课题7:加工中心认识项目
加工中心实训报告实训内容

加工中心实训报告实训内容一、实训目的和背景加工中心是一种高效、高精度的数控机床,广泛应用于各个制造行业。
为了提高学生的加工技能和对加工中心的操作和维护能力,我们进行了加工中心实训。
二、实训内容1. 设备介绍我们对加工中心进行了详细的介绍。
加工中心是一种多功能、高精度的数控机床,具有铣削、钻孔、攻丝等多种加工能力。
我们了解了加工中心的各个部件及其功能,包括主轴、工作台、刀库等。
2. 设备操作我们学习了加工中心的操作流程。
首先是设备的开机操作,包括启动电源、打开主控器等。
然后是设备的程序输入和设置,我们学会了使用G代码和M代码编写程序,设置切削参数和工件坐标系等。
接下来是设备的加工操作,包括夹紧工件、选择刀具、设定加工路径等。
最后是设备的关机操作,包括关闭主控器、切断电源等。
3. 加工实践为了让我们更好地掌握加工中心的操作技巧,我们进行了加工实践。
首先是简单零件的加工,我们根据给定的工艺图纸,选择合适的刀具和加工路径,进行了铣削和钻孔操作。
然后是复杂零件的加工,我们需要自己设计工艺流程和选择刀具,进行多道工序的加工操作。
通过这些加工实践,我们提高了自己的加工能力和技术水平。
4. 故障排除和维护在实训过程中,我们还学习了加工中心的故障排除和维护方法。
当设备出现故障时,我们需要根据故障现象和报警信息,进行问题分析和排除。
同时,我们还学会了设备的日常维护和保养,包括清洁设备、加油润滑等。
三、实训收获通过加工中心实训,我们获得了以下收获:1. 掌握了加工中心的基本操作和编程技巧,提高了自己的加工能力;2. 熟悉了加工中心的各个部件和功能,了解了数控机床的工作原理;3. 学会了使用G代码和M代码编写程序,能够根据工艺要求进行加工操作;4. 熟悉了加工中心的故障排除和维护方法,能够及时处理设备故障和保养设备。
四、实训总结通过加工中心实训,我们不仅提高了自己的加工技能,还增加了对加工中心的了解和掌握。
实训内容包括设备介绍、设备操作、加工实践和故障排除维护等方面,通过系统的学习和实践,我们取得了丰硕的成果。
加工中心课程设计

加工中心课程设计一、教学目标本课程旨在让学生掌握加工中心的基本概念、原理和操作方法。
通过本课程的学习,学生将能够:1.描述加工中心的基本组成、工作原理和应用领域。
2.解释加工中心各种刀具的作用和选用原则。
3.演示加工中心的操作步骤和编程方法。
4.分析加工中心加工过程中的工艺参数和质量控制。
5.探讨加工中心在现代制造业中的地位和作用。
二、教学内容本课程的教学内容主要包括以下几个部分:1.加工中心的基本概念:介绍加工中心的定义、分类和特点。
2.加工中心原理:讲解加工中心的工作原理、结构及功能。
3.加工中心刀具:介绍刀具的类型、选用原则和维护方法。
4.加工中心操作:教授操作步骤、编程方法和加工工艺。
5.加工中心应用:分析加工中心在制造业中的应用案例。
三、教学方法为了提高教学效果,本课程将采用以下教学方法:1.讲授法:讲解加工中心的基本概念、原理和操作方法。
2.讨论法:学生探讨加工中心的应用案例和产业发展趋势。
3.案例分析法:分析加工中心在实际生产中的应用实例,提高学生的实践能力。
4.实验法:安排学生进行加工中心操作实验,巩固所学知识。
四、教学资源为了支持教学内容和教学方法的实施,我们将准备以下教学资源:1.教材:选用权威、实用的加工中心教材作为主要教学资料。
2.参考书:提供相关领域的参考书籍,丰富学生的知识体系。
3.多媒体资料:制作精美的PPT、视频等多媒体教学资源,提高学生的学习兴趣。
4.实验设备:确保每个学生都能在实验课上亲手操作加工中心,提高实践能力。
五、教学评估本课程的评估方式包括以下几个方面:1.平时表现:考察学生在课堂上的参与程度、提问回答和小组讨论的表现。
