重汽供方过程审核书
过程审核作业指导书
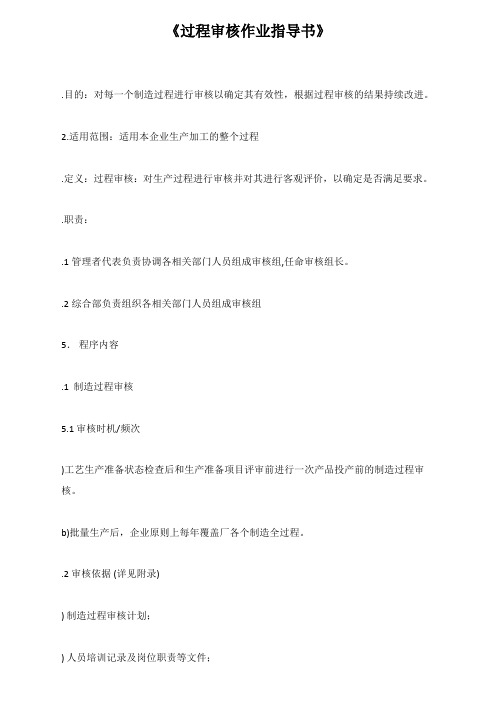
《过程审核作业指导书》.目的:对每一个制造过程进行审核以确定其有效性,根据过程审核的结果持续改进。
2.适用范围:适用本企业生产加工的整个过程.定义:过程审核:对生产过程进行审核并对其进行客观评价,以确定是否满足要求。
.职责:.1管理者代表负责协调各相关部门人员组成审核组,任命审核组长。
.2综合部负责组织各相关部门人员组成审核组5.程序内容.1 制造过程审核5.1 审核时机/频次)工艺生产准备状态检查后和生产准备项目评审前进行一次产品投产前的制造过程审核。
b)批量生产后,企业原则上每年覆盖厂各个制造全过程。
.2 审核依据 (详见附录)) 制造过程审核计划;) 人员培训记录及岗位职责等文件;) 工艺规程文件;d) 产品检验文件;e) 设备、工装管理文件等。
5.3 审核要素) 人员/素质;b) 生产设备/工装;) 运输/搬运/贮存/包装;d) 缺陷分析/纠正措施/持续改进。
.4 基于以下问题的过程,为了消除出现的缺陷,应随时进行制造过程审核:) 产品质量下降;b) 顾客抱怨;c) 生产流程更改;) 过程不稳定;e) 强制降低成本;) 内部部门的愿望。
5.5 制造过程审核采取定量评定方法,根据生产中过程满足该要求的情况进行过程符合性评定。
每个标准的得分分为0、4、6、8和10分,满足要求的程度是打分的根据。
评定不满8分则必须制定改进措施并确定落实期限,出现微小偏差要及时纠正。
打分依据如下表:*):“绝大部分符合”指的是证明已满足了约3/4以上的规定要求,并且没有特别的风险。
每个标准的得分填入《制造过程审核评定表》(附录A),并计算过程要素符合率。
单道工序过程要素符合率的计算公式如下:n[%]=[各相关标准实际得分的总和/各相关标准满分的总和]×100%注n:为工序号)件/总成过程要素总符合率的计算公式如下:p[%]=[E1+E2+------En]/n.6 零件/总成制造过程审核的评定在完成零件/总成过程要素总符合率的计算后,需按下表进行零件/总成制造过程审核的评定。
供方审核报告模版

供方审核报告模版
一、审核目的
本次供方审核的主要目的是评估供方的综合实力、质量管理体系和交货能力,确保供方能够满足我们对产品和服务的需求,保证我们项目的顺利进行。
二、审核范围
1.供方的组织架构和人员配置;
2.供方的质量管理体系和相关证书;
3.供方的生产设备和工艺流程;
4.供方的质量控制措施和检测手段;
5.供方的供货能力和交货周期;
6.供方的售后服务和技术支持;
7.其他相关内容。
三、审核方法
本次审核采用的方法主要包括:
1.文件审查:审核供方的组织结构、质量管理体系文件、设备清单等相关文件;
3.采访:与供方的相关人员进行面对面的交流,了解其质量管理制度的实施情况、供货能力和售后服务等;
4.查阅资料:查阅供方的相关合同、业绩报表和客户反馈等资料。
四、审核结果
经过审核,供方审核结果如下:
1.组织架构和人员配备合理,有足够的技术力量和生产经验来满足我们的需求;
2.供方的质量管理体系完善,已取得了相关证书,并能够有效执行;
