关键零部件和材料确认检验作业指导书
来料检验作业指导书
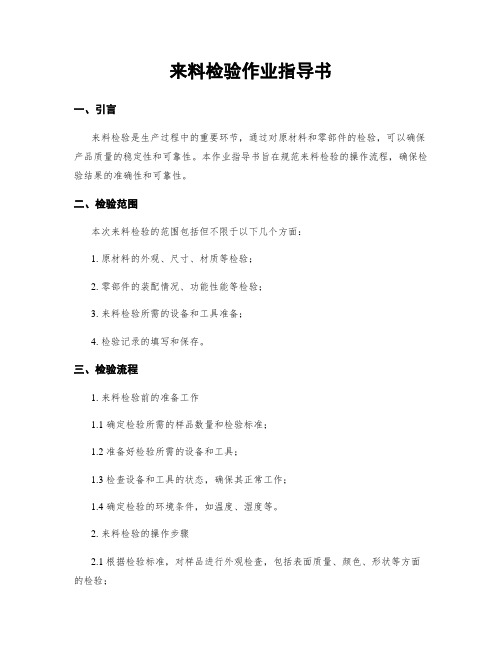
来料检验作业指导书一、引言来料检验是生产过程中的重要环节,通过对原材料和零部件的检验,可以确保产品质量的稳定性和可靠性。
本作业指导书旨在规范来料检验的操作流程,确保检验结果的准确性和可靠性。
二、检验范围本次来料检验的范围包括但不限于以下几个方面:1. 原材料的外观、尺寸、材质等检验;2. 零部件的装配情况、功能性能等检验;3. 来料检验所需的设备和工具准备;4. 检验记录的填写和保存。
三、检验流程1. 来料检验前的准备工作1.1 确定检验所需的样品数量和检验标准;1.2 准备好检验所需的设备和工具;1.3 检查设备和工具的状态,确保其正常工作;1.4 确定检验的环境条件,如温度、湿度等。
2. 来料检验的操作步骤2.1 根据检验标准,对样品进行外观检查,包括表面质量、颜色、形状等方面的检验;2.2 使用相应的测量工具对样品的尺寸进行测量,并与标准值进行比对;2.3 对样品的材质进行检验,可以使用化学分析、物理性能测试等方法;2.4 对样品的装配情况进行检验,确保零部件的连接坚固、无松动等;2.5 对样品的功能性能进行检验,如电气性能、机械性能等;2.6 检查样品的包装情况,确保无损坏和污染;2.7 根据检验结果,判定样品的合格与否,并记录检验结果。
四、数据分析与处理1. 对于合格的样品,按照规定的流程进行入库操作;2. 对于不合格的样品,应即将通知供应商,并进行退货或者重新加工等处理;3. 对于检验结果的统计和分析,可以采用图表、报表等方式进行展示,并及时通知相关部门。
五、检验记录与保存1. 检验记录应详细、准确地记录检验过程和结果,包括样品信息、检验项目、检验方法、检验结果等;2. 检验记录应由检验人员签字确认,并及时归档保存,以备查阅。
六、安全注意事项1. 在进行来料检验时,应确保操作人员的人身安全,如佩戴防护设备、遵守操作规程等;2. 对于有毒、有害或者易燃易爆物品的检验,应采取相应的安全措施,如通风设备、防爆措施等。
来料检验作业指导书
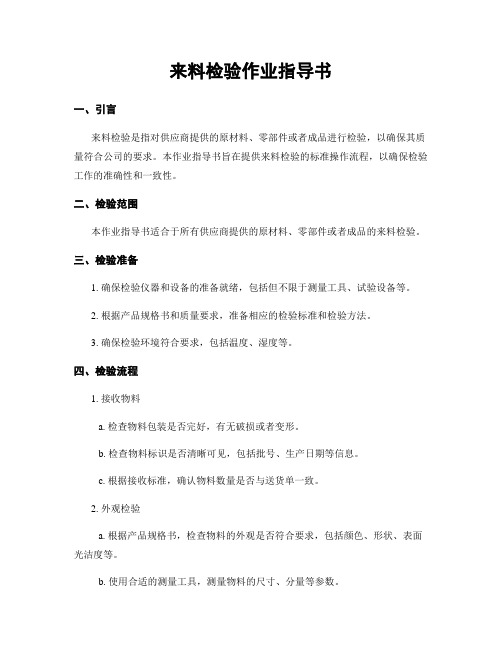
来料检验作业指导书一、引言来料检验是指对供应商提供的原材料、零部件或者成品进行检验,以确保其质量符合公司的要求。
本作业指导书旨在提供来料检验的标准操作流程,以确保检验工作的准确性和一致性。
二、检验范围本作业指导书适合于所有供应商提供的原材料、零部件或者成品的来料检验。
三、检验准备1. 确保检验仪器和设备的准备就绪,包括但不限于测量工具、试验设备等。
2. 根据产品规格书和质量要求,准备相应的检验标准和检验方法。
3. 确保检验环境符合要求,包括温度、湿度等。
四、检验流程1. 接收物料a. 检查物料包装是否完好,有无破损或者变形。
b. 检查物料标识是否清晰可见,包括批号、生产日期等信息。
c. 根据接收标准,确认物料数量是否与送货单一致。
2. 外观检验a. 根据产品规格书,检查物料的外观是否符合要求,包括颜色、形状、表面光洁度等。
