浅谈陶瓷隧道窑运行中自动控制的设计
陶瓷隧道窑微机温度控制系统

陶瓷隧道窑微机温度控制系统摘要目前我国陶瓷隧道窑炉大多采用人工或简单仪表控制,要想使窑炉长期达到最佳工作状态是不可能的,造成产品合格率、一级品率一直处于较低的水平。
陶瓷隧道窑炉是由预热带、烧成带和冷却带三个部分组成,瓷件烧成温度在1320℃左右,窑内温度场主要由烧成带12对喷嘴燃冷煤气产生,窑炉系统用8组风机来调节窑内的压力场。
排烟风、助燃风将直接影响烧成带的温度场,急冷风会影响最终产品的质量。
温度控制系统将采集的各点温度值,经A/D转换后与设定值进行比较,控制器输出经由D/A变换,变成 4~20mA形式模拟量输出给电动执行器,驱动蝶形阀调节喷嘴的煤气进给量,从而控制烧成带的温度。
12只温度传感器与12个喷嘴一一对应。
关键词:MSP430F149单片机、热电偶,变送器、大林算法、I2C总线、多路开关一.总体方案设计 1.对象的工艺过程陶瓷隧道窑炉是由预热带、烧成带和冷却带三个部分组成,瓷件烧成温度在1320℃左右,窑内温度场主要由烧成带12对喷嘴燃冷煤气产生,窑炉系统用8组风机来调节窑内的压力场。
排烟风、助燃风将直接影响烧成带的温度场,急冷风会影响最终产品的质量。
温度控制系统将采集的各点温度值,经A/D转换后与设定值进行比较,控制器输出经由D/A变换,变成 4~20mA 形式模拟量输出给电动执行器,驱动蝶形阀调节喷嘴的煤气进给量,从而控制烧成带的温度。
12只温度传感器与12个喷嘴一一对应。
窑温控制示意图2.对象分析被控过程传递函数se s s G 403o )251(25.2)(-+=是一个大的延迟环节,而且温度的控制对系统的输出超调量有严格的限制,用最少拍无纹波数字控制器的设计,和PID算法效果欠佳,所以本设计采用大林算法设计数字控制器。
3.控制系统设计要求窑温控制在1320±10℃范围内。
微机自动调节:正常工况下,系统投入自动。
模拟手动操作:当系统发生异常,投入手动控制。
微机监控功能:显示当前被控量的设定值、实际值,控制量的输出值,参数报警时有灯光报警。
隧道窑炉温自动控制

隧道窑炉温自动控制隧道窑炉温自动控制A、测温点的选取对炉温控制而言,起关键作用的是烧成带。
为此,目前隧道窑的整个温度制度的控制,通常简化为对烧成带内若干个特定点的温度定值控制,即将烧成带的所有燃烧室分成若干个区,每一区选择一个测温点作为温度控制点。
其温度控制数值由工艺给定的温度控制来决定。
采用热电偶作为检测元件的有两种测温点选择方案;一种是选在侧墙上,将热电偶按垂直方向插入窑内,另一种是选在窑顶上,将热电偶按垂直方向插入窑内。
采用全辐射高温计作为检测元件的一般是在侧墙上留出水平方向的测温孔。
B、对温度测量信号的处理用全辐射高温计测量窑内火焰空间的温度时,很容易受到各种干扰因素的影响。
其中特别是火焰的脉动干扰,常使测量信号也出现严重的脉动情况。
全辐射高温计输出的热电毫伏信号,直接送至电子电位差计记录下来的温度曲线,其脉动辐度可达30~40℃,而把这样的温度测量信号送入炉温控制系统是不适当的。
因为这种脉动信号将使调节器的输出电流也随着发生波动,导致调节阀的频繁动作,显然这种情况对控制系统的工作是十分不利的。