3.供方的生产设备齐全,工艺流程科学合理,能够按时交付产品;
4.供方的质量控制措施和检测手段完备,能够确保产品质量;
5.供方的供货能力强,可按时满足我们的需求,交货周期可靠;
6.供方的售后服务和技术支持体系健全,能够及时解决问题,并提供必要的技术指导;
7.其他相关内容符合我们的要求。
五、结论与建议
本次审核结果显示,供方具备满足我们需求的能力,可以作为合格供方。
建议在合同签订后,继续保持对供方的监督和审核,以确保其持续符合我们的要求,并及时解决出现的问题。
六、审核报告编制人员:
编制人:xxx
审核人:xxx。
重汽供方过程审核书

Q/ZZ中国重型汽车集团有限公司企业标准Q/ZZ 50239.4 —2011供方过程审核书2011-06-03 发布2011-06-07 实施中国重型汽车集团有限公司发布Q/ZZ 50239.4 -2011、八前言本标准的附录A、附录B为规范性附录。
本标准为首次制定。
本标准由中国重型汽车集团有限公司提出;本标准由中国重型汽车集团有限公司质量部归口;本标准起草单位:中国重型汽车集团有限公司质量部;本标准主要起草人: 蔡东、张晓东、陈克俊I供方过程审核书1 范围和目的本标准规定了对过程审核的审核内容和报告格式。
供方过程审核的目的是,确认候选供方是否完成了对新配套产品的生产准备,具备批量供货的条件。
过程审核是对整个产品的制造、供货、管理的全过程是否从人、机、料、法、环五个方面全面准备充分,可以持续保持稳定质量向中国重汽供货的基本评价。
2 供方过程审核的内容和报告格式2.1 报告格式见附录A。
2.2 审核内容见附录B。
3 中国重汽的审核人员组成3.1 制造单位负责本产品的采购质量工程师、质量部分管工程师、技术部门专家(第一家供方,必要时参加;第一家之后增加供方,必须参加);技术中心工艺所专家(第一家供方,原则上必须参加,第一家之后增加供方,必要时参加)、产品所设计员(必要时);质量部专家(必要时,可委托制造单位质量部代行职责)。
3.2 审核组长由质量部从组成人员中指定。
4 过程审核的时机过程审核最好在供方进行生产样件制造期间进行。
附录A:编号:中国重汽供方过程审核书候选供方名称 : _________________________审核日期: ________________________供方过程审核书注:分值=(按评审内容所得分值/评审项目数/10 )*100%附录B:供方过程审核内容注意事项:应重点围绕准备为中国重汽配套的产品进行审核。
一、管理和人员--1员工清晰自己对本产品制造的职责,特别是在自检、过程确认(设备点检/首件检验/末件检验)、过程控制(理解控制图)、有序和清洁、零件准备/存放、进行/报请对检验(测量)器具的标定和校准、不合格品隔离等方面。
供方审核记录范例
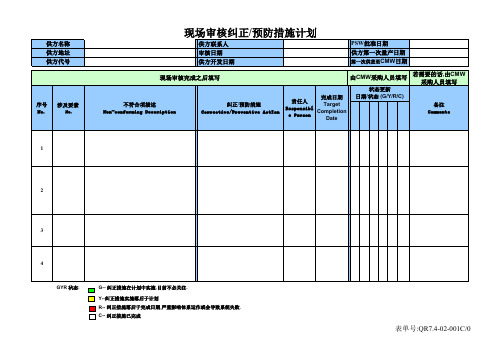
由CMW采购人员填写
完成日期
责任人 Responsibl
Target
e Person Completion
Date
状态更新 日期/状态 (G/Y/R/C)
若需要的话,由CMW 采购人员填写
备注 Comments
1
2
3
4
GYR 状态:
G-- 纠正措施在计划中实施,目前不必关注.
