冲压件毛刺检验规范及标准
剪板冲压毛刺控制标准

剪板冲压毛刺控制标准文件管理序列号:[K8UY-K9IO69-O6M243-OL889-F88688]QS/ZG电梯有限公司企业标准版本号:A0 ZG-CS62-2017发放部门:质管部持有部门:总经办、生产部、质管部剪板冲压毛刺控制标准编制:审核:批准:2017年06月15日发布 2017年07月01日实施电梯有限公司批准评审会签记录版本记录1.目的为标准规定了钣金冲裁加工毛刺长度标准,确定生产过程毛刺质量的控制标准。
2.范围本规范适用于公司所有的冲裁产品毛刺质量控制。
3.管理职责由制造部负责对冲裁产品进行自检工作,超出标准及时对隐患点处理。
由质管部负责对冲裁产品做好监控工作,并妥善保管相关检验记录。
4.冲裁件毛刺的极限值说明4.1冲裁件毛刺超过一定的高度是不允许的,冲压件毛刺高度的极限值(mm)见下表。
* f级(精密级)适用于较高要求的零件;m级(中等级)适用于中等要求的零件;g级(粗糙级)适用于一般要求的零件。
表1 冲压件毛刺高度的极限值4.2等级要求:技术图纸未注则按m级控制4.3毛刺的方向要求:毛边方向:朝里(朝使用时不可视的方向或折弯方向)。
4.4需要压毛边(毛刺打磨)的部位:对暴露在外面的断口;人手经常触摸到的锐边;需要过线缆的孔或槽;有相对滑动的部位需要对毛刺增加打磨工序,具体按图纸技术要求执行。
4.5常用材料抗拉强度参考(具体需查材料手册):冷轧钢板08F:295MPa; 1Cr18Ni9(SUS304不锈钢):≥520MPa;热轧钢板Q215:335~410mpa;热轧钢板Q235:375~500MPa;热轧钢板Q345:490~620MPa.5.不合格品控制按QSE-QP24-2017《不合格品控制程序》执行。
6.相关文件6.1 JB/T4129 -1999《冲压件毛刺高度》6.2 QSE-QP24-2017《不合格品控制程序》7.相关记录。
冲压件毛刺检验指导书
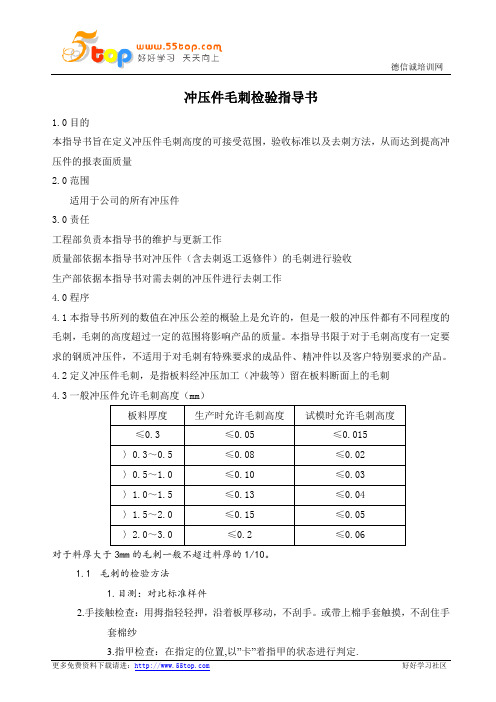
冲压件毛刺检验指导书1.0 目的本指导书旨在定义冲压件毛刺高度的可接受范围,验收标准以及去刺方法,从而达到提高冲压件的报表面质量2.0 范围适用于公司的所有冲压件3.0 责任工程部负责本指导书的维护与更新工作质量部依据本指导书对冲压件(含去刺返工返修件)的毛刺进行验收生产部依据本指导书对需去刺的冲压件进行去刺工作4.0 程序4.1 本指导书所列的数值在冲压公差的概验上是允许的,但是一般的冲压件都有不同程度的毛刺,毛刺的高度超过一定的范围将影响产品的质量。
本指导书限于对于毛刺高度有一定要求的钢质冲压件,不适用于对毛刺有特殊要求的成品件、精冲件以及客户特别要求的产品。
