回转窑处理高炉瓦斯泥的结圈机理分析
回转窑处理高炉瓦斯泥的结圈机理分析

s t . Th e u t ho t a h e i f me hod a fe tv l le it h i o ma i n i ot r uls e r s ls s w h t t r e k nds o t s c n e f c i e y a l v a e t e rng f r to n r a y
Ab t a t Zi c wa x r c e r m n an l s u n c a sud t ot r in. The r w a e i l s r c : n s e t a t d f o Pa g g b a t f r a e g s l ge wih r a y k l a m t ra s, o r to nd rng m a e i lf r ton we e a l e y t ma ia l pe a i n a i t ra o ma i r nayz d s s e tc ly;f t r o e,wa h kin,me ha i a ur he m r s l c nc l
回转 窑结 圈严重 而被 迫停 窑 , 成生 产周期 短 ( 造 一般
只有 6 2天 ) 作业 率低 ( O ) 生 产成本 高 , ~1 、 5 、 严重 影 响 了该 厂 的生 产顺 行 。为 了能够 有效地解 决 回转 窑结 圈 问题 , 们对 结 圈机 理进 行 了系统 分析 , 时 我 同
回转窑结圈处理机

回转窑结圈处理机1.引言1.1 概述回转窑是一种常见的工业设备,广泛应用于水泥生产等领域。
它以其高效、节能的特点,成为了生产过程中不可或缺的一部分。
然而,长期以来,回转窑在生产过程中常常会出现结圈的问题,给生产造成了一定的困扰,也浪费了大量的能源和资源。
为了解决这个问题,结圈处理机应运而生。
结圈处理机是一种专门用于解决回转窑结圈问题的设备,它通过分解和破碎结圈料,有效地防止了结圈的形成。
同时,结圈处理机还可以将结圈料转化为可再利用的原料,从而实现了资源的循环利用和节能减排的目标。
本文将重点介绍回转窑结圈处理机的工作原理、优势以及应用前景展望。
通过深入了解和研究回转窑结圈处理机,相信读者们可以更加深刻地认识到它在工业生产中的重要作用,以及它所具有的巨大潜力和广阔的发展空间。
接下来的章节将一一详细介绍回转窑的工作原理和结圈处理机的相关知识,以期能够为读者们提供全面而深入的了解。
1.2 文章结构本文共分为三部分,每一部分都围绕着回转窑结圈处理机展开详细的讨论。
下面将对每一部分的内容进行简要介绍。
第一部分是引言部分,主要包括概述、文章结构和目的。
在概述中,将介绍回转窑结圈处理机在工业生产中的重要性和应用背景。
接下来,将明确本文的结构,即分为引言、正文和结论。
最后,明确文章的目的,即通过对回转窑结圈处理机的深入研究,探讨其优势和应用前景。
第二部分是正文部分,分为两个小节:回转窑的工作原理和结圈处理机的介绍。
在回转窑的工作原理部分,将详细介绍回转窑的基本工作原理、工作过程和相关参数。
在结圈处理机的介绍部分,将对结圈处理机的结构、工作原理和应用场景进行详细解析。
第三部分是结论部分,也分为两个小节:结圈处理机的优势和应用前景展望。
在结圈处理机的优势部分,将总结回转窑结圈处理机相比传统处理方法的优势,并提出相关的案例支持。
在应用前景展望部分,将探讨回转窑结圈处理机在未来的发展趋势和应用领域,以及可能面临的挑战和解决方案。
回转窑结圈的原因及处理方法

回转窑结圈的原因及处理方法1、结圈的危害回转窑“结圈”的部位一般在距窑口一定距离的固体燃料集中燃烧点附近的耐火窑衬上,厚度可达200-500 mm左右。
