压力管道焊接技术
压力管道的焊接工艺及检验

压力管道的焊接工艺及检验1、焊接施工程序2、焊接准备⑴ 对焊工和无损检测人员的要求 ① 对焊工的要求:A 、凡参加钢管焊接的焊工,必须持有有效合格证书。
B 、焊接方法和焊接位置等均应与焊工本人考试合格的项目相符。
工中断焊接工作6个月以上者,应重新进行考试。
② 对无损检测人员的要求:无损检测人员应经过专业培训,通过考试取得无损检测资格证书。
⑵ 对焊接环境的要求焊接环境出现下列情况时,采取有效的防护措施:① 风速:气体保护焊大于2m /s ,手工电弧焊大于8m /s 。
② 相对湿度大于90% ③ 环境温度低于-5℃。
④ 雨天和雪天的露天施焊。
⑶ 焊接材料预处理① 焊条放置于通风、干燥和室温不低于5℃的专设库房内,并及时作好实测温度、焊条烘焙记录和焊条发放记录。
烘焙温度和时间严格按厂家说明书的规定进行。
烘焙后的焊条保存在100~150℃的恒温箱内。
② 场使用的焊条装入保温筒,随用随取。
焊条在保温筒内的时间不超过4h ,超过后重新烘焙,重复烘焙的次数不宜超过2次。
③ 丝在使用前清除铁锈和油污。
④ 焊接气体保证具有足够的纯度二氧化碳气体纯度不低于99.5%。
⑷ 焊接工艺规程编制 ① 焊缝分类一类焊缝:钢管管壁纵缝、明管环缝、凑合节合拢环缝;二类焊缝:管壁环缝,加劲环、阻水环的对接焊缝和阻水环角焊缝。
三类焊缝:不属于一、二类的其他焊缝。
②焊接工艺评定600kg级钢板我局在多个电站使用,具有现成的焊接工艺评定和成熟的焊接水平,因此采用现有的焊接工艺评定,并在现场按照经监理人批准的焊接程序和工艺,通过生产性焊接试验加以修定并完善制造订出用于工程实际的焊接规范。
试板与实际使用的焊件相同,试验在监理监督下进行。
③编制焊接工艺规程钢管施焊前,根据已批准的焊接工艺评定(PQR)报告,结合本工程的实际情况,编制压力钢管焊接工艺规程(WPS)。
3、生产性焊接工艺⑴焊接方法焊接包含环缝的焊接、纵缝的焊接、加劲环的焊接、灌浆孔的补强板的焊接,其他附件的焊接。
压力管道焊接施工工艺及质量检测

压力管道焊接施工工艺及质量检测一、引言压力管道焊接施工工艺及质量检测是确保工程质量和施工安全的重要环节。
本文将从工艺流程、施工规范、质量检测等方面进行详细讨论,以帮助读者更好地了解压力管道焊接施工工艺及质量检测的相关知识。
二、压力管道焊接工艺1. 工艺准备在开始压力管道的焊接施工前,首先需要准备相关的工艺文件,包括焊接工艺规程、工艺指导书等。
同时需要对焊接设备和工具进行检查和校准,确保其正常和可靠。
2. 材料准备对于压力管道焊接施工,材料选择和准备非常重要。
需要根据设计要求选择符合标准的管材和焊材,并进行库存管理,防止材料出现质量问题或者误用。
3. 焊接工艺焊接工艺是决定焊接质量的关键因素之一。
在进行焊接前,需要根据设计要求和材料性质选择适当的焊接工艺。
常见的焊接方法包括手工电弧焊、气体保护焊、埋弧焊等。
在焊接过程中,需要控制焊接参数,如电流、电压、焊接速度等,以确保焊缝的质量。
三、施工规范1. 操作规程在压力管道焊接施工中,必须按照相关的操作规程进行施工。