4.2 定义冲压件毛刺,是指板料经冲压加工(冲裁等)留在板料断面上的毛刺4.3 一般冲压件允许毛刺高度(mm)板料厚度生产时允许毛刺高度试模时允许毛刺高度≤0.3 ≤0.05 ≤0.015〉0.3~0.5 ≤0.08 ≤0.02〉0.5~1.0 ≤0.10 ≤0.03〉1.0~1.5 ≤0.13 ≤0.04〉1.5~2.0 ≤0.15 ≤0.05〉2.0~3.0 ≤0.2 ≤0.06对于料厚大于3mm的毛刺一般不超过料厚的1/10。
1.1毛刺的检验方法1.目测:对比标准样件2.手接触检查:用拇指轻轻押,沿着板厚移动,不刮手。
或带上棉手套触摸,不刮住手套棉纱3.指甲检查:在指定的位置,以”卡”着指甲的状态进行判定.确认位置以各表面进行.不可”卡”着指甲4.过纸检查:在指定的位置,以A4纸作R部,约45o倾斜,以前端部”卡”着状态移动,进行判定..前端不可”卡”着F5.卡尺测量(毛刺较大),4.5毛刺的清除1、对于小毛刺可以先用锉刀或刮刀修锉,然后用砂纸进行精砂;对于较大毛刺先采用旋转研磨机去除毛刺,然后用抛光轮抛光但注意造成零件的变形量,更不能伤到产品其它表面。
注意在使工具手工去刺时,工具防向要与毛刺方向成一定的倾角。
2、喷砂。
钣金冲压件毛刺高度标准及检验方法
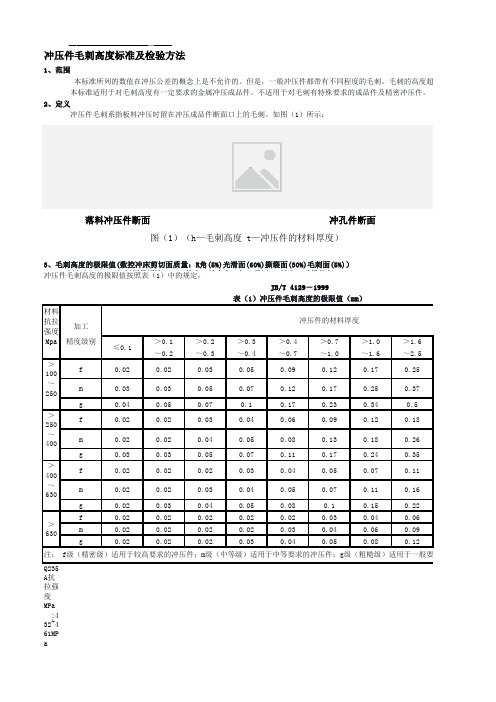
材料抗拉强度加工Mpa 精度级别>0.1>0.2>0.3>0.4>0.7>1.0>1.6~0.2~0.3~0.4~0.7~1.0~1.6~2.5>100f 0.020.020.030.050.090.120.170.25~250m 0.030.030.050.070.120.170.250.37g 0.040.050.070.10.170.230.340.5>250f 0.020.020.030.040.060.090.120.18~400m 0.020.020.040.050.080.130.180.26g 0.030.030.050.070.110.170.240.35>400f 0.020.020.020.030.040.050.070.11~630m 0.020.020.030.040.050.070.110.16g0.020.030.040.050.080.10.150.22f 0.020.020.020.020.020.030.040.06m 0.020.020.020.020.030.040.060.09g0.020.020.020.030.040.050.080.12Q235A抗拉强度MPa :432~461MP a本标准适用于对毛刺高度有一定要求的金属冲压成品件。
不适用于对毛刺有特殊要求的成品件及精密冲压件。
2、定义冲压件毛刺高度标准及检验方法1、范围本标准所列的数值在冲压公差的概念上是不允许的。
但是,一般冲压件都带有不同程度的毛刺。
毛刺的高度超过用性能。
冲压件毛刺系指板料冲压时留在冲压成品件断面口上的毛刺。
