SPC所有公式详细解释及分析
SPC公式汇总范文

SPC公式汇总范文SPC,也就是统计过程控制,是一种用来监控和控制过程稳定性和一致性的统计方法。
它通过收集、分析和解释过程中产生的数据,帮助组织了解过程的特性并进行持续改进。
SPC的使用可以有效地降低过程变异性,并减少缺陷和不一致性的发生。
SPC方法的基础是SPC公式,下面将对常用的SPC公式进行汇总和解释。
1.均值和范围控制图公式:-均值控制图公式:控制界限的计算通常是通过计算样本均值的上下界限,即控制上界限=过程平均值+3σ/样本大小的平方根;控制下界限=过程平均值-3σ/样本大小的平方根;其中,σ表示样本中的标准差。
-范围控制图公式:控制界限的计算通常是通过计算样本范围的上下界限,即控制上界限=过程范围平均值+3*A2/样本大小的平方根;控制下界限=过程范围平均值-3*A2/样本大小的平方根;其中,A2是与样本大小相关的常数。
2.方差和标准差控制图公式:-方差控制图公式:控制界限的计算通常是通过计算样本方差的上下界限,即控制上界限=过程方差*F/(样本大小-1);控制下界限=过程方差*F/(样本大小-1);其中,F是与样本大小和置信水平相关的常数。
-标准差控制图公式:控制界限的计算是通过计算样本标准差的上下界限,即控制上界限=过程标准差+3σ/样本大小的平方根;控制下界限=过程标准差-3σ/样本大小的平方根;3.质量比率控制图公式:-质量比率控制图公式:控制界限的计算通常是通过计算样本中缺陷项目的数量比率的上下界限,即控制上界限=过程中缺陷比率的上界限;控制下界限=过程中缺陷比率的下界限;4.不良品数控制图公式:-不良品数控制图公式:控制界限的计算通常是通过计算样本缺陷数量的上下界限控制上界限=过程中缺陷数的平均值+3σ/样本大小的平方根;控制下界限=过程中缺陷数的平均值-3σ/样本大小的平方根;需要注意的是,以上是一些常见的SPC公式,具体使用时可能会根据实际情况进行调整和计算。
此外,还有其他一些SPC公式,例如强度控制图公式、极差控制图公式等,但由于篇幅限制无法一一列举。
SPC常用公式和参数

SPC常用公式和参数SPC(Statistical Process Control,统计过程控制)是一种质量管理方法,通过使用统计方法来监控生产过程中的变异性,以及使过程保持在可控状态,确保产品质量的稳定性。
在SPC中,常用的公式和参数用于描述、分析和控制过程的变异性,以及进行质量指标的计算和分析。
下面是SPC中常用的公式和参数:1. 均值(Mean):均值是一组数据的平均值,用于描述数据的集中趋势。
均值可以表示为:Mean = (x1 + x2 + ... + xn) / n其中,x1 ~ xn表示一组数据,n表示数据的个数。
2. 范围(Range):范围用于描述一组数据的离散程度,即最大值与最小值之间的差异。
范围可以表示为:Range = xmax - xmin其中,xmax表示一组数据的最大值,xmin表示最小值。
3. 标准差(Standard Deviation):标准差是一组数据的离散程度的度量,用于衡量数据的波动性。
标准差可以表示为:Standard Deviation = sqrt[((x1 - mean)^2 + (x2 - mean)^2+ ... + (xn - mean)^2) / n]其中,x1 ~ xn表示一组数据,mean表示数据的均值,n表示数据的个数。
4. 方差(Variance):方差是标准差的平方,也是一组数据的离散程度的度量。
Variance = (Standard Deviation)^25. 控制图(Control Chart):控制图是SPC中最常用的工具,它用于监控过程的变异性,并确定过程是否处于可控状态。