2.作业:布置适量的作业,评估学生对课程内容的掌握和应用能力。
3.考试:定期进行考试,全面检验学生的知识水平和理解能力。
评估方式应客观、公正,能够全面反映学生的学习成果。
我们将结合以上三个方面进行综合评分,以保证评估的全面性和准确性。
六、教学安排本课程的教学安排如下:1.教学进度:按照教材和大纲进行教学,确保完成所有预定内容。
加工中心基础实训报告

一、实训背景随着我国制造业的快速发展,数控加工中心作为一种高精度、高效率的自动化加工设备,在航空航天、汽车制造、精密模具等行业得到了广泛应用。
为了提高我国制造业的竞争力,培养具备数控加工中心操作与编程能力的人才成为当务之急。
本次实训旨在让学生了解加工中心的基本结构、操作方法及编程技巧,提高学生的实际操作能力。
二、实训目的1. 熟悉加工中心的基本结构、工作原理及操作方法;2. 掌握加工中心编程的基本技巧,能够独立编写简单零件的加工程序;3. 培养学生实际操作加工中心的能力,提高学生解决实际问题的能力;4. 增强学生对数控加工行业的认识,激发学生对数控技术的兴趣。
三、实训内容1. 加工中心基本结构及工作原理加工中心主要由床身、工作台、主轴、数控系统、自动换刀系统等组成。
床身是加工中心的主体,起到支撑和固定作用;工作台用于安装和固定工件,可进行X、Y、Z三个方向的移动;主轴用于安装刀具,带动刀具进行切削;数控系统负责对加工过程进行控制和监控;自动换刀系统用于实现刀具的快速更换。
2. 加工中心操作方法(1)开机前准备:检查机床各部位是否正常,调整机床至参考零位,装夹工件。
(2)编程:根据零件图纸要求,编写加工程序。
加工程序包括刀具路径、加工参数、刀具补偿等内容。
(3)试切:在加工前进行试切,检查刀具路径是否正确,加工参数是否合理。
(4)正式加工:启动加工中心,按照编程好的加工程序进行加工。
(5)加工后处理:加工完成后,对工件进行检测、清理等工作。
3. 加工中心编程技巧(1)合理选择刀具:根据加工材料和加工要求,选择合适的刀具。
(2)优化刀具路径:合理规划刀具路径,提高加工效率。
(3)设置合理的加工参数:包括切削速度、进给速度、切削深度等。
(4)刀具补偿:根据刀具实际尺寸对加工程序进行补偿,保证加工精度。
四、实训总结本次实训使学生掌握了加工中心的基本结构、操作方法及编程技巧,提高了学生的实际操作能力。
以下是实训过程中的一些体会:1. 加工中心是一种高精度、高效率的自动化加工设备,掌握其操作和编程技巧对于提高我国制造业的竞争力具有重要意义。
加工中心实习实训报告
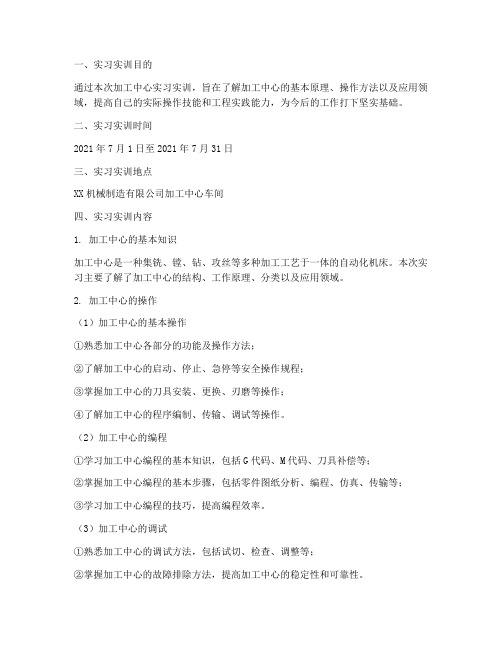
一、实习实训目的通过本次加工中心实习实训,旨在了解加工中心的基本原理、操作方法以及应用领域,提高自己的实际操作技能和工程实践能力,为今后的工作打下坚实基础。
二、实习实训时间2021年7月1日至2021年7月31日三、实习实训地点XX机械制造有限公司加工中心车间四、实习实训内容1. 加工中心的基本知识加工中心是一种集铣、镗、钻、攻丝等多种加工工艺于一体的自动化机床。
本次实习主要了解了加工中心的结构、工作原理、分类以及应用领域。
2. 加工中心的操作(1)加工中心的基本操作①熟悉加工中心各部分的功能及操作方法;②了解加工中心的启动、停止、急停等安全操作规程;③掌握加工中心的刀具安装、更换、刃磨等操作;④了解加工中心的程序编制、传输、调试等操作。
(2)加工中心的编程①学习加工中心编程的基本知识,包括G代码、M代码、刀具补偿等;②掌握加工中心编程的基本步骤,包括零件图纸分析、编程、仿真、传输等;③学习加工中心编程的技巧,提高编程效率。
(3)加工中心的调试①熟悉加工中心的调试方法,包括试切、检查、调整等;②掌握加工中心的故障排除方法,提高加工中心的稳定性和可靠性。
