首件末件自主检查表
五金制品首件末件检查记录表

→判定NG→品质部门负责人审核→返回生产(重新送检)。
五金制品□首件□末件检查记录表
冲速: 吨位: 模高:
五 客户 金 生 申请 产 日期 填 写 产品类别:
品名规格
模穴 数量
□五金
订单 编号
实际 穴数
原材料规格 调试担当
机器 编号
确认
首件时机: □正常生产 □模具大修 □换机台 □持续生产 □参数变更
NO 检验项目
检验标准
检验数据判定12345
6
7
8
检验员
□OK可生产 □NG不可生产 □NG,但可附加条件生产
备注:生产部在生产调试机器OK生产开始前,须完整填写好此表格的规定的相关内容,交品质部检验确认,尺寸检验NG时须记录全部不良真实数 据,OK时只记录最大值及最小值即可,记录为MIN~MAX(汽车产品需记录全模数据),当确认NG需要附加条件生产才能满足品质要求时,生产组 长以上人员必须签名确认后方可生产.
9
10
11 五 金 12 品 13 质 填 14 写 15
16
17
18
19
20
21
22 检具
最终判定结果:
(1)目测 (2)卡尺(3)千分尺(4)高度计(5)塞规(6)显微镜(7)投影仪(9)二次元(10)推
拉力计(11)扭力计(12)钳子 (13)荷重仪 (14)其它
附加条件生产说明:
生产确认
审核
首末件检查记录表

□依检查重点略图 □目视 □量仪
判□定依检□查重点略图 □手感 □
□OK □NG □OK □NG
末件
:
________ 判定 □
□目视 □量仪 □手感 □
□OK □NG
A.砂粒异物 B.漆面刮伤 C.油点 D.流漆 E.表面粗糙 F.缩水 G.素材碰刮伤 H.变形 I.没抛亮 J.喷薄 K.咬漆 L.短射 M.毛边 N.
课长:
组长:
品管员:
注:对可选择项, 应在被选中项目前 的“□”内画“√ ”
QR-040-03-A1
首末件检查记录表
制程别:□成型
□装配 □涂装 检查时机:□开机开线 □设修 □模修 □停电 □换班换线 □换产品
□白班 □夜班 年 月日
品名
检查项目
件号
材质/ 规格
首末件别
检查时间
检查项目
判定基准
检查方式 判定结果 异常处置
首件
:
□依检查重点略图 □目视 □量仪
判定 □
□手感 □
□OK □NG
末件
:
□依检查重点略图 □目视 □量仪
判定 □
□手感 □
ห้องสมุดไป่ตู้
□OK □NG
首件
:
□依检查重点略图 □目视 □量仪
判定 □
□手感 □
□OK □NG
末件
:
□依检查重点略图 □目视 □量仪
判定 □
□手感 □
□OK □NG
首件
:
□依检查重点略图 □目视 □量仪
判定 □
□手感 □
□OK □NG
末件
:
□依检查重点略图 □目视 □量仪
判定 □
首末检查记录表

□首件□末件文件编号:
产品名称
产品图号
班次
产品净重
产品毛重
零件号
检查时间
1件
2件
3件
序号
检测项目
检验内容
备注
1
外观
缩痕□裂纹□翘曲□划伤□缺料□顶白□杂质□银丝□气泡□修边□颜色不均□表面光泽不均□
2
色差
在标准光源箱中与色板/上批末件相比,是否有明显色差。
3
试配1
用标准()进行试装,是否出现配合间隙过大
4
试配1
用标准()进行试装,是否出现过紧或过松
5
尺寸
标准值()
实测值()
6
尺寸
标准值()
实8
