高速铣削加工工艺
铣削加工工艺步骤
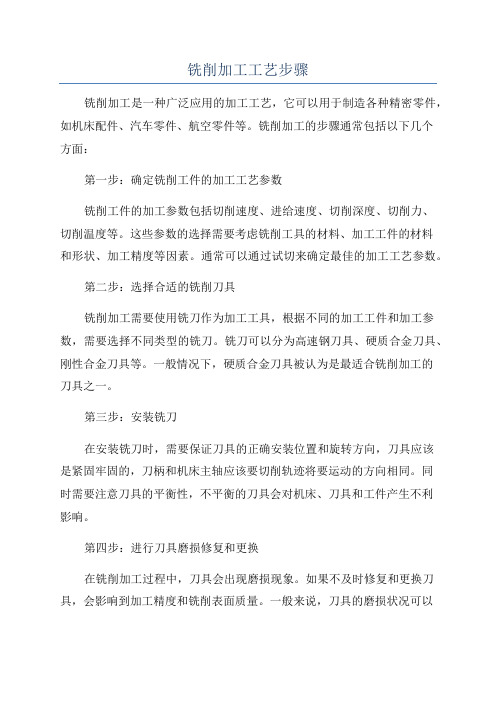
铣削加工工艺步骤铣削加工是一种广泛应用的加工工艺,它可以用于制造各种精密零件,如机床配件、汽车零件、航空零件等。
铣削加工的步骤通常包括以下几个方面:第一步:确定铣削工件的加工工艺参数铣削工件的加工参数包括切削速度、进给速度、切削深度、切削力、切削温度等。
这些参数的选择需要考虑铣削工具的材料、加工工件的材料和形状、加工精度等因素。
通常可以通过试切来确定最佳的加工工艺参数。
第二步:选择合适的铣削刀具铣削加工需要使用铣刀作为加工工具,根据不同的加工工件和加工参数,需要选择不同类型的铣刀。
铣刀可以分为高速钢刀具、硬质合金刀具、刚性合金刀具等。
一般情况下,硬质合金刀具被认为是最适合铣削加工的刀具之一。
第三步:安装铣刀在安装铣刀时,需要保证刀具的正确安装位置和旋转方向,刀具应该是紧固牢固的,刀柄和机床主轴应该要切削轨迹将要运动的方向相同。
同时需要注意刀具的平衡性,不平衡的刀具会对机床、刀具和工件产生不利影响。
第四步:进行刀具磨损修复和更换在铣削加工过程中,刀具会出现磨损现象。
如果不及时修复和更换刀具,会影响到加工精度和铣削表面质量。
一般来说,刀具的磨损状况可以通过刀具的质量控制指标来判断,切削力、加工表面质量的变化等也可以用来判断。
第五步:进行铣削加工操作在进行铣削加工操作时,需要确定加工工件的位置和机床主轴的转速。
同时,需要根据加工要求进行铣削刀具的进给和切削运动,实现加工表面的质量和精度要求。
在加工过程中,需要不断监测刀具的磨损和加工表面质量的变化,及时进行修复和调整。
第六步:完成后处理工作铣削加工完成后,需要进行后处理工作,包括加工表面的清洁和润滑等。
同时还需要对加工工艺参数、加工实际情况和工件质量进行分析和总结,为今后的铣削加工提供参考和借鉴。
高速加工介绍

高速加工一、高速加工概述新一代的机床性能大大改进,主轴转速可以轻松达到20 000r/min以上,进给速度可以达到30 000mm/min,大大提高了加工效率以及设备的利用率,这更需要使用者研究规划工艺、优化程序、选择合适的刀具。
高速加工的概念是伴随着机床设备的发展不断更新的。
一般采用高的主轴转速、高的进给速度、较小的背吃刀量,其切削速度伴随刀具材料的超硬耐磨性的发展而不断提高。