操作规程包括焊接操作、检查与试验、防火与防护等内容。
施工人员必须熟悉并遵守这些操作规程,以减少事故发生的风险。
2. 焊接工艺评定在压力管道焊接施工前,必须进行焊接工艺评定。
评定焊接工艺的目的是确定所选用的焊接方法和焊接参数是否能够满足设计和规范要求。
通过对样板的焊接试验和性能检测,评定焊缝质量和焊接工艺的合格性。
3. 检验与试验施工过程中应进行必要的检验与试验,以确保焊接质量符合要求。
检验包括焊缝外观检查、尺寸检查、焊缝的无损检测等;试验包括压力试验、泄漏试验等。
其中,焊缝的无损检测是重要的一项质量检测手段,常用的方法有超声波检测、射线检测等。
四、质量检测压力管道焊接质量检测是确保工程质量的重要环节。
以下是一些常用的质量检测方法:1. 脉冲电流检测脉冲电流检测是一种用于检测焊接缺陷的无损检测方法。
通过施加脉冲电流并观察检测信号的变化,可以准确定位和评估焊接缺陷,如裂纹、孔洞等。
压力管道焊接技术与质量控制
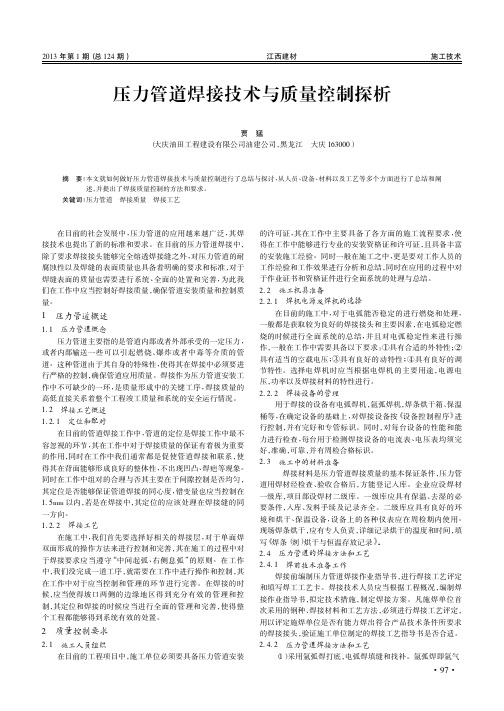
压力管道焊接技术与质量控制探析贾猛(大庆油田工程建设有限公司油建公司,黑龙江大庆163000)摘要:本文就如何做好压力管道焊接技术与质量控制进行了总结与探讨,从人员、设备、材料以及工艺等多个方面进行了总结和阐述,并提出了焊接质量控制的方法和要求。
关键词:压力管道焊接质量焊接工艺在目前的社会发展中,压力管道的应用越来越广泛,其焊接技术也提出了新的标准和要求。
在目前的压力管道焊接中,除了要求焊接接头能够完全熔透焊接缝之外,对压力管道的耐腐蚀性以及焊缝的表面质量也具备着明确的要求和标准,对于焊缝表面的质量也需要进行系统、全面的处置和完善,为此我们在工作中应当控制好焊接质量,确保管道安装质量和控制质量。
1压力管道概述1.1压力管道概念压力管道主要指的是管道内部或者外部承受的一定压力,或者内部输送一些可以引起燃烧、爆炸或者中毒等介质的管道。
这种管道由于其自身的特殊性,使得其在焊接中必须要进行严格的控制,确保管道应用质量。
焊接作为压力管道安装工作中不可缺少的一环,是质量形成中的关键工序,焊接质量的高低直接关系着整个工程竣工质量和系统的安全运行情况。
1.2焊接工艺概述1.2.1定位和配对在目前的管道焊接工作中,管道的定位是焊接工作中最不容忽视的环节,其在工作中对于焊接质量的保证有着极为重要的作用,同时在工作中我们通常都是促使管道焊接和联系,使得其在背面能够形成良好的整体性,不出现凹凸、焊疤等现象。
同时在工作中组对的合理与否其主要在于间隙控制是否均匀,其定位是否能够保证管道焊接的同心度,错变量也应当控制在1.5mm以内,若是在焊接中,其定位的应该处理在焊接缝的同一方向。
1.2.2焊接工艺在施工中,我们首先要选择好相关的焊接层,对于单面焊双面形成的操作方法来进行控制和完善,其在施工的过程中对于焊接要求应当遵守“中间起弧、右侧息弧”的原则。
在工作中,我们没完成一道工序,就需要在工作中进行操作和控制,其在工作中对于应当控制和管理的环节进行完善。
压力容器压力管道焊接知识

精品课件
49
精品课件
50
精品课件
51
