谷轮柔性涡旋压缩机应用解析
谷轮压缩机的介绍

美国谷轮全封涡旋压缩机介绍美国谷轮涡旋压缩机技术为中高温制冷应用提供了完美的解决方案.谷轮压缩机压缩机简洁的结构设计为您带来高效和稳定的应用.美国谷轮涡旋压缩机所有部件均密封在隔音外壳内,并底部配有弹性减震装置,最大限度地降低了噪声问题。
美国谷轮涡旋压缩机独特的卸载启动设计使单相压缩机,启动时无须启动电容/继电器,大多数应用中无需曲轴加热器和气液分离器。
美国谷轮涡旋压缩机确保高效能比,涡旋盘磨合而不是磨损,随运行时间的增加表现更好,更高的寿命和可靠性美国谷轮涡旋压缩机特点:美国谷轮涡旋压缩机是高可靠性,高能效比,紧凑型系统设计的理想选择。
使用的制冷剂包括R22R404A R507R134a,等。
美国谷轮涡旋压缩机轴向及径向的谷轮专利柔性设计提供了前所未有的耐液击和容忍杂质的能力,确保涡旋盘间的密封。
美国谷轮涡旋压缩机允许涡旋盘沿径向和轴向分开,碎屑或液体可通过涡旋盘而不损坏压谷轮涡旋压缩机缩机。
使进口压缩机维护更加简便,使用寿命更长,设计寿命为15年。
美国谷轮涡旋压缩机轴向及径向的谷轮专利柔性设计提供了前所未有的耐液击和容忍杂质的能力,确保涡旋盘间的密封。
美国谷轮涡旋压缩机宽广的运行工况范围,带油面测试阀,所有型号均有曲轴箱加热器,可选择带油视镜欧洲谷轮涡旋压缩机介绍:欧洲谷轮涡旋压缩机轴向及径向的谷轮专利柔性设计提供了前所未有的耐液击和容忍杂质的能力,确保涡旋盘间的密封。
欧洲谷轮涡旋压缩机宽广的运行工况范围,带油面测试阀,所有型号均有曲轴箱加热器,可选择带油视镜。
欧洲谷轮涡旋压缩机确保高效能比,涡旋盘磨合而不是磨损,随运行时间的增加表现更好,更高的寿命和可靠性。
欧洲谷轮涡旋压缩机是高可靠性,高能效比,紧凑型系统设计的理想选择。
使用的制冷剂包括R22R404A R507R134a,等。
欧洲谷轮涡旋压缩机特点:欧洲谷轮涡旋压缩机内部没有往复运动机构,所以结构简单、体积小、重量轻、零件少(特别是易损件少)欧洲谷轮涡旋压缩机独特的卸载启动设计使单相压缩机,启动时无须启动电容/继电器,大多数应用中无需曲轴加热器和气液分离器欧洲谷轮涡旋压缩机卸载启动技术,压缩部件在停机后互相分开,压缩机内部全面的压力平衡,无需附加启动装置。
谷轮压缩机
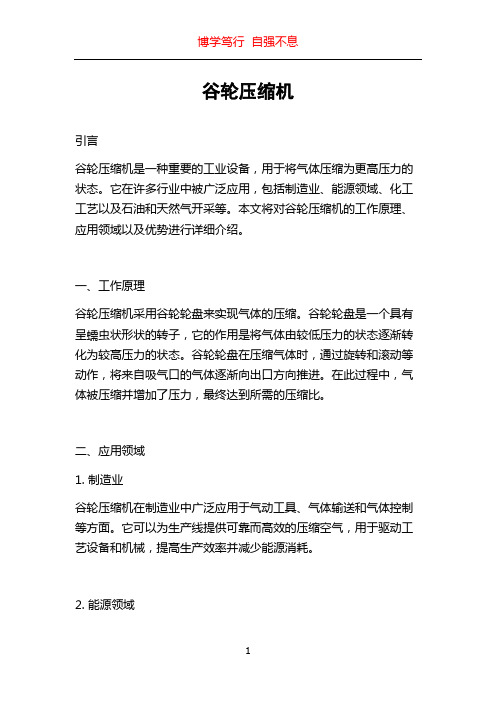
谷轮压缩机引言谷轮压缩机是一种重要的工业设备,用于将气体压缩为更高压力的状态。
它在许多行业中被广泛应用,包括制造业、能源领域、化工工艺以及石油和天然气开采等。
本文将对谷轮压缩机的工作原理、应用领域以及优势进行详细介绍。
一、工作原理谷轮压缩机采用谷轮轮盘来实现气体的压缩。
谷轮轮盘是一个具有呈蠕虫状形状的转子,它的作用是将气体由较低压力的状态逐渐转化为较高压力的状态。
谷轮轮盘在压缩气体时,通过旋转和滚动等动作,将来自吸气口的气体逐渐向出口方向推进。
在此过程中,气体被压缩并增加了压力,最终达到所需的压缩比。
二、应用领域1. 制造业谷轮压缩机在制造业中广泛应用于气动工具、气体输送和气体控制等方面。
它可以为生产线提供可靠而高效的压缩空气,用于驱动工艺设备和机械,提高生产效率并减少能源消耗。
2. 能源领域能源领域对于高效可靠的压缩机要求极高。
谷轮压缩机能够提供稳定的气体压力,使其在发电厂、核电站、石油和天然气工艺以及石油化工等领域得到广泛应用。
它可以用于驱动涡轮机、压缩站和天然气输送管道等设备。
3. 化工工艺化工工艺中需要将气体进行压缩和处理,以满足各种生产需求。
谷轮压缩机能够提供高效的压缩性能,并能适应不同的工作环境和气体成分。
因此,它被广泛应用于化工工艺中的气体压缩、净化、干燥和输送等过程。
4. 石油和天然气开采在石油和天然气开采的过程中,需要进行气体压缩和输送,以满足生产需求。
谷轮压缩机因其高效、可靠和适应性,成为石油和天然气行业的首选设备之一。
它可以用于压裂、注水、气体回收和输送等关键应用中。
三、优势1. 高效可靠谷轮压缩机采用谷轮轮盘来实现气体的压缩,具有高度的压缩效率和良好的稳定性。
它能够提供持续稳定的气体压力,并具有较低的能源消耗和维护成本。
2. 多功能性谷轮压缩机能够适应不同的气体成分和工作环境。
它可以根据不同的需求调整工作参数,以实现最佳的压缩效果。
3. 紧凑型设计谷轮压缩机通常采用紧凑型设计,占用空间小,并且安装和维护简便。
艾默生涡旋变频压缩机和电控解决方案说明书

艾默生全系列涡旋变频压缩机和电控解决方案全面的安全保护和可靠性谷轮涡旋TM 压缩机传承了CoreSense TM 保护技术,将产品可靠性提升到新的高度。
通过将主动保护算法集成于电机控制变频器中,确保压缩机和变频器在各种异常工况运行的安全性。
主要有以下保护特征:• 电机和涡旋温度保护• 电机堵转检测• 相序保护和更正• 最大运行电流检测• 排气温度保护• 频繁启停循环保护该系列变频压缩机产品建立在高度的可靠性和经过验证的高性能基础之上,融合了艾默生25年的涡旋压缩机技术及全世界超过1亿台的运行经验。
为了帮助客户应对变频化的市场趋势,艾默生开发了4~25HP 变频压缩机和变频器的整体解决方案,全系列产品搭载多项创新技术,以业界顶级能效水平助力系统进入能效升级新时代。
结合谷轮引以为豪的喷气增焓技术,超低温环境下也能保证系统强效制热安全可靠。
同时推出的艾默生EVD 系列变频器专门针对永磁电机设计,完美匹配变频压缩机,一站式解决方案帮助客户快速响应市场需求。
变频压缩机型谱图浮动密封圈变容积比涡旋喷气增焓技术(可选)导油管高效集中卷六极永磁电机3.4mm厚壳设计柔性液体刹车容积式油泵谷轮涡旋™变频压缩机优势:• 优异的性能和噪音表现• 卓越的可靠性• 搭载高效艾默生永磁电机有效提升节能效果• 中国研发中心为亚太市场应用量身打造,苏州生产• 广泛适用于变频多联机、柜式空调、地暖等应用• 900-7200rpm 宽广频率范围,让系统设计更加游刃有余• 可变容积比技术(VVR)显著改善涡旋低转速下的能效运行范围喷气增焓(EVI)技术特点:• 专利技术的喷气增焓结构设计• EVI 回路气体进入压缩机后,通过特殊设计的通道注入涡旋, 注入涡旋的气体经过压缩,和吸气口吸入的气体一起排出,进入制冷循环• 喷气增焓带来制热能力的上升和排气温度的降低• 喷气增焓可取代系统辅助电加热艾默生谷轮涡旋™变频压缩机给家用制冷和制热系统带来了变革。
谷轮涡旋

蒸发温度 oC
0 28.73 32.26 35.50 38.16 40.53 42.68 44.68 46.59 48.49 50.44 52.51 17.32 15.64 14.13 12.79 11.59 10.50 9.52 8.60 7.75 6.93 6.12 34.71 38.68 42.25 45.06 47.56 49.86 52.12 54.46 57.01 59.91 63.30 22.23 19.85 17.79 16.00 14.45 13.09 11.88 10.78 9.75 8.75 7.73
13.79 12.46 11.26 10.19 9.20 8.29 7.43 6.61 5.79
26.62 29.63 32.10 34.21 35.95 37.59 39.28 41.14 43.31
17.57 15.76 14.18 12.79 11.55 10.42 9.35 8.31 7.25
电气代码 50 Hz
M 380 - 420 V D 380 - 420 V
60 Hz 460 V
压缩机配置说明
压缩机型号
ZB130KQ/E
ZB150KQ/E ZB190KQ/E ZB220KQ/E
电机代码 TED TWM
BOM配置代码 550 551 522 523
焊接接口 √
√
螺纹接口 √ √
视油镜 √ √ √ √
5 54.11 58.61 62.91 67.00 70.84 74.42 77.72 80.73 83.41 85.75
27.66 24.86 22.33 20.08 18.08 16.33 14.82 13.52 12.43 11.53
涡旋压缩机原理
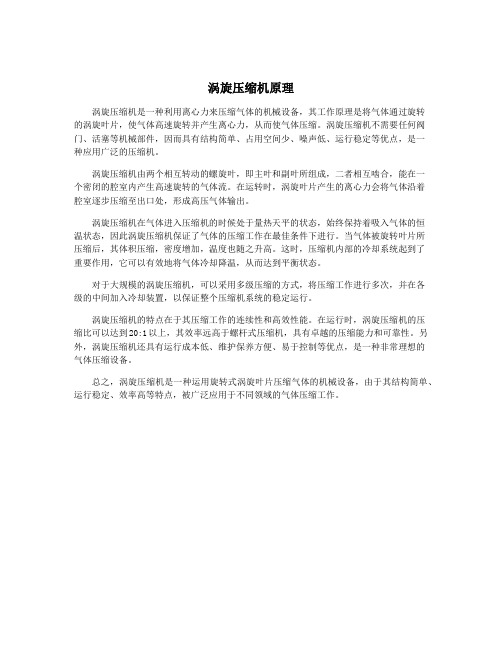
涡旋压缩机原理
涡旋压缩机是一种利用离心力来压缩气体的机械设备,其工作原理是将气体通过旋转
的涡旋叶片,使气体高速旋转并产生离心力,从而使气体压缩。
涡旋压缩机不需要任何阀门、活塞等机械部件,因而具有结构简单、占用空间少、噪声低、运行稳定等优点,是一
种应用广泛的压缩机。
涡旋压缩机由两个相互转动的螺旋叶,即主叶和副叶所组成,二者相互啮合,能在一
个密闭的腔室内产生高速旋转的气体流。
在运转时,涡旋叶片产生的离心力会将气体沿着
腔室逐步压缩至出口处,形成高压气体输出。
涡旋压缩机在气体进入压缩机的时候处于量热天平的状态,始终保持着吸入气体的恒
温状态,因此涡旋压缩机保证了气体的压缩工作在最佳条件下进行。
当气体被旋转叶片所
压缩后,其体积压缩,密度增加,温度也随之升高。
这时,压缩机内部的冷却系统起到了
重要作用,它可以有效地将气体冷却降温,从而达到平衡状态。
对于大规模的涡旋压缩机,可以采用多级压缩的方式,将压缩工作进行多次,并在各
级的中间加入冷却装置,以保证整个压缩机系统的稳定运行。
涡旋压缩机的特点在于其压缩工作的连续性和高效性能。
在运行时,涡旋压缩机的压
缩比可以达到20:1以上,其效率远高于螺杆式压缩机,具有卓越的压缩能力和可靠性。
另外,涡旋压缩机还具有运行成本低、维护保养方便、易于控制等优点,是一种非常理想的
气体压缩设备。
总之,涡旋压缩机是一种运用旋转式涡旋叶片压缩气体的机械设备,由于其结构简单、运行稳定、效率高等特点,被广泛应用于不同领域的气体压缩工作。
涡旋压缩机的特性与应用技术
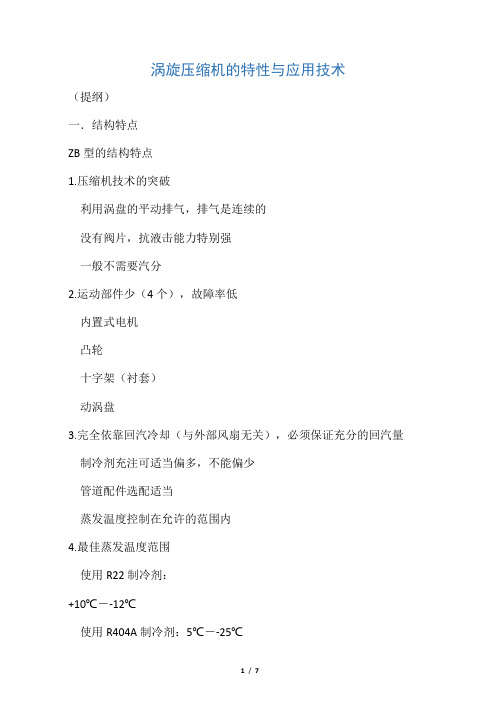
11.适用范围:
一切所以R
22、R134a、R
404A、R
407C、R410的蒸发xx制冷系统
12.压缩机保护器件
压力控制器由于涡旋压缩机有时高低压会快速平衡,对于要求抽空停机的系统需要配合温度控制器或电气延时控制
建议配置相序和缺相保护器(除ZB92KC,ZB11MC和ZF24以上压缩机外)建议配置吸气过滤器防止杂质进入压缩机损坏压缩机涡盘
ZF压缩机的结构和ZB压缩机的异同
最佳蒸发温度范围:
+10℃--40℃(R22和R404A)
吸排气口全部是螺纹连接
全部带油视镜
ZF24以上压缩机都有保护模块
所有ZF压缩机都有喷液冷却口:
ZF18以下压缩机配喷液阀,ZF24以上压缩机配喷液组件(须另配”电磁阀)
其余和ZB型压缩机基本相同
ZF压缩机的低温性能特别好,超过半封闭碟阀压缩机
润滑油失效压缩机运行时视油镜中可见润滑油发黑,低压表压力正常,短时运行系统降温正常压缩机曾经发生过热导致润滑油碳化,系统太脏导致润滑油变性更换润滑油
19.液击
加入太过量的制冷剂压缩机剧烈震动,声音很大立即停机,释放制冷剂至0.3-
0.4MP表压,再次开机,缓慢加入制冷剂,重新调试通常压缩机不会坏
20.压缩机故障及损坏
17.电源跳闸
压缩机刚启动就跳闸电源问题,检查交流接触器或空气开关
压缩机不转,测量显示3相阻值不平衡,绝缘电阻很小压缩机线圈坏
18.压缩机过热原因
回汽量不足排气温度高、高压表压力不高
制冷剂充注太少视液镜中制冷剂不连续,有气泡;(可略多加,不可少加)膨胀阀太小低压表压力偏低,相应蒸发温度低于允许范围(膨胀阀选择留有余量)
数码涡旋压缩机原理(简易)
数码涡旋压缩机:
1、谷轮公司独有的轴向“柔性”密封技术,通过PWM阀的开启和关闭,实现压
缩机的容量调节。
容量调节范围为10%~100%。
2、PWM阀在控制器的控制下,可自由的调节开启——关闭的时间比例,实现“0
——1”输出,体现数码功能。
