套圈热处理
国内外轴承制造技术对比分析

国内外轴承制造技术对比分析轴承制造技术是保证轴承寿命和可靠性得以实现并充分发挥其设计潜能的重要手段。
在轴承零件中,对产品性能影响较大的零件是滚动体和套圈,因此,套圈和滚动体制造技术直接影响着轴承的可靠性和使用寿命。
本文就国内外轴承套圈和滚动体的制造技术进行粗浅的对比分析,谬误之处请同行多多指正。
一、轴承套圈制造技术套圈的一般加工过程为:锻造加工→车削加工→热处理加工→磨超加工。
1、套圈锻造加工。
通过锻造加工消除金属内在缺陷,改善金相组织,使金属流线分布合理,金属紧密度好,从而提高轴承的使用寿命。
同时锻造质量水平,对产品的材料利用率和机械加工成本有重要影响。
目前,国内套圈锻造加工以热锻加工为主,就个体而言,我国的套圈锻造技术在某些企业的某些产品中已达到国外先进水平(或已采用先进的制造设备和加工工艺,如采用了高速镦锻工艺),但普遍的水平是采用热锻加工,以压力机锻造→辗扩成形生产线为主。
锻造加热采用煤加热、煤气加热、油加热、具有一定经济实力的企业采用电加热。
加热火耗损失为1%~3%,表面脱碳层深度为0.3~0.4mm,材料利用率为40%~50%。
20世纪80年代,我国广东、浙江、江苏一些中小型企业,在小型轴承套圈上推广了冷挤压工艺,对外径80mm≤φ≤130mm的套圈采用了温挤工艺,φ≤80mm的套圈采用了冷辗扩工艺(目前行业上已扩大到φ≤150mm以下),材料利用率达到60%以上。
国外轴承企业在20世纪60~70年代,中小型套圈已普遍采用了温挤、冷挤和冷辗扩工艺,特别是高速镦锻工艺的普遍应用使生产效率有了明显提高,产品质量和材料利用率均有提高。
与国内普遍采用的锻造工艺相比,生产效率提高3~4倍,产品表面脱碳层深度≤0.2mm,产品加工余量是普通方法的75%~65%,公差是普通方法的50%,几何精度如圆度、平行差等是普通方法的50%,产品批质量水平较高。
2、套圈车削加工。
套圈车削加工承担着快速去除毛坯硬化层,去除多余金属量,经济地取得产品的形状、粗加工尺寸和几何位置精度的任务,对精加工表面均匀地、合理地留一定深度的留量,并加工好非工作表面。
高铁轴承GCr18Mo套圈贝氏体等温淬火热处理工艺仿真优化研究

1 研究亮点为优化国产高铁使用的GC r18M o轴承套圈的贝氏体等温淬火工艺,开展试验测试轴承钢的热物理参数以及过冷奥氏体等温转变曲线,基于试验测得的轴承钢材料参数,采用D E FO RM-H T软件建立轴承套圈的热处理工艺全流程仿真模型。
针对贝氏体等温淬火工艺中的加热温度、等温温度、等温时间和回火温度,采用正交试验法设计16种贝氏体等温淬火工艺仿真方案并进行仿真分析。
基于仿真结果,以轴承套圈的贝氏体体积分数和硬度构建优化目标函数,结合蒙特卡洛法和复合形法对工艺参数进行线性回归分析及优化,在优化得出的工艺参数范围内开展3组验证性热处理试验。
研究成果可为国内GC r18M o轴承套圈的贝氏体等温热处理提供有效的工艺参考。