在控制图中,常用的参数有:- 中心线(Center Line):控制图的中心线表示过程的平均值或目标值。
- 控制限(Control Limit):控制限是确定过程的可控状态的界限。
常用的控制图有三个控制限:- 上控制限(Upper Control Limit,UCL):表示过程变异性在正常范围内的上限,超过该限制则表明过程存在特殊原因。
SPC各值计算公式

SPC各值计算公式SPC(统计过程控制)是一种统计方法,用于检测和控制过程的稳定性和变异性。
SPC各值计算公式包括控制图参数和过程能力指数等。
以下是常见的SPC各值计算公式及其解释:1.控制图参数:a.X̄控制图上的中心线是过程的平均值的估计量。
计算公式为:X̄=ΣX/n,其中X是测量值的总和,n是样本大小。
b. R 控制图上的极差线是过程的极差的估计量。
计算公式为:R = Xmax - Xmin,其中Xmax和Xmin是样本中最大值和最小值。
c.S控制图上的标准偏差线是过程的标准偏差的估计量。
计算公式为:S=√(Σ(X-X̄)²/(n-1)),其中Σ(X-X̄)²是样本值与平均值的差的平方的总和。
d.UCL控制图上的上限控制限是过程的可接受上限。
计算公式为:UCL=X̄+3S,其中3是标准差的倍数,用于确定上限控制限。
e.LCL控制图上的下限控制限是过程的可接受下限。
计算公式为:LCL=X̄-3S,其中3是标准差的倍数,用于确定下限控制限。
2.过程能力指数:a.Cp过程能力指数是衡量过程发生误差在可接受范围内的能力。
计算公式为:Cp=(USL-LSL)/(6σ),其中USL和LSL是规范上限和下限,σ是标准偏差的估计量。
b. Cpk 过程能力指数是衡量过程发生误差在可接受范围内的能力,同时考虑了过程的中心线偏移。
计算公式为:Cpk = min((USL - X̄) /(3σ), (X̄ - LSL) / (3σ)),其中USL和LSL是规范上限和下限,X̄是过程的平均值的估计量,σ是标准偏差的估计量。
c. Cpm 过程能力指数是衡量过程发生误差在可接受范围内的能力,同时考虑了过程的中心线偏移和过程的极差。
计算公式为:Cpm = (USL - LSL) / (6√((ΣR/n)² + σ²)),其中USL和LSL是规范上限和下限,ΣR/n是极差均值的估计量,σ是标准偏差的估计量。
SPC所有公式详细解释及分析

SPC所有公式详细解释及分析SPC(统计过程控制)是一种通过统计方法对产品或过程的变化进行控制的质量管理工具。
它以数据为基础,通过收集、分析和解释数据,帮助确定过程是否稳定、符合规范,并提供改进措施。
在SPC中,有一些重要的公式用于计算和分析数据,下面将介绍其中一些常用的公式及其详细解释和分析。
1. 平均值(Mean):平均值是统计数据的中心点,通过计算数据的总和除以数据的个数得到。
平均值用于评估过程的中心位置,并对过程的稳定性进行评估。
2. 中位数(Median):中位数是将数据按照大小顺序排列后,排在中间位置的数值,它能够反映数据的集中趋势。
与平均值相比,中位数对异常值的影响较小,更适用于非正态分布的数据。
3. 标准差(Standard Deviation):标准差是数据分布离散程度的度量,用于描述数据的波动性。
标准差越大,表示数据越分散;标准差越小,表示数据越集中。
标准差可以帮助确定过程是否稳定,是否存在特殊因素影响。
4. 变异系数(Coefficient of Variation):变异系数是标准差除以平均值的比值,用于比较不同数据集的离散性。
较小的变异系数表示数据越稳定,较大的变异系数表示数据集的离散性较大。
5. 极差(Range):极差是数据的最大值和最小值之间的差别,用于评估数据的波动范围。
较大的极差表示数据集的波动性较大,较小的极差表示数据集的波动性较小。
