数控机床的切削用量.pptx
数控课件——切削用量的概念

刀具的磨损原因
❖ (1)硬质点磨损 ❖ (2)粘结磨损 ❖ (3)扩散磨损 ❖ (4)氧化磨损 ❖ (5)相变磨损
►在低温区,一般以硬质点磨损为主;在高温 区以粘结磨损、扩散磨损、氧化磨损、相变 磨损为主。
工件材料的机械、物理性能对可 切削性的影响
► ①硬度:工件材料的高温硬度高时,刀具材料与工件材料的硬度比下降, 可切削性很低,切削高温合金即属此种情况。材料加工硬化倾向大,可 切削性也差。工件材料中含硬质点(如Si02,A1203等)时,对刀具的擦伤 性大,可切削性降低。
► 精加工时(表面粗糙度Ra1.6~0.8μm), 背吃刀量为0.1~0.4㎜。
►(2)进给量的选择
►粗加工时,进给量主要考虑工艺系统 所能承受的最大进给量。
►精加工和半精加工时,最大进给量主 要考虑加工精度和表面粗糙度。另外 还要考虑工件材料,刀尖圆弧半径、 切削速度等。
数控机床切削用量选择还应注意的问
切削用量的概念
►切削用量的概念:
切削加工过程中切削速度(υ ) 、进给量 ( f )和背吃刀量( ap )的总称。
►1. 切削用量的选择原则和方法 合理的切削用量概念:是指充分利用机床和
刀具的性能,并在保证加工质量的前提下, 获得高的生产率与低加工成本的切削用量。
在不考虑辅助工时情况下,有生产率公式P = Ao υ f ap
►分析:(P57)
►在刀具耐用度一定,从提高生产率角度考虑, 对于切削用量的选择有一个总的原则:首先 选择尽量大的背吃刀量,其次选择最大的进 给量,最后是切削速度。当然,切削用量的 选择还要考虑各种因素,最后才能得出一种 比较合理的最终方案。
数控机床切削用量选择
►自动换刀数控机床主轴或装刀所费时间较多, 所以选择切削用量要保证刀具加工完一个零 件,或保证刀具耐用度不低于一个工作班, 最少不低于半个工作班。
数控机床加工的切削用量
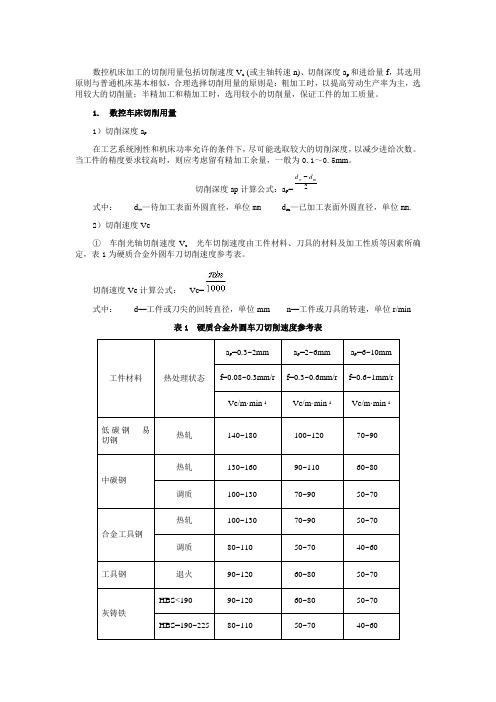
数控机床加工的切削用量包括切削速度V c (或主轴转速n)、切削深度a p 和进给量f ,其选用原则与普通机床基本相似,合理选择切削用量的原则是:粗加工时,以提高劳动生产率为主,选用较大的切削量;半精加工和精加工时,选用较小的切削量,保证工件的加工质量。
1. 数控车床切削用量 1)切削深度a p在工艺系统刚性和机床功率允许的条件下,尽可能选取较大的切削深度,以减少进给次数。
当工件的精度要求较高时,则应考虑留有精加工余量,一般为0.1~0.5mm 。
切削深度ap计算公式:a p =式中: d w —待加工表面外圆直径,单位mm d m —已加工表面外圆直径,单位mm. 2)切削速度Vc① 车削光轴切削速度V c 光车切削速度由工件材料、刀具的材料及加工性质等因素所确定,表1为硬质合金外圆车刀切削速度参考表。
切削速度Vc 计算公式: Vc=式中: d —工件或刀尖的回转直径,单位mm n —工件或刀具的转速,单位r/min表1 硬质合金外圆车刀切削速度参考表2mw d d注:表中刀具材料切削钢及灰铸铁时耐用度约为60min。