精品课件
52
精品课件
53
2.3 焊接裂纹
裂纹是焊接结构中比较普遍而又十分严重的 一种缺陷。严重的裂纹明显地削弱容器的承 载能力和耐腐蚀性能。即使开始不很严重的 裂纹,由于在裂纹尖端处存在应力集中,低 温、交变或冲击载荷的作用会使裂纹扩展, 从而有造成突然脆断的可能。由于裂纹而造 成的事故在国内、外都为数不少。
埋弧自动焊的缺点是占地面积较大,设备费用较高,且仅适用于平焊 位置的焊接。
精品课件
20
埋弧自动焊特别适用于厚度10mm以上 受压壳体纵、环缝的焊接。既可焊接 碳钢,也可焊接低合金钢、耐热钢和 不锈钢等。
精品课件
21
精品课件
22
精品课件
23
精品课件
24
精品课件
25
精品课件
26
精品课件
44
精品课件
45
外部缺陷有表面裂纹、表面气孔、咬边、凹 陷、满溢、焊瘤、弧坑等,这些缺陷主要与 焊接工艺和操作技术水平有关。还有些是外 观形状和尺寸不合要求的外部缺陷,如错边、 角变形和余高过高等。
精品课件
46
内部缺陷有气孔、夹渣、裂纹、未焊 透、未熔合等。
精品课件
47
2.2 焊接缺陷的危害
精品课件
54
焊接裂纹可能产生在焊缝区,也可能产生在 热影响区或熔合处;有时出现纵向裂纹,有 时出现横向裂纹;在断弧处还会出现火口裂 纹亦称弧坑裂纹。从形成裂纹的本质来看, 大体上可分为热裂纹和冷裂纹两大类。
精品课件
55
精品课件
56
精品课件
57
精品课件
压力管道焊接技术与质量控制

89智能管廊冒N0.122020智能城市INTELLIGENT CITY 压力管道焊接技术与质量控制马军林(宁夏青龙管业集团股份有限公司,宁夏青铜峡751600)摘要:在社会经济全面快速发展的今天,压力管道的应用范围越来越广,压力管道的质量标准也越来越高。
在压力管道使用过程中,焊接是非常重要的工序。
为更好地发挥压力管道的作用,应该采用科学有效的焊接技术,同时做好全方位的质量控制工作,以更好地提升压力管道的使用质量以及使用可靠性。
关键词:压力管道;焊接技术;质量控制在社会实践中,压力管道的应用范围不断扩大。
在压力管道的正常使用过程中,需要采用科学的焊接工艺以及焊接技术,保障压力管道整体的密封性,同时更需要做好压力管道防腐蚀性的防治以及处理等工作,只有这样才能够更好地提升压力管道的使用质量。
同时,在压力管道使用中,焊接面是相对薄弱的区域。
为综合提升压力管道的使用长效,必须采用科学的焊接技术,运用规范的焊接工艺,以更好地提升它的焊接标准。
1压力管道焊接技术在压力管道的使用过程中,必须依托于科学的焊接技术,才能够更好地提升压力管道的使用质量和压力管道的应用成效。
在压力管道的使用过程中,应该结合实际需要,科学选择压力管道焊接际1.1定位与组对工作压力管道的焊接是一项非常系统且非常复杂的工程,应力管道的焊接前,应该阙科学的准备工作,充更好换升焊融度。
在正式焊接前,要为焊接工作选取合适的接头,从根本上保证间隙、坡口形式与钝边大小之间的规格匹配,依托这一科学的形式,能够在很大程度上保障焊接质量。
在压力管道的焊接过程中,要做好精准的定位以及组对工作,在这项工作开展过程中要严格管理它的缝隙,避免缝隙过大影响焊接质量,同时也要规避接口组对中可能存在的问题,从源头上做好焊接准备工作。