3. 加工中心的维护与保养(1)了解加工中心各部件的结构、功能及维护保养方法;(2)掌握加工中心的润滑、冷却、清洁等保养方法;(3)了解加工中心的安全防护装置及操作规程。
五、实习实训心得1. 加工中心实习实训让我对加工中心的基本原理、操作方法有了更深入的了解,提高了自己的实际操作技能。
2. 通过编程、调试等实践操作,我掌握了加工中心的编程技巧和故障排除方法,为今后的工作打下了坚实基础。
3. 实习实训过程中,我深刻体会到团队合作的重要性。
在遇到问题时,与同事共同探讨、解决问题,提高了自己的沟通能力和团队协作能力。
4. 加工中心实习实训使我认识到,理论知识与实际操作相结合的重要性。
在今后的工作中,我将不断学习,提高自己的综合素质。
六、实习实训总结通过本次加工中心实习实训,我收获颇丰。
加工中心教案

加工中心教案教案标题:加工中心教案教案目标:1. 了解加工中心的定义、功能和应用领域;2. 掌握加工中心的操作流程和安全注意事项;3. 培养学生的加工中心操作技能和创新能力;4. 提高学生的团队合作和沟通能力。
教案步骤:引入(5分钟):1. 引导学生回顾之前学习的有关机械加工的知识,如车床、铣床等;2. 引入加工中心的概念,解释其与传统机械加工设备的区别和优势;3. 引发学生的兴趣和好奇心,激发他们对加工中心的学习热情。
知识讲解(15分钟):1. 介绍加工中心的基本结构和主要组成部分,如机床、刀库、数控系统等;2. 解释加工中心的工作原理和加工过程,包括自动换刀、自动换工件等;3. 分析加工中心在各个行业中的应用领域,如汽车制造、航空航天等。
操作演示(20分钟):1. 展示加工中心的操作流程,包括开机准备、程序输入、刀具装夹、工件装夹等;2. 演示加工中心的常见操作技巧,如刀具选择、刀具路径规划等;3. 强调操作中的安全注意事项,如佩戴防护眼镜、保持工作区整洁等;4. 鼓励学生积极参与操作演示,提问解答和互动交流。
实践操作(30分钟):1. 将学生分成小组,每个小组配备一台加工中心进行实践操作;2. 要求学生根据提供的加工任务,编写相应的加工程序;3. 引导学生进行实际的刀具装夹和工件装夹操作;4. 监督学生的操作过程,及时纠正错误和提供指导。
总结反思(10分钟):1. 要求学生对本节课的学习进行总结,回答相关问题;2. 引导学生思考加工中心的优势和应用前景;3. 鼓励学生提出自己的创新想法和改进建议;4. 对学生的表现进行评价和鼓励。
拓展延伸:1. 鼓励学生自主学习和探索加工中心的更多应用领域;2. 组织学生参观实际的加工中心,与专业人员进行交流;3. 鼓励学生参加相关的技能竞赛和项目实践活动;4. 提供相关的学习资源和参考资料,帮助学生进一步提升技能。
教案评估:1. 观察学生在操作过程中的技能掌握情况;2. 评估学生对加工中心知识的理解和应用能力;3. 收集学生的反馈意见和建议,改进教学方法和内容;4. 根据学生的表现,给予相应的奖励和鼓励。
加工中心实验报告
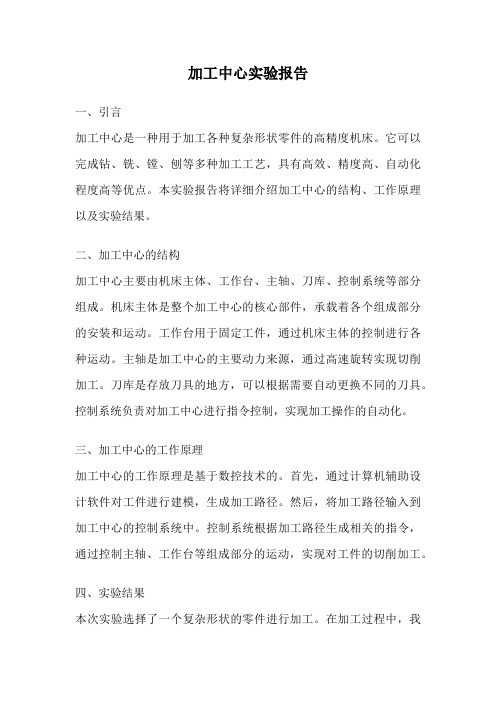
加工中心实验报告一、引言加工中心是一种用于加工各种复杂形状零件的高精度机床。
它可以完成钻、铣、镗、刨等多种加工工艺,具有高效、精度高、自动化程度高等优点。
本实验报告将详细介绍加工中心的结构、工作原理以及实验结果。
二、加工中心的结构加工中心主要由机床主体、工作台、主轴、刀库、控制系统等部分组成。
机床主体是整个加工中心的核心部件,承载着各个组成部分的安装和运动。
工作台用于固定工件,通过机床主体的控制进行各种运动。
主轴是加工中心的主要动力来源,通过高速旋转实现切削加工。
刀库是存放刀具的地方,可以根据需要自动更换不同的刀具。
控制系统负责对加工中心进行指令控制,实现加工操作的自动化。
三、加工中心的工作原理加工中心的工作原理是基于数控技术的。
首先,通过计算机辅助设计软件对工件进行建模,生成加工路径。
然后,将加工路径输入到加工中心的控制系统中。