压缩机运转原理:
1、当PWM阀关闭时,定子上端面压力大于涡旋盘压缩腔压力,将定子向下压紧,实
现定子和转子的密封并负载。
2、当PWM阀开启时,定子上端面的压力与吸气压力一致,此时涡旋盘压缩腔压力大
于定子上端面的压力,将定子托起,使定子和转子脱离,实现卸载。
3、压缩机卸载时,不再对制冷剂进行压缩,故其功率仅为负载时的5%,实现节能。
变容量控制原理
通过压缩机周期性的负载和卸载来实现变容量冷媒控制。
以一次负载加一次卸载的时间为一个控制周期,一般一个周期时间为15~20秒。
通过负载在一个周期内所占时间的比例来实现不同的冷媒输出量,实现无级容量调节。
例如:总能力为10匹,控制周期为20秒。
若要输出5匹的能力,则负载时间占用周期时间的50%,即负载10秒,卸载为10秒即可。
若要输出2匹的能力,则负载时间占用周期时间的20%,即负载4秒,卸载为16秒即可,依次类推。
如下图列举输出能力分别为20%、50%、100%的控制原理图。
谷轮ZW系列(中间补气涡旋)压缩机应用指南
AE4-1381May 2011ZW21 to ZW61KAE and ZW30 to ZW61KSECopeland Scroll® Water Heating CompressorsTABLE OF CONTENTSSection Page Section PageIntroduction (2)ZW**KA Application (2)ZW**KS ApplicationVapour Injection - Theory of Operation (2)Heat Exchanger and Expansion Device Sizing (3)Flash Tank Application (3)Intermediate Pressure and Vapour Injection Superheat (3)Application ConsiderationsHigh Pressure Cut-Out (4)Low Pressure Cut-Out (4)Discharge Temperature Protection (4)Discharge Temperature Control (4)Discharge Mufflers (4)Oil Dilution and Compressor Cooling (4)Electrical Considerations (5)Brazing and Vapour Injection Line (5)Low Ambient Cut-Out (5)Internal Pressure Relief Valve (5)Internal Temperature Protection (5)Quiet Shutdown (5)Discharge Check Valve (5)Motor Protector (5)Accumulators (5)Screens (6)Crankcase Heat-Single Phase (6)Crankcase Heat-Three Phase (6)Pump Down Cycle (6)Minimum Run Time (6)Reversing Valves (6)Oil Type (7)System Noise & Vibration (7)Single Phase Starting Characteristics (7)PTC Start Components (7)Electrical Connections (7)Deep Vacuum Operation (7)Shell Temperature (7)Suction & Discharge Fittings (7)Three Phase Scroll Compressors (8)Brief Power Interruptions ..........................................8Assembly Line ProceduresInstalling the Compressor (8)Assembly Line Brazing Procedure (8)Pressure Testing (8)Assembly Line System Charging Procedure (8)High Potential (AC Hipot) Testing (9)Unbrazing System Components (9)Service ProceduresCopeland Scroll Functional Check (9)Compressor Replacement After Motor Burn (10)Start Up of a New or Replacement Compressor (10)FiguresBrief Product Overview (11)ZW21KAE Envelope (R-134a) (11)ZWKAE Envelope (R-407C, Dew Point) (12)ZWKA Envelope (R-22) (12)ZWKS Envelope (R-22) (13)ZWKSE Envelope (R-407C, Dew Point) (13)Heat Pump with Vapour Injection – EXV Control (14)Heat Exchanger Schematic (14)Heat Pump with Flash Tank (15)Possible Flash Tank Configuration (15)Oil Dilution Chart (16)Crankcase Heater (17)Compressor Electrical Connection (17)Scroll Tube Brazing (17)How a Scroll Works (18)IntroductionThe ZW**KA and ZW**KS Copeland Scroll®compressors are designed for use in vapour compression heat pump water heating applications. Typical model numbers include ZW30KA-PFS and ZW61KSE-TFP. This bulletin addresses the specifics of water heating in the early part and deals with the common characteristics and general application guidelines for Copeland Scroll compressors in the later sections. Operating principles of the scroll compressor are described in Figure 15 at the end of this bulletin.As the drive for energy efficiency intensifies, water heating by fossil-fueled boilers and electric elements is being displaced by vapour compression heat pumps. Emerson Climate Technologies has developed two lines of special water heater compressors to meet the requirements of this demanding application. ZW**KA compressors are designed for lighter duty applications where the ambient temperature does not fall below 0°C and where lower water temperatures can be accepted as the ambient temperature falls. ZW**KS compressors are equipped with a vapour injection cycle which allows reliable operation in cold climates with significantly enhanced heating capacity, higher efficiency, and minimal requirement to reduce water outlet temperatures. Figure 1gives a brief product overview.Water heating is characterized by long operating hours at both high load and high compression ratios. Demand for hot water is at its highest when ambients are low and when conventional heat pump capacity falls off. On the positive side, the system refrigerant charge is usually small, so the risk to the compressor from dilution and flooded starts will usually be lower than in split type air-to-air heat pumps.Water heaters must operate in a wide range of ambient temperatures, and many systems will require some method of defrost. Some systems such as Direct Heating, Top Down Heating or Single Pass Heating operate at a constant water outlet temperature with variable water flow. Others such as Recirculation Heating, Cyclic Heating or Multipass Heating use constant water flow with the water outlet and inlet temperatures both rising slowly as the storage tank heats up. Both system types need to cope with reheating a tank where the hot water has been partially used, and reheating to the setpoint temperature is required. More complex systems deliver water at relatively low temperatures for under-floor heating circuits and are switched over to sanitary water heating a few