通过了解高速加工的特点,虽然不一定能达到高速加工的要求,但在实际生产中采用高速加工的概念指导加工,还是可以取得一定效果的。
二、高速加工工艺1.高速加工程序特点:(1)全程无空刀路、无抬刀,都是在有效切削零件。
(2)所有刀路流畅,都是圆滑过渡,无拐点。
(3)刀路步距均匀、梳密一致,效率高。
(4)路径最短。
这符合优质刀路的特点,因此该加工程序很好。
2.发动机缸体高速铣削工艺发动机缸体高速铣削工艺的要求。
除了发动机缸体高速铣削工艺对精度、计算稳度的要求极高之外,其在使用中还有一些特殊的要求,主要集中在以下几点:首先发动机缸体高速铣削工艺在使用中不能和任何工装及工件发生碰撞;其次加工刀具在轨迹上必须保障绝对的平滑,以及十分均匀的切削深度;最后在发动机缸体高速铣削工艺使用中,其导致的设备振动必须控制在一定范围内。
3.发动机缸体高速镗孔工艺发动机缸体高速调头镗孔工艺的优势。
高速调头镗孔工艺的优势主要几种在三个方面,其一为在镗孔中镗杆较短,因此在切削速度上有所提升;其二为因为镗轴伸长较短,因此在精度方面更有保障;其三为切削设备占用空间较小,因此工作人员的工作活动空间更大,工作更为直观、安全。
三、高速加工刀具1.刀具的要求:高硬度、高耐磨、高强度和韧性、高耐热性、良好的工艺性。
(1)硬质合金涂层刀具最常用(2)TiC(TiN)基硬质合金金属陶瓷(3)陶瓷刀具耐热耐磨但强度韧性差(4)立方氮化硼刀具CBN 一般用来精加工高硬度淬火钢、高温合金、工具钢、高速钢,耐热耐磨但脆性大、韧性差(5)聚晶金刚石刀具PCD 不宜加工铁及其合金高速加工刀具刀柄:采用1:10 短锥柄代替传统的7:24 长锥柄成为发展趋势。
高速铣削加工的刀具轨迹编程工艺设计
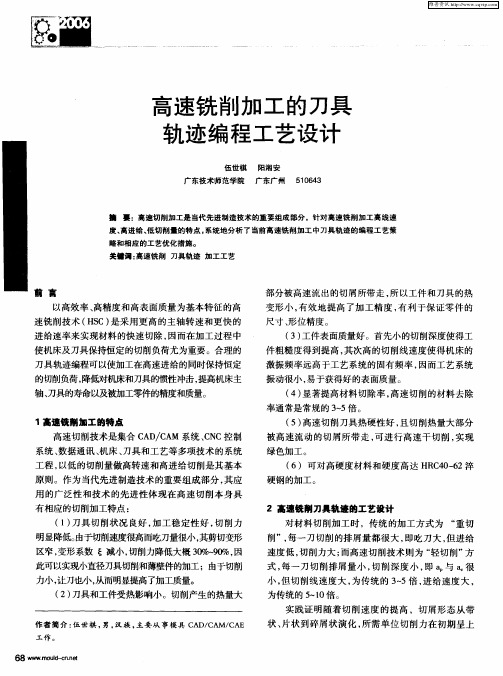
工程 , 以低 的切削量做高转速和高进 给切削是其基本 原则。作为当代先进制造技术的重要组成部分 , 其应
用 的广泛性和技术的先进性体现在高速切削本身具 有相应的切削加工特点 :
( ) 具切 削状 况 良好 , 工 稳 定 性 好 , 削 力 1刀 加 切
( )可对高硬度材料和硬度高达 H C 0 6 6 R 4 —2淬
维普资讯
f t 具工程 F模
2 0 .o8总 6 0 6N . 5期
升趋势 , 而后急剧下降 , 这说 明高速切 削 比常规切削 轻快 , 两者的机理不 同 , 因此其刀轨的工艺设计也有
其特 点 。
22 高 速铣 削 刀具 轨 迹的 工艺 规划 .
