冲压件通用检验规范
常见冲压件检验标准

1 目的对冲压件检验的方法、频次、项目和合格标准作出规定。
2 适用范围本规程适用于所有冲压件的检验。
3 抽样依据3.1 除非有特别说明,抽样依据按《抽样检验计划》规定的要求进行。
3.2 若客户有要求时,则依客户的要求抽样检验。
3.3 其它未列入的项目有必要时参照国家或行业标准执行。
4 检验设备及工具卷尺、卡尺、3M 胶带、盐雾试验箱、ROHS 测试仪,高度规,塞规 面类 外观面定义A 级面 客户经常看到的面。
如面板,机箱的上表面、正面,出给客户的零件等。
B 级面 不移动的情况下,客户偶尔能看到的面,如机箱的后面、侧面、顶部或同等面等。
C 级面 产品在移动或被打开时才能看到的面,如机箱的底面,内部零件的表面等6 检验条件 6.1所有检验均应在正常照明光源为40W 荧光灯(相当于80-120LUX 光照),裸眼或矫正视力在1.0以上,并模拟最终使用条件下进行。
检测过程中不使用放大镜,所检验表面和人眼取正常观察角度±45º角内,距离300mm 。
A 级面在检测时应转动,以获得最大反光效果。
B 级面和C 级面在检测期间不必转动。
6.2 A 级面停留15秒,B 级面停留10秒,C 级面停留5秒。
6.3 抽验水准(AQL):不合格(缺陷)类别 严重 主要 一般 缺陷类别代码A B C AQL1.52.57 检查项目外观检查、结构尺寸检查、材质检查、特定试验(包括盐雾试验、附着力试验等)、包装检查。
8 判定条件8.1所有的机构、功能要求以图面为准,关于机构尺寸公差如图面未直接于尺寸后标注其公差,则本公司孔的尺寸公差以±0.10mm 管制,其他尺寸以±0.20mm 进行管制,除非客戶有更为严格或特別要求。
QE 人員可视需要在SIP 制定時缩小其公差,以利于生产管制,如丽辰公司供货商的产品有因SIP 缩小公差管制的问题被判拒收,且可证实是丽辰公司事前未有通知厂商時,当批可以尽量吸收的原则协调处理,但供货商必须于下批改善。
常见冲压件检验标准
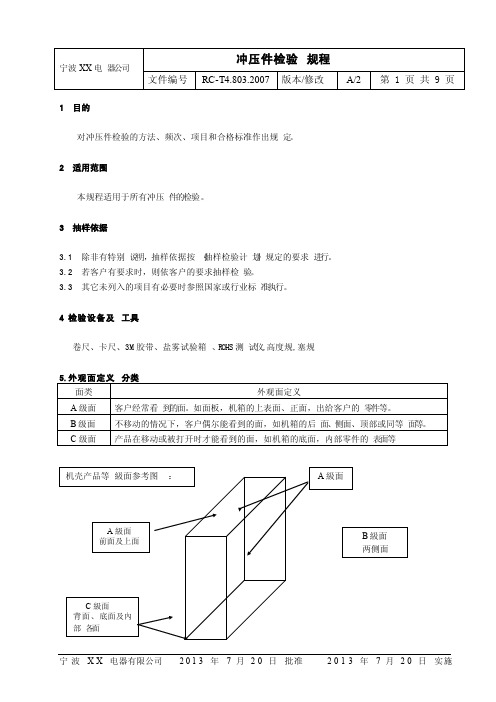
1 目的对冲压件检验的方法、频次、项目和合格标准作出规定。
2 适用范围本规程适用于所有冲压件的检验。
3 抽样依据3.1 除非有特别说明,抽样依据按《抽样检验计划》规定的要求进行。
3.2 若客户有要求时,则依客户的要求抽样检验。
3.3 其它未列入的项目有必要时参照国家或行业标准执行。
4 检验设备及工具卷尺、卡尺、3M胶带、盐雾试验箱、R OHS测试仪,高度规,塞规6 检验条件6.1所有检验均应在正常照明光源为40W荧光灯(相当于80-120LUX光照),裸眼或矫正视力在1.0以上,并模拟最终使用条件下进行。
检测过程中不使用放大镜,所检验表面和人眼取正常观察角度±45º角内,距离300m m。
A级面在检测时应转动,以获得最大反光效果。
B级面和C级面在检测期间不必转动。