times per day to provide higher temperature water for sanitary use. In addition, some countries have specific water temperature requirements for legionella control.ZW**KA ApplicationThe application envelopes for ZW**KA compressors are shown in Figures 2 - 4.Appropriate system hardware and control logic must be employed to ensure that the compressor is always operating within the envelope. Small short-term excursions outside the envelope are acceptable at the time of defrost when the load on the compressor is low. Operation with suction superheat of 5 -10K is generally acceptable except at an evaporating tem-perature above 100C when a minimum superheat of 10K is required.ZW**KS ApplicationThe ZW**KS* vapour-injected scroll compressors differ from ZW**KA models in many important details:• Addition of vapour injection• Significantly different application envelopes• Some differences in locked rotor amps (LRA), maximum continuous current (MCC), andmaximum operating current (MOC) – seenameplatesThe application envelopes for ZW**KS compressors are shown in Figures 5 and 6.Vapour Injection – Theory of Operation Operation with vapour injection increases the capacity of the outdoor coil and in turn the capacity and efficiency of the system – especially in low ambient temperatures. A typical schematic is shown in Figure 7. A heat exchanger is added to the liquid line and is used to cool the liquid being delivered to the heating expansion device. Part of the liquid refrigerant flow is flashed through an expansion valve on the evaporator side of the heat exchanger at an intermediate pressure and used to subcool the main flow of liquid to the main expansion device. Vapour from the liquid evaporating at intermediate pressure is fed to the vapour injection port on the ZW**KS compressor. This refrigerant is injected into the mid-compression cycle of the scroll compressor and compressed to discharge pressure. Heating capacity is increased, because low temperature liquid with lower specific enthalpy supplied to the outdoor coil increases the amount of heat that can be absorbed from the ambient air. Increased heat absorbed from the ambient increases the system condensing temperature and in turn the compressor power input. The increase in power inputalso contributes to the improvement in the overall heating capacity.Vapour Injection can be turned on and off by the addition of an optional solenoid valve on the vapour injection line on systems using a thermostatic expansion valve. Alternatively, an electronic expansion valve can be used to turn vapour injection on and off and to control the vapour injection superheat. A capillary tube is not suitable for controlling vapour injection.The major advantage of the electronic expansion valve is that it can be used to optimise the performance of the system and at the same time control the discharge temperature by injecting “wet vapour” at extreme operating conditions.The configurations and schematics shown are for reference only and are not applicable to every system. Please consult with your Emerson Application Engineer.Heat Exchanger and Expansion Device Sizing Various heat exchanger designs have been used successfully as subcoolers. In general they should be sized so that the liquid outlet temperature is less than 5K above the saturated injection temperature at the customer low temperature rating point. At very high ambient temperatures, it will normally be beneficial to turn vapour injection off to limit the load on the compressor motor. Application Engineering Bulletin AE4-1327 and Emerson Climate Technologies Product Selection Software can be used to help size the subcooling heat exchanger and thermal expansion valves, but selection and proper operation must be checked during development testing. Plate type subcoolers must be installed vertically with the injection expansion device connected at the bottom through a straight tube at least 150mm long to ensure good liquid distribution. See the schematic in Figure 8. Flash Tank ApplicationA possible flash tank configuration is shown in Figure9. This particular configuration is arranged to have flow through the flash tank and expansion devices in heating, and it bypasses the tank in defrost mode. The flash tank system works by taking liquid from the condenser and metering it into a vessel through a high-to-medium pressure expansion device. Part of the liquid boils off and is directed to the compressor vapour injection port. This refrigerant is injected into the mid-compression cycle of the scroll compressor and compressed to discharge pressure. The remaining liquid is cooled, exits from the bottom of the tank at intermediate pressure, and flows to the medium-to-low pressure expansion device which feeds the outdoor coil. Low temperature liquid with lower specific enthalpy increases the capacity of the evaporator without increasing mass flow and system pressure drops.Recommended tank sizing for single compressor application in this size