1.2填充工作压力管道内的压力非常大,所以对于焊接面的要求也非常高。
为更好地提升压力管道的焊接质量,全方位优化压力管道的焊接工艺,应该做好科学全面的清理以及填充作业。
压力管道的定义和管道焊接技术标准
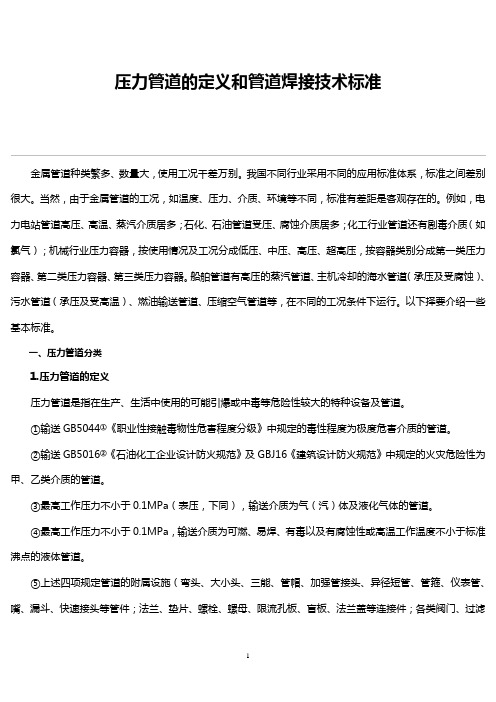
压力管道的定义和管道焊接技术标准金属管道种类繁多、数量大,使用工况千差万别。
我国不同行业采用不同的应用标准体系,标准之间差别很大。
当然,由于金属管道的工况,如温度、压力、介质、环境等不同,标准有差距是客观存在的。
例如,电力电站管道高压、高温、蒸汽介质居多;石化、石油管道受压、腐蚀介质居多;化工行业管道还有剧毒介质(如氯气);机械行业压力容器,按使用情况及工况分成低压、中压、高压、超高压,按容器类别分成第一类压力容器、第二类压力容器、第三类压力容器。
船舶管道有高压的蒸汽管道、主机冷却的海水管道(承压及受腐蚀)、污水管道(承压及受高温)、燃油输送管道、压缩空气管道等,在不同的工况条件下运行。
以下择要介绍一些基本标准。
一、压力管道分类1.压力管道的定义压力管道是指在生产、生活中使用的可能引爆或中毒等危险性较大的特种设备及管道。
①输送GB5044①《职业性接触毒物性危害程度分级》中规定的毒性程度为极度危害介质的管道。
②输送GB5016②《石油化工企业设计防火规范》及GBJ16《建筑设计防火规范》中规定的火灾危险性为甲、乙类介质的管道。
③最高工作压力不小于0.1MPa(表压,下同),输送介质为气(汽)体及液化气体的管道。
④最高工作压力不小于0.1MPa,输送介质为可燃、易焊、有毒以及有腐蚀性或高温工作温度不小于标准沸点的液体管道。
⑤上述四项规定管道的附属设施(弯头、大小头、三能、管帽、加强管接头、异径短管、管箍、仪表管、嘴、漏斗、快速接头等管件;法兰、垫片、螺栓、螺母、限流孔板、盲板、法兰盖等连接件;各类阀门、过滤器、流水器、视镜等管道设备,还包括管道支架以及安装在压力管道上的其他设施)。
①GB5044分为四级(与99容规相同):极度危害(1级)<0.1mg/m3;高度危害(2级)0.1~1mg/m3;中度危害(3级)1.0~10mg/m3;轻度危害(4级)>10mg/m3。
②GB5016标准对可燃气体火灾危险性分甲、乙两类,甲类气体为可燃气体与空气混合物的爆炸下限不大于10%(体积),乙类气体为可燃气体与空气混合物的爆炸下限不小于10%(体积)。
《压力管道焊接》课件
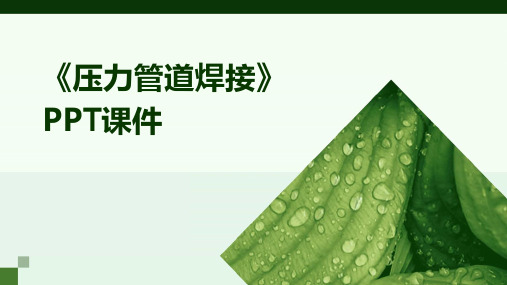
定期对焊接设备进行 检查和维护,确保其 处于良好状态。
在焊接过程中,严格 控制焊接电流、电弧 电压、焊接速度等工 艺参数。
焊接缺陷的识别与控制
常见的焊接缺陷包括未熔合、未焊透、夹渣、气孔等。
在焊接过程中,应通过观察、检测和无损检测等方法,及时发现并处理焊接缺陷。
对焊接缺陷进行分类和记录,分析原因并采取相应的措施,以避免类似缺陷的再次 出现。
01
焊接废弃物的分类