为此,必须设法减少温度测量信号的脉动,经常采用的方法是利用由电容和电阻组成的电子滤波器,对脉动信号进行滤波。
全辐射高温计输出的热电毫伏信号送至DBW型温度变送器,变送器输出的脉动电信号进入RC滤波器,滤除脉动分量后的电流信号经电阻R1进入调节器。
同时从电阻R1上取得电压毫伏信号送至电子电位差计作记录用。
~ 1 ~RC滤波器中的电阻R和电容C的取值,可以通过实验来确定,一般R取1KΩ左右,C取4000uF左右。
C、热电偶的安装为了保证热电偶的测量精度,灵敏度和可检验性,使用寿命,以及安装和维护的方便,必须注意热电偶在窑炉上的安装基本方法和特点。
①窑炉碹顶上安装热电偶测量燃烧式工业窑炉火焰空间温度时,一般采用窑炉碹顶上安装热电偶,在碹顶测量点耐火砖预留孔内,插入WRR型或WRP型热电偶,并用耐火泥填塞孔隙,防止窜火,这是最简单的安装方法。
自控日用瓷高温(还原焰)轻型隧道窑的设计及热工特征

成一个大的空间 , 窑道上部切面大 , 在烟气几何压 头的作用 , 上部流过的热烟气多而温度高,而坯垛 中下部温度低, 形成窑道切面上下部温度较大的差 异。 为了克服上述弊端, 轻体隧道窑采用悬挂式平
吊顶 ,烧成 带 向氧化带 、预 热带方 向分 倒梯 式降 低 窑顶 的高 度 。烧成 带高 温 区,上部 设烧 嘴 ,窑顶 与
( m W/ )
73 3
( ℃)
7 7
.
( ℃/ ) 量 ( / ) m W MJ m 16 .
16 .1
9
18 29
39 2
重质砖组合样体
轻质砖组合样体纤
轻型隧道 A 7 55
44 1
79 2
7 . 74
窑墙体
B 3o 0
5 7
76 5
7 3 9
连续式轻型隧道窑窑体在正常运行中处于稳态 传热过程 , 其窑体材料主要有足够大的热阻以减少
2 、轻型隧道窑主要 技术参数
窑 全长 :0 6 m
散热。 连续式窑有停窑、烘窑及窑温波动这些非稳 态传热问题 , 因此减少窑体蓄热以求快速烘窑、 停
窑, 并有利 自动控制。 以连续式窑窑体轻型化是 所
.
15 .5
3. 85
维模块组合窑体
注 :蓄热量是指窑墙从常温到达稳态时的蓄热量。
拱顶 的 自重 由墙体 承受 。 型隧道 窑悬 挂式 平 吊顶 轻
热带 窑道上 下部 温差 。
其结构使窑顶和窑墙脱开, 窑顶的 自重力不再作用
于 窑体 , 而全 由钢 架立柱 承受 , 横推力 几乎 为零 。 弧 形拱的 最大缺 陷是 预热 带 , 坯垛 顶面 与拱 顶之 间形
隧道窑控制系统及操作应用

隧道窑控制系统及操作应用隧道窑控制系统使用与窑炉基本故障排除方法自动焙烧控制系统,实现自动焙烧首先必须要建立一个标准,利马窑炉控制设备提供了三种建立标准的办法,第一个是在机柜内有一个空气开关,这个开关上下扳动一次就可以自动建立这个扳动时刻为参考点的标准,这个扳动时刻一定是窑炉工作状况良好,烧出的砖质量好的情况下完成。
第二个是可以根据所烧出砖的历史数据,选择比较理想的那车转,在顶车前五分钟的数据为参考点设定一个标准。
第三个通过操作面板上界面人工修正的一个标准,通常可以参考设备的人工修正标准来控制焙烧。
正常焙烧温度、产量和质量的控制一、合理配风,控制焙烧窑的温度、产量和质量主要是合理配风。