6. 四分位数(Quartiles):四分位数是将数据按大小顺序排列后,将数据分为四等份的数值。
第一四分位数是中位数的前一半数据的中位数,第二四分位数即中位数,第三四分位数是中位数之后的一半数据的中位数。
四分位数可以帮助了解数据的分布情况。
7. 直方图(Histogram):直方图使用柱状图形象地展示数据的分布情况。
通过将数据按照一定的区间划分,并统计每个区间内的数据个数,可以直观地了解数据的分布情况。
8. 管理图(Control Chart):管理图是SPC最重要的工具之一,它通过将数据的统计量(如平均值、标准差等)绘制在图表上,并与控制限进行比较,用于监控过程的稳定性。
SPC常见参数公式
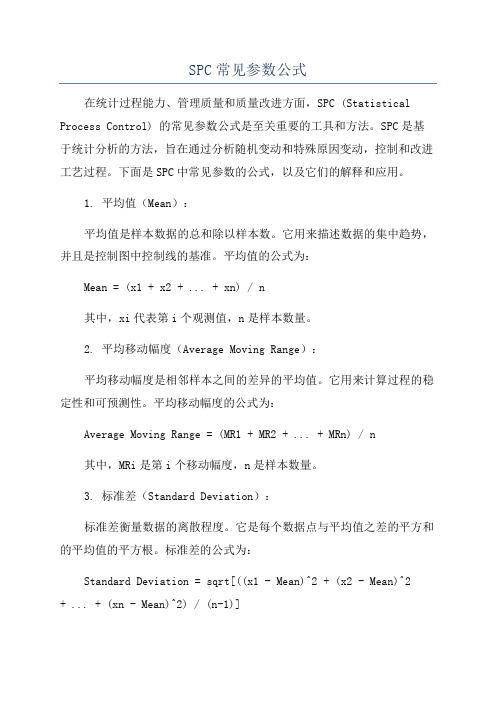
SPC常见参数公式在统计过程能力、管理质量和质量改进方面,SPC (Statistical Process Control) 的常见参数公式是至关重要的工具和方法。
SPC是基于统计分析的方法,旨在通过分析随机变动和特殊原因变动,控制和改进工艺过程。
下面是SPC中常见参数的公式,以及它们的解释和应用。
1. 平均值(Mean):平均值是样本数据的总和除以样本数。
它用来描述数据的集中趋势,并且是控制图中控制线的基准。
平均值的公式为:Mean = (x1 + x2 + ... + xn) / n其中,xi代表第i个观测值,n是样本数量。
2. 平均移动幅度(Average Moving Range):平均移动幅度是相邻样本之间的差异的平均值。
它用来计算过程的稳定性和可预测性。
平均移动幅度的公式为:Average Moving Range = (MR1 + MR2 + ... + MRn) / n其中,MRi是第i个移动幅度,n是样本数量。
3. 标准差(Standard Deviation):标准差衡量数据的离散程度。
它是每个数据点与平均值之差的平方和的平均值的平方根。
标准差的公式为:Standard Deviation = sqrt[((x1 - Mean)^2 + (x2 - Mean)^2+ ... + (xn - Mean)^2) / (n-1)]其中,xi是第i个观测值,Mean是平均值,n是样本数量。
4. 极差(Range):极差是样本中最大值与最小值之间的差异。
它用来衡量过程的变异程度。
极差的公式为:Range = xmax - xmin其中,xmax是样本的最大值,xmin是样本的最小值。
5. 方差(Variance):方差是每个数据点与平均值之差的平方和的平均值。
它衡量数据的离散程度。
方差的公式为:Variance = [(x1 - Mean)^2 + (x2 - Mean)^2 + ... + (xn - Mean)^2] / (n-1)其中,xi是第i个观测值,Mean是平均值,n是样本数量。
SPC常用公式和参数
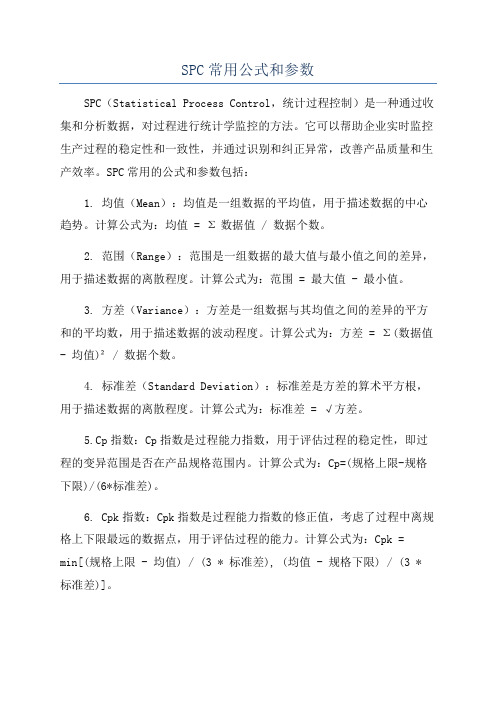
SPC常用公式和参数SPC(Statistical Process Control,统计过程控制)是一种通过收集和分析数据,对过程进行统计学监控的方法。
它可以帮助企业实时监控生产过程的稳定性和一致性,并通过识别和纠正异常,改善产品质量和生产效率。
SPC常用的公式和参数包括:1. 均值(Mean):均值是一组数据的平均值,用于描述数据的中心趋势。
计算公式为:均值= Σ数据值 / 数据个数。
2. 范围(Range):范围是一组数据的最大值与最小值之间的差异,用于描述数据的离散程度。
计算公式为:范围 = 最大值 - 最小值。
3. 方差(Variance):方差是一组数据与其均值之间的差异的平方和的平均数,用于描述数据的波动程度。
计算公式为:方差= Σ(数据值- 均值)² / 数据个数。
