Effects of interfacial transition zones
The effect of climate on acoustic signals中文翻译

气候变化对声学信号的影响:大气吸声是否会对鸟的歌声和蝙蝠的定位叫声造成影响?生态学和进化生物学系,图森,亚利桑那大学,1041东洛厄尔街,亚利桑那州85721 沿着生态梯度的信号差异可能会导致新物种生成。
目前的研究验证了这个假说,沿气候梯度的声音吸收的变化为声学信号的差异做出了选择,这不仅有助于理解物种的多样性,而且对了解生物如何应对气候变化也有帮助。
由于吸声会随温度、湿度和声音频率而变化,个体或物种的信号结构可能会随空间或时间上的气候变化而改变。
特别是具有较低频率、较窄带宽和较长持续时间的信号在高吸声环境中应该会更易检测到。
通过研究北美木莺和美国西南地区的蝙蝠,这项工作发现了信号结构和吸声之间存在关联的证据。
整个活动范围具有较高的平均吸收值的莺鸟更可能具有较窄带宽的歌声。
在具有较高吸收值的栖息地发现的蝙蝠种类更可能有较低频率的叫声。
此外,蝙蝠的定位叫声结构会随着季节而变化。
在具有较高吸声的雨季中,蝙蝠会使用具有较长持续时间、较低频率的叫声。
这些结果表明,尽管吸声的影响不算太大,但由于吸声的变化,信号可能会随着气候梯度发生改变。
1 绪论因为环境会影响声学和视觉信号从信号发送者到接收者的传输方式(Morton, 1975; Wiley 和Richards, 1978; Richards 和Wiley, 1980; Endler,2000),所以信号系统往往会沿生态梯度发生改变(Hunter 和Krebs,1979; Wiley, 1991; Marchetti,1993;Badyaev和Leaf,1997;McNaught and Owens, 2002;Slabbekoorn and Smith, 2002; Tobias et al., 2010)。
这种改变对于物种的形成和多样化有重要意义,因为信号方面的变化可能导致合子前隔离(West-Eberhard, 1983; Endler, 1992;Schluter 和Price, 1993; Grant 和Grant, 1996; Irwin 等,2001)。
粉磨方式对混凝土强度和耐久性及水泥性能的影响

引言立磨作为料床粉磨的代表设备,其在水泥终粉磨系统中具有节能、工艺布置简单、水泥质量稳定、易操作维护、占地面积小和环保等独特优势,在国内外水泥粉磨生产中已经被广泛应用[1]。
目前,立磨终粉磨系统与辊压机+球磨联合粉磨(以下简称联合粉磨)系统已经发展成为水泥粉磨技术的主流。
传统思维认为采用球磨作为粉磨设备时所得的成品颗粒近似为球状或椭球状结构,而采用立磨作为粉磨设备时所得的成品颗粒多为片状和针状结构的混合物,因此立磨不适合粉磨水泥熟料[2]。
但随着立磨技术的升级,立磨水泥的需水性能和净浆流动性能达到甚至超过球磨机[3-5]。
目前,学术界和业界对立磨粉磨水泥的工作性能逐渐改观,其流动性好,在实际施工中逐渐得到了认可。
然而,对立磨水泥制备混凝土的强度和耐久性问题研究较少,需要进一步探究立磨粉磨方式对混凝土强度和耐久性的影响。
本文通过对同一水泥厂家分别采用立磨和联合粉磨生产的水泥进行性能测试,对比两种水泥制备的混凝土粉磨方式对混凝土强度和耐久性及水泥性能的影响张海姣1 李 扬2 赵宇翔2 焦留军3 郑永超21. 北京建筑材料检验研究院股份有限公司 北京 1000412. 北京建筑材料科学研究总院有限公司 固废资源化利用与节能建材国家重点实验室 北京 1000413. 唐山冀东装备工程股份有限公司 河北省水泥装备技术创新中心 河北 唐山 063000摘 要:立磨粉磨方式已逐渐成为制备水泥的主流生产方式之一,但目前尚不清楚立磨粉磨方式是否会对水泥混凝土的强度和耐久性产生影响。
本文通过测试立磨水泥与辊压机+球磨联合粉磨水泥制备的混凝土的强度和耐久性,研究立磨水泥和辊压机+球磨联合粉磨水泥的粒度分布、水化放热及其制备的混凝土的微观形貌。
结果表明:立磨水泥粒度小于3 μm的比例较小,早期水化速率较慢,导致其早期强度略微低于辊压机+球磨联合粉磨水泥;两种水泥制备的混凝土的界面过渡区致密性均较好,耐久性表现良好;立磨水泥与辊压机+球磨联合粉磨水泥的强度和耐久性基本一致。
IP专用承载网网络规划和路由部署的方法

(1)核心层:由核心节点和相关中继链路构成,实现全网省际业务的转接功能。
通常核心节点CR(Core Router,核心路由器)设置在业务量大且具备完善省际传输汇接条件的枢纽城市,比如广州、成都、武汉。
(2)汇聚层:由汇聚节点和相关中继链路构成,实现各省业务向核心层网络的汇聚。
一般汇聚节点BR(Border Router,边界路由器)设置在各个省会城市,比如南宁、长沙。
(3)接入层:由接入节点和相关中继链路构成,实现各地市业务向汇聚层网络的汇聚,接入节点AR设置在具有业务接入需求的各个省内地市。
1.1 网络拓扑规划每个层级的网络节点设备成对互联,接入层和汇聚层的网络节点成对上联到上一层级设备,形成“口”字型的互联模式。
这样规划的目的是提高承载网络的安全性,如果单边设备出现故障,成对设备中的另一个设备可以承载故障侧的业务,使业务不受影响。
核心层的CR设备采用的是“双星”型结构,进一步提高了核心节点之间的鲁棒性。
在汇聚层和接入层,考虑到降低链路成本和网络复杂性,以及遵循最少链路、高速链路设置原则,因此并不设置成对设备之间的互联。
1.2 链路轻载要求在“口”字型网络结构中,虽然单边设备可以作为冗余保护业务,但是也会带来另一个隐患问题。
如果单边设备所承载业务流量过大,就会导致流量拥塞,因此需要保证单边链路的流量在正常情况下始终处于轻载状态,即单边链路峰值带宽利用率一般设置为<40%。
如果某一边设备出现故障,业务就会叠加到成对设备中的另一边上,总的链路峰值带宽利用率会低于2×40%=80%,从而保证业务不受影响。
2 路由规划部署IP承载网在IGP(Interior Gateway Protocol,内部网关协议)层面上使用ISIS(Intermediate System to Intermediate System,中间系统到中间系统)路由协议,在level-2路由域上运行,而转发层面使用的是MPLS多协议标签交换体系中的LDP(Label Distribution Protocol,标签分发协议),以VPN 的形式承载不同业务,可运行MPLS-VPN和MPLS-BGP(Border Gateway Protocol,边界网关协议)这两个协议。
Influence of the interfacial zone on the chloride diffusivity of mortars
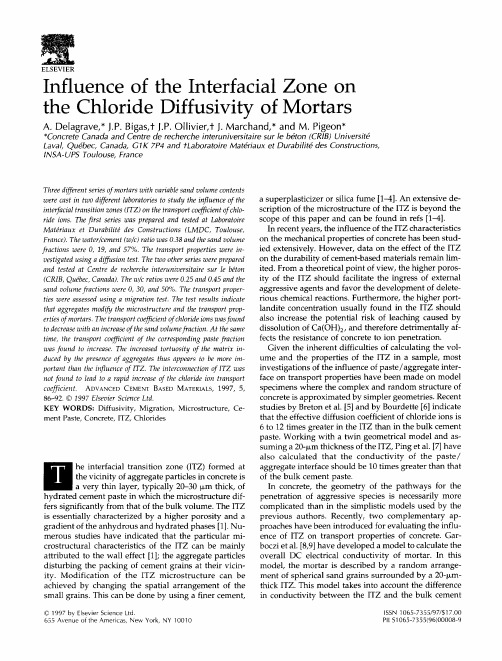
Influence of the Interfacial Zone
*Concrete Canada and Centre de recherche interuniversitaire sur le b6ton (CRIB) Universit6 Laval, Quebec, Canada, GI K 7P4 and tLaboratoire Mat6riaux et Durabilit6 des Constructions, INSA-UPS Toulouse, France
© 1997 by Elsevier Science Ltd. 655 Avenue of the Americas, New York, NY 10010
a superplasticizer or silica fume [1-4]. An extensive description of the microstructure of the ITZ is beyond the scope of this paper and can be found in refs [1-4]. In recent years, the influence of the ITZ characteristics on the mechanical properties of concrete has been studied extensively. However, data on the effect of the ITZ on the durability of cement-based materials remain limited. From a theoretical point of view, the higher porosity of the ITZ should facilitate the ingress of external aggressive agents and favor the development of deleterious chemical reactions. Furthermore, the higher portlandite concentration usually found in the ITZ should also increase the potential risk of leaching caused by dissolution of Ca(OH) 2, and therefore detrimentally affects the resistance of concrete to ion penetration. Given the inherent difficulties of calculating the volume and the properties of the ITZ in a sample, most investigations of the influence of paste/aggregate interface on transport properties have been made on model specimens where the complex and random structure of concrete is approximated by simpler geometries. Recent studies by Breton et al. [5] and by Bourdette [6] indicate that the effective diffusion coefficient of chloride ions is 6 to 12 times greater in the ITZ than in the bulk cement paste. Working with a twin geometrical model and assuming a 20-p~m thickness of the ITZ, Ping et al. [7] have also calculated that the conductivity of the paste/ aggregate interface should be 10 times greater than that of the bulk cement paste. In concrete, the geometry of the pathways for the penetration of aggressive species is necessarily more complicated than in the simplistic models used by the previous authors. Recently, two complementary approaches have been introduced for evaluating the influence of ITZ on transport properties of concrete. Garboczi et al. [8,9] have developed a model to calculate the overall DC electrical conductivity of mortar. In this model, the mortar is described by a random arrangement of spherical sand grains surrounded by a 20-Dmthick ITZ. This model takes into account the difference in conductivity between the ITZ and the bulk cement
Interfacial transition zone in concrete
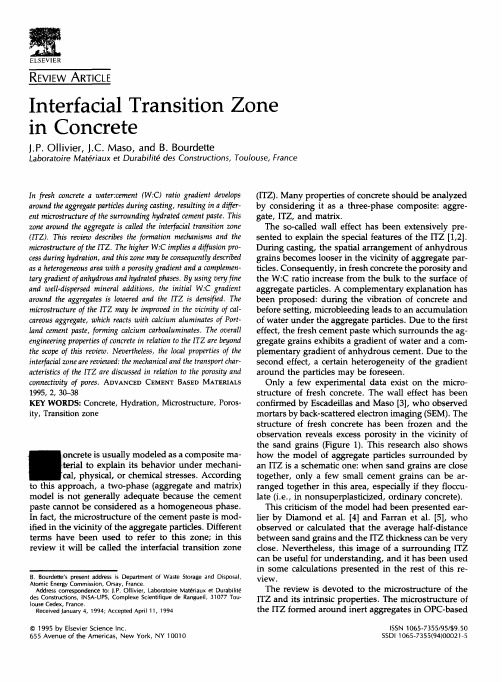
In fresh concrete a water:cement (W:C) ratio gradient develops around the aggregate particles during casting, resulting in a different microstructure of the surrounding hydrated cement paste. This zone around the aggregate is called the interracial transition zone (ITZ). This review describes the formation mechanisms and the microstructure of the ITZ. The higher W:C implies a diffusion process during hydration, and this zone may be consequently described as a heterogeneous area with a porosity gradient and a complementary gradient of anhydrous and hydrated phases. By using very fine and well-dispersed mineral additions, the initial W:C gradient around the aggregates is lowered and the ITZ is densified. The microstructure of the ITZ may be improved in the vicinity of calcareous aggregate, which reacts with calcium aluminates of Portland cement paste, forming calcium carboaluminates. The overall engineering properties of concrete in relation to the ITZ are beyond the scope of this review. Nevertheless, the local properties of the interfacial zone are reviewed: the mechanical and the transport characteristics of the ITZ are discussed in relation to the porosity and connectivity of pores. ADVANCEDCEMENTBASEDMATERIALS
外文-机制砂特性对道路混凝土抗压抗折强度的影响