②车削螺纹主轴转速n切削螺纹时,车床的主轴转速受加工工件的螺距(或导程)大小、驱动电动机升降特性及螺纹插补运算速度等多种因素影响,因此对于不同的数控系统,选择车削螺纹主轴转速n存在一定的差异。
下列为一般数控车床车螺纹时主轴转速计算公式:n≤–k式中:p—工件螺纹的螺距或导程,单位mm。
k—保险系数,一般为80。
3)进给速度进给速度是指单位时间内,刀具沿进给方向移动的距离,单位为mm/min,也可表示为主轴旋转一周刀具的进给量,单位为mm/r。
⑴确定进给速度的原则①当工件的加工质量能得到保证时,为提高生产率可选择较高的进给速度。
②切断、车削深孔或精车时,选择较低的进给速度。
③刀具空行程尽量选用高的进给速度。
④进给速度应与主轴转速和切削深度相适应。
⑵进给速度V f的计算 V f = n f式中:n—车床主轴的转速,单位r/min。
4.4 切削用量的选择 数控车削加工中的切削用量包括背吃刀量.pptx
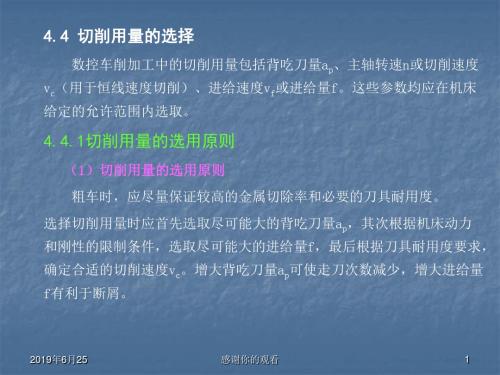
在工厂的实际生产过程中,切削用量一般根据经验并通过查 表的方式进行选取。
常用硬质合金或涂层硬质合金切削不同材料时的切削用量推 荐值见表4-3。
表4-4为常用切削用量推荐表,供参考。
2019年6月25
2019年6月25
感谢你的观看
8
频率和数控装置插补运算速度的约束,由于升降频率特性满足不 了加工需要等原因,则可能因主进给运动产生出的“超前”和 “滞后”而导致部分螺牙的螺距不符合要求。
●车削螺纹必须通过主轴的同步运行功能而实现,即车削螺 纹需要有主轴脉冲发生器(编码器),当其主轴转速选择过高, 通过编码器发出的定位脉冲(即主轴每转一周时所发出的一个基 准脉冲信号)将可能因“过冲”(特别是当编码器的质量不稳定 时)而导致工件螺纹产生乱纹(俗称“乱扣”)。
2019年6月25
感谢你的观看
1
精车时,对加工精度和表面粗糙度要求较高,加工余量不大且 较均匀。选择精车的切削用量时,应着重考虑如何保证加工质量, 并在此基础土尽量提高生产率。因此,精车时应选用较小(但不能 太小)的背吃刀量和进给量,并选用性能高的刀具材料和合理的几 何参数,以尽可能提高切削速度。
图4-24 阶梯走刀路线车圆弧
图4-25 同心圆弧走刀路线车圆弧
2019年6月25
感谢你的观看
19
图4-27为车圆弧的车锥法切削路线 即先车一个圆锥,再车圆弧。
(2)车圆锥的走刀路线分析
图4-27 车锥法走刀路线车圆弧
图4-26 车圆锥走刀路线
2019年6月25
感谢你的观看
20
(3)车螺纹时轴向进给距离的分析
数控机床加工的切削用量

数控机床加工的切削用量包括切削速度V c (或主轴转速n)、切削深度a p 和进给量f ,其选用原则与普通机床基本相似,合理选择切削用量的原则是:粗加工时,以提高劳动生产率为主,选用较大的切削量;半精加工和精加工时,选用较小的切削量,保证工件的加工质量。