明显降低。 由于切削速度很高而吃刀量很小, 其剪切变形 区窄 , 变形系数 专减小, 切削力降低大概 3% ̄0 因 0 9 %, 此可以实现小直径刀具切削和薄壁件的加工 ;由于切削 力小, 让刀td , e, 从而明显提高了 加工质量。 () 2 刀具和工件受热影响小。切削产生的热量大
硬钢 的加工 。 2 高速铣 削 刀具轨 迹 的工艺 设计
对材料切削加工时 ,传统 的加工方式为 “ 重切 削”, 每一刀切削 的排屑量都很大 , 即吃刀大 , 但进给
速度低 , 切削力大; 而高速切削技术则为 “ 轻切 削” 方 式, 每一刀切削排屑量小 , 切削深度 小 , £ 与 a很 即 L e Ⅱ
时, 针对 圆刀 片和球 头 铣 刀 , 应注 意 有效 直径 的概 念 。 ( 2) 相邻 的两 层 切 削刀 路 之 间通 过 圆 滑 刀路 过
图 1刀 路 之 间通 过 圆弧 进 行 过 渡
渡, 既有效 的解决了刀路平滑的要求 , 又符合螺旋下
先进制造工艺--高速切削技术
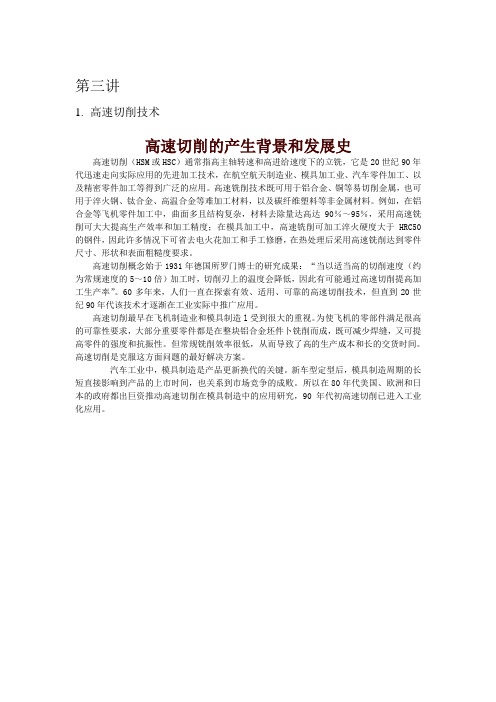
第三讲1.高速切削技术高速切削的产生背景和发展史高速切削(HSM或HSC)通常指高主轴转速和高进给速度下的立铣,它是20世纪90年代迅速走向实际应用的先进加工技术,在航空航天制造业、模具加工业、汽车零件加工、以及精密零件加工等得到广泛的应用。
高速铣削技术既可用于铝合金、铜等易切削金属,也可用于淬火钢、钛合金、高温合金等难加工材料,以及碳纤维塑料等非金属材料。
例如,在铝合金等飞机零件加工中,曲面多且结构复杂,材料去除量达高达90%~95%,采用高速铣削可大大提高生产效率和加工精度;在模具加工中,高速铣削可加工淬火硬度大于HRC50的钢件,因此许多情况下可省去电火花加工和手工修磨,在热处理后采用高速铣削达到零件尺寸、形状和表面粗糙度要求。
高速切削概念始于1931年德国所罗门博士的研究成果:“当以适当高的切削速度(约为常规速度的5~10倍)加工时,切削刃上的温度会降低,因此有可能通过高速切削提高加工生产率”。
60多年来,人们一直在探索有效、适用、可靠的高速切削技术,但直到20世纪90年代该技术才逐渐在工业实际中推广应用。
高速切削最早在飞机制造业和模具制造l受到很大的重视。
为使飞机的零部件满足很高的可靠性要求,大部分重要零件都是在整块铝合金坯件卜铣削而成,既可减少焊缝,又可提高零件的强度和抗振性。
但常规铣削效率很低,从而导致了高的生产成本和长的交货时间。
高速切削是克服这方面问题的最好解决方案。
汽车工业中,模具制造是产品更新换代的关键。
