75t锅炉脱硫技术方案
锅炉烟气脱硫技术方案

锅炉烟气脱硫技术方案锅炉烟气脱硫技术是指通过一系列化学反应或物理吸附作用,将烟气中的SO2转化为可排放的形式,从而达到减少环境污染的目的。
下面是一份锅炉烟气脱硫技术方案。
1. 工艺流程锅炉烟气脱硫工艺主要包括前处理、吸收反应、释放反应、过滤、水洗和降温等程序。
前处理:对烟气进行处理,主要包括除尘、脱酸和脱氧等。
吸收反应:采用干法吸收或湿法吸收等技术,将烟气中的SO2和吸收剂产生化学反应,形成硫酸。
释放反应:通过加热、稀释等方式,将硫酸分解为SO2和H2O,其中SO2可以与碱性物质反应,生成稳定的硫化物,如CaSO3、CaSO4等。
过滤:通过布袋过滤器等装置,去除烟气中的颗粒物和异味物质等。
水洗:采用水雾冲洗或水浴冷凝等方式,将烟气中的微量颗粒和一部分SO2洗净。
降温:将烟气降温至环境标准,通过冷凝、燃烧余热等方式回收能量。
2. 工艺特点(1)适用广泛:该工艺适用于燃煤、燃油和燃气等不同种类的锅炉烟气。
(2)效果显著:该工艺可以将烟气中的SO2去除率达到90%以上,满足国家相关标准。
(3)投资低:该工艺设备采用常规材料和技术,成本相对较低。
(4)运行费用低:该工艺采用高效吸收剂,可降低吸收剂的用量及维护费用。
(5)环保安全:该工艺在脱硫过程中不会产生二氧化碳等有害物质,且操作简单,对工人的伤害小。
3. 工艺设备(1)烟气处理系统:包括前处理、吸收、排放和过滤等装置。
(2)吸收液循环系统:包括吸收液储罐、泵、管道和冷却器等组成。
(3)SO2释放系统:包括加热器、分离器、冷却器和泵等。
(4)废弃物处理系统:包括废水处理系统和废渣处理系统等。
(5)控制系统:包括机电自动控制系统和PLC控制系统等。
4. 工艺布局工艺布局应尽量紧凑,设备间的距离要短,不仅方便操作、检修,还能节约场地,降低工程费用。
设备的高度要考虑到操作、维护和安全等因素,同时也要注意烟道的结构和通风情况,以便保证烟气流畅,工艺效果和安全性能达到最佳。
75t链条炉脱硫脱硝pncr脱硝原理及工艺流程
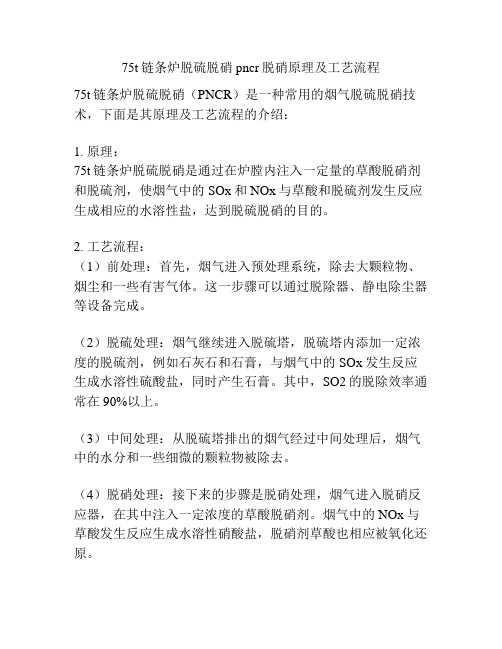
75t链条炉脱硫脱硝pncr脱硝原理及工艺流程
75t链条炉脱硫脱硝(PNCR)是一种常用的烟气脱硫脱硝技术,下面是其原理及工艺流程的介绍:
1. 原理:
75t链条炉脱硫脱硝是通过在炉膛内注入一定量的草酸脱硝剂和脱硫剂,使烟气中的SOx和NOx与草酸和脱硫剂发生反应生成相应的水溶性盐,达到脱硫脱硝的目的。
2. 工艺流程:
(1)前处理:首先,烟气进入预处理系统,除去大颗粒物、烟尘和一些有害气体。
这一步骤可以通过脱除器、静电除尘器等设备完成。
(2)脱硫处理:烟气继续进入脱硫塔,脱硫塔内添加一定浓度的脱硫剂,例如石灰石和石膏,与烟气中的SOx发生反应生成水溶性硫酸盐,同时产生石膏。
其中,SO2的脱除效率通常在90%以上。
(3)中间处理:从脱硫塔排出的烟气经过中间处理后,烟气中的水分和一些细微的颗粒物被除去。
(4)脱硝处理:接下来的步骤是脱硝处理,烟气进入脱硝反应器,在其中注入一定浓度的草酸脱硝剂。
烟气中的NOx与草酸发生反应生成水溶性硝酸盐,脱硝剂草酸也相应被氧化还原。
(5)除尘:最后一步是除尘处理,通过除尘器将剩余的颗粒
物和细微粉尘从烟气中去除,使排放口的烟气达到环保要求。
总的来说,75t链条炉脱硫脱硝(PNCR)的原理是通过在炉
膛内注入草酸脱硝剂和脱硫剂,使烟气中的SOx和NOx与草
酸和脱硫剂发生反应生成水溶性盐,从而实现烟气中SOx和NOx的脱除。
其工艺流程包括前处理、脱硫处理、中间处理、脱硝处理和除尘处理等步骤。
半干法脱硫技术方案(1)