如图(1)所示:落料冲压件断面冲孔件断面图(1)(h—毛刺高度 t—冲压件的材料厚度)3、毛刺高度的极限值(数控冲床剪切面质量:R角(5%)光滑面(60%)撕裂面(30%)毛刺面(5%))(30%)毛刺面(5%),可切板厚最厚达4MM.。
特点:精度高,加工灵活.。
缺点:受模具限冲压件毛刺高度的极限值按照表(1)中的规定。
冲压件外观通用检验规范
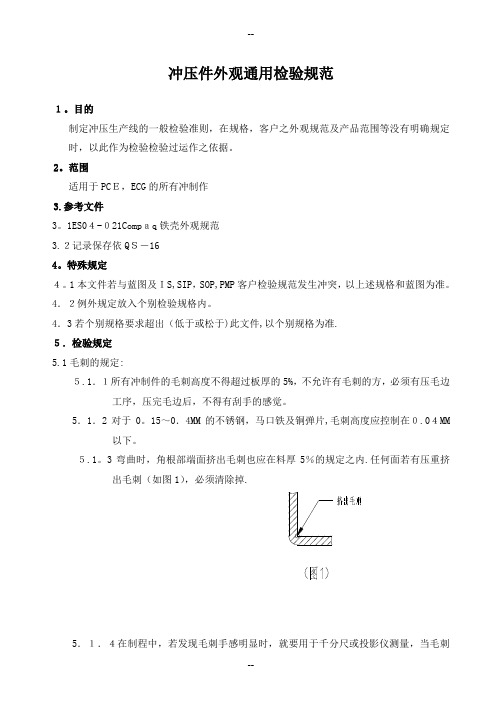
冲压件外观通用检验规范1。
目的制定冲压生产线的一般检验准则,在规格,客户之外观规范及产品范围等没有明确规定时,以此作为检验检验过运作之依据。
2。
范围适用于PCE,ECG的所有冲制作3.参考文件3。
1ES04-021Compaq铁壳外观规范3.2记录保存依QS-164。
特殊规定4。
1本文件若与蓝图及IS,SIP,SOP,PMP客户检验规范发生冲突,以上述规格和蓝图为准。
4.2例外规定放入个别检验规格内。
4.3若个别规格要求超出(低于或松于)此文件,以个别规格为准.5.检验规定5.1毛刺的规定:5.1.1所有冲制件的毛刺高度不得超过板厚的5%,不允许有毛刺的方,必须有压毛边工序,压完毛边后,不得有刮手的感觉。
5.1.2对于0。
15~0.4MM的不锈钢,马口铁及铜弹片,毛刺高度应控制在0.04MM 以下。
5.1。
3出毛刺(如图1)5.1.4在制程中,若发现毛刺手感明显时,就要用于千分尺或投影仪测量,当毛刺高度大于4%时,就要做好检查记录并要求修模,但已冲零件放行。
5.2平面度的规定:5.2.1冲件平面不允许有与蓝图不符之最严重翘曲。
5.7聚固件5.7.1紧固件须与基材紧密相连,符合安装程序及制程中尺寸。
5。
7.2紧固件在安装中不能变形或挤压变形.5.7.3基材安装中不能变形或凸出。
5.7.4长的压件如螺柱STANDOFF,ETC须垂直度〈1。
5°5.10字模:5.10。
1字模清晰完整,距离18``目视可识别清楚,压印之每一个单个字体深度一致,深度差距在0.1MM,有异议时送检测剖开测量。
5.10.2不允许缺齿,缺角.5.10.3版次与蓝图及ECN版次一致。
5.10。
4字模在零件中的位置及方向必须与图面一致。
5。
10.5字模面之背部不能有凹陷及凸出手感,弹片例外。
5。
10.6字模中每一个单个字体所使用之字型格式一样.5。
10。
7量.5.105.11沙拉孔:有怀疑时,5。
12螺纹5。
12。
1所有攻牙,必须用牙规测量。
五金(冲压件)的检验标准
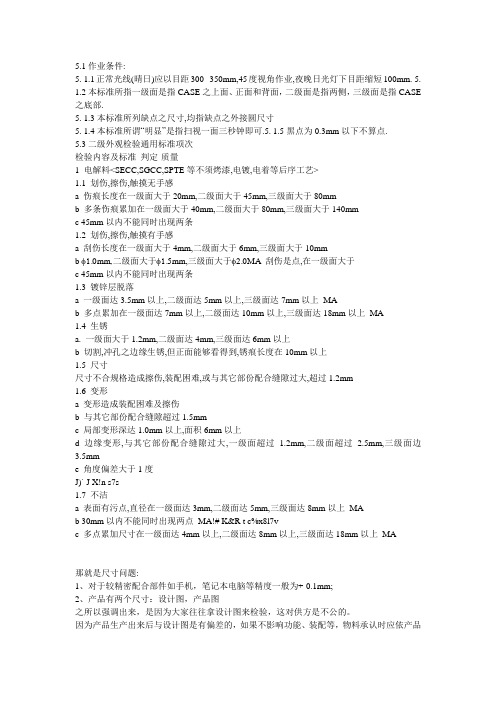
