金属塑性加工技术 4-金属塑性变形力学解析方法
金属材料的塑性变形行为及其动力学机理
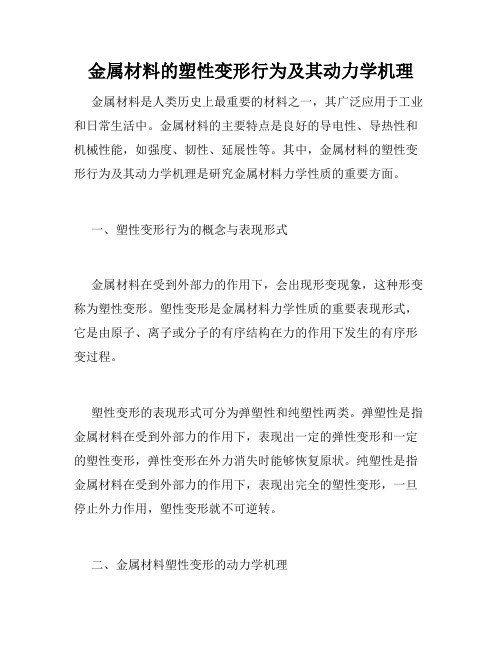
金属材料的塑性变形行为及其动力学机理金属材料是人类历史上最重要的材料之一,其广泛应用于工业和日常生活中。
金属材料的主要特点是良好的导电性、导热性和机械性能,如强度、韧性、延展性等。
其中,金属材料的塑性变形行为及其动力学机理是研究金属材料力学性质的重要方面。
一、塑性变形行为的概念与表现形式金属材料在受到外部力的作用下,会出现形变现象,这种形变称为塑性变形。
塑性变形是金属材料力学性质的重要表现形式,它是由原子、离子或分子的有序结构在力的作用下发生的有序形变过程。
塑性变形的表现形式可分为弹塑性和纯塑性两类。
弹塑性是指金属材料在受到外部力的作用下,表现出一定的弹性变形和一定的塑性变形,弹性变形在外力消失时能够恢复原状。
纯塑性是指金属材料在受到外部力的作用下,表现出完全的塑性变形,一旦停止外力作用,塑性变形就不可逆转。
二、金属材料塑性变形的动力学机理金属材料塑性变形的动力学机理主要包括滑移和剪切。
滑移是指晶格内部原子、离子或分子在外部应力作用下,在一定的晶格面和方向上沿晶格平面错开,使得整个晶体沿应力方向发生了塑性形变。
可以把滑移想象成晶格平面的滑动,其中滑动较容易发生的是(111)面和(100)面。
滑移不仅适用于单晶材料,也适用于多晶和多晶固溶体材料。
剪切是指在晶体中沿着一个晶面剪切另一个晶面而引起塑性形变。
剪切主要涉及到晶界和变形区的相互作用,其中晶界可以作为剪切面。
剪切的能量消耗要比滑移大得多,但是它对温度敏感性比滑移小,容易引起大规模位错滞后和晶界移动。
在金属材料中,滑移和剪切是相互竞争的,它们的作用对金属的塑性变形和强度产生了重要影响。
三、金属材料塑性变形的调节和增强方法金属材料塑性变形的调节和增强主要包括合金化、微结构控制和纳米加工等方法。
合金化是一种有效的方法,可以通过合理选择合金元素来控制晶体结构和化学成分,从而调控金属材料的塑性变形。
例如,添加易形变的合金元素可以促进位错堆积,增加位错密度和位错强度,从而提高金属材料的塑性变形。
第一章 金属塑性变形

图:冷变形金属在加热时组织 和性能的变化示意图
3)晶粒长大 冷变形金属刚刚结束再 结晶时的晶粒是比较细 小、均匀的等轴晶粒, 如果再结晶后不控制其 加热温度或时间,继续 升温或保温,晶粒之间 便会相互吞并而长大。
原因:晶体内部的各种缺陷(特别是位错)的运动更 容易产生滑移,而且位错运动所需切应力远远小于刚 性的整体滑移所需的切应力。当位错运动到晶体表面 时,晶体就产生了塑性变形。
未变形
位错运动
塑性变形
图:晶体中通过位错运动而造成滑移的示意图
2. 多晶体金属的塑性变形
多晶体的塑性变形与单晶体的相同处,在于它也是 以滑移和孪生为其塑性变形的基本方式。但多晶体是由 许多形状、大小、取向各不相同的晶粒所组成,这就使 多晶体的变形过程增加了若干复杂因素,具有区别于单 晶体塑性变形的特点。
首先,多晶体的塑性变形受到晶界的阻碍和位向不 同的晶粒的影响;其次,任何一个晶粒的塑性变形都不 是处于独立的自由变形状态,需要其周围的晶粒同时发 生相适应是变形来配合,以保持晶粒之间的结合和整个 物体的连续性。因此,多晶体的塑性变形要比单晶体的 情况复杂得多。