Influence of manufactured sand characteristics on strength and abrasion resistance of pavement cement concreteLi Beixing ⇑,Ke Guoju,Zhou MingkaiKey Laboratory for Silicate Materials Science and Engineering of Ministry of Education,Wuhan University of Technology,P.O.Box 430070,Wuhan,Chinaa r t i c l e i n f o Article history:Received 23July 2010Received in revised form 10March 2011Accepted 11April 2011Available online 17May 2011Keywords:Pavement cement concrete Manufactured sand Particles characteristics Abrasion resistance Strengtha b s t r a c tManufactured sand (MS)particles are generally more angular with a rougher surface texture than river sand (RS)particles.MS can also contain significant quantities of particles smaller than 75l m called rock microfines.This paper present results from a laboratory study on the influence of the MS characteristics,such as rock microfines content,surface roughness,crushing value and rock types of MS particles,on the strength and abrasion resistance of pavement cement concrete (PCC).Resulted show that the increment of limestone microfines amount in MS from 4.3%to 20%by mass increases the compressive and flexural strengths and improves the abrasion resistance of the MS-PCC.The MS-PCC has higher compressive and flexural strengths when the surface roughness of the sand particles is larger and the crushing value is lower.The abrasion resistance of MS-PCC is improved with the increment of surface roughness and deceases of crushing value and Los Angeles abrasion value of sand particles,while has not evident rela-tion with the silicon content of sand.Ó2011Elsevier Ltd.All rights reserved.1.IntroductionConcrete pavements can be constructed using a variety of aggregates.Constructability and long-term performances are influ-enced by the characteristics and physical properties of the aggre-gates mon river sand (RS),which is most commonly used fine aggregate in the production of concrete,is expensive due to excessive cost of transportation from natural sources.Also large-scale depletion of these sources creates environmental prob-lems.Economy and sustainability objectives are better served if locally-available,durable aggregates can be used –even if some of the individual aggregate sizes do not meet grading or other physical properties normally specified.This will help minimize cost,energy,and CO 2expenditures for the project.In such a situa-tion the manufactured sand (MS)can be an economic alternative to the river sand (RS)in concrete pavement.Manufactured sands are produced by crushing rock depositions to produce a fine aggregate which is generally more angular and has rougher surface texture than naturally weather sand particles.The production of MS also generates high percentages of micro-fines,particles that pass the 75l m sieve,ranging from 5%to 20%.Generally the microfines are washed out since the Chinese national standard JTG F 30-2003limits the amount of microfines to 5%[1],and it is not feasible to eliminate a portion of them.The elimination of the microfines represents a wasted aggregate resource and leads to a disposal problem for producers.In addition,the elimination of the microfines often produces a harsh mix that does not finish well,leading to the necessity of adding natural sand for increasing workability [2].Previous researches have shown that good quality concrete can be made using MS with high amount of microfines [3–9].Generally the compressive strength,flexural strength,and abrasion resistance as well as freezing resistance tend to increase to a certain limit with increasing proportions of microfines.After the limit is reached,the strength decreases be-cause there is not enough paste to coat the aggregate;imperme-ability varies without law and shrinkage,while slightly higher,is still within acceptable ranges.Water reducers and mineral admix-tures can be used to improve workability,since in many cases the more angular MS results in reduced workability.Another issue using manufactured sands,particularly carbonate materials,is the low acid insoluble (AI)residue.Low values of AI are generally believed to result in polishing of the mortar matrix,which in turn leads to reduced surface friction [10].It is important to determine the feasibility of using MS for pav-ing.As natural sands are depleted in various areas of China,MS will result in less expensive fine aggregate if they can be used success-fully.In China,many aggregate quarries produce MS from different mineralogical sources.In localities near the quarries,this MS is commonly used in concrete when good quality natural sand is not longer available.However,little work has been done so far on the effect of MS particles characteristics on the pavement per-formances of concrete.The main objective of this research is to0950-0618/$-see front matter Ó2011Elsevier Ltd.All rights reserved.doi:10.1016/j.conbuildmat.2011.04.004⇑Corresponding author.Tel.:+862787877512;fax:+862787641294.E-mail addresses:libx0212@ (B.Li),keguoju@ (G.Ke),zhou-mingkai@ (M.Zhou).provide information about the effects of microfines content,sur-face roughness,crushing value and parent rock types as well as Los Angeles abrasion value of manufactured sands on the strengths and abrasion resistance of MS-PCC.2.Experimental procedure2.1.Raw materialsA42.5grade ordinary Portland cement(PÁO42.5;342m2/kg Blaine specific sur-face area)was used,with52.6MPa compressive and10.5MPaflexural strengths at 28days,respectively.Coarse aggregate was crushed limestone with a maximum size of26.5mm.A commercial naphthalene-based superplasticizer of KDNOF-1 was incorporated in the concrete mixtures.Thirteenfine aggregates from different mineralogical sources were used.Three natural siliceous river sands(RS)having round and smooth particles were used as reference sands.Manufactured sands were selected with different petrographic characteristics(limestone,quartzite,granite,basalt and granite gneiss).Table1 gives the physical and chemical characteristics of thefine aggregates.The signs of MLS,MQS,MGS,MBS and MGGS represents manufactured sands from limestone, quartzite,granite,basalt and granite gneiss,respectively.The aggregate crushing value is a value which indicates the ability of an aggregate to resist crushing.The lower thefigure the stronger the aggregate,i.e.the greater its ability to resist crush-ing.Crushing value offine aggregates are tested per the Chinese national standard JTG E42-2005[11].The surface texture,also called surface roughness,of particles is the sum of their minute surface features.BS EN933-6:2001‘‘Geometrical Properties of Aggregates,Assessments of Surface Characteristics,Flow Coefficient of Aggre-gates’’test method was used to determine the surface characteristics of both natu-ral and manufactured sands[12].Theflow coefficient is defined as the time offlow required for the material to pass through an orifice.The grading of the aggregates was kept constant according to Fuller curve to diminish the effect of grading,so that the test results indicate only the shape and texture of particles.The limestonefines used as partial replacement of sand were those obtained by sieving the limestone manufactured sand below75l m.The Blaine specific surface area of the limestone microfines was279.8m2/kg,less than that of the cement. 2.2.Mixture composition and test methodsThe parameters for reference mixture of concrete used in this study were de-scribed as:360kg/m3cement content,0.42water to cement ratio and35%sand ra-tio.The superplasticizer of KDNOF-1was employed to maintain a constant workability of slump in the order of40–50cm.Amount of the superplasticizer was0.3%of the sum amount of cement and microfines in MS by mass.In concrete mixtures,in order to shield the influences offineness modulus and stone micro-fines,if without special explanations,thefineness modulus of all sands was ad-justed to3.0and the stone microfines content wasfixed to7%.The150mm size concrete cubes,concrete beams of size100mmÂ100mmÂ400mm were used as test specimens to determine the compressive andflexural strengths,respectively.The compaction of the specimens was obtained by means of vibration.All the test specimens were demoulded at1day,and then cured in water for27days.Curing temperature was22±2°C.Three specimens were employed in compression andflexural strengths measurement for each type of concrete.The strength measurements were carried out using Controls3000KN hydraulic press.Cubic samples with a150mm side were prepared for surface abrasion test by the rotating-cutter method in accordance with Chinese national standard of JTG E 30-2005[13].In compliance with JTG E30-2005,the abrasion system had a erect principal axis,a horizontal steel disc,which had a rotating speed of17.5±0.5r/ min,a counter and a lever,which could apply200N on the specimens.In the test procedure,the specimens werefixed in the holding device of the abrasion machine,the load was applied to the specimen and the disc was rotated for30revolutions. After that,the surfaces of the disc and the sample were cleaned.The above-men-tioned procedure repeated for90revolutions.The