Y--纠正措施实施落后于计划 R-- 纠正措施落后于完成日期,严重影响体系运作或会导致系统失败. C-- 纠正措施已完成
表单号:QR7.4-02-001C/0
供方名称 供方地址 供方代号
序号 涉及要素
No.
No.
现场审核纠正/预防措施计划
供方联系人 审Байду номын сангаас日期 供方开发日期
PSW批准日期 供方第一次量产日期 第一次供货至CMW日期
现场审核完成之后填写
不符合项描述 Non-conforming Description
纠正/预防措施 Corrective/Preventive ActIon
过程审核资料
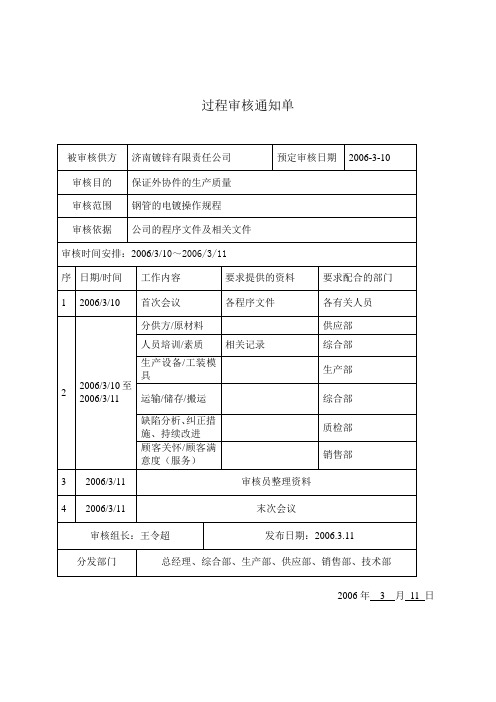
过程审核通知单
2006年 3 月11 日
过程审核计划
编制:王培刚审批:王令超
3
过程审核提问记录表
4
5
6
7
8
过程审核提问记录表
过程要素符合率Ee计算公式:
各相关项目实际得分总和
Ee= ×100%
各相关项目满分总和
过程审核总符合率计算公式:
E1+E2+E3+…En
Epg =91% .
各要素之和
E
降级原因说明:
1.若总符合率超过90%或80%,但其在一个或多个要素上符合率只达到75%以下,则从A降到AB
或从AB降到B;
2.若有的提问得分为0,此不符合要求可能会给产品质量和过程绘制量造成严重的影响,则可从A
降到AB或从AB降到B级。
在特别情况下,也可降为D级。
3.须说明降级的原因。
审核组长:王令超
参加审核人员:王令超、游子荣、王业厚、王培刚、张涛
被审核单位:济南电镀有限责任公司
2006年3月11日
10
过程审核不合格项通知单
审核不合格项整改计划
编制:王培刚审批:王令超
审核不合格项整改计划完成情况验证表
编制:王培刚审批:王令超
13
- 14 -。
供方审核作业指导书
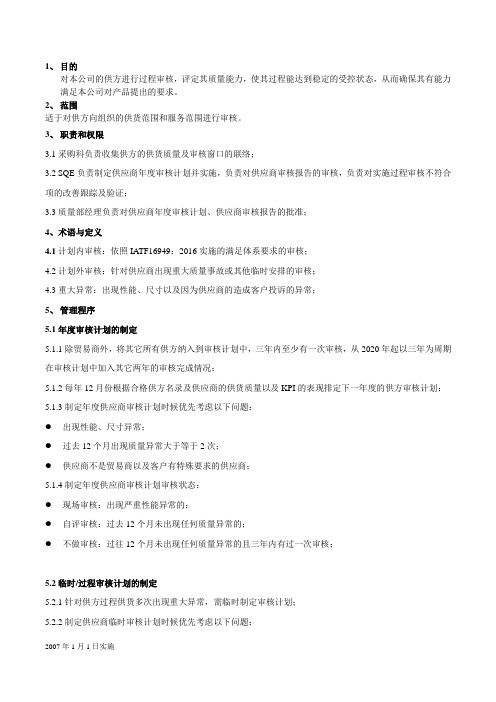
1、目的对本公司的供方进行过程审核,评定其质量能力,使其过程能达到稳定的受控状态,从而确保其有能力满足本公司对产品提出的要求。
2、范围适于对供方向组织的供货范围和服务范围进行审核。
3、职责和权限3.1采购科负责收集供方的供货质量及审核窗口的联络;3.2 SQE负责制定供应商年度审核计划并实施,负责对供应商审核报告的审核,负责对实施过程审核不符合项的改善跟踪及验证;3.3质量部经理负责对供应商年度审核计划、供应商审核报告的批准;4、术语与定义4.1计划内审核:依照IATF16949:2016实施的满足体系要求的审核;4.2计划外审核:针对供应商出现重大质量事故或其他临时安排的审核;4.3重大异常:出现性能、尺寸以及因为供应商的造成客户投诉的异常;5、管理程序5.1年度审核计划的制定5.1.1除贸易商外,将其它所有供方纳入到审核计划中,三年内至少有一次审核,从2020年起以三年为周期在审核计划中加入其它两年的审核完成情况;5.1.2每年12月份根据合格供方名录及供应商的供货质量以及KPI的表现排定下一年度的供方审核计划;5.1.3制定年度供应商审核计划时候优先考虑以下问题:●出现性能、尺寸异常;●过去12个月出现质量异常大于等于2次;●供应商不是贸易商以及客户有特殊要求的供应商;5.1.4制定年度供应商审核计划审核状态:●现场审核:出现严重性能异常的;●自评审核:过去12个月未出现任何质量异常的;●不做审核:过往12个月未出现任何质量异常的且三年内有过一次审核;5.