5.1作业条件:5. 1.1正常光线(晴日)应以目距300--350mm,45度视角作业,夜晚日光灯下目距缩短100mm. 5.1.2本标准所指一级面是指CASE之上面、正面和背面,二级面是指两侧,三级面是指CASE 之底部.5. 1.3本标准所列缺点之尺寸,均指缺点之外接圆尺寸5. 1.4本标准所谓“明显”是指扫视一面三秒钟即可.5. 1.5黑点为0.3mm以下不算点.5.3二级外观检验通用标准项次检验内容及标准判定-质量1 电解料<SECC,SGCC,SPTE等不须烤漆,电镀,电着等后序工艺>1.1 划伤,擦伤,触摸无手感a 伤痕长度在一级面大于20mm,二级面大于45mm,三级面大于80mmb 多条伤痕累加在一级面大于40mm,二级面大于80mm,三级面大于140mmc 45mm以内不能同时出现两条1.2 划伤,擦伤,触摸有手感a 刮伤长度在一级面大于4mm,二级面大于6mm,三级面大于10mmb φ1.0mm,二级面大于φ1.5mm,三级面大于φ2.0MA 刮伤是点,在一级面大于c 45mm以内不能同时出现两条1.3 镀锌层脱落a 一级面达3.5mm以上,二级面达5mm以上,三级面达7mm以上MAb 多点累加在一级面达7mm以上,二级面达10mm以上,三级面达18mm以上MA1.4 生锈a. 一级面大于1.2mm,二级面达4mm,三级面达6mm以上b 切割,冲孔之边缘生锈,但正面能够看得到,锈痕长度在10mm以上1.5 尺寸尺寸不合规格造成擦伤,装配困难,或与其它部份配合缝隙过大,超过1.2mm1.6 变形a 变形造成装配困难及擦伤b 与其它部份配合缝隙超过1.5mmc 局部变形深达1.0mm以上,面积6mm以上d 边缘变形,与其它部份配合缝隙过大,一级面超过 1.2mm,二级面超过 2.5mm,三级面边3.5mme 角度偏差大于1度J)` J X!n s7s1.7 不洁a 表面有污点,直径在一级面达3mm,二级面达5mm,三级面达8mm以上MAb 30mm以内不能同时出现两点MA!# K&R t c%x8l7vc 多点累加尺寸在一级面达4mm以上,二级面达8mm以上,三级面达18mm以上MA那就是尺寸问题:1、对于较精密配合部件如手机,笔记本电脑等精度一般为+-0.1mm;2、产品有两个尺寸:设计图,产品图之所以强调出来,是因为大家往往拿设计图来检验,这对供方是不公的。
冲压件尺寸精度质量要求
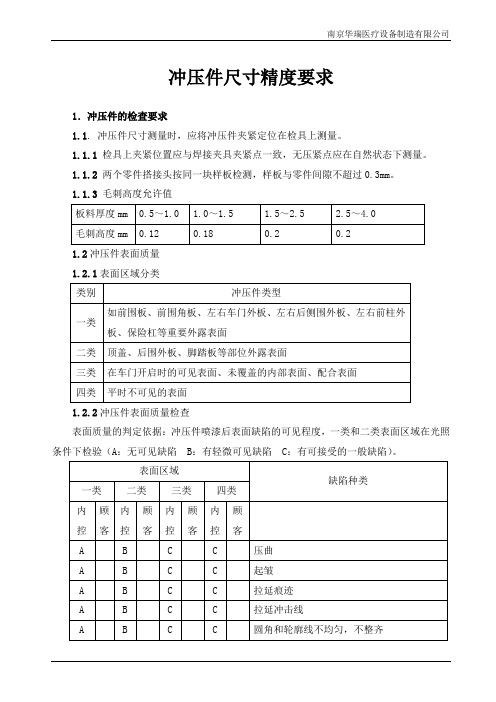
冲压件尺寸精度要求1.冲压件的检查要求1.1. 冲压件尺寸测量时,应将冲压件夹紧定位在检具上测量。
1.1.1 检具上夹紧位置应与焊接夹具夹紧点一致,无压紧点应在自然状态下测量。
1.1.2两个零件搭接头按同一块样板检测,样板与零件间隙不超过0.3mm。
1.1.3毛刺高度允许值1.2冲压件表面质量1.2.1表面区域分类1.2.2冲压件表面质量检查表面质量的判定依据:冲压件喷漆后表面缺陷的可见程度,一类和二类表面区域在光照条件下检验(A:无可见缺陷 B:有轻微可见缺陷 C:有可接受的一般缺陷)。
1.3.冲压件尺寸公差要求2. 冲压件未注公差尺寸的极限偏差2.1平冲压件长度L,直径D、d未注公差尺寸的极限偏差按表1规定。