mass loss was measured in kg/ 0.0125m2due to wear.The abrasion test was carried out at28days ages.3.Results and discussion3.1.Influence of limestone microfines content in MSStrength and abrasion resistance of concretes using MLS0sand with limestone microfines content from4.3%to20%by mass were tested.As shown in Fig.1,with the increase of microfines content, the compressive strength of concrete isfirstly increased and then reduced,up to the maximum at10%microfines;theflexural strength increases with increase of the microfines content,but the strength increment becomes smaller when the microfines con-tent exceeds10%.Abrasion resistance of the MS concrete is perceived to be a problem for concrete containing microfines.The use of limestone microfines as part of thefine aggregate resulted in reduced abra-sion loss(Fig.2).Any variation in abrasion resistance was likely re-lated to the volume and abrasion resistance of the paste,as thefine and coarse aggregate sources were held constant.The microfines played a further role in enhancing abrasion loss,which was likely related to their hardness and their bonding within the paste.The improvement in abrasion resistance when microfines are used has been documented in other research[3,14].The main reasons for the appropriate limestone microfines improving strength and abrasion resistance of concretes are that: limestone microfines act as nucleation sites for CH and C–S–H reaction products at early hydration ages and accelerate the hydra-tion of clinker minerals[15],and carboaluminates are formed by the reaction between limestone microfines and C3A[16],resulting in an improvement in early strength;meanwhile,the microfines also can improvefine-particle packing,thus increase the density of paste matrix and interfacial transition zone in hardened con-crete[17],and improve the pore structure of abrasion area.3.2.Influence of particle characteristics and parent rock types of MSThe Chinese national standard of JTG F30-2003approves the use of MS in PCC and specifies that the crushing value of MS used in highway PCC should be less than20–25%by mass and micro-fines content in MS should be lower than3–5%by mass,based on the abrasion resistance.With a view to the skid resistance of concrete,the silicon content in the sand should be higher than 25%by mass[1].In order to discuss the rationality of the specifica-tion and to make clear the influence of surface roughness and crushing value of MS particles on pavement performance of con-crete,the strengths and abrasion resistance of concretes made from four types of manufactured sands,such as MLS0,MGS,Table1Physical and chemical characteristics offine aggregates.Sand samples Apparent density(kg/m3)Packing density(kg/m3)Fineness modulus Microfines content(<75l m)(%)SiO2content(%)Crushing value(%)Roughness(s)RS026501677 2.79 1.870.0328.014.8 RS126701690 2.440.585.307.213.1 RS226621680 2.650.879.0115.213.8 MLS026901839 3.05 4.3 5.0517.318.3 MLS126961842 3.29 3.0 5.107.815.8 MLS226841834 3.018.7 5.0226.516.6 MLS326921839 3.43 1.0 4.9813.318.1 MQS26831876 3.00 6.599.227.816.9 MGS26751893 2.75 6.054.2313.815.2 MBS28701987 3.54 1.050.5311.118.7 3850 B.Li et al./Construction and Building Materials25(2011)3849–3853MQS,and MBS were investigated,and compared with those of the river sand(RS0)concrete.3.2.1.Effect of surface roughness of sand particles on strengthFig.3shows the surface texture of sand particles has a signifi-cant effect on concrete strength,as the angular particles have lar-ger surface area,and the rough surfaces enhance bond between aggregate particles and cement matrix,thus increasing strength, particularlyflexural strength.3.2.2.Influence of crushing value of sand particles on strengthFrom Fig.4a,it is found that there is no evident relationship be-tween the crushing value of sand and compressive strength of con-crete.However,it can be seen from Fig.4b there is a remarkable relation between crushing value of sand andflexural strength of concrete,with the increase of crushing value,theflexural strength tends to decrease.The MQS and MBS concretes with smaller crush-ing value achieved higherflexural strength;on the contrary,the MGS and MLS0concretes with larger crushing value achieved low-erflexural strength;and the crushing value of RS0is the largest, theflexural strength of RS0concrete is the lowest.Therefore,fine aggregate with a low crushing value helps improve theflexural strength of concrete.3.2.3.Influence of SiO2content or parent rock types of MS on abrasion resistanceFrom Fig.5we can see that abrasion loss of the MLS0concrete isn’t the largest,although the SiO2content in MLS0is the smallest; while the concrete made from RS0containing a lot of SiO2has the largest abrasion loss,because RS0has the biggest crushing value and the smallest roughness;the SiO2content of MQS is the highest and its crushing value is the lowest,but MQS has relatively small roughness which negatively affects the bonding between aggregate and paste,so the abrasion resistance of MQS concrete was inferior to that of MGS and MBS concretes.It can be concluded that abra-sion resistance of concrete is related to not only the silica or quartz content of sand,but also roughness and crushing value of sand.3.2.4.Effect of multi-factors coupling on the abrasion resistanceSynthesis of Figs.4a and6reveals that compressive strength of MLS0concrete is relatively higher,but its abrasion resistance is worse,while compressive strength of MQS concrete is relatively lower,but its abrasion resistance is higher.This suggests that the abrasion resistance of concrete not totally depends on its compres-sive strength,and the crushing value of aggregate is also impor-tant.In general,the lower the crushing value,the stronger the aggregate.So the aggregate with low crushing value is beneficial to the abrasion resistance of concrete.In the system of concrete,the surface texture and crushing va-lue of sand particles are the two key factors which affect the strength and abrasion resistance of concrete.The surface rough-ness concerns the interlocking force among aggregates and the bonding between paste and aggregate;the crushing value involves the aggregate strength and directly reflects its wear resistance.The sand particles with both large roughness and low crushing value are beneficial to enhance the abrasion resistance of concrete. Hence,it can be concluded that so long as the crushing value of MS meets the requirement,even limestone MS with very low14.815.216.918.318.714.815.216.918.318.7Roughness (s)Roughness (s)(a) Compressive strength(b) Flexural strengthbetween surface roughnessB.Li et al./Construction and Building Materials25(2011)3849–38533851SiO 2content also can be utilized to produce PCC superior to RS in abrasion resistance,because MS has the natural characteristics of rough surface and angularity.3.3.Influence of Los Angeles abrasion value of aggregate on strengths and abrasion resistanceIn order to study the effect of abrasion of fine aggregate on the abrasion resistance of concrete,three granite gneiss coarse aggre-gates with different Los Angeles value were separately crushed into manufactured granite gneiss sands (MGGS).As shown in Table 2,the Los Angeles abrasion value of aggregate has no direct relation with the MGGS concrete strength,but is related to the concrete abrasion resistance.With the decrease of Los Angeles abrasionvalue,the abrasion loss of concrete decreased.This indicates that the sand particles participate in the abrasion process of concrete,the abrasive resistance of sand accounts for the abrasion resistance of concrete.parison of limestone manufactured sand and river sand concretesAt present,the MS used in China are mainly produced by lime-stone rock,the investigations on strength and abrasion resistance of limestone MS concretes and comparison with RS concretes will have universal significance.Three types of RS and four types of limestone