2 研究内容1)仿真模型建立与准确性分析基于DE FO R M-H T软件,构建G C r18M o套圈热处理全流程仿真模型,并通过金相组织、硬度以及残余奥氏体含量的仿真结果与测试结果对比分析,完成仿真模型准确性的校验。
轴承外圈模型与有限元模型见图1。
G Cr18M o钢的化学成分、不同温度下的热物理性能参数,以及G Cr18M o钢的相变温度及TT T曲线详见原文。
基于所建立的热处理仿真模型,进行GC r18M o轴承套圈的热处理仿真,仿真结果如图2所示。
由图2可知,套圈热处理后组织主要为贝氏体以及少量的残余奥氏体,硬度分布比较均匀。
将仿真结果与试验结果对比,见表1,误差均在1%以内,表明仿真模型具有准确性。
(a)轴承外圈简化模型(单位:m m);(b)有限元模型图1轴承外圈模型与有限元模型(a)贝氏体仿真结果;(b)残余奥氏体仿真结果;(c)硬度仿真结果图2套圈的热处理仿真结果表1仿真与试验对比2)热处理工艺参数仿真优化针对高碳铬钢轴承贝氏体等温淬火工艺参数,依据国内某轴承厂提供的热处理工艺参数的控制范围,建立正交试验方案,并利用所构建的热处理仿真模型完成各方案的仿真分析。
基于仿真分析结果,采用基于蒙特卡洛法和复合形优化方法开发的热处理参数优化设计软件Op ti m um D es ig n,通过多元线性回归方法,优化热处理工艺参数范围。
渗碳钢制轴承套圈渗碳及热处理工艺
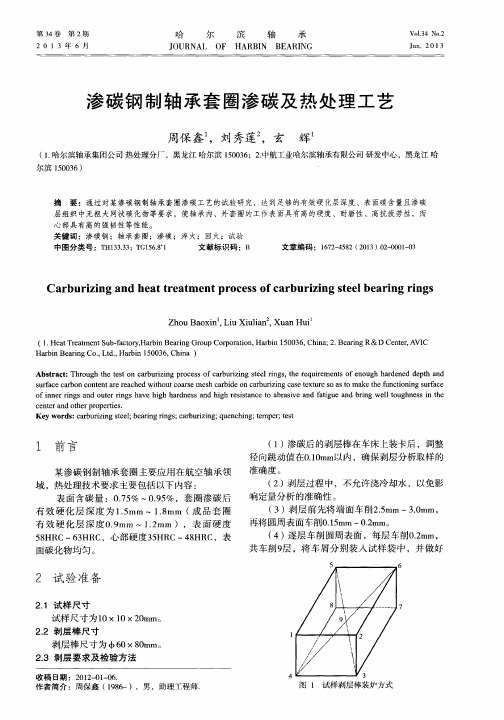
C a r bur i z i ng a nd h e a t t r e a t me n t pr o c e s s o f c a r bur i z i ng s t e e l be a r i ng r i ng s
Zh o u Ba o xi n , Li u Xi ul i a n , Xua n Hu i
6
2 试 验 准 备
c e n t e r a n d o t h e r p r o p e r t i e s . Ke y wo r d s : c a r b u r i z i n g s t e e l ; b e ri a n g r i n g s ; c a r b u r i z i n g ; q u e n c h i n g ; t e mp e r ; t e s t
s u r f a c e c a r b o n c o n t e n t a r e r e a c h e d wi t h o u t c o a r s e me s h c a r b i d e o n c a r b u r i z i n g c a s e t e x t u r e S O a s t o ma k e t h e f u nc t i o n i n r e a t me n t S u b — f a c t o r y , H a r b i n B e a r i n g G r o u p C o r p o r a t i o n , Ha r b i n 1 5 0 0 3 6 , C h i n a ; 2 . Be a r i n g R&D C e n t e r , A V I C Ha r b i n B e a r i n g C o . , L t d . , Ha r b i n 1 5 0 0 3 6 , C h i n a)