4. 标准差(Standard Deviation):标准差是方差的算术平方根,用于描述数据的离散程度。
计算公式为:标准差= √方差。
5.Cp指数:Cp指数是过程能力指数,用于评估过程的稳定性,即过程的变异范围是否在产品规格范围内。
计算公式为:Cp=(规格上限-规格下限)/(6*标准差)。
6. Cpk指数:Cpk指数是过程能力指数的修正值,考虑了过程中离规格上下限最远的数据点,用于评估过程的能力。
计算公式为:Cpk =min[(规格上限 - 均值) / (3 * 标准差), (均值 - 规格下限) / (3 * 标准差)]。
7. 控制限(Control Limits):控制限是一组上限和下限,用于判断过程数据是否正常。
常用的控制限包括平均数控制限(X控制限)和范围控制限(R控制限),计算公式为:X控制限 = 均值± 3 * 标准差,R控制限 = D4 * 范围平均数。
8. 过程能力指数(Process Capability Index):过程能力指数用于评估过程的能力是否满足产品规格要求,常用的指数包括Cp、Cpk和Cpm。
Spc应用计算公式(超全)
SPC所有公式详细解释及分析SPC统计制程管制计量值管制图: Xbar-R(平均-全距)、Xbar-S(平均-标准差)、X-MR(个别值-移动全距)、EWMA、CUSUM等管制图。
计数值管制图:不良率p、不良数np、良率1-p、缺点数c、单位缺点数u等管制图。
常用分析工具:直方图、柏拉图、散布图、推移图、%GRR...等。
公式解说制程能力指数制程能力分析制程能力研究在于确认这些特性符合规格的程度,以保证制程成品不符规格的不良率在要求的水准之上,作为制程持续改善的依据。
制程能力研究的时机分短期制程能力研究及长期制程能力研究,短期着重在新产品及新制程的试作、初期生产、工程变更或制程设备改变等阶段;长期以量产期间为主。
制程能力指针 Cp 或 Cpk 之值在一产品或制程特性分配为常态且在管制状态下时,可经由常态分配之机率计算,换算为该产品或制程特性的良率或不良率,同时亦可以几 Sigma 来对照。
计数值统计数据的数量表示缺点及不良(Defects VS. Defectives)缺点代表一单位产品不符要求的点数,一单位产品不良可能有一个缺点或多个缺点,此为计点的品质指针。
例如描述一匹布或一铸件的品质,可用每公尺棉布有几个疵点,一铸件表面有几个气孔或砂眼来表达,无尘室中每立方公尺含微粒之个数,一片PCB有几个零件及几个焊点有缺点,一片按键有几个杂质、包风、印刷等缺点,这些都是以计点方式表示一单位产品的特性值。
不良代表一单位产品有不符要求的缺点,可能有一个或一个以上,此将产品分类为好与坏、良与不良及合格与不合格等所谓的通过-不通过(Go-NoGo)的衡量方式称为计件的品质指针。
例如单位产品必须以二分法来判定品质,不良的单位产品必须报废或重修,这是以计件方式来表示一单位产品的特值。
每单位缺点数及每百万机会缺点数(DPU VS. DPMO)一单位产品或制程的复杂程度与其发生缺点的机会有直接的关系,越复杂容易出现缺点;反之越简单越不容易出现缺点。
SPC计算公式和判定准则
SPC计算公式和判定准则SPC(Statistical Process Control,统计过程控制)是一种通过统计方法对过程进行监控和控制来确保产品质量的方法。
SPC包含了一系列的计算公式和判定准则,用于对过程数据进行分析和判断。
本文将介绍SPC的常用计算公式和判定准则。
一、计算公式1. 平均值(X-bar)和范围(R)控制图的计算公式:平均值控制图:X-bar = (X1 + X2 + ... +Xn)/n范围控制图:R = Xmax - Xmin2.方差(S)控制图的计算公式:方差控制图:S = √((∑(xi - x̄)²)/(n-1))其中,xi为单个数据点,x̄为平均数,n为样本个数。