MS are used to compared their pavement performances.Table 3shows,the three concretes of MLS0,MLS1and MLS3are superior to three concretes of RS0,RS1and RS2in flexural strength and abrasion resistance.The reason may be the three manufac-tured sands have rougher surface and great angularity than river sands.While the low flexural strength and abrasion resistance of MLS2concrete should be attributed to large crushing value of the paring MLS2and RS0,their crushing value are more than 25%,so the flexural strength and abrasion resistance of two7.811.113.817.3287.811.113.817.328Crushing value (%)MBSCrushing value (%)(a) Compressive strength (b) Flexural strengthFig.of crushing strengths of concrete at RS05.0550.5354.2370.0399.22Content of SiO (%)between SiO abrasion resistance RS07.811.113.817.328Crushing value (%)abrasion resistance Table 2Effect of Los Angeles abrasion value on strengths and abrasion loss of concrete at 28days.SandsLos Angeles abrasion value (%)Compressive strength (MPa)Flexural strength (MPa)Abrasion loss (kg/m 2)MGGS124.648.68.1 1.521MGGS238.947.88.0 1.973MGGS355.148.67.92.082Table 3Pavement performance comparison between limestone manufactured sand and river sand concretes.SamplesRoughness (s)Crushing value (%)Compressive strength (MPa)Flexural strength (MPa)Abrasion loss (kg/m 2)RS014.828.046.97.4 2.281RS113.17.247.87.8 1.804RS213.815.248.07.7 1.822MLS018.317.349.78.0 1.600MLS115.87.849.48.2 1.644MLS216.626.548.57.6 1.911MLS318.113.350.18.11.5913852 B.Li et al./Construction and Building Materials 25(2011)3849–3853concretes are the worst,and MLS2concrete is relatively better than RS0concrete.It can be conclude from the angle of abrasion resis-tance that when crushing value of limestone MS is not more than 26.5%,its utilization to PCC is feasible,and the MS concretes gen-erally have higherflexural strength and better abrasion resistance than RS concretes.4.Conclusions(1)The increment of microfines in MS from4.3to20%do notadversely affect the strengths and abrasion resistance of MS concretes,when the microfines content is10%,the pave-ment performances of the MS concrete achieve the best.(2)With the increase of surface roughness of MS particles,thecompressive andflexural strengths of concrete increase;while with the increase of crushing value of MS particles, theflexural strength of concrete decreases.There is no evi-dent relationship between crushing value of MS and com-pressive strength of MS concrete.(3)The effect of MS on abrasion resistance of PCC is comprehen-sive results of particles characteristics of sand.The abrasion resistance of the MS-PCC has better relation with surface roughness,crushing value and Los Angeles abrasion loss of the sand particles,while has no evident relation with the sil-icon content of the sand.MS with large roughness,low crushing value and good abrasion resistance is suitable for producing high quality PCC.(4)Due to natural rough and angular characteristics of MS par-ticles,so long as the crushing value of MS particles is less than26.5%,MS-PCC is generally superior to RS-PCC inflex-ural strength and abrasion resistance.AcknowledgementThefinancial support under the Science and Technology Item of Communication Construction for West China(Grant Number 2009318811082)is gratefully acknowledged.References[1]JTG F30-2003.Technical specification for construction of highway cementconcrete pavements.Beijing:Ministry of Transport of the People’s Republic of China;2003.[2]Ahn N.Experimental study on the guidelines for using higher contents ofaggregate microfines in Portland cement concrete.Ph.D.Thesis.University of Texas at Austin;2000.[3]Quiroga PN,Ahn N,Fowler DW.Concrete mixtures with high microfines.ACIMater J2006;103(4):258–64.[4]Cai JW,Li BX,Zhou MK,Hu XM.Effects of crusher dust on properties of low/medium strength concrete with manufactured sand.J Wuhan Univ Technol 2006;28(4):27–30.[5]Quiroga PN,Fowler DW.The effects of aggregate characteristics on the per-formance of portland cement concrete.ICAR Research Report104-1F.International Center for Aggregates Research,University of Texas at Austin;2004.[6]Donza H,Cabrera O,Irassar EF.High-strength concrete with differentfineaggregate.Cem Concr Res2002;32(11):1755–61.[7]Li Beixing,Wang Jiliang,Zhou Mingkai.Effect of limestonefines content inmanufactured sand on durability of low-and high-strength concretes.Construct Building Mater2009;23(8):2846–50.[8]Katz A,Baum H.Effect of high levels offines content on concrete properties.ACI Mater J2006;103(6):474–82.[9]Wang Jiliang,Zhou Mingkai,He Tusheng.Effects of stone dust on resistance tochloride ion permeation and resistance to freezing of manufactured sand concrete.J Chinese Ceram Soc2008;36(4):482–6.[10]Bulmer GGB,Colley boratory studies of the skid resistance of concrete.ASTM J Mater1966;1(3):536–59.[11]JTG E42-2005.Test method of aggregate for highway engineer-ing.Beijing:Ministry of Transport of the People’s Republic of China;2005. [12]BS EN933-6:2001.Tests for geometrical properties of aggregates.Assessmentof surface characteristics.Flow coefficient of aggregates.London:British Standards Institute;2002.[13]JTG E30-2005.Specification of test methods of cement and concrete forhighway engineering.Beijing:Ministry of Transport of the People’s Republic of China;2005.[14]Stewart JG,Norvell JK,Juenger MCG,Fowler DW.Influence of microfineaggregate characteristics on concrete performance.J Mater Civil Eng2007;19(11):957–64.[15]Bonavetti VL,Donza H,Rahhal VF,Irassar EF.Influence of initial curing on theproperties of concrete containing limestone blended cement.Cem Concr Res 2000;30(5):703–8.[16]Bonavetti VL,Rahhal VF,Irassar EF.Studies on the carboaluminate formationin limestonefiller-blended cements.Cem Concr Res2001;31(6):853–9. [17]Tragardh J.Microstructural features and related properties of self-compactingconcrete,In:SkarendahlÅ,PeterssonÖ,editors.Proceeding of thefirst international RILEM symposium on self-compacting concrete,Cachan Cedex: RILEM Publication;1999.p.175–86.B.Li et al./Construction and Building Materials25(2011)3849–38533853。
考虑界面影响的混凝土弹性模量的数值预测_应宗权
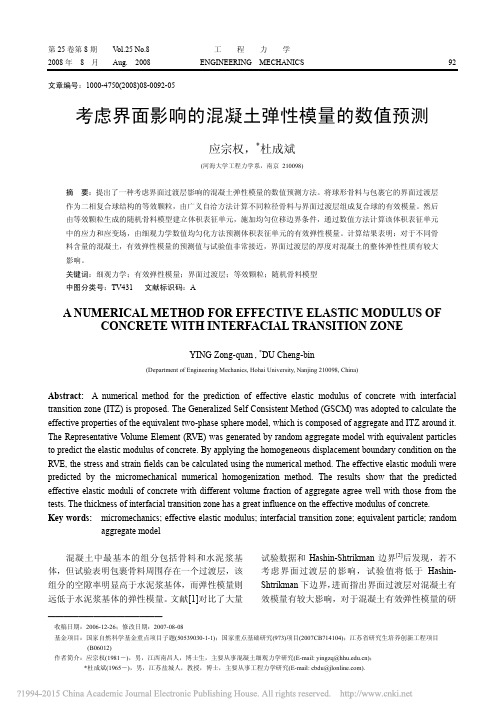
第25卷第8期 V ol.25 No.8 工 程 力 学 2008年 8 月 Aug. 2008 ENGINEERING MECHANICS92———————————————收稿日期:2006-12-26;修改日期:2007-08-08基金项目:国家自然科学基金重点项目子题(50539030-1-1);国家重点基础研究(973)项目(2007CB714104);江苏省研究生培养创新工程项目(B06012)作者简介:应宗权(1981―),男,江西南昌人,博士生,主要从事混凝土细观力学研究(E-mail: yingzq@); 文章编号:1000-4750(2008)08-0092-05考虑界面影响的混凝土弹性模量的数值预测应宗权,*杜成斌(河海大学工程力学系,南京 210098)摘 要:提出了一种考虑界面过渡层影响的混凝土弹性模量的数值预测方法。
将球形骨料与包裹它的界面过渡层作为二相复合球结构的等效颗粒,由广义自洽方法计算不同粒径骨料与界面过渡层组成复合球的有效模量。
然后由等效颗粒生成的随机骨料模型建立体积表征单元,施加均匀位移边界条件,通过数值方法计算该体积表征单元中的应力和应变场,由细观力学数值均匀化方法预测体积表征单元的有效弹性模量。
计算结果表明:对于不同骨料含量的混凝土,有效弹性模量的预测值与试验值非常接近,界面过渡层的厚度对混凝土的整体弹性性质有较大影响。
关键词:细观力学;有效弹性模量;界面过渡层;等效颗粒;随机骨料模型 中图分类号:TV431 文献标识码:AA NUMERICAL METHOD FOR EFFECTIVE ELASTIC MODULUS OFCONCRETE WITH INTERFACIAL TRANSITION ZONEYING Zong-quan , *DU Cheng-bin(Department of Engineering Mechanics, Hohai University, Nanjing 210098, China)Abstract: A numerical method for the prediction of effective elastic modulus of concrete with interfacial transition zone (ITZ) is proposed. The Generalized Self Consistent Method (GSCM) was adopted to calculate the effective properties of the equivalent two-phase sphere model, which is composed of aggregate and ITZ around it. The Representative V olume Element (RVE) was generated by random aggregate model with equivalent particles to predict the elastic modulus of concrete. By applying the homogeneous displacement boundary condition on the RVE, the stress and strain fields can be calculated using the numerical method. The effective elastic moduli were predicted by the micromechanical numerical homogenization method. The results show that the predicted effective elastic moduli of concrete with different volume fraction of aggregate agree well with those from the tests. The thickness of interfacial transition zone has a great influence on the effective modulus of concrete. Key words: micromechanics; effective elastic modulus; interfacial transition zone; equivalent particle; randomaggregate model混凝土中最基本的组分包括骨料和水泥浆基体,但试验表明包裹骨料周围存在一个过渡层,该组分的空隙率明显高于水泥浆基体,而弹性模量则远低于水泥浆基体的弹性模量。