6.2 A级面停留15秒,B级面停留10秒,C级面停留5秒。
6.3抽验水准(AQL):7 检查项目外观检查、结构尺寸检查、材质检查、特定试验(包括盐雾试验、附着力试验等)、包装检查。
8 判定条件8.1所有的机构、功能要求以图面为准,关于机构尺寸公差如图面未直接于尺寸后标注其公差,则本公司孔的尺寸公差以±0.10mm管制,其他尺寸以±0.20mm进行管制,除非客戶有更为严格或特別要求。
QE人員可视需要在SIP制定時缩小其公差,以利于生产管制,如丽辰公司供货商的产品有因SIP缩小公差管制的问题被判拒收,且可证实是丽辰公司事前未有通知厂商時,当批可以尽量吸收的原则协调处理,但供货商必须于下批改善。
8.2产品因为工艺的特性或设计结构的影响,而存在固有外观缺失(如冲压模具痕;电镀白斑、水紋,这类缺失通常以样品为基准進行判定,但其限度样品的建立需充分遵照本准则之要求,当未有建立样品時也可根据本标准進行判定。
冲压件检验规范

1. 目的明确钣金冲压生产过程产品检验、测量方法及判定标准,为产品检验提供依据2. 范围本标准适用于公司所有钣金冲压半成品及成品3. 引用文件本规范在应用下列文件时,凡是注明日期的引用文件,仅注明日期的版本适用于本文件,凡是未注明日期的引用文件,仅最新版适用于本文件3.1GB/T 1804 一般未注公差的线性和角度尺寸公差3.2GB/T 13916-2013 冲压件形状和位置未注公差3.3GB/T GB/T 15055-2007 冲压件未注公差尺寸极限偏差4. 检验条件4.1视力要求:裸视或矫正视力1.0以上4.2照明要求:在自然光或60W-100W的日光灯照明条件下检验,距离约50-60cm4.3对于需要主观判断的缺陷,允许用不超过4X的显微镜,超过4X的显微镜可用来辅助分析,但不能用来接收或拒收零件5. 缺陷分类5.1严重缺陷:可能造成产品性能故障及安全隐患的缺陷5.2重要缺陷:可能导致产品的可用性降低的不符合项5.3轻微缺陷:不影响产品正常使用,产品外观、包装及运输防护等其它轻微不符合项6. 检验方法6.1检具测量用钢板尺、卷尺、塞尺、卡尺、高度尺,靠模、功能规、检验工装及测量平台等测量工具,结合工艺图纸对产品的尺寸、位置、形状等部位进行测量6.2目视检验目视检验产品外观无生锈、凹坑、划痕、裂纹、缺料、多料、毛刺等不符合产品质量要求缺陷7. 检验标准7.1尺寸检验判定标准7.1.1产品检验按照图纸公差要求接受检验翻孔不均匀高度尺寸不符合图纸要求7.2外观检验判定标准坑包容易产生应力集中、喷涂后影响产品外观生产运输过程中产生挤压、磕碰、刮擦后留下的痕迹钣金件在折弯成型过程中产生的折痕,折皱现象编制:审核:批准:日期:日期:日期:。
常见冲压件检验标准样本
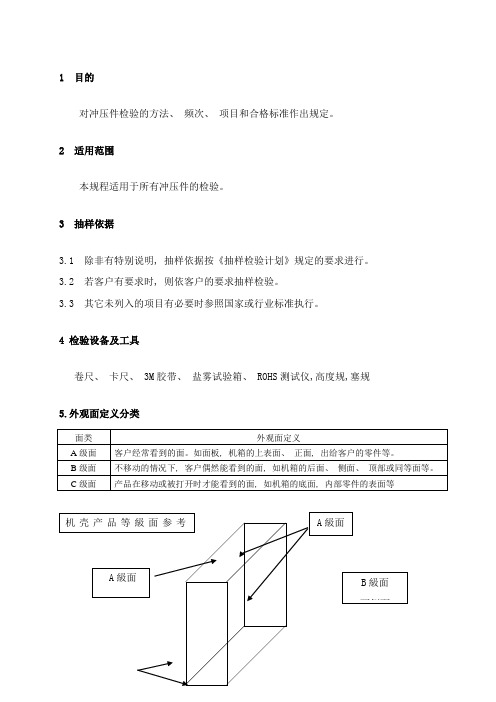
1 目的对冲压件检验的方法、频次、项目和合格标准作出规定。