3.标准差(σ)控制图的计算公式:标准差控制图:σ = √((∑(xi - x̄)²)/n)其中,xi为单个数据点,x̄为平均数,n为样本个数。
4. 标准分数(Z-score)的计算公式:标准分数:Z=(X-μ)/σ其中,X为观测值,μ为总体平均值,σ为总体标准差。
5.概率(P)的计算公式:概率:P=1-Z其中,Z为标准分数。
二、判定准则SPC通过控制图上的控制限来进行判定,一般包括控制线和规范线。
常用的判定准则有以下几种:1.控制线:控制线用于界定过程是否处于统计控制状态。
一般有上限控制线(UCL)和下限控制线(LCL)。
当数据点超过控制线时,表明过程处于非随机状态,可能存在特殊原因。
2.规范线:规范线用于界定过程是否处于规范状态。
一般有上限规范线(USL)和下限规范线(LSL)。
当数据点超过规范线时,表明产品或过程不符合规格要求。
3.判定准则:SPC根据运行趋势和控制限来进行判定,常见判定准则包括:-单点超出控制限:当单个数据点超出控制限时,可能存在特殊原因,需要进行调查和纠正。
-一组连续点趋势逐渐上升或下降:当连续的数据点呈增加或减少的趋势时,表明过程可能不稳定,需要进行调查和纠正。
SPC所有公式详细解释及分析
SPC所有公式详细解释及分析SPC(统计过程控制)是一种用于监控和控制过程变异的统计方法。
在SPC中,有许多公式用于计算统计量和确定控制界限,以帮助检测异常和评估过程的稳定性。
本文将详细解释和分析一些常见的SPC公式。
1. 平均值(Mean):平均值是样本数据的算术平均值。
计算平均值的公式是将所有观测值相加,然后除以观测值的个数。
平均值可以用来了解过程的中心位置。
2. 范围(Range):范围表示样本数据的最大值和最小值之间的差异。
计算范围的公式是将样本数据的最大值减去最小值。
范围主要用于检测过程变异的大小。
3. 方差(Variance):方差用于测量样本数据的离散程度。
计算方差的公式是将每个观测值与平均值的差异平方后相加,并除以观测值的个数减1、方差越大,表示过程的波动性越大。
4. 标准差(Standard Deviation):标准差是方差的平方根,用于衡量过程数据的离散程度。
标准差可以用来判断过程的稳定性和控制界限的设定。
标准差越大,表示过程的变异性越大。
5. 控制图界限(Control Limits):控制图界限是用来判断过程是否处于统计控制的范围内。
常用的控制图包括X-bar图和R图。
在X-bar图中,控制界限由平均值加减3倍标准差计算得到。
在R图中,控制界限由平均范围的加减2.66倍平均范围的标准差计算得到。
如果一个点超出了控制界限,则表示该点可能是异常值或过程发生了变化。
6. 过程能力指数(Process Capability Index):过程能力指数用来衡量过程在规格限制内产生产品的能力。
常用的过程能力指数包括Cp、Cpk、Pp和Ppk。
Cp和Pp表示过程的潜在能力,只考虑过程的平均值和规格限制的距离;Cpk和Ppk表示过程的实际能力,同时考虑过程的变异性。
7. 规格上限与规格下限(Specification Limits):规格上限和规格下限是产品或过程的设计要求。
当产品或过程的测量值超出规格限制时,表示产品或过程不符合设计要求,可能需要调整或改进。
SPC计算公式及参数
類別
-R
X-Rm
平均值(個別值)
管制圖
【 (X)Leabharlann 制圖】管制上限管制中心線
管制下限
全距(移動全距)
管制圖
【R(Rm)管制圖】
管制上限
D4*
管制中心線
管制下限
D3*
2)計量值管制圖之常數對照表﹕
樣本數值(n)
A2
D3
D4
E2
2
1.880
0
3.267
1.128
0.184
1.816
