铣削铝合金加工工艺
铝合金零部件高速铣削工艺研究

铝合金零部件高速铣削工艺研究摘要:本文研究了铝合金零部件的高速铣削工艺,研究内容涵盖了刀具选择、切削速度、进给量、切削深度以及冷却液的选择等方面。
根据铝合金较低的硬度和加工表面要求,选用了单刃、双刃或多刃实心刀具进行高速铣削,并平衡了切削速度、进给量和切削深度之间的关系。
在冷却液的选择方面,建议使用水溶性切削液或喷雾切削液以降低加工温度和摩擦力,并防止铝屑和必要零件产生热膨胀和变形等问题。
通过实验验证了所提出的高速铣削工艺的可行性和有效性。
关键词:铝合金;零部件;高速铣削工艺引言:铝合金是一种轻质高强度材料,广泛应用于航空、汽车、电子等领域中的零部件制造。
高速铣削是一种有效的铝合金加工方法,可以在保证加工质量的前提下提高生产效率。
本文旨在研究铝合金零部件的高速铣削工艺,包括刀具选择、切削速度、进给量、切削深度以及冷却液的选择等方面。
通过对每个因素的分析,确定了高速铣削的工艺参数,最终实现了对铝合金零部件的高速铣削。
一、合理选择刀具在铝合金高速铣削中,刀具的选择是非常重要的。
由于铝合金是一种相对较软的材料,因此可以选择单刃、双刃或多刃实心刀具。
对于单刃刀具而言,由于只有一个刃口,其切削力较大。
然而,单刃刀具比较容易进行切削力的控制,适用于工件形状复杂的加工。
此外,单刃刀具相对简单,对机床的稳定性要求较低。
双刃刀具则具有两个刃口,能够分摊切削力,因此能够减小每个刃口的切削力。
这样一来,双刃刀具在加工过程中对机床的稳定性要求更高。
双刃刀具适用于需要较高精度和表面质量的加工。
多刃实心刀具是指具有多个刃口的刀具,它能够进一步减小切削力,并提高加工效率。
多刃实心刀具适用于大批量生产和高效率加工的情况下。
然而,多刃实心刀具的设计要求更高,对机床的稳定性和刚性要求也更高[1]。
因此,在选择刀具时,需要根据具体的加工要求、工件形状和尺寸、加工精度要求等因素综合考虑。
单刃刀具适用于复杂形状的加工,双刃刀具适用于高精度和表面质量要求较高的加工,而多刃实心刀具适用于大批量和高效率的加工。
铝合金工艺流程

铝合金工艺流程1.1原料准备那可是相当关键的。
咱得先把铝合金的原料找齐喽,就像厨师做菜得先备好食材一样。
这原料的质量直接决定了最后铝合金产品的好坏。
那些铝合金原料,主要是铝锭啦,还有可能加入一些其他的金属元素,像镁、硅之类的,就好比做菜时加的各种调料,为的是调出不同的“口味”,也就是让铝合金具备不同的性能。
1.2熔炼是个大环节。
把这些原料一股脑儿地放进熔炉里,那熔炉就像个大熔炉(哈哈,这词儿有点意思),熊熊烈火烤着。
这个时候温度得控制好,不能太高也不能太低,就像走钢丝一样得小心翼翼。
温度太高了,原料可能就烧过头了,就像煮饭煮糊了一样,铝合金的质量就完蛋了;温度太低呢,原料又熔不完全,就好比那夹生饭,也不行。
二、铝合金成型的那些事儿。
2.1铸造可是个技术活。
熔好的铝合金液得倒进模具里,这就像是把水倒进特定形状的容器里,让它变成咱们想要的形状。
这模具就像个魔法盒,铝合金液进去之后就被塑造成各种各样的模样。
不过在铸造的时候,得注意让铝合金液均匀地流进模具的每个角落,不然就会出现有的地方厚有的地方薄的情况,就像一个人穿的衣服,这儿多一块布那儿少一块布,那多难看呀。
2.2挤压这个过程也很有趣。
有些铝合金产品是通过挤压做出来的。
就好比把面团从一个模子里挤出来一样,把铝合金通过特定的挤压机和模具,挤出咱们想要的形状,像铝合金的管材、型材啥的。
在挤压的时候,压力的控制很重要,压力太大了,可能会把模具挤坏,这就好比是用力过猛把东西捏碎了;压力太小呢,铝合金又挤不出来或者形状不达标,就像挤牙膏的时候没使上劲,牙膏出不来或者出得歪歪扭扭的。
2.3锻造对于一些对强度要求比较高的铝合金产品来说是个好办法。
就像是打铁一样,用锤子一下一下地把铝合金敲打成想要的形状。
这个过程中,每一下的力度和位置都很有讲究,要是乱敲一气,那铝合金的内部结构就会被破坏,就像一个房子的地基没打好,房子肯定不结实。
三、铝合金的后续加工与处理。
3.1机械加工是必不可少的。
铝合金加工工艺

铝合金加工工艺铝合金加工工艺:1、铣削加工:铣削加工是利用机床上安装的刀具削减铝材表面的工艺,它包括立铣、侧铣、表面铣、槽铣等。
可以对材料做出定位精度高的平面、孔和槽,可以进行沉陷型零件的加工,也可以按照图纸要求使零件规格紧凑,加工效率高、精度高、表面光洁度好。
2、数控攻牙:数控攻牙是一种用于机械装配过程中螺纹用齿丝或牙形螺母的精密攻牙加工工艺。
2.1、数控攻牙:数控攻牙是一种具有一定容差范围的攻牙加工,可以用于各种铝合金零件,以确保零件的装配及使用的正确性,改善了零件的可靠性和使用寿命。
2.2、冷冲压成型:冷冲压成型是把金属在低温下,利用模具的受力形状和它们之间的摩擦,把金属齿轮状件加工到模具形状,可以用于加工各种复杂形状的铝合金零件,可以有效提高零件的加工精度,减少加工周期,并具有成型速度快的特点。
3、冲孔加工:冲孔加工是一种加工精密孔的工艺,用于多种零件模具或机械零件,可以进行各种方孔、圆孔、排列孔等复杂形状的冲孔加工,比直接用切削加工孔的质量更高,精度也更高。
4、冲切加工:冲切加工是指利用压床和冲程机等特种冲击机械,将铝合金材料用强力冲击挤出成品零件的工艺,可以进行多次冲压,以最小的浪费来实现低成本的加工,冲击力和冲击频率高,加工精度高。
5、钻削/纵鑽/倒角加工:钻削/纵鑽/倒角加工是一种利用机械工具将高硬度物质在精度高的条件下实现孔、槽、倒角等加工的技术,特别适用于在铝合金材料上进行精密精细加工,它能满足零件加工外形尺寸及表面精度要求。
6、火花机:火花机加工是通过火花机把磁通传输到执行机构上,然后发射出火花,利用火花能量有效地把铝合金材料切割、修整,可以较快地实现型形和尺寸的精确加工,表面光洁度好,加工效率高,精度能满足高度要求。
7、冲压:冲压是把金属在低温下,利用模具的受力形状、把金属齿轮状件加工到模具形状的工艺,适用于各种铝合金材料,可以实现高效率的操作,模具制作精度高,产品尺寸、形状精度高,能够满足高准确度要求。
3A21—F铝合金板材在数控加工中防止变形的工艺措施
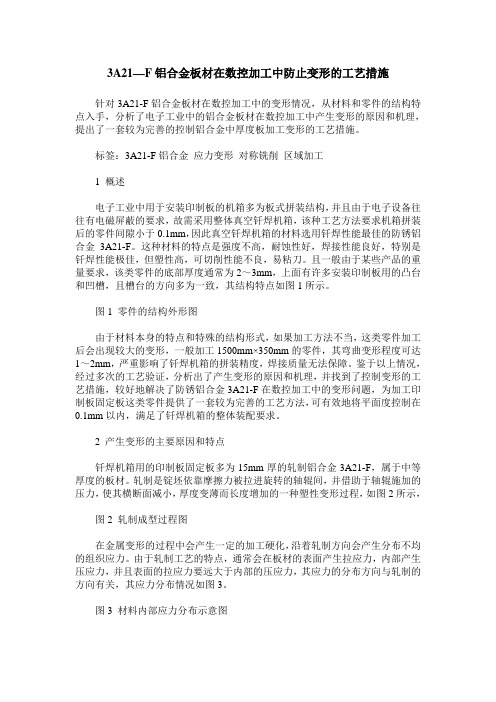
3A21—F铝合金板材在数控加工中防止变形的工艺措施针对3A21-F铝合金板材在数控加工中的变形情况,从材料和零件的结构特点入手,分析了电子工业中的铝合金板材在数控加工中产生变形的原因和机理,提出了一套较为完善的控制铝合金中厚度板加工变形的工艺措施。
标签:3A21-F铝合金应力变形对称铣削区域加工1 概述电子工业中用于安装印制板的机箱多为板式拼装结构,并且由于电子设备往往有电磁屏蔽的要求,故需采用整体真空钎焊机箱,该种工艺方法要求机箱拼装后的零件间隙小于0.1mm,因此真空钎焊机箱的材料选用钎焊性能最佳的防锈铝合金3A21-F。
这种材料的特点是强度不高,耐蚀性好,焊接性能良好,特别是钎焊性能极佳,但塑性高,可切削性能不良,易粘刀。
且一般由于某些产品的重量要求,该类零件的底部厚度通常为2~3mm,上面有许多安装印制板用的凸台和凹槽,且槽台的方向多为一致,其结构特点如图1所示。
图1 零件的结构外形图由于材料本身的特点和特殊的结构形式,如果加工方法不当,这类零件加工后会出现较大的变形,一般加工1500mm×350mm的零件,其弯曲变形程度可达1~2mm,严重影响了钎焊机箱的拼装精度,焊接质量无法保障。
鉴于以上情况,经过多次的工艺验证,分析出了产生变形的原因和机理,并找到了控制变形的工艺措施,较好地解决了防锈铝合金3A21-F在数控加工中的变形问题,为加工印制板固定板这类零件提供了一套较为完善的工艺方法,可有效地将平面度控制在0.1mm以内,满足了钎焊机箱的整体装配要求。
2 产生变形的主要原因和特点钎焊机箱用的印制板固定板多为15mm厚的轧制铝合金3A21-F,属于中等厚度的板材。
轧制是锭坯依靠摩擦力被拉进旋转的轴辊间,并借助于轴辊施加的压力,使其横断面减小,厚度变薄而长度增加的一种塑性变形过程,如图2所示,图2 轧制成型过程图在金属变形的过程中会产生一定的加工硬化,沿着轧制方向会产生分布不均的组织应力。
典型薄壁零件数控铣削加工工艺

典型薄壁零件数控铣削加工工艺随着制造业的发展,数控加工技术逐渐成为最常用的加工方法之一。
而在数控加工领域中,数控铣削技术是常见的加工方法之一。
本文将介绍典型薄壁零件数控铣削加工工艺,包括工艺准备、加工流程、刀具选择和切削参数等方面的内容。
一、工艺准备1.1 材料选择因为薄壁零件通常是轻型结构件,所以材料一般选择铝合金、镁合金、不锈钢等轻质、高强度的材料。
1.2 工件夹紧在加工薄壁零件时,一定要保证工件夹紧牢固。
否则,易造成加工过程中工件的振动或位移,导致加工精度降低。
1.3 加工精度要求由于薄壁零件的厚度较小,所以在加工过程中要保证加工精度高,以防加工出错或造成损失。
二、加工流程2.1 预处理将所选材料进行预处理,包括去表面氧化层、去毛刺等。
2.2 下刀编制好数控加工程序后,进行下刀和切割。
2.3 清洗清洗零件,以便检查和测试。
2.4 检测检测零件的精度、结构、特性等。
如果不合格,要重新加工。
进行表面处理,包括抛光、喷漆、防锈等。
三、刀具选择在加工薄壁零件时,需要选用比较特殊的刀具。
常用的刀具主要包括切割刀具、削铣刀具、倒角刀具、钻头等。
3.1 切割刀具为了保证零件表面的质量和精度,需要选用切割刀具。
切割刀具的作用是将零件中的材料割离,形成所需的几何形状。
在进行倒角时,需要选用倒角刀具。
倒角刀具能够将薄壁零件边缘处的角进行倒角处理,使其具有更好的平滑度和美观度。
3.4 钻头在加工薄壁零件时,常常需要进行孔加工。
钻头是一种常用的刀具,在加工孔时经常被使用。
四、切削参数在加工薄壁零件时,需要注意切削参数的选择。
切削参数对加工质量起着重要的影响。
4.1 切削速度切削速度是指刀具在切割过程中移动的速度。
切削速度过快,容易导致刀具磨损、表面质量差等问题。
切削速度过慢,加工效率低下。
切削深度是指刀具在一次切削过程中切入材料的深度。
切削深度过大,会导致切屑对切削影响的加重,影响加工质量和效率。
总之,在加工薄壁零件时需要注意工艺准备、加工流程、刀具选择和切削参数等方面的内容。
铝合金材料的铣削加工工艺浅析

维普资讯
进给运 动的切削 加工 方法 。他通 过 铣 刀刀 刃 的切 割和刀 面 的推 挤 , 工件 表 层 的金 属 材 料 变 为 切 把 屑。 由于工件材料 不 同 , 削条件 不 同 , 切 切削 过 程
中的变形 也 不 同 , 因而 产 生不 同 的切 屑 。按 切 屑
件的零点( x坐标) 。在 Y 工作台纵 向) ( 方向, 用工 作 台的 T形槽 固定 多个定位 挡块 , 一般 间 隔 5米左 右, 这些定位挡块的侧定位面必须在一条直线上。 工件的侧面贴上, 确定工件的零点( Y坐标) 。 2 2 工件 夹紧 : .
o ◎ o 铝 点 焊 时 需 要 较 大 的 点 焊 电 流
注释 : 0
最适合
备, 采用高速强力切削来提高效率、 减少塑性变形, 。 适 合 避免出现薄臂处切不断而撕裂现象。同时由于铝合 △ 如 果可 以的话 , 应避 免 ( 别是薄板 ) 特 金材料 比较软 , 进行锯切加工和人工打磨的工序非 常多 , 因此噪音大、 铝粉尘 , 有 需要作好 防护。 2 1 工件定位 : . 在 x( 工作 台横 向) 方向 , 用工作 台 的 T形 槽 固 定一个挡块 , 然后选用 一块合适 长度 的隔板调 整工 2 铝 合 金 材料 的 / -前 准 备 jr n- 铣削是指铣刀旋转作主运动, 工件或铣刀作
c粒 切 状 屑
d崩 切 碎 屑
起 振动 ; 切削 试件 拐角 处 时 , 因切 人角 和 铣削 长 度 的增 加 , 逆铣 的摩擦 效应 也 会 引起 切 削振 动 , 在 并
螺纹铣削
图1所示为M6标准内螺纹的铣削加工实例。
工件材料:铝合金;刀具:硬质合金螺纹钻铣刀;螺纹深度:10mm;铣刀转速:2,000r/mi n;切削速度:314m/min;钻削进给量:0.25mm/min;铣削进给量:0.06mm/齿;加工时间:每孔1.8s。
图1所示加工工位流程为:①位,螺纹钻铣刀快速运行至工件安全平面;②位,螺纹钻铣刀钻削至孔深尺寸;③位,螺纹钻铣刀快速提升到螺纹深度尺寸;④位,螺纹钻铣刀以圆弧切入螺纹起始点;⑤位,螺纹钻铣刀绕螺纹轴线作X、Y方向插补运动,同时作平行于轴线的+Z方向运动,即每绕螺纹轴线运行360°,沿+Z方向上升一个螺距,三轴联动运行轨迹为一螺旋线;⑥位,螺纹钻铣刀以圆弧从起始点(也是结束点)退刀;⑦位,螺纹钻铣刀快速退至工件安全平面,准备加工下一孔。
该加工过程包括了钻孔、倒角、内螺纹铣削和螺纹清根槽铣削,采用一把刀具一次完成,加工效率极高。
3 螺纹铣刀主要类型在螺纹铣削加工中,三轴联动数控机床和螺纹铣削刀具是必备的两要素。
以下介绍几种常见的螺纹铣刀类型:(1) 圆柱螺纹铣刀圆柱螺纹铣刀的外形很像是圆柱立铣刀与螺纹丝锥的结合体(见图2上,图2下为锥管螺纹铣刀),但它的螺纹切削刃与丝锥不同,刀具上无螺旋升程,加工中的螺旋升程靠机床运动实现。
由于这种特殊结构,使该刀具既可加工右旋螺纹,也可加工左旋螺纹,但不适用于较大螺距螺纹的加工。
常用的圆柱螺纹铣刀可分为粗牙螺纹和细牙螺纹两种。
出于对加工效率和耐用度的考虑,螺纹铣刀大都采用硬质合金材料制造,并可涂覆各种涂层以适应特殊材料的加工需要。
圆柱螺纹铣刀适用于钢、铸铁和有色金属材料的中小直径螺纹铣削,切削平稳,耐用度高。
缺点是刀具制造成本较高,结构复杂,价格昂贵。
(2) 机夹螺纹铣刀及刀片机夹螺纹铣刀适用于较大直径(如D>25mm)的螺纹加工。
其特点是刀片易于制造,价格较低,有的螺纹刀片可双面切削,但抗冲击性能较整体螺纹铣刀稍差。
铝合金机加工工艺流程
铝合金机加工工艺流程铝合金是一种常见的金属材料,具有轻、强、耐腐蚀等特点,被广泛用于汽车、航空航天及其他工业领域。
铝合金的机加工工艺流程主要包括铸造、锻造、铣削、钻孔、车削、铣削等工序,下面将对铝合金的机加工工艺流程进行介绍。
首先是铝合金的铸造工艺。
铸造是将铝合金熔化后,通过特定的模具进行注入、浇铸成型的工艺。
铸造工艺根据需要可以分为压力注射铸造、重力铸造、低压铸造等不同的方法。
铸造后得到的铝合金铸件可以作为下一步加工的基础。
接下来是铝合金的锻造工艺。
锻造是通过对铝合金适当加热,然后利用锻压机对铝合金进行塑性变形,得到所需形状和尺寸的工艺。
锻造可以进一步提高铝合金的性能,增加其塑性和韧性。
锻造工艺可以分为自由锻造、轴对称锻造、坯料预成型锻造等不同方法。
铣削是铝合金机加工工艺中常见的方法之一。
铣削是通过将铝合金放置在铣床上,利用铣刀在铝合金上按照所需形状和尺寸切削的工艺。
铣削可以对铝合金进行平面、曲面、开槽等多种形状的加工,通常需要多次切削来得到最终的形状。
钻孔也是铝合金机加工中常见的方法之一。
钻孔是通过将铝合金放置在钻床上,利用钻头在铝合金上进行钻孔的工艺。
钻孔可以得到不同直径和深度的孔,同时还可进行多孔和不规则孔的加工。
车削是对铝合金进行精密加工的一种工艺。
车削是在车床上将铝合金跟刀具固定在一起,利用车床旋转的方式对铝合金进行切削和修整的工艺。
车削可以进行精确的外圆、内圆、端面等形状的加工,同时还可以进行螺纹和花键等加工。
最后是铣削加工。
铣削加工是将铝合金放置在铣床上,利用多刀具同时进行铣削的工艺。
铣削加工可以同时进行多个平面的加工,提高加工效率和精度。
综上所述,铝合金的机加工工艺流程包括铸造、锻造、铣削、钻孔、车削、铣削等工序。
这些工序能够根据需要对铝合金进行不同形状和尺寸的加工,最终得到所需的零件和产品。
同时,适当选择机械设备和工艺参数,合理操作和控制,可以提高铝合金的加工质量和生产效率。
铝合金腔体高精度内螺纹铣削加工
铝合金腔体高精度内螺纹铣削加工作者:周广晏张怡来源:《中国机械》2013年第07期摘要:随着电子产品结构件的加工精度逐步提高,用传统的丝锥手工攻丝加工的螺纹孔很难达到设计精度要求。
本文研究了铝合金腔体高精度内螺纹铣削加工中的工艺方法,包括加工原理、刀具选择以及编程方式。
在MIKRON数控机床上进行了螺纹铣削的加工试验,并对铣削的螺纹进行了加工精度检测评估。
关键词:螺纹铣削内螺纹加工精度正文:1.引言电子产品中使用螺纹连接的铝合金材料的结构件,其螺纹孔加工的典型工艺流程为:数铣点出中心孔——钳工打螺纹底孔——钳工用丝锥攻丝加工内螺纹。
此方法加工内螺纹存在以下问题:(1)很难控制攻丝深度和垂直度,螺纹精度不高;(2)丝锥加工螺纹毛刺较多,去除困难。
随着数控技术的发展,螺纹铣削加工开始应用到螺纹加工当中。
螺纹铣削具有以下优势:⑴螺纹垂直度较好,毛刺少,尺寸精度高,无需退刀槽就能靠近底部加工出精确深度的螺纹;(2)不受螺纹结构和旋向的限制,用同一把螺纹铣刀可以加工不同结构、旋向的螺纹;(3)螺纹铣刀耐用度高,能降低加工成本。
随电子产品的发展,其铝合金结构件上螺纹孔的加工精度提出了更高的要求,丝锥攻丝加工内螺纹的方法已经很难满足精度要求,研究数控加工是实现高精度内螺纹铣削加工成为必须。
2.高精度内螺纹加工存在问题分析电子产品中一个典型的铝合金腔体结构内螺纹结构如下图:(单位:mm,下同)图中螺纹孔大小为M5×0.5,要求此螺纹孔最小深度为3.3,且不允许深度为3.5的平面有毛刺。
使用手工攻丝加工很难实现,面对此类工艺瓶颈,急需寻找一种新的精度更高的内螺纹加工方法。
3.内螺纹铣削加工工艺研究3.1加工原理考虑到螺纹铣削法在加工精度上的优势,采用以下工艺流程进行加工:数铣点出螺纹孔中心孔——数铣加工出螺纹孔底孔——数铣铣削出螺纹孔内螺纹。
通过工件一次装夹和定位,就可加工出一个完整的螺纹孔。
螺纹孔内螺纹铣削中,利用数控铣床的螺旋插补功能,刀具在XY方向上做圆周运动,同时沿Z轴做直线运动,从而走出螺旋线轨迹的方法形成螺纹。
铝合金焊缝的电火花铣削工艺研究
砂 轮 磨 削。 Fra bibliotek关键词 : 电火 花铣 削 ; 焊 缝处 理 ; 铝 合金 焊缝 中图分 类号 : T G 6 6 1 文献标 识码 : A 文章 编号 : 1 0 0 9 — 2 7 9 X( 2 0 1 3 ) 0 5 — 0 o 1 8 — 0 3
S t u d y o n EDM - mi l l i n g f o r Al u mi n u m AH o y We l d i n g J o i n t
火花铣 削铝合金 焊缝 的加 工 效率进 行 了研 究。结果表 明 : 铣 削工 艺影 响焊缝 力 学性 能 , 电火花铣 削
工 艺与砂轮 磨 削工 艺处 理 的焊缝 抗拉 性 能相 当;砂 轮 磨 削焊缝表 面为各 向异性 划痕 沟槽 式 分布 ,
电火花铣 削焊缝 表 面为 各 向 同性较 均 匀凹坑 ; 同等 尺 寸要 求下 , 电 火花铣 削工 艺 的尺 寸精 度 高 于
a c c u r a c y .A t l a s t ,t h e p r o c e s s i n g e f i f c i e n c y f o E D M- mi l l i n g o n a l u mi n u m a l l o y w e l d i n g j o i n t s i s r e s e a r c h e d . T h e r e s u l t s s h o w t h a t mi l l i n g p r o c e s s e s e f f e c t e d m e c h a n i c l a p r o p e r t i e s f o w e l d i n g j o i n t s , t h e E D M— mi l l i n g p r o c e s s a n d g r i n d i n g m i l l i n g p r o c e s s i s s i mi l r a o n t e n s i l e p r o p e r t i e s o f w e l d i n g j o i n t s . he T s u r f a c e o f w e l d i n g j o i n t s g r i n d e d a p p e a r t h a t a l u m i n u m l a l o y h a v e s o me a n i s o t r o i c s c r a t c h ro g o v e
- 1、下载文档前请自行甄别文档内容的完整性,平台不提供额外的编辑、内容补充、找答案等附加服务。
- 2、"仅部分预览"的文档,不可在线预览部分如存在完整性等问题,可反馈申请退款(可完整预览的文档不适用该条件!)。
- 3、如文档侵犯您的权益,请联系客服反馈,我们会尽快为您处理(人工客服工作时间:9:00-18:30)。
铣削铝合金加工工艺
1. 概述
铝合金是一种常用的轻质高强度材料,被广泛应用在航空、汽车、电子等行业中。
铣削是一种常见的加工方法,可用于铝合金零
部件的加工和制造。
2. 铣削工艺的选择
在铣削铝合金时,需要根据工件的形状、尺寸和要求选择合适
的铣削工艺。
以下是一些常用的铣削工艺:
2.1 平面铣削
平面铣削适用于铝合金表面的平面加工和修整。
可使用平铣刀
或立铣刀进行铣削操作。
此工艺可以达到较高的加工精度和平面度。
2.2 端铣削
端铣削适用于铝合金的边缘加工和倒角。
用端铣刀进行削除材料,可以获得整齐的边缘,并消除可能的锋利边缘。
2.3 深孔铣削
深孔铣削适用于铝合金工件的孔内加工。
使用长刀具,沿孔的
轴线进行铣削操作。
这种工艺可以获得较深的孔内加工效果。
2.4 铣削槽加工
铣削槽加工适用于铝合金工件上的槽加工。
使用槽铣刀进行切割,可以制造出各种形状和尺寸的槽。
此工艺常用于制造槽轨等零
部件。
3. 加工参数调整
在铣削铝合金时,需要根据具体工件和工艺要求进行加工参数
的调整。
以下是一些常见的加工参数:
3.1 切削速度
切削速度是指刀具切削工件时的线速度。
在铝合金加工中,通
常选择较高的切削速度以提高生产效率。
3.2 进给速度
进给速度是指刀具在单位时间内移动的距离。
在铝合金加工中,适当的进给速度可以保证加工表面光滑,并减少刀具磨损。
3.3 切削深度
切削深度是指每次刀具进入工件的深度。
在铝合金加工中,一般选择较小的切削深度以减少切削力和切削温度。
3.4 刀具选择
针对不同的铝合金材料和加工工艺,选择合适的刀具是非常重要的。
常见的铣削刀具包括平铣刀、立铣刀、端铣刀和槽铣刀等。
4. 加工质量控制
在铣削铝合金加工过程中,需要进行质量控制以确保加工零部件的质量。
以下是一些常用的质量控制措施:
4.1 尺寸测量
通过合适的测量工具,对加工零部件的尺寸进行测量和验证。
确保加工尺寸符合设计要求。
4.2 表面质量检查
检查加工零部件的表面质量,包括表面粗糙度和平整度。
确保表面满足要求,不影响零部件的功能和外观。
4.3 检查倒角效果
对倒角工艺进行检查,确保边缘倒角光滑平整,避免锋利边缘。
5. 安全注意事项
在铣削铝合金加工过程中,需要注意以下安全事项:
5.1 切削润滑
使用合适的切削润滑剂或冷却液来降低切削温度,并提供良好
的切削条件。
5.2 刀具保护
正确使用和保护刀具,避免刀具损坏或意外事故发生。
5.3 手部防护
在操作过程中,需戴上适当的手套和防护眼镜,以保护手部和
眼部安全。
以上是铣削铝合金加工工艺的简要介绍,希望对您有所帮助。
如有其他疑问,请随时咨询。