2临时/过程审核计划的制定5.2.1针对供方过程供货多次出现重大异常,需临时制定审核计划;5.2.2制定供应商临时审核计划时候优先考虑以下问题:●同一供方出现3次/月同类异常;●同一供方出现5次/月质量异常;5.3审核前的准备5.3.1根据排定的供应商年度审核计划或临时审核计划,在实施现场审核前10天提出申请,由营销部经理批准后方可实施现场审核;5.3.2申请批准后由SQE制定现场审核实施计划并成立审核小组;5.3.3SQE在审核前一周内编制“XX供应商审核通知”由采购发给对应供应商进行联络,同时收集以下信息:●供应商产品异常信息;●供应商上次审核的不符合项;●供应商调查表●对应产品的3P文件等工艺文件5.4、审核的实施5.4.1、首次会议:阐述审核的目的及时间安排并签到5.4.2、实施审核:由审核员结合顾客要求和体系质量要求,结合其控制计划对供方的制造过程特性实施实地考查,对发现的不符合项,当场向陪审人员进行问题阐述,在适当时,和陪审人员一起寻找解决问题的方式和途径,对过程审核中发现的任何不符合项都必须予以登记;5.4.3、末次会议:审核员进行审核意见汇总,并召开末次会议将发现的问题向供方陪审人员及供方高层管理者进行陈述;5.4.4、供方过程审核报告:审核组组长汇总供方过程审核发现的不符合项目,编写“供方过程审核报告”传递给供方启动不符合项整改活动;5.4.5..对于审核结果进行评分,进行分级管理:A级:以后可视其供货的业绩采取自主审核的方式进行管理;B级:要求在规定的时间3个月内整改完毕;C级:建议采购将其淘汰,或者给三个月时间进行整改后在次进行复审。
过程审核作业指导书(WI-PZ-20) new

过程审核作业指导书(WI-PZ-20)1.0目的用于对质量能力进行评定,使过程能达到受控和有能力在各种干扰因素的影响下仍然稳定受控。
2.0 适用范围与汽车产品制造相关的过程3.0 参考资料:《内部审核管理程序》4.0 职责4.1审核员4.1.1按照审核计划或根据发生的事件实施过程审核。
4.1.2审核员由项目工程师或工程部指定技术人员担任。
4.1.3准备审核(研究资料、制定审核提问表、邀请专家参加等)。
4.1.4实施审核,并进行评分。
4.1.5末次会议和撰写报告。
4.1.6要求采取纠正措施,验证措施的有效性。
4.2被审核部门4.2.1提供所有必要的信息。
4.2.2过程负责人员参与。
4.2.3提供专业人员。
4.2.4确定纠正预防措施并落实4.3业务代表4.3.1过程中工艺技术审核的指导4.4技术部负责项目开发和策划过程中过程审核的实施5.0作业指导5.1过程审核员资格5. 1.1有汽车工业(汽车生产商和供应商)过程管理经验5.1.2必须至少(在专家,如过程技术人员、工艺专家的支持下)进行过一次过程审核5.1.3与被审核活动无直接责任关系5.2审核频次5.2.1制造过程审核采用生产工艺控制方法进行(顾客有特定要求的,依顾客要求执行),每3个日历年覆盖全部制造过程,以确定其有效性和效率。
每个制造过程审核应涵盖所有班次和适当的抽样,并包括对PFMEA、PQCT及相关文件的有效执行的审核。
品质部于每年底制定下年度的过程审核计划报管理者代表批准,过程审核的对象为汽车客户的部品5.2.2在项目开发和策划过程中,制定项目计划时,或每款产品在试生产阶段进行一次过程审核。
5.2.3非定期性的过程审核:产品质量下降;顾客索赔及抱怨;生产流程更改;过程不稳定;部门的愿望等情况下实施临时性过程审核。