表1注:上表中如果是孔类其公差取正值;如果是轴类则取负值;若是非孔轴类则取正负值,此时其偏差数值取表中值之半。
2.2未注公差成形尺寸的极限偏差2.2.1弯曲长度尺寸及拉延深度未注公差尺寸的极限偏差按表2规定。
表22.2.2加强筋、加强窝高度h未注公差尺寸的极限偏差按表3规定。
表32.3未注公差圆角半径极限偏差2.3.1冲裁圆弧半径R的极限偏差按表4规定。
表42.3.2两冲裁面构成的内部和外部尖角如图样上未注明要求时,按小于或等于料厚t 取值。
2.3.3 未注公差成形圆角半径的极限偏差按表5规定表52.4.未注公差的极限偏差2.4.1冲裁角度未注明公差尺寸的极限偏差按表6规定。
表62.4.2弯曲角度未注明公差尺寸的极限偏差按表7规定表72.5. 成形拉延件允许有局部材料变薄或增厚,变薄后的最小厚度为: t min =75%tt min —材料的的最小厚度,mm t —材料的公称厚度,mm2.6. 冲压件的孔心距、孔边距及孔组距未注公差尺寸的极限偏差。
2.6.1 带料、扁条料等材料冲孔对边缘距离未注公差尺寸的极限偏差按表8规定。
表82.6.2 孔距公差及组孔间距未注公差尺寸的极限偏差按表9规定。
冲压件检验标准
.冲压件检验判定标准一、质量判定基本定义1、某些描述中使用的一些主观评价词汇的定义:轻微的:指容易接受的,感觉不太明显、不太大、力量很小、不太持久的。
明显的:指较突出的、较清晰的、不用置疑的。
显著的:指非常突出的、一定觉察得到的、鲜明突出的、完全清晰可见的。
2、冲压件在整车上分区定义汽车分三个区域:两个外区和一个内区。
A区:汽车的上部至车身腰线,分界线为:车身腰线装饰条或保护条的下边线车身腰线装饰槽下边线车身上开合件边框的有关部位:汽车内2区的某些部位,从外面完全看的见,可根据具体情况视做1区处理B区:坐在司机或乘客座位上,关上车门后能看得见的部位,位于:车身腰线以上所有上车时能看见的部位,车身周边,车身边框以及:后侧窗,后行李箱隔板,尾门内板,车身尾门框,行李箱,发动机舱,发动机罩内表面,天窗窗框,油箱加注孔入口所有坐在司机或乘客座位上,关上车门能看的见的,位于车身腰线以下的部位。
C区:位于车身装饰条或保护条以下的部分、不影响客户直观视觉效果的部位。
3、检验基本条件定义:站立,在缺陷扣分区内,在冲压件四周,离件1米进行检查允许俯身,但不能蹲下检查涉及到间隙及高低不平的缺陷,应予以测量判别。
4、检测:–是靠视觉、触觉……进行评判的.。
–只有在有疑问的情况下,才使用检具,根据间隙标准的定义或有关基本标准的定义来核实或明确某些缺陷的扣分级别:·对间隙及高低不平的检查使用塞尺·对冲压件上的坑包、麻点的检查要使用面积规·对表面检查使用尺子5.缺陷分类–外观类:裂纹,缩颈坑包,起皱麻点变形锈蚀材料缺陷起皱,波纹,棱线毛刺拉毛,划伤圆角叠料压痕其它冲压件判定标准6、尺寸要求:冲压件按其功能分为三类,A类是外表面件,其要求最高,其次是B类,主要是结构件。