常见汽车级机床用零件机加热处理工艺路线
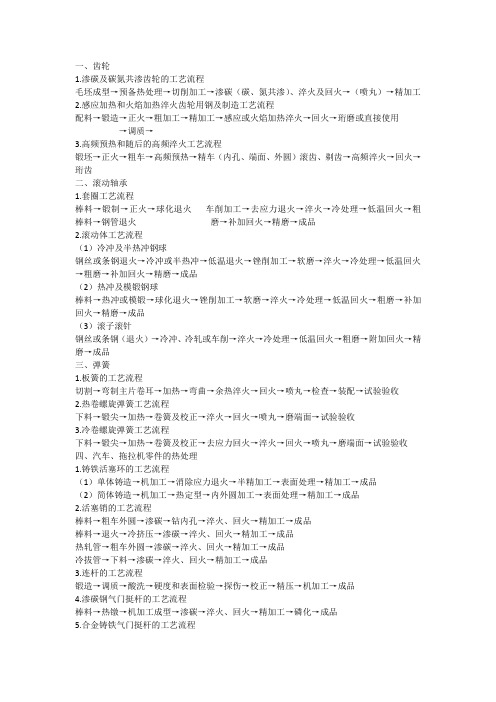
一、齿轮1.渗碳及碳氮共渗齿轮的工艺流程毛坯成型→预备热处理→切削加工→渗碳(碳、氮共渗)、淬火及回火→(喷丸)→精加工2.感应加热和火焰加热淬火齿轮用钢及制造工艺流程配料→锻造→正火→粗加工→精加工→感应或火焰加热淬火→回火→珩磨或直接使用→调质→3.高频预热和随后的高频淬火工艺流程锻坯→正火→粗车→高频预热→精车(内孔、端面、外圆)滚齿、剃齿→高频淬火→回火→珩齿二、滚动轴承1.套圈工艺流程棒料→锻制→正火→球化退火车削加工→去应力退火→淬火→冷处理→低温回火→粗棒料→钢管退火磨→补加回火→精磨→成品2.滚动体工艺流程(1)冷冲及半热冲钢球钢丝或条钢退火→冷冲或半热冲→低温退火→锉削加工→软磨→淬火→冷处理→低温回火→粗磨→补加回火→精磨→成品(2)热冲及模锻钢球棒料→热冲或模锻→球化退火→锉削加工→软磨→淬火→冷处理→低温回火→粗磨→补加回火→精磨→成品(3)滚子滚针钢丝或条钢(退火)→冷冲、冷轧或车削→淬火→冷处理→低温回火→粗磨→附加回火→精磨→成品三、弹簧1.板簧的工艺流程切割→弯制主片卷耳→加热→弯曲→余热淬火→回火→喷丸→检查→装配→试验验收2.热卷螺旋弹簧工艺流程下料→锻尖→加热→卷簧及校正→淬火→回火→喷丸→磨端面→试验验收3.冷卷螺旋弹簧工艺流程下料→锻尖→加热→卷簧及校正→去应力回火→淬火→回火→喷丸→磨端面→试验验收四、汽车、拖拉机零件的热处理1.铸铁活塞环的工艺流程(1)单体铸造→机加工→消除应力退火→半精加工→表面处理→精加工→成品(2)简体铸造→机加工→热定型→内外圆加工→表面处理→精加工→成品2.活塞销的工艺流程棒料→粗车外圆→渗碳→钻内孔→淬火、回火→精加工→成品棒料→退火→冷挤压→渗碳→淬火、回火→精加工→成品热轧管→粗车外圆→渗碳→淬火、回火→精加工→成品冷拔管→下料→渗碳→淬火、回火→精加工→成品3.连杆的工艺流程锻造→调质→酸洗→硬度和表面检验→探伤→校正→精压→机加工→成品4.渗碳钢气门挺杆的工艺流程棒料→热镦→机加工成型→渗碳→淬火、回火→精加工→磷化→成品5.合金铸铁气门挺杆的工艺流程合金铸铁整体铸造(间接端部冷激)→机械加工→淬火、回火→精加工→表面处理→成品合金铸铁整体铸造(端部冷激)→机械加工→消除应力退火→精加工→表面处理→成品钢制杆体→堆焊端部(冷激)→回火→精加工→成品钢制杆体→对焊→热处理→精加工→表面处理→成品6.马氏体型耐热钢排气阀的工艺流程马氏体耐热钢棒料→锻造成型→调质→校直→机加工→尾部淬火→抛光→成品7.半马氏体半奥氏体型耐热钢(Gr13Ni7Si2)排气阀的工艺流程棒料→顶锻→精压→热处理→精加工→成品8.