2.970
1.010
10
0.308
0.223
1.777
3.078
0.975
16
0.212
0.363
1.637
3.532
0.849
註:X-Rm管制圖查計量值管制圖之常數對照表時,查n=2之數值。
3)計數值管制圖的計算公式﹕
類別
nP
P
C
U
管制
上限
管制
中心線
管制
下限
A平均值﹕ =(X1+X2+…+Xn)/n;
2.660
3
1.023
0
2.574
1.693
1.772
4
0.729
0
2.282
2.059
1.457
5
0.577
0
2.114
2.326
1.290
6
0.483
0
2.004
2.534
1.184
7
0.419
0.076
1.924
2.704
- 1、下载文档前请自行甄别文档内容的完整性,平台不提供额外的编辑、内容补充、找答案等附加服务。
- 2、"仅部分预览"的文档,不可在线预览部分如存在完整性等问题,可反馈申请退款(可完整预览的文档不适用该条件!)。
- 3、如文档侵犯您的权益,请联系客服反馈,我们会尽快为您处理(人工客服工作时间:9:00-18:30)。
SPC所有公式详细解释及分析
SPC统计制程管制
计量值管制图: Xbar-R(平均-全距)、Xbar-S(平均-标准差)、X-MR(个别值-移动全距)、EWMA、CUSUM等管制图。
计数值管制图:不良率p、不良数np、良率1-p、缺点数c、单位缺点数u等管制图。
常用分析工具:直方图、柏拉图、散布图、推移图、%GRR...等。
公式解说
制程能力指数
制程能力分析
制程能力研究在于确认这些特性符合规格的程度,以保证制程成品不符规格的不良率在要求的水准之上,作为制程持续改善的依据。
制程能力研究的时机分短期制程能力研究及长期制程能力研究,短期着重在新产品及新制程的试作、初期生产、工程变更或制程设备改变等阶段;长期以量产期间为主。
制程能力指针 Cp 或 Cpk 之值在一产品或制程特性分配为常态且在管制状态下时,可经由常态分配之机率计算,换算为该产品或制程特性的良率或不良率,同时亦可以几 Sigma 来对照。
计数值统计数据的数量表示
缺点及不良(Defects VS. Defectives)
缺点代表一单位产品不符要求的点数,一单位产品不良可能有一个缺点或多个缺点,此为计点的品质指针。
例如描述一匹布或一铸件的品质,可用每公尺棉布有几个疵点,一铸件表面有几个气孔或砂眼来表达,无尘室中每立方公尺含微粒之个数,一片PCB有几个零件及几个焊点有缺点,一片按键有几个杂质、包风、印刷等缺点,这些都是以计点方式表示一单位产品的特性值。
不良代表一单位产品有不符要求的缺点,可能有一个或一个以上,此将产品分类为好与坏、良与不良及合格与不合格等所谓的通过-不通过(Go-NoGo)的衡量方式称为计件的品质指针。
例如单位产品必须以二分法来判定品质,不良的单位产品必须报废或重修,这是以计件方式来表示一单位产品的特值。
每单位缺点数及每百万机会缺点数(DPU VS. DPMO)
一单位产品或制程的复杂程度与其发生缺点的机会有直接的关系,越复杂容易出现缺点;反之越简单越不容易出现缺点。
因此,以每单位缺点数(DPU)来比较复杂程度不同的产品或制程品质是不公平的,在管理上必须增加一个衡量产品或制程复杂程度的指针,Six Sigma 以发生缺点的机会(Opportunities)来衡量。
DPU 是代表每件产品或制程平均有几个缺点,而DPMO 是每检查一百万个机会点平均有几个缺点。
一个机会点代表一产品或制程可能会出现缺点的机会,它可能
是一个零件、特性、作业等等。
先进的Six Sigma推广机构建义下列几个规则依其复杂程度来计算一个产品或制程出现缺点的机会数(Opportunities)。
单位缺点数(DPU):DPU=总缺点数/总检验单位数=Defects/Units