装配
零件是否组装到位
操作人员
班长确认
质检员
日期
备注:如有质量缺陷,在对应的“□”中打“X”,好的在对应“”中打“”。
首件检查表

彩卡:□字模糊 □色差 □材质不符 □尺寸不符 □内容不符
吸塑:□刮伤 □污渍 □变形 □麻点 □水纹
彩盒:□字模糊 □色差 □材质不符 □尺寸不符 □内容不符 包装
纸箱:□印字不符 □材质不符 □尺寸不符
贴纸:□内容不符 □位置不符 □尺寸不符
胶袋:□尺寸不符 □材质不符 □易破损
结果判定 审核:
□ PASS
□
NG
组长: 检验员:
□ □ □ □ □ □
生产:
外观 线材: □烫伤 □拉花 □起毛 □破皮 □粘胶
调音壳:□缝隙 □刮伤 □粘胶 □破损 □未锁紧 □错位
护套:□破损
□烫伤
□粘胶
咪壳:□缝隙
□胶水外露 □方向错
耳挂:□缝隙
□刮伤
尾扣:□缺料
□破损 □烫伤
喇叭音质: □杂音
□小音 □无音
调音板音质:□杂音 电性能
咪头音质:□杂音
□音小 □啸叫
咪转臂松紧度合适且转动受力合格
耳套装配良好,无过松易脱落、过紧难套现象
耳壳:□划伤 □刮伤 □披锋 □缺料 □喷油不良 □色差
喇叭盖: □缺料 □披锋 □未锁到位
饰片: □刮伤 □移位 □喷油不良 □色差
支架/钢条:□变形
□氧化 □表面粗糙 □电镀不良
头带扣:□螺丝打花
□刮伤 □漏锁螺丝 □扣未锁紧
首件检查表
型号 产品名称
客户 工单号
线别/班次 日期
检验项目
项目要求
检验结果
备注
各组件与材料清单、BOM核对规格一致
规格 各组件与样板核对规格一致
材料应有标示及IQC、IPQC检验合格标签
左右支架伸缩顺畅无支架紧或拉伸不到位现象
首件确认检查表

□ 已执行ROHS规版 本类别序号1□ OK □ NG □ OK □ NG 2□ OK □ NG □ OK □ NG 3□ OK □ NG □ OK □ NG 4□ OK □ NG □ OK □ NG 5□ OK □ NG □ OK □ NG 6□ OK □ NG□ OK □ NG 7□ OK □ NG□ OK □ NG 8□ OK □ NG □ OK □ NG 9□ OK □ NG □ OK □ NG 10□ OK □ NG □ OK □ NG 11□ OK □ NG □ OK □ NG 12□ OK □ NG □ OK □ NG 13□ OK □ NG □ OK □ NG 14□ OK □ NG □ OK □ NG 15□ OK □ NG □ OK □ NG 16□ OK □ NG□ OK □ NG17□ OK □ NG □ OK □ NG 18□ OK □ NG □ OK □ NG 19□ OK □ NG □ OK □ NG 20□ OK □ NG □ OK □ NG 21□ OK □ NG □ OK □ NG 22□ OK □ NG □ OK □ NG 23□ OK □ NG □ OK □ NG 24□ OK □ NG□ OK □ NG 25□ OK □ NG□ OK □ NG 26□ OK □ NG□ OK □ NG生产自检IPQC确认结果IPQC检查详细记录检查内容作业员&作业指导书生产设备、工治具(含在线测试/老化设备)物料(含辅料)制造方法包装纸箱确认,纸箱规格以及外箱字唛物料不可掉落地板上(掉落的物料经IQC确认合格后可用)生产工序排布是否符合《生产工艺流程图》和《质量控制计划》顺序?