5.3审核前准备5.3.1确定审核的过程范围A.审核员或审核小组必须确定要审核的过程。
同时要确定其向外的接口B.把过程划分为工序(把所确定范围内的过程分为单个的过程段)并考虑接口的问题C.根据现有的过程文件资料(作业指导书及检验指导书、过程指导文件、生产工艺文件及检验计划、程序文件、FMEA、上次审核的活动计划、进货检验结果、平面图、顾客调查等)进行过程描述5.3.2确定审核员5.3.3编写针对该具体过程的审核提问表,并必须在审核前及时把提问表传达给被审核方,在需要时进行解释5.3.4需要时制订审核计划5.4审核实施5.4.1首次会议召集相关过程负责人会议,说明审核的目的、范围、依据等5.4.2审核过程①按事先拟定的提问表进行审核,既可按照编码顺序,也可随机提问。
重汽供方过程审核书

Q/ZZ准企业标司团型中国重汽车集有限公201150239.4Q/ZZ -供方过程审核书2011-06-03发布 2011-06-07实施中国重型汽车集团有限公司布发前言B为规范性附录。
本标准的附录A、附录本标准为首次制定。
本标准由中国重型汽车集团有限公司提出;本标准由中国重型汽车集团有限公司质量部归口;本标准起草单位:中国重型汽车集团有限公司质量部;蔡东、张晓东、陈克俊本标准主要起草人:I供方过程审核书1范围和目的本标准规定了对过程审核的审核内容和报告格式。
供方过程审核的目的是,确认候选供方是否完成了对新配套产品的生产准备,具备批量供货的条件。
过程审核是对整个产品的制造、供货、管理的全过程是否从人、机、料、法、环五个方面全面准备充分,可以持续保持稳定质量向中国重汽供货的基本评价。
2供方过程审核的内容和报告格式2.1报告格式见附录A。
2.2 审核内容见附录B。
3中国重汽的审核人员组成3.1制造单位负责本产品的采购质量工程师、质量部分管工程师、技术部门专家(第一家供方,必要时参加;第一家之后增加供方,必须参加);技术中心工艺所专家(第一家供方,原则上必须参加,第一家之后增加供方,必要时参加)、产品所设计员(必要时);质量部专家(必要时,可委托制造单位质量部代行职责)。
3.2 审核组长由质量部从组成人员中指定。
4过程审核的时机过程审核最好在供方进行生产样件制造期间进行。
2附录 A:编号:中国重汽供方过程审核书候选供方名称 :审核日期 : 3供方过程审核书候方 080V02201-0158(机有I适MC07I□新供□在用供方新类别产□在用供方同类别产:邮:::中人和:审职杭重杭重审未审审完管和32产研3生现23分方11成管业审员及组分分综分分10达预8 偏6 的差4 不满预,的差0 未到期Nb: 未审969供结6A□ B□ C□□批准,可按流程继续开发□可按流程继续开发,需整改□不批准,停止开发4不 (;C级)满B要求);级(部分足预期要求期全满( A )方级审过程核分(供等级:级完足预要求) 期能满足预*100%)评审项目数(按评审内容所得分值注:分值=//105附录B:供方过程审核内容注意事项:应重点围绕准备为中国重汽配套的产品进行审核。
- 1、下载文档前请自行甄别文档内容的完整性,平台不提供额外的编辑、内容补充、找答案等附加服务。
- 2、"仅部分预览"的文档,不可在线预览部分如存在完整性等问题,可反馈申请退款(可完整预览的文档不适用该条件!)。
- 3、如文档侵犯您的权益,请联系客服反馈,我们会尽快为您处理(人工客服工作时间:9:00-18:30)。
Q/ZZ
中国重型汽车集团有限公司企业标准