海洋环境下港口工程混凝土界面过渡区氯离子扩散系数模型
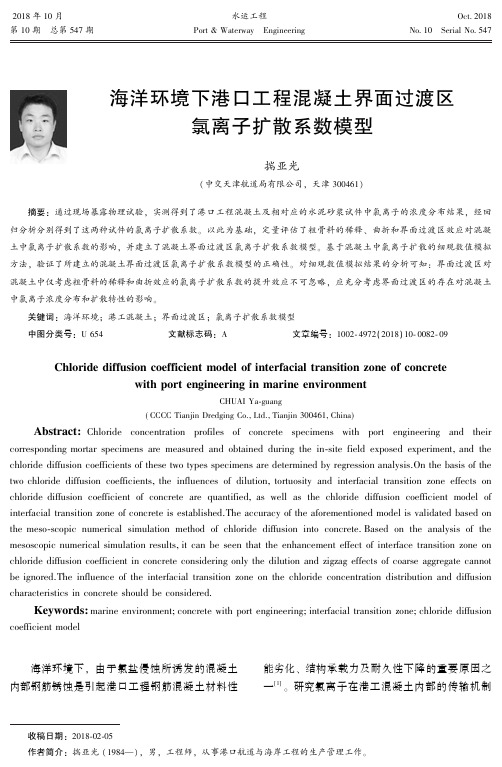
Abstract Chloride concentration profiles of concrete specimens with port engineering and their
摘要: 通过现场暴露物理试验ꎬ 实测得到了港口工程混凝土及相对应的水泥砂浆试件中氯离子的浓度分布结果ꎬ 经回
归分析分别得到了这两种试件的氯离子扩散系数ꎮ 以此为基础ꎬ 定量评估了粗骨料的稀释、 曲折和界面过渡区效应对混凝
土中氯离子扩散系数的影响ꎬ 并建立了混凝土界面过渡区氯离子扩散系数模型ꎮ 基于混凝土中氯离子扩散的细观数值模拟
中图分类号: U 654
文献标志码: A
文章编号: 1002 ̄ 4972(2018)10 ̄ 0082 ̄ 09
Chloride diffusion coefficient model of interfacial transition zone of concrete with port engineering in marine environment
���锈蚀、 提高港工钢 筋混凝 土 结 构 在 氯 盐 环 境 下 的 耐 久 性 具 有 重 要 意义 2 ꎮ
混凝土是由水泥、 水、 粗骨料和细骨料经混 合后形成的一种典型的非均匀多相复合材料 3 ꎮ 通常情况下ꎬ 其细观结构可被视为是由水泥砂浆、 粗骨料和界面过渡区这三相介质共同构成 4 ꎮ 若 将混凝土中的粗骨料假设为三维球形ꎬ 则混凝土 三相复合材料的细观构造见图 1ꎮ 其中ꎬ Farran 5 首次发现在混凝土的粗骨料和水泥砂浆这两相介 质之间存在一层厚度较小、 但其内氢氧化钙含量 和孔隙率较高的物质ꎬ 并将其命名为界面过渡区 ( interfacial transition zoneꎬ 简称 ITZ) ꎮ 由于 ITZ 的 微观构造相对疏松且其内孔隙率相比水泥砂浆介 质更大ꎬ 因此ꎬ 其内氯离子扩散系数较水泥砂浆 而言要大很多ꎮ 根据刘恒 6 、 Yang 等 7 ̄9 的研究表 明: ITZ 中氯离子的扩散系数为水泥砂浆中扩散系 数的几十倍甚至上百倍ꎮ 同样ꎬ Nilsen 等 10 经研 究后发现: 若不考虑 ITZ 的影响ꎬ 仅仅将混凝土 视为由水泥砂浆和粗骨料的两相介质构成的数值 模型不能较好地预测混凝土的耐久性ꎮ 综上所 述ꎬ ITZ 的存在会影响混凝土中氯离子的扩散特 性ꎬ 从而影响混凝土的耐久性和使用寿命ꎮ 因 此ꎬ 建立合理的混凝土界面过渡区氯离子扩散系 数模型ꎬ 对于定量评估其内氯离子的长期扩散特 性及预测混凝土结构的使用寿命具有十分重要的 意义ꎮ
- 1、下载文档前请自行甄别文档内容的完整性,平台不提供额外的编辑、内容补充、找答案等附加服务。
- 2、"仅部分预览"的文档,不可在线预览部分如存在完整性等问题,可反馈申请退款(可完整预览的文档不适用该条件!)。
- 3、如文档侵犯您的权益,请联系客服反馈,我们会尽快为您处理(人工客服工作时间:9:00-18:30)。
Effects of interfacial transition zones on the stress –strain behavior of modeled recycled aggregate concreteJianzhuang Xiao a ,⁎,Wengui Li a ,b ,David J.Corr b ,Surendra P.Shah ba Department of Building Engineering,Tongji University,Shanghai 200092,PR ChinabCenter for Advanced Cement-Based Materials,Northwestern University,Evanston,IL 60208,United Statesa b s t r a c ta r t i c l e i n f o Article history:Received 27October 2012Accepted 2May 2013Available online xxxx Keywords:Concrete (E)Aggregate (D)Interfacial transition zone (B)Finite element analysis (C)NanoindentationBased on nanoindentation tests and analysis,the constitutive relationship of the Interfacial Transition Zones (ITZs)in Recycled Aggregate Concrete (RAC)is put forward.Together with the meso/micro-scale mechanical properties of each phase in Modeled Recycled Aggregate Concrete (MRAC),the plastic-damage constitutive models are employed in numerical studies on MRAC under uniaxial compression and uniaxial tension loadings to predict the overall mechanical behavior,particularly the stress –strain relationship.After the calibration and validation with the experimental results,a parametric study has been undertaken to analyze the effects of ITZs and new mortar matrix on the stress –strain relationship of MRAC.It is revealed that the mechanical properties of new mortar matrix and relative mechanical properties between ITZs and mortar matrices play a signi ficant role in the overall stress –strain relationship and failure patterns of MRAC under both uniaxial compression and uniaxial tension loadings.©2013Elsevier Ltd.All rights reserved.1.IntroductionThe behaviors of Recycled Aggregate Concrete (RAC)are deter-mined by properties of the waste concrete,the new mix composition,the mixing approach and the deterioration condition of Recycled Coarse Aggregates (RCAs)[1–3].It is generally accepted that the Interfacial Transition Zones (ITZs),the quality of the old mortar,and the old mortar content of the original concrete in fluence the properties of RAC.In recent years,RAC has been proven to be commercially and technically sound for both non-structural and structural applications [4–7].Xiao et al.found that properly designed and constructed RAC frame structures have good load-bearing capacity,deformation and energy dissipation ability to withstand earthquake-type loadings [8].Quasi-brittle multiphase materials,such as concrete,are widely applied in engineering.Most of them have intrinsic heterogeneous and nonlinear mechanical behaviors due to the random distribution of multiple phases over the nano-,micro-,meso-and macro-scales [9–15].A better understanding of mechanical properties including the failure processes by both experiments and computer modeling has become one of the most critical research topics for concrete [16–19].Corr et al.predicted the mechanical properties of concrete in tension with the consideration of meso-scale randomness in the cohe-sive interface properties [20,21].Mondal et ed a nanoindenter along with in-place scanning probe microscopy imaging to determine the nano-scale local mechanical properties of ITZs [22].Cusatis et al.formulated the Lattice Discrete Particle Model (LDPM)and simulated experiments include uniaxial compression and multiaxial compression,tensile fracture,shear strength,and cyclic compression tests [23,24].Yip et al.developed an irregular lattice model to simulate the fracture process of multiphase particles,such as concrete [25].Moreover,con-crete was simulated with plastic-damage constitutive model,and showed a very good correlation with the experimental results [26].To characterize the random heterogeneity in cementitious materials numerically,different phases in the material such as the mortar matrix,aggregates and ITZs can be explicitly modeled by the Finite Element Analysis (FEA),and the material mechanical properties are directly assigned to the elements [27–29].Al-Rub et al.and Nagai et al.simulat-ed the mortar matrix,coarse aggregate of random shapes and sizes and interfaces in concrete specimens under 2D tensile and compressive loadings [30,31].Rao et ed a unit cell approach to model the deformation and failure of single aggregate concrete [32,33].Xiao et al.numerically simulated the stress distribution characteristics of Recycled Aggregate Concrete (RAC)by commercial FEA software the ABAQUS 6.8[11].However,for the previous investigations,the thick-ness,elastic modulus and strength of ITZs relative to the mortar matrix were not considered during the numerical simulation.Moreover,some numerical simulations even neglected the existence of the ITZs between aggregate and mortar matrix [34].With the emergence of nanoindentation technology,the proper-ties of the ITZs are available to be measured experimentally [9,22].Due to the recent advances in understanding the microstructure,thickness,and strength of the ITZ and the developments of computa-tional power,the micromechanical behavior of concrete can be effec-tively simulated to get a deeper insight into the effect of each phaseCement and Concrete Research 52(2013)82–99⁎Corresponding author.Tel.:+862165982787;fax:+862165986345.E-mail address:jzx@ (J.Xiao).0008-8846/$–see front matter ©2013Elsevier Ltd.All rights reserved./10.1016/j.cemconres.2013.05.004Contents lists available at SciVerse ScienceDirectCement and Concrete Researchj ou r n a l h o m e p a g e :h t tp ://e e s.e l s e v i e r.c o m /C E MC ON /d e f a ul t.a s p(such as aggregate size and shape,ITZ thickness and micromechanical properties,and the mortar matrix mechanical properties,etc.)[35].Compared to conventional concrete,RAC contains more types of ITZs [36,37].The old ITZ is between the original aggregate and the old paste matrix,while the new ITZ is between the old paste matrix and the new paste matrix.Xiao et al.[38]and Tam et al.[3]found that the microstructure of RAC was much more complicated than that of conventional concrete.It is well known that the compressive strength and elastic modulus of RAC are lower than those of conven-tional concrete.One of the major reasons for the lower strength exhibited by RAC is the weak ITZs and old adhered mortar.Etxeberria et al.