3×75t锅炉烟气脱硫除尘工程总承包技术方案业主方:总包方:山东先进能源科技有限公司二○一八年三月目录1、技术规范 (2)1.1工程范围 (2)1.1.1设计范围: (2)1.1.2设计内容 (2)1.1.3设备制造及供货 (4)1.1.4设备及系统安装 (25)1.2设计基础资料 (26)1.2.1锅炉主要特性 (26)1.2.6厂址气象和地理条件 (28)1.2.7土建设计基础资料 (29)1.3工程方案 (30)1.3.1工艺设计 (30)1.3.2主要设计原则 (30)1.3.3方案设计 (31)1.4性能保证值 (34)1.5总包方提供的基本参数 (35)1.6设备清册(设备厂家供参考、设备选型以初设选型为准) (41)2业主人员培训 (48)2.1培训内容 (48)2.2培训方式 (48)2.3设计联络会 (49)3 监造、检验和性能验收试验 (51)2.1概述 (51)2.2工厂检验 (51)2.3设备监造 (52)1、技术规范1.1工程范围山东临沂电厂位于位于临沂市以南,距市区约3公里,在大菜园村以南,许家冲村以西地区,北距临沂火车站3公里,东距沂河5公里,位于临沂市规划区范围以内。
为改善电厂周围及临沂地区的大气环境,根据临沂发电厂二氧化硫治理规划和环保要求,临沂电厂将继续对剩余锅炉进行脱硫技改工作,本期工程将先行对5#、6#锅炉加装脱硫装置。
综合各方面情况考虑,临沂电厂机组设计含硫量为2.0%。
本工程为改造工程,采用循环流化床(干法)脱硫工艺,其装置在60%-100%BMCR工况下进行全烟气脱硫,脱硫效率不低于90%。
本工程包括脱硫除尘岛内系统正常运行、紧急情况处理及检修等所必需具备的工艺系统设计、设备选择、采购、运输及储存、制造及安装、土建建(构)筑物的设计、施工、调试、试验及检查、试运行、考核验收、消缺、培训和最终交付投产等方面的内容。
总包应对脱硫除尘岛的性能负全部责任。
2X75t锅炉半干法脱硫工艺图

半干法脱硫技术方案2×75t/h循环流化床锅炉烟气脱硫除尘技术方案第一章技术规范1.1总则本技术方案适用于2×75t/h循环流化床锅炉烟气脱硫除尘工程系统的功能设计。
1.2.工程概况项目名称: 2×75t/h循环流化床锅炉烟气脱硫除尘工程建设地点:现有2台75t/h锅炉,根据该公司的环保目标,SO2达标排放浓度减排90%以上,粉尘达标排放浓度为30mg/Nm3。
所以现对二台锅炉做出以下半干法脱硫配有单元布袋除尘器。
本技术方案所涉及范围为1台75吨锅炉炉后全套除尘、脱硫系统等。
1.3设计和运行条件1.3.1锅炉1.3.2 烟气参数表根据贵公司的所提供的参数1.3.3吸收剂本技术方案的脱硫剂采用消石灰。
根据《建筑石灰试验方法化学分析方法》(JC/T478.1一92)和《建筑石灰试验方法物理试验方法》(JC/T478.1一92),检验结果如下:氢氧化钙(Ca(0H)2)>含量:90 % 粒度:100% < 1mm 90% < 0.8mm消化速度:T60<4min1.3.4设计要求脱硫率>90% ,SO2排放浓度≤100mg/Nm³,除尘器排放浓度≤30mg/Nm³1.4规范与标准脱硫除尘系统及其配套辅机设计、制造、检验原则上采用中国现行规范和标准,但凡按引进技术设计制造的设备,均按引进技术相应的标准,若本公司使用的规范及标准与本技术规范所用标准发生矛盾时,按较高标准执行。
本技术规范书要求符合(但不限于)下列规范及标准:设计标准1) 技术方案的设计符合《火力发电厂设计技术规程》(DL5000-2000)规定。