range is a minimum of 200 mm high by 75 mm in diameter with 3/8 in. (9.5mm) tubing connections, although it is possible to use a larger tank to combine the liquid/vapour separation and receiver functions in one vessel. A sight tube (liquid level gauge) should be added to the tank for observation of liquid levels during lab testing. See schematic diagram Figure 10 for clarification.It is important to maintain a visible liquid refrigerant level in the tank under all operating conditions. Ideally the liquid level should be maintained in the 1/3 to 2/3 full range.Under no circumstances should the level drop to empty or rise to a full tank. As the tank level rises, liquid droplets tend to be swept into the vapour line leading to “wet” vapour injection. Although this can be useful for cooling a hot compressor, the liquid quantity cannot be easily controlled. Compressor damage is possible if the tank overflows. If liquid injection is required for any reason, it can be arranged as shown in Figures 7 and 9.Since liquid leaves the tank in a saturated state, any pressure drop or temperature rise in the line to the medium-to-low pressure expansion device will lead to bubble formation. Design or selection of the medium-to-low pressure expansion device requires careful attention due to the possible presence of bubbles at the inlet and the low pressure difference available to drive the liquid into the evaporator. An electronic expansion valve is the preferred choice. Intermediate Pressure and Vapour Injection SuperheatPressure in the flash tank cannot be set and is a complex function of the compressor inlet condition and liquid condition at the inlet of the high-to-medium pressure expansion device. However, liquid level can be adjusted, which in turn will vary the amount of liquid subcooling in the condenser (water to refrigerant heat exchanger) and vary the injection pressure. Systems with low condenser subcooling will derive the biggest gains by the addition of vapour injection. Systems operating with high pressure ratios will show the largest gains when vapour injection is applied. Such systems will have higher vapour pressure and higher injectionmass flow. Intermediate pressures in flash tank and heat exchanger systems should be very similar unless the subcooling heat exchanger is undersized and there is a large temperature difference between the evaporator and the liquid sides. Vapour exiting a flash tank will be saturated and may pick up 1 - 2K superheat in the vapour line to the compressor. Vapour injection superheat cannot be adjusted on flash tank systems. Heat exchanger systems will be at their most efficient when the vapour injection superheat is maintained at approximately 5K.APPLICATION CONSIDERATIONSHigh Pressure Cut OutIf a high pressure control is used with these compressors, the recommended maximum cut out settings are listed in Figure 1. The high pressure control should have a manual reset feature for the highest level of system protection. It is not recommended to use the compressor to test the high pressure switch function during the assembly line test.Although R-407C runs with higher discharge pressure than R-22, a common setting can be used. The cutout settings for R-134a are much lower, and the switches must be selected or adjusted accordingly.Low Pressure Cut OutA low pressure cut out is an effective protection against loss of charge or partial blockage in the system. The cut out should not be set more than 3 - 5K equivalent suction pressure below the lowest operating point in the application envelope. Nuisance trips during defrost can be avoided by ignoring the switch until defrost is finished or by locating it in the line between the evaporator outlet and the reversing valve. This line will be at discharge pressure during defrost. Recommended settings are given in Figure 1. Discharge Temperature ProtectionAlthough ZW compressors have an internal bi-metal Therm-O-Disc®(TOD) on the muffler plate, external discharge temperature protection is recommended for a higher level of protection and to enable monitoring and control of vapour injection on ZW**KS* models. The protection system should shut down the compressor when the discharge line temperature reaches 125°C. In low ambient operation, the temperature difference between the scroll center and the discharge line is significantly increased, so protection at a lower discharge temperature, e.g. 120°C when the ambient is below 0°C, will enhance system safety. For the highest level of system protection, the discharge temperature control should have a manual reset feature. The discharge sensor needs to be well insulated to ensure that the line temperature is accurately read. The insulation material must not deteriorate over the expected life of the unit.Discharge Temperature ControlSome systems use an electronic expansion valve to control the vapour injection superheat and a thermistor to monitor the discharge temperature. This combination allows the