[39]indicated that adhered old mortar on RCAs was the weakest point.Contrary to the common beliefs,Nagataki and Gokce et al.reported that adhered mortar is not always the primary parameter determining the quality of the RAC [40].Rasheeduzzafar and Khan [41]concluded that the weakest link in RAC depended on the relative strength of old mortar and new mortar or the relative quality of old ITZ and new ITZ.In this paper,Modeled Recycled Aggregate Concrete (MRAC)is a volume element of RAC which is used to simplify the real RAC for ex-perimental study [10,11].A plastic-damage model is adopted within FEA analysis.The mechanical properties of ITZs in MRAC are obtained by a nanoindentation technique.Due to the ratio of height to thick-ness being 3for the MARC,two-dimensional micro-scale numerical modeling is conducted in order to investigate the effects of ITZs on the overall behavior and failure process of MRAC under both uniaxial compression and uniaxial tension loadings.The experimental and numerical results show a good relation with each other.The results show that the micromechanical properties of ITZ have an obviousin fluence on the stress –strain relationship and failure patterns of MRAC.2.Modeled recycled aggregate concreteIn the current paper,a representative volume element of RAC is idealized as an MRAC consisting of nine recycled coarse aggregate surrounded by a mortar matrix [10,11].Recycled coarse aggregate is idealized to have a round shape.The MRAC used in numerical simula-tion is shown in Fig.1.In general,the MRAC was used to obtain the effective properties of multiphase composites.The MRAC means that the recycled coarse aggregates are embedded within new mortar matrix as a square array.This is an assumption made to simplify the real RAC and provide useful information regarding crack initiation and mechanical response of RAC under loadings.The previous exper-imental results show that the failure pattern of MRAC can provide in-sights into the in fluences of the mechanical properties of each phase on the failure mechanism of RAC [10,20,21,42,43].It has been found that idealization of regular distribution of recycled coarse aggregates in RAC not only simpli fies the problem but also assists in studying the effect of different phases on overall failure behavior of RAC.3.Constitutive relationshipsRecycled aggregate concrete,which is considered as a cementitious composite including natural aggregate,old ITZ,old mortar matrix,new ITZ and new mortar matrix (see Fig.1a),can be numerically modeled using finite element models.The details of each constitutive model used in this numerical simulation are described in the following.a) MRAC specimenb) MRAC schematicFig.1.Modeled Recycled Aggregate Concrete (MRAC).a) uniaxial tensionb) uniaxial compressionFig.2.Stress –strain relation under uniaxial loading.83J.Xiao et al./Cement and Concrete Research 52(2013)82–99Fig.3.Nanomechanical properties and characteristics of ITZs in RAC.84J.Xiao et al./Cement and Concrete Research 52(2013)82–993.1.Mortar matrixMortar matrix shows softening behavior after reaching its peak tensile stress or compressive stress,which is due to toughening me-chanics within the fracture process zone.Both micro-cracking devel-opment and irreversible deformations contribute to the nonlinear response of mortar matrix.A plastic-damage constitutive model for mortar matrix is developed by former investigators [26,30,44].Anisotropic damage with a plasticity yield criterion and a damage cri-terion is introduced to adequately describe the plastic and damaged behaviors of mortar matrix.Moreover,in order to account for differ-ent effects under tensile and compressive loadings,two damage criteria are adopted:one for compression and a second for tension such that the total stress is decomposed into tensile and compressive components.For cyclic loading,stiffness recovery caused by crack opening and closing is also considered.The compressive stiffness is recovered upon crack closure as load changes from tension to com-pression.On the other hand,the tensile stiffness is not recovered as the load changes from compression to tension once crushing micro-cracks have developed.In this study,the tension and compres-sion stiffness recovery factors are 0.0and 1.0,respectively.The strain equivalence hypothesis is used in deriving the constitutive equations,so that the strains in the effective (undamaged)and damaged con fig-urations are set equal [26,30,45].This leads to a decoupled algorithm for the effective stress computation and the damage evolution.The following information is used for either isotropic or anisotrop-ic damage.And the damage tensor d ij (d t and d c )degenerates to the scalar damage variable in case of uniaxial loading.The plasticity and the compressive damage loading surface are more dominate in case of shear loading and compressive crushing (modes II and III cracking)whereas the tensile damage loading surface is dominant in case of mode I cracking.In the uniaxial loading,the elastic stiffness degrada-tion variables are assumed as increasing functions of the equivalentplastic strain ˜εpl t and ˜εpl c with ˜εpl t being the tensile equivalent plastic strain and ˜εplc being the compressive equivalent plastic strain.It should be noted that the material behavior is controlled by both plas-ticity and damage.It is assumed that the uniaxial stress –strain curves can be converted into stress versus plastic –strain curves.Thus σt ¼σt ˜εpl t ;_εpl t ;θ;f i σc ¼σc ˜εpl c ;_εpl c ;θ;f i8<:ð1Þ0.00000.00010.00020.00030.00040.00050.00060.00.51.01.52.02.53.03.5S t r e s s (M P a )Strain0.0000.0020.0040.0060.0080.0100.0120.0145101520253035404550S t r e s s (M P a )Straina) Uniaxial tensionb) Uniaxial compressionFig.4.Uniaxial stress –strain relation of ITZ and mortar matrix.Table 1Mechanical properties of each phase in MRAC.MRACThickness (μm)Elasticmodulus (E)(GPa)Poisson's ratio (ν)Strength (MPa)Compressive (f c )Tensile (f t )Natural aggregate –80.00.16––Old mortar (OM)–25.00.2245.0 3.00New mortar (NM)–23.00.2241.4 2.76Old ITZ (OI)5020.00.2036.0 2.40New ITZ (NI)6018.00.2033.12.21Fig.3(continued ).85J.Xiao et al./Cement and Concrete Research 52(2013)82–99where the subscripts t and c refer to tension and compression,respec-tively;˜εpl t and ˜εpl c are the equivalent plastic strains,_εpl t and _εpl c are the equivalent plastic rates,θis the temperature,and f i (i =1,2,…)are other prede fined field variables.When the mortar matrix specimen is unloaded from any point on the strain softening branch of the stress –strain curve,the unloading response is less stiff.The degradation of the elastic stiffness is charac-terized by two damage variables,d t and d c ,which are assumed to be functions of the plastic strain,temperature,and field variables:d t ¼d t ˜εpl t ;θ;f i ;0≤d t ≤1d c ¼d c ˜εpl c ;θ;f i ;0≤d c≤1:8<:ð2ÞThe damage variables can take values from zero,representing theundamaged material,to one,which represents total loss of strength.If E 0is the initial (undamaged)elastic modulus,the stress –strain relations (ε−σ)under uniaxial tension and compression loading are respectively as shown:σt ¼1−d t ðÞE 0εt −˜εpl tσc ¼1−d c ðÞE 0εc −˜εpl c8<:ð3ÞThe model assumes that the uniaxial tensile and compressive re-sponse are characterized by damaged plasticity,as shown in Fig.2[30,45],where εt el and εc elare the tensile and compressive equivalent elastic strain,respectively.a) Overall FEA model b) Details of each phaseFig.5.2D micro-scale FEA model of MRAC.Table 2Mixture proportion of cement mortar in MRAC [10].MRACOld mortar(w/c ratio)Mass,kg/m 3New mortar (w/c ratio)Mass,kg/m 3Water Cement SandWater Cement Sand MRAC-30-200.451603565650.55160276589MRAC-30-300.451603565650.45160356565MARC-30-400.451603565650.36160444539a) Test and DIC setupb) Failure patternFig.6.Experimental study on MRAC under uniaxial compression.0.0000.0010.0020.0030.0040.00551015202530354045S t r e n g t h (M P a )Strainparison of compressive stress –strain curves (MRAC30-30).86J.Xiao et al./Cement and Concrete Research 52(2013)82–993.2.ITZsDue to the difficulties in determining the