多晶体塑性变形的特点: • 1、各晶粒变形的不同时性; • 2、各晶粒变形的相互协调性; • 3、多晶体的塑性变形也具有不均匀性。
重要齿轮、连杆、炮管、枪管等; 板料冲压-汽车制造、电器、仪表及日用品。
第一章 金属的塑性变形
第一节 金属塑性变形的实质 金属在外力作用下产生塑 性变形的实质是晶体内部 的原子产生滑移。 1. 单晶体金属的塑性变形
滑移面
单晶体的塑性变形主要通过滑移进行。 整体刚性
滑移
(a)未变形(b)弹性变形(c)弹塑性变形(d)塑性变形 图:单晶体滑移变形示意图
塑性变形与轧制技术:金属压力加工方法
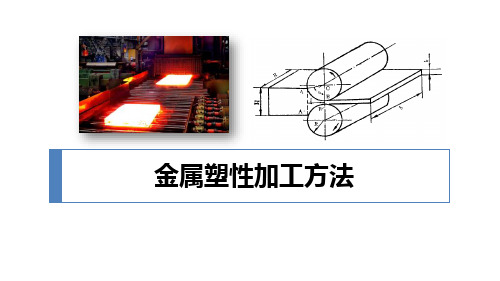
金属塑性加工方法
一、金属塑性加工的概念 二、金属塑性加工的特点 三、金属塑性加工方法
一般零件机械制造方法
铸造
金
属
切削加工:车、铣、刨、磨、钻、铰、插等
零
件
机
压力加工
锻造 自由锻、模锻
械 制 造
塑性成型
冲压 拉深、弯曲、冲裁、 翻边、拉型等方轧制法 Nhomakorabea特种加工
一、什么是塑性加工
2、改善金属组织性能,结构致密,精度高
如:气泡焊合、缩孔压实、疏松压密
3、生产率高,适用于大量生产
连续化、自动化和高速化。
三、金属压力加工的主要方法
常见的压力加工基本方法有:锻造、轧制、挤压、冲压、拉拔等。
锻造
挤压
拉拔
轧制
1、锻造
锻造:用锻锤锤击或用压力机压头压缩工件。 分为自由锻和模锻。
组合加工方法
基本方法 锻造 轧制 挤压 拉拔 冲压 拉伸 ……
组合方法 锻轧 轧挤 拔轧 搓轧 液态铸轧 粉末轧制 ……
谢谢大家!
锻造
2、轧制
轧制:坯料通过转动的轧辊收到压缩,使其断面减小、形状改变、长 度增长。
分为:纵轧、横轧、斜轧。
3、挤压
挤压:把材料放在挤压筒中垫片在挤压轴推动下,迫使金属从一定形 状和尺寸的模孔中挤压出。
分为正挤压和反挤压。
挤压型材
挤压型材模具
其他塑性加工方法
4、拉拔:用拉拔机的钳子把金属料从一定形状和尺寸的模孔中拉出 可生产各种断面的型材、线材和管材。 5、冲压:靠压力机的冲头把板带顶入凹模中进行拉延。 可生产各种杯件和壳体。 6、拉伸成型:用拉伸法成型。
概念:利用金属能够产生永久变形的能力,使其在外力作用下进行塑 性成型的一种金属加工技术,也叫金属压力加工。
4 金属的塑性变形与再结晶(二)

培养学生思考问题、解决问题的能力
教学重点
1、冷变形金属的回复与再结晶
2、热变形对金属组织与性能的影响
教学难点
冷变形金属的回复与再结晶
教学用具
教学方法
阅读法、归纳法、举例分析法
教学手段
课堂授课
课型
理论课
板书内容
1、回复
2、再结晶
3、结晶后的晶粒长大
4、热变形和冷变形
5、热变形对金属组织与性能的影响
提示:去应力退火由于加热温度较低(没有发生晶体结构的改变),所以只是加热时降低了金属的强度,并没有改变组织结构,冷却后材料的性能不会发生改变。
2、再结晶:冷变形组织在加热时重新彻底改变组织的过程称为再结晶。
再结晶的加热温度较高,材料内部组织发生了晶格类型的改变,冷却时由于同素异构转变的原因,原先的组织与性能发生了改变。再结晶后材料的性能取决于加热后的冷却速度。
怀化万昌中专学校备课
年月日(星期)班级:第周总第()课时
课题
4-3冷变形金属的回复与再结晶4-4金属的热塑性变形
教学目标
知识目标
1、了解金属塑性变形的实质
2、了解塑性变形对金属组织和性能的影响
3、冷塑性变形后的回复与再结晶