一般产品只要有一个缺点就应视为不良品,但是一个不良品可能有一个以上的缺点,因此以平均每件几个缺点较能完全表示品质,以DPU(Defects Per Unit)为单位。
DPMO=(总缺点数/总缺点机会数)×106 =Defects/(Opportunities/Unit×Units) ×106
一般不同产品的每件检点数不同,检点数愈多,出现缺点的机会越多,DPU就可能愈大,以DPU的大小来比较产品品质的好坏似乎不太合理,除非这些产品的复杂程度差不多,因此用总出现缺点的机会数数与总缺点数之比来比较品质会客观一点,以DPMO(Defects Per Million Opportunities)为单位。
DPU 是代表每件产品或制程平均有几个缺点,而DPMO 是每检查一百万个机会点平均有几个缺点。
一个机会点代表一产品或制程可能会出现缺点的机会,它可能是一个零件、特性、作业等等。
先进的Six Sigma推广机构建义下列几个规则依其复杂程度来计算一个产品或制程出现缺点的机会数
制程能力指数Ca或k(准确度;Accuracy):表示制程特性中心位置的偏移程度,值等于零,即不偏移。
值越大偏移越大,越小偏移越小。
制程准确度Ca(Caoability of Accuracy)
标准公式
简易公式
T=USL-LSL=规格上限-规格下限=规格公差
PS.单边规格(设计规格)因没有规格中心值,故不计算Ca
制造规格将单边规格公差调整为双边规格,如此方可计算Ca
(Xbar -μ) (实绩平均值-规格中心值)
Ca(k) =──────=───────────
(T / 2) (规格公差/2)
T=USL-LSL=规格上限-规格下限=规格公差
PS.制程特性定义
单边规格(设计规格)因没有规格中心值,故不计算Ca
制造规格将单边规格公差调整为双边规格,如此方可计算Ca
当Ca = 0 时,代表量测制程之实绩平均值与规格中心相同;无偏移
当Ca =±1 时,代表量测制程之实绩平均值与规格上或下限相同;偏移100%
评等参考:Ca值愈小,品质愈佳。
依Ca值大小可分为四级
制程特性定义
制程特性依不同的工程规格其定义如下:。
制程精密度Cp(Caoability of Precision)
制程能力指数Cp、Pp、CPU、CPL(精密度;Precision):表示制程特性的一致性程度,值越大越集中,越小越分散。
或:双边能力指数(长期)
:双边绩效指数(短期)
:单边上限能力指数
:单边下限能力指数
USL:特性值之规格上限;即产品特性大于USL在工程上将造成不合格
LSL:特性值之规格下限;即产品特性小于LSL在工程上将造成不合格
:制程平均数估计值;即制程目前特性值的中心位置
:制程标准差估计值;即制程目前特性值的一致程度
PS.制程特性定义
单边规格(设计规格)因没有规格上限或下限
没有规格下限 Cp = CPU = Cpk
没有规格上限 Cp = CPL =Cpk
简易公式
制程精密度Cp(Caoability of Precision)
量测制程之实绩平均值与规格中心的差异性。
(USL-LSL) (规格上限-规格下限)
Cp =──────=───────────
6 σ(6个标准差)
PS.单边规格(设计规格)因没有规格上限或下限
(USL-X) (规格上限-平均值)
Cpu =──────=───────────
3 σ(3个标准差)
(X -LSL) (平均值-规格下限)
Cpl =──────=───────────
3 σ(3个标准差)
制程精密度Cp(Caoability of Precision)之参考判定
当Cp愈大时,代表工厂制造能力愈强,所制造产品的常态分配越集中。
等级判定:依Cp值大小可分为五级
综合制程能力指数Cpk:
同时考虑偏移及一致程度。