properties of ITZ with traditional testing methods,the understanding of the thickness,and elastic modulus and strength of ITZ related to mortar matrix is limit-ed.With the emergence of nanoindentation techniques,it is now possible to directly measure the micromechanical properties of the quite thin ITZ.The nanoindentation involves performing indents at micro or nano scale[46,47].In this study,four indentation areas(150μm×100μm)were taken randomly for nanoindentation within the old ITZ and new ITZ regions,respectively.Total341indents were performed in an array at each studied area(Fig.3(a)and(b)).These four studied areas were used for statistical analysis including the average and standard deviation.Hardness testing on cement paste found that there is a linear relationship between hardness and strength[46,47].The hard-ness obtained from nanoindentation is assumed to provide a linear relationship between hardness and strength.As the indentation hard-ness characteristics at the ITZs in RAC were observed to generally be similar to those of the elastic modulus[9,35],this study will focus on the elastic modulus in the following analysis.Fig.3(c)and(d)re-spectively shows the contour maps of elastic modulus of old and new ITZs.The darker areas mean the lower modulus region,while the brighter areas mean the higher modulus regions.In this study,the distribution of elastic modulus was used as a basis for the property characteristics of old ITZ and new ITZ,such as the thickness,elastic modulus and strength related to old and new mortar matrices,re-spectively.Fig.3(e)and(f)shows the elastic modulus distributions with the distance across old ITZ and new ITZ.It is well established that the microstructure in the ITZ region is quite different from thata) Experimental (point a)b) Numerical (point a) c) Experimental (point b)d) Numerical (point b) e) Experimental (point c)f) Numerical (point c)Fig.8.Micro-scale crack development at different loading levels.87J.Xiao et al./Cement and Concrete Research52(2013)82–9988J.Xiao et al./Cement and Concrete Research52(2013)82–99a) Experimental (Point b)b) Numerical (Point b)c) Experimental (Point c)d) Numerical (Point c)e) Experimental (Point d)f) Numerical (Point d)g) Experimental (Point e)h) Numerical (Point e)pressive failure pattern at different loading levels.of the mortar matrix.In this test,greater porosity in the ITZs caused the reduced elastic modulus and strength,relative to those of related mortar matrix [9,11,35,48].In this study,the ITZ thickness was estimated by locating the place where there is slight variation in the elastic modulus with the distance from the natural aggregate or old mortar matrix surface,and the elastic modulus distribution of the ITZs seems to be close to that of mortar ma-trix.Based on the nanoindentation results,the thicknesses of old ITZ and new ITZ are found to be around 50μm and 60μm,respectively.Moreover,the average elastic modulus of old ITZ and new ITZ were found to be approximately 80%and 85%of those of old mortar matrix and new mortar matrix,respectively [9,35].It is assumed that there is a linear relationship between indentation hardness and strength.Considering that the hardness has a similar distribution with the mod-ulus in the ITZ regions (see Fig.3(g)–(j)),the strengths of old ITZ and new ITZ are assumed to be 80%and 85%of those of old mortar matrix and new mortar matrix,respectively [35,46,47].Based on the current and previous experimental data,the ratios of ITZs'mechanical proper-ties to those of mortar matrix are assumed to be mainly ranged 0.5to 1.0[22,49,50].The constitutive relation of ITZ is simulated with dam-aged plasticity model,which is similar to that of mortar matrix,but the elastic modulus and strength are a little lower than those of mortar matrix.For the mortar matrix,elastic modulus,the strength (peak stress),and deformation capacity (peak strain and ultimate strain)parameters are obtained according the experimental data from Refs.[20,21,51].In case of the ITZs,the relative mechanical properties (elastic modulus and strength)to that of mortar matrix can be provided by the nanoindentation test,however,recently it is still a big challenge to obtain the deformation capacity parameters of ITZs.So in this study,the deformation capacity of ITZs is assumed to be similar with that ofmortar bining the descriptions in this and above sections,the predicted uniaxial tensile and compressive stress –strain relation-ships for both ITZ and mortar matrix based on the plastic-damage con-stitutive model are shown in Fig.4.3.3.Natural aggregateGranite cylinders are used as natural aggregate in the MRAC.Based on the experiment results [10],there were no cracks or damage observed in the natural aggregates during loading.In the current study,natural aggregate is modeled as linear-isotropic material.It behaves linearly throughout the analysis.For the numer-ical calibration validation,the material parameters of each phase in MRAC,which were determined according to the experimental data,are listed in Table 1[10,35].However,the Poisson's ratios of new ITZ and old ITZ were de fined as 0.20according to the study by Ramesh et al.[52].4.FEA simulation and test veri fication4.1.FEA modelThe software program (ABAQUS 6.11)was used for the FEA analyses.4-node plane stress quadrilateral (CPS4R)elements were used to mesh the MRAC.The 2D micro-scale FEA model of MRAC is shown in Fig.5.The model was subjected to a uniformly distributed displacement at the top edge,as the displacement-controlled loading scheme was used.The Y degrees of freedom were fixed at the bottom edge,while the X degrees of freedom and rotation were not constrained.The FEA model has a total of 34,240elements in this simulation.4.2.Modeling implementationIn this paper,ABAQUS/explicit quasi-static analyses were applied for the numerical simulation [53,54].The explicit method was origi-nally developed,and is primarily used to solve dynamical problems involving deformable bodies.Acceleration and velocity at a particular point in time are assumed to be constant during a time increment and are used to solve for the next point in time.ABAQUS/explicit uses a forward Euler integration scheme as follows [55,56]:ui þ1ðÞ¼ui ðÞþΔti þ1ðÞ_ui þ1ðÞð4Þ_ui þ12ðÞ¼_u i −12ðÞþΔti þ1ðÞþΔti þ1ðÞ2€ui ðÞð5Þwhere u is the displacement and the superscripts refer to the timeincrement.The term ‘explicit ’refers to the fact that the state of the0.00000.00010.00020.00030.00040.00050.00.51.01.52.02.53.03.5S t r e s s(M P a )StrainFig.10.Numerical tensile stress –strain curve of MRAC30-30.a) Point a b) Point b c) Point cFig.11.Simulated micro-scale crack development at different loading levels.89J.Xiao et al./Cement and Concrete Research 52(2013)82–99analysis is advanced by assuming constant values for the velocity _u,and the acceleration €u,across half time intervals.The accelerations are com-puted at the start of the increment by €ui ðÞ¼M −1⋅F i ðÞ−Ii ðÞð6Þwhere F is the vector of externally applied forces,I is the vector of in-ternal element forces and M is the lumped mass matrix.As the lumped mass matrix is diagonalized it is a trivial process to invert it,unlike the global stiffness matrix in the implicit solution method.Therefore each time increment is computationally inexpensive to solve.A stability limit determines the size of the time increment:Δt ≤2ωmaxð7Þwhere ωmax is the maximum element eigenvalue.A conservative and practical method of implementing the above inequality is:Δt ¼min Le cð8Þwhere L e is the characteristic element length and c d is the dilatational wave speed:c d¼ffiffiffiffiffiffiffiffiffiffiffiffiffiffiffiλþ2μρs ð9Þhere,λand μare the Laméelastic constants and ρis the material den-sity.A quasi-static problem solved using the explicit method would have much smaller time increments than an equivalent problem solved by implicit method.Although the incremental solution is easy to obtain using