奥氏体耐热钢排气阀的工艺流程棒料→顶锻→精压→阀面和尾部堆焊耐热合金→热处理→杆部滚压或软氮化→精加工→成品9.半轴调质的工艺流程合金结构钢棒料→锻造成形→正火或退火→机械加工→调质→校直→精加工→成品10.半轴的表面淬火的工艺流程棒料→锻造成形→预先热处理→校直→机械加工→表面淬火→校直→精加工→成品11.柱塞副和喷油嘴偶件的工艺流程热扎退火棒料→自动机加工成型→热处理→精加工→时效→成品12.拖拉机履带板(1)40SiMn2履带板的热处理热轧成形→下料→机加工→热处理→成品(2)ZGMn13履带板的热处理铸造成型→热处理→成品五、金属切削机床零件的热处理1.机床导轨(1)MM7125平面磨床立柱镶钢导轨锻造→正火→机加工→消除应力退火→机加工→淬火→回火→磨(2)M9025工具曲线磨床镶钢导轨锻造→退火→机加工→淬火→回火→磨(3)S788轴承磨床镶钢导轨机加工→消除应力退火→机加工→渗碳→淬火→回火→磨→时效(4)MZ208轴承磨床镶钢导轨锻造→退火→机加工→消除应力退火→机加工→淬火→冰冷处理→回火→磨→时效2.机床主轴(1)CA6104车窗主轴(45钢)下料→粗加工→正火→机加工→高频淬火→回火→磨(2)T68、T611镗床的镗杆及MGB132磨床的主轴(35CrMoAlA钢)下料→粗车→调质→精车→消除应力处理→粗磨→渗氮→粗磨(3)SGC630精密丝杠车床主轴(12CrNi3A)锻造→正火→机加工→渗碳→正火→校直→消除应力→机加工→头部淬火→颈部淬火→回火→磨→时效(4)X62W万能升降台铣床主轴(球墨铸铁QT60-2)铸造→机加工→淬火→回火(5)M1040无心磨床主轴(球墨铸铁QT60-2)铸造→机加工→正火→机加工3.丝杠(1)7级或7级精度一下的一般丝杠(45钢)下料→正火或调质→校直→消除应力处理→机加工(2)6级或6级以上精密不淬硬丝杠(T10或T12钢)球化退火→机加工→消除应力处理→机加工→时效→精加工(3)中大型精密淬硬丝杠(CrWMn)锻造→球化退火→机加工→消除应力→机加工→消除应力→机加工→淬火、回火→冰冷处理→回火→探伤→机加工→时效→精加工→时效→精加工(4)中小型精密淬硬丝杠(9Mn2V)锻造→球化退火→机加工→消除应力→机加工→淬硬淬火→回火→冰冷处理→回火、探伤→机加工→时效→精加工→时效→精加工(5)滚珠丝杠(GCr15,GCr15SiMn)4.弹簧卡头(1)卧式多轴自动车床夹料卡头(9SiCr)锻造→退火→机加工→淬火→回火→机加工→磨开口→胀大定型(2)卧式多轴自动车床送料卡头(T8A钢)锻造→退火→机加工→淬火→回火→磨(3)仪表机床小型专用卡头(60Si2)退火→机加工→淬火→回火→磨(4)磨阀辨机床专用卡头(65Mn)锻造→正火→高温→回火→机加工→淬火→回火→机加工5.摩擦片(1)X62W万能升降台铣床摩擦片(A3)机加工→渗碳→淬火→回火→机加工→回火(2)DLMO电磁离合器摩擦片(65Mn)冲片→淬火→回火→磨(3)电磁离合器摩擦片(6SiMnV)锻造→退火→切片→淬火→回火→磨6.FW250万能分度头主轴(45)锻造→正火→机加工→淬火→回火→机加工7.