2) DL/T5054-1996 《火力发电厂汽水管道设计技术规定》3) DL/T5072-1997 《火力发电厂保温油漆技术规范》4) DL468-92 《电站锅炉风机选型和使用导则》第二章技术方案2.1对脱硫除尘装置总的技术要求1) 锅炉脱硫系统在正常工况下运行时,保证系统的脱硫效率大于90%,除尘效率高于99.8%,脱硫后除尘器出口烟温不低于97℃。
275th锅炉烟气脱硫工程技术方案

2×75t/h锅炉烟气脱硫工程技术方案目录第一章概述 (1)1.1.总则 (1)1.2.基本原则 (1)1.3.基本数据及设计要求 (1)1.4设计原则 (2)1.5设计依据 (3)1.6.标准和规 (3)第二章脱硫工程建设条件 (6)2.1吸收剂供应 (6)2.2脱硫副产物处置及综合利用 (6)2.3脱硫场地 (6)2.4供水供电 (6)2.5FGD装置和现有系统的相互影响 (7)第三章脱硫工艺方案选择 (8)3.1、几种常用脱硫工艺介绍 (8)3.2、脱硫工艺确定 (11)第四章脱硫工程方案 (12)4.1设计基础数据 (12)4.2脱硫工艺系统概述 (12)4.3箱罐和容器 (15)4.4管道 (16)4.5防腐措施 (16)4.6脱硫系统主要技术指标 (17)4.7锅炉二氧化硫脱硫前后对比 (18)4.8石灰—石膏法石灰粉量 (18)4.9主要设备结构特点及简图 (19)4.10主要工艺设备及费用清册 (21)第五章热控系统 (25)5.1脱硫分散控制系统的监控围包括: (25)6.2热控主要设备清册 (27)第六章土建、暖通、消防和给排水部分 (28)6.1脱硫岛的总体布置 (28)6.2结构部分 (28)6.3建筑部分 (28)6.4采暖、通风、空气调节及除尘系统 (28)第七章节约和合理利用能源 (30)7.1节约能源 (30)7.2节约用水 (30)第八章节约和合劳动安全和劳动保护 (31)8.1劳动安全 (31)8.2劳动保护 (32) (33)3410.1安全目标 (34)10.2安全生产保障保证体系 (34)10.3安全保证计划 (35)10.4安全保证措施 (35)10.5安全生产动态管理 (38)10.6安全生产制度及保障措施 (39)10.7大型机械设备安装及拆除措施 (41)第十一章施工现场组织机构图 (43)第一章概述1.1.总则某能源2×75t/h锅炉,为了保护工厂周围的生产、生活环境,并使个烟气锅炉烟气排放总量及指标达到有关标准,锅炉计划配套建设烟气脱硫装置。
75t锅炉烟气脱硫设计方案

75t锅炉烟气脱硫设计方案第一篇:75t锅炉烟气脱硫设计方案75t/h燃煤锅炉烟气脫硫技术方案第一部分设计参数及要求1.设计基本参数(由买方单位提供)锅炉型号:CG-65/3.82-M12 锅炉蒸发量:65t/h.台锅炉台数:2台燃煤消耗量:12t/h.台热态烟气量:160000m3/h.台排烟温度:130℃ 燃煤含硫:1.5% 燃煤灰分:26% 烟尘初始浓度:57000mg/m3 现有除尘器:三级静电除尘器除尘效率:95% 引风机型号:YKK4502-6压:3776Pa 2.设计要求SO2排放浓度:≤200mg/N m3流量:197000 m3/h 全烟尘浓度:≤80mg/N m3系统长期稳定运行,操作维护方便。
3.脱硫工艺采用双碱法旋流板塔脱硫除尘工艺。
第二部份设计方案一、设计原则二、设计工艺三、吸收及再生液流程说明四、设计系统液气比及钙硫比和PH值五、设计技术保证一、设计原则1.本项目工程我公司的原则是:为采购方着想,提供的设备要高效,使用方便耐用;在满足采购方提出的排放要求的前提下,投资及运行费用尽可能的低,经济效益尽可能的高。
2.所选择的工艺成熟可靠,不能产生二次污染。
3.原有引风机、土建烟道、烟囱不作改动,全部利用。
二、设计工艺1.本项目采购方指定要求采用双碱法旋流板塔脱硫工艺。