新车型定型后,模具制造周期的长短直接影响到产品的上市时间,也关系到市场竞争的成败。
所以在80年代美国、欧洲和日本的政府都出巨资推动高速切削在模具制造中的应用研究,90年代初高速切削已进入工业化应用。
图16 高速切削在生产应用中的发展历程图17 采用高速切削后产品质量提高的历程a一硬质合金切钢 b一硬质合金切铸铁c—CBN切铸铁图16是德国宝马公司(BMW)采用高速切削的历程。
高速切削加工技术

广东工业大学研究了高速主轴系统和快速进给系统 东北大学研究了高速磨削技术 成都工具研究所研究了高速切削刀具的发展和产业化等 尽管我国高速切削加工技术的研究还有待于全面深入,但 通过我国科技工作者的艰苦努力,高速切削加工和高速切 削机床的基础理论研究取得了令人鼓舞的成就,对促进我 国高速切削加工技术的发展起到了重大作用。
➢ 以切削速度和进给速度界定:高速加工的切削速度和 进给速度为普通切削的5~10倍。
➢ 以主轴转速界定:高速加工的主轴转速≥10000 r/min
➢ 高速切削是个相对的概念,是相对常规切削而言。高 速切削包括高速软切削、高速硬切削、高速干切削和 大进给切削等。超高速加工的切削速度范围因不同的 刀具材料、工件材料和切削方式而异,目前,高速切 削的高速范围国内外专家尚无共识。
➢ 我国高速切削刀具材料已有很大的发展,特别是陶瓷刀具,而 且初步具备了开发高速切削刀具的能力 ➢ 但金刚石、立方氮化硼、TiC(N)基硬质合金(金属陶瓷)、涂层刀 具和超细晶粒硬质合金刀具的性能、品种与国外差距很大。 ➢ 高速切削刀具制造技术也相对落后,还没有形成自己特色的高 速切削刀具制造体系。
高速加工的切削速度范围
➢ 高速加工切削速度范围因不同的工件材料而异 ➢ 高速加工切削速度范围随加工方法不同也有所不同
➢ 车削: 700-7000 m/min ➢ 铣削: 300-6000 m/min ➢ 钻削: 200-1100 m/min ➢ 磨削: 50-300 m/s
塑料 铝合金 铜 铸铁 钢 钛合金 镍合金
10
100
1000
切削速度V(m/min)
高速与超高速切削速度范围
10000
➢ 自从Salomon提出高速切削的概念以来,高速切削技 术的发展经历了高速切削理论的探索、应用探索、初 步应用和较成熟应用等四个阶段。
高速铣削与电加工工艺组合应用
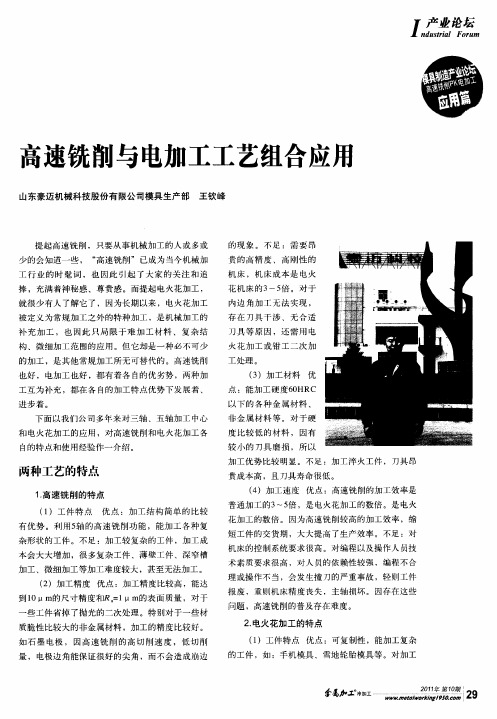
加 普 及 ,加 工效 率 会 更 高 ,质量 会 更 好 ,成 本 会 更
低 ,从而满足高精度、高复杂零件的加工。
2电火花加 工技 术 .