根据废弃物的性质和成分,将其 分为可回收利用和不可回收利用 两类。
02
可回收利用废弃物 的处理
对可回收利用的废弃物进行清洗 、整理后,交给专业的回收公司 进行回收再利用。
03
不可回收利用废弃 物的处理
对不可回收利用的废弃物进行无 害化处理,如填埋、焚烧等,以 避免对环境造成污染。
01
02
03
04
材料准备
确保所有使用的管材、焊材和 保护气体等符合标准要求,并
经过质量检验。
设备检查
对焊接设备进行全面检查,确 保其处于良好工作状态,特别 是焊机、焊枪、送丝机构等。
环境要求
确保焊接环境符合工艺要求, 如温度、湿度、清洁度等。
焊工技能
焊工应具备相应的技能和资质 ,并熟悉焊接工艺规程。
02 03
焊接工艺
快速焊接,减小热影响区,控制变形
实例分析
该燃气公司的压力管道焊接要求高, 涉及高压气体,需严格控制焊接质量 和安全。
05
04
焊接质量检测
无损检测和气密性试验
THANK YOU
感谢观看
焊接过程
坡口制备
根据工艺要求,对管材进行坡口制备,确保坡口 质量。
焊接参数选择
压力管道焊接作业指导书
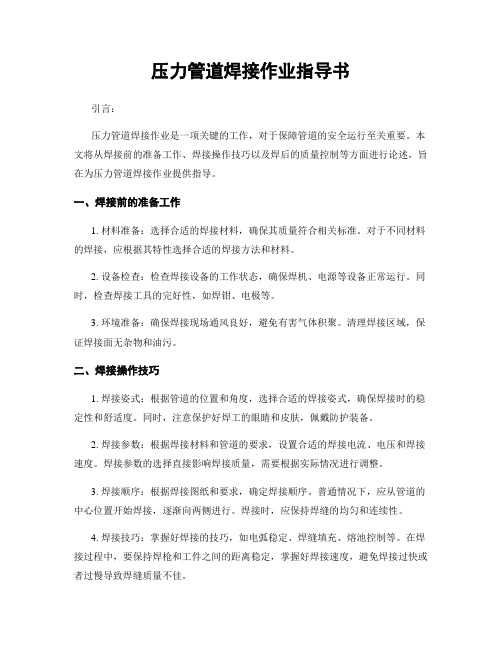
压力管道焊接作业指导书引言:压力管道焊接作业是一项关键的工作,对于保障管道的安全运行至关重要。
本文将从焊接前的准备工作、焊接操作技巧以及焊后的质量控制等方面进行论述,旨在为压力管道焊接作业提供指导。
一、焊接前的准备工作1. 材料准备:选择合适的焊接材料,确保其质量符合相关标准。
对于不同材料的焊接,应根据其特性选择合适的焊接方法和材料。
2. 设备检查:检查焊接设备的工作状态,确保焊机、电源等设备正常运行。
同时,检查焊接工具的完好性,如焊钳、电极等。
3. 环境准备:确保焊接现场通风良好,避免有害气体积聚。
清理焊接区域,保证焊接面无杂物和油污。
二、焊接操作技巧1. 焊接姿式:根据管道的位置和角度,选择合适的焊接姿式,确保焊接时的稳定性和舒适度。
同时,注意保护好焊工的眼睛和皮肤,佩戴防护装备。
2. 焊接参数:根据焊接材料和管道的要求,设置合适的焊接电流、电压和焊接速度。
焊接参数的选择直接影响焊接质量,需要根据实际情况进行调整。
3. 焊接顺序:根据焊接图纸和要求,确定焊接顺序。
普通情况下,应从管道的中心位置开始焊接,逐渐向两侧进行。
焊接时,应保持焊缝的均匀和连续性。
4. 焊接技巧:掌握好焊接的技巧,如电弧稳定、焊缝填充、熔池控制等。
在焊接过程中,要保持焊枪和工件之间的距离稳定,掌握好焊接速度,避免焊接过快或者过慢导致焊缝质量不佳。
三、焊后的质量控制1. 焊缝检查:焊接完成后,应对焊缝进行检查。
通过目测、放射性检测、超声波检测等方法,确保焊缝的质量符合相关标准。
如发现焊缝有裂纹、气孔、夹渣等缺陷,应及时进行修复。
2. 强度测试:对焊接后的管道进行强度测试,确保其能够承受设计压力。
常用的测试方法包括水压试验、气密性测试等。
3. 防腐处理:对焊接后的管道进行防腐处理,延长其使用寿命。
根据管道的材质和使用环境,选择合适的防腐方法,如涂覆、喷涂等。
结语:压力管道焊接作业是一项复杂而重要的工作,需要焊工具备一定的技术和经验。