“结圈”对球团生产的危害有以下几方面:(1)降低产量,增加劳动强度窑圈一经形成,对燃料烧烧所产生的热气流势必起阻碍作用,如图-1所示。
热气流被部分阻挡在A区,影响了球团的焙烧效果。
同时,由于链篦机上生球的干燥、预热过程是利用窑尾废气进行的,故此,结圈也对生球的干燥、预热产生不良影响。
具体地说,就是透气性差,火焰不进,后部温度低,干燥时水分不易脱除,生球爆裂、粉化严重,成品率低,从而降低了劳动生产率。
另外,圈结形成后,如不及时处理,就会使圈的纵向长度、厚度增加,当圈掉下时,必然增加工人的劳动强度,有时甚至需停机处理,也影响了球团矿的产量。
(2) 增加了设备负荷如图-1所示,一定面积及厚度的结圈使物料流被阻于B区,此时,被阻的料量要高出正常时许多,加之圈本身的重量,必然增加了托轮、轴承的磨损,同时,增加了电机的负荷,甚至烧毁。
(3) 浪费能源在实际看火操作中,当出现“结圈”现象后,由于热气流被阻于A区,为保证链篦机的干燥和预热效果,看火工往往采用加大给煤量的方式,这无疑造成了能源浪费。
2、结圈的原因结圈的原因,在生产中主要可以归纳为操作不当。
具体地说,是由于上料量过大,干燥效果差,生球爆裂,粉化严重,致使透气性差,使得引风机抽动火焰的作用不明显,火焰只在窑内一定距离燃烧。
在大于1 200℃的高温下,未完全氧化的Fe3O4就与磁铁矿中一定数量的SiO2发生反应形成液相。
2Fe3O4+3SiO2+2CO=3Fe2SiO4+2CO22FeO+SiO2=Fe2SiO4另外,当给煤量较大时,在1 150℃条件下,Fe2O3也会部分分解为Fe3O4,与SiO2作用而生成2FeO·SiO2,形成渣相粘结。
这就使得物料在流经焙烧带时,所产生的液相、渣相极易粘附在窑衬的表面,同时粘结物料而产生结圈现象。
日照泰东回转窑的结圈分析及处理
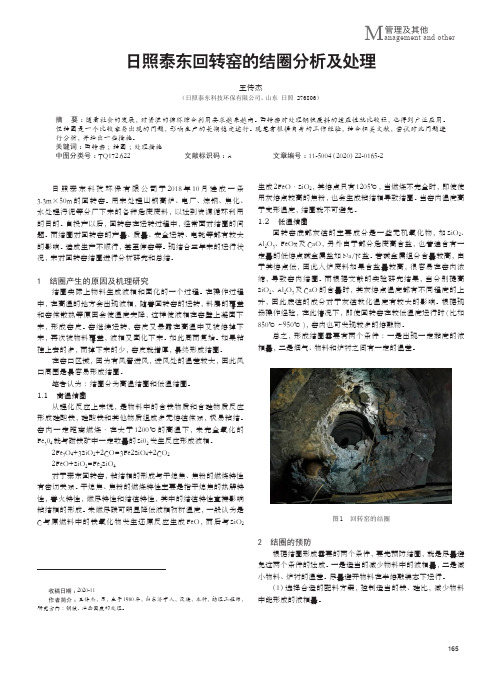
165管理及其他M anagement and other日照泰东回转窑的结圈分析及处理王传杰(日照泰东科技环保有限公司,山东 日照 276806)摘 要:随着社会的发展,对资源的循环综合利用要求越来越高。
回转窑对处理钢铁废料的适应性就比较强,也得到广泛应用。
但结圈是一个比较容易出现的问题,影响生产的长期稳定运行。
现笔者根据自身的工作经验,结合相关文献,尝试对此问题进行分析,并给出一些措施。
关键词:回转窑;结圈;处理措施中图分类号:TQ172.622 文献标识码:A 文章编号:11-5004(2020)22-0165-2 收稿日期:2020-11作者简介:王传杰,男,生于1980年,山东济宁人,汉族,本科,助理工程师,研究方向:钢铁、冶金固废的处理。
日照泰东科技环保有限公司于2018年10月建成一条3.3m×50m 的回转窑。
用来处理山钢高炉、电厂、炼钢、焦化、水处理污泥等分厂下来的各种危废废料,以达到资源循环利用的目的。
自投产以后,回转窑在运转过程中,经常面对结圈的问题。
而结圈对回转窑的产量、质量、安全运转、电耗等都有较大的影响。
造成生产不顺行,甚至停窑等。
现结合三年来的运行状况,来对回转窑结圈进行分析研究和总结。
1 结圈产生的原因及机理研究结圈实际上物料生成液相和固化的一个过程。
在操作过程中,在高温的地方会出现液相,随着回转窑的运转,料层的覆盖和窑体散热等原因会使温度突降,这样使液相在窑壁上凝固下来,形成窑皮。
窑继续运转,窑皮又暴露在高温中又被熔掉下来,再次被物料覆盖,液相又固化下来。
如此周而复始。
如果粘挂上去的多,而掉下来的少,窑皮就增厚,最终形成结圈。
在窑口区域,因为有风管进风,进风处的温差较大,因此风口周围是最容易形成结圈。