所谓合理配风,就是窑里面焙烧点的氧气不多也不少,我们是用空气来烧砖,空气中的氧含量是21℅,可以用简单的办法检测窑里面是不是缺氧(风的大小)或不缺氧,在焙烧窑温度顶点(最高温度点)往前(进砖方向)走一个车位,打开火眼管盖子,将一块木柴从火眼管放进去,盖上管盖。
揭开管盖,木柴已经燃烧有明火了,证明窑里面不缺氧;如果当揭开管盖,木柴过一两秒钟突然冒出明火就证明窑里面缺氧。
计算机配风就是根据每次加风或是减风,焙烧段的温度是升高还是减少来决定的。
二、及时顶车,顶车就是烧砖,烧砖就等于往窑里面投煤(砖里面有内燃煤),控制风及顶车实质上就是控制氧气和煤耗,控制这两个就可以把窑烧好,烧出质量好产量高的产品。
风闸的使用风闸的使用正确与否显得十分重要,风闸的使用大致分为三种,一是梯形闸,二是桥型闸,三是倒梯形闸。
梯形闸,就是从进砖的方向的风闸开得最大,从风闸的2号或者3号是最高的一个拉闸,最大的拉闸,就是风管半径的一个拉闸。
例如直径400MM的风闸,最大的拉闸就是200MM,往后走可以拉6对、8、9对闸,并逐步减小。
拉梯形闸,要求砖坯要干,砖坯进窑就加温,出高产量。
桥型闸,2、3车位是最低的,8、9车位也是最低的,中间是最大的,也就是风闸呈中间大两头小分布格局。
浅谈隧道窑控制方法

浅谈隧道窑控制方法随着窑操作控制包括温度、气氛和压力控制三部分。
其中压力制度是温度控制和气氛制度的保证。
1、各带温度的控制根据制品的原料性质、制品的形状和大小以及入窑水分等工艺要求,制定一条合理的烧成温度曲线,焙烧时就按照这条曲线来保证一定的升温、保温和冷却制度。
隧道窑大致分为预热带、烧成带和冷却带三个部分。
下面分别简述各带的温度控制。
1.1预热带的温度控制预热带是指制品入窑到第一燃烧室止,一般为十几个车位。
温度控制是指按升温曲线均匀加热,一般在窑顶板上都安装有热电偶来监控温度。
如果窑头温度过高,易使入窑水分高的制品炸裂,入窑水分低于0.5%,则窑头温度可高一些。
500℃左右是石英昌型转变温度,有体积变化,应保持温度稳定。
所以,不但要控制窑顶温度,还要控制窑车台面温度,使上下温差减少。
预热带的温度控制手段主要是通过调节风闸和排烟风机的变频器来控制气体流量。
风闸开启大,则预热带负压大,易漏入冷空气,加剧气体分层,增大了上下温差,风闸开启小,则抽力不足,烟气量小,升温慢。
高档焙烧窑采用变频柜来控制制品的升温。
风闸调好后锁定,如果预热带未端风闸开启大,则大量烟气过早排出,热利用率低,窑头温度低,制品升温慢。
如预热带风闸不开,则大量烟气涌向窑头,致使窑头温度过高,不利于制品预热。
窑头的风闸也不能开启过大,以免该处负压大,从窑门涌入大量冷空气。
总之,要保证制品在一定的温度下预热,并保证上下温差小,窑车接头处必须严密不漏气,砂封板接头要靠紧,砂封板要埋入砂中4-6cm。
另外,合理的码歪也能减少制品上下温差,根据内燃和外燃的不同情况,坯体要合理码放,坯垛与窑墙间距不能太大,内部要有足够和畅通的气体通道,增加气流阻力,减少上部和周边气流,使气流在坯垛中分布均匀,达到上下内外温度均匀。
1.2烧成带的温度控制烧成带的温度控制是指要控制实际燃烧温度和高烧成温度。