system designer to inject a small quantity of liquid to keep the discharge temperature within safe limits and avoid an unnecessary trip. Liquid injection should begin at approximately 115°C and should be discontinued when the temperature falls to 105°C. Correct functioning of this system should be verified during system development. It is far preferable to use liquid injection into the vapour injection port to keep the compressor cool rather than inject liquid into the compressor suction which runs the risk of diluting the oil and washing the oil from the moving parts. If some operation mode requires liquid injection but without the added capacity associated with “wet” vapour injection, a liquid injection bypass circuit can be arranged as shown in Figures 7 and 9.Caution: Although the discharge and oil temperature are within acceptable limits, the suction and discharge pressures cannot be ignored and must also fall within the approved application envelope.Discharge MufflersDischarge mufflers are not normally required in water heaters since the refrigerant does not circulate within the occupied space.Oil Dilution and Compressor CoolingThe oil temperature diagram shown in Figure 11is commonly used to make a judgment about acceptable levels of floodback in heat pump operation. Systems operating with oil temperatures near the lower limit line are never at their most efficient. Low ambient heating capacity and efficiency will both be higher if floodback is eliminated and the system runs with 1 - 5K suction superheat. Discharge temperature can be controlled by vapour injection, “wet” vapour injection, or even liquid injection if necessary. In this situation, the oil temperature will rise well into the safe zone, and the compressor will not be at risk of failure from diluted oil. The oil circulation rate will also be reduced as crankcase foaming disappears. Special care needs to be taken at the end of defrost to ensure that the compressor oil is not unacceptably diluted. The system will resume heating very quickly and bearing loads willincrease accordingly, so proper lubrication must be ensured.Electrical ConsiderationsMotor configuration and protection are similar to those of standard Copeland Scroll compressors. In some cases, a larger motor is required in the ZW**KS* models to handle the load imposed by operating with vapour injection. Wiring and fuse sizes should be reviewed accordingly.Brazing the Vapour Injection LineThe vapour injection connection is made from copper coated steel, and the techniques used for brazing the suction and discharge fittings apply to this fitting also. Low Ambient Cut-OutA low ambient cut-out is not required to limit heat pump operation with ZW**KS compressors. Water heaters using ZW**KA compressors must not be allowed to run in low ambients since this configuration would run outside of the approved operating envelope causing overheating or excessive wear. A low ambient cut-out should be set at 0°C for ZW**KA modelsIn common with many Copeland Scroll compressors, ZW models include the features described below: Internal Pressure Relief (IPR) ValveAll ZW compressors contain an internal pressure relief valve that is located between the high side and the low side of the compressor. It is designed to open when the discharge-to-suction differential pressure exceeds 26 - 32 bar. When the valve opens, hot discharge gas is routed back into the area of the motor protector to cause a trip.Internal Temperature ProtectionThe Therm-O-Disc® or TOD is a temperature-sensitive snap disc device located on the muffler plate between the high and low pressure sides of the compressor. It is designed to open and route excessively hot discharge gas back to the motor protector. During a situation such as loss of charge, the compressor will be protected for some time while it trips the protector. However, as refrigerant leaks out, the mass flow and the amperage draw are reduced and the scrolls will start to overheat.A low pressure control is recommended for loss of charge protection in heat pumps for the highest level of system protection. A cut out setting no lower than 2.5 bar for ZW**KA* models and 0.5 bar for ZW**KS* models is recommended. The low pressure cut-out, if installed in the suction line to the compressor, can provide additional protection against an expansion device failed in the closed position, a closed liquid line or suction line service valve, or a blocked liquid line screen, filter, orifice, or TXV. All of these can starve the compressor for refrigerant and result in compressor failure. The low pressure cut-out should have a manual reset feature for the highest level of system protection. If a compressor is allowed to cycle after a fault is detected, there is a high probability that the compressor will be damaged and the system contaminated with debris from the failed compressor and decomposed oil.If current monitoring to the compressor is available, the system controller can take advantage