4、冷、热加工的概念
能力目标
1、金属材料的回复温度、再结晶温度的确定
2、材料冷、热加工状态的判定
3、冷变和热变的区别:热变塑性好,加工容易,无加工硬化现象,材料性能不变或强度、硬度略有增加,适合强度较高的材料或变形量较大的工件;冷变时形变抗力大,塑变后残余应力较大,加工尺寸叫精准,有形变硬化效果,提高材料的硬度和强度,塑性降低,适合塑性较好的材料或变形量较少的工件。
四、热变形对金属组织与性能的影响
塑性变形

第四节 金属的热加工
一、冷加工与热加工的区别
在金属学中,冷热加工的界限是以再结晶温度来划
分的。低于再结晶温度的加工为冷加工,而高于再 结晶温度的加工为热加工。
轧制
模锻
拉拔
如 Fe 的再结晶温度为451℃,其在400℃ 以下的加
工仍为冷加工。而 Pb 的再结晶温度为-33 ℃,则其 在室温下的加工为热加工。热加工动态再结晶 示意图来自 热加工使铸态金属中的
非金属夹杂沿变形方向 拉长,形成彼此平行的
宏观条纹,称作流线,
由这种流线体现的组织
吊 钩 中 的 纤 维 组 织
称纤维组织。它使钢产
生各向异性,在制定加
工工艺时,应使流线分
布合理,尽量与拉应力
方向一致。
滚压成型后螺纹内部的纤维分布
在加工亚共析钢时,发现钢中的F与P呈带状分布,
塑性变形有两种形式:滑移和孪生。
(一)滑移 1. 滑移与滑移带
1)滑移是指晶体的一部分沿一定的晶面和晶向相对于
另一部分发生滑动位移的现象。
⑵滑移常沿晶体中原子密度
最大的晶面和晶向发生。
因为原子密度最大的晶面
和晶向之间原子间距最大,
结合力最弱,产生滑移所
需切应力最小。 沿其发生滑移的晶面和晶向分别叫做滑移面和滑移方 向。通常是晶体中的密排面和密排方向。
完整的等轴晶粒。这种冷变
650℃加热
形组织在加热时重新彻底改
组的过程称再结晶。
T再=0.4T熔 (K)
670℃加热
再结晶也是一个晶核形成 和长大的过程,但不是相变 过程,再结晶前后新旧晶粒 的晶格类型和成分完全相同。 由于再结晶后组织的复原, 因而金属的强度、硬度下降, 塑性、韧性提高,加工硬化 消失。
工程材料—金属的塑性加工
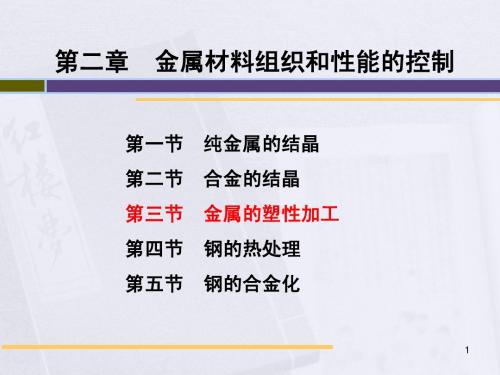
1. 回复
回复是指在加热温度较低时,由于金属中的点缺 陷及位错近距离迁移而引起的晶内某些变化。如空 位与其他缺陷合并、同一滑移面上的异号位错相遇 合并而使缺陷数量减少等。
由于位错运动使其由冷 塑性变形时的无序状态 变为垂直分布,形成亚 晶界,这一过程称多边 形化。
1. 回复
在回复阶段,金属组织变化 不明显,其强度、硬度略有 下降,塑性略有提高,但内 应力、电阻率等显著下降。 工业上,常利用回复现象将 冷变形金属低温加热,既稳 定组织又保留加工硬化,这 种热处理方法称去应力退火。
2.3.1 金属的塑性变形
1.单晶体金属的塑性变形 2.多晶体金属的塑性变形 3.塑性变形对金属组织与性能的影响
2.多晶体金属的塑性变形
(1)不均匀的塑性变形过程 单个晶粒变形与单晶体相似,多晶体变形比单晶体复杂。
2.多晶体金属的塑性变形
(2)晶粒位向的影响
由于各相邻晶粒的位向不同,晶粒间的这种相互 约束,使得多晶体金属的塑性变形抗力提高。
铜拉伸试样表面滑移带
1.单晶体金属的塑性变形 (2) 孪生
孪生是指晶体的一部分沿 一定晶面和晶向相对于另
一部分所发生的切变。