图5 N示 为加 工 中心 、电火花 、测量一豪迈公司从1 9 年开始设计制造轮胎模具 97
电火花 机 床 以 来 ,推 动 了我 国轮 胎 模具 制 造 的
具制造 商 ,由8 年前的轮胎模具 进 口,到现在 口模具 ,并且 出口量连年 以翻番的速度增长。
,
图5 加工中心、电火花、测量一体化的 自动化生产单元
中 国 整个 轮 胎 模具 制 造 行 业 都 在 大规 模 地 应
高精 度夹具 在 电火花 加工 中的应 用 、普及 , 对 提 高 电火 花加 工 的 自动化 奠 定 了基 础 。3 R、
图2 是五轴加工中心力
破坏 了工件原有材料的特性 。因电火花加工是 电能 转热能会产生大量的热量 ,需用非导 电加工液对工 件和 电极冷却 ,并且把 间隙放电产生的微细颗粒带
走 。在 大 电流 加 工 时加 工 液 的温 度 在4 ~8  ̄ 0 0C,影 响机 床精 度和 工 件精 度 。
0
高速铣削与电加工工艺组合应用
山东豪迈 机械 科技股份 有 限公 司模具 生产部 王钦峰
提起高速铣削 ,只要从事机械加工的人或多或
少 的会 知 道 一 些 , “ 速 铣 削 ” 已成 为 当今 机 械加 高 工 行 业 的 时 髦 词 ,也 因 此 引 起 了 大 家 的 关 注 和 追 捧 ,充满 着 神 秘 感 、尊 贵 感 。而提 起 电火 花 加 工 , 就 很 少 有 人 了解 它 了 ,因为 长 期 以来 , 电火 花加 工 的 现 象 。 不 足 :需 要 昂
高速铣加工工艺
高速铣加工工艺使用高速加工技术,不仅要有适合高速加工的设备—高速加工中心,还要选择适合进行高速加工的刀具.和专业的高速编程软件如powermill编程软件并选用合适的高速铣加工工艺,才能发挥最大的效益.刀具的选择(1)刀柄的选择:高速加工要选用HSK系列的刀柄,该刀柄采用锥面和端面双重定位,刚性好、精度裔.可满足日益发展的离速和高精度加工需求。
同时选用热缩式刀夹可以获得更高的同心度和平衡性能。
(2)刀具几何参数的选择:高速切削加工切削力及扭矩较小,可以先用较大的后角较尖锐的切削楔,例如在切削45钢时后角a=12′^-16,以便降低工件材料在后刀面的接触摩擦效应,有利于提高刀具寿命。
(3)刀具材料的选择:切削钢件使用的硬质合金刀具必须具有很高的热硬度.因此Tic含最较高的P类合金优于we含量较高的K类硬质合金。
与硬质合金相比.陶瓷刀具的寿命要高得多,但它性脆,导热能力差,只适用于小的背吃刀量和进给量。
使用涂层硬质合金刀具,如物理气相沉积(PVD)方法涂段的TiN涂层刀具,可以大幅度提高刀具的抗磨损能力,从而提高刀具寿命.根据切削速度的不同,可以达到50%-200%之间。
选择合适的切削用t使用高速加工技术,选择合适的切削用最和进给量,不仅能有效地提高加工效率,同时有利于廷长刀具的使用寿命,从而达到最佳的效益.(1)进给量的选择:在进给量增大时,刀具寿命先是上升,而在达到临界值后迅速下降。
这是因为,初始阶段,由于刀具在工件的切阴次数减少,之后进给童增大引起的切削力增加.工件切削路径变长和前刀面接触温度上升,造成刀具前刀面月牙洼磨损,使刀具寿命下降。
(2)背吃刀量的选择:铣刀的轴向背吃刀量对刀具寿命影响较少.在加工过程中.铣削宽度应当尽最选得大些。
相反,径向背吃刀量对刀具寿命的影响很大.后者随前者增大而下降。
一般推荐径向背吃刀量为铣刀直径的5%-100/0. 切削液对刀具寿命影响有限,这是因为铣阴主轴高速旋转,切削液若要达到切削区,首先要克服极大的离心力,即使它克服了离心力进入切削区,也可能由于切削区的高沮而立即燕发,切削效果很小甚至没有:同时切削液会使I1具刃部的温度橄热变化,容易导致裂纹的产生。
高速铣削工艺优化研究在数控加工中的应用
sr eacr yo cli sl. e apitni eapet hn,e abi t i d2 u sh cu c c u n r usf rp lao xm l e i t s it oo i z et a f  ̄ a ge t t ci n t A a g h c il f p m e y