笔者认为:结圈分为高温结圈和低温结圈。
1.1 高温结圈从理化反应上来说,是物料中的含铁物质和含硅物质反应形成硅酸铁,硅酸铁和其他物质组成多元熔渣体系,极易粘结。
回转窑接圈原因分析

1 结圈的形成回转窑内形成结圈的因素很多,但液相的产生和固化是结圈的主要形成过程。
而物料温度、煤灰和原料组成又是决定液相的生成和固化的主要因素。
在煅烧过程中,料在1200℃左右出现液相,在1250℃左右液相粘度开始变小,液相量增加,由于料层覆盖温度突降,加之筒体表面散热,液相在窑壁上凝固下来,形成窑皮。
窑继续运转,窑皮又暴露在高温中而被熔掉下来,再次被物料覆盖,液相又凝固下来,如此周而复始。
如果粘挂上去的多,掉下来的小,窑皮就增厚,反之就变薄。
在正常情况下,窑皮可保持在200mm左右的厚度。
该温度条件及区域内若熔化和固化的过程达到平衡,窑皮就不会增厚。
当熔化的少固化的多,其厚度增长到一定程度,即形成圈。
当物料与液相的温差大时,在足够液相的条件下,圈体越结越厚。
1.1 前结圈的形成前结圈(又称窑口圈),是结在回转窑烧成带末端部位的圈。
在正常煅烧条件下,物料温度为1350~1450℃,液相量约为24%,其粘度较大。
当熟料离开烧成带时,液相开始冷却,进入冷却带的液相已基本固化。
在烧成带和冷却带的交界处存在着较大的温差,窑口物料温度高于窑皮温度。
当熟料进入冷却带时,带有液相的高温熟料覆盖在温度较低的末端窑皮上,就会很快粘结、越粘越厚,最后形成前结圈。
在煅烧过程中,当烧成带高温部分温度过于集中时,冷却带与烧成带交界处出现很大的温差,加之高温急烧液相量增多,粘度较小,熟料进入冷却带时,仍有大量液相迅速冷却在交界的附近,促进了前圈的增长。
1.2 熟料圈的形成熟料圈(又称二道圈),是结在窑内烧成带与放热反应带之间的圈,也是回转窑内危害最大的结圈。
在熟料煅烧过程中,当物料温度达到1280℃时,其液相粘度较大,熟料圈最易形成,冷却后比较坚固,不易除掉,在正常煅烧情况下,熟料圈体的内径部分,往往被烧熔而掉落,保持正常的圈体内径。
如果在1250~1280℃温度范围内出现的液相量偏多,往往形成妨碍生产的熟料圈。
熟料圈一般结在烧成带的边界或更远,开始是烧成带后边的窑皮逐渐增长,逐渐长厚,发展到一定程度即形成熟料圈。
回转窑窑后结圈原因分析及处理方法

回转窑窑后结圈原因分析及处理方法巩义市恒昌冶金建材设备厂生产的1000t/d熟料生产线是由天津水泥工业设计研究院有限公司设计的,主要包括TDF型分解炉、单系列五级旋风预热器、Φ3.2m×50m回转窑及TC-836篦式冷却机。
自2007年2月以来,窑后频繁发生结圈、结球的工艺事故,巩义市恒昌冶金建材设备厂技术人员现将原因分析及解决措施介绍如下,供同仁参考。
1、结圈情况2007年3月19日最为严重,窑前返火,窑尾有漏料现象,无法操作煅烧,迫使停窑处理。
从窑内看,主窑皮长达22m,副窑皮长到窑尾,35~37m处形成后结圈,结圈最小孔洞呈不规则状,直径约l.5m,进窑观察该圈明显分为两层,且层次明确、清晰,第一层厚约150mm,呈黄白色,第二层厚约460mm,呈黑色,圈体非常致密。
对圈体取样分析见表1。
表1 圈体取样分析结果从表l可以看出,第一层硫碱含量较高,是硫碱圈,第二层明显是煤粉圈,熟料液相出现过早、过多导致结圈。
2、原因分析(1)由于2006年煤价不断上涨,加之公路运输距离远,为了降低成本,采用当地劣质煤煅烧,煤质下降,灰分高,挥发分低,发热值低,煤工业分析如表2、3。
实际生产中,煤可燃性差,煤粉燃烧不完全,大量煤灰不均掺入生料中,液相在窑后面提前出现,而未燃尽的煤灰产生沉积及液相的提前出现结圈。