1. 数控车床切削用量 1)切削深度a p在工艺系统刚性和机床功率允许的条件下,尽可能选取较大的切削深度,以减少进给次数。
当工件的精度要求较高时,则应考虑留有精加工余量,一般为0.1~0.5mm 。
切削深度ap 计算公式:a p =式中: d w —待加工表面外圆直径,单位mm d m —已加工表面外圆直径,单位mm. 2)切削速度Vc① 车削光轴切削速度V c 光车切削速度由工件材料、刀具的材料及加工性质等因素所确定,表1为硬质合金外圆车刀切削速度参考表。
切削速度Vc 计算公式: Vc=式中: d —工件或刀尖的回转直径,单位mm n —工件或刀具的转速,单位r/min表1 硬质合金外圆车刀切削速度参考表2mw d d注:表中刀具材料切削钢及灰铸铁时耐用度约为60min。
②车削螺纹主轴转速n切削螺纹时,车床的主轴转速受加工工件的螺距(或导程)大小、驱动电动机升降特性及螺纹插补运算速度等多种因素影响,因此对于不同的数控系统,选择车削螺纹主轴转速n存在一定的差异。
下列为一般数控车床车螺纹时主轴转速计算公式:n≤–k式中:p—工件螺纹的螺距或导程,单位mm。
k—保险系数,一般为80。
3)进给速度进给速度是指单位时间内,刀具沿进给方向移动的距离,单位为mm/min,也可表示为主轴旋转一周刀具的进给量,单位为mm/r。
⑴确定进给速度的原则①当工件的加工质量能得到保证时,为提高生产率可选择较高的进给速度。
②切断、车削深孔或精车时,选择较低的进给速度。
③刀具空行程尽量选用高的进给速度。
④进给速度应与主轴转速和切削深度相适应。
⑵进给速度V f的计算V f = n f式中:n—车床主轴的转速,单位r/min。
车削运动和切削用量.pptx

4、( B )是衡量主运动大小的参数。
A、进给量 B、 切削速度 C、切削深度 D、切削厚度 13 第14页/共19页
切削用量三要素:
切削速度υc
进给量ƒ
切削深度ɑp
υc
=
πd n
1000
d—工件待加工表面最大直径。 n—主运动每分钟转数(r/min)
教学的重点、难点、方法
重点:
1、车削运动和加工面的形成。 2、切削用量的基本概念。
难点:
1、切削用量的选择原则。
教学用具-----多媒体课件、投影仪
1
第2页/共19页
车削运动
• 车削工件时,必须使工件和刀具作相对运动.根据运动的性质和作用,车削运动可分为 工件的旋转运动,和车刀的直线(或曲线)运动.
2、过渡表面 : 车刀切削刃在工件上形成的表面.
它将在下一转被切除.
3、待加工表面: 工件上等待切除多余金属层的表面.
表面。
它可能是毛坯表面或加工过的
4
第5页/共19页
车削时工件上形成的表面?
如何判断? 2 3
1
待加工表面n
过渡表面 已加工表面
主运动
f
进给运动
5
第6页/共19页
切削用量的基本概念
≈
640r/min
8
第9页/共19页
D ap
d
2) 进给量 ƒ
n
• 工件每转一圈,车刀沿进
f
给方向移动的距离.
• 单位为mm/r
3)切削深度ɑp
f
2
1
• 车削工件上已加工表面和待加工表面之间的垂直距离.