控制系统根据加工路径生成相关的指令,通过控制主轴、工作台等组成部分的运动,实现对工件的切削加工。
四、实验结果本次实验选择了一个复杂形状的零件进行加工。
在加工过程中,我们通过合理的刀具选择、加工路径规划等措施,成功地完成了对零件的加工。
实验结果表明,加工中心具有高精度、高效率的特点,能够满足对复杂形状零件的加工需求。
五、总结与展望通过本次实验,我们深入了解了加工中心的结构和工作原理,并通过实际操作验证了其加工能力。
加工中心作为一种高精度机床,具有广泛的应用前景。
未来,我们将进一步研究和改进加工中心的技术,提高其加工精度和效率,为工业生产提供更好的支持。
六、致谢感谢实验中心提供的设备和技术支持,使本次实验得以顺利进行。
同时,也要感谢指导老师对实验过程的指导和建议。
以上是对加工中心实验的详细介绍和分析,通过本次实验,我们深入了解了加工中心的结构、工作原理以及实验结果,并对其应用前景进行了展望。
加工中心作为一种高精度机床,将在工业生产中发挥重要作用。
数控铣床加工中心教案

数控铣床加工中心教案第一章:数控铣床加工中心概述1.1 课程目标让学生了解数控铣床加工中心的基本概念、特点和应用领域。
让学生了解数控铣床加工中心的基本结构和组成。
1.2 教学内容数控铣床加工中心的定义和发展历程。
数控铣床加工中心的特点和优势。
数控铣床加工中心的应用领域。
数控铣床加工中心的基本结构和组成。
1.3 教学方法讲授法:讲解数控铣床加工中心的基本概念、特点和应用领域。
参观法:参观数控铣床加工中心,了解其结构和组成。
1.4 教学评估课堂问答:学生能够回答数控铣床加工中心的基本概念和特点。
实践操作:学生能够观察和描述数控铣床加工中心的结构和组成。
第二章:数控铣床加工中心的基本操作2.1 课程目标让学生掌握数控铣床加工中心的基本操作步骤。
让学生了解数控铣床加工中心的安全操作规程。
2.2 教学内容数控铣床加工中心的基本操作步骤。
数控铣床加工中心的安全操作规程。
2.3 教学方法演示法:演示数控铣床加工中心的基本操作步骤。
实践操作法:学生亲自动手操作数控铣床加工中心。
2.4 教学评估实践操作:学生能够独立完成数控铣床加工中心的基本操作。
课堂问答:学生能够回答数控铣床加工中心的安全操作规程。
第三章:数控铣床加工中心的编程与操作3.1 课程目标让学生了解数控铣床加工中心的编程原理和方法。
让学生掌握数控铣床加工中心的编程操作步骤。
3.2 教学内容数控铣床加工中心的编程原理和方法。
数控铣床加工中心的编程操作步骤。
3.3 教学方法讲授法:讲解数控铣床加工中心的编程原理和方法。
实践操作法:学生亲自动手操作数控铣床加工中心进行编程操作。
3.4 教学评估实践操作:学生能够独立完成数控铣床加工中心的编程操作。
课堂问答:学生能够回答数控铣床加工中心编程的基本原理和方法。
第四章:数控铣床加工中心的刀具选择与更换4.1 课程目标让学生了解数控铣床加工中心的刀具选择原则。
让学生掌握数控铣床加工中心的刀具更换方法。
4.2 教学内容数控铣床加工中心的刀具选择原则。
加工中心操作实验
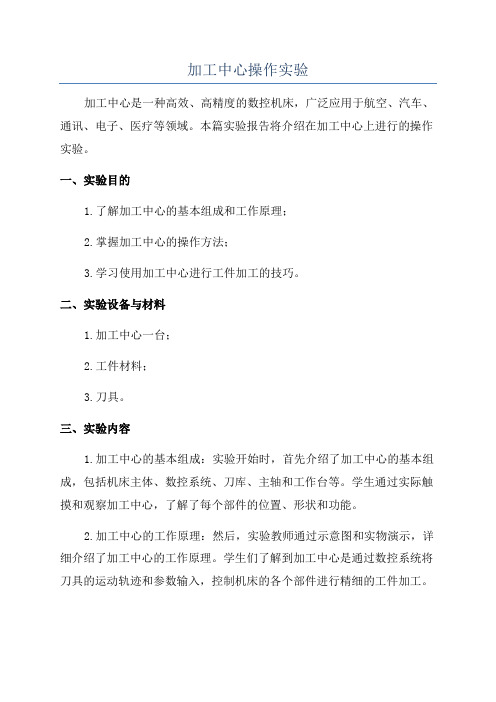
加工中心操作实验加工中心是一种高效、高精度的数控机床,广泛应用于航空、汽车、通讯、电子、医疗等领域。
本篇实验报告将介绍在加工中心上进行的操作实验。
一、实验目的1.了解加工中心的基本组成和工作原理;2.掌握加工中心的操作方法;3.学习使用加工中心进行工件加工的技巧。
二、实验设备与材料1.加工中心一台;2.工件材料;3.刀具。
三、实验内容1.加工中心的基本组成:实验开始时,首先介绍了加工中心的基本组成,包括机床主体、数控系统、刀库、主轴和工作台等。
学生通过实际触摸和观察加工中心,了解了每个部件的位置、形状和功能。
