球墨铸铁性能及生产工艺共70页
球墨铸铁性能及生产工艺
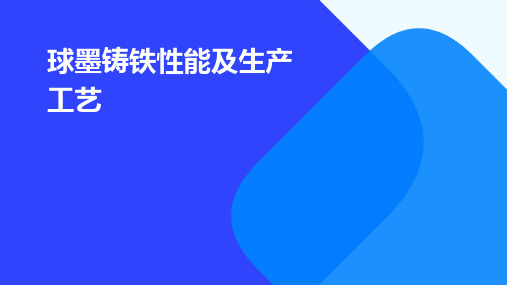
铸造缺陷预防
总结词
铸造缺陷会影响球墨铸铁的质量和性能,因此需要采取一系列措施预防铸造缺陷的产生。
详细描述
在生产过程中,要严格控制浇注温度、模具温度、冷却速度等工艺参数,以防止产生气 孔、缩孔、夹渣等铸造缺陷。同时,要定期检查模具的磨损情况,及时修复和更换损坏
的模具,以防止出现不均匀冷却等缺陷。
质量检测与评估
用于生产建筑构件、水 管、阀门等。
用于制造各种承受复杂 应力的机械零件和工具。
在电力、化工、船舶等 领域也有广泛应用。
02
球墨铸铁性能
力学性能
强度
球墨铸铁具有较高的强度,其抗拉强度和屈 服点均高于灰铸铁。
耐磨性
球墨铸铁的耐磨性优于其他铸铁,适用于需 要承受摩擦和磨损的场合。
韧性
球墨铸铁的韧性较好,不易脆化,能够承受 较大的冲击和振动。
提高生产效率与降低成本
自动化和智能化铸造生产线
采用先进的机器人技术、传感器技术和大数据分析技术, 实现铸造生产线的自动化和智能化,提高生产效率,降低 人工成本。
高效熔炼与连铸技术
研究新型的熔炼和连铸技术,提高铁水的纯净度和连铸坯 的质量,减少生产过程中的损耗和废品率,降低生产成本。
循环经济与资源再利用
的机械性能。
废钢
适量加入废钢,调节铁水成分,降 低成本。
球化剂和孕育剂
选用合适的球化剂和孕育剂,提高 球墨铸铁的球化率和石墨形态。
熔炼与浇注
熔炼
采用电炉或冲天炉熔炼铁水,控制熔炼温度和时间,确保铁 水质量。
浇注
根据铸件的大小和复杂程度,选择合适的浇注系统和浇注温 度,确保铁水充型良好。
球化与孕育处理
通过废旧铸件回收、再生利用和资源循环利用,降低原材 料成本,同时减少对环境的污染。
球墨铸铁生产工艺流程

球墨铸铁生产工艺流程1. 材料准备球墨铸铁的主要成分是铁、碳、硅和镁。
一般来说,球墨铸铁的成分控制在3.5%-3.9%的碳,2.2%-2.8%的硅,0.03%-0.06%的镁。
在制备球墨铸铁的过程中,需要准备精炼铁水、回炉铁、进口硅铁合金、球化剂等原材料。
2. 炉前工作在球墨铸铁的生产过程中,首先需要对电炉进行检查和清理,确保设备运行正常。
同时,检查原材料的质量和数量,确保可以满足生产需求。
此外,需要准备好炉前操作所需的工具和设备,以便顺利进行下一步工作。
3. 铁水处理将铁水倒入电炉中加热,同时加入进口硅铁合金和球化剂,经过一段时间的加热和充分搅拌后,将炉内的铁水进行处理。
通过添加进口硅铁合金和球化剂,可以改善铁水的流动性和液相组织,有利于球化铁水形成球墨体。
4. 浇注铸造在铁水处理完成后,将炉内的铁水倒入铸造模具中,待冷却后形成球墨铸铁坯件。
在浇注过程中,需要注意控制浇注速度和温度,以确保铸件质量。
同时,需要对浇注后的铸件进行冷却处理,以确保铸件的内部结构均匀和稳定。
5. 除砂清理在球墨铸铁的生产过程中,铸件表面通常会附着一层砂壳,需要进行除砂清理。
除砂清理的方法有机械清理、水压清理、化学清理等。
通过除砂清理,可以将铸件表面的砂壳去除,为后续的加工和装配工作提供条件。
6. 热处理球墨铸铁在生产过程中需要进行热处理,以提高其机械性能和耐磨性。
热处理的方法包括正火、淬火和回火,具体的热处理工艺参数需要根据不同的材料和要求进行调整。
通过热处理,可以改善球墨铸铁的硬度、强度和耐磨性。
7. 检验和包装最后,需要对球墨铸铁进行质量检验,包括化学成分分析、力学性能测试、金相分析等。
只有通过检验合格的球墨铸铁才能被包装出厂。