一般火焰温度应高于制品烧成温度50℃-100℃,火焰温度的控制通过调节单位时间内燃料消耗量和空气的配比来实现,单位时间内燃料的燃烧的彻底而空气量又恰当,则火焰温度高。
一种陶瓷辊道窑温度自动控制系统设计

传统的陶瓷辊道窑生产中,当出现异常情况时,会导致窑炉空窑,这就需要窑炉操作员及时对窑炉温度进行监控并结合产品在窑炉内空窑的位置进行手动调节。
由于原料配方或者设备故障原因等客观存在的因素导致出现空窑,对异常问题的处理高度依赖个人经验。
本文设计的方案主要是通过获取各段窑炉的传动线速度并监控进砖信号开发对窑炉内产品位置进行实时动态仿真模拟控件,从而获取产品在窑炉内的位置状态信息,根据这些信息系统利用算法进行智能分析出窑炉内哪个位置存在空窑或稀窑,然后根据用户设定的温度控制参数,系统将自动进行温度调节,从而实现窑内温度自动调节到生产需求。
空窑温度控制系统的投入使用将大大降低窑炉操作人员的工作强度,提升温度控制的及时度及精度,同时也在节约能源方面发挥着举足轻重的作用。
窑炉空窑温度自动控制系统硬件设计主要包括传动数据采集系统、进砖信号采集系统、温度控制系统三个部分,系统硬件结构图如图1所示。
整个系统基于计算机系统实现功能,通过PLC 采集进砖信号实现砖块位置传输给计算机,通过通讯模式实现对传动速度的采集和温度的采集,汇总给计算机通过算法实现窑炉空窑温度自动控制的功能。
整个系统运行的最终目的是:当窑炉空窑或稀窑时,系统可以控制窑炉降低温度,当空窑结束时,控制窑炉恢复生产温度,从而达到在不影响产品质量的情况下节能的目的。
计算机获取窑炉的速度,主要是通过采集变频器的频率,通过电机和辊棒之间线性关系换算成窑炉速度(如图2)。
龙威舜,蓝万聪(佛山市科达机电有限公司,佛山528000),辊道窑炉的烧成温度稳定对产品烧成质量起决定性的作用,辊道窑是一种连续性生产模式,这种模式决定了温度的自动控制要求比较高。
由于各种原因,导致辊道窑很难持续满窑生产,会出现不间断的空窑现象。
在传统窑炉的温度控制中,往往需要人工根据经验针对空窑的情况进行手动调节温度,这样无形中增加了很大的操作难度,同时容易产生不良品。
本文设计了一套窑炉空窑温度自动控制系统,当出现空窑时,根据空窑位置及设定的温度控制参数进行自动调节,进而保持窑炉内部的温度稳定。
全自动还原焰日用陶瓷隧道窑的设计
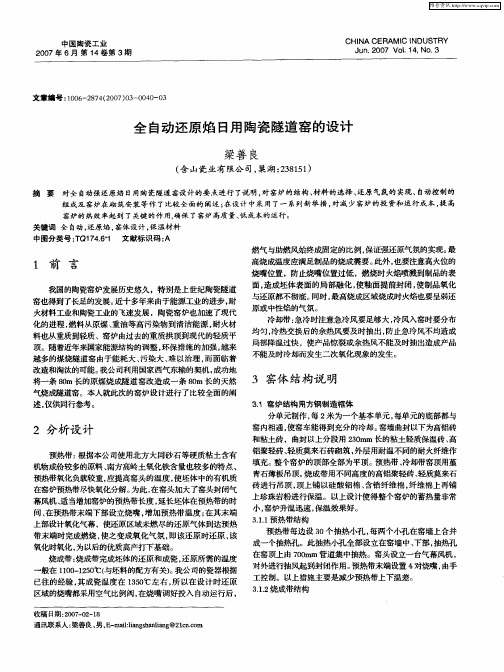
全 自动还 原焰 日用 陶瓷 隧道 窑 的设 计
梁善 良
( 山瓷 业有 限公 司 , 含 巢湖 :31 1 285 )
摘 要 对全 自动强还原焰 日用陶瓷隧道 窑设计的要点进行 了说 明 , 对窑炉的结构 、 材料 的选择 、 还原 气氛的实现 、 自动控 制的 组 成 及 窑 炉 在 砌 筑 安 装 等 作 了 比较 全 面 的 阐 述 ; 设 计 中 采 用 了一 系列 新 举 措 , 减 少 窑 炉 的投 资 和 运 行 成 本 , 高 在 对 提
述, 仅供同行参考 。
局部降温过快 , 产品惊裂或余热风不能及时抽出造成产品 使 不能及时冷却而发 生二次氧化 现象的发生 。
3 窑体 结 构 说 明
31窑炉结构用方钢制造框体 .