在线检查岗位检查方法是否正确?物料/半成品摆放或搬运方法是否符合要求?有无导致损坏的隐患?(例如:不允许堆叠,必要的防护等)查看ECN,检查是否按照ECN规定有效执行(如有需注明ECN编号)各工位使用的物料须有IQC检验合格标识物料必须在有效期内:化学胶剂/油剂,看容器的制造日期标签其他物料,以IQC检验日期算有效存储期限(具体以“物料仓储有效期限规定”)特采、挑选物料是否按评审结果执行?并且在物料外箱明确标识?ECN变更的前3~5批次物料,是否在物料包装标明“变更后”字样?物料装配是否符合SOP和样机的要求,不得少件、错件、零件外观/性能完好产品标签内容确认:内部标签与机壳标签、外箱标签同类内容的一致性保证调出测试程序查看测试项目,对照成品质量标准核对不得遗漏,标准值设定须一致检查生产设备和测试设备的参数设置,查看是否符合作业指导书和规范的要求电批/扭力批设置的扭力是否正确(根据SOP规定,参考螺丝规格及装配工件材质),须附上扭矩测试记录工作台与电烙铁是否正确接地?电烙铁温度是否符合SOP 要求(实测值)核对BOM,检查实际用料与BOM规定的一致(包括物料规格、数量、位置号、品牌、丝印(参见物料承认书))装配到整机的物料必须完好并符合SOP要求(物料本体不得破损、紧固程度、机壳内不得有金属异物等等)作业员是否熟悉SOP内容,是否按照SOP操作?机器设备、工治具状态能否正常运作(查看加工动作)?机器设备、工治具是否在开线生产前点检和保养?烧录程序版本是否符合BOM规定?烧录成功是否有状态标识?生产在线测试设备是否定期点检校准?测试程序版本符合SOP和工单要求(出货地/客户特殊要求)环保状态BOM编号检查项目工序现场有与产品装配相匹配的作业指导书?作业文件有经过审核和受控作业员是否有接受对应的装配技能培训,是否持有其工作岗位的上岗证?作业员是否有效佩戴静电手环?着装符合ESD防护要求□ 已执行ROHS规版 本类别序号生产自检IPQC确认结果IPQC检查详细记录检查内容环保状态BOM编号检查项目线缆插接与接线图是否一致?是否导通、极性接反、连接□ 已执行ROHS规版 本类别序号生产自检IPQC确认结果IPQC检查详细记录检查内容环保状态BOM编号检查项目。
品质确认(首件)检查表
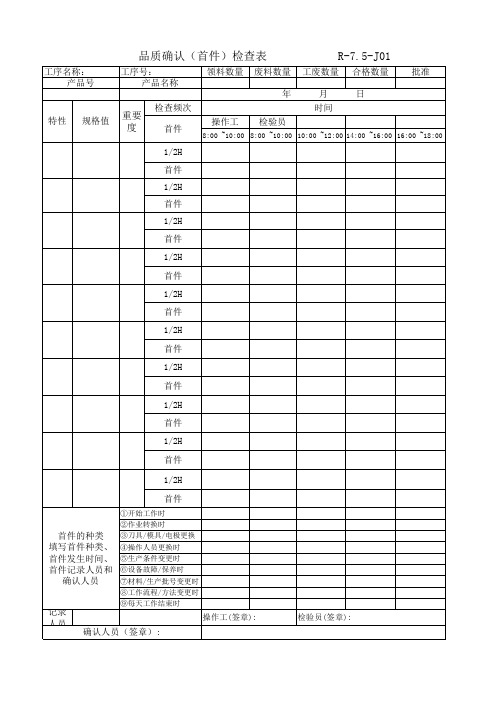
首件的种类 填写首件种类、首 件发生时间、首件 记录人员和确认人 员
①开始工作时 ②作业转换时 ③刀具/模具/电极更换 ④操作人员更换时 ⑤生产条件变更时 ⑥设备故障/保养时 ⑦材料/生产批号变更时 ⑧工作流程/方法变更时 ⑨每天工作结束时
记录人员 确认人员(签章):
操作工(签章):
检验员(签章):
R-7.5-J01
工废数量 合格数量 日 批准
重要 度
检查频次 首件 1/2H 首件 1/2H 首件 1/2H 首件 1/2H 首件 1/2H 首件 1/2H 首件 1/2H 首件 1/2H 首件 1/2H 首件 1/2H 首件 ~10:00 10:00 ~12:00 14:00 ~16:00 16:00 ~18:00
0012h12h品质确认首件检查表r75j01重要开始工作时作业转换时操作人员更换时生产条件变更时每天工作结束时记录人员首件的种类填写首件种类首件发生时间首件记录人员和确认人员刀具模具电极更换设备故障保养时材料生产批号变更时工作流程方法变更时操作工签章