2.加工中心的工作原理:然后,实验教师通过示意图和实物演示,详细介绍了加工中心的工作原理。
学生们了解到加工中心是通过数控系统将刀具的运动轨迹和参数输入,控制机床的各个部件进行精细的工件加工。
3.加工中心的操作方法:在掌握了加工中心的基本构造和工作原理后,学生开始学习加工中心的操作方法。
首先,他们学习如何正确打开和关闭机床的电源,并了解各个面板和按钮的功能。
接下来,他们学习了机床参数的设定和调整,包括进给速度、主轴转速和刀具补偿等。
4.工件加工实践:在掌握了加工中心的操作方法后,学生开始进行实际的工件加工实践。
首先,他们根据给定的零件图纸和工艺要求,选择合适的刀具,并进行刀具的装夹和校准。
然后,他们通过数控系统设定刀具路径和运动参数,并开始进行工件加工。
在整个加工过程中,学生需要不断观察和检查工件的加工质量,并及时调整刀具路径和运动参数,以保证工件加工的精度和表面质量。
同时,他们还需要注意保持机床的清洁和润滑,以确保机床的正常运行和寿命。
四、实验结果与分析通过实验,学生们成功完成了工件的加工,并取得了较好的加工质量。
实验教师对学生们的表现给予了肯定,并对他们的操作技巧和注意事项做了一些指导。
同时,实验教师还根据实际情况,对加工中心操作方法做了一些补充和修正。
五、实验心得通过参与加工中心操作实验,我进一步了解了加工中心的基本构造、工作原理和操作方法。
- 1、下载文档前请自行甄别文档内容的完整性,平台不提供额外的编辑、内容补充、找答案等附加服务。
- 2、"仅部分预览"的文档,不可在线预览部分如存在完整性等问题,可反馈申请退款(可完整预览的文档不适用该条件!)。
- 3、如文档侵犯您的权益,请联系客服反馈,我们会尽快为您处理(人工客服工作时间:9:00-18:30)。
课题7:加工中心认识项目7.1任务:定位孔板的加工定位孔板零件如图2.1.1所示,在400mm×300mm×70mm板料上加工4个φ30H7通孔、2个φ40H7盲孔、4个M10的螺纹孔,零件上下表面和台阶面已加工至尺寸。
图2.1.1 定位孔板零件图7.2 加工中心加工对象加工中心是在数控铣床的基础上发展起来的。
它和数控铣床有很多相似之处,主要区别在于增加了刀库和自动换刀装置,能自动更换刀具对工件进行多工序加工。
通过在刀库上安装不同用途的刀具,加工中心可在一次装夹中实现零件的铣、钻、镗、铰、攻螺纹等多工序加工。
随着工业的发展,加工中心将逐渐取代数控铣床,成为一种主要的加工机床。
7.3换刀相关指令与长度补偿指令1.自动返回参考点G28指令机床参考点(R),是机床上一个特殊的固定点,一般位于机床坐标系原点的位置,可用G28指令移动刀具到这个位置。
在加工中心上,机床参考点一般为主轴换刀点,使用自动返回参考点G28指令主要用来进行刀具交换准备。
格式:G28 X__Y__Z__;式中,X、Y、Z为中间点在工件坐标系中的坐标值。
该指令将刀具以快速移动速度向中间点(X Y Z )定位,然后从中间点以快速移动的速度移动到原点。
如G90 G28 X100.0 Y100.0,执行该程序段时,刀具从当前点移动到参考点的路线如图2.1.5所示。
在立式加工中心编程中,G91 G28 Z0比较常见,该程序段表示主轴由当前Z坐标(中间点,X、Y坐标保持不变)快速移动到机床坐标系的Z轴零点。
G90 G28 Z0则表示主轴快速移动到工件坐标系的Z轴零点(中间点,X、Y 坐标保持不变),然后快速移动到机床坐标系的Z轴零点。
在G28中指定的坐标值(中间点)会被记忆,如果在其他的G28指令中,没有指定坐标值,就以前G28指令中指定的坐标值为中间点。
3.换刀功能及应用(1)T指令T指令用来选择机床上的刀具,如T02表示选2号刀,执行该指令时刀库将2号刀具放到换刀位置做换刀准备。
(2)M06 指令M06 指令实施换刀,即将当前刀具与T指令选择的刀具进行交换。