(2)2007年以来,由于机械原因,高温风机l号轴与密封圈强烈摩擦,产生局部高温,使轴侧曲,水平振动最高达6.4mm/s。
为了降低振动,不得不降低高温风机转速,由原来的1130r/min降至l060r/min,有时更低,严重影响了窑内通风,加上煤质又差,更多的窑头燃烧不完全的煤粉沉积在窑后燃烧,使窑内后部温度升高,液相量增加,加速了窑后结圈的形成。
(3)为了处理窑后结圈,我厂在迫不得已的情况下停窑烧后圈,由于煤质差,二、三次风温低,燃料不完全或未燃烧的煤粉落在圈上及圈后的积料上,不断燃烧,造成物料发粘,不但圈未烧掉,反而越结越厚,这也是第一层圈形成的主要原因。
回转窑结圈的原因
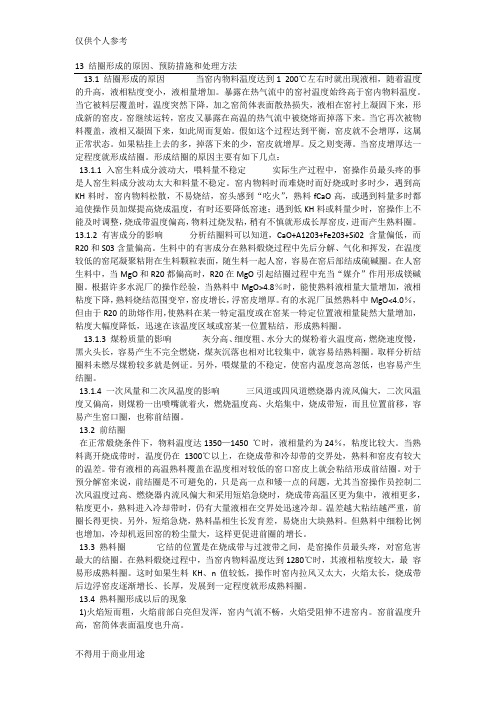
13 结圈形成的原因、预防措施和处理方法13.1 结圈形成的原因当窑内物料温度达到1 200℃左右时就出现液相,随着温度的升高,液相粘度变小,液相量增加。
暴露在热气流中的窑衬温度始终高于窑内物料温度。
当它被料层覆盖时,温度突然下降,加之窑简体表面散热损失,液相在窑衬上凝固下来,形成新的窑皮。
窑继续运转,窑皮又暴露在高温的热气流中被烧熔而掉落下来。
当它再次被物料覆盖,液相又凝固下来,如此周而复始。
假如这个过程达到平衡,窑皮就不会增厚,这属正常状态。
如果粘挂上去的多,掉落下来的少,窑皮就增厚。
反之则变薄。
当窑皮增厚达一定程度就形成结圈。
形成结圈的原因主要有如下几点:13.1.1 入窑生料成分波动大,喂料量不稳定实际生产过程中,窑操作员最头疼的事是人窑生料成分波动太大和料量不稳定。
窑内物料时而难烧时而好烧或时多时少,遇到高KH料时,窑内物料松散,不易烧结,窑头感到“吃火”,熟料fCaO高,或遇到料量多时都迫使操作员加煤提高烧成温度,有时还要降低窑速;遇到低KH料或料量少时,窑操作上不能及时调整,烧成带温度偏高,物料过烧发粘,稍有不慎就形成长厚窑皮,进而产生熟料圈。
13.1.2 有害成分的影响分析结圈料可以知道,CaO+A1203+Fe203+Si02含量偏低,而R20和S03含量偏高。
生料中的有害成分在熟料煅烧过程中先后分解、气化和挥发,在温度较低的窑尾凝聚粘附在生料颗粒表面,随生料一起人窑,容易在窑后部结成硫碱圈。
在人窑生料中,当MgO和R20都偏高时,R20在MgO引起结圈过程中充当“媒介”作用形成镁碱圈。
根据许多水泥厂的操作经验,当熟料中MgO>4.8%时,能使熟料液相量大量增加,液相粘度下降,熟料烧结范围变窄,窑皮增长,浮窑皮增厚。
有的水泥厂虽然熟料中MgO<4.0%,但由于R20的助熔作用,使熟料在某一特定温度或在窑某一特定位置液相量陡然大量增加,粘度大幅度降低,迅速在该温度区域或窑某一位置粘结,形成熟料圈。
回转窑后结圈的原因分析与解决措施

回转窑后结圈的原因分析与解决措施发布时间:2022-04-25T02:30:40.147Z 来源:《工程管理前沿》2022年1期作者:田硕[导读] 近年来,由于国家倡导节能减排的生产,从而加大了对一些浪费资源和污染比较大的企业改革田硕山东申丰水泥集团有限公司山东省枣庄市 277300引言:近年来,由于国家倡导节能减排的生产,从而加大了对一些浪费资源和污染比较大的企业改革,这就给了新型熟料回转窑一个重要的市场,让他们可以快速的发展起来。
熟料回转窑设备结构坚固、运转平稳、出窑产品质量高。
此外,在环保方面,利用熟料窑焚烧危险废物、垃圾,这不仅使废物减量化、无害化,而且将废物作为燃料利用,节省煤粉,做到废物的资源化。
关键词:回转窑后结圈解决措施摘要:熟料回转窑后结圈往往形成于烧成带和过渡带之间。