万能分度头蜗杆(20Cr)正火→机加工→渗碳→机加工→淬火→回火→机加工8.三爪卡盘卡爪(45)正火→机加工→淬火→回火→高频淬火→回火→法蓝→磨加工9.三爪卡盘丝(45)锻造→正火→机加工→淬火→回火→法蓝→磨六、活塞1.20CrMnMo钢制活塞的热处理锻造→正火→检验→机加工→渗碳→检验→正火→淬火→清洗→回火→检验→喷砂→磨削2.钒钢活塞的热处理下料→锻造→检验→预先淬火→球化退火→检验→机加工→淬火→回火→检验→磨削七、凿岩机钎尾锻造→退火→检验→渗碳→检验→淬火→回火→清洗→检验→磨削。
薄壁轴承套圈的热处理工艺

热处理中 , 一些外径较大的薄壁轴承套圈按 常规热处理工艺淬火后 , 出现很大的椭圆变形 , 不 得不进行分选 ,对超差的套圈进行修正 。因此 , 应 对薄壁轴承套圈的热处理工艺进行研究 , 以减小 套圈的变形 。
1 热处理变形主要原因
轴承套圈产生变形的主要原因之一是在热处 理加热 、冷却过程中 , 套圈表面与内部热胀冷缩不 均及组织转变不同时产生的热应力和较大组织应 力 。当套圈出现整体的塑性变形时 , 变形表现为 直径方向的胀大或缩小 ; 当出现局部的塑性变形 时则表现为圆度或圆柱度误差加大 。由于淬火油 的冷却速度快 ,远远超过套圈在加热炉里的加热
·28·
《轴承 》2010. №. 1
台循环油泵和一台冷却油泵正常开动 ; 回火温度 180 ℃,回火时间 3 h。
按该工艺热处理后套圈圆度误差较大 , VD sp超 过 0. 20 mm 的占 50%以上 , 因此分选及校正的工 作量很大 。
图 1 6014 - 2RLD外圈车件图
3 热处理工艺试验分析及改进
由新的热处理工艺得到的组织和硬度都符合 JB / T 1255 - 2001《高碳铬轴承钢滚动轴承零件热 处理技术条件 》的要求 。从新 、原热处理工艺处理 的套圈中各随机抽样 100 件 , 测量 VD sp , 结果分别 见表 1及图 2。
可以看出 , 6014 - 2RLD 外圈按原工艺处理
后 , VD sp ≤0. 2 mm 的 外圈 只有 45% , VD sp ≤0. 25 mm 的外圈仅占 73% ; 而按新工艺处理后 , VD sp ≤ 0. 2 mm 的外圈就有 74% , VD sp ≤0. 25 mm 的外圈 达 90% 。因此 ,新的热处理工艺确实能够减小套 圈的变形 。
滚动轴承套圈加工工艺
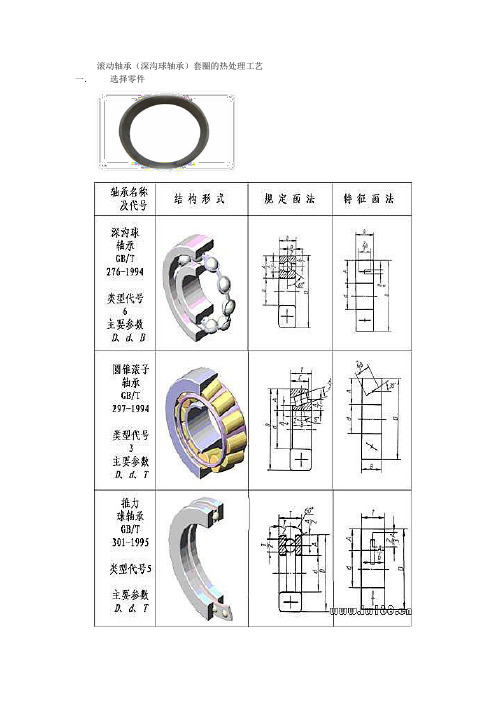
套圈的冷却一般在30~80℃的10号、20号机油中冷却。冷却方法使用分级淬火:在正常奥氏体化温度后,再投入120~170℃的10号机油中冷却2~5分钟,再放入30~60℃10号机油中冷却,为减少残余奥氏体的稳定性,分级淬火后应立即进行冷处理和回火。
5.回火
回火的目的
消除内应力,稳定组织和尺寸,提高圈套的综合机械性能。回火是热处理淬火后必不可少的工序,是决定零件内在质量的关键工序。