计算公式:
数控机床加工的切削用量

单元4数控机床加工的切削用量教学目的1、了解数控机床的运动(主运动、进给运动);2、了解数控机床加工刀具的角度及其作用;3、了解数控机床加工中有关切削层的参数及其作用;4、了解数控机床加工中的切削用量及其选用原则。
5、掌握常用不同材料零件在粗加工、半精加工和精加工时的切削用量选用;教学重点1、数控机床加工刀具的角度及其作用;2、数控加工中粗加工、半精加工和精加工时的切削用量选择;教学难点1、刀具的角度及其作用;2、切削用量选用教学方法讲练结合教学内容一、车削加工与刀具1. 车削加工原理在普通车床和一般数控车床上,可以进行工件的外表面、端面、内表面以及内外螺纹的加工。
对于车削中心,除上述各种加工外,还可进行铳削、钻削等加工。
从上述介绍可以看出:在切削过程中,刀具和工件之间必须具有相对运动,这种相对运动称为切削运动。
根据切削运动在切削过程中的作用不同可以分为主运动、和进给运动。
各种机床的主运动和进给运动参见下表。
主运动是指机床提供的主要运动。
主运动使刀具和工件之间产生相对运动,从而使刀具的前刀面接近工件并对工件进行切削。
在车床上,主运动是机床上主轴的回转运动,即车削加工时工件的旋转运动。
2)进给运动进给运动是指由机床提供的使刀具与工件之间产生的附加相对运动。
进给运动与主运动相配合,可以形成完整的切削加工。
在普通车床上,进给运动是机床刀架(溜板)的直线移动。
它可以是纵向的移动(与机床主轴轴线平行),也可以是横向的移功(与机床主轴轴线垂直),但只能是一亇方向的移动。
在数控车床上,数控车床可以同时实现两亇方向的进给,从而加工出各种具有复杂母线的回转体工件。
在数控车床中,主运动和进给运动是由不同的电机来驱动的,分别称为主轴电机和坐标轴伺服电机。
它们由机床的控制系统进行控制,自动完成切削加工。
2. 切削用量切削用量是指机床在切削加工时的状态参数。
不同类型的机床对切削用量参数的表述也略有不同,但其基本的含义都是一致的,如下图所示。
切削用量的计算ppt

切削用量的选择原则
合理的切削用量是指充分利用刀具的切削性能和机床性 能,在保证加工质量的前提下,获得高的生产率和低的加 工成本的切削用量。
1、粗加工的选择原则 粗加工的目的一般以提高生产率为主,但也应考虑经济性和加工成本。 因此在机床刚度和刀具的刚性和耐用度的允许下,尽量优先选择较大 的切削深度,再选择较大的进给速度,最后根据刀具耐用度要求,确 定合适的切削速度(转速)。 2、精加工的选择原则 精加工的目的是保证工件的加工精度和表面质量要求,故一般选用较 小的进给量f,尽可能选用较高的切削速度υc,根据刀具的刚性选择 合适的切削深度。但在能够保证工件的加工精度和表面质量的前提下, 可以适当提高进给速度,提高生产效率,降低生产成本。 2、半精加工,应在保证加工质量的前提下,兼顾切削效率、经济性和 加工成本。
经验 类比
1 2 3
实验计算
查表
Page 13
4
Page 14
单击添加您的公司信息 (联系方式及落款)
Page 11
影响切削用量的要素
不同的工件材料要采用与之适应的刀具材料、刀片类型,要 注意到可切削性。可切削性良好的标志是,在高速切削下有效 地形成切屑,同时具有较小的刀具磨损和较好的表面加工质量。 较高的切削速度、较小的背吃刀量和进给量,可以获得较好的 表面粗糙度。合理的恒切削速度、较小的背吃刀量和进给量可 以得到较高的加工精度。
Page 5
影响切削用量选择的因素:
机床 切削 液
工 6
影响切削用量的要素
1、影响切削用量的因素有: 机床 切削用量的选择必须在机床主传动功率、进给传动功率以及主轴 转速范围、进给速度范围之内。机床—刀具—工件系统的刚性是限制切 削用量的重要因素。切削用量的选择应使机床—刀具—工件系统不发生 较大的“振颤”。如果机床的热稳定性好,热变形小,可适当加大切削 用量。
选择合理的切削用量.精选PPT

确定了背吃刀量ap,进给量f 和刀具耐用度T,则可以按下面公式计算或由表确定切削速度υ 和机床转速n 。 切削用量对加工质量的影响