- 1、下载文档前请自行甄别文档内容的完整性,平台不提供额外的编辑、内容补充、找答案等附加服务。
- 2、"仅部分预览"的文档,不可在线预览部分如存在完整性等问题,可反馈申请退款(可完整预览的文档不适用该条件!)。
- 3、如文档侵犯您的权益,请联系客服反馈,我们会尽快为您处理(人工客服工作时间:9:00-18:30)。
1.3 我国已经建成和将要建设的管道工 程
1865年在美国宾夕法尼亚州建立了第一条输油管道,直径 50mm,全长9km ,材质是丝扣连接的铸铁管。 1874 年该州 又建立了一条直径 100mm ,长度 96km 的管道,开始了与铁 路的竞争。 在第一次世界大战前,机械接头也由焊接取代。第二次世 界大战期间,美国政府资助建立了一条直径 630mm,全长 2240km的成品油管道。 美国 1977 年建成投产的横贯阿拉斯加的原油管道,全长 1276.8km,管径1220mm,是世界上第一条进入北极地区的 原油管道,其中615km采用高架铺设。
1983 年投产的沙特阿拉伯的东西原油管道,引起各 国注意。这条管道自东向西横贯沙特阿拉伯中部地 区,全长 1202km,管径 1220mm ,穿越了浩瀚的沙漠 地区。 随着英国北海油田的开发,兴建了一批海洋原油管 道,总长度达4000余公里,在深100多米的海底铺设。 这些管道的成功建设,标志着管道已可以通过极为 复杂的地质、地理条件与气候恶劣的地区。
低合金高强钢(HSLA) 自60年代开始,随着输油、气管道输送压力和 管径的增大,开始采用低合金高强钢(HSLA),主 要以热轧及正火状态供货。这类钢的化学成分: C≤0.2%,合金元素≤3~5%。
API 5L X56、X60、X65微合金控轧钢 随着管线钢的进一步发展,到60年代末70年 代初,美国石油组织在API 5LX和API 5LS标准中 提出了微合金控轧钢X56、X60、X65三种钢,屈服 强度提高到392~457MPa。这种钢突破了传统钢的 观念,碳含量为0.1-0.14%,在钢中加入≤0.2%的 Nb、V、Ti等合金元素,并通过控轧工艺使钢的力 学性能得到显著改善。
钢材的力学性能 管线钢的发展历史 管线钢组织分类 相关标准中钢号的含义 管道工业的发展方向 焊管的生产 西气东输工程用钢管情况 压力管道用其它钢管
钢材在一定的温度条件和外力作用下抵抗 变形和断裂的能力,称为力学性能。 常规力学性能,如强度、塑性、硬度和韧性等。 高温性能,如抗蠕变性能、持久强度、瞬时强 度和热疲劳性等。 低温性能,如低温冲击韧性、脆性转变温度等。
多元微合金化控轧控冷钢 到1973年和1985年,API标准又相继增加了X70 (屈服强度达482MPa)和X80钢,而后又开发了 X100管线钢,碳含量降到0.01-0.04%,碳当量相 应地降到0.35以下,屈服强度达551.2~689MPa, 真正出现了现代意义上的多元微合金化控轧控冷 钢。