of the compressor TOD and internal protector operation. The controller can lock out the compressor if current draw is not coincident with the contactor energizing, implying that the compressor has shut off on its internal protector. This will prevent unnecessary compressor cycling on a fault condition until corrective action can be taken.Quiet Shut downAll scrolls in this size range have a fast acting valve in the center of the fixed scroll which provides a very quiet shutdown solution. Pressure will equalize internally very rapidly and a time delay is not required for any of the ZW compressors to restart. Also refer to the section on “Brief Power Interruption”. Discharge Check ValveA low mass, disc-type check valve in the discharge fitting of the compressor prevents the high side, high pressure discharge gas from flowing rapidly back through the compressor. This check valve was not designed to be used with recycling pump down because it is not entirely leak-proof.Motor ProtectorConventional internal line break motor protection is provided. The protector opens the common connection of a single-phase motor and the center of the Y connection on three-phase motors. The three-phase protector provides primary single-phase protection. Both types of protectors react to current and motor winding temperature.AccumulatorsThe use of accumulators is very dependent on the application. The scroll’s inherent ability to handle liquid refrigerant during occasional operating flood back situations often makes the use of an accumulator unnecessary in many designs. If flood back is excessive, it can dilute the oil to such an extent thatbearings are inadequately lubricated, and wear will occur. In such a case, an accumulator must be used to reduce flood back to a safe level that the compressor can handle.In water heaters, floodback is likely to occur when the outdoor coil frosts. The defrost test must be done at an outdoor ambient temperature of around 0°C in a high humidity environment. Liquid floodback must be monitored during reversing valve operation, especially when coming out of defrost. Excessive floodback occurs when the sump temperature drops below the safe operation line shown in Figure 11 for more than 10 seconds.If an accumulator is required, the oil return orifice should be 1 - 1.5mm in diameter depending on compressor size and compressor flood back results. Final oil return hole size should be determined through testing. ScreensScreens with a mesh size finer than 30 x 30 (0.6mm openings) should not be used anywhere in the system with these compressors. Field experience has shown that finer mesh screens used to protect thermal expansion valves, capillary tubes, or accumulators can become temporarily or permanently plugged with normal system debris and block the flow of either oil or refrigerant to the compressor. Such blockage can result in compressor failure.Crankcase Heater - Single PhaseCrankcase heaters are not required on single phase compressors when the system charge is not over 120% of the limit shown in Figure 1. A crankcase heater is required for systems containing more than 120% of the compressor refrigerant charge limit listed in Figure 1. This includes long line length systems where the extra charge will increase the standard factory charge above the 120% limit.Experience has shown that compressors may fill with liquid refrigerant under certain circumstances and system configurations, notably after longer off cycles when the compressor has cooled. This may cause excessive start-up clearing noise, or the compressor may lock up and trip on the protector several times before starting. The addition of a crankcase heater will reduce customer noise and light dimming complaints since the compressor will no longer have to clear out liquid during startup. Figure 12lists the crankcase heaters recommended for the various models and voltages.Crankcase Heat – Three-PhaseA crankcase heater is required for three-phase compressors when the system charge exceeds the compressor charge limit listed in Figure 1and an accumulator cannot be piped to provide free liquid drainage during the off cycle.Pump Down CycleA pump down cycle for control of refrigerant migration is not recommended for scroll compressors of this size. If a pump down cycle is used, a separate external check valve must be added.The scroll discharge check valve is designed to stop extended reverse rotation and prevent high-pressure gas from leaking rapidly into the low side after shut off. The check valve will in some cases leak more than reciprocating compressor discharge reeds, normally used with pump down, causing the scroll compressor to cycle more frequently. Repeated short-cycling of this nature can result in a low oil situation and consequent damage to the compressor. The low-pressure control differential has to be reviewed since a relatively large volume of gas will re-expand from the high side of the compressor into the low side on shut down. Minimum