在包装过程中,需要注意保护铸件表面不受损坏,并标注清晰的产品信息,以便后续的使用和销售。
综上所述,球墨铸铁的生产工艺流程包括材料准备、炉前工作、铁水处理、浇注铸造、除砂清理、热处理、检验和包装等步骤。
球墨铸铁管生产工艺流程

球墨铸铁管生产工艺流程
1.材料准备:生产球墨铸铁管的主要原材料有铸铁、球墨铸铁抛丸砂、球墨铸铁造型砂以及铝镁合金等。
在生产之前,首先对这些原材料进行检
测和筛选,确保其质量和互相配比的准确性。
2.铸造准备:将合格的原材料混合,并按照一定的比例投入到铸铁炉
中进行熔炼。
在熔炼过程中,需要控制好炉内温度和炉内气氛,以保证熔
融铸铁的质量。
3.铸型制备:在熔化的铸铁熔液进行净化处理和温度调节后,将其倒
入球墨铸铁造型砂中,在铸型砂的辅助作用下形成球墨铸铁管的形状。
4.铸造操作:将铸型放置在铸造机上,并注入熔化的铸铁熔液。
在铸
造过程中,需要控制好铸铁的流动速度和温度,以保证球墨铸铁管的成型
质量。
5.出模和冷却:经过一定的时间后,铸造完成的球墨铸铁管从铸造机
上取下,并放置在冷却池中进行冷却。
冷却的过程中,需要逐渐降低管材
温度,以防止因温度变化过大而产生内部应力。
6.清理和检验:冷却后的球墨铸铁管经过打砂、清理等处理后,进行
外观检查和尺寸检测,以确保其质量符合要求。
7.补修和涂漆:对于有缺陷或尺寸不合格的球墨铸铁管,进行修复和
补焊,然后对整体进行除锈和涂漆处理,增加其防腐蚀能力和外观美观。
8.包装和发运:最后,对球墨铸铁管进行包装,并按照客户的要求进
行标记和装箱,最终发运到使用地点。
总之,球墨铸铁管的生产工艺流程涉及到材料准备、铸造准备、铸型制备、铸造操作、出模和冷却、清理和检验、补修和涂漆以及包装和发运等环节。
通过精细的工艺控制和质量检查,可以生产出高质量的球墨铸铁管,满足各种工程项目的需求。
球墨铸铁管生产工艺 球墨铸铁管生产所需的设备

球墨铸铁管产品功能、性能特征及技术参数说明一、球墨铸铁管质量标准和技术要求铸造方式:离心铸造工艺。
口径范围:DN100-1000mm。
重量及其允许偏差范围:壁厚按GB/T13295-2008标准K10、K9执行,重量最大偏差为-5%。
尺寸:符合GB/T13295-2008标准的要求;接口形式:滑入式T型胶圈接口。
胶圈的型式、尺寸及允许偏差符合GB/T 13295-2008标准附录C1.1的规定。
橡胶圈材质:三元乙丙橡胶,物理性能符合ISO 4633的要求。
材质:管道的材质为铁素体基体的球墨铸铁,在组织中有一定数量的球状石墨,组织致密,易于切削、钻孔,符合GB/T13295-2008的要求。
化学成份:球墨铸铁管的P含量≤0.05%,S含量≤0.015%。
机械性能:抗拉强度≥420Mpa,屈服强度≥300Mpa,延伸率≥10%,硬度≤230HBS。
密封性:球墨铸铁管出厂前水压试验压力5MPa,并保证无渗漏冒汗或其他损坏。
表面质量:内外表面光洁,光滑平整,轮廓清晰,无裂缝,冷隔、错箱等妨碍使用的明显缺陷,凡使壁厚减薄的局部缺陷允许存在,但其深度不得超过(2+0.05T)mm其中T为管体壁厚。
外形:当球墨铸铁管在间距约为管长L 2/3的两个台架上滚动校验时,球铁管的直线度最大偏差fm(mm)不应大于管有效长度L(m)的1.25倍,即fm(mm)≤1.25L。
有效长度:球墨铸铁管的有效长度为6000mm。
涂前,管件表面光洁、无铁锈、铁片及杂物,涂后,涂层表面光洁、均匀、粘附牢固,不因气温变化而发生异常。
内衬:采用水泥砂浆内衬,涂覆后附着力强,渗水率小,化学稳定性好,施工方便。