解放后铺设的第一条输气管道,是 1958 年建成的四 川省永川黄瓜山气田至永川化工厂的原料天然气管 道,全长 20km ,管径 159mm 。随着四川天然气工业 的迅速发展,从 1963 年至 1984 年陆续建设形成了四 川地区输气干、支线延展总长度达3525km,可与 54 个气田相连接,承担着向川、滇、黔 3 省 13 个地区 600多个用户的供气任务。 70年代后,随着油田天然气的开发,大庆、辽河、 华北、胜利、大港、中原等油田,都相应建成了一 批向城市供气的长距离输气管道。
西气东输工程,近3900公里。
涩宁兰输气管道工程,全长950公里。
忠县至武汉输气管道工程,全长760公里。 邯郸至石家庄至涿州输气管道工程,全长 362公里。 陕京输气工程复线,全长近900公里 济宁联络线,全长1000多公里
2.1 2.2 2.3 2.4 2.5 2.6 2.7 2.8
1、国内外压力管道的发展过程 2、压力管道用钢及制管 3、压力管道焊接施工 4、焊接应力和变形 5、焊接工艺评定 6、焊接质量控制 7、管道的在线焊接及修复
与公路、水道、铁路以及航空运输相比,管道运输成
本最低。 系统化 网络化
人类离不开管道
人体内的管道和容器、生活、交流
1.1 国外压力管道的发展历史 1.2 我国早期的输油管道和输气管道
铁素体—珠光体钢:基本成分是C-Mn,采用热轧 正火生产工艺。 少珠光体钢:基本成分是Mn-Nb、Mn-V、Mn-Nb-V 等。为微合金控轧钢,通过晶粒细化和Nb、V第二 相的沉淀强化可获得较好的强韧配合。 针状铁素体钢:典型成分为C-Mn-Nb-Mo。通过微 合金化和控制轧制,综合利用晶粒细化、微合金 化元素的析出相和位错亚结构的强化效应来提高 屈服强度和冲击韧性。
屈服强度:σs 抗拉强度:σb
N/mm2或KN/mm2 N/mm2或KN/mm2
延伸率:δ5或δ10
断面收缩率:φ % 硬度:HB HR J
%
HV HL
冲击韧性:ak
C、Mn、Si型普通碳素钢 早期的管线钢一直采用C、Mn、Si型的普通碳素 钢,在冶金上侧重于性能,对化学成分没有严格的 规定,钢的屈服强度一般为295~360MPa。
我国的第一条长输管道是 1957 年建设的克拉玛依到 独山子的输油管道,管径150mm,全长147km。 1965 年胜利油田开始建设由东营至辛店炼油厂的输 油管道,管径 426mm ,全长约 80km ,是我国第一次 在盐碱腐蚀地带建设的原油管道。 1970 年 8 月 3 日,国家批准在东北地区兴建著名的 “八三管道工程”,干线全长593km,管径720mm。
原苏联 1964 年建设的第一条“友谊”输油管道,第 一次采用 1020mm 管径的钢管,全长 5500km 。 1977 年 又修建了第二条“友谊”输油管道,全长 4412km , 管径1220mm。
1983年乌连戈伊-波马雷-乌连戈罗德干线投入使用, 这条管道第一次把苏联的天然气送到了西欧。该管 道长达 4450km ,直径 1420mm ,工作压力 7.5MPa 。经 过水域、河流、森林、永冻土区,施工难度,管径, 里程,泵站数量,输量均堪称世界之最。这条管道 充分显示了原苏联在管道设计和建造方面的实力。 在西伯利亚、北极区的管道铺设得益于闪光对焊技 术的应用。