2 适用范围本规程适用于所有冲压件的检验。
3 抽样依据3.1 除非有特别说明, 抽样依据按《抽样检验计划》规定的要求进行。
3.2 若客户有要求时, 则依客户的要求抽样检验。
3.3 其它未列入的项目有必要时参照国家或行业标准执行。
4 检验设备及工具卷尺、卡尺、 3M胶带、盐雾试验箱、 ROHS测试仪,高度规,塞规5.外观面定义分类C級面背面、底面6 检验条件6.1所有检验均应在正常照明光源为40W荧光灯(相当于80-120LUX光照), 裸眼或矫正视力在1.0以上, 并模拟最终使用条件下进行。
检测过程中不使用放大镜, 所检验表面和人眼取正常观察角度±45º角内, 距离300mm。
A级面在检测时应转动, 以获得最大反光效果。
B级面和C级面在检测期间不必转动。
6.2 A级面停留15秒, B级面停留10秒, C级面停留5秒。
6.3抽验水准(AQL):不合格( 缺陷) 类别严重主要一般缺陷类别代码 A B CAQL 0 1.5 2.57 检查项目外观检查、结构尺寸检查、材质检查、特定试验( 包括盐雾试验、附着力试验等) 、包装检查。
8 判定条件8.1所有的机构、功能要求以图面为准, 关于机构尺寸公差如图面未直接于尺寸后标注其公差, 则本公司孔的尺寸公差以±0.10mm管制, 其它尺寸以±0.20mm进行管制, 除非客戶有更为严格或特別要求。
QE人員可视需要在SIP制定時缩小其公差, 以利于生产管制, 如丽辰公司供货商的产品有因SIP缩小公差管制的问题被判拒收, 且可证实是丽辰公司事前未有通知厂商時, 当批能够尽量吸收的原则协调处理, 但供货商必须于下批改进。
8.2产品因为工艺的特性或设计结构的影响, 而存在固有外观缺失( 如冲压模具痕; 电镀白斑、水紋, 这类缺失一般以样品为基准進行判定, 但其限度样品的建立需充分遵照本准则之要求, 当未有建立样品時也可根据本标准進行判定。
冲压件检验标准.docx

冲压件检验标准.docx冲压件检验判定标准一、量判定基本定1、某些描述中使用的一些主价的定:微的:指容易接受的,感不太明、不太大、力量很小、不太持久的。
明的:指突出的、清晰的、不用置疑的。
著的:指非常突出的、一定察得到的、明突出的、完全清晰可的。
2、冲件在整上分区定汽分三个区域:两个外区和一个内区。
A区:汽的上部至身腰,分界:身腰装条或保条的下身腰装槽下身上开合件框的有关部位:汽内 2 区的某些部位,从外面完全看的,可根据具体情况做 1 区理B区:坐在司机或乘客座位上,关上后能看得的部位,位于:身腰以上所有上能看的部位, 身周 , 身框以及:后窗,后行李箱隔板, 尾内板,身尾框,行李箱, 机,机罩内表面,天窗窗框,油箱加注孔入口所有坐在司机或乘客座位上,关上能看的的,位于身腰以下的部位。
C区:位于身装条或保条以下的部分、不影响客直效果的部位。
3、基本条件定:站立,在缺陷扣分区内,在冲件四周,离件1 米行允俯身,但不能蹲下涉及到隙及高低不平的缺陷,予以量判。