2.双碱法:双碱法是同时利用钠碱NaOH与石灰乳Ca(OH)2的方法,是利用Na(OH)在脱硫塔内与溶于水的SO2+ H2O+O2→SO42-(硫酸根)反应,生成Na(SO)4 ,硫酸钠以溶液状排出脱硫塔外后,再在反应池内与Ca(OH)2反应,即NaSO4+Ca(OH)2+H2O→CaSO4↓+ NaOH。
这样硫酸钙被沉淀,SO2被除去,NaOH再生,重复使用,消耗的是石灰。
运行费用同样较低,设备不易阻塞,有利于提高脱硫效率,是目前中小型企业,采用的较经济、较先进的工艺。
故此,本方案也选用该脱硫工艺。
吸收反应:2NaOH + SO2 → Na2SO3 + H2O Na2CO3 + SO2 → Na2SO3 + CO2 Na2SO3 + SO2 + H2O → 2NaHSO3 该过程中由于是用钠碱作为吸收液,因此系统不会生成沉淀性结垢。
75吨锅炉双碱法脱硫方案
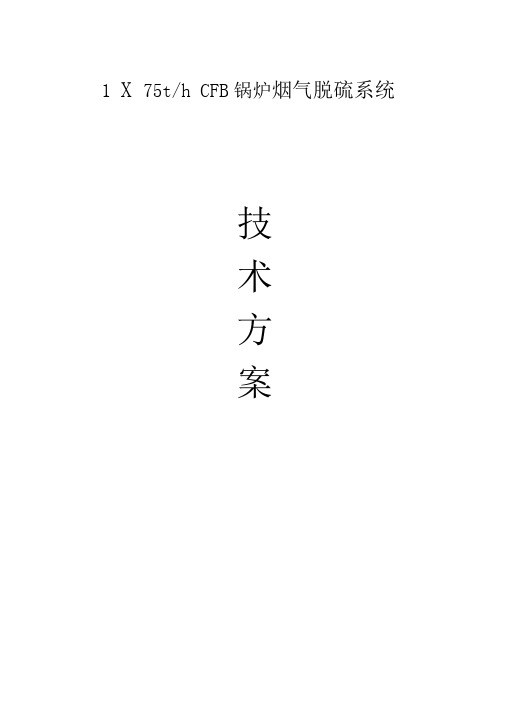
1 X 75t/h CFB锅炉烟气脱硫系统技术方案目录1 建设方概况2...2 设计依据及设计原则2...2.1 设计依据和标准2...2.2 工程主要原始资料3..2.3 设计原则4...3 设计范围及要求5...3.1 设计范围5...3.2 主要技术要求5...4 工艺选择5...4.1 脱硫技术简介........................................................................... 5. ..5 双碱法脱硫机理7...6 双碱法脱硫工艺的优势8..7 双碱法工艺描述8...7.1 双碱法工艺流程工艺描述........................................................................... 8. .7.2 分系统描述9...1建设方概况1台75t/h循环流化床锅炉,通过烟囱排放烟气;按国家环保要求,需要进行烟气脱硫和脱销,以保证锅炉出口烟气S02达标排放,本工艺建议采用钠钙双碱法脱硫工艺。
本方案为1炉1塔的烟气脱硫工程钠钙双碱法技术方案。
2设计依据及设计原则2.1设计依据和标准GB3095-1996 《环境空气质量标准》GB16297- 1996 《大气污染物综合排放标准》GB13223-2011 《火电厂大气污染物排放标准》HJ/T 75- 2001 《火电厂烟气排放连续监测技术规范》GB12348-90 《工业企业厂界噪声标准》GB8978-1996 《污水综合排放标准》DLGJ102-91 《火力发电厂环境保护设计技术规疋(试仃)及条文说明》HJ462-2009 《工业锅炉及窑炉湿法烟气脱硫工程技术规范》DL/T 5196 —2004 《火力发电厂烟气脱硫设计技术规程》DL 5000 —2000 《火力发电厂设计技术规程》DL/T 5094 —1999 《火力发电厂建筑设计规程》DL/T5121 —2000 《火力发电厂烟风煤粉管道设计技术规程》DL/T5054-1996 《火力发电厂汽水管道设计技术规定》GB/T17116.1-1997 《管道支吊架第一部分:技术规范》GB/T17116.2-1997 《管道支吊架第二部分:管道连接部件》GB/T17116.3-1997 《管道支吊架第三部分:中间连接件和建筑结构连接件》GB4272-92 《设备及管道保温技术通则》GB50046-95 《工业建筑防腐蚀设计规范》GB50052-95 《供配电系统设计规范》GB50054-95 《低压配电设计规范》GB50055-93 《通用用电设备配电设计规范》GB50057-94 《建筑物防雷设计规范》GB50217-94 