水泥内衬符合GB/T 17457-1998标准和GB/T 17219-1998标准的要求,水泥砂浆内衬材料全部由国家法定单位检验,放射性物质含量符合国家标准GB6566-2001的要求,确保需方输水管网水质达到国家相关标准要求。
外防腐:先采用热喷锌,热喷锌质量符合GB/T17456标准技术要求;再采用热喷涂沥青漆防腐处理,热喷涂沥青漆质量符合GB/T 17459标准技术要求。
球墨铸铁的工艺设计
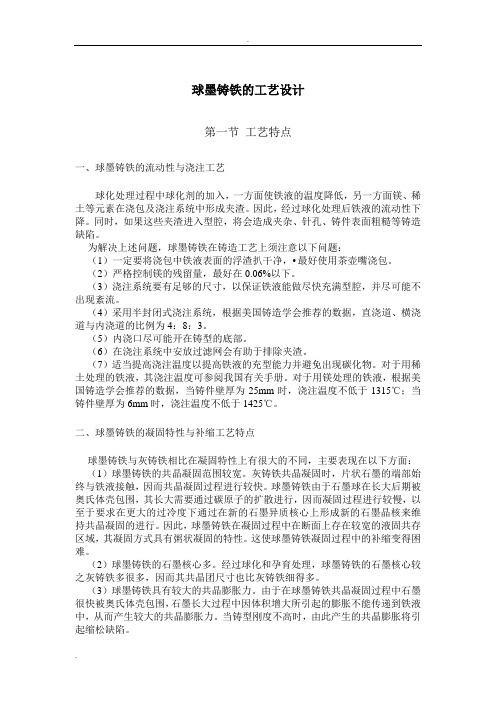
球墨铸铁的工艺设计第一节工艺特点一、球墨铸铁的流动性与浇注工艺球化处理过程中球化剂的加入,一方面使铁液的温度降低,另一方面镁、稀土等元素在浇包及浇注系统中形成夹渣。
因此,经过球化处理后铁液的流动性下降。
同时,如果这些夹渣进入型腔,将会造成夹杂、针孔、铸件表面粗糙等铸造缺陷。
为解决上述问题,球墨铸铁在铸造工艺上须注意以下问题:(1)一定要将浇包中铁液表面的浮渣扒干净,•最好使用茶壶嘴浇包。
(2)严格控制镁的残留量,最好在0.06%以下。
(3)浇注系统要有足够的尺寸,以保证铁液能做尽快充满型腔,并尽可能不出现紊流。
(4)采用半封闭式浇注系统,根据美国铸造学会推荐的数据,直浇道、横浇道与内浇道的比例为4:8:3。
(5)内浇口尽可能开在铸型的底部。
(6)在浇注系统中安放过滤网会有助于排除夹渣。
(7)适当提高浇注温度以提高铁液的充型能力并避免出现碳化物。
对于用稀土处理的铁液,其浇注温度可参阅我国有关手册。
对于用镁处理的铁液,根据美国铸造学会推荐的数据,当铸件壁厚为25mm时,浇注温度不低于1315℃;当铸件壁厚为6mm时,浇注温度不低于1425℃。
二、球墨铸铁的凝固特性与补缩工艺特点球墨铸铁与灰铸铁相比在凝固特性上有很大的不同,主要表现在以下方面:(1)球墨铸铁的共晶凝固范围较宽。
灰铸铁共晶凝固时,片状石墨的端部始终与铁液接触,因而共晶凝固过程进行较快。
球墨铸铁由于石墨球在长大后期被奥氏体壳包围,其长大需要通过碳原子的扩散进行,因而凝固过程进行较慢,以至于要求在更大的过冷度下通过在新的石墨异质核心上形成新的石墨晶核来维持共晶凝固的进行。
因此,球墨铸铁在凝固过程中在断面上存在较宽的液固共存区域,其凝固方式具有粥状凝固的特性。
这使球墨铸铁凝固过程中的补缩变得困难。
(2)球墨铸铁的石墨核心多。
经过球化和孕育处理,球墨铸铁的石墨核心较之灰铸铁多很多,因而其共晶团尺寸也比灰铸铁细得多。
(3)球墨铸铁具有较大的共晶膨胀力。
球墨铸铁500—7的铸造生产工艺

球墨铸铁500—7的铸造生产工艺作者:张燕明针对铸件结构、尺寸特点,选择适当的化学成分,使用球铁专用浇包,加强球化处理过程控制,稳定生产出符合技术要求的铸态QT500-7薄壁小型球墨铸铁件铸态高强度球墨铸铁的生产可以通过合金化强化基体组织等措施而获得,但是铸态综合性能良好的QT500-7球墨铸铁的生产,由于生铁、废钢和合金等原材料含有许多强化基体组织的微量合金元素导致球墨铸铁的性能下降,其生产难度较大。
现将我公司小型(重量1~10Kg)、薄壁球墨铸铁件(壁厚5~20mm)多年生产实践总结如下。
1性能及金相组织的要求抗拉强度≥500N/mm2,屈服强度≥320N/mm2,延伸率≥7,布氏硬度170~230,球化等级≤3,珠光体15?~45?,渗碳体≤1,石墨大小≥6级。
2化学成分的选择化学成分对集基体组织和铸造生铁机械性能起着重要作用,根据铸件结构特点、大小及要求化学成分选择如下:3.6?~3.9?C,原铁液含Si量选择为1.2?~1.6?,终Si量控制在2.6?~2.9?,碳当量(CE):4.5?~4.7?,0.2?~0.3?Mn,<0.05?P,<0.03?S,<0.03?RE残,0.035?~0.06?Mg同时应保证RE残/Mg残≤2/3。
3球化处理工艺笔者所在的企业采用0.5T中频炉熔化铁液,出铁温度在1520℃以上。
采用0.5T球铁专用凹坑式浇包冲入法进行球化处理。
球化剂为GB4138-88的FeSiMg8RE5,孕育剂为硅钡复合孕育剂,炉前检验合格后,快速浇注。
控制浇注时间在15min内,防止球化孕育衰退。
3.1球化剂处理铁液量0.5吨,球化剂的粒度应为10~20mm,球化剂粒度小于10mm的质量分数不大于10?,球化剂应烘干并预热,预热温度最好在150~200℃,如无条件也可制作专用料斗在炉口烘烤。
生产球铁希望铁液温度高,气体含量小不氧化,化学成分稳定。
现国内多采用各种冲天炉熔炼铁液,由于各种炉型都有自己的特点,应从实际出发,选择更利于生产球铁的炉型。
关于球墨铸铁的工艺

关于球墨铸铁的工艺
球墨铸铁是一种铸铁的变种,也被称为球墨铸造、球墨铁、球形石墨铸铁等。
它是通过在铸铁中加入球状石墨形成的,使其具有更好的韧性和良好的抗拉强度。
球墨铸铁的工艺主要包括以下几个步骤:
1. 材料选择:选择合适的生铁和铸造辅助材料,通过合理的混配,得到适合球墨铸铁生产的铁水。
2. 融化和浇注:将所选材料投入到高温炉中进行融化,融化后的铁水通过浇注系统注入到铸造模具中。
3. 控制冷却速度:在铸铁凝固过程中,需要控制冷却速度以控制石墨球的形态和分布。
一般采用加入合适的冷却剂或设计合适的冷却方式来实现。
4. 顶水处理:在铸铁凝固后,通过顶水操作来扩展铁水的容积,进而使球墨铸铁材料中形成球状石墨。
5. 退火处理:球墨铸铁在顶水处理后会存在一定的应力和组织不稳定性,需要进行适当的退火处理,使其获得更加稳定的组织和性能。
6. 加工和热处理:球墨铸铁可以通过机械加工、热处理等方式进行进一步的改性和提升性能。
球墨铸铁的工艺需要严格控制各个环节,包括材料的选择与配比、浇注温度和速度的控制、冷却方式的选择、顶水处理的操作等。
这些环节的控制会直接影响到
球墨铸铁材料的性能和质量。
球墨铸铁熔炼与铸造工艺

球墨铸铁是一种高强度、高韧性的铸铁材料,其熔炼与铸造工艺主要包括以下几个步骤。
原料准备:主要原料是铸铁和球化剂。
铸铁通常是废铁、废钢等回收材料,而球化剂则是一种能够使铸铁中的碳以球形形式存在的添加剂。
熔炼铸造:将原料放入高温熔炉中进行熔炼,熔炼温度通常在1400℃以上。
在熔炼过程中,加入球化剂,使铸铁中的碳以球形形式存在。
浇注铸造:将熔融的球墨铸铁液体倒入铸型中,待其冷却凝固后,取出铸件。
热处理:对铸件进行热处理,以提高其强度和韧性。
通常采用淬火和回火的方法进行热处理。
加工和表面处理:对铸件进行加工和表面处理,以达到所需的形状和表面质量。
在整个铸造过程中,还需要特别注意以下几点:
球墨铸铁铸造工艺比普通灰铁铸件造型更为严格,其缩量要大于普通灰铁铸件,因此在造型时要加大冒口尺寸,确保冒口内铁液能够完全补充需要的缩量。
造型用型砂不能使用水泥砂造型,而要选用树脂砂或水玻璃砂进行造型,且耐火涂料要选择高温耐火材料。
在熔炼过程中,要严格控制球墨铸铁的含量要求,如要求球墨铸件材质为QT450材质,就需要控制五大元素含量在特定范围内。
浇铸时要采用高温出炉低温浇铸的原则,开始浇铸后要保证每个冒口铁液都能浇满,并持续为冒口补充铁液直至冒口内铁液不再下沉减少为止。