有重要影响。 在切削加工性差的材料时,由于这些材料硬度高、强度高、导热系数低,必须首先考虑选择合理的切削速度。
(3)切削速度的确定
• 根据已选定的背吃刀量、进给量f及刀具 耐用度T计算
c
Cv Tmassxp
f
f
Kv(m/min)
• 确则定可了以按背下吃刀面公量式ap,计进算给或量由f表和确刀定具切耐削用速度度Tυ,
和机床转速cn。Tma6Cs0sxvpTmCfaVpxfvfyK v kvv(m/min)
• =0.5~2mm B、精车时,选用高的切削速度,小的切削深度和进给量。
数控机床加工时应注意零件加工中的某些特殊因素: 切削用量对刀具耐用度的影响
在切削加工性差的材料时,由于这些材料硬度高、强度高、导热系数低,必须首先考虑选择合理的切削速度。
• 粗车时,应选较低的切削速度,精加工时选择较高的切削速度;
• 当刀具寿命一定时,切削速度υ对生产率
影响最大,进给量f 小。
次之,背吃刀量ap最
• 在刀具耐用度一定,从提高生产率角度 考虑,对于切削用量的选择有一个总的 原则:
• 首先选择尽量大的背吃刀量,其次选择 最大的进给量,最后是切削速度。
• 当然,切削用量的选择还要考虑各种因 素,最后才能得出一种比较合理的最终 方案。
• 半精加工时(表面粗糙度Ra6.3~3.2μm), 背吃刀量一般为0.5~2㎜。)
• 精加工时(表面粗糙度Ra1.6~0.8μm),背 吃刀量为0.1~0.4㎜。
- 1、下载文档前请自行甄别文档内容的完整性,平台不提供额外的编辑、内容补充、找答案等附加服务。
- 2、"仅部分预览"的文档,不可在线预览部分如存在完整性等问题,可反馈申请退款(可完整预览的文档不适用该条件!)。
- 3、如文档侵犯您的权益,请联系客服反馈,我们会尽快为您处理(人工客服工作时间:9:00-18:30)。
④数控机床为了保证刀具的稳 定,一般使用前角较小的刀具。
刀具的几何角度对加工的影响
后角的选择原则:
①工件材料:工件硬度、强度较高以及脆性材料 选用较小的后角。 ②加工过程:精加工选用较大的后角;粗加工选 用较小的后角。
刀具的几何角度对加工的影响
② 精加工时切削用量的选择原则 首先根据粗加工 后的余量确定背吃刀量;其次根据已加工表面的粗 糙度要求,选取较小的进给量;最后在保证刀具耐 用度的前提下,尽可能选取较高的切削速度。
钻孔时
ap = dm/2
例题:
车外圆时工件加工前直径为62mm,加工后直径为56 mm,工件转速为4r/s,刀具每秒钟沿工件轴向移动2mm,
求v、f、ap。
解:
v =πdn/1000 = π·62·4/1000 = 0.779 m/s f = vf /n = 2/4 = 0.5 mm/r ap = (dw-dm)/2=(62-56)/2=3 mm
2. 切削宽度 aw aw= ap/sinκr
3. 切削层面积 Ac ( κ'r = 0) Ac= ac aw= f ap
切削层
正切屑与倒切屑
正切屑: ac≤ aw
倒切屑: ac>aw
产生倒切屑的情况下,主要 切削工作以由原来的副切削刃承 担,此时,原副切削刃上刀具的 副前角 、副刃倾角对切削过程的
漯河第一中等专业学校
段克华
一、金属切削的基本知识
金属切削的基本知识 切削运动和工件加工表面
主运动
切下切屑形成工件表面形状所需要的最 基本运动,速度最高、消耗功率最多。
进给运动
使切削工具不断切下切屑所需要的运动
待加工表面 即将切去切屑的表面
过渡表面
切削刃正在切削着的表面
已加工表面 已切去切屑的表面
副偏角的选择原则:
①在不引起震动的情况下,刀 具应选用较小的副偏角。 ②精加工时刀具的副偏角应该 选更小一些。
刀具的几何角度对加工的影响
刃倾角的选择原则:
①粗加工刀具应选用刃倾角<0°, 使刀具具有良好的强度和散热条件。
②精加工刀具应选用刃倾角>0°, 使切屑流向待加工表面,以提高加 工质量。
③断续切削应该选用刃倾角<0°, 以提高刀具强度。
刀具的几何角度
在正交平面内测 量的角度
(1)前角γo