4、 :–是靠、触?? 行判的. 。
–只有在有疑的情况下,才使用具,根据隙准的定或有关基本准的定来核或明确某些缺陷的扣分:· 隙及高低不平的使用塞尺· 冲件上的坑包、麻点的要使用面· 表面使用尺子5.缺陷分–外 :裂 ,坑包,起麻点形材料缺陷起,波,棱毛刺拉毛,划圆角叠料压痕其它冲压件判定标准判定描述一区二区项目三区外部内部外部内部1、封闭裂纹长度≥80mm或宽度≥3mm(料厚≥);宽度≥2mm (料厚≤)2、不报废封闭裂纹长度≥ 50mm;宽度≥ 2mm裂纹长度小于 80mm或宽度小于 3mm(料厚≥);长度≤ 80mm且宽度≤ 2mm(料厚≤)返工安全件减震器////报废缩颈部位厚度 / 料厚≤ 20%且长度≥ 80mm返工缩颈缩颈部位厚度 / 料厚≥ 20%长度≤ 80mm放行放行放行放行放行安全件减震器受力部位缩颈≥料厚的10%////报废面积≥ 8cm2或长度≥ 10cm高度≥ 3mm报废返工报废返工返工222面积4cm ≤S< 8cm 上或长度5cm≤L< 10cm面积≥ 100cm 坑包返工返工返工返工放行或长度≥ 10cm坑包高度≥ 1mm返工返工返工放行放行零件 2/3 面积上能看到麻点或小凸包。
冲压件通用检验标准

文件编号:
版本:A/0
编制:
审批:
检验项目
检验内容
检验方法
检测工具
缺陷程度
严重
主要
次要
开料
用错材料
不允许用错材质和材料厚度
样板、卡尺
√
尺寸规格不良
工件的尺寸、规格是否与图纸、样板一致;
卡尺、样板
√
划伤
轻微划伤,砂房可去掉
目视、触摸
√
伤痕过深,后工序无法去掉。(不接受)
目视、触摸
样板
√
钻眼攻丝
位置
眼位所在位置是否与样板、图纸相一致;
卡尺、样板
√
尺寸
眼位尺寸是否与样板、图纸一致,如刀肉内径是否与图纸要求的尺寸一致;
卡尺、样板
√
内表面
眼位内表面不能有披锋、丝牙是需攻穿整个部件;
不能有滑牙或烂牙现象
目视
√
试装
使用相应的丝公进行试装,判断其是否进出畅顺;对于重要部件必须进行产品试装。
目视、卡尺
√
试装
刀肉的眼位一定要经过试装判断其是否符合产品的质量要求;
试装
√
打字
位置
是否与样板、图纸所在位置相一致;
卡尺
√
内容
是否与样板、图纸内容相一致;
目视
√
质量
字体是否清晰完整、字体的深度是否达到质量要求。
目视、样板
√
指
甲
印纸相一致
卡尺
√
指甲印质量
指甲印内表面是否光滑、深度是否达到客户要求
√
披锋
在砂房或水磨工序是否可以去掉。
目视、测试
√
打眼
冲压车间零件检验规范

冲压车间零件检验规范为提升车间零件质量,规范零件检查流程,防止质量批量问题发生,现对零件检查流程及内容明确如下:一、生产过程三检要求:1.“三检”人员即为操作者检、班长检、检验岗检2.三检要求;(1)班组生产零件3件(含3件)以上的每批次;(2)更换操作者;(3)更改或调整生产设备、工艺装备、技术文件、工艺方法、工艺参数;(4)模具型面、冲头修理;(5)材料牌号更改等。