四.加工工艺
棒料→锻制→正火→球化退火→车削加工→去应力退火→淬火→冷处理→低温回火→粗磨→补加回火→精磨→成品
1.正火
正火的目的
(1)消除网状碳化物及线条状组织
(2)返修退火的不合格品
(3)为满足特殊性能的需要
(4)为退火做组织准备
加热温度
正火加热温度主要依据正火目的和正火前组织状态来决定。此处正火主要是为了消除或减少粗大网状碳化物,所以正火温度选在930~950℃之间。如果一次正火不能消除粗大网状碳化物,可以以相同温度二次正火。
综上所诉,要求套圈要有1)高的接触疲劳强度2)高的耐磨性3)高的弹性极限4)适宜的硬度5)一定的韧性6)良好的尺寸稳定性7)良好的防锈能力8)良好的工艺性能
三.材料选择
套圈的材料选择一般有6种GCr4 ,GCr15 ,GCr15SiMn ,GCr15SiMo ,GCr18Mo
牌号
C
Si
Mn
Cr
Mo
P
7.热处理设备
7.1.中温箱式电阻炉
此次生产所要的最高温度为950℃。900℃以下的为低温箱式电阻炉,1300℃以上的为高温箱式电阻炉,为节约成本选用中温箱式电阻炉。中温箱式电阻炉适用于中小型钢制机件的淬火、退火、正火热处理。
轴承套圈的材料和最终热处理方法

轴承套圈的材料和最终热处理方法
轴承套圈的材料通常选择高强度、高耐磨损和耐腐蚀的材料。
以下是常用的轴承套圈材料和一种常见的热处理方法:
1. 铬钼合金钢:铬钼合金钢具有较高的硬度和耐磨性,适用于高负荷和高速运转的应用。
对于这种材料,常用的热处理方法是淬火和回火。
淬火可提高材料的硬度,并增加其强度和韧性,而回火可以减轻淬火后的应力,提高材料的耐腐蚀性能。
2. 不锈钢:不锈钢具有良好的耐腐蚀性能,适用于一些特殊环境或要求无锈蚀的应用。
常见的不锈钢材料包括奥氏体不锈钢(如304和316)和马氏体不锈钢(如440C)。
不锈钢的热处理方法包括退火和固溶处理。
3. 铜合金:铜合金具有优良的导热性和抗磨损性能,广泛应用于柔软轴承套圈中。
对于铜合金,常用的热处理方法是固溶处理和时效处理。
需要注意的是,选择轴承套圈的材料和热处理方法应根据具体的应用需求和工作环境来确定,以确保其性能和耐久性能得到最佳发挥。
大直径不锈钢轴承套圈热处理工艺分析

. 0 8 3 } 1
2 0 1 0 O
度 的提高 , 材料 的硬 度先 增 加 后 减 小 , 当淬火 温 度
为 1 6 C时硬度 最 大 , 到 6 R 。 0o 0 达 2H C
图 5 淬 火温度对残余奥 氏体含量的影响
甚
三
型
+ 三 量
图 6 淬 火 温度 对 冲 击 功 的 影 响
摘要 : 分析了热处理工艺参数对 9 r8大直径不锈钢轴承套 圈力学性 能的影响 , C1 介绍 了大直径 、 壁厚不锈钢 小 轴承套圈的畸变控制措施。试验结果表明 : C 1 9 r8大直径轴承套圈经 1 6 C 0o 淬火 +一 0℃深冷处理 +10℃ 0 7 6 低温回火处理后 , 各项性能指标 均满足技术要求。
2 2 冷处 理 温度 和 回火 温度 对 硬度 的影 响 .