前面与基面的夹角
r (2)后角αo
主后面与切削平面的夹角
(3)楔角βo
前面与主后面的夹角
0 90 ( 0 0 )
刀具的几何角度
在基面内测量的 角度
(1)主偏角κr
主切削刃与进给速度方向 的夹角,恒为正。 r
(2)副偏角κr ˊ
副切削刃与进给速度反方向 的夹角,恒为正
(m/s 或 m/min)
主运动为旋转运动
v =πd n/1000
往复运动
v = 2Lnr /1000
L-刀具或工件作往复直线运动的行程长度
nr-刀具或工件每分钟(或每秒钟)往复的次数
2. 进给量 f
进给速度 vf=n f (mm/s 或 mm/
车削外圆时
ap = (dw-dm)/2
主偏角
主偏角影响刀具的耐用度、已加工表面粗糙度 与切削力的大小。
副偏角
副偏角的功能在于减小副切削刃与以加工表面 的摩擦。
刃倾角 刃倾角主要影响切屑流向和刀尖强度。
刀具的几何角度对加工的影响
前角的选择原则:
①工件材料:塑性材料选用较 大的前角;脆性材料选用较小 的前角。
②刀具材料:高速钢选用较大 的前角;硬质合金选用较小的 前角。
主偏角的选择原则:
①工件材料:加工淬火钢等硬 质材料时,选用较大主偏角。
②使用硬质合金刀具进行精加 工时,应选用较大的主偏角。
③用于单件小批量生产的车刀, 主偏角应选为45°或90°,以 提高刀具的通用性。
④需要从工件中间切入的车刀, 例如加工阶梯轴类的工件,应 根据工件的形状选择主偏角。
刀具的几何角度对加工的影响
④工艺系统的整体刚性较差时,应 选用较大的刃倾角,以减小震动。
刃倾角对排屑方向的影响
切削层
切削层参数
由切削刃正在切削的这一层金属叫作切削层。切削层的 截面尺寸称为切削层参数。它决定了刀具切削部分所承受的 负荷和切屑尺寸的大小,通常在基面Pr内度量。
1. 切削厚度 ac (λs= 0) ac= f sinκr
切削刀具
刀具的组成
三面
前刀面Aγ 后刀面Aα 副后刀面A α′
两刃
主切削刃 S 副切削刃 S′
一尖
过渡刃
刀具角度的参考系
(1) 基面pr
过切削刃上的某个选定点且垂直于主 运动方向的平面
(2)切削平面ps
过切削刃上的某个选定点且垂直于基
面的平面
(3)正交平面po
过切削刃上的某个选定点且同时垂直 于基面和切削平面的平面
根据加工性质、加工要求、工件材料及刀具材料和尺寸查切 削用量手册并结合实践经验确定,并考虑:
(1)生产效率 (2)机床特性(机床功率) (3)刀具差异(刀具耐用度) (4)加工表面粗糙度
车削加工切削用量的选择
切削用量选择原则
① 粗加工时切削用量的选择原则 首先选取尽可能 大的背吃刀量;其次要根据机床动力和刚性的限制 条件等,选取尽可能大的进给量;最后根据刀具耐 用度确定最佳的切削速度。
金属切削的基本知识 切削运动和工件加工表面
平面刨削的切削运动与加工表面
机床类型 数控车床 数控铣床
数控磨床
数控镗床
各种机床的主运动和进给运动
主运动 主轴(工件) 主轴(刀具)
主轴(砂轮刀具)
主轴(刀具)
进给运动 刀架
工作台
工作台(或砂轮轴),视磨床种类而 定
工作台
切削用量三要素
1. 切削速度 v
(3)刀尖角εr
主切削刃与副切削刃的夹角
r 180 (kr kr' )
刀具的几何角度
在切削平面内测 量的角度
刃倾角λs
主切削刃与基面的夹角 r
刀具的几何角度对加工的影响
刀具角度
角度的作用
前角
前角主要影响切屑变形和切削力的大小以及 刀具耐用度和加工表面质量的高低。
后角
后角的主要作用是减小后刀面与过渡表面层 之间的摩擦,减轻刀具磨损。
影响,比前角 、刃倾角更为重
要。这说明,在刀具切削时判定 主切削刃和副切削刃除与切削运 动有关外,还与切削层尺寸参数 有关 。
二、车削加工切削用量的选择
车削加工切削用量的选择
切削用量选择原则
切削用量的大小对切削力、切削功率、刀具磨损、加工质 量和加工成本均有显著影响。数控加工中选择切削用量时,就 是在保证加工质量和刀具耐用度的前提下,充分发挥机床性能 和刀具切削性能,使切削效率最高,加工成本最低。