2 分析设计
分单元制作 , 2 每 米为一 个基本 单元 , 每单元的底部都与 窑 内相通 , 车能得到 充分 的冷却 。 墙曲封以下为高铝砖 使窑 窑
一
小。 窑炉升温迅速 , 保温效果好 。
收稿 1 :0 7 0 — 8 3 20 - 2 1 期 通讯联 系人 : 梁善良 , E m il n sal n @2c . I 男, - a : ghni g ln O l li a a Cl
维普资讯
冷却带 : 急冷时注意急冷风要足够大 , 冷风入窑时要分布 均匀 , 冷热交换后的余热风要及时抽 出 , 防止急冷风不均造成
火材料工业和陶瓷工业的 飞速发展 , 陶瓷窑 炉也 加速 了现 代 化的进程 , 料从原煤 、 油等 高污染物到清 洁能源 , 燃 重 耐火材 料也从重质到轻质 、窑炉 由过去的重质拱顶到现 代的轻质平 顶 。随着近年来国家能源结构的调整 , 环保措施的加强 , 来 越 越多的煤烧隧道窑 由于能耗大 、 污染 大 、 以治理 , 难 而面 临着 改造和淘汰的可能。 我公司利用国家西气东输 的契机, 成功地 将一条 8 m长的原煤烧 成隧道 窑改造 成一条 8 m长 的天 然 0 0 气烧成隧道窑。本人就此次的窑炉设计进行 了比较全面的阐
微电脑自动控制环型旋转式节能烤花隧道窑的研发-精选文档

微电脑自动控制环型旋转式节能烤花隧道窑的研发1 前言近年来,陶瓷工业窑炉发展十分迅猛。
微电脑自动控制环型旋转式节能烤花隧道窑具有低能耗、低污染、高效率、运行灵活、操作方便、造价低、占用场地少等优点。
因此,赢得各中、小型陶瓷产品烤花加工厂家的喜爱。
2 烤花隧道窑所存在的问题为对新型烤花窑炉的设计有较明确的目标,笔者组织了一个科研小组对当前较常用的烤花隧道窑进行全面的调查与分析。
?分析,旧式烤花隧道窑所存在的问题如下。
2.1能耗大烤花隧道窑的窑体内胆为普通低铝轻质砖,中间夹一层保温棉,外壁封普通铁皮。
由于普通低铝轻质砖含泥量高,同时在升温的过程中要吸收大量的热量,且升温速度较缓慢。
因此,要达到烧成的额定温度,一般需要10h左右,造成能量消耗严重。
2.2窑内上、下温差大窑内上、下温差大的原因:一方面是由于烧成段的火枪布局不合理所造成的。
它的烧成段加热火枪采用两侧排列,底部无加热火枪。
根据热传递原理,热总是上升的,这样窑的顶部温度高而下部温度低;另一方面由于测温热电偶装在窑的顶部,因而只能测到窑内顶部温度,而测不剑下部的温度,因此所测的温度值与窑内的实际温度偏差很大。
温差大导致产品生产速度慢、合格品率低。
2.3占用场地大窑的墙壁较厚,一般单面墙壁厚度为63cm,如工作截面有效宽度为80cm时,两侧墙壁厚度为126cm,总宽度约206cm,因而工作场地较浪费。
2.4建成进度慢窑体由普通低铝轻质砖、高铝粉加保水剂作粘合剂组成。
如果粘合剂真正要凝固,需要相当长的时间,从而大大影响建造速度。
一般建造一座长30m的辊底烤花隧道窑需要约3个月的时间。
2.5操作灵活性差,产品质量不稳定烤花隧道窑烧成调节为手工操作,加上普通低铝轻质砖要吸收一定热能,存在升温依赖性,烧成产品稍改变,就必须调节液化气的压力和空气的配比。
要达到所需要的工作温度,需要调整较长的时间,导致出产量低、产品质量不稳定。