3.三检内容:从板材投入到出产品的每一道工序都要例行检查,即压印点、开裂、细颈、皱纹、切边、冲孔、整形,查周边及孔毛刺、孔窝、孔数、拉伤、磕碰、变形、棱线、下限等,首件要保留至该批零件全部加工完。
4.尾件:做为下批生产时首件检查的参考件和参照件,自噬体零件加工回去之前都必须存有尾件展开标注,对尾件的检查和首件相同,零件上要标明生产日期,例如存有故障必须准确说明并及时意见反馈给工艺人员精心安排磨具维修。
5.抽检和巡检:检查岗应在做完抽检工作之余对零件逐个检查,班长抽检率不小于百分之一,工长不小于四百分之一,抽检必须对零件进行全面检查并做标记,工、班长应对生产过程进行巡检,包括对装架入库之前的零件进行外观检查.各相关人员具体工作:1.首尾件三检2.抽检,隔四百件全面抽检一次3.县丞,外木四百件县丞一次1.首尾件三检2.抽查,外木一百件全面抽查一次3.巡检,隔一百件对每序零件巡检一次1.首尾件三检2.抽检,逐件检查,并且隔五十件全面抽检一次3.县丞,至少每半个小时对每序零件县丞一次4.在换料、修模、修设备等停线后再生产的第一件需进行全面检查1.抽查,外木两个小时全面抽查一次2.巡检,隔两个小时对每序零件巡检一次二.定检建议:1.在一下情况均需进行上检具检查确认:(1)更改或调整生产设备、工艺装备、技术文件、工艺方法、工艺参数;(2)模具型面、冲头修理;(3)材料牌号更改等。
2.定检内容:对照零件静态检查表,对零件面差、阶差、孔位进行检查,并作好记录。
冲压及其产品检验规范
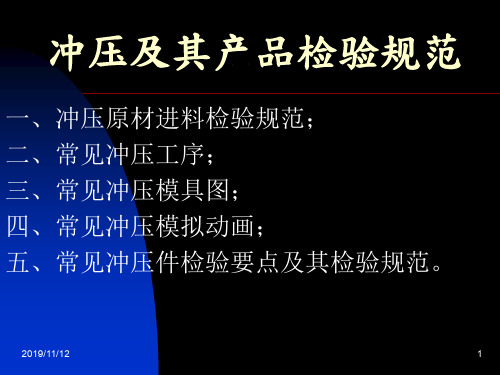
2019/11/12
折弯角度一般采用角度规进行测量保证其在标准范围内bk1v101折弯角度90但对对称折弯也可以用卡尺测量其底端和顶端如bk1v101折弯间距908若二者尺寸相差过大如超过01mm则角度偏差
冲压及其产品检验规范
一、冲压原材进料检验规范; 二、常见冲压工序; 三、常见冲压模具图; 四、常见冲压模拟动画; 五、常见冲压件检验要点及其检验规范。
量之折弯高度 (5)孔间距:
孔间距以及其他图示重点尺寸按SIP要求进行管控 。
3、其他注意事项
(1)折弯开裂:一般不允许折弯处有开裂之不良; (2)印字:印字清晰、端正、正确; (3)抽芽:抽芽口不可崩裂,牙口需加倒角; (4)平面度:不可超过标准; (5)注意有无漏工程、有无漏冲孔。
2019/11/12
2019/11/12
1
一、冲压原材进料检验规范
外观
(1)凹凸痕: 产品表面无凸出之不良; 对于凹痕, 正视面不允许,背面允许3点L≤2.5MM,W≤1MM
且正面目视不可有明显亮斑.
(2)刮伤: 不可有刮手之刮伤 ;正视面 L≤20mm;W≤0.3mm一条,背面允许L≤30mm ; W≤0.5mm间隔五条 .
