和形状取决于工件的最大尺寸以及加工的精 度等因素。
工具架
安装车刀的工作台,可以上下运动,通常由铸铁 或钢板制成。
主轴
负责旋转工件和切削工具的轴心部分。由电机或 齿轮带动,使用支撑轴承来保持稳定。主轴的精 度直接影响到工件和刀具的加工质量。
车床是加工工件最常用的机床之 一。工件被夹在主轴上,通过一 系列不同类型的车刀进行切削加 工。在车削加工中,设备的稳定 性和精度对于切削质量和生产速 度至关重要。
车削加工可以在生产线的任何阶 段完成。它可以用来加工零部件、 制造原型,以及在批量生产中进 行量产。车削加工不仅可以减少 金属材料的浪费,而且可以提高 工件生产效率。
切削液在金属加工过程中起着重 要的作用。它可以降低切削温度、 减少工具磨损和摩擦力、排除颗 粒物等。
工艺参数的选择
1 刀具材料
2 切削速度
刀具材料的选择直接影响到切削加工的效果 和产出。硬质合金是一种常见的材料,具有 高硬度、高强度、高耐磨性、耐高温等优点。
切削速度是指工件表面上相对于刀具切削速 度的大小。选择合适的切削速度可以在保证 加工质量的基础上,最大化提高生产效率。
3 切削深度
切削深度是刀具与工件的接触长度。合适的 切削深度要根据加工条件、工件材料和切削 工具等方面来进行选择。
第一章 车工绪论
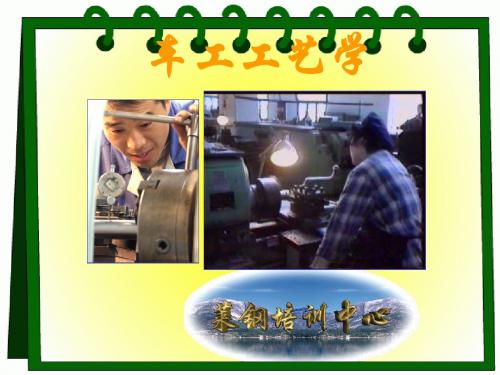
回主页
下一页
退出
四、车刀
1、车刀的种类和用途
(3)切断刀
用来切断工件或切槽 (4)车孔刀 ---用来车内孔
(5)成形车刀:用来车圆弧面和成型面 (6)螺纹车刀:用来车螺纹
回主页
下一页
退出
四、车刀
(7)硬质合金可转位车刀
结构形式 刀片的形状
回主页
下一页
退出
四、车刀
2、车削的基本概念 (1)工作运动切削加工时刀
1、润滑的作用:保证车床正常运转和减少
磨损。 2、车床润滑的主要形式: (1)浇油润滑:车床外露的滑动表面 (2)溅油润滑:齿轮箱内的零件 (3)油绳润滑:车床进给箱 (4)弹子油杯润滑:尾座和中小滑板轴承 (5)黄油杯:交换齿轮架、溜板箱等部位 (6)油泵循环润滑: (注意加油的时间)
回主页 下一页 退出
回主页 下一页 退出
四、车刀
确定车刀切削角度的辅助平面
三个假想平面
回主页
下一页
退出
四、车刀
车刀的主要角度和作用
(1)在正交平面内测量的角度 前角γ0: 前刀面与基面之间的夹角。 —前角的主要作用是使切刃锋利,影 响切削变形和切削力大小,并使切屑 容易排出。
分正副。
主后角α0: 切削平面与主后刀面的夹角。(有副 后角) —减少刀具与工件之间的摩擦状况。 另外有副后角。 回主页 下一页
具和工件之间的相对运动。
1)主运动-消耗机床的主要动力 和形成切削速度。 将切屑切下所必须的基本运动。-工件的旋转 (2)进给运动:使工件上多余的 材料不断被去除的工作运动。 --车刀的运动(纵向、横向)
回主页 下一页 退出
四、车刀
(2)切削加工时形成的三个表面
- 1、下载文档前请自行甄别文档内容的完整性,平台不提供额外的编辑、内容补充、找答案等附加服务。
- 2、"仅部分预览"的文档,不可在线预览部分如存在完整性等问题,可反馈申请退款(可完整预览的文档不适用该条件!)。
- 3、如文档侵犯您的权益,请联系客服反馈,我们会尽快为您处理(人工客服工作时间:9:00-18:30)。
教 案
教学过程:
Ⅰ:清点人数、组织教学 Ⅱ:复习旧课,导入新课 Ⅲ:讲授新课 一、车刀工作图
车刀工作图的作图步骤是:
1、根据车刀的进给方向画出车刀在基面上的投影图,标出主偏角、副偏角和刀尖角;
2、画出主切削刃的延长线,作出剖视图(主截面),标出前角、后角和楔角;
3、画出副切削刃的延长线,作出副剖视力(副截面),标出副偏角、副后角。
4、画出切削平面的右视图,标出刃倾角;
5、画出刀尖的局部放大图。
具体绘制如下图所示;
注记及反馈
二、前角的选择
1、前角的作用