最后是C类,例如支架之类。
冲压件放于合格的检具上,特殊要求的尺寸和公差按产品图纸要求,其它按照“冲压件的未注允许公差表”执行。
补充:冲压件的未注允许公差表一般位置精度:(A类件:±0.5,B类件:±1.0,C类件:±1.5)一般孔:中心位置精度: ±0.5直径轮廓:(塞规测量)+0.5, -0.0;(最大值/最小值之间的差值,游标卡尺测量)0.15孔距(孔与孔):±0.5工具孔:直径: +0.2, -0.0 基准到基准: ±0.2阶梯(搭接):深度(高度差): +0.3, -0.0 位置精度:±1.0配合面精度:(B类面:±0.7,C类面:±1.0)翻边宽度: +1.0, -0.5一般曲率半径: ±0.5角度: ±2 度安装孔:直径轮廓(塞规测量):±0.5 孔距(孔与孔,塑料件装配用):±0.5孔距(孔与孔,金属件装配用):±0.3一致性同一批中的五个样品的所有的检点的六个标准值不得超过1.0 毫米。
冲压件检验标准
1 目的对冲压件检验的方法、频次、项目和合格标准作出规定。
2 适用范围本规程适用于所有冲压件的检验。
3 抽样依据3.1 除非有特别说明,抽样依据按《抽样检验计划》规定的要求进行。
3.2 若客户有要求时,则依客户的要求抽样检验。
3.3 其它未列入的项目有必要时参照国家或行业标准执行。
4 检验设备及工具卷尺、卡尺、3M胶带、盐雾试验箱、ROHS测试仪,高度规,塞规6 检验条件6.1所有检验均应在正常照明光源为40W荧光灯(相当于80-120LUX光照),裸眼或矫正视力在1.0以上,并模拟最终使用条件下进行。
检测过程中不使用放大镜,所检验表面和人眼取正常观察角度±45º角内,距离300mm。
A级面在检测时应转动,以获得最大反光效果。
B级面和C级面在检测期间不必转动。
6.2 A级面停留15秒,B级面停留10秒,C级面停留5秒。
6.3抽验水准(AQL):7 检查项目外观检查、结构尺寸检查、材质检查、特定试验(包括盐雾试验、附着力试验等)、包装检查。
8 判定条件8.1所有的机构、功能要求以图面为准,关于机构尺寸公差如图面未直接于尺寸后标注其公差,则本公司孔的尺寸公差以±0.10m m管制,其他尺寸以±0.20m m进行管制,除非客戶有更为严格或特別要求。
QE人員可视需要在SIP制定時缩小其公差,以利于生产管制,如丽辰公司供货商的产品有因SI P缩小公差管制的问题被判拒收,且可证实是丽辰公司事前未有通知厂商時,当批可以尽量吸收的原则协调处理,但供货商必须于下批改善。
8.2产品因为工艺的特性或设计结构的影响,而存在固有外观缺失(如冲压模具痕;电镀白斑、水紋,这类缺失通常以样品为基准進行判定,但其限度样品的建立需充分遵照本准则之要求,当未有建立样品時也可根据本标准進行判定。