Q/ZZ 50239.4-2011
供方过程审核书
______________________________________________________________________________________________________________
前言
本标准的附录A、附录B为规范性附录。
本标准为首次制定。
本标准由中国重型汽车集团有限公司提出;
本标准由中国重型汽车集团有限公司质量部归口;
本标准起草单位:中国重型汽车集团有限公司质量部;
本标准主要起草人: 蔡东、张晓东、陈克俊
精品资料
供方过程审核书
1范围和目的
本标准规定了对过程审核的审核内容和报告格式。
供方过程审核的目的是,确认候选供方是否完成了对新配套产品的生产准备,具备批量供货的条件。
过程审核是对整个产品的制造、供货、管理的全过程是否从人、机、料、法、环五个方面全面准备充分,可以持续保持稳定质量向中国重汽供货的基本评价。
2供方过程审核的内容和报告格式
2.1报告格式见附录A。
2.2 审核内容见附录B。
3中国重汽的审核人员组成
3.1制造单位负责本产品的采购质量工程师、质量部分管工程师、技术部门专家(第一家供方,必要时参加;第一家之后增加供方,必须参加);技术中心工艺所专家(第一家供方,原则上必须参加,第一家之后增加供方,必要时参加)、产品所设计员(必要时);质量部专家(必要时,可委托制造单位质量部代行职责)。
3.2 审核组长由质量部从组成人员中指定。
4过程审核的时机
过程审核最好在供方进行生产样件制造期间进行。
附录A:
编号:
中国重汽
供方过程审核书
候选供方名称:
审核日期:
供方过程审核书
注:分值=(按评审内容所得分值/评审项目数/10)*100%
附录B:
供方过程审核内容
注意事项:应重点围绕准备为中国重汽配套的产品进行审核。
一、管理和人员-- 1 员工清晰自己对本产品制造的职责,特别是在自检、过程确认(设备点检/首件检验/末件检验)、过程控制(理解控制图)、有序和清洁、零件准备/存放、进行/报请对检验(测量)器具的标定和校准、不合格品隔离等方面。
0□ 4□ 6□ 8□ 10□未评审□
完成所交付的任务。
0□ 4□ 6□ 8□ 10□未评审□
0□ 4□ 6□ 8□ 10□未评审□
0□ 4□ 6□ 8□ 10□未评审□
—建筑物状况良好(如防火能力)
—未来投资计划(包括建筑物更新,技术改造)能保证供方持续经营
—员工穿着、精神状态良好
—设备处于良好管理状态
—清洁保持良好(厕所/生产场所/废品隔离区等地方)
—其它硬件/软件状况使人认为供方有持续的良好管理
0□ 4□ 6□ 8□ 10□未评审□
从业员进行教育?特殊工种必须有特别的审核。
0□ 4□ 6□ 8□ 10□未评审□
7 公司员工对本岗位的满意度,员工流失率统计。
0□ 4□ 6□ 8□ 10□未评审□
二、质量和改进
1 供方至少取得ISO9000体系或TS16949认证,执行良好。
0□ 4□ 6□ 8□ 10□未评审□
到使用,记录保持完整清晰和并可追溯。
0□ 4□ 6□ 8□ 10□未评审□
0□ 4□ 6□ 8□ 10□未评审□
0□ 4□ 6□ 8□ 10□未评审□
0□ 4□ 6□ 8□ 10□未评审□
0□ 4□ 6□ 8□ 10□未评审□
参数更改等。
0□ 4□ 6□ 8□ 10□未评审□
0□ 4□ 6□ 8□ 10□未评审□
9 供方应有材料质量测试实验室(按质量体系的要求配备),制订的检验计划、充分的设备配置,能保证原