the implicit method,it is unusual for an analysis to take 100,000increments to solve.In order to maintain ef ficiency ofc) Point d d) Point ea) Point b b) Point cFig.12.Simulated tensile failure pattern at different loading levels.Table 3Mechanical properties of each phase in parametric analysis.New mortar matrixOld ITZNew ITZr ¼0:8ENME OM;f NMf OM;E NI E OI ;f NI f OI¼0:8 :MRAC30-20;r ¼0:5EOIE OM;f OI f OM¼0:5;r ¼0:5ENIE NM;f NI f NM¼0:5;r ¼1:0E NM E OM ;fNM f OM ;E NI E OI ;fNIf OI¼1:0 :MRAC30-30;r ¼0:8EOI E OM ;fOIf OM¼0:8 ;r ¼0:8ENI E NM ;f NIf NM ¼0:85 ;r ¼1:2ENME OM;f NMf OM ;E NI E OI ;f NI f OI ¼1:2:MRAC30-40r ¼1:0EOIE OM;f OIf OM¼1:0;r ¼1:0ENI E NM ;fNI f NM¼1:0;Note:E OM and f OM are elastic modulus and strength of old mortar,respectively.E NM and f NM are elastic modulus and strength of new mortar,respectively.E OI and f OI are elastic modulus and strength of old ITZ,respectively.E NI and f NI are elastic modulus and strength of new ITZ,respectively.90J.Xiao et al./Cement and Concrete Research 52(2013)82–99the analyses,it is important to ensure that the sizes of the elements are as regular as possible.This is so that on small element does not reduce the time increment for the whole model.On the other hand, the implicit FEA method encounters numerical difficulties when solv-ing non-linear quasi-static problems.The iterative approach may have trouble achieving convergence in analyses with a highly non-linear material behavior,such as the plastic-damage model for cement-based materials.In the case of the explicit method,the solver equations can be solved directly to determine the solution without iteration,thus providing an alternative method.It is important when performing a quasi-static simulation that the inertial forces do not affect the mechanical response and provide unrealistic dynamic results.To reduce the dynamic effects,the ratio of the duration of the load and the fundamental natural period of the method should be greater thanfive.It has been shown that by keeping the ratio of kinetic energy to the total internal energy at b5%the dynamic effects in the model are negligible[57,58].This is the criterion for quasi-static behavior that is employed in this study.The ABAQUS/explicit quasi-static solver used an analysis time of 0.1s(period time).A displacement-controlled loading scheme was adopted in this simulation.After trial and comparison,the damage variables for the plastic-damage constitutive model are determined. In order to obtain complete stress–strain curves,all the analyses for uniaxial tension and compression were ended at a displacement d=0.09mm(ultimate strain0.0006)and0.9mm(ultimate strain 0.006),respectively.A computer with an Intel®Core I7processor and8GB physical memory was used for all the simulations.In this study,the FEA numerical response depends on two sets of parame-ters.Thefirst set is relevant to the tensile and compressive stress data which are provided as a tabular function of strain,which is directly obtained from the constitutive relation of each phase in MRAC.These mechanical properties are provided by experimental study and mix design.The other one is the definition of the damage variable as a tabular function of the inelastic strain for both the ten-sion and compression.If the damage variable is specified,ABAQUS au-tomatically calculates the inelastic and plastic strain values.The calibration of the damage variables is obtained through the best fitting of the complete compressive stress–strain curves as well as failure patterns(crack initiation and propagation)of MRAC with dif-ferent mixture proportions.4.3.Simulation results4.3.1.Uniaxial compressionAccording to the above parameters and descriptions,the complete compressive stress–strain curve and failure process of MRAC under uniaxial compression loading were calculated.In order to calibrate and validate the FEA,the simulation results will be compared with the test results the authors had completed by using Digital Image Cor-relation(DIC)technique on the displacement and strain measure-ments at microscale[10,51].The DIC technique was applied to record the initiation and propagation of surface microcracks for the tested samples.The experimental data are relevant to compression tests on MRAC specimens with the same old cement mortar mixture design(w/c=0.45)but three different new cement mortar mixture designs(w/c=0.36,0.45,and0.55).The mixture proportion details of MRAC specimens are listed in Table2.The experimental setup and basic failure pattern are shown in Fig.6.Fig.7shows the comparison between experimental and numerical complete stress–strain curves.The strain is evaluated by dividing the prescribed displacement by total height,and the stress is computed by the reaction force over the cross-section area.It can be found that the agreement between experimental data and numerical results is excellent,which is sufficient to assess the modeling capability of this numerical simulation.In addition to matching the stress–strain curves,the model also simulated crack initiation and propagation correctly.Fig.8shows the comparison on the plastic strain progres-sion(damage parameter)of MRAC30-30between experimental and numerical results at different loading levels.Each snapshot represents the strain levels in the Y direction.It should be noted that the contour map is scaled differently in each snapshot in order to show the strain range.The strain localization phenomenon was apparent at both new and old ITZs.The bond initiation and propagation of bond cracks were evident ahead of the macro-crack formation.For both the experimental and numerical results,the bond cracksfirst appeared around the weak ITZs and then connected with each others.As the load increased,the localized bond cracks increased and propagated around the aggregate.As the macro-crack formed at the ITZs,the strain contour map became less meaningful,while the crack estimation became dependent on the displacement contour map.Fig.9shows lateral displacement(failure pattern)comparison of MRAC30-30at different loading levels between experimental and numerical results[10,51].It is observed that the bond cracks around old and new ITZs developed across old mortar matrix,and propagates into new mortar matrix.In thefinal crack pattern,most cracks lined up vertically with the loading direction for both experimental and numerical results.Overall,the FEA analyses predict remarkably well the whole failure pattern of the MRAC under compression including the crack initiation,propagation and pattern.4.3.2.Uniaxial tensionBecause the uniaxial tensile test is still a big challenge,there is no available experiment data of MRAC under tensile for validation at this moment.In the tensile numerical simulation,the parameters applied for the simulation were assumed based on previous calibration of compression modeling.Additionally,parameter adjustments were not permitted except the displacement-controlled loading.Fig.10 shows the predicted stress–strain behavior of MRAC30-30resulting from the FEA simulation.The model is capable of predicting the com-plete stress–strain curve quite well considering the inelastic behavior of MRAC including strain softening,localization of deformation,and micro-crack pattern at different loading levels.Besides predicting the stress–strain curve,the model can also simulate the micro-crack initiation and propagation reasonably by the plastic strain progres-sion(see Fig.11).The fracture process starts around the aggregates as the cracks form,and propagates along both old and new ITZs. With the loading increased,the vertical displacement progression shows that one main crack dominates and propagates through the whole MRAC,while all the other micro-cracks closed(see Fig.12).0.0000.0010.0020.0030.00451015202530354045Stress(MPa)Strainpressive stress–strain curves with different new mortar matrices.91J.Xiao et al./Cement and Concrete Research52(2013)82–99。