在熟料煅烧过程中,当窑内温度达到1280℃时,其液相粘度较大,此时,如果生料的KH、n率值较低,操作使窑内拉风较大,火焰太长,烧成带后边浮窑皮逐渐增长、增厚,发展到一定程度就形成了熟料回转窑的后结圈。
一、后结圈情况A企业配置一条5000t/d预分解熟料回转窑。
于2021年10月份在窑尾38米、43米处出现两道结圈,严重时窑尾出现漏料,窑投料量下降,熟料质量波动,窑况很不稳定。
二、原因分析2.1原煤内水偏高加剧了结圈的发生2021年煤价不断上涨,原煤库存为0吨,原煤随来随用,严重影响煤的均化效果。
煤粉内水偏高,窑头喷煤管燃烧速度慢、燃烧时间长,火焰的热力分散,燃烧时热力强度低,高温点后移,烧成带拉长,高温点不集中,熟料烧结不致密,二次风温偏低,恶性循环更加加剧了火焰燃烧速度。
物料预烧不好,容易产生不完全燃烧,没有燃尽的煤粉颗粒和CO不能在烧成带燃烧,部分聚集在窑尾燃烧,促使液相在过渡带提前出现,将未熔的物料黏结在一起,形成后结圈。
停窑后取结圈料化学分析结果发现:正常熟料烧失量为0.42%,结圈料为1.66%、2.06%也验证了这一点。
- 1、下载文档前请自行甄别文档内容的完整性,平台不提供额外的编辑、内容补充、找答案等附加服务。
- 2、"仅部分预览"的文档,不可在线预览部分如存在完整性等问题,可反馈申请退款(可完整预览的文档不适用该条件!)。
- 3、如文档侵犯您的权益,请联系客服反馈,我们会尽快为您处理(人工客服工作时间:9:00-18:30)。
doi:10.3969/j.issn.1007-7545.2012.05.017
回转窑处理高炉瓦斯泥的结圈机理分析
姚增远
(攀枝花钢城集团有限公司冶金辅料分公司,四川攀枝花617000)
摘要:采用回转窑从攀钢高炉瓦斯泥中提取锌,对生产原料、生产操作、结圈物等进行系统分析,并根据其结果分别采用洗窑、机械处理、降铁处理3种方式进行工业试验。
结果表明,3种方式均能够在一定程度上有效地缓解回转窑结圈、提高生产效率和降低生产成本。
关键词:高炉瓦斯泥;回转窑;结圈
中图分类号:TF065.7 文献标识码:B 文章编号:1007-7545(2012)05-0000-00 Mechanism Analysis of Rotary Kiln Ring Formation on Treating Blast Furnace Gas Mud
YAO Zeng-yuan
(Panzhihua Gangcheng Group Co., Metallurgical Auxiliary Branch, Panzhihua 617000, Sichuan, China) Abstract: Zinc was extracted from Pangang blast furnace gas sludge with rotary kiln. The raw materials, operation and ring material formation were analyzed systematically; furthermore, wash kiln, mechanical processing and iron reduction processing were used to undertake industrial test based on the analyzing results. The results show that three kinds of methods can effectively alleviate the ring formation in rotary kiln in a certain extent, improve production efficiency and reduce production cost.