《电力工程电缆设计规范》GBJ65-83 《工业与民用电力装置的接地设计规范》DL/T 5175-2003 《火力发电厂热工控制系统设计技术规定》NDGJ16-89 《火力发电厂热工自动化设计技术规疋》SDGJ17-88 《火力发电厂厂用电设计技术规定》GB50037-1996 《建筑地面设计规范》GBJ10-89 《混凝土结构设计规范》GB50017 《钢结构设计规范》2.2 工程主要原始资料2.2.1 锅炉配置的主要设备锅炉配置引风机:Q约为150000m3/h, P约为5076-4912Pa222锅炉参数(单台炉)额定蒸发量(B —MCR): 75t/h额定蒸发压力(表压): 5.29MP a额定工况时耗煤量:t/h排烟温度:暂按150°C -170r 收到基含硫量<1.5%烟气排放量约为150000 m3/h 223锅炉燃料成份224脱硫剂成份吸收剂采用当地生产的生石灰粉根据《建筑石灰试验方法化学分析方法》(JC/T478.1-92 )和《建筑石灰试验方法物理试验方法》(JC/T478.1-92)规定的检验方法,生石灰粉品质应满足以下条件:CaO 纯度>85%活性t6o w 4min(注:t60表示石灰加水后升温60C所需时间,按DIN EN459-2标准执行)粒径<2mm2.2.5烟气脱硫装置(FGD)设计参数(根据经验值)2.3设计原则(1)脱硫和脱销系统能够安全可靠运行。
t锅炉脱硫技术方案
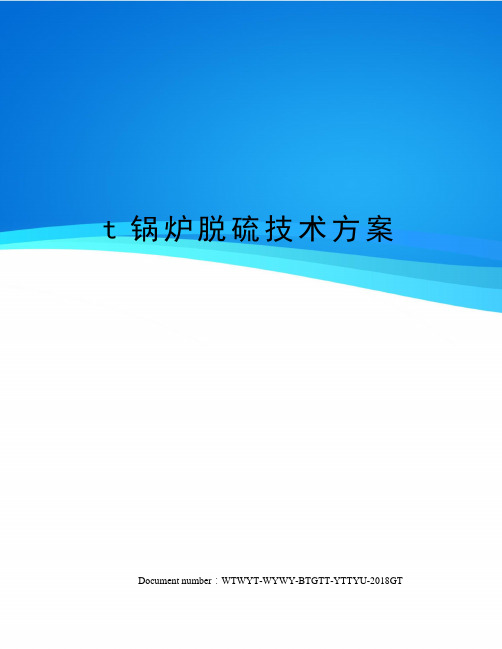
t锅炉脱硫技术方案 Document number:WTWYT-WYWY-BTGTT-YTTYU-2018GT75t/h煤粉炉烟气脱硫(湿式钙法)技术方案目录3×75t/h煤粉炉烟气脱硫工程1 总则1)本技术方案适用于中盐吉兰泰盐化集团制碱事业部3×75t/h煤粉炉烟气脱硫工程,根据环保要求,结合业主实际情况及业主方要求,对中盐吉兰泰盐化集团制碱事业部3×75t/h煤粉炉烟气脱硫工程编制本技术方案。
本技术方案设计为三炉三塔湿式钙法法脱硫工艺,脱硫效率达到98%以上,能够满足国家现有的相关安全、环保等强制性法规、标准的要求,并具有前瞻性。
2)本技术方案的内容是按3×75t/h煤粉炉脱硫系统编制。
其中脱硫岛主要包括浆液制备及输送系统、烟气系统、SO2吸收系统、工艺水系统、副产品处理系统,脱硫岛外辅助系统主要包括向脱硫岛的供电、供水、供气及结构建筑工程部分。
3)脱硫装置是完整的、安全的、经济的、可靠的。
脱硫装置按20年寿命设计。
所提供的设备是最新技术。
4)本工程设计根据目前国内同类型锅炉烟气脱硫项目的经验,并结合本工程的实际情况,原则上设备及材料国内采购,关键设备进口。
5)脱硫岛整体设计布局紧凑、合理、系统顺畅,运行经济,节省占地,节省投资,脱硫工艺流程合理,并缩短各种工艺管线,,及维护和检修的方便。
6)贯彻节约用水的原则,减少水量消耗。
7)工艺系统设计和设备技术先进、安全可靠与锅炉100%同步运行。
8)系统年利用小时数按8400小时考虑(24小时350天)。
2 概述项目概述中盐吉兰泰盐化集团制碱事业部现有75t/h煤粉炉三台,从锅炉烟囱排出的废气含有SO2、氮氧化物、粉尘等既影响操作区环境,又污染大气,根据环保有关规定,SO2、颗粒物等污染物排入大气必须达标排放。
河北华强科技开发有限公司对业主方提供的锅炉相关数据资料进行了认真分析,根据业主的实际情况和具体要求,,结合我公司的技术优势,采用湿式法烟气脱硫工艺的技术方案,脱硫系统采用三炉三塔设计方案。
- 1、下载文档前请自行甄别文档内容的完整性,平台不提供额外的编辑、内容补充、找答案等附加服务。