6
脏污
2019/11/12
7
尺寸
(1)长度:用卷尺测量,一般要求公差不超过±0.50mm;
(2)宽度:用卷尺或卡尺测量,一般要求公差不超过 ±0.30mm; (3)厚度:用千分尺进行测量,一般要求公差不超过 ±0.03mm。
- 1、下载文档前请自行甄别文档内容的完整性,平台不提供额外的编辑、内容补充、找答案等附加服务。
- 2、"仅部分预览"的文档,不可在线预览部分如存在完整性等问题,可反馈申请退款(可完整预览的文档不适用该条件!)。
- 3、如文档侵犯您的权益,请联系客服反馈,我们会尽快为您处理(人工客服工作时间:9:00-18:30)。
1.目的:
制定试模样品的一般检验准则,在规格、客户之外观规范及产品蓝图等没有明确规定时,以此作为检验之依据。
2.范围:
适用于本厂所有冲压件。
3.特殊规定:
3.1本文件若与蓝图及客户检验规范发生冲突,以蓝图和客户要求为准。
4.检验规定:
4.1毛刺的规定:
4.1.1所有冲制件的毛刺高度不得超过板厚的5%,不允许有毛刺的地方,必须有压毛边工
站,压完毛边后,不得有刮手的感觉。
4.1.2对于0.15~0.4MM
4.1.3
4.2平面度的规定:
4.2.1
4.2.2
量。
4.2.3
4.3由于冲孔引起的凸起。
在冲孔边缘会引起突起或凹陷,当超过尺寸界限时拒收。
生变形。
4.7紧固件
4.7.1紧固件须与基材紧密相连,符合安装程序及制程中尺寸。
4.7.2紧固件在安装中不能变形或挤压变形。
4.7.3基材安装中不能变形或凸出。
4.8螺柱(standoff) 、螺母(nut) 、螺钉(screw)压合的规定:
4.8.1所有的螺柱、螺母、螺钉与冲压件母面压合时,必须压牢,不得压偏,螺母(nut)压合
后不得与母面有间隙存在。
螺柱(standoff) 、螺钉(screw)不允许高出母面。
4.8.2螺柱或螺母与冲压件母面的结合力必须符合客户规格或蓝图要求,并作推力、扭力、
拉力测试。
4.8.3螺母(nut) 、螺柱(standoff) 、螺钉(screw),进料时除按规定对尺寸,外观检查外,还
应对其硬度进行测试,硬度依据蓝图或规格。
4.8.4螺柱(standoff)、螺母(nut)与冲件基体压合后,必须用牙规检验,检验数与频率依
个别SPEC之要求。
4.9
4.10字模:
4.10.1字模清晰完整,距离460mm目视可识别清楚。
压印之每一个单个字体深度一致,
深度差距在0.1mm。
有疑议时送检测剖开测量。
4.10.2不允许缺齿,缺角。
4.10.3版次与蓝图及ECN版次一致。
4.10.4字模在零件中的位置及方向必须与图面一致。
4.10.5字模面之背部不能有凹陷及凸出手感,弹片例外。
4.10.6字模中每一个单个字体所使用之字型格式一样。
4.10.7上盖商标的压字深度必须在0.4±0.1mm。
4.11色拉孔:
所有的色拉孔,不允许偏位,要有倒角,其深度H要在规格之内。
如图所示(图6),若有怀疑时,需用实物实配。
4.12铆接:
4.12.1不允许漏铆。
4.12.24.12.34.12.44.12.5铆接面±2°扳动后仍不松动,铆接部位无间隙存在. 。
4.13断差:连续模生产,过桥冲断时,断差不应超过0.2mm ,且通过客户TVR 及FAI 之要求则
允收。
4.22弯曲,拉深时零件表面不允许拉伤,破坏锌层。
4.23不允许有铁屑存在于冲件的任何部位。
4.24不允许漏冲孔。