3 新型窑炉的研发针对烤花隧道窑所存在问题,根据国内目前中小型陶瓷烤花加工厂的迫切需求,通过分析与研究,成功研发出环型旋转式节能自动控制烤花隧道窑φ5m~φ14m系列,并从2002年开始投放使用至今,深得广大用户的欢迎和好评。
- 1、下载文档前请自行甄别文档内容的完整性,平台不提供额外的编辑、内容补充、找答案等附加服务。
- 2、"仅部分预览"的文档,不可在线预览部分如存在完整性等问题,可反馈申请退款(可完整预览的文档不适用该条件!)。
- 3、如文档侵犯您的权益,请联系客服反馈,我们会尽快为您处理(人工客服工作时间:9:00-18:30)。
围一
关键词 : 自动 化 ; 劳动 强 度 ; 精度 ; 质 量
l 前 言
本 文 以某 陶 瓷 工 艺 厂 设 计 、 安 装 的 陶 瓷 隧 道 窑 运 行 操 作 工 艺 流 程 自动 控 制 为 例 ,分 析 了其 中 的 五 个 主 要 组
传动流程 示意 图如图 1 所示 。 当前 , 随着社 会科学 技术 的不 断进步 , 人们 对各 自的 成部分 , 工作 环境 、 劳 动强度 、 控 制精 度 、 产 品质量 等 方面 要求 越 来 越高 , 迫 切需求探 索一种能够 解决 以上 问题 的方 法 。 而
固 一圆 圈
f
K8
右
f
K7
f
f
R1 6 K6
控 制单元 前 , 把 它们有 机 的贯穿在 一起 , 形 成一 个 闭环 的
控 制 系统 ,最 后 实 现 陶 瓷 隧道 窑 整 个 运 行 操 作 工 艺 流 程
自动 化
K 一位 置判 断器 、 K 1 一 A 车 位 窑 车 到 位 判 断 ,且 使 A 推 杆 前 进, 同时 后 退 、 K 2 一托车 A到达主车道后端 、 K 3 一 托 车 A 到 达 回车道 后端 、 K 4 一托 车 A上推 杆前 进 、 K 5 一 托 车 A 上 推 杆 后 退、 K 6 一B车位 窑车 到位 、 K 7 ~ 推杆 前进 、 K 8 一 C车 位 到 位 、
浅谈 陶瓷 隧道 窑运 行 中 自动控制 的设 计
吴 俊 杰
( 广 东 省 枫 溪 陶瓷 丁业 研 究 所 , 潮州 5 2 1 0 3 1 )
摘
要: 在 陶 瓷 隧 道 窑 运 行 中引 入 自动 化 控 制 系 统 , 使 之
劳动强度大大降低 、 工作效率大大提 高、 控制精度 高 、 产 品 质 量提 高 、 故障率低 , 从 而 提 高 了经 济 效 益 。
前 进 的 自动控 制 任 务 。
2 . 2 托车 自动控 制系统 的运行方式
托 车 系 统 由托 车 、 平移传 动装置 、 托 车 上 窑 车 推 拉 装 置、 电气 控 制 装 置 等 部 分 组 成 。 托 车 的 主要 任 务 是 承 载 窑
车 :平移传动装置 的主要任务 为完成 托车的左右移动 : 推
推车方向
窑 眉
产厂家 的喜爱 。
从 现 有 陶 瓷 隧 道 窑 的 操 作 工 艺 流 程 分 析 得 知 ,它 由
回车方向
传动 、 温度检测 、 故 障检测 、 装车检 测 、 进 车检测 等部 分组
成 。实 践 证 明 , 要 实 现 自动 控 制 , 就 必 须 在 独 立 开 环 自动
制装置 、 位 置判断器等组合 而成 。运行时 , 当窑前 、 窑车 D
位、 K 9判 断 器 等 判 断 到 已 有 窑 车 到 位 , 同时 , 主 轨 道 末 端 A车位 K 1判 断 器 判 断 A 位 是 空 车位 状 态 ,即 : K 9 ・ K1 = 1 时。 发 出指令给 电气控制装 置 , 电气 控 制 装 置 接 到 该 指 令
拉 装 置 的 主 要 任 务 为 完成 主 、 回轨 道 上 的窑 车 进 、 出 。A托 车 是 把 主 轨 道 A位 窑 车 送 上 托 车 ,然 后 平 移 到 回车 轨 道 , 再把托车 上的窑车送上 回车轨道 , B托 车 是 把 回车 轨 道 C 位 的窑 车 送 上 托 车 , 然后 托车平移 至主轨道 , 再 把 托 车 上
后, 使推杆 开始T作 , 窑车前进 ; 当判断器 K 1 或 K1 5进行
判断 ( 即K 1 + K1 5 = 1 时) 时, 窑 车 已到 达 A 车 位 或 推 杆 档 块 已 到位 时 , 发 出指令给 电气控制装 置 , 电气 控 制 装 置 接
到该指令 后 。 使推杆 档块停 止前进 。 同时 , 延时 2 s 后. 推 杆档块后 退复位 。 周而复 始的控制 , 从 而完成 了轨道 窑车
陶 瓷 隧道 窑 运 行 操 作 自动 控 制 系 统 的 问世 ,基 本 可 以 解 决这些 问题 , 大 大 降低 了 陶 瓷 隧 道 窑 的劳 动 生 产 强 度 . 同 时, 也 推 动 劳 动 生 产 力 向前 发 展 。 因 此 , 深 得 各 大 陶 瓷 生
左
圆 圈 道圈 兰 占
作 者简介 : 吴俊杰 , 男, 1 9 5 6年 7月 出生 , 1 9 8 0年 7月 毕 业 于 华 南 理 X - 大
学电力 系, 分 配 到 广 东省 枫 溪 陶 瓷 工 业 研 究 所 , 从事陶瓷窑炉研发。
到位、 K1 7, K1 8 一 托 车 上 负 载判 断
图 1 传动流程 图
2 传 动 自动 控 制 部 分 系 统 简介
K 9 一A推杆前 进 、 K1 0 一 托车 B到达 主轨道 、 K 1 1 一 托 车 B上 推杆后 退 、 K1 2 一 托车 B上推杆 前进 、 K 1 3 一 托 车 B到 达 回 车 道、 K1 4 一 推 杆 A后 退 、 K1 5 一推杆 A前进 、 K 1 6 一 推 杆 B后 退
传 动 自动 控 制 由 窑 内主 轨 道 窑 车 、 窑外 回车道窑 车 、 这 样 完成 了 从 主 车 道 A 位 窑 车 送 到 回车 道 B位 处 , 同 时 窑前托车 、 窑 后 托 车 四部 分 组 成 。由 于 窑 内与 窑 外 轨 道 窑 复 位 于 主 车 道 的 一 个 周 期 动 作 , 周 而复位 , 使 轨道 窑车 自
2 . 1 轨道窑车 自动控制系统 的运行方 式
轨 道 窑 车 自动 控 制 系 统 由 推 杆 ( 螺 旋 式 推 杆 或 液 压 式推 杆 ) 、 档块 、 减速 器 、 调 速 电机 、 皮带 、 皮 带轮 、 电气 控
表 常开闭合杆 的运 行 逻 辑 关 系
车运行 作用 相 同 , 窑前 和窑 后托 车运 行作 用相 同 , 因此 , 动推 拉 ,托车上 的负载窑 车 自动传送 而成 为一个 自动控
本文只讨论轨道 窑车和托车 的运行情况 。 制 环 节 。表 1 ~ 表 6是 各 传 动 装 置 的 逻 辑 关 系 , 其中, K = I