【 摘
要】 以降低数控 实践教学成本 , 高加工效率为 目 , 提 标 构建 了高速铣 削加工参数多 目 标优化
方案 , 合理设 定 了各类 约束 条件 , 并利 用复合形 法进 行优化 。具体 分析 了数控铣 削加 工切削量 、 径 背吃 刀量等较 主要 的切 削 用量的优 化选择 进 行 了探 讨 , 为合
关键 词 : 优化 , I 实验教学 ; 应用 ; 高速铣 削
【 bt c】no etr ueh o Ce em n le hn dipoem h i c ny2 A s at / r ro e c t csoN x r et a i a r a in e i c r d d e tf p i atc g n m v c n gf e i f
K yWod : pi zt nE p r na T ah gA pi t nH g ed ln e r s t ai ;x ei tl eci ; p lai ; i S e l g o mi o me n c 0 h p Mii
机 械 设 计 与 制 造
Ma h n r De in c iey sg 文章编号 :0 1 39 (0 2 0 — 0 0 0 10 — 9 7 2 1 )7 0 9 — 2 & Ma u a t r n fcue
第 7期 21 0 2年 7月
高速铣 削工艺优化研 究在数控加工 中的应 用 术
高速铣削加工技术概述
1 引言
高速铣削加工 不但具有加工 速度高 以及 良好 的加工精度
和表 面质量 , 而且与传统 的切削加 工相 比具有温 升低 ( ̄ / II J
降低 了 3 %,刀具 的切 削寿命提 高了 7 %。还 可加工淬硬零 0 0
件, 许多零件一次装夹可完成粗 、 半精和精加 工等全部 工序 , 对 复杂型面也 能达 到零件表面质量要求 , 进而提高 了加工生产率
20 0 8年 1 1月
广 西轻 工 业
G A G JI N Io IH D sR U N Ⅺ (瓜 A FLG TI u T Y ) N 机 械 与 电 气
第 1 期( 1 总第 1 0 ) 2 期
高 速铣 削 加 工技 术概 述
高发 伟
( 东 东阳 光铝业 股份有 限公 司, 东 韶 关 5 7 1 广 广 1 2) 2
21 可部分替代某些工艺 .
高 速切削时 的切 削力 小 , 有较高 的稳 定性 , 可加工高 质量
的薄壁零件 。 采用 分层铣削 的方法 , 可切削出壁厚 02 m, .r 壁高 a 2 rm的薄壁零件 。刀刃和工件的接触 时间非 常短 , 0 a 避免 了侧
壁 的变形 。
如 电火花加工、 磨削加工等高强度和高硬度 加工也是 高速
切 削的一大 特点 ,高速切削 已可 加工硬度 达 HR 6 C 0的零件。
3 高速 铣削加 工在 螺纹 加工 中的应用
用高速铣削刀盘加工螺纹 的方法又称旋风铣削法 , 加工 其 表面是刀齿旋转形成 的回转表 面在不同连续位置的包络面 , 它
一
采用带涂层的硬质合金刀具加工模具 , 直接将 淬硬工具钢一次
进制造技术领域重要 的研究方 向之一【3 1】 .。 长期以来 , 们对模具 的加工一 直采 用铣 削——磨削或者 人
高速铣削工艺在模具加工中的应用
工 淬硬 后 的模具 , 取代 电火 花 加工 和磨 削 加 工 。可 以 2 高速铣削对加 工工艺的要求
{ 电极加 工 l
t
毛坯退火 卜 _ 叫租加工 卜 叫半精加工
毛坯淬火 H 粗加工 H 半精加工 H 精加工I-局部手工打磨 -l ,
经济效益不好 。高速切削技术在模具工 理 、 削或 电火 花 加 工 , 后 手 工 打磨 、 光 , 样 使 产效率很低 , 磨 最 抛 这
主 得 加工 周期 很 长 。特 别 是手 工 加 工 时 间 , 占整个 加 业 中的应 用 更 是凤 毛麟 角 , 要 原 因是 对 高 速加 工技 要
l 引言