(3)自动换刀程序的编写①无机械手的加工中心换刀程序T02 M06或M06 T02;换刀程序的含义:将2号刀具安装到主轴上。
换刀过程:先把主轴上的旧刀具送回到它原来所在的刀座上去,刀库回转寻刀,将2号刀转换到当前换刀位置,再将2号刀装入主轴。
无机械手换刀中,刀库选刀时,机床必须等待,因此换刀将浪费一定时间。
②带机械手的加工中心换刀程序…T02;刀库选刀(选2号刀)…使用当前主轴上的刀具切削……M06;实际换刀,将当前刀具与2号刀进行位置交换(2号刀到主轴)…使用当前主轴上的刀具切削……T05;下一把刀准备(选5号刀)…使用当前主轴上的刀具切削……这种换刀方法,选刀动作可与前一把刀具的加工动作相重合,换刀时间不受选刀时间长短的影响,因此换刀时间较短。
4.刀具长度补偿(1)长度补偿的目的刀具长度补偿功能用于在Z轴方向的刀具补偿,它可使刀具在Z轴方向的实际位移量大于或小于编程给定位移量。
有了刀具长度补偿功能,当加工中刀具因磨损、重磨、换新刀而长度发生变化时,可不必修改程序中的坐标值,只要修改存放在寄存器中刀具长度补偿值即可。
其次,若加工一个零件需用几把刀,各刀的长度不同,编程时不必考虑刀具长短对坐标值的影响,只要把其中一把刀设为标准刀,其余各刀相对标准刀设置长度补偿值即。
(2)长度补偿指令格式:G43(G44) G00(G01) Z H ;G49 G00(G01) Z ;G43为刀具长度正补偿,G44为刀具长度负补偿,G49为取消刀具长度补偿指令,均为模态G代码。
格式中,Z值是属于G00或G01的程序指令值。
H为刀具长度补偿寄存器的地址字,它后面的两位数字是刀具补偿寄存器的地址号,如H01是指01号寄存器,在该寄存器中存放刀具长度的补偿值。
在G17的情况下,刀具长度补偿G43、G44只用于Z轴的补偿,而对X轴和Y轴无效。
执行G43时,Z基准刀=Z指令值+H ;执行G44时,Z基准刀=Z指令值-H 。
例:钻图2.1.6所示的孔,设在编程时以主轴端部中心作为基准刀的刀位点。
钻头安装在主轴上后,测得刀尖到主轴端部的距离为100mm ,刀具起始位置如图中所示。
钻头比基准刀长100mm ,将100mm 作为长度偏置量存入H01地址单元中。
加工程序为:N10 G92 X0 Y0 Z0; 坐标原点设在主轴端面中心N20 S300 M03; 主轴正转N30 G90 G43 G00 Z-245 H01;钻头快速移到离工件表面5mm 处N40 G01 Z-270 F60; 钻头钻孔并超出工件下表面5mmN50 G49 G00 Z0; 取消长度补偿,快速退回 在N30程序段中,通过G43建立了刀具长度补偿。
由于是正补偿,基准刀刀位点(主轴端部中心)到达的Z 轴终点坐标值为(-245+(H01))mm=-145mm ,从而确保钻头刀尖到达-245mm 处。
同样,在N40程序段中,确保了钻头刀尖到达-270mm 处。
在N50中,通过G49取消了刀具长度补偿,基准刀刀位点(主轴端部中心)回到Z 轴原点,钻头刀尖位于-100mm 处。
(3)刀具长度补偿量的确定 方法一:① 依次将刀具装在主轴上,利用Z 向设定器确定每把刀具Z 轴返回机床参考点时刀位点相对工件坐标系Z 向零点的距离,如图2.1.7所示的A 、B 、C (A 、B 、C 均为负值,即各刀具刀位点刚接触工件坐标系Z 向零点处时显示的机床坐标系Z 坐标),并记录下来。
② 选择一把刀作为基准刀(通常为最长的刀具),如图中的T03,将其对刀值C 作为工件坐标系中Z 向偏置值,并将长度补偿值H03设为0。
③ 确定其他刀具的长度补偿值,即H01=±│A-C │,H02=±│B-C │。
当用G43时,图2.1.6 刀具长度补偿实例 图2.1.7 刀具长度补偿量的确定若该刀具比基准刀长则取正号,比基准刀短取负号;用G44时则相反。
方法二:①工件坐标系中(如G54)Z向偏置值设定为0,即基准刀为假想的刀具且足够长,刀位点接触工件坐标系Z向零点处时显示的机床坐标系Z值为零。
②通过机内对刀,确定每把刀具刀位点刚接触工件坐标系Z向零点处时显示的机床坐标系Z坐标(为负值),G43时就将该值输入到相应长度补偿号中即可,G44时则需要将Z坐标值取反后再设定为刀具长度补偿值。
7.4任务决策和执行1.图样分析根据图样需加工4×φ30H7导柱孔,孔距为300±0.015、200±0.015,孔边距50±0.015,孔轴线对底面A的垂直度公差为φ0.015,表面粗糙度为Ra1.6μm;2×φ40H7孔,孔距为120±0.015,表面粗糙度为Ra1.6μm;4×Ml0螺纹孔,深25。
零件上下表面和台阶面已加工至尺寸。
2.工艺分析与设计4×φ30H7导柱孔为7级精度孔,垂直度要求为0.015mm,底孔可钻削完成,考虑其垂直度要求,采用镗孔加工消除钻孔时产生的轴线偏斜影响,最后用铰刀完成孔的精加工。
2×φ40H7孔为盲孔,孔底为平面,精度为7级,可采用钻孔、粗铣、精铣孔方式完成。
螺纹孔钻底孔,然后攻螺纹完成。
工艺过程如下:1) 钻中心孔因钻头定位性不好,先采用中心钻钻出中心孔。
2) 钻底孔用φ29mm钻头钻出4×φ30H7底孔,2×φ40H7孔钻深到29.8mm,用φ8.7mm钻头钻出4×Ml0螺纹底孔。
3) 粗铣孔用φ25mm立铣刀粗铣2×φ40H7到φ39.8mm,切削深度分两层完成。
4) 镗孔用φ29.8mm镗刀对φ30H7孔进行镗孔,纠正钻孔时轴线的偏斜,并且保证铰孔时加工余量。
5) 铰孔用铰刀铰4×φ30H7到尺寸。
6) 精铣孔用φ25mm立铣刀精铣φ40H7孔到尺寸。
7) 攻螺纹孔用M10mm丝锥攻螺纹到尺寸。
3.装夹方案用精密平口钳装夹工件,保证工件下表面水平,基准面与X向平行,夹紧时注意工件是否产生上浮。
4.刀具与工艺参数见表2-1、表2-2。
表2-1 数控加工刀具卡表5-2 数控加工工序卡(4)程序编制工件坐标系X、Y轴原点设置在工件右下角,Z轴原点设在零件最高表面上。
程序如下(立式加工中心,无机械手换刀)。
O0010;主程序名N10 G17 G21 G40 G54 G80 G90 G94 ;程序初始化N20 G28 G91 Z0;回换刀点N30 G00 G90 G54 X-50.0 Y50.0 M03 S400;建立工件坐标系,快速定位到点N40 G43 Z10.0 H01;长度补偿N50 G98 G81 Z-16.0 R-5.0 F100;中心钻孔循环N60 Y250.0;N70 X-350.0;N80 Y50.0;N90 G99 X-140.0 Z-6.0 R5.0;N100 Y250.0;N110 X-260.0;N120 Y50.0;N130 Y150.0;N140 X-140.0;N150 G80 M05;N160 G28 G91 Z0;回换刀点N180 T02 M06;换2号刀N190 G00 G90 G54 X-50.0 Y50.0 M03 S300;N200 G43 Z10.0 H02;N210 G99 G83 Z-79.0 R15.0 Q5.0 F30;钻φ30底孔N220 Y250.0;N230 X-350.0;N240 Y50.0;N250 G80;N260 G00 X-140.0 Y150.0;N270 G99 G83 Z-29.8 R5.0 Q5.0 F30;钻φ40底孔N280 X-260.0;N290 G80 M05;N300 G28 G91 Z0;N310 G28 X0 Y0;N320 T03 M06;换3号刀N330 G00 G90 G54 X-140.0 Y50.0 M03 S600;N340 G43 Z10.0 H03;N350 G99 G83 Z-28.0 R5.0 Q5.0 F60;钻M10螺纹底孔N360 Y250.0;N370 