- 2、"仅部分预览"的文档,不可在线预览部分如存在完整性等问题,可反馈申请退款(可完整预览的文档不适用该条件!)。
- 3、如文档侵犯您的权益,请联系客服反馈,我们会尽快为您处理(人工客服工作时间:9:00-18:30)。
75t/h煤粉炉烟气脱硫(湿式钙法)技术方案目录1 总则 (1)2 概述 (2)2.1 项目概述 (2)2.2 脱硫系统概述 (2)2.3 总体设计原则 (3)2.4设计主要标准和规范 (3)2.5 设计参数 (4)3 脱硫工艺说明 (5)3.1湿式钙法脱硫工艺介绍 (5)3.2工艺特点 (6)4.1 处理烟气量 (7)原始排放浓度 (7)4.2 SO24.3 脱硫效率 (7)4.4 生石灰粉耗量、年脱硫量、石膏年产量 (7)4.5 脱硫反应循环液气比 (7)4.6 Ca/S摩尔比 (7)4.7 10%CaO浆液量 (8)4.8 溶液循环流量 (8)4.9 耗水量 (8)4.10 电耗量 (8)5 运行费用(单台系统) (8)5.1 经济指标 (8)5.2 脱硫运行成本 (8)6 建造费用 (9)3×75t/h煤粉炉烟气脱硫工程1 总则1)本技术方案适用于中盐吉兰泰盐化集团制碱事业部3×75t/h煤粉炉烟气脱硫工程,根据环保要求,结合业主实际情况及业主方要求,对中盐吉兰泰盐化集团制碱事业部3×75t/h煤粉炉烟气脱硫工程编制本技术方案。
本技术方案设计为三炉三塔湿式钙法法脱硫工艺,脱硫效率达到98%以上,能够满足国家现有的相关安全、环保等强制性法规、标准的要求,并具有前瞻性。
2)本技术方案的内容是按3×75t/h煤粉炉脱硫系统编制。
其中脱硫岛主要包括浆液制备及输送系统、烟气系统、SO2吸收系统、工艺水系统、副产品处理系统,脱硫岛外辅助系统主要包括向脱硫岛的供电、供水、供气及结构建筑工程部分。
3)脱硫装置是完整的、安全的、经济的、可靠的。
脱硫装置按20年寿命设计。
所提供的设备是最新技术。
4)本工程设计根据目前国内同类型锅炉烟气脱硫项目的经验,并结合本工程的实际情况,原则上设备及材料国内采购,关键设备进口。
5)脱硫岛整体设计布局紧凑、合理、系统顺畅,运行经济,节省占地,节省投资,脱硫工艺流程合理,并缩短各种工艺管线,,及维护和检修的方便。
6)贯彻节约用水的原则,减少水量消耗。
7)工艺系统设计和设备技术先进、安全可靠与锅炉100%同步运行。
8)系统年利用小时数按8400小时考虑(24小时350天)。
2 概述2.1 项目概述中盐吉兰泰盐化集团制碱事业部现有75t/h煤粉炉三台,从锅炉烟囱排出的废气含有SO2、氮氧化物、粉尘等既影响操作区环境,又污染大气,根据环保有关规定,SO2、颗粒物等污染物排入大气必须达标排放。
河北华强科技开发有限公司对业主方提供的锅炉相关数据资料进行了认真分析,根据业主的实际情况和具体要求,,结合我公司的技术优势,采用湿式法烟气脱硫工艺的技术方案,脱硫系统采用三炉三塔设计方案。
我公司引进国外先进、可靠性高、技术成熟的喷淋空塔烟气脱硫工艺,对该技术进行深入的研究、消化,并在工程实践中不断优化和完善该工艺,比如脱硫塔烟气均流装置已形成了具有自身特色的高效脱硫技术工艺。
2.2 脱硫系统概述2.2.1本工程为脱硫塔改造工程,我公司根据贵公司提供的数据设计如下方案:1)炉内喷钙脱硫+炉外半干法脱硫(原有设备),炉内喷钙脱硫效率50%,炉外半干法脱硫效率80%,贵公司提供的数据为:SO2初始浓度为4500mg/Nm3,脱硫后净烟气SO2浓度为150mg/Nm3。
4500mg/Nm3*50%*20%=450mg/Nm3,故这种改造方式不能达到脱硫要求。