Run TimeThere is no set answer to how often scroll compressors can be started and stopped in an hour, since it is highly dependent on system configuration. Other than the considerations in the section on Brief Power Interruptions, there is no minimum off time. This is because scroll compressors start unloaded, even if the system has unbalanced pressures. The most critical consideration is the minimum run time required to return oil to the compressor after startup.Since water heaters are generally of compact construction, oil return and short cycling issues are rare. Oil return should not be a problem unless the accumulator oil hole is blocked.Reversing ValvesSince Copeland Scroll compressors have very high volumetric efficiency, their displacements are lower than those of comparable capacity reciprocating compressors. As a result, Emerson recommends that the capacity rating on reversing valves be no more than 2 times the nominal capacity of the compressor with which it will be used in order to ensure proper operation of the reversing valve under all operating conditions.The reversing valve solenoid should be wired so that the valve does not reverse when the system isshut off by the operating thermostat in the heating or cooling mode. If the valve is allowed to reverse at system shutoff, suction and discharge pressures are reversed to the compressor. This results in pressures equalizing through the compressor which can cause the compressor to slowly rotate until the pressures equalize. This condition does not affect compressor durability but can cause unexpected sound after the compressor is turned off.Oil TypeThe ZW**K* compressors are originally charged with mineral oil. A standard 3GS oil may be used if the addition of oil in the field is required. See the compressor nameplate for original oil charge. A complete recharge should be ~100 ml less than the nameplate value.ZW**K*E are charged with POE oil. Copeland 3MAF or Ultra 22 CC should be used if additional oil is needed in the field. Mobil Arctic EAL22CC, Emkarate RL22, Emkarate 32CF and Emkarate 3MAF are acceptable alternatives. POE oil is highly hygroscopic, and the oil should not be exposed to the atmosphere except for the very short period required to make the brazing connections to the compressor.System Noise and VibrationCopeland Scroll compressors inherently have low sound and vibration characteristics, but the characteristics differ in some respects from those of reciprocating or rotary compressors. The scroll compressor makes both a rocking and a torsional motion, and enough flexibility must be provided to prevent vibration transmission into any lines attached to the unit. This is usually achieved by having tubing runs at least 30cm long parallel to the compressor crankshaft and close to the shell. ZW compressors are delivered with rubber grommets to reduce vibration transmission to the system baseplate.Single Phase Starting CharacteristicsStart assist devices are usually not required, even if a system utilizes non-bleed expansion valves. Due to the inherent design of the Copeland Scroll, the internal compression components always start unloaded even if system pressures are not balanced. In addition, since internal compressor pressures are always balanced at startup, low voltage starting characteristics are excellent for Copeland Scroll compressors. Starting current on any compressor may result in a significant “sag” in voltage where a poor power supply is encountered. The low starting voltage reduces the starting torque of the compressor and subsequently increases the start time. This could cause light dimming or a buzzing noise where wire is pulled through conduit. If required, a start capacitor and potential relay can be added to the electrical circuit. This will substantially reduce start time and consequently the magnitude and duration of both light dimming and conduit buzzing.PTC Start ComponentsFor less severe voltage drops or as a start boost, solid state Positive Temperature Coefficient devices rated from 10 to 25 ohms may be used to facilitate starting for any of these compressors.Electrical ConnectionThe orientation of the electrical connections on the Copeland Scroll compressors is shown in Figure 13 and is also shown on the wiring diagram on the top of the terminal box cover.Deep Vacuum OperationScrolls incorporate internal low vacuum protection and will stop pumping (unload) when the pressure ratio exceeds approximately 10:1. There is an audible increase in sound when the scrolls start unloading. This feature does not prevent overheating and destruction of the scrolls, but it does protect the power terminals from internal arcing.Copeland Scroll compressors(as with any refrigerant compressor) should never be used to evacuate a refrigeration or air conditioning system. The scroll compressor can be used to pump down refrigerant in a unit as long as the pressures remain within the operating envelope. Prolonged operation at low suction