b. 使用合适的测量工具,测量物料的尺寸、分量等参数。
3. 功能性检验a. 根据产品规格书和质量要求,进行相应的功能性检验,如电气性能、机械性能等。
b. 使用合适的试验设备,对物料进行功能性验证。
4. 化学成份检验a. 根据产品规格书和质量要求,进行化学成份的检验。
b. 使用适当的化学分析方法,对物料进行化学成份的分析。
5. 物理性能检验a. 根据产品规格书和质量要求,进行物理性能的检验,如硬度、强度等。
b. 使用合适的测量工具和试验设备,对物料进行物理性能的测试。
6. 检验记录与报告a. 在检验过程中,及时记录检验结果和相关数据。
b. 生成检验报告,包括检验结果、不合格项、原因分析等信息。
五、不合格品处理1. 对于不合格品,根据公司的不合格品管理程序进行处理,包括但不限于退货、返修、报废等。
2. 记录不合格品的处理过程和结果,以便追溯和改进。
六、检验员培训1. 定期对检验员进行培训,确保其熟悉本作业指导书中的检验流程和方法。
2. 培训内容包括但不限于检验仪器的使用、检验标准的理解和应用等。
进货检验作业指导书
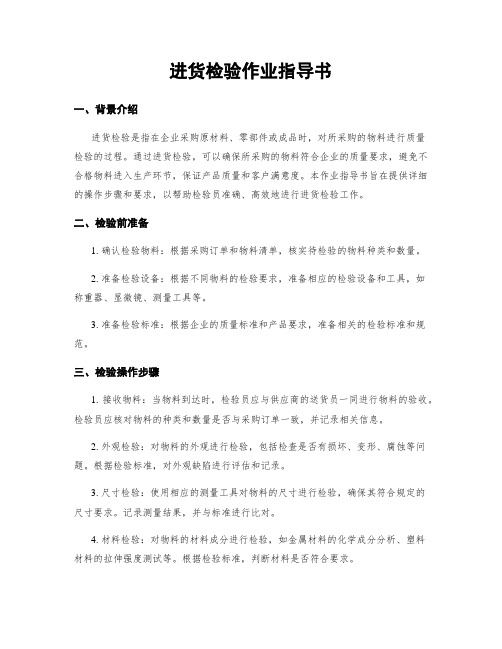
进货检验作业指导书一、背景介绍进货检验是指在企业采购原材料、零部件或成品时,对所采购的物料进行质量检验的过程。
通过进货检验,可以确保所采购的物料符合企业的质量要求,避免不合格物料进入生产环节,保证产品质量和客户满意度。
本作业指导书旨在提供详细的操作步骤和要求,以帮助检验员准确、高效地进行进货检验工作。
二、检验前准备1. 确认检验物料:根据采购订单和物料清单,核实待检验的物料种类和数量。
2. 准备检验设备:根据不同物料的检验要求,准备相应的检验设备和工具,如称重器、显微镜、测量工具等。
3. 准备检验标准:根据企业的质量标准和产品要求,准备相关的检验标准和规范。
三、检验操作步骤1. 接收物料:当物料到达时,检验员应与供应商的送货员一同进行物料的验收。
检验员应核对物料的种类和数量是否与采购订单一致,并记录相关信息。
2. 外观检验:对物料的外观进行检验,包括检查是否有损坏、变形、腐蚀等问题。
根据检验标准,对外观缺陷进行评估和记录。
3. 尺寸检验:使用相应的测量工具对物料的尺寸进行检验,确保其符合规定的尺寸要求。
记录测量结果,并与标准进行比对。
4. 材料检验:对物料的材料成分进行检验,如金属材料的化学成分分析、塑料材料的拉伸强度测试等。
根据检验标准,判断材料是否符合要求。
5. 功能性检验:对物料的功能进行检验,如电子产品的电气性能测试、机械产品的运转测试等。
根据产品要求,进行相应的功能性测试,并记录测试结果。
6. 包装检验:对物料的包装进行检验,包括包装完整性、防潮性、防震性等。
根据检验标准,评估包装的质量,并记录相关信息。
7. 样品留存:根据企业的要求和产品特点,留存一定数量的样品作为备案和后续检验的参考。
四、检验结果处理1. 合格品处理:对于经检验合格的物料,可以进入下一生产环节或仓储环节。
记录合格品的数量和相关信息。
2. 不合格品处理:对于经检验不合格的物料,应及时与供应商联系,协商处理方式,如退货、更换等。
摩托车关键零部件和材料的检验验证和定期确认检验程序

考查其是否持续符合质量要求。
4.4.2 定期确认检验的“关键零部件”,控制要求按照表 1 规定执行。
名称
发动机 轮胎 轮辋
车轮 制动器
检验项目
依据标准
怠速排放、标定功率、最 大扭矩、最低燃油消耗率
QC/T29117.7-93 GB14621-2002 GB/T5363-1995
轮胎外缘尺寸测定
GB/T521-93
设备精度:
5)热衰退试验
测量和记录转速、转矩和温度
6)热恢复试验
仪器精度±1%;转速、温度的控制
7)最终效能
精度±2%;转动惯量精度±5%;制
8)水衰退性能
动时间间隔精度±10%
9)水恢复性能
10)耐温性能;(20/70 小
时)
11)耐久性能(500 小时)
12)液压制动器密封性试
验
13)拖带力矩试验
4.3.7 进货检验员及时对供应部门的进货物料进行统计、汇总,并填写《合格供应商供货业绩单》,
作为对供应商下年评定合格供方评估的依据。
4.4 关键零部件、材料定期确认检验
4.4.1 技术部应对所购关键零部件和 材料,制订检验项目、检查标准、频次等,提出具体要求,
按《关键零部件和材料定期确认检验控制要求》执行,并与供应商签定《合同书》、《技术协议》
轮胎强度试验
GB/T13203-1991
轮胎耐久性能检验
GB/T13204-2002
轮胎高速性能检验
GB/T13205-1991
GB/T1518-1997
轮辋断面尺寸对称度)(切 QC/T 71-1993
取式样,投影测量)
QC/T 722-2004
标定直径周长极限偏差; QC/T 723-2004
原材料检验作业指导书

1.目的
对原材料进货进行检查(抽检),宏观控制制品的质量,向客户提供合格产品。
2.适用范围
适用XXX所有进货的原材料。
3.职责
质量技术部负责实施此项工作。
每批次原材料按《零部件抽检比例表》进行抽取检验并做好记录。
4.来料检验
4.1外观确认:
确认来料外形状态:金属加工件按图纸进行确认,并有抽检尺寸记录。
化学品粉末、颜色、颗粒、杂质等。
4.2对于新批次的原材料,核对供应商的《出厂检验报告》,进行对比判定。
4.3包装确认
主要是产品整体包装是否合格,要求无脏污、破损、变形、泄
漏;
包括标签、批号、产地、品名、生产日期、保质期、注意事项等。
4.4称重
对每一批次的原材料包装进行称重确认,进行抽检,并做好记录。
4.5标识标签
对每一批次的原材料确认合格后进行标识区分,“蓝色贴”表示前一批次的标识。
如新进的原料材料不用标识,进行区分批次。
批次号用标签进行标识。
4.6合格入库
对于抽检后的原材料通知生产部进行入库,可使用。
5.记录(填写如下表)。
冲压件检验作业指导书(两篇)

引言概述:冲压件是一种常见的金属加工零部件,广泛应用于汽车、家电、机械等领域。
为了确保冲压件的质量,提高生产效率和产品可靠性,进行冲压件检验工作是至关重要的。
本文是冲压件检验作业指导书的第二部分,旨在提供详细的工作指导,帮助检验员正确执行冲压件检验任务。
正文内容:一、检验前准备1.准备检验设备和工具:包括显微镜、测量工具(卡尺、千分尺、测微计等)、外观检验工具(手电筒、放大镜等)等。
2.准备冲压件技术标准和图纸:检验员需要熟悉冲压件的技术标准和图纸,了解要求的尺寸、外观等要求。
3.准备检验记录表格:根据实际需求,准备相关的检验记录表格,方便记录检验结果。
二、尺寸检验1.测量尺寸:使用合适的测量工具,按照冲压件的技术标准和图纸上的要求,测量冲压件的各个尺寸。
2.校验测量工具:定期校验测量工具,确保其准确性。
校验工具时,可以使用已知尺寸的标准样品进行比对,校验结果应在允许范围内。
3.记录尺寸:将测量结果记录在检验记录表格中,及时发现异常尺寸并进行记录。
三、外观检验1.观察表面缺陷:使用手电筒、放大镜等工具,仔细观察冲压件表面是否存在破损、划痕、氧化等缺陷。
2.检测涂层质量:如冲压件表面有涂层,利用视觉和手感,观察涂层是否均匀、无起皱、无脱落等。
3.检查装配性能:如冲压件需要用于装配,可以进行装配试验,检查冲压件的装配性能,确保其能够正常使用。
四、材料检验1.材料标识检查:检查冲压件上的材料标识是否清晰、准确,与技术要求一致。
2.化学成分分析:根据需要可以进行化学成分分析,以验证材料的成分符合要求。
3.硬度检验:使用硬度测量仪器,对冲压件进行硬度检验,确认其硬度符合技术要求。
五、其他检验1.物理性能检验:如冲压件需要承受一定的载荷或振动,可以进行物理性能检验,包括强度、刚性等。
2.功能性能检验:如冲压件需要具备特定的功能,可以进行功能性能检验,确保其能够满足产品要求。
3.环境适应性检验:对于要求耐腐蚀等特殊环境要求的冲压件,需要进行相应的环境适应性检验。
来料检验作业指导书
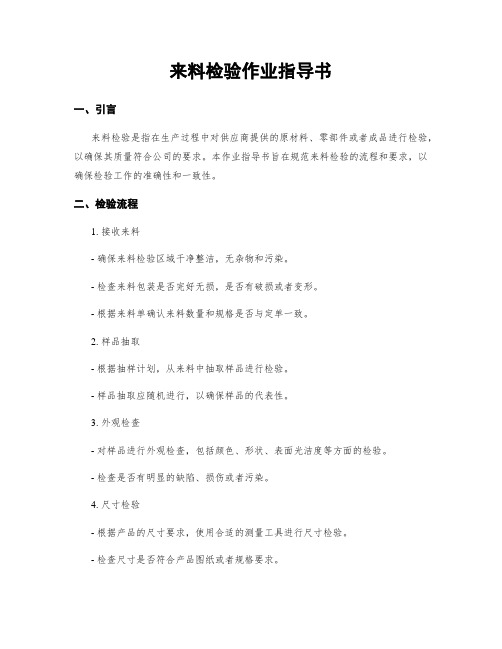
来料检验作业指导书一、引言来料检验是指在生产过程中对供应商提供的原材料、零部件或者成品进行检验,以确保其质量符合公司的要求。
本作业指导书旨在规范来料检验的流程和要求,以确保检验工作的准确性和一致性。
二、检验流程1. 接收来料- 确保来料检验区域干净整洁,无杂物和污染。
- 检查来料包装是否完好无损,是否有破损或者变形。
- 根据来料单确认来料数量和规格是否与定单一致。
2. 样品抽取- 根据抽样计划,从来料中抽取样品进行检验。
- 样品抽取应随机进行,以确保样品的代表性。
3. 外观检查- 对样品进行外观检查,包括颜色、形状、表面光洁度等方面的检验。
- 检查是否有明显的缺陷、损伤或者污染。
4. 尺寸检验- 根据产品的尺寸要求,使用合适的测量工具进行尺寸检验。
- 检查尺寸是否符合产品图纸或者规格要求。
5. 功能检验- 对样品进行功能性测试,确保其满足产品的设计要求。
- 根据产品的功能要求,使用相应的测试设备进行测试。
6. 化学成份分析- 对样品进行化学成份分析,以确定其成份是否符合要求。
- 使用合适的化学分析仪器和方法进行分析。
7. 物理性能测试- 对样品进行物理性能测试,如强度、硬度、耐磨性等方面的检验。
- 使用合适的测试设备和方法进行测试。
8. 检验结果记录- 将检验结果记录在检验报告中,包括样品信息、检验项目、检验结果等。
- 检验报告应有明确的标识,以便追溯和审核。
9. 判定结果- 根据检验结果和产品要求,对样品进行判定,判断是否合格或者不合格。
- 合格样品可放行使用,不合格样品需进行退货或者重新加工。
10. 不合格品处理- 对不合格样品进行处理,包括退货、返修或者报废等。
- 不合格品的处理应符合公司的相关流程和要求。
三、检验要求1. 检验设备和工具应符合国家标准或者行业标准,并定期进行校准和维护。
2. 检验人员应具有相关的专业知识和技能,并经过培训和考核合格。
3. 检验记录应保存至少一年,以备追溯和审核。
来料检验作业指导书
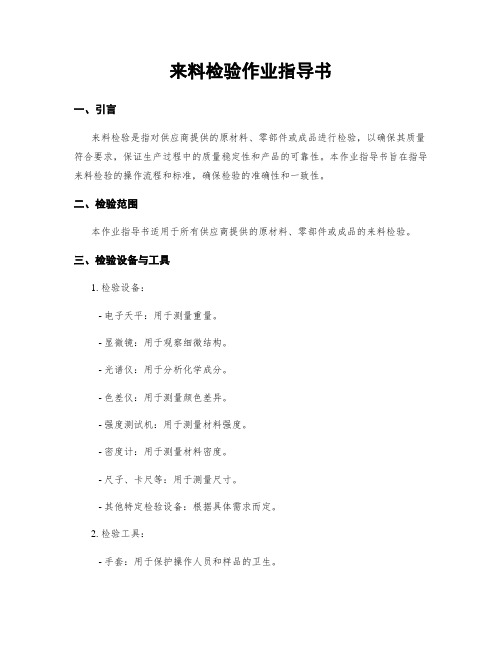
来料检验作业指导书一、引言来料检验是指对供应商提供的原材料、零部件或成品进行检验,以确保其质量符合要求,保证生产过程中的质量稳定性和产品的可靠性。
本作业指导书旨在指导来料检验的操作流程和标准,确保检验的准确性和一致性。
二、检验范围本作业指导书适用于所有供应商提供的原材料、零部件或成品的来料检验。
三、检验设备与工具1. 检验设备:- 电子天平:用于测量重量。
- 显微镜:用于观察细微结构。
- 光谱仪:用于分析化学成分。
- 色差仪:用于测量颜色差异。
- 强度测试机:用于测量材料强度。
- 密度计:用于测量材料密度。
- 尺子、卡尺等:用于测量尺寸。
- 其他特定检验设备:根据具体需求而定。
2. 检验工具:- 手套:用于保护操作人员和样品的卫生。
- 清洁布:用于清洁样品和检验设备。
- 样品容器:用于存放样品。
- 样品标签:用于标识样品信息。
- 记录表格:用于记录检验结果。
四、检验流程1. 接收样品:- 检查样品包装是否完好,有无破损或渗漏。
- 核对样品标签与实际样品是否一致。
- 登记样品信息,包括供应商、批次号、生产日期等。
2. 外观检验:- 观察样品外观,检查有无明显瑕疵、污染或变形。
- 根据产品要求,检查颜色、光泽、纹理等特征。
- 拍照记录样品外观。
3. 尺寸检验:- 使用尺子、卡尺等工具测量样品的尺寸。
- 比对测量结果与产品要求的尺寸范围。
- 记录尺寸测量结果。
4. 化学成分检验:- 根据产品要求,选择适当的检验方法。
- 使用光谱仪等设备,分析样品的化学成分。
- 比对分析结果与产品要求的化学成分范围。
- 记录化学成分检验结果。
5. 物理性能检验:- 根据产品要求,选择适当的检验方法。
- 使用强度测试机、密度计等设备,测量样品的物理性能。
- 比对测量结果与产品要求的物理性能范围。
- 记录物理性能检验结果。
6. 其他特殊检验:- 根据具体产品要求,进行特殊检验。
- 使用相应的检验设备和工具,进行检验。
- 比对检验结果与产品要求的特殊要求。
- 1、下载文档前请自行甄别文档内容的完整性,平台不提供额外的编辑、内容补充、找答案等附加服务。
- 2、"仅部分预览"的文档,不可在线预览部分如存在完整性等问题,可反馈申请退款(可完整预览的文档不适用该条件!)。
- 3、如文档侵犯您的权益,请联系客服反馈,我们会尽快为您处理(人工客服工作时间:9:00-18:30)。
作 业 指 导 书 文件名关键零部件和材料确认检验作业指文件编号:
受控正本 编制: 审核: 批准:
受控副本 第 2页 共 7页
作业指导书 标题 : 关键零部件和材料确认检验作业指导书 文件修改情况记录 版次/ 页次 修 改 内 容 修改人 审核 批准 日期
A
B 第 3页 共 7页
作业指导书 标题 : 关键零部件和材料确认检验作业指导书 1、目的 : 依据 3C强制性认证或 CQC标志认证实施规则的要求,对关键零部件和材料进定期抽样进行确 认检验,确保其质量满足认证产品要求。
2、适用范围 适用于公司所有 3C 认证或 CQC标志认证产品的关键零部件和材料的定期确认检验 。
3、职责 品管部:负责关键零部件和材料的定期确认检验 。
4、定义 关键零部件和材料 关键零部件和材料:是指各型号对应的产品 型式试验报告 所附 “元件”清单中列出的零部 件/ 材料。
5、程序
5.1 确认检验方式
各关键零部件 /材料,品管部 IQC必须定期进行确认检验。检验的方式可以任选以下方式: 1)当每批来料检验时必须要上网查询供应商 CCC/CQC 认证证书的有效性。
2)要求供应商提交有效的确认检验报告;
3)抽样送样到 CNAS 认可测试能力的检测机构进行检验(如新宝产品验证中心或其它第
三 方机构);
5.2 认证证书有效性查询
5.2.1 若是通过 3C或CQC认证(即元件清单中有注明 3C或 CQC认证编号)的零部件
和材料, 则由品管部 IQC 在每批来料时去 CQC网上查询其认证是否仍然有效。 5.2.2 查询方法为登录 CQC以下地址
“ www.cqc.com.cn/Chinese/search/index.asp ” 输入零部件和材料的认证编号,直接查询证书是否有效。若“现状态”栏显示为“有效”, 同时网站中显示零部件的厂家、产品名称、型号 / 规格与认证报告、实物一致,可认定该 零部件的认证仍然是有效的,则判定该零部件或材料确认验证合格。 5.2.3 若查询时状态栏显示为“暂停”或“失效”、“找不到证书”、或显示的厂
家、 产品名称、型号 / 规格与认证报告、实物不一致时,可认定该零部件的认证有问
5、 第 4页 共 7页
题,则判 作业指导书 标题 : 关键零部件和材料确认检验作业指导书 定该零部件或材料确认验证不合格。 5.2.4 查询完后,在《关键零部件和材料确认检验记录表》中记录查询的零部件名称、
认证编号、查询日期、查询结果等。 5.3 确认检验报告
5.3.1 PMC 部要求供应商提供一年内由有资质的检测机构出具的合格的产品型式试验报
告, 并对检验报告进行检查; 5.3.2 如供应商无法提供有效的产品型式试验报告, 由技术工程部会同质量管理科将采
购的 关键零部件和材料送有资质的检测机构进行检验,并对检验报告进行检查。
5.4 其它确认检验方式
5.4.1 针对型式试验报告 中有列出 ,但本身是没有 3C或 CQC认证零部件和材料
(如塑胶材 料、发热管等),则需供应商提供在规定的时间内提供有效的检测报告,或者定期抽样送 样到 CNAS 认可测试能力的检测机构进行检验 (如新宝产品验证中心或其它第三方机构) 5.4.2 检验的项目、要求、频次等具体参考附件 8.1 《相关零部件确认检验要求》。
5.4.3 确认检验过程中若出现不合格,则及时通知相关部门处理,具体按《不合格品
管理 程序》处理。
6. 相关文件
6.1 《不合格品管理程序》
7. 相关记录
7.1 《关键零部件和材料确认检验记录表》
8. 附件:
8.1 《相关零部件确认检验要求》 第 5页 共 7页
作业指导书 标题 : 关键零部件和材料确认检验作业指导书 8.1 相关零部件确认检验要求
序号 元件 名称 检验项目 检验要求 检验方法 (仪 器)
1 电 源 插 头
标志 标志内容及符号符合规定要求,且经久耐用清晰可辨 方法一、送到第三
方检测机构检验。
方法二:要求厂家 在规 定 的时 间 内 (每三批货 )提交有 效的检验报告。
方法三、定时上网 查询供应商 CCC 证书的有效性
方法一、送到第三 方检测机构检验。
方法二:要求厂家 在规 定 的时 间 内 (每三批货 )提交有 效的检验报告。
方法三、定时上网 查询供应商 CCC 证书的有效性 结构、尺寸 插头尺寸应符合有关标准要求,插头应有足够的机械强度 电气强度和绝缘电阻 500V 兆欧表不得小于 5 兆欧 2000V 1min 100mA 无闪络击 穿 爬电距离和和电气间隙 爬电距离大于 4mm 电气间隙大于 3mm 绝缘材料的耐非正常 热、耐燃 650℃灼热丝试验 2 电 源 线 标志 标志内容及符号符合规定要求,且经久耐用清晰可辨 结构 导体、绝缘、填充、内护层、护套应符合要求 绝缘电阻和电气强度 大于 0.011 兆欧 km(2×1.0m ㎡ ) 2000V 5min 100mA 无闪络 击穿 3 器具 耦合 器 标志 标志和内容清晰可辨符合规定的要求,且经久耐用 爬电距离和电气间隙 爬电距离和电气间隙大于 3mm. 绝缘电阻和电气强度 500V 兆欧表不得小于 5M 2000V 1min 100mA 无闪络击穿 绝缘材料的耐非正常热 和耐燃 750 ℃和 650℃灼热丝试验 4 温控 器 标志 标志内容及符号符合规定要求,且经久耐用清晰可辨 绝缘电阻和电气强度 500V 兆欧表不得小于 5M 2000V 1min 100mA 无闪络击穿 发热 控制器在正常使用时温度不应过高,限定值见标准。 制造偏差和漂移 2 型动作控制器应符合规定的制造偏差和漂移 机械强度 能承受( 0.5±0.04 )Nm 的冲击试验 . 电气间隙、爬电距离绝 缘穿通距离 爬电距离大于 8mm 电气间隙大于 6mm( 加强绝缘 ) 耐热性、耐燃性 650℃灼热丝试验 5 热熔 断器 标志 标志内容及符号符合规定要求,且经久耐用清晰可辨 绝缘电阻和电气强度 500V 兆欧表不得小于 5M 2000V 1min 100mA 无闪络击穿 发热 控制器在正常使用时温度不应过高,限定值见标准。 爬电距离和电气间隙 爬电距离大于 8mm 电气间隙大于 6mm( 加强绝缘 耐热耐燃 5℃球压试验、 650℃灼热丝试验 6 电 路 板 P C B 板 外观、标志与尺寸 标志内容及符号符合规定要求 合格性通过测量来检验,具体部位及限定值见标准 球压试验 施加 20N的力,体持 1 小时进行球压试验, 球压温度: 125℃ 压 痕直径应小于 2MM 灼热丝试验 BWT 750℃试验条件下,应该未起燃眉
针焰试验 应符合标准规定要求。 第 6页 共 7页
作业指导书 标题 : 关键零部件和材料确认检验作业指导书
7 快速 连接 端子 插拔力测试 根据《 65-03-WI-226 》测试端子的插拔力应符合要求
方法一、送到第三 方检测机构检验。
方法二:要求厂家 在规 定 的时 间 内 (每三批货 )提交有 效的检验报告。
方法三、上网查询 供应商 CCC 证书 的有效性
外观与尺寸 合格性通过测量来检验,需要符合产品图纸要求及标准规定 8 外壳 外观、标志与尺寸
标志内容及符号符合规定要求
合格性通过测量来检验,具体部位及限定值见标准
球压试验 施加 20N的力,体持 1 小时进行球压试验, 球压温度: 75℃ 压 痕直径应小于 2MM 灼热丝试验 GWT 550℃试验条件下,应该未起燃
9 压力 行程 开关 标志 标记内容及符号符合规定要求且经久耐用清晰可辨
绝缘电阻和电气强度 500V兆欧表 1min 不得小于 2 兆欧 1250V 1min 100mA
发热 开关在正常使用时的温度不应过高 , 限定值见标准 .
耐久性 能经受电气和和热的耐久性
10 内 部 布 线
机械强度 能承受 (0.5 ±0.04)Nm 的冲击试验
电气间隙 ,爬电距离和绝 缘穿通距离 爬电距离大于 8mm电气间隙大于 6mm(加强绝缘 )
耐热性 ,耐燃性 650℃灼热丝试验 外观 布线槽应平滑没有锐边 , 布线有保护 . 金属导线孔也应有保护 . 布线与运动部件隔开 , 相应位置应该有绝缘层 . 弯曲试验 按标准要求的弯曲试验后无损坏 电气强度 带电部件与金属部件间应经受 1000V 的电气强度试验
电气应力 内部布线的绝缘应能经受正常使用中可能出现的电气应力
11 电机
耐热性 ,耐燃性 导线和包裹在绝缘层外面的金属箔之间施加 2000V电压. 持续 15min, 不应该击穿 . 介电强度 击穿电流值不应大于 10mA.
空载试验 测试过程中,产品不能出现火灾、电击等安全隐患。试验后, 待电机冷却到室温再进行 1000V/1min 的耐压测试, 不得有被 击穿的 现象。
匝间绝缘 试验过程中要求电动机应无冒烟、火花、击穿等现象
泄漏电流 ─ 对 I 类便携式器具,应≤ 0.75mA; ─ 对 II 类器具,应≤ 0.25mA
12 发热 管
堵转试验 绕组温度不应超过规定值, 试验期间, 不得出现闪络活有熔化 金属的现象。堵转试验后,待产品冷却到室温进行耐压测试。 方法一、送到第三
方检测机构检验。
方法二:要求厂家 在规 定 的时 间 内 (每三批货 )
温升试验 试验后的绕组限值不得超过规定值
非正常试验 试验后待产品冷却到室温还应进行 1000V/1min 的耐压测试。
标志 标志内容及符号符合规定要求,且经久耐用清晰可辨 绝缘电阻和电气强度 500V 兆欧表不得小于 2M 1000V 1min 100mA 无闪络击穿
功率 在标准偏差范围内