2)炉外半干法脱硫(原有设备)+冲渣水脱硫,贵公司提供的冲渣水数据为170m3/h,如此水量只能让SO2浓度为4500mg/Nm3脱硫至2600mg/Nm3左右,而半干法脱硫(原有设备)脱硫效率为80%,即2600mg/Nm3*0.2=520mg/Nm3,故这种改造方式亦不能达到脱硫要求。
3)湿法(石灰-石膏法)烟气脱硫装置,此法烟气脱硫是现今用途最广、工艺最成熟、脱硫效率较高的一种脱硫工艺,在合适液气比的情况下可达到98%以上。
按SO2浓度为4500mg/Nm3计算,4500mg/Nm3*0.02=90mg/Nm3,完全满足环保要求。
2.2.2本工程为在75t/h煤粉炉引风机出口烟道至主烟囱间建设烟气脱硫装置。
脱硫入口烟气接自煤粉炉引风机出口经烟道至脱硫塔,经过脱硫后,净烟气通过塔顶烟囱排放,新标准规定系统不设旁路系统。
2.2.3本工程建设内容为烟气系统、SO2吸收系统、吸收剂输贮及制备系统、副产物系统、检修起吊设施、废水处理系统、烟囱防腐、给排水系统、热力系统、供配电系统、仪表及控制系统、通信及火灾自动报警系统、结构建筑、总图及运输等保证脱硫系统正常运行的全部设施。
2.3 总体设计原则本装置采用三炉三塔系统配置。
烟气脱硫效达98%以上。
按照《工业锅炉及窑炉湿法烟气脱硫工程技术规范》(HJ462-2009)的规定和中盐吉兰泰盐化集团制碱事业部的要求,烟气脱硫后达到如下指标:<150(mg/Nm3) 烟尘<50(mg/Nm3)SO2脱硫工艺系统主要由吸收浆液制备及输送系统、烟气系统、SO2吸收系统、工艺水系统、脱硫副产品处理系统、电气控制系统、滤液处理系统组成。
烟气进入吸收塔进行脱硫。
脱硫后的净烟气通过塔顶烟囱或者经原烟囱排放至大气。
2.4设计主要标准和规范2.5 设计参数2.5.2脱硫剂参数2.5.3能源介质条件(1)电源:220/380V±10%(单相/三相);频率:50Hz±2%。
(2)蒸汽:0.6~0.8MPa(表压)(3)原水:在界区处的工作数据—温度:地下水;—绝压:≥0.4MPa;—经过滤,无泥砂、腐蚀性物质和有机物。
3 脱硫工艺说明3.1湿式钙法脱硫工艺介绍3.1.1 原理湿式钙法脱硫工艺是一种利用碱金属钙的氧化物。
氢氧化物作为SO2的吸收剂,净化处理烟气的工艺。
系统主要由吸收剂制备系统、二氧化硫吸收系统和烟气系统组成。
来自除尘器的烟气经过升压后经原烟道挡板门后进入吸收塔,在吸收塔内进行SO2的脱除。
吸收液通过喷嘴雾化喷入吸收塔,分散成细小的液滴并覆盖吸收塔的整个断面。
这些液滴与塔内烟气逆流接触,发生传质与吸收反应,烟气中的SO2、SO3被吸收。
SO2吸收产物的氧化和中和反应在吸收塔底部的氧化区完成并最终形成石膏。
为了维持吸收液恒定的pH值并减少石灰耗量,石灰浆液被连续加入吸收塔,同时吸收塔内的吸收剂浆液被搅拌机、氧化空气和吸收塔循环泵不停地搅动,以加快石灰在浆液中的均布和溶解。
3.1.2 化学过程1)SO2 + H2O→H2SO3吸收2)Ca(OH)2 + H2SO3→CaSO3+ 2H2O 中和3)CaSO3 + 1/2 O2→CaSO4氧化4)CaSO3 + 1/2 H2O→CaSO3·1/2H2O 结晶5)CaSO4 + 2H2O→CaSO4·2H2O 结晶6)CaSO3 + H2SO3→Ca(HSO3)2pH控制同时烟气中的HCL、HF与Ca(OH)2的反应,生成CaCl2或CaF2。
吸收塔中的pH值通过注入石灰石浆液进行调节与控制,一般pH值在5.5~6.5之间。
3.1.3工艺流程图本工程脱硫系统由烟气系统、喷淋反应塔吸收系统、氧化钙制浆系统、石膏回收系统、废水处理系统、工艺水系统、自动控制系统等组成。
氧化钙湿法脱硫工艺流程:氧化钙粉经加水消化制成10~15%浓度的浆液,用乳液泵打入脱硫塔下部贮液槽中,再经循环泵打入喷淋系统,喷淋脱硫。