冷处 理温 度及 回火 温 度 对 硬 度 的影 响分 别 见
图 3和 图 4 由图可 以看 出 , 。 随着冷 处理 和 回火温
・
4 4・
《 轴承) m0 №. 2 . 7
110c淬 火 , 下降 到室 温 以下 。 因此 , 火 温 5 = I Ms 淬 度越 高 , 残余 奥氏体量 越多 。 随着马 氏体 中含 碳 量 和合 金元 素 量 的增 加 , 马 氏体 被强化 , 同时残余 奥 氏体 量 也在 增 加 , 这两
/
∞ 鼹 卯
、
壹
径 变动 量 ≤2 0 m 端 面 翘 曲 ≤1 1mm( 械 加 . m, . 机 工 工艺 对热 处理 的要 求 ) ( ) 、 ;3 淬 回火组 织按J / BT
16 准 第 二 级 别 图评 定 , 4 0标 2~5级 为 合 格 组 织 ,
- 1、下载文档前请自行甄别文档内容的完整性,平台不提供额外的编辑、内容补充、找答案等附加服务。
- 2、"仅部分预览"的文档,不可在线预览部分如存在完整性等问题,可反馈申请退款(可完整预览的文档不适用该条件!)。
- 3、如文档侵犯您的权益,请联系客服反馈,我们会尽快为您处理(人工客服工作时间:9:00-18:30)。
淬火:将钢加热到Ac1以上30°—50°,保温一段时间,之后以大于临界速度的速度冷却,得到马氏体的方法。
高碳铬轴承钢的淬火温度一般是830°—860°,在实际生产中800°—860°都能淬火合格,对于薄壁套圈可以适当降低温度,以减小变形。
对于壁厚较厚的套圈,可选择较高的温度淬火,可以增加淬透性。
晶格分为:体心、面心、密排六方。
膨胀量:冷碾扩>冷轧管>锻件>冷拔
珠光体:铁素体+渗碳体的机械混合物
奥氏体:碳在γ-铁中形成的固溶体
马氏体:碳在α-铁中形成的固溶体
轴承钢含碳量0.95%-1.05%,加热到735°开始向奥氏体转变,继续加热到765°转变结束。
Cr元素加入后,钢的淬透性增加A3线下降,Acm线左移,固相线JE降低奥氏体区减小,使加热时的过烧温度下降。
一般球化退火温度780°-800°
图1.轴承套圈球化退火曲线
套圈球化退火>20h钢管球化退火>13h
图2.轴承套圈淬火曲线
冷处理是为了稳定残余奥氏体,回火(大于4h)是为了消除内应力,稳定组织。
针状屈氏体:冷却不足
块状屈氏体:加热不足
残余奥氏体的危害:
回火不充分,会使零件边磨边变。
工件的表面颜色的影响因素:
淬火前,产品不清洁、炉子密封性不好、保护气氛不好、炉内油烟大、淬火油问题。
影响产品外观,影响轴承噪声和寿命。
边磨边变的原因:
淬火温度高,加热时间长、残余奥氏体多、冷处理温度高、回火温度低,时间长、抛光时间长造成内应力大。