Key words: blast furnace gas sludge; rotary kiln; ring formation
目前,国内高炉瓦斯泥大部分采用回转窑火法工艺进行锌的富集和铁的分离,从而有效地解决了瓦斯泥在高炉循环应用中对高炉造成的危害,并减少了部分瓦斯泥长期露天堆放对环境的污染,且使其中的锌、铁等有价元素得到了充分合理的利用[1]。
但由于瓦斯泥自身特点造成该工艺存在先天性不足——回转窑易结圈。
以攀钢瓦斯泥火法富集锌生产线为例:该生产线自2008年3月投产以来多次因回转窑结圈严重而被迫停窑,造成生产周期短(一般只有6~12天)、作业率低(50%)、生产成本高,严重影响了该厂的生产顺行。
为了能够有效地解决回转窑结圈问题,我们通过对结圈机理进行了系统的分析,同时结合国内同行的生产现状,利用该生产线多次进行试生产操作摸索和理论分析,得出3种目前解决回转窑结圈的有效途径,为攀钢高炉瓦斯泥在回转窑内进行有价元素的回收利用提供依据。
1 原料
1.1 攀钢高炉瓦斯泥
攀钢高炉瓦斯泥用磨机磨到-0.074 mm占90%,主要化学成分(%):TFe 29~35、ZnO 7~10、C 16~20、Al2O3 2~4、SiO2 10~12、CaO 3~5。
可以看出,瓦斯泥主要含铁、炭、锌、Al2O3、SiO2,其中氧化锌将在生产过程中被还原成锌蒸汽后迅速再氧化成氧化锌小颗粒被收集,炭将被氧化释放出热量,氧化铁部分被还原后留在渣中,Al2O3和SiO2留在炉渣中[2]。
瓦斯泥中化学成分波动较大,这主要与高炉原料的波动有关。
1.2 燃料
回转窑处理瓦斯泥采用的燃料一般为无烟煤,主要指标:发热量≥23 012 kJ/kg、粒度3~25 mm 占25%以上、挥发份≤10%、灰分≤35%、水分≤3.0%。
采用无烟煤作为瓦斯泥提锌热源主要是为了减少进入氧化锌产品中的杂质,提高氧化锌产品的质量,降低环境污染。
2 结圈物分析
根据回转窑结圈位置的不同,分别对窑中结圈物和窑头结圈物进行取样分析,结果如下。
窑头渣物相(%):金属铁+硫化铁3~5、硅酸盐83~86、黑钛石6~9、钛铁晶石2~4、镁铝尖晶石1。
窑中渣物相(%):金属铁+硫化铁38~41、硅酸盐41~44、黑钛石1~3、钛铁晶石15~18、镁铝尖晶石0.3。
窑头结圈物熔点1 177 ℃,化学成分(%):TFe 30.24、MFe 26.32、SiO2 26.06、CaO 12.48、C 3.56、P 0.045、S 0.58。
窑中结圈物熔点1 211 ℃,化学成分(%):TFe 50.62、MFe 46.99、SiO2 19.14、CaO 8.40、C 4.13、P 0.030、S 0.863。
作者简介:姚増远(1981-),男,四川人,助理工程师.