为了避免溶液饱和,塔底定期自动外排5%左右的脱硫废水,废水经处理后大部分循环回用,小部分达标后排放。
在我国,重庆珞璜电厂首次引进了日本三菱公司的石灰石—石膏湿法脱硫工艺,脱硫装置与两台360MW燃煤机组相配套。
机组燃煤含硫量为4.02%,脱硫装置入口烟气二氧化硫浓度为3500ppm,设计脱硫效率大于95%。
该工艺的流程图见下图。
详细脱硫除尘流程图见附图。
3.2工艺特点(1)脱硫效率高。
湿式钙法脱硫工艺脱硫率高达98%以上,脱硫后的烟气不但二氧化硫浓度很低,而且烟气含尘量也大大减少。
(2)技术成熟,运行可靠性好。
国外湿式钙法脱硫装置投运率一般可达98%以上,由于其发展历史长,技术成熟,运行经验多,因此不会因脱硫设备而影响设备的正常运行。
特别是新建脱硫工程采用湿法脱硫工艺,使用寿命长,可取得良好的投资效益。
(3)吸收剂资源丰富,价格便宜。
作为湿式钙法脱硫工艺吸收剂的石灰石,在我国分布很广,资源丰富,许多地区石灰石品位也很好,碳酸钙含量在90%以上,优者可达95%以上,制得石灰价格也低廉。
运行费用低。
(4)脱硫副产物便于综合利用。
湿式钙法脱硫工艺的脱硫副产物为脱硫石膏。
在日本、德国脱硫石膏年产量分别为250万吨和350万吨左右,基本上都能综合利用,主要用途是用于生产建材产品和水泥缓凝剂。
脱硫副产物综合利用,不仅可以增加厂效益、降低运行费用,而且可以减少脱硫副产物处置费用,延长灰场使用年限。
(5)技术进步快。
近年来国外对石灰-石膏湿法工艺进行了深入的研究与不断的改进,如吸收装置由原来的冷却、吸收、氧化三塔合为一塔,塔内流速大幅度提高,喷嘴性能进一步改善等。
通过技术进步和创新,可望使该工艺占地面积较大等问题逐步得到妥善解决。
(6)占地面积小:锅炉现场虽然紧凑,但完全能够满足工艺设备布置。
(7)采用PLC模块控制,整套设备自动化程度高,操作简便,控制可靠,启停灵活。
4 脱硫工艺计算(单台计算)4.1 处理烟气量引风机风量:159000m3/h4.2 SO2原始排放浓度本设计浓度为4500mg/Nm34.3 脱硫效率本脱硫系统的脱硫效率应不低于η,以满足排标要求:η≥(4500-150)/4500×100%=96.6%4.4 生石灰粉耗量、年脱硫量、石膏年产量由3.1.2可简化成化学方程式:SO2+2H2O+Ga0+1/2O2=GaSO3·2H2O32 56 1566010 X Y=( 103*6010*56/32)/8400h/85%=1473kg/h每小时石灰耗量:G石灰h石灰年耗量:G石灰a=6010*56/32/85%=12375t/a=159000m3*0.0045kg*8400h*10-3=6010t/a年脱硫量:GSO2石膏年产量=(6010*156/32)*1.1= 32230t/a4.5 脱硫反应循环液气比取12~15 L/Nm34.6 Ca/S摩尔比取1.054.7 10%CaO浆液量每小时CaO浆液量:G=1473/10%=14730 kg/h 4.8 溶液循环流量=1908~2385 m3/h循环量G循环4.9耗水量每小时蒸发耗水量= 0.6 t每年耗水量:G=5040 t4.10电耗量电耗量:520kWh5 运行费用(单台系统)5.1 经济指标电费: 0.65元/kWh水费: 1.5元/吨石灰: 300元/吨石膏: 150元/吨人员工资: 3.5万元/人·年5.2 脱硫运行成本年运行时间按8400(24小时350天)小时计算:运行费用统计表.6 建造费用此方案采用一炉一塔式,塔身及内件采用玻璃钢材质,配有烟气系统、喷淋反应塔吸收系统、氧化钙制浆系统、石膏回收系统、废水处理系统、工艺水系统、自动控制系统等组成。