pressures will result in overheating of the scrolls and permanent damage to the scroll tips, drive bearings and internal seal. (See AE24-1105 for proper system evacuation procedures.)Shell TemperatureCertain types of system failures, such as condenser or evaporator blockage or loss of charge, may cause the top shell and discharge line to briefly but repeatedly reach temperatures above 175ºC as the compressor cycles on its internal protection devices. Care must be taken to ensure that wiring or other materials, which could be damaged by these temperatures, do not come in contact with these potentially hot areas. Suction and Discharge FittingsCopeland Scroll compressors have copper plated steel suction and discharge fittings. These fittings are far more rugged and less prone to leaks than。
涡旋式压缩机简介及压缩机常见故障暖通吧分享
电源缺相和电压异常
电源电压变化范围不能超过额定电压的±10%三相间的电压不平衡不能超过3%如果发生缺相时压缩机正在运转它将继续运行但会有大的负载电流电机绕组会很快过热正常情况下压缩机会被热保护当电机绕组冷却至设定温度接触器会闭合但压缩机启动不起来出现堵转并进入堵转-热保护-堵转死循环 如果缺相发生压缩机启动时压缩机将启动不起来出现堵转进入堵转-热保护-堵转死循环 电压不平衡百分数计算方法为相电压与三相电压平均值的最大偏差值与三相电压平均值比值. 作为电压不平衡的结果在正常运行时负载电流的不平衡是电压不平衡百分点数的4-10倍
空调压缩机国内主要生产企业
优点: 结构简单、体积小、重量轻与活塞压缩机比:零件减少90%、体积减小40%、重量减轻15% 无吸排气阀减少了易损件降低吸排气阻力损失降低噪音与振动易于实现变转速 无余隙容积容积效率提高 不直接接触采用油膜密封摩擦损失小机械效率高 多压缩室同时工作工作连续压缩力矩变化平稳 缺点: 精度要求高形位公差都在微米级 无排气阀变工况性能欠佳 工作腔不易实施外部冷却压缩过程的热量难排出因此只能够压缩绝热指数小的气体或者内冷却 大排量涡旋压缩机难实现受齿高限制排量大直径大不平衡旋转质量增大机器不紧凑且重量增加
高压腔与低压腔涡旋压缩机特点
高压腔涡旋 压缩机结构
排气口
吸气口
定盘
动盘
机架
曲轴
电机定、转子
壳体
防自转滑环
主轴承
内置式过流、过热保护器
压差供油
低压腔涡旋压缩机结构
排气口
吸气口
定盘
动盘
机架
曲轴
电机定、转子
壳体
防自转滑环
主轴承
离心供油
壳体内高低压分隔板
高压腔结构
涡旋式汽车空调压缩机简介讲解
涡旋式汽车空调压缩机简介涡旋式压缩机是自上世纪八十年代发展起来的一种高效率、低噪音、高可靠性压缩机。
凭借着这些优点,涡旋式压缩机在制冷行业得到了迅猛的发展。
目前已经广泛的应用于家用空调,中央空调、汽车空调,空气压缩等各个领域。
在汽车空调领域中,涡旋式压缩机被称为第三代压缩机,正在以其独特的性能优势逐渐代替传统的斜盘式压缩机和旋转式压缩机。
涡旋式压缩机在制冷系统中的卓越性能表现,使得时隔20年的今天,它依然是专家学者研究的热点。
从家用空调认识涡旋式压缩机1、认识涡旋式压缩机国内大部分用户对涡旋式压缩机的认识,可能首先是从家用空调开始的。
家用空调压缩机经历了活塞式、旋转式、涡旋式等几个发展阶段。
活塞式、旋转式压缩机目前多用于窗机、分体机等匹数较低的机型。
而柜机由于其系数较高,活塞式、旋转式压缩机已不能充分满足其整机匹配的需要,只有采用涡旋式压缩机才能保持较高的热效率和能效比。
2、涡旋式压缩机的优点涡旋式压缩机的能效比高(高效率),意味着与其他压缩机相比,在提供相同制冷量的情况下,涡旋式压缩机耗功要小得多,也就是节能,对于家用空调而言就是省电。
涡旋式压缩机的另一个优点就是噪音低,一般比活塞式压缩机低3~5dB (A),是家用静音空调的基础。
涡旋式压缩机的再一个优点就是可靠性高。
设计原理和较少的零部件为其高可靠性提供了充分的保证。
功耗、噪音、可靠性是用户对家用空调选择的重要依据。
由于涡旋式压缩机具有的高能效比、低噪音和高可靠性等诸多优点,涡旋式压缩机已经越来越多的被用于家用空调系统和中央空调系统。
在中、大型中央空调机组上,一个明显的趋势就是应用螺杆和涡旋技术。
活塞机在3年前还处于主导地位,现在的市场份额却急剧下降到10%左右。
世界上第一台涡旋式压缩机于1983年由日立发明制造,在世界上被公认为涡旋式压缩机的“鼻祖”。
其专利变频涡旋式压缩机及其一直领先的制造技术在日本被公认为该领域的标志。
家用空调的节能技术主要有变频系统和数码涡旋系统。
- 1、下载文档前请自行甄别文档内容的完整性,平台不提供额外的编辑、内容补充、找答案等附加服务。
- 2、"仅部分预览"的文档,不可在线预览部分如存在完整性等问题,可反馈申请退款(可完整预览的文档不适用该条件!)。
- 3、如文档侵犯您的权益,请联系客服反馈,我们会尽快为您处理(人工客服工作时间:9:00-18:30)。
热泵系统一般都需要 回油孔的孔径一般在1.5mm左右 低温制热试验以确定气分的大小及回油孔是否合适 判定依据以压缩机底部温度高于吸气温度10C以上
排气消音器
单冷型 - 可不加消音器 热泵型 - 不经过测试,需加消音器 – 空腔型消音器 – 消音器距压缩机15~45cm范围以内 – 消音器的横截面与进口面积之比在20:1至30:1范围内 – 消音器的长度一般在10~15cm
高低压保护器
Summit系列 – 高压保护 - 需要 没有内置压力释放阀(IPR阀) 压力设定值应小于30Kg/cm2 高压保护动作后应为人工复位
–
–
低压保护 - 需要 低压保护动作后应为人工复位 单冷应用 - 不低于2Kg/cm2 热泵应用 - 不低于0.5Kg/cm2 四通换向阀动作或制热启动时,低压保护有可能误动作,可 采取暂时旁通的方法,时间不超过60秒
曲轴箱加热器的功率 Quantum和Quest系列 Summit 系列
70W 90W
初次开机前,曲轴箱加热器应通电12~24小时,防止油被稀释和轴 承应力过大
排气管温度保护器
排气温度要求小于145 º C Quantum和Quest系列 - 不需要 – 具有内置热蝶(TOD)排气温度保护器 Summit系列热泵应用时 - 需要 – 排气管温度保护器的设定值不高于135 º C – 排气管感温包的位置距压缩机排气管接口小于15cm – 排气管温度保护器动作后应为人工复位 – 如果是自动复位应对一段时间内的保护次数进行限定 – 排气管温度保护器动作后至少应有30分钟的延时
谷轮柔性涡旋压缩机应用
压缩机型号
型号举例
ZR144KC-TFD-522
ZR:空调涡旋 匹数:144/12 = 12匹 冷量:144000x(5/6)x0.3 = 36000W(ARI工况) TFD:三相+内置保护+380V/50Hz 522:焊口、四脚、带接地螺钉
压缩机选型
Calculator计算软件 产品样本 因特网在线产品信息(OPI)
高真空运行保护
不允许作为系统抽真空用
只允许在运行范围内作抽空循环用 长时间低压运行会造成涡旋盘和轴承的损坏
当压缩比达到10:1左右时,压缩机会自动卸载(浮动密封动作), 从而防止产生电弧。
膨胀阀系统在低负荷时提供储液功能 确保膨胀阀前液体为纯液体 提高膨胀阀系统对制冷剂充注量的容忍性
吸气气液分离器结构
A
B
A
B
C
D
吸气气液分离器功能
毛细管系统在低负荷时提供储液功能 除霜前后提供暂储液功能 回油孔大小将影响回液多少 回油孔滤网过小易堵塞回油孔,我们建议为30目
吸气气液分离器使用
膨胀阀系统
过热度控制好,整体能效高,选择泄孔型将有助于启 动,但价格高,感温包位置较为关键
膨胀阀系统的负荷调节能力好,单冷热泵都适合
低环境温度制热也建议使用一个较制冷小的膨胀阀
热泵应用时பைடு நூலகம்过试验来确定制热可允许的最低环温
热泵应用建议配合使用高压储液器和分液头
高压储液器结构
高压储液器功能
高低压保护器
Quantum和Quest系列 – 高压保护 - 不需要 具有内置压力释放阀(IPR阀) 当压力超过26~32Kg/cm2时,IPR阀会打开 高压排气直接进入内置保护器区域并使其动作
–
低压保护 - 一般不需要 如果担心以下情况,可考虑加低保护: A。制冷剂泄漏,排气温度保护会动作,但会自动复位 B。有液管阀或热力膨胀阀时,防止未打开 低压保护动作后应为人工复位
在线产品信息OPI
提供各种方式查找需要的压缩机 提供下载所有压缩机的性能参数(PDF格式) 提供下载压缩机外形尺寸图(PDF或DXF格式) 提供电气参数如RLA、LRA、静态电阻 充油量 Calculator等软件及应用指南(英文)下载
在线产品信息OPI
网站: 点击 Online Product Information 新用户应先注册 输入用户名和密码
Calculator计算软件
提供各种方式查找需要的压缩机 包含谷轮所有压缩机的参数,可生成PDF文件 任一工况下冷量、功耗、能效比 提供性能参数表 提供电气参数如RLA、Imax、LRA
产品样本
只包含一种平台的压缩机 性能参数表不详细 提供压缩机外形尺寸图 提供电气参数如RLA、LRA、电容 充油量 附件信息
系统设计考虑因素
毛细管和膨胀阀 高压储液器与吸气气液分离器 排气消音器的使用 压缩机保护器的选择 压缩机参数测量
毛细管系统
低成本 停机时压力很快平衡,但无法阻止制冷剂流动 对制冷剂充注量很敏感,只能优化于某一点 毛细管系统的负荷调节能力差,单冷型较适合 热泵应用时在低环境温度制热易发生过量回液 热泵应用时通过试验来确定制热可允许的最低环温
压缩机电流值定义
LRA:堵转电流,可从样本、Calculator软件、OPI上找到
Imax:最大运行电流,在最高蒸发、最高冷凝温度且电压为90% 额定值下的电流,也是压缩机能够正常工作的最高电流 RLA = MCC/1.4,MCC:保护器动作前的电流,即在Imax工况 下,将电压继续下降直到保护器动作时的电流
内置电机保护器
可同时感应温度和电流 单相:对运行绕组和启动绕组均起保护。有故障时,保护器切断 公共端 三相:连在Y型电机中心,对三相均起保护。只要其中一相有故 障,保护器同时切断三相,包括缺相情况 由于是自动复位,我们建议增加一个电流互感器来帮助确定是否 压缩机已内保动作 如果希望另加过流保护器且在压缩机内保之前动作,设定值应界 入Imax和MCC之间
压缩机保护器的选择
曲轴箱加热器
排气温度保护 高低压保护 电机保护 真空运行保护
曲轴箱加热器
当系统充注量超过极限充注量时,需要加曲轴箱加热器 极限充注量的规定 Quantum系列 Quest 系列 Summit 系列
单相:3.6x1.2=4.3Kg 且环境温度变化很大 三相:3.6Kg 4.5Kg 7 Kg