通过对结圈物的分析得知,瓦斯泥在经回转窑处理后形成的渣主要成分有金属铁、氧化硅、氧化铝和氧化钙及部分杂质组成的各种盐类。
其中窑内结圈物熔点较高、且含铁量较高,这是造成结圈不易处理的主要原因。
窑头和窑中结圈物的SEM照片见图1和图2。
图1中标注1的为铝镁尖晶石,标注8~10的为黑钛石,其余的为硅酸盐相。
图2中标1的为硫化铁,标2~4的为钛铁晶石,标5的为金属铁,其余的为硅酸盐相。
图1 窑头结圈物的SEM照片
Fig.1 SEM photograph of material in kiln head ring formation
图2 窑中结圈物的SEM照片
Fig.2 SEM photograph of material in kiln ring formation
通过对窑内结圈物显微结构的分析,可知窑头结圈物主要是以硅酸盐相为主,黑钛石呈细针状或无定形状均匀分布,相对来讲比较脆,用机械方法易清理。
而窑中结圈物夹杂重金属铁有近1/3多,且金属铁呈粗大长链条状或圆粒状,金属铁边部吸附难还原八面体钛铁晶石,相对比较坚固,难清除。
结圈物铁含量较高,主要是由于瓦斯泥在回转窑中经过一系列的反应后,氧化锌被还原收集、碳被氧化[3],而铁的氧化物部分被还原成液体金属不能够及时排出,并在窑壁进行了富集造成的。
3 工艺操作分析
结合实际生产操作及结圈现象观察,发现当窑内温度一旦有较大的波动将会很快造成窑内物料粘壁、结圈出现。
分析认为造成此现象主要是由于以下几方面:
1)瓦斯泥与无烟煤混料时不均匀造成回转窑内温度容易波动;
2)在生产过程中由于窑速与下料量不匹配造成窑内温度波动较大,从而影响到窑内物料的状态;
3)煤粉质量的影响。
若灰分高、细度粗、水分大则容易产生不完全燃烧,煤灰在沉落相对比较集中时,容易形成熟料圈,但此类结圈随着窑温变化易脱落。
4 讨论
通过以上分析可知,造成瓦斯泥在回转窑内易结圈难处理的原因主要有以下3点:
1)瓦斯泥原料成分不稳定、且铁含量较高;
2)生产过程中操作不当;
3)结圈物中金属相较多、且熔点较高。
针对以上情况并结合国内同行的生产经验,决定在稳定操作的前提下分别采用以下3种方式对窑内结圈进行处理:
“洗窑”:当发现回转窑内的结圈物影响到物料在窑内的正常通行时,采用直接向回转窑内输送高热值无烟煤迅速提高窑内温度,使结圈物在高温下软化,并在重力的作用下脱离窑壁后随物料排出回转窑。
“机械处理”:制作一根较长的撞杆,一旦发现窑内有粘壁或结圈现象,立即用撞杆进行机械撞击处理。
“降铁处理”:对入窑原料进行优化。
根据入窑瓦斯泥全铁含量检测结果,配入适量的低铁高锌废渣使其入窑料中铁含量降至20%以下。
该方式广泛应用于湖南等地的回转窑有色冶炼生产线。
5 工业应用效果
为了验证以上3种方式的可行性,我们利用攀钢高炉瓦斯泥处理生产线进行工业试验,其效果如下。
5.1 洗窑方式
采用该方式能够很好地处理回转窑结圈,在设备允许的条件下可不停窑无限期延长生产周期。
但由于采用高热值无烟煤进行高温清圈,氧化锌粉收得率降低,生产成本相对较高。
5.2 机械处理
采用该方式对窑头结圈能够很好地进行清理,但一旦结圈距离窑头较远时,由于窑内温度较高,伸入窑内的撞杆易软化变形,撞击力降低,对结圈部位的清理效果较差。
若能够对撞杆做进一步的改进优化,提高其清圈能力,该方式将会是一种最优的处理回转窑结圈的工艺。
5.3 降铁处理
该方式由于降低了入窑料的铁含量,使形成的渣子中金属铁含量明显降低,大大缓解了回转窑的结圈,最长可达到一个月不结圈。
且由于渣中铁含量的降低,即便有结圈也只要稍提高窑内温度便可使结圈物脱落。
但采用该方式生产形成的渣子由于铁含量较低,其经济价值较小。
6 结论
洗窑、机械处理和降铁处理这三种处理结圈的方式均能在一定程度上达到提高生产率、降低生产成本、保证生产顺行的目的,需要根据情况选用。
参考文献
[1] 白仕平,张丙怀,伍成波,等. 利高炉瓦斯泥高效利用的实验研究[J]. 中国冶金,2007,17(6):40-45.
[2] 张鑫,丁跃华,罗志俊,等, 攀钢瓦斯泥脱锌还原工艺研究[J]. 云南冶金,2008,37(3):32-36.
[3] 张红军. 直接还原铁在我国的发展现状及前景[J]. 鞍山钢铁学院学报,2002,5(11):24-31.。