• 发生切变的部分称孪生带或孪晶,沿其发生孪生的 晶面称孪生面。 • 孪生的结果使孪生面两侧的晶体呈镜面对称。
1.单晶体金属的塑性变形
与滑移相比:
孪生使晶格位向发生改变; 所需切应力比滑移大得多, 变形速度极快, 接近声速; 孪生时相邻原子面的相对位移量小于一个原子间距 .
2.3.1 金属塑性变形
2.3.2 金属的回复和再结晶
2.3.3 塑性变形和再结晶在工程应用
2.3.2 金属回复和再结晶
4章 金属的塑性变形与再结晶
③金属的一些强度指标 σe、σs、σb,都是反映金属材料在一定条件下对 塑性变形的抵抗能力。
所以,塑性变形是一个很有用的变形状态。塑性变形为什么会产生 这些现象,它们的机理是什么?另外,经过塑性变形后的零件,再加热 时,又会出现什么情况?这就是本章要学习的内容。
4.1 金属的塑性变形
——单晶体金属的塑性变形 一、单晶体金属的塑性变形
第4章 金属的塑性变形与再结晶
第4章 金属的塑性变形与再结晶
金属在外力作用下,随着力的增加,可先后发生弹性变形、塑性变 形,直至断裂。金属受力后表现的这三个过程,在此要着重研究塑性 变形呢,这是因为在生产实际中存在着许多与塑性变形有关的问题。 例如: ①许多机械零件为了性能和尺寸的要求,要进行压力加工,如:锻造、 轧制、冲压……,这些加工工艺的主要特点,就是使材料的形状和尺 寸在外力的作用下,发生不能自行恢复的变形——塑性变形; ②冷压力加工中的塑性变形还能提高材料的某些力学性能;
3. “形变织构”的产生
4.3 塑性变形对金属组织和性能的影响
——塑性变形对力学性能的影响
二、塑变对力学性能的影响
1. 加工硬化 ——金属经冷塑性变形后,随着塑性变 形量的增加,金属的强度、硬度提高,塑 性、韧性下降的现象。
4.3 塑性变形对金属组织和性能的影响
——塑性变形对力学性能的影响
2. 产生加工硬化的主要原因: 1)位错密度↗——塑性变形时,晶体内部的位错 增殖;(p21图2—15) 2)亚晶粒↗——变形量增加,亚结构细化,亚晶 界阻碍位错运动; (p22图2—18) 3)空位密度↗——点缺陷; (p20图2—11) 4)几何硬化——晶粒由有利位向转到不利位向而 发生几何硬化,使变形抗力增加。 (p64图4—6)
金属塑性加工技术1-金属塑性加工原理-塑性变形力学基础
即
' x xy xz 1 0 0 x xy xz . . ' 0 1 0 y yz y yz m ' . . . . z z 0 0 1
π平面
1 ON σ σ σ 3σ m I1 3
2 m 2 m 2 m
金属塑性加工原理与技术
σ OQ σ 1 2 σ3
2 2
2
(σ 1 σ m )2 (σ 2 σ m )2 (σ 3 σ m )2
1 (2σ 1 σ 2 σ 3 )2 (2σ 2 σ 1 σ 3 )2 (2σ 3 σ 1 σ 2 )2 3 1 (2[(σ 1 σ 2 )2 ] 2[( σ 1 σ 2 )(σ 1 σ 3 ) ] 3 1 3[( σ 1 σ 2 )2 (σ 2 σ 3 )2 (σ 3 σ 1 )2 ] 3 2 2 2 σ e 3τ 8 I 1 3I2 2I 2 3 3
2 2 总应力 P8 8 8
八面体上的正应力与塑性变形无关,剪应力与 塑性变形有关。
金属塑性加工原理与技术
八面体应力的求解思路:
ij (i, j x, y, z) 1, 2 , 3 8 , 8
I1, I 2
求得:
2 2 8 ( I1 3I 2 ) 3