X-260.0;N380 Y50.0;N390 G80 M05N400 G28 G91 Z0;N410 G28 X0 Y0;N420 T04 M06;换4号刀N430 G00 G90 G54 X-140.0 Y150.0 M03 S400;定位在第一个φ40孔上N440 G43 Z50 H04;铣刀长度补偿N450 Z5.0;N460 G01 Z-15.0 F160;第一次铣削深度下刀N470 G91 G41 X5.0 Y-15.0 D04;N480 M98 P0001;调用铣削子程序N490 G90 Z-29.8 F160;第二次铣削深度下刀N500 G01 G91 G41 X5.0 Y-15.0 D04;N510 M98 P0001;调用铣削子程序N520 G90 G00 X-260.0 Y150.0;定位在第二个φ40孔上N530 G01 Z-15.0 F160;第一次铣削深度下刀N540 G91 G41 X5.0 Y-15.0 D04;N550 M98 P0001;调用铣削子程序N560 G90 G01 Z-29.8 F160;第二次铣削深度下刀N570 G91 G41 X5.0 Y-15.0 D04;N580 M98 P0001;调用铣削子程序N590 M05;N600 G28 G91 Z0;N620 T05 M06;换5号刀N630 G00 G90 G54 X-50.0 Y50.0 M03 S300;N640 G43 Z10.0 H05;N650 G98 G85 Z-75.0 R-5.0 F50;粗镗φ30孔N660 Y250.0;N670 X-350.0;N680 Y50.0;N690 G80 M05;N700 G28 G91 Z0;N710 G28 X0 Y0;N720 T06 M06;换6号刀N730 G00 G90 G54 X-50.0 Y50.0 M03 S80;铰φ30孔N740 G43 Z10.0 H06;N750 G98 G85 Z-75.0 R-5.0 F30;N760 Y250.0;N770 X-350.0;N780 Y50.0;N790 G28 G91 Z0;N800 G80 M05;N810 G28 G91 Z0;N820 G28 X0 Y0;N830 T04 M06;换4号刀N840 G00 G90 G54 X-140.0 Y150.0 M03 S400;定位在第一个φ40孔上N850 G43 Z50.0 H04;N860 Z10.0;N870 G01 Z-30.0 F160;N880 G91 G41 X5.0 Y-15.0 D05;半径补偿D05 N890 M98 P0001;调用铣削子程序,精铣孔N900 G00 X-260.0 Y150.0;定位在第二个φ40孔上N910 G90 Z-30.0;N920 G01 G91 G41 X5.0 Y-15.0 D05;半径补偿D05N930 M98 P0001;调用铣削子程序,精铣孔N940 M05;N950 G28 G91 Z0;N960 G28 X0 Y0;N970 T07 M06;换7号刀N980 G00 G90 G54 X-140.0 Y50.0 M03 S60;定位在第一个螺纹孔上N990 G43 Z10.0 H07;N1000 G99 G84 Z-25.0 R5.0 F90;攻螺纹N1010 Y250.0;N1020 X-260.0;N1030 Y50.0;N1040 G80 M05;N1060 G28 X0 Y0;N1070 M30;程序结束铣削子程序:O0001;N10 G91 G03 X15.0 Y15.0 R15.0 F160;N20 I-20.0 J0;N30 X-15.0 Y15.0 R15.0;N40 G40 X-5.0 Y-15.0;N50 G90 G00 Z10.0;N230 M99;练习:加工图示端盖零件,单件。