8.3本指导准則已有定义而SIP另有规定的则以SIP之规格为准;本准则如与客戶标准有冲突時,以客戶之标准为准。
冲压件外观通用检验规范
冲压件外观通用检验规范
1.目的
制定冲压生产线的一般检验准则,在规格,客户之外观规范及产品范围等没有明确规定时,以此作为检验检验过运作之依据。
2.范围
适用于PCE,ECG的所有冲制作
3.参考文件
3.1ES04-021Compaq铁壳外观规范
3.2记录保存依QS-16
4.特殊规定
4.1本文件若与蓝图及IS,SIP,SOP,PMP客户检验规范发生冲突,以上述规格和蓝图为准。
4.2例外规定放入个别检验规格内。
4.3若个别规格要求超出(低于或松于)此文件,以个别规格为准。
5.检验规定
5.1毛刺的规定:
5.1.1所有冲制件的毛刺高度不得超过板厚的5%,不允许有毛刺的方,必须有压毛边工
序,压完毛边后,不得有刮手的感觉。
5.1.2对于0.15~0.4MM
5.1.3
刺(如图1)
5.1.4在制程中,若发现毛刺手感明显时,就要用于千分尺或投影仪测量,当毛刺高度
大于4%时,就要做好检查记录并要求修模,但已冲零件放行。
5.2平面度的规定:
5.2.1冲件平面不允许有与蓝图不符之最严重翘曲。
09冲压件验收标准
冲压件验收标准1.检验人员:由进料检验员进行检验;2.检验地点:进料待检区和进料检验室;3.检验时机:供应部开出送检单的24小时内;4.抽样方法:按《进料检验员质量控制规范》进行抽样。
5.检验项目:①形位尺寸②外观及表面质量③表面平面度或变形度。
6.检验方法:①用游标卡尺、高度尺:测量冲件的形状尺寸和位置度尺寸、毛刺尺寸大小②用平台、塞尺:测量冲压件的平面度、变形度③肉眼观察:外观及表面质量。
7.验收标准:①尺寸公差必须符合工艺图纸要求(可以使用检具)。
②材料厚度符合相应国家标准的普通精度要求(材料宽度按1500mm档执行),公差精确到小数点后一位,采用进一法。
③未注要求的尺寸公差:按未注尺寸公差查照表-金属零件执行。
④外观无明显拉模、锐口、毛刺、磕碰伤;基材无明显锈蚀、氧化皮、麻坑等;冲压件变形部位不允许有裂纹(不论大小)。
⑤未作要求的平面度和变形:冲压件长度≤100mm:平面度1.0mm;100mm<冲压件长度≤200mm:平面度1.5mm;200mm<冲压件长度≤400mm:平面度3.0mm;400mm<冲压件长度≤800mm:平面度5.0mm;冲压件长度>800mm:平面度8.0mm;使用平台和标准块测量,合格的在记录上打√,不需要记录具体数据.不合格打×.⑥材料表面麻点,每50*50 mm2范围内允许存在2点;冲件变形部位不允许有裂纹(不论大小)。
8.检验记录:检验结果记录在进料检验记录上.判定合格的直接入库,判定不合格的通知供应部退货处理,供应商提供《纠正预防措施报告》,重新送货再报检验员检验合格的方可入库.。