材料质量受控。
0□ 4□ 6□ 8□ 10□未评审□
0□ 4□ 6□ 8□ 10□未评审□
最佳是电子数据化的。
0□ 4□ 6□ 8□ 10□未评审□
0□ 4□ 6□ 8□ 10□未评审□
坏情况、包装状态、生产数据、批次等,抽查表明入厂检查执行有效。
0□ 4□ 6□ 8□ 10□未评审□
要求在产品上标识永久二维码及流水号,供方有能力实现。
0□ 4□ 6□ 8□ 10□未评审□
实施、信息取得闭环。
0□ 4□ 6□ 8□ 10□未评审□
1 供方在本产品的研发中执行了标准的研发流程;用于策划和实施的工具和资源足够。
0□ 4□ 6□ 8□ 10□未评审□
2 供方为本产品的研发配备充分的有水准的人力和物资资源;采用CA系统(CATIA V5/pro-E)软件和相关分析工具。
对本产品开展了“设计失效模式及后果分析(DFMEA),并有针对性地采取了相关风险防范措施。
把过去的品质实绩(过往缺陷等)及预测的项目反映到设计及规格上的规则、途径是否明确?品质缺陷的不良预防、再发防止项目有否依据以上的规则途径反映到图纸及规格中?
0□ 4□ 6□ 8□ 10□未评审□
0□ 4□ 6□ 8□ 10□未评审□
0□ 4□ 6□ 8□ 10□未评审□
验证、试验需要。
0□ 4□ 6□ 8□ 10□未评审□
清晰哪些变更应事先通知中国重汽并得到同意方可启动。
0□ 4□ 6□ 8□ 10□未评审□
0□ 4□ 6□ 8□ 10□未评审□
1 生产设备/工装模具/刀具能保证满足产品特定的质量要求
-生产设备、工装模具的选型及设计,过程(工艺)的设计充分考虑了“过程失效模式及后果分析(PFMEA)的关键风险要素;
-产品的符合性达标,特别是供方定义的(包括中国重汽定义的)可测量的重要产品特性,其符合性被有效保证;
-供方对过程能力的研究、测定(评审)表明,在规定的工艺参数条件下,过程能力满足要求;
-工装模具/设备/机器的保养和维修状态能满足要求。
0□ 4□ 6□ 8□ 10□未评审□
2 将在批量生产中使用的测量和检验设备能有效地满足质量监控要求
-检验规范、检验计划清晰,完整;
-检测装置(设备)充分、精度合适,并处于检定(校准)周期内。
0□ 4□ 6□ 8□ 10□未评审□
-照明、清洁有序、环境保护、工作环境满足要求;
-工位器具、零件搬运满足要求;
-安全生产满足要求。
0□ 4□ 6□ 8□ 10□未评审□
-操作说明和要求清晰、完整;
-过程参数(如,进给量/速度/循环时间/压力/温度)清晰、完整;
-设备/工装摸具型号清晰、完整;
-检验规范(量具、检验器具、方法、检验频次)清晰、完整,重要的特性被特殊重视;
-所用材料清晰、完整;
-对工作环境的要求清晰、完整。
0□ 4□ 6□ 8□ 10□未评审□
-明确不合格品的分类及特性,如废品、返工返修件、调整零件、车间里的余料等;
-设置隔离库(区)、标识明显的废品箱、返工返修件箱、调整件箱等;
-分选工位、返修工位设置清晰。
0□ 4□ 6□ 8□ 10□未评审□
设备合适地存放。
-产品的周转器具及存放定置、合理、有序、防损伤;
-运输器具配置合理、有效;
-现场有序、清洁;
-工装模具、检测设备合适地存放,防损伤、有序、清洁、标识清晰。
0□ 4□ 6□ 8□ 10□未评审□
7 现场物流过程保证了不混批/不错料,并确保了可追溯性
-半成品、原料、不同检验状态的件与成品有效分隔,并标识清晰;
。