π平面
金属塑性加工原理与技术
π 平面
金属塑性加工原理与技术
例题
• 已知一点的应力状态
6 -4 1 -2 10MP a
金属塑性加工原理与技术
ij 3
2
求该点的主应力值及主轴方向
第四章金属材料的塑性变形与再结晶
滑移方向上原子间距的 小于孪生方向上的原
整数倍,较大。
子间距,较小。
很大,总变形量大。
有限,总变形量小。
有一定的临界分切 压力 一般先发生滑移
所需临界分切应力远高于 滑移
滑移困难时发生
变形机制
全位错运动的结果 分位错运动的结果 34
(二) 多晶体金属的塑性变形
单个晶粒变形与单晶体相似,多晶体变形比单晶体复杂
① 晶界的特点:原子排列不规则;分布有大量缺陷
② 晶界对变形的影响:滑移、孪生多终止于晶界,极少穿 过。
35
当位错运动到晶界附近时,受到晶界的阻碍而堆积 起来,称位错的塞积。要使变形继续进行, 则必须增加 外力, 从而使金属的变形抗力提高。
36
晶界对塑性变形的影响
Cu-4.5Al合金晶 界的位错塞积
55
(4) 几何硬化:由晶粒转动引 起 由于加工硬化, 使已变形部 分发生硬化而停止变形, 而 未变形部分开始变形。没有 加工硬化, 金属就不会发生 均匀塑性变形。
未变形纯铁
加工硬化是强化金属的重要
手段之一,对于不能热处理
强化的金属和合金尤为重要
变形20%纯铁中的位错
56
2 对力学性能的影响
利弊
d. 孪生本身对金属塑性变形的贡献不大,但形成 的孪晶改变了晶体的位向,使新的滑移系开动, 间接对塑性变形有贡献。
33
总结
滑移
孪生
相同点
晶体位向
位移量 不 同 对塑变的贡献 点
变形应力
变形条件
1 切变;2 沿一定的晶面、晶向进行;3 不 改变结构。 不改变(对抛光面 改变,形成镜面对称关系 观察无重现性)。 (对抛光面观察有重现性)
1、晶粒取向和晶界对塑性变形的影响
塑性加工力学课件
x yx zx ij xy y zy xz yz z
X平面
西安建筑科技大学
X方向 Y方向 Z方向
Y平面
Z平面
8
第二章 应力理论
3、全应力的分解: 空间任意点的全应力可表示为:
S j ijli (i, j x, y, z)
二次不变量反映了形状改变的剧烈程度,此表达式会经常用到!
西安建筑科技大学
17
第二章 应力理论
7.应力平衡微分方程:
在外力作用下,尽管变形体内各点应力状态不同,但根据内力 与外力相抗衡原则,变形过程的每一瞬间变形体内任意截取得 单元体仍满足力平衡条件。 平衡微分方程即是表示变形体内无限相邻的任意两点应力状态 之间关系的方程。是求解变形体内应力分布规律的重要方程之 一。 直角坐标系的平衡微分方程 圆柱坐标系的平衡微分方程 球坐标系的平衡微分方程
常规塑性加工,表面力>>体积力。金属变形主要靠表面力 完成。
西安建筑科技大学 6
第二章 应力理论
2、内力与应力:
工件发生塑性变形时,要满足两个基本力学条件,即 (1)外力平衡; (2)应力状态:变形体内产生与外力抗衡的内力; [举例] 简单拉伸试件受力分析!
截面上各点的内力大小方向不同。考虑截面上任意一点M,假设材料为均匀连 续介质,在M点周围区微小区域⊿A,作用的内力为⊿P,则有:
l x cos(N , x ) cos l y cos(N , y ) cos l cos(N , z ) cos z
S x x yx zx l x S y xy y zy l y S l yz z z z xz