大大减少加工时间 , 简化加工过程 , 降低成本 , 具有十
高速 切 削技 术 模 具 是制 造业 中用 量 大 、影 响 面广 的 工具 产 品。 分广 阔 的应 用 前 景 。在 工 业 发 达 国家 , 极 模 具 技术 是 衡量 国家 的科 技 水平 的重 要 标 志 之一 , 没 在模 具 制 造业 已经 得到 广 泛 的 应 用 , 大地 提 高 了模 所 有高水平的模具就没有高质量的产品。由于模具型面 具 的生 产效 率 。图 l 示 为传 统 加 工方 式与 高速 加工
关键 字 :高速铣 削 ; 工策略 ; 工特征 加 加
App ia in fHi h- e d M iln c no o y lc to o g Sp e li g Te h l g i e & M od M a f c ur n Di J nu a t e 【 src]h pl ao f ih sedmiigtcnl yhdaosdarvlt nr hne AbtatT eapi tno g-pe ln hoo a rue oui aycag ci h l e g e o
- 1、下载文档前请自行甄别文档内容的完整性,平台不提供额外的编辑、内容补充、找答案等附加服务。
- 2、"仅部分预览"的文档,不可在线预览部分如存在完整性等问题,可反馈申请退款(可完整预览的文档不适用该条件!)。
- 3、如文档侵犯您的权益,请联系客服反馈,我们会尽快为您处理(人工客服工作时间:9:00-18:30)。
4
高速铣削工艺相对常规加工具有以下优点:
1 2 3 4
提高生产率
改善工件的加工精度和表面质量 实现整体结构零件加工
有利于加工薄壁零件和高强度、高硬度 脆性材料
1
高速铣削工艺条件 对机床软硬件的要求
电主轴 如直线电机驱动装置
具有前馈控制、位置度高分辨率、自适应 控制、NURBS插补功能,配以速加工的 CNC/CAM软件,具有螺旋三轴联动、斜率 分析等功能。
高速铣削加工工艺
高速铣削的基本概念
高速铣削工艺条件 高速铣削工艺要点
高速加工采用全新的加工工艺 , 从刀具、切削参数、 走刀路径的选择及程序的编制,都不同于传统的加工。
1
零件精细结构部位的加工 难加工材料的加工
微小结构的铣削加工
4
2
薄壁类零件的加工 模具零件的加工
3
5
高速铣削的基本概念
所罗门曲线
1 2
保持切削载荷平稳
最小的进给率损失
3ห้องสมุดไป่ตู้
最大的程序处理速度
刀具路径必须符合高速铣削要求
1 2 3 4 5
进退刀采用斜坡和螺旋方式
大量采用分层加工
金属切除率尽量保持恒定 避免急剧变化的刀具运动
满足等量切削和等载荷切削条件
高速铣削加工用量的确定主要考虑加工效率、加工 表面质量、刀具磨损以及加工成本。 不同刀具加工不同工件材料时,加工用量会有很大 差异,目前尚无完整的加工数据。
高速铣削必须充分关注有效切削速度和浅深度铣削。
高速铣削在切削区产生很高的温度,冷却液在接近 切削刃处汽化,对切削区域几乎没有冷却作用,反 而会加大铣刀刃在切入切出过程的温度变化。 大部分情况下高速铣削不建议使用冷却液,常采用 压缩空气冷却、油雾冷却或水雾冷却,冷却方式以 通过主轴的刀具内冷效果最好。
高速切削( HSM )一般是指在主轴高转速和 高进给率下的立铣加工,切削速度和进给率至少 是普通切削的 5~10 倍。
1
HSM 不是简单意义上的高速切削
高速切削并非一定要高转速主轴切削
2
3
在小尺寸零件的粗加工到精加工,及任何尺寸 的超精加工中, HSM 意味着高生产率切削
主要应用在采用 BT40 刀柄的加工中心上。
高速主轴单元 快速进给和高加/ 减速的驱动系统
高性能的CNC控制 系统
2
刀具要求
硬质合金、涂层刀具、金属陶瓷等 小直径铣刀一般用整体式,大直径 铣刀一般用机夹式
刀具材料
刀具结构
高性能的CNC控 当机床最高转速达到15000r/min时, 制系统 通常需要采用HSK高速铣刀刀柄。
高速铣削工艺要点 高速铣削工艺必须考虑 3 个关键问题: