SPC常用计算方法
SPC各值计算公式

SPC各值计算公式SPC(统计过程控制)是一种统计方法,用于检测和控制过程的稳定性和变异性。
SPC各值计算公式包括控制图参数和过程能力指数等。
以下是常见的SPC各值计算公式及其解释:1.控制图参数:a.X̄控制图上的中心线是过程的平均值的估计量。
计算公式为:X̄=ΣX/n,其中X是测量值的总和,n是样本大小。
b. R 控制图上的极差线是过程的极差的估计量。
计算公式为:R = Xmax - Xmin,其中Xmax和Xmin是样本中最大值和最小值。
c.S控制图上的标准偏差线是过程的标准偏差的估计量。
计算公式为:S=√(Σ(X-X̄)²/(n-1)),其中Σ(X-X̄)²是样本值与平均值的差的平方的总和。
d.UCL控制图上的上限控制限是过程的可接受上限。
计算公式为:UCL=X̄+3S,其中3是标准差的倍数,用于确定上限控制限。
e.LCL控制图上的下限控制限是过程的可接受下限。
计算公式为:LCL=X̄-3S,其中3是标准差的倍数,用于确定下限控制限。
2.过程能力指数:a.Cp过程能力指数是衡量过程发生误差在可接受范围内的能力。
计算公式为:Cp=(USL-LSL)/(6σ),其中USL和LSL是规范上限和下限,σ是标准偏差的估计量。
b. Cpk 过程能力指数是衡量过程发生误差在可接受范围内的能力,同时考虑了过程的中心线偏移。
计算公式为:Cpk = min((USL - X̄) /(3σ), (X̄ - LSL) / (3σ)),其中USL和LSL是规范上限和下限,X̄是过程的平均值的估计量,σ是标准偏差的估计量。
c. Cpm 过程能力指数是衡量过程发生误差在可接受范围内的能力,同时考虑了过程的中心线偏移和过程的极差。
计算公式为:Cpm = (USL - LSL) / (6√((ΣR/n)² + σ²)),其中USL和LSL是规范上限和下限,ΣR/n是极差均值的估计量,σ是标准偏差的估计量。
SPC计算公式

計
量 值 概 念
多品質特性圖
基礎篇
7.品質指標:
5.
USL :規格上限 SL :規格中心值
品質規格要求
計
量 值 概 念
LSL :規格下限
XUCL:Xbar管制圖的管制上限 Xbar: Xbar管制圖的中心值 XLCL:Xbar管制圖的管制下限 RUCL:Rbar管制圖的管制上限 RBar:Rbar管制圖的中心值 RLCL:Rbar管制圖的管制下限 Ca Cp Cpk PPM :製程准确度 製程精密度(製程潛力) 製程能力 Parts Per Million
σa是統計上的標準差概念, 即是按上述公式計算出來的 σs是為了在品管中有一個相對比較值而引進的, 計算方法是 σs=(USL-LSL)/6
技術篇
2.管製界限
1.
S P C 的 品 質 指 標
管製中心線(Center Line):
即實際數據的平均值(即Xbar)
CL=Xbar 管製上限(Upper Control Level, 縮寫為UCL):
LCL CL UCL
B.單邊上限規格
Cp=(USL-CL)/3σa=CpU
LCL
SL CL
USL UCL
技術篇
3.品質指標
1.
S P C 的 品 質 指 標
製程能力指數(Cpk):
A.雙邊規格 Cpk= (1-Ca)*Cp B.單邊上限規格 CPK=CPU=Cp C.單邊下限規格 CPK=CPL=C p
技術篇
3.品質指標
1.
C.單邊下限規格
LSL LCL SL CL USL UCL
S P C 的 品 質 指 標
Cp=(CL-LSL)/3σa=CpL
SPC计算公式

S P C 的 品 質 指 標
組距(R) : 一組數據中的最大值減最小值 R=MAX-MIN 平均數(Mean, 但通常用Xbar或X表示): 把一組數據 全部相加, 再除以該組數據的個數.
X=(X1+X2+……Xn)/n
中位數(Median,通常用M表示): 把一組數據先按大小順序排列起來, 然
技術篇
3.品質指標 1.
S P C 的 品 質 指 標
百萬分之不良PPM: 有些地方叫DPPM, 它是一 人概率的概念
A.計數值之PPM計算:
不良數 PPM= ╳1000000 抽樣數
B.計量值之PPM計算 靜態:PPM=Φ[(LSL-Xbar)/σ]+Φ[(USL-Xbar)/σ] 動態:PPM=Max{Φ[(LSL-Xbar)/σ+1.5]+Φ[(USL-Xbar)/σ+1.5],
LCL CL UCL
B.單邊上限規格
Cp=(USL-CL)/3σa=CpU
LCL
SL CL
USL UCL
技術篇
3.品質指標 1.
S P C 的 品 質 指 標
製程能力指數(Cpk): A.雙邊規格 Cpk= (1-Ca)*Cp
B.單邊上限規格 CPK=CPU=Cp
C.單邊下限規格 CPK=CPL=C p
Ca :製程准确度
Cp
Cpk
製程精密度(製程潛力)
製程能力
品質六大特質分析
PPM
Parts Per Million
SGMs 規格標準差
基礎篇
SGMa 製程標準差
單邊規格沒有Ca
等級評定後之處置原則(Ca等級之處置) A級:作業員遵守作業標準操作,並達到規格之要求,須繼續維持。 B級:有必要可能將其改進為A級。 C級:作業員可能看錯規格,不按作業標準操作或檢討規格及作業標準。 D級:應採取緊急措施,全面檢討所有可能影響之因,必要時得停止生產。 以上僅是些基本原則,在一般應用上Ca如果不良時,其對策方法是製造單位為主,技術單位 副,品管單位為輔
SPC常用公式和参数
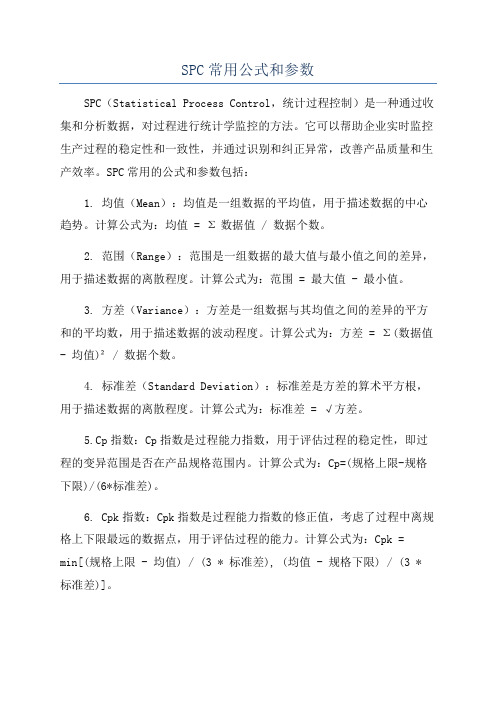
SPC常用公式和参数SPC(Statistical Process Control,统计过程控制)是一种通过收集和分析数据,对过程进行统计学监控的方法。
它可以帮助企业实时监控生产过程的稳定性和一致性,并通过识别和纠正异常,改善产品质量和生产效率。
SPC常用的公式和参数包括:1. 均值(Mean):均值是一组数据的平均值,用于描述数据的中心趋势。
计算公式为:均值= Σ数据值 / 数据个数。
2. 范围(Range):范围是一组数据的最大值与最小值之间的差异,用于描述数据的离散程度。
计算公式为:范围 = 最大值 - 最小值。
3. 方差(Variance):方差是一组数据与其均值之间的差异的平方和的平均数,用于描述数据的波动程度。
计算公式为:方差= Σ(数据值- 均值)² / 数据个数。
4. 标准差(Standard Deviation):标准差是方差的算术平方根,用于描述数据的离散程度。
计算公式为:标准差= √方差。
5.Cp指数:Cp指数是过程能力指数,用于评估过程的稳定性,即过程的变异范围是否在产品规格范围内。
计算公式为:Cp=(规格上限-规格下限)/(6*标准差)。
6. Cpk指数:Cpk指数是过程能力指数的修正值,考虑了过程中离规格上下限最远的数据点,用于评估过程的能力。
计算公式为:Cpk =min[(规格上限 - 均值) / (3 * 标准差), (均值 - 规格下限) / (3 * 标准差)]。
7. 控制限(Control Limits):控制限是一组上限和下限,用于判断过程数据是否正常。
常用的控制限包括平均数控制限(X控制限)和范围控制限(R控制限),计算公式为:X控制限 = 均值± 3 * 标准差,R控制限 = D4 * 范围平均数。
8. 过程能力指数(Process Capability Index):过程能力指数用于评估过程的能力是否满足产品规格要求,常用的指数包括Cp、Cpk和Cpm。
Spc应用计算公式(超全)

SPC所有公式详细解释及分析SPC统计制程管制计量值管制图: Xbar-R(平均-全距)、Xbar-S(平均-标准差)、X-MR(个别值-移动全距)、EWMA、CUSUM等管制图。
计数值管制图:不良率p、不良数np、良率1-p、缺点数c、单位缺点数u等管制图。
常用分析工具:直方图、柏拉图、散布图、推移图、%GRR...等。
公式解说制程能力指数制程能力分析制程能力研究在于确认这些特性符合规格的程度,以保证制程成品不符规格的不良率在要求的水准之上,作为制程持续改善的依据。
制程能力研究的时机分短期制程能力研究及长期制程能力研究,短期着重在新产品及新制程的试作、初期生产、工程变更或制程设备改变等阶段;长期以量产期间为主。
制程能力指针 Cp 或 Cpk 之值在一产品或制程特性分配为常态且在管制状态下时,可经由常态分配之机率计算,换算为该产品或制程特性的良率或不良率,同时亦可以几 Sigma 来对照。
计数值统计数据的数量表示缺点及不良(Defects VS. Defectives)缺点代表一单位产品不符要求的点数,一单位产品不良可能有一个缺点或多个缺点,此为计点的品质指针。
例如描述一匹布或一铸件的品质,可用每公尺棉布有几个疵点,一铸件表面有几个气孔或砂眼来表达,无尘室中每立方公尺含微粒之个数,一片PCB有几个零件及几个焊点有缺点,一片按键有几个杂质、包风、印刷等缺点,这些都是以计点方式表示一单位产品的特性值。
不良代表一单位产品有不符要求的缺点,可能有一个或一个以上,此将产品分类为好与坏、良与不良及合格与不合格等所谓的通过-不通过(Go-NoGo)的衡量方式称为计件的品质指针。
例如单位产品必须以二分法来判定品质,不良的单位产品必须报废或重修,这是以计件方式来表示一单位产品的特值。
每单位缺点数及每百万机会缺点数(DPU VS. DPMO)一单位产品或制程的复杂程度与其发生缺点的机会有直接的关系,越复杂容易出现缺点;反之越简单越不容易出现缺点。
SPC计算公式和判定准则

SPC计算公式和判定准则SPC(Statistical Process Control,统计过程控制)是一种通过统计方法对过程进行监控和控制来确保产品质量的方法。
SPC包含了一系列的计算公式和判定准则,用于对过程数据进行分析和判断。
本文将介绍SPC的常用计算公式和判定准则。
一、计算公式1. 平均值(X-bar)和范围(R)控制图的计算公式:平均值控制图:X-bar = (X1 + X2 + ... +Xn)/n范围控制图:R = Xmax - Xmin2.方差(S)控制图的计算公式:方差控制图:S = √((∑(xi - x̄)²)/(n-1))其中,xi为单个数据点,x̄为平均数,n为样本个数。
3.标准差(σ)控制图的计算公式:标准差控制图:σ = √((∑(xi - x̄)²)/n)其中,xi为单个数据点,x̄为平均数,n为样本个数。
4. 标准分数(Z-score)的计算公式:标准分数:Z=(X-μ)/σ其中,X为观测值,μ为总体平均值,σ为总体标准差。
5.概率(P)的计算公式:概率:P=1-Z其中,Z为标准分数。
二、判定准则SPC通过控制图上的控制限来进行判定,一般包括控制线和规范线。
常用的判定准则有以下几种:1.控制线:控制线用于界定过程是否处于统计控制状态。
一般有上限控制线(UCL)和下限控制线(LCL)。
当数据点超过控制线时,表明过程处于非随机状态,可能存在特殊原因。
2.规范线:规范线用于界定过程是否处于规范状态。
一般有上限规范线(USL)和下限规范线(LSL)。
当数据点超过规范线时,表明产品或过程不符合规格要求。
3.判定准则:SPC根据运行趋势和控制限来进行判定,常见判定准则包括:-单点超出控制限:当单个数据点超出控制限时,可能存在特殊原因,需要进行调查和纠正。
-一组连续点趋势逐渐上升或下降:当连续的数据点呈增加或减少的趋势时,表明过程可能不稳定,需要进行调查和纠正。
SPC计算公式范文
SPC计算公式范文SPC(Statistic Process Control)是一种通过统计方式对过程进行控制的方法,它可以帮助我们检测并识别过程中的特殊因子,并及时采取纠正措施,以保持过程处于控制状态。
SPC计算公式是SPC方法中常用的一些统计计算公式,包括均值、标准差、控制图等。
以下是SPC方法中常用的几个计算公式。
1. 均值(Mean)均值是一组数据的平均值,用于描述数据集中的集中趋势。
均值的计算公式如下:Mean = (x1 + x2 + x3 + ... + xn) / n其中,x1、x2、x3等是数据集中的各个数据点,n是数据点的个数。
2. 范围(Range)范围表示一组数据的最大值和最小值之间的差值,用于描述数据集中的离散程度。
范围的计算公式如下:Range = xmax - xmin其中,xmax是数据集中的最大值,xmin是数据集中的最小值。
3. 标准差(Standard Deviation)标准差表示数据集中各个数据点与均值之间的离散程度,用于描述数据集的分布情况。
标准差的计算公式如下:Standard Deviation = √ ((x1 - M ean)² + (x2 - Mean)² + (x3 - Mean)² + ... + (xn - Mean)² ) / (n-1)其中,x1、x2、x3等是数据集中的各个数据点,Mean是数据集的均值,n是数据点的个数。
4. 方差(Variance)方差是标准差的平方,也是描述数据集的分布情况的统计指标。
方差的计算公式如下:Variance = ((x1 - Mean)² + (x2 - Mean)² + (x3 - Mean)² + ... + (xn - Mean)² ) / (n-1)其中,x1、x2、x3等是数据集中的各个数据点,Mean是数据集的均值,n是数据点的个数。
SPC所有公式详细解释及分析
SPC所有公式详细解释及分析SPC(统计过程控制)是一种用于监控和控制过程变异的统计方法。
在SPC中,有许多公式用于计算统计量和确定控制界限,以帮助检测异常和评估过程的稳定性。
本文将详细解释和分析一些常见的SPC公式。
1. 平均值(Mean):平均值是样本数据的算术平均值。
计算平均值的公式是将所有观测值相加,然后除以观测值的个数。
平均值可以用来了解过程的中心位置。
2. 范围(Range):范围表示样本数据的最大值和最小值之间的差异。
计算范围的公式是将样本数据的最大值减去最小值。
范围主要用于检测过程变异的大小。
3. 方差(Variance):方差用于测量样本数据的离散程度。
计算方差的公式是将每个观测值与平均值的差异平方后相加,并除以观测值的个数减1、方差越大,表示过程的波动性越大。
4. 标准差(Standard Deviation):标准差是方差的平方根,用于衡量过程数据的离散程度。
标准差可以用来判断过程的稳定性和控制界限的设定。
标准差越大,表示过程的变异性越大。
5. 控制图界限(Control Limits):控制图界限是用来判断过程是否处于统计控制的范围内。
常用的控制图包括X-bar图和R图。
在X-bar图中,控制界限由平均值加减3倍标准差计算得到。
在R图中,控制界限由平均范围的加减2.66倍平均范围的标准差计算得到。
如果一个点超出了控制界限,则表示该点可能是异常值或过程发生了变化。
6. 过程能力指数(Process Capability Index):过程能力指数用来衡量过程在规格限制内产生产品的能力。
常用的过程能力指数包括Cp、Cpk、Pp和Ppk。
Cp和Pp表示过程的潜在能力,只考虑过程的平均值和规格限制的距离;Cpk和Ppk表示过程的实际能力,同时考虑过程的变异性。
7. 规格上限与规格下限(Specification Limits):规格上限和规格下限是产品或过程的设计要求。
当产品或过程的测量值超出规格限制时,表示产品或过程不符合设计要求,可能需要调整或改进。
SPC计算公式及参数
類別
-R
X-Rm
平均值(個別值)
管制圖
【 (X)Leabharlann 制圖】管制上限管制中心線
管制下限
全距(移動全距)
管制圖
【R(Rm)管制圖】
管制上限
D4*
管制中心線
管制下限
D3*
2)計量值管制圖之常數對照表﹕
樣本數值(n)
A2
D3
D4
E2
2
1.880
0
3.267
1.128
0.184
1.816
2.970
1.010
10
0.308
0.223
1.777
3.078
0.975
16
0.212
0.363
1.637
3.532
0.849
註:X-Rm管制圖查計量值管制圖之常數對照表時,查n=2之數值。
3)計數值管制圖的計算公式﹕
類別
nP
P
C
U
管制
上限
管制
中心線
管制
下限
A平均值﹕ =(X1+X2+…+Xn)/n;
2.660
3
1.023
0
2.574
1.693
1.772
4
0.729
0
2.282
2.059
1.457
5
0.577
0
2.114
2.326
1.290
6
0.483
0
2.004
2.534
1.184
7
0.419
0.076
1.924
2.704
SPC计算公式和判定准则
SPC计算公式和判定准则SPC(Statistical Process Control,统计过程控制)是一种用于监测和控制过程稳定性的方法,通过对过程进行统计分析和监测,可以及时发现过程中的变异,从而采取相应的控制措施,提高过程的稳定性和可控性。
本文将介绍SPC的计算公式和判定准则,以帮助读者了解如何应用SPC进行过程监控和控制。
1. SPC计算公式SPC计算公式是用于计算各种统计指标和控制图的数学公式,下面是常用的SPC计算公式。
1.1 均值(Mean)均值是一组数据的平均值,用于表示过程的中心位置。
计算均值的公式如下:均值公式均值公式其中,mu 表示均值,n 表示数据的数量,x_i 表示第i 个数据。
1.2 极差(Range)极差是一组数据的最大值和最小值之差,用于表示过程的变异程度。
计算极差的公式如下:极差公式极差公式其中,R 表示极差,x_{\text{max}} 表示数据的最大值,x_{\text{min}} 表示数据的最小值。
1.3 标准偏差(Standard Deviation)标准偏差是一组数据的离均差平方和的平均值的平方根,用于表示过程的稳定性。
计算标准偏差的公式如下:标准偏差公式标准偏差公式其中,sigma 表示标准偏差,n 表示数据的数量,x_i 表示第i 个数据,\bar{x} 表示数据的均值。
2. SPC判定准则SPC判定准则用于判断一个过程是否处于稳定状态,常用的判定准则有以下几种。
2.1 均值控制图(Mean Control Chart)均值控制图用于监测过程均值是否稳定。
常用的均值控制图有Xbar-R 控制图和 Xbar-S 控制图。
•Xbar-R 控制图:对应的是过程均值和极差的统计指标。
当连续 n 个点全部落在中心线(均值线)的上方或下方时,表示过程中有特殊原因的变异,需要采取相应措施进行调整。
•Xbar-S 控制图:对应的是过程均值和标准偏差的统计指标。
当连续 n 个点全部落在中心线(均值线)的上方或下方时,表示过程中有特殊原因的变异,需要采取相应措施进行调整。
- 1、下载文档前请自行甄别文档内容的完整性,平台不提供额外的编辑、内容补充、找答案等附加服务。
- 2、"仅部分预览"的文档,不可在线预览部分如存在完整性等问题,可反馈申请退款(可完整预览的文档不适用该条件!)。
- 3、如文档侵犯您的权益,请联系客服反馈,我们会尽快为您处理(人工客服工作时间:9:00-18:30)。
SPC常用计算方法SPC基础知识及常用计算方法SPC基础知识一、 SPC定义:1、 SPC——统计制程管制:是指一套自制程中去搜集资料,并加以统计分析,从分析中去发气掘制程的异常,立即采取修正行动,使制程恢复正常的方法。
也就是说:品质不应再依赖进料及出货的抽样检验,而应该采取在生产过程中,认良好的管理方法,未获得良好的品质。
2、良好品质,必须做到下面几点:①变异性低②耐用度③吸引力④合理的价格3、变异的来源:大概来自5个方面:①机器②材料③方法④环境⑤作业人员应先从机器,材料方法,环境找变异,最后考虑人。
4、 SPC不是一个观念,而是要行动的步骤一、确立制程流程——首先制程程序要明确,依据制程程序给制造流程图,并依据流程图订定工程品质管理表。
步骤二、决定管制项目——如果把所有对品质有影响的项目不论大小,轻重缓急一律列入或把客户不很重视的特性一并管制时,徒增管制成本浪费资料且得不赏失,反之如果重要的项目未加以管制时,则不能满足设计者,后工程及客户的需求,则先去管制的意义。
步骤三、实施标准化——欲求制程管制首先即得要求制程安定,例如:在风浪很大的船上比赛乒乓球,试部能否确定谁技高一筹,帮制程作业的安定是最重要的先决条件,所以对于制程上影响产品口质的重要原因,应先建立作业标准,并透过教育训练使作业能经标准进行。
步骤四、制程能力调查——为了设计、生产、销售客户满意且愿意购买的产品,制造该产品的制程能力务必符合客户的要求。
因此制程的能力不足时,必顺进行制程能力的改善,而且在制程能力充足后还必须能继续,所以在品质管理的系统中制程能力的掌握很重要。
步骤五、管制图运用——SPC的一个基本工具就是管制图,而管制图又分计量值管制图与计数值管制图。
步骤六、问题分析解决——制程能力调查与管制图是可筛提供问题的原因系由遇原因或非机遇原因所造成,但无法告知你确切的原因为何及如何解决决问题?解决问题?而问题的解决技巧,在于依据事实找出造成变异的确切原因,并提此对策加以改善,及如何防止再发生。
步骤七、制程之继续管制——经过前6个步骤,人制程能力符合客户的要求,且管制图上的点未出管制界限时,则可将此管制界限沿有作为制程之继续管制,但当制程条件如有变动时,如机器,材料,方法等产生异动时,则须回到步骤三,不可沿原先之管制界限。
SPC的应用步骤其流程图如下:Ca制程准确度Cp制程精密度Cpk制程能力指数二、管制图的运用管制图的种类又依数值资料是计量值或计数值者,划分为二大类即计量值管制图与计数值管制图,计量值管制图不但只告诉你制程有问题了,还可以告诉你制程在什么地方出了问题,是中心值产生了问题还是变异量产生了问题。
而在计量值管制图应用不便或应用时,则可采用计数值管制图,但计数值管制图只能告知你制程有了问题,但却不能如计量值管图一般指明问题出在何处。
数据的种类管制图名称管制图记号计量值平均值与全距管制图中位值与全距管制图个别值与移动全距管制图平均值标准差管制图X-R ChartX-R ChartX-Rm ChaetX-S Chaet计数值不良率管制图不良数管制图缺点数管制图单位缺点数管制图 P-ChartPu-ChartC-ChartU-Chart管制图编号、制品名称、品质特性、测量单位、规格、制造部门、机器号码、工作者、抽样方法、测定者、期限需清楚填入,以便资料的整理与分析,及知道管制图的背景。