(1)前角主要影响车刀的锋利程度、切削力的大小与切屑变形的大小,前角越大小切屑变形越小。
(2)影响车刀的强度、受力情况和散热条件。
(3)影响加工表面的质量。
2、前角正负的确定(如图)
当前刀面与切削平面之间的夹角小于900时为正前角;反之为负前角。
3、前角的选择
总的原则是:在刀具强度允许的条件下,尽量选择较大的前角。
具体情况应根据工件的材料、刀具材料、加工性质等因素具体选择合理的前角。
(1)加工脆性材料时或硬度较高的材料时应选择较小的前角,加工塑性材料或硬度较低的材料时应选择较大前角。
(2)高速钢材料的车刀前角一般大于硬质合金材料车刀的前角。
(3)精加工时应选择较大的前角,粗加工时应选择较小的前角。
三、后角的选择
1、后角的作用
(1)后角与过渡表面相对,主要影响与过渡表面的磨擦
力,减大的后角要提高工件的表面的质量,处长刀具的寿命。
(2)增在后角虽可使车刀锋力,但会使楔角减小,易造成车刀强度减小,散热条件变差和磨损加快等。
2、后角的正负(如图)
当后刀面与基面间的夹角小于900时为正后角;反之为负后角。
3、后角的选择
(1)粗车进,切削深、进给快,村注车刀有足够的强度,所以应选择较小的后角。
(2)精车时,为保证刀刃锋利,应选择较大的后角。
四、主偏角与副偏角的选择
1、主偏角的作用与选择:主偏角主要影响车刀的散热条件,影响轴向切削力和径向切削力之比,以及断屑情况。
当工件刚性较差时应选择较在原主偏角,车削细长轴时,为减小径向力应选择较大的主偏角,车削硬度高的工件要选择较小的主偏角。
2、副偏角的作用与选择
副偏角主要影响副切削刃与已加工表面的磨擦,影响车刀强度和工件表面粗糙度,尤其在粗精车过程中要注意对副偏角的选择。
五、刃倾角的选择
1、刃倾角的正负
有正负零三种情况:刀尖位于主切削刃最高点时为正,刀尖位于主切削刃最低点时为负,主切削刃与基面平行时为零。
2、刃倾角的作用
主要控制切屑排出的方向、影响刀尖强度和切削的平稳性以及刀刃的锋利程度。
3、刃倾角的选择
其选择主要由工件材料、刀具材料和加工性质决定。
如下图。
Ⅳ、本节小结;刀具的各种角度的作用。
Ⅴ、课外作业:
Ⅵ:教学反馈
教 案
教学过程:
Ⅰ:清点人数、组织教学 Ⅱ:复习旧课,导入新课 Ⅲ:讲授新课
第四节:车刀的磨损及车刀的刃磨
刀具在切削过程中存在磨损的问题,主要有非正常磨损和正常磨损两种形式,非正常磨损主要指切削刃或刀面上产生裂纹、崩刃、卷刃或碎裂等现象。
一、刀具的磨损
这里我们主要介绍车刀的正常磨损。
1、车刀的正常磨损:主要是后刀面的磨损、前刀面的磨损和前后刀面的同时磨损。
如下图所示:
注记及反馈
2、刀具的磨损过程
为分三个阶段:(1)初期磨损阶段,刃磨后的刀具由于表面粗糙度值大,表面层组织不耐磨,所以刚开始切削阶段磨损较快。
(2)正常磨损阶段,刀具经过初期磨损阶段,很快在刀具后刀面上磨出一条较窄的磨损带,使接触面积增大,磨损减小,这个阶段是刀具工作的有效期间,使用刀时不要超出这个阶段,(3)急剧磨损阶段,刀具正常磨损以后,如果不及时刃磨,就会使磨擦增在,切削温度上升,使刀具很快失去切削能力,必须避免这一阶段。
二、刀具的磨损标准及寿命
刀具的磨损标准也称为刀具的磨损限度,是指在后刀面上的那段磨损量,
刀具的寿命是指刀具从开始切削一直到达到磨钝标准为止的总切削时间,也就是两次刃磨刀具的切削时间。
三、车刀的刃磨
1、砂轮的选择
常用的砂轮有氧化铝砂轮和碳化硅砂轮,氧化铝砂轮适用于磨高速钢车刀;碳化硅砂轮适用于磨硬质合金车刀。
2、车刀的刃磨步骤:
(1)在氧化铝砂轮上磨去焊渣并将车刀底平面磨平;
(2)在氧化铝砂轮上将粗磨出刀杆上的主后刀面和副后刀面;
(3)在碳化硅砂轮上粗磨出刀头上的主后刀面和副后刀面;
(4)磨断屑槽;
(5)精磨主后刀面和副后刀面;
(6)磨负倒棱;
(7)磨过渡刃;
(8)用油石修整。
Ⅳ、本节小结;刀具正常磨损的过程和刃磨步骤。
Ⅴ、课外作业:
Ⅵ:教学反馈
教 案
教学过程:
Ⅰ:清点人数、组织教学 Ⅱ:复习旧课,导入新课 Ⅲ:讲授新课
第五节:切削用量的选择
切削用量的选择原则是:
1、粗车时,首先选择一个大的切削深度,其次选择一个较大的进给量,再次选择一个相对合理的切削速度。
2、精车时,进给量应该选得小一些,切削速度应该根据刀具材料选择。
第六节: 金属切削过程
金属的切削过程是指工件上多余的金属层,在刀刃的切割、前刀面的推挤下产生变形滑移而变成切屑的过程。
一、切屑的类型
主要有带状屑、挤裂切屑、单元屑和崩碎屑四种(如下图):
注记及反馈
二、积屑瘤
1、积屑瘤的成因:用中等切削速度车削塑性材料进,由于切屑和前刀面的剧烈磨擦,当切削温度达到一定程度时,而磨擦力超过切屑内部结合力时,一部分金属离开切屑被“冷焊”到前刀面上,便形成了积屑瘤。
2、积屑瘤对切削加工的影响;
(1)粗车时积屑瘤能代替切削刃进行切削,起到了保护前刀面和刀尖的作用。
(2)各屑瘤聚集在刀刃处,增大了车刀的实际前角,能减小切屑变形的切削力。
(3)积屑瘤超出刀尖时能影响尺寸精度,其脱落嵌出工件后会影响工件的加工精度和表面质量。
三、切削力
切削力,是切削时,工件材料抵抗车刀切削所产生的阻力。
影响切削力的因素有很多,主要有工件的材料、切削用量和刀具的几何参数。
四、切削热和切削温度
影响切削热的因素主要有工件的材料,刀具的几何角度和切削用量等,其中影响最大的是切削速度,其次是进给量,而影响最小的是切削速度。
五、断屑
1、切屑的形状
切屑的形状主要有三种:即“C”型屑,带状屑和螺旋切屑。
2、影响切屑的因素:
(1)车刀的几何角度:其中影响最大的前角和主偏角,增大前角切屑变形小,减前小切屑变形大,断屑容易;切削深度增大不易断屑;刃倾角也可以通过改变切屑流的方向而
影响切屑。
(2)切削用量的影响:其中影响最大的进给量,其次是切削深度,再次是切前速度。
(3)断屑槽:有三种,即直线圆弧型、直线型和圆弧型。
第七节:表面粗糙度
一、表面粗糙度:
是指加工表面上较小的间距和微小的峰谷所形成的微观几何不平度。
其值的大小对工件的耐磨性、耐腐蚀性、疲劳强度、配合性质等都有影响。
二、表面粗糙度的影响因素
影响表面粗糙度的因素主要有残留面积、积屑瘤和振动等。
残留面积:车削时,车刀主副切削刃在已加工表面留有痕迹,这些未被切去的部分的截面积就是残留面积。
三、表面粗糙度值大的现象原因及解决措施
1、残留面积中的残留高度较高
解决的方法是:减小主偏角和副偏角、增大刀尖圆弧半径、减小进给量。
2、工件表面有硬点或毛刺
主要是要尽可能地消除积屑瘤的影响。
3、工件表面有振纹
查找振动部位,分析原因,着手解决。
Ⅳ、本节小结;
Ⅴ、课外作业:
Ⅵ:教学反馈
教 案
复习主要内容:
一、车床的组成及各部分功能
主轴变速箱: 交换齿轮箱 进给箱 溜板箱 刀架 尾座
二、车削运动和切削用量
车削运动
切削用量:衡量车削运动大小的参量:主要有三个要素: 切削深度:待加工表面与已加工表面的距离。
进给量:工件每转一周,车刀沿进给方向移动的
距离。
切削速度:主运动的线速度, 三、切削液
作用:冷却、润滑、清洗、防锈。
注记及反馈
种类:乳化液和切削油 强调选择切削液和注意事项。
四、车刀
车刀的种类:外圆车刀、端面车刀、切断刀、内孔
车刀、成形车刀、各种螺纹车刀等。
车刀的组成:前刀面、后刀面、副后刀面、主切削
刃、副切削刃、刀尖。
测量车刀的辅助平面:切削平面、基面、截面。
前角:影响车刀的锋利程度、切削力大
后角:影响车刀的强度、受力情况和散
主偏角:影响车刀的散热条件、影响轴
副偏角:主要影响工件表面粗糙度 刃倾角:主要控制切屑排出的方向、影响刀尖强度的切削的平稳性及刀刃的锋利程度。
五、切削用量的选择:
总的原则是:粗车时,首先选择一个大的切削深度,其次选择一个较大的进给量,再次选择一个相对合理的切削速度。
精车时,进给量应该选得小一些,切削速度应该根据刀具材料选择。
六、金属切削过程及表面粗糙度:
Ⅳ、本节小结; Ⅴ、课外作业:
车
刀的角度。