品质确认(首件)检查表
工序名称: 产品号 工序号: 产品名称 领料数量 废料数量 年 特性 规格值 月 时间
首中末件产品检验报表-IATF16949空白表单
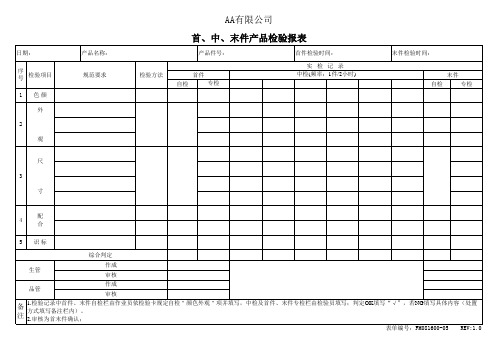
表单编号:FM081600-05 REV:1.0
日期:
序 号
检验项目
1 色颜
外
2
观
尺 3 寸
产品名称: 规范要求
检验方法
AA有限公司
首、中、末件产品检验报表
产品件号:
首件
自检
专检
首件检验时间:
实检记录 中检(频率:1件/2小时)
末件检验时间:
末件
自检
专检
4配 合Βιβλιοθήκη 5 识标综合判定生管
作成 审核
品管
作成 审核
备 注
1.检验记录中首件、末件自检栏由作业员依检验卡规定自检"颜色外观"项并填写,中检及首件、末件专检栏由检验员填写;判定OK填写“√”,若NG填写具体内容(处置 方式填写备注栏内)。 2.审核为首末件确认;
首末件检验记录表

代码号产品名称加工工艺班 组生产日期
检验依据检验时间 时 分
1225
外观
□开机首检 □修模首件 □转产首件□生产参数变更 □材料变更 □其他:□工程图纸 □标准样件 □制程检验标准 □产品标准 □其它判定备注项目检验标准1、产品新开机生产时,由最终工序准备好5个样件置于待检区,并通知IPQC检验员,检查判定合格后生产。
□少孔 □开裂 □变形 □起皱、叠料 □孔毛刺 □边毛刺 □划伤 □压痕 □拉痕 □缺料 □尺寸 □焊渣最终判定结果
□合格 □不合格是否同意量产: □是 □否检验员签名:尺寸
注意事
项填写说明2、检验员判定合格后从样品中随机挑选1个样件,进行首件标识。
并连同巡检记录表一起置于产线最终检查工位。
3、适用范围:产品新开机、开线、修模、变更工艺/参数、变更材料等均需要进行首件检查。
4、检查结果:合格项目打“√”,不合格项目打“×”,无此检查项目打“0”;本表单保留一年。
1、所有项目均需连续检查最少5件。
2、根据质量统计的不良项目进行持续跟进。
首末件检验记录表
首件
末件判定首件信息检查
记录。
- 1、下载文档前请自行甄别文档内容的完整性,平台不提供额外的编辑、内容补充、找答案等附加服务。
- 2、"仅部分预览"的文档,不可在线预览部分如存在完整性等问题,可反馈申请退款(可完整预览的文档不适用该条件!)。
- 3、如文档侵犯您的权益,请联系客服反馈,我们会尽快为您处理(人工客服工作时间:9:00-18:30)。
检查频度 记录频度
Hale Waihona Puke 自 1 2 3主 4
检 5
查 6
记 录 7 8
9
10
日 检查 结果 1.良品数( 2.不良品数( 3.不良原因: )PCS )PCS
积
存
状
A:作业不注意 D:图面错误
况 不良原因类别 B:素材不良 C:刀具设备不良 E:量具不准 F:其 它 原 因
备注
首件、末件、自主检查表
班次: 部品名称 ( )早班 型号 ( )夜班 日期:
班 组: 机床编号: 操 作 者: 年 月 日
部品品番 工序名称 说明: 一人操作多台设备,有几台设备应做几份记录 首 末 判定 件 检 查 末件 实测 判定 首件 实测
检查项目 基准规格 使用量具 重要等级
检查项目 基准规格 使用量具