制程要因(人员、设备、材料、方法、环境)之任何变更资料,须详细记载,以便日后追查非机遇性原因时可作为参考之资料,此点非常重要。
中心线(CL)记以实线,管制上限(UCL)及管制下限(LCL)记以虚线,并在中心线及管制上限、管制下限的尾端处,分别记入CL、UCL、LCL等符号及其数值。
依据UCL与LCL之计算位数,比所测定样本的位数多一位数或两位数即可。
根据UCL与LCL之距离决定坐标位置,太宽与太窄均不适宜,并预留管制界限外的空间。
依据规定进行抽样,并计算测定值,立刻将计算之数值点绘至管制图上。
若有点的判读时属异常,则应立即追究原因,并将原因填入原因追查栏内,千万不可置之不理。
计量值管制图平均值与全距管制图(X-R Chart)对于平均值面看,如果缺少标准差,平均值就是一个没有意义的数字,换言之标准差愈小平均值具代表性,标准差愈大即平均值不具代表性,如有二组数据分别为10,11,12与1,11,21其平均值皆为11,但何组数据其平均值11较具有代表性呢?X是平均值,如有一组数据为10,11,12,则其平均值 =10+11+12 ,X管制图主要是用来观察分配平均值的变化情形。
R是全距,也是英文Range的第一个字母为代表,如有一组数据为10,11,12,则其全距R等于最大值减最小值=12-10=2,R管制图主要是用来观察分配其变异的散布情形。
X-R管制图是把握制程状能最有效的一种管制图。
X:各组的平均值X(念作X,Double、Bar):各组的平均(X)的平均值,即是X管制图的中心线。
R:每组中的最大值减去最小值R:各组全距(R)平均值,即是R管制图的中心线。
A2,D4,D3,d2:是X-R管制图的系数(如表10-2)管制图的公式:X管制图的管制界限:管制中心线 CL=X管制上限UCL=X+A2R管制下限 LCL=X-A2RR管制图的管制界限:管制中心线 CL=R管制上限UCL=D4R管制下限 LCL=D4R平均值(X)的抽样分配其标准差(σX)与母体标准差(σ)的关系,全距(R)的抽样分配其平均值(R)与原母体标准差(σ)的关系R,全距(R)的抽样分配其标准差(σR)与母体标准差(σ)的关系,首先看他距管制图即R—管制图,如所有的点皆在管制界限内,代表全距皆在统计管状态下,则继续看平均值管制图即X—管制图,如只有一或二个点在管制界限外,则剔除这一或二个全距的样本,然后重新计算新的全距管制界限,如其余的点皆在新的管制界内则可视为全距在统计管制状态下,继续看X—管制图,如剩于的点超出新的管制界限时,则代表全距非在统计管制状态下,此时,应找出非机遇原因并修正非机遇原因然后予以标准化后,重新搜集新的资料。
如有3点以上的全距的管制界限外,则代表全距在非统计的管制状下,前言之即全距失控,则应找出非机遇性原因,并修正非机遇原因然后予标准化,标准化后再重新搜集资料。
如R——管制图在统计管制计态下,则继续看X——管制图,台点皆在管制界限内则代表平均值是统计管制状态下,简言之即在控制中,则可沿用此一管制界限作为制程管制用之管制界限,如有一或二个平均平均值的点在管制界限外,则剔除这一或二组平均值的样本,然后计算新的管制界限,如其余的点皆在新的管制界限内可视为平均值在统计管制状下,则沿用此一管制界限作为制程管制用管制图的管制界限,如剩余的点有点超出新的管制界限时,则代表平均值非在统计管制状态下,此时应找出非机遇原因并修正机遇原因,然后予以标准化,并重新搜集新的资料。
中位值与全距管制图(X-R Chart)3、个别值与移动全的全距管制图(X-Rm Chart)此管制图用于计量值特性的管制,一般每次低能获取一个数据,故管制图不如X-R管制图来得灵敏,但却可与X-R管制图造成同式样的型态,郊并且可用同一方法来判读,所以X-R管制图不适用之处就可应用此管制图,譬如设耐久性试验须耗用时间很久方能完成者、化学药品之浓度属极为均匀一致的、须做破坏性试验者、产量不大批量很小……等场合时,即可使用此--管制图。
X:每次之测定值X:每次测定值(X)的平均值,即是X管制图的中心线。
Rm:是求出相邻数据之差(全距),其相邻可以2个为一组,也可以3个为一组。
2007-8-110:16:34 ---实用,易用-SPC软件下载试用编辑帖子帖子评价单帖屏蔽删除帖子kuai头衔:社区公民等级:一年级研究生会员帮派:无帮无派帖数:50金钱:4110积分:1信息 | 留言 | QQ | Email | 主页 | 编辑| 引用 | 管理第 1 楼A.4 选择控制图的刻度两个控制图的纵坐标分别用于X和R的测量值,用于确定刻度值的一些通用的指南是有帮助的,尽管它们在特殊情况下可能要修改。
对于X图,坐标上的刻度值的最大值与最小值之差应少为子组均值(X)的最大与最小值差的2倍。
对于R图,刻度值应从最低值0开始到最大值之间的差值为初始阶段所遇到的最大极差(R)的2倍。
注:一个有用的建议是将R图的刻度值设置为均值图的刻度值的2倍(例如:平均值图上1个刻度代表0.01英寸,则在极端差图上1刻度代表0.02英寸,在一般的子组大小情况下,均值和极差的控制限将具有大约相同的宽度,给分析以直观的帮助。
A.5 将均值和极差画到控制图上将均值和极差分别画在其各自的图上。
该工作在确定了刻度以后尽快完成。
将各点用直线联接起来从而得到可见的图形趋势。
简要地浏览一下所有画上去的点,看它们是否合理,如果有的点比别的点高得很鑫或低得很多,需确认计算及图是否正确的,应确保所画的X和R点在纵向是对应的。
注:为了再次强调生产现场的所有控制限的控制图的应用,还没有计算控制限(由于没有足够的数据)的初期操作控制图上应清楚地注明“初始研究”字样。
这样,这些标有“初始研究”的控制图,不论是用于能力的初次确定还是用于过程经过改进/改变后的研究,是仅允许用在生产现场中还没有控制限的过程控制图。
B.计算控制限首先计算极差图的控制限,再计算均值图的控制限,计量型数据的控制图的控b.链——在下列现象之一表明过程已改变或出现这种趋势:·连续7点位于平均值的一侧;·连续7点上升(后续等于或大于前点)或下降;标记促使人们作出决定的点,并从这点做一条参考线延伸到链的开始点将是有帮助的。
分析时应考虑开始出现改变或趋势的大致时间。
高于平均极差的链或上升说明存在下列情况之一或全部:·输出值的分布宽度增加,其原因可观胆无规律的(例如设备工作不正常或固定松动)或是由于过程中的某个要素变化(例如,使用新的不是很一致的原材料),这些都是常见的问题,需要纠正;·测量系统改变(例如,新的检验员或量具)。
低于平均极差的链,或下降链表明存在下列情况之一或全部:·输出值分布宽度减小,这常常是一个好状态,应研究以便推广应用和改进过程;·测量系统改变,这样会遮掩过程真实性能的变化。
注:当子组数(n)变得更小(5或更小)时,低于R的链的可能性增加,则8点或更多点组成的链才能表明过程变差减小。
---------------------------------------------------------------SPConline论坛欢迎您!2007-8-1 10:16:56 --- 实用,易用-SPC软件下载试用编辑帖子帖子评价单帖屏蔽删除帖子kuai头衔:社区公民等级:一年级研究生会员信息 | 留言 | QQ | Email | 主页 | 编辑| 引用 | 管理第 2 楼c.明显的非随机图形——除了会出现超过控制界的